本紹介論文は、[Publisher]によって出版された論文「Hohl- und Verbundguss von Druckgussbauteilen – Numerische Auslegungsmethoden und experimentelle Verifikation」の研究内容です。
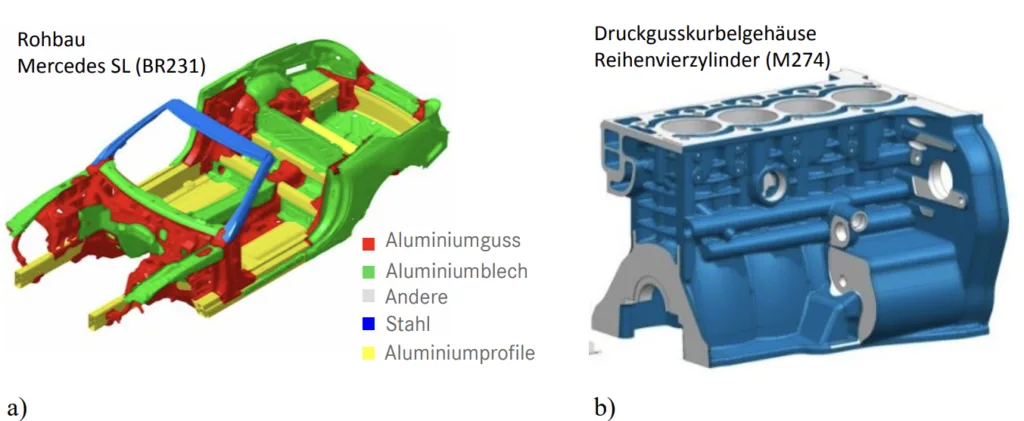
1. 概要 (Overview):
- タイトル: Hohl- und Verbundguss von Druckgussbauteilen – Numerische Auslegungsmethoden und experimentelle Verifikation (ダイカスト部品のキャビティおよび複合鋳造 – 数値設計手法と実験的検証)
- 著者: Paul Fickel
- 出版年: 2017
- 掲載ジャーナル/学会: Fakultät Energie-, Verfahrens- und Biotechnik der Universität Stuttgart (シュトゥットガルト大学 エネルギー・プロセス工学・バイオテクノロジー学部)
- キーワード: Hinterschnitten (アンダーカット), Druckguss (ダイカスト), Salzkerne (ソルトコア), St-Al-Verbunde (鋼-アルミニウム複合材), Numerische Auslegungsmethoden (数値設計手法), experimentelle Verifikation (実験的検証)
2. 概要 (Abstract)
最新技術によると、アンダーカットを持つアルミニウム高圧ダイカスト(HPDC)部品の製造プロセスは、HPDCツールに統合された複雑なスライダーを使用することによってのみ可能です。サンドコア、流体噴射、ガラスコア、金属溶融コア、または圧縮ソルトコアなどの既知のシステムは、HPDCプロセスで制限付きでのみ使用可能です。したがって、現在、液相から製造されたソルトコアと金属インサートのみが、HPDCでうまく使用される可能性があります。鋳造ソルトコアは、高レベルの曲げおよび圧縮強度を達成し、アルミニウム鋳造プロセスの後、例えばウォータージェット切断によって残留物なしで除去することができます。アルミニウム鋳造品に残る鋼インサートは、部品を補強します。この作業は、鋳造ソルトコアの製造を可能にするためのいくつかの基礎研究を提示します。予備調査では、塩化ナトリウム-炭酸ナトリウム相図内の塩合金が、さらなる調査のために選択されます。主要な試験片に基づいて、プロセスパラメータの依存性と、結果として生じる強度および高温割れ傾向が実証されます。機械的特性評価のために、曲げ、引張、および圧縮試験が室温および最大500°Cの温度で実行されます。ソルトコア鋳造プロセスの数値シミュレーションへのアプローチが提示され、実験結果によって検証されます。ソルトコアに加えて、鋼インサートが調査され、アルミニウム-鋼複合構造が特徴付けられました。力-、形状-、および化学的結合が考慮されました。鋼インサートとアルミニウム鋳造間のより良い化学結合のために、さまざまなコーティングが適用され、等級分けされました。機械的引張、押出し、剪断、および接着引張試験、ならびに光学および走査型電子顕微鏡調査が、結合品質を特徴付けるために実行されました。これに基づいて、数値シミュレーション手法が開発されました。HPDCプロセス中のソルトコアと鋼インサートの生存可能性と破壊挙動が調査されました。したがって、コアの生存可能性を予測するための数値的手法が導入され、実験結果によって検証されました。両方の技術が応用例に転用されました。
3. 研究背景 (Research Background):
研究テーマの背景 (Background of the research topic):
アンダーカットを持つアルミニウム構造部品の製造は、スライダー、砂型システム、ガス噴射プロセス、ガラスコア、金属溶融コア、または圧縮ソルトコアを使用するダイカストプロセスにおいて制約があります。現在、液相から製造されたソルトコアと永久金属インサートのみがダイカストで使用できる可能性があります。
先行研究の状況 (Status of previous research):
第2章で詳述されている先行研究では、以下を含む、ダイカストでアンダーカットを作成するためのさまざまな方法を調査しました。
- プロセス関連のアプローチ (Process-related approaches): スライダー技術 (Schiebertechnologie) およびガス噴射 (Gasinjektion).
- 永久インサート (Permanent inserts): 金属フォーム (Metallschäume)、鋼鉄および軽金属インサート (Stahl- und Leichtmetalleinleger)、Combicore インサートチューブ (Combicore Einlegerohre).
- 消失性中子技術 (Lost core technology): ダイカストプロセスにおける消失性中子 (Verlorene Kerntechnologie) の現在の取り組み、特にダイカストでアンダーカットを作成するためのソルトコア (Salzkerne zur Herstellung von Hinterschnitten im Druckguss).
- ダイカストにおけるインサートの数値モデリング.
研究の必要性 (Need for research):
軽量構造を可能にするために、現在の鋳造プロセスと材料を開発する必要があります。特に、耐圧消失性中子 (セラミックまたはソルト) の開発と、高強度金属インサートを使用したダイカストプロセスの最適化が必要です。
4. 研究目的と研究課題 (Research purpose and research question):
研究目的 (Research purpose):
本研究の全体的な目的は、鋳造ソルトコアを用いて、力-適合、形状-適合、および一体結合された鋼-アルミニウム結合と、複雑な中空鋳造部品を数値的に設計するために必要なデータを開発することです。この研究では、鋼-アルミニウム複合鋳造(St-Al-Verbundguss)とソルトコア(Salzkerne)の使用を調査します。
主要研究課題 (Core research):
- 鋳造ソルトコア製造の基礎を実験的および数値的に調査します。
- 塩化ナトリウム-炭酸ナトリウム相図から塩合金を選択します。
- 実験研究によって検証された、ソルトコア製造プロセスのためのシミュレーション手法を確立します。
- ダイカストにおける鋼インサートを研究します。
- 鋼インサートとアルミニウム鋳造の化学的結合を改善するために、さまざまなコーティングを適用および評価します。
- 機械的試験および金属組織学的手法による特性評価。
- 結合 (力-適合、形状-適合、および一体結合) のためのシミュレーション手法を開発および適用します。
- ダイカスト試験におけるコア荷重と損傷挙動を調査します。
5. 研究方法論 (Research Methodology)
この研究では、実験的方法と数値的方法の両方を使用します。
- 実験的方法 (Experimental): 基本形状および試験片、金型設計、試験環境を作成します。塩合金のバリエーションを計画し、機械的および金属組織学的手法を用いて材料を特性評価します。曲げ棒およびスパイラル鋳造試験を用いて材料モデルを調整します。鋳造プロセスも実験を用いて検討します。
- 数値的方法 (Numerical): ソルトコア製造プロセス、熱亀裂予測、包囲プロセスの表現のためのシミュレーションモデルを開発します。ソルトコアおよびインサート荷重の予測、鋼-アルミニウム複合材の特性評価、数値表現のためにシミュレーションを実施します。凝集結合のモデリング手法も開発します。
- 分析方法 (Analysis method): 有限差分法(Finite-Difference-Method, FDM), 有限要素法(Finite-Element-Method, FEM)
6. 主要研究結果 (Key research results):
主要研究結果と提示されたデータ分析 (Key research results and presented data analysis):
このプロジェクトは、検証済みシミュレーション手法の開発と実験的調査を組み合わせます。この研究は、ソルトコアの製造プロセス、ダイカスト中のコアおよびインサートの荷重、結果として生じる鋼-アルミニウム複合材の特性評価/シミュレーションのプロセスを理解することに焦点を当てています。塩の組成と鋳造パラメータは、熱亀裂などの欠陥形成に大きな影響を与えました。
![[2] HENNING, F.; MOELLER, E.: Handbuch Leichtbau Methoden, Werkstoffe, Fertigung. Carl Hanser Verlag München Wien, 2011, ISBN 978-3-446-42267-4](https://castman.co.kr/wp-content/uploads/image-1547-1024x355.webp)
![[3] KLEIN, B.: Leichtbau-Konstruktion Berechnungsgrundlagen und Gestaltung. 10. Auflage Springer Fachmedien Wiesbaden, 2013, ISBN 978-3-658-02271-6](https://castman.co.kr/wp-content/uploads/image-1548-1024x379.webp)
![[4] OSTERMANN, F.: Anwendungstechnologie Aluminium. 2. Auflage Springer-Verlag Berlin Heidelberg, 2007, ISBN 978-3-540-71196-4](https://castman.co.kr/wp-content/uploads/image-1549-1024x286.webp)
![[8] ILSCHNER, B.; SINGER, R.F: Werkstoffwissenschaften und Fertigungstechnik – Eigenschaften, Vorgänge, Technologien. 5. Auflage Springer-Verlag Berlin Heidelberg, 2010, ISBN 978-3-642-01733-9](https://castman.co.kr/wp-content/uploads/image-1550-1024x359.webp)
![Abbildung 2.9: Salzkerne für Gießanwendungen: a) oben: Geschossener Salzkern; unten: Im Druckgussverfahren hergestellter Salzkern [12], b) gepresste und gesinterte Salzkerne der Fa. Emil-Müller-GmbH / CeramTec AG [48]](https://castman.co.kr/wp-content/uploads/image-1551-1024x553.webp)
![Abbildung 2.11: Bühler Pilotbauteil [54]: a) Salzkern Pilotbauteil, b) Schnitt durch Pilotbauteil
mit sichtbarem Salzkern, c) Schnitt durch Pilotbauteil entkernt](https://castman.co.kr/wp-content/uploads/image-1552-1024x328.webp)
![Abbildung 2.12: Phasendiagramm für NaCl+Na2CO3 [62] mit eingezeichneten Gitterstrukturänderungen und dazugehörigen Gittertypen](https://castman.co.kr/wp-content/uploads/image-1553-1024x731.webp)
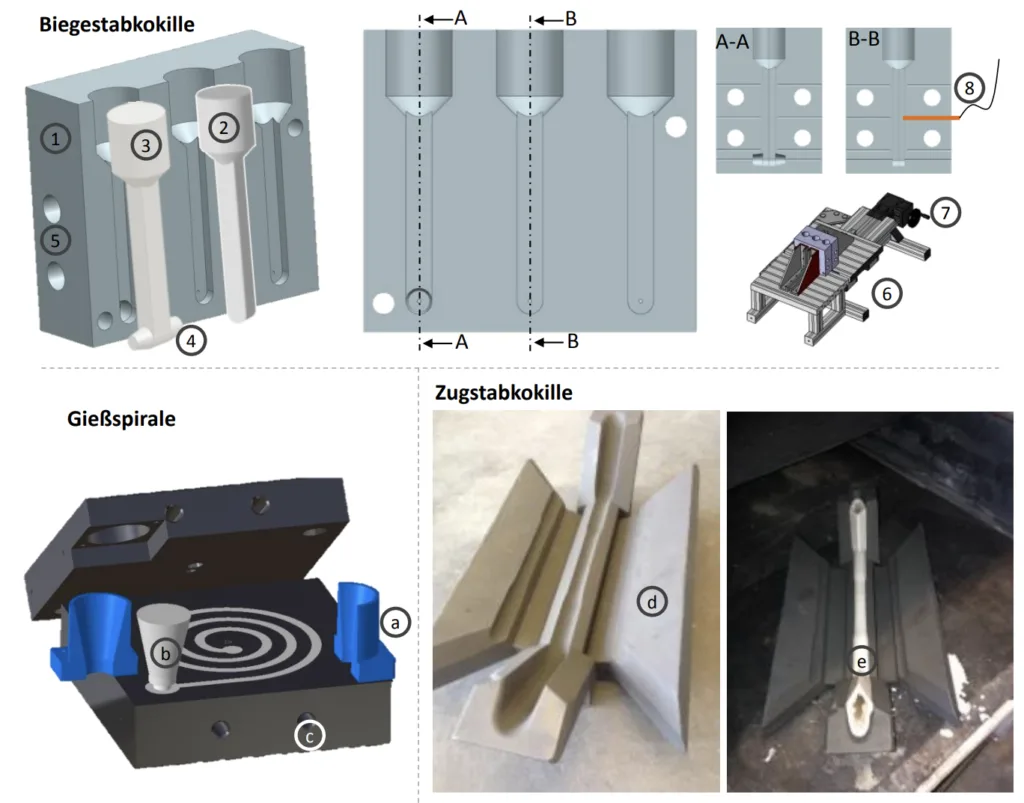
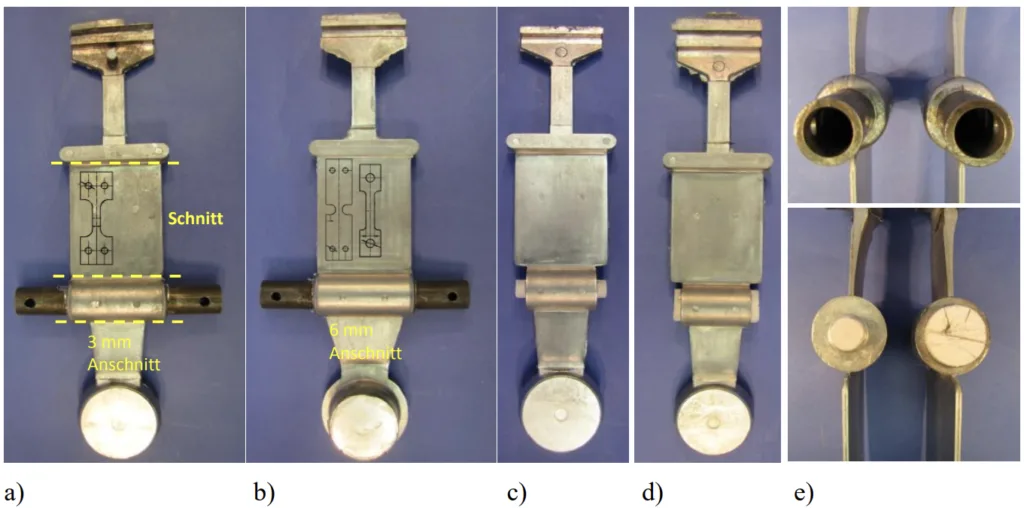
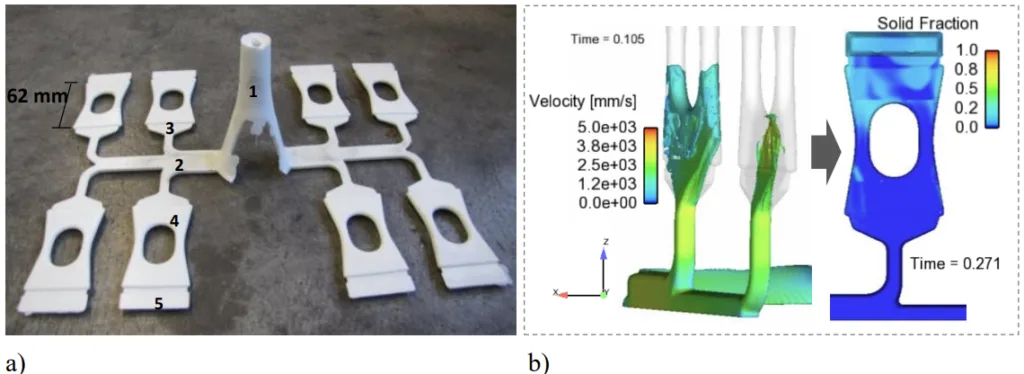
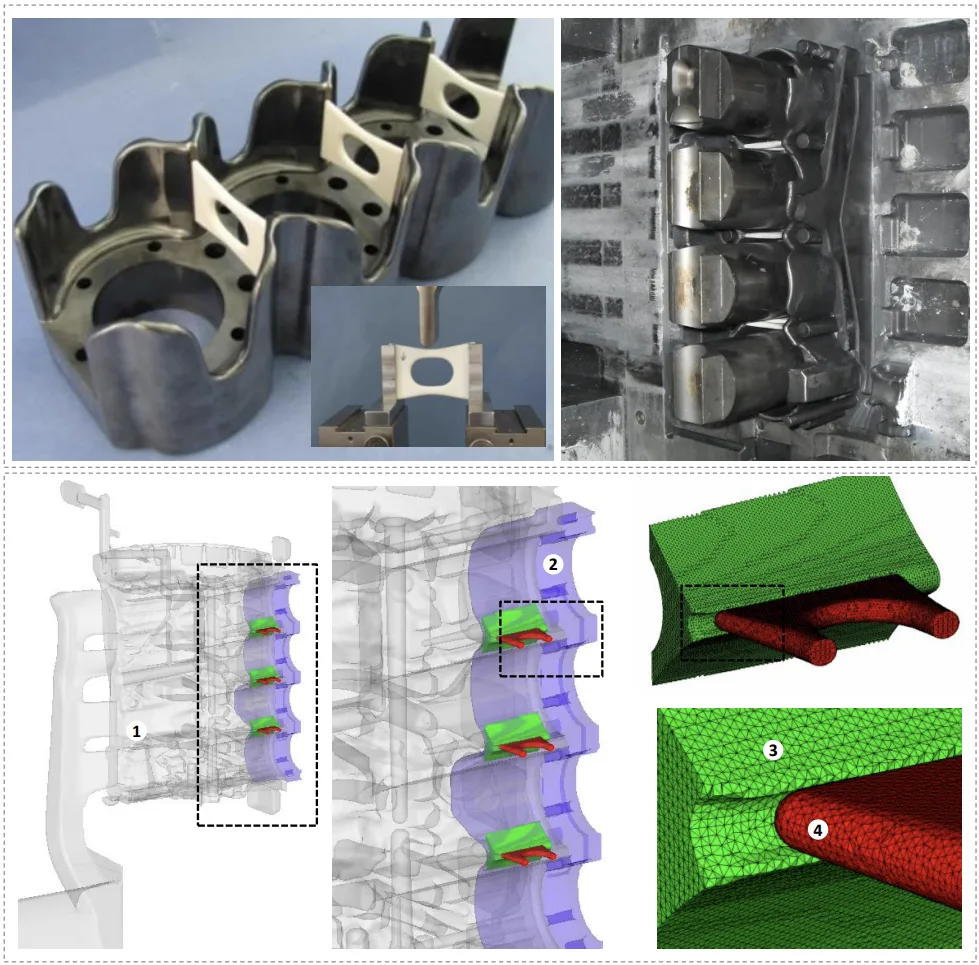
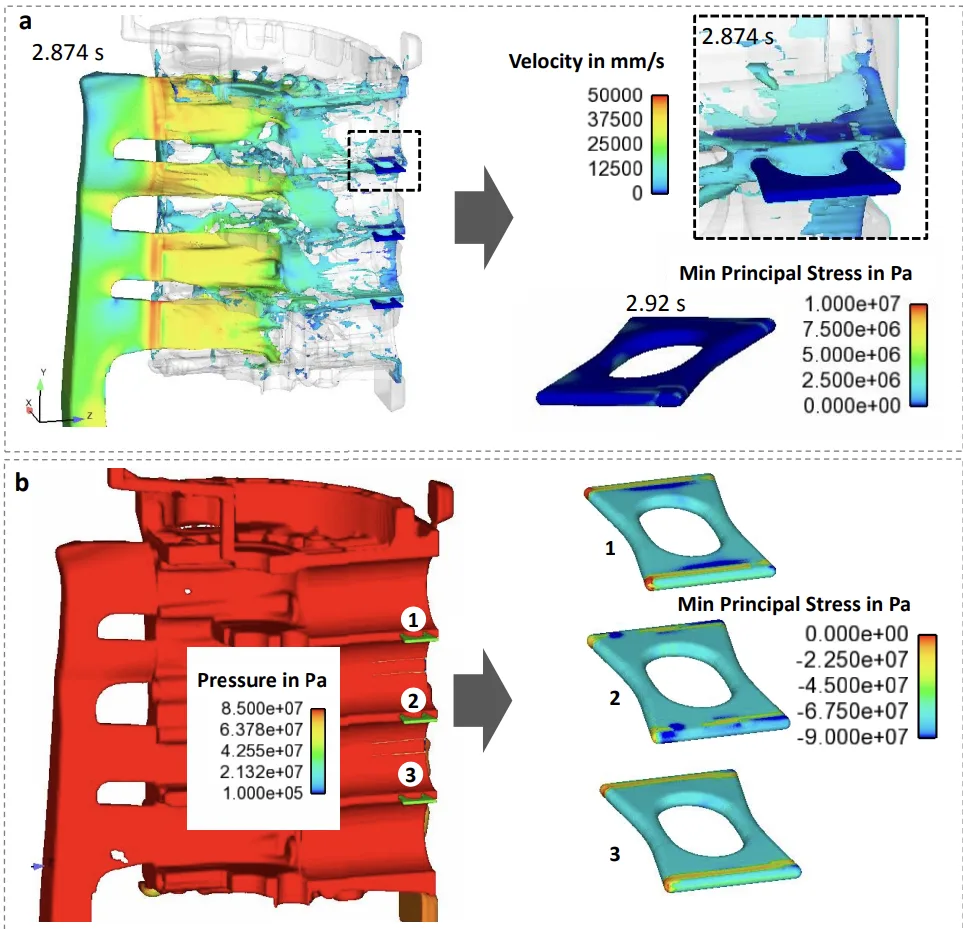
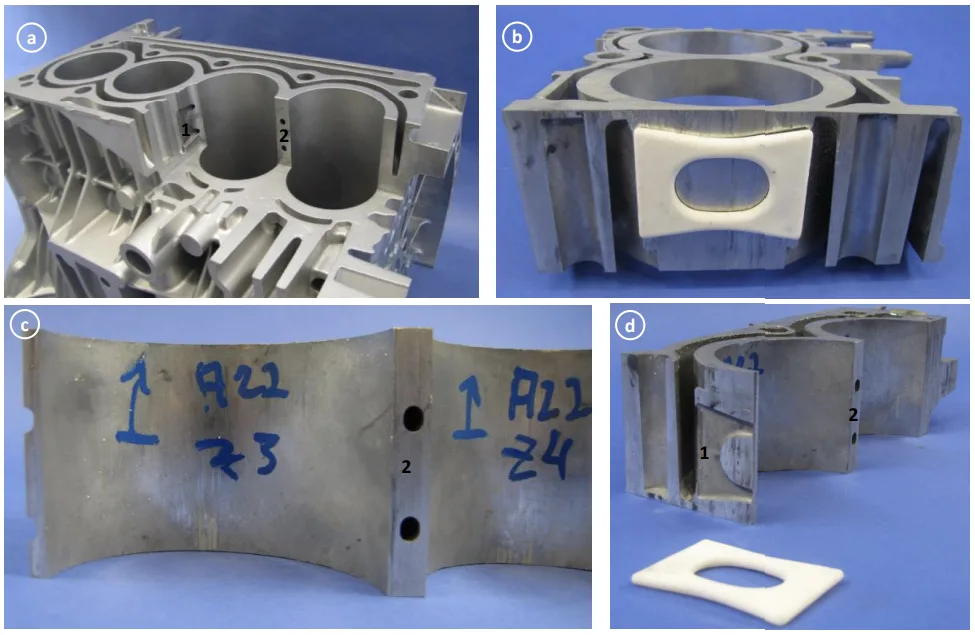
図表リスト (List of figure names):
- Abbildung 1.1: a) Rohbau des Mercedes SL (BR231) inkl. Angabe der verwendeten Materialien, b) Druckgusskurbelgehäuse am Beispiel eines Reihenvierzylinders M274
- Abbildung 2.1: a) Fluidmanagementmodul mit sieben Schiebern [9], b) Druckgusswerkzeug mit komplexem Schieber (1), Schieberkulisse (2) und Hydraulikaggregat (3) [10][11]
- Abbildung 2.2: Ölfiltergehäuse mit dreidimensional verlaufenden medienführenden Kanälen [9] a) Gussbauteil, b) Röntgenaufnahme des Gussbauteils, c) Schnitt der Hohlgeometrie
- Abbildung 2.3: Demonstratorbauteil mit umgossenem Schaumkern [13], a) Demonstrator in der Ansicht von oben und im Schnitt, b) Ausschnitt aus umgossener Schaumplatte
- Abbildung 2.4: Beispiel für eine Verbundgussanwendung a) Variostruct®-Hybrid Stahl-Aluminium mit Anschnitten und Überlauf [17], b) Prinzipgeometrie ausgeführt als Formschlussprobe [17], c) Dachquerträger als SADH (Stahlblech-Aluminiumdruckguss-Hybrid) [17][21]
- Abbildung 2.5: Beispiele für einen Verbundgussdemonstrator [22] sowie die Bildung von intermetallischen Phasen im Benetzungs- und Tauchversuch zwischen Stahlblechen und Aluminiumlegierungen: a) Eine kraft-und formschlüssige Stahl-Aluminium Verbindung, hergestellt im Squeezecasting-Verfahren, b) Benetzungsprobe Stahl-Al99,98 [24], c) oben: Al-Al-Verbindung nicht behandelt; unten: Al-Substrat behandelt mit 3-stufigem Prozess [25]
- Abbildung 2.6: Combicore-Einlegerrohre[38]; a) Darstellung verschiedener Einlegerrohre zur Realisierung verschiedener Kanalgeometrien, b) Schnitt durch ein umgossenes Combicore-Rohr, c) Teilschnitt eines Combicore-Rohr inkl. eingebetteter Drahtwendel
- Abbildung 2.7: Darstellung von Hohlräumen mit Sand- und metallischen Ausschmelz-kernen: a) Druckgussbauteil mit Sandkern, oben: Längsschnitt durch Umgussbauteil, unten: entkerntes Bauteil [6], b) Druckgussbauteil mit Ausschmelzkern, oben: Längsschnitt durch Umgussbauteil, unten: aufschmelzendes metallisches Kernmaterial [6]
- Abbildung 2.8: Darstellung von Hohlräumen mittels Glas- und Keramikkernen: a) Glaskern und dazugehöriges Umgussbauteil für ein Pumpengehäuse [44], b) Prototyp eines Einzylinder-motorblocks, hergestellt mittels Keramikkern [44]
- Abbildung 2.9: Salzkerne für Gießanwendungen: a) oben: Geschossener Salzkern; unten: Im Druckgussverfahren hergestellter Salzkern [12], b) gepresste und gesinterte Salzkerne der Fa. Emil-Müller-GmbH / CeramTec AG [48]
- Abbildung 2.10: Gepresste Salzkerne und Druckgussumguss a) links: gepresster Salzbiege-riegel und Umgussbauteil; rechts: CT-Aufnahme des Umgussbauteils [10], b) entkerntes verripptes Hohlgussbauteil, hergestellt mit einem gepressten Salzkern [52]
- Abbildung 2.11: Bühler Pilotbauteil [54]: a) Salzkern Pilotbauteil, b) Schnitt durch Pilotbauteil mit sichtbarem Salzkern, c) Schnitt durch Pilotbauteil entkernt
- Abbildung 2.12: Phasendiagramm für NaCl+Na2CO3 [62] mit eingezeichneten Gitterstruktur-änderungen und dazugehörigen Gittertypen
- Abbildung 2.13: Schematische Abbildung der Kristallstruktur und des Risswachtstums für verschiedene Salzzusammensetzungen, a u. b : Eutektische Zusammen-setzung, c u. d: Reinsalz, e u. f: Zusammensetzung zwischen Eutektikum und Reinsalz [56]
- Abbildung 2.14: Diskretisierung eines Kreisbogens im Beispiel mit a) der Finite-Differenzen-Methode und Viereckselementen und b) der Finite-Element-Methode und unstrukturierten Dreickeckselementen, nach [72]
- Abbildung 2.15: Belastungssimulation für Salzkerne im Druckguss: a) Darstellung mean iso stress der Bühler Salzkerne bei Anschnittgeschwindigkeit 80 m/s oben und 120 m/s unten [86]
- b) Belastung für gepresste Salzkerne bei Anschnitt-geschwindigkeit 15 m/s oben und 35 m/s unten [10]
- Abbildung 3.1: Vorgehensweise und Arbeitspakete der vorliegenden Arbeit
- Abbildung 4.1: Darstellung der Biegestab-, Gießspiralen- und Zugstabkokille für die Salzkernprinzipuntersuchungen
- Abbildung 4.2: Skizzierter, nicht maßstabsgetreuer Versuchsaufbau für die Prinzip-untersuchungen mit der Biegestab- und Spiralkokille
- Abbildung 4.3: a) Aufbau des 3-Punkt-Biegeversuchs für die Ermittlung der Biegefestig-keiten von Salzkernen; b) Aufbau der Druckprüfung inkl. Probenabbildung zur Ermittlung der Druck-festigkeiten von Salzkernen; c) Prüfaufbau für die Zugprüfung
- Abbildung 4.4: Na2Cl-Na2CO3 Phasendiagramm inkl. eigezeichneter molarer Zusammen-setzungen für die Voruntersuchungen und Bereiche mit den zu erwartenden höchsten mechanischen Festigkeiten
- Abbildung 4.5: a) Gegenüberstellung der gemittelten Abkühlkurven für die Salzlegierungen Nr. 1 bis Nr. 7. b) Exemplarische Ergebnisdarstellung der stark untereutektischen, der unter-eutektischen und der stark übereutektischen Salzlegierungen für die Voruntersuchungen zur Auswahl einer geeigneten Salzlegierungsmischung
- Abbildung 4.6: a) Darstellung der Abkühlkurven im Mehrfachkokillen Gießexperiment für die Prozessparameterkombination =720 °C/ = 300 °C, =700 °C/ = 200 °C und = 680 °C/ = 100 °C b) Vorgehen zur Ermittlung der Abkühlraten im Biegestäbchen-gießversuch exemplarisch dargestellt an dem Prozessparameter TS =720 °C, TK =300 °C
- Abbildung 4.7: Darstellung der Gießspiralen bei den Prozessparametern = 720 °C/ = 300 °C, =700 °C/ = 200 °C und =680 °C/ = 100 °C
- Abbildung 4.8: Übersicht der Rissentstehung in der Warmrissprobe bei = 700 °C, die Ergebnisse sind tabellarisch dargestellt bei = 100 °C, 200 °C und 300 °C sowie der Ausformzeit von 15 s, 30 s, 45 s und 60 s inkl. Beispiel für die Rissgruppeneinteilung
- Abbildung 4.9: Simulationsmodell für die Mehrfachkokille in Flow3D, Darstellung der Ver-netzung, der Einfüllöffnung und der History Probes zur Aufzeichnung der Temperaturkurven
- Abbildung 4.10: Netzrandbedingungen und Oberflächentemperaturen im Mehrfachkokillen-modell dargestellt für = 100 °C, = 200 °C und = 300 °C
- Abbildung 4.11: a) Gießspiralemodell in Flow3D mit Darstellung der Schmelzeinitiierung (1) und der Vernetzung der Spirale (2 u. 3), b) Oberflächentemperaturen der Spiralkokille bei 100 °C, 200 °C und 300 °C Kokillentemperatur
- Abbildung 4.12: a) FDM-Vernetzung der Rissprobengeometrie, b) FEM-Vernetzung der Rissprobengeometrie, c) FEM Vernetzung der Mehrfachkokille zur Realisierung der Festkörperinteraktion zwischen Kokille und erstarrender Schmelze
- Abbildung 4.13: Darstellung des Temperaturfeldes im Verlauf der Erstarrung im Längschnitt bei der Rissprobengeometrie für das FDM-Netz (oben) und FEM-Netz (unten)
- Abbildung 4.14: a) Prinzipgeometrie für Verbundgussuntersuchungen inkl. Angabe des Umguss- und Einlegermaterials und Darstellung der Zugprobenentnahme-bereiche; b) Einleger-variation im Druckgussversuch, 1: geteiltes Rohr für Auszugversuche, 2: 30 mm Salzkern für Aluminiumcharakterisierung, 3: 17 mm Salzkern zur Darstellung der Einlegerbelastung
- Abbildung 4.15: a) Modulares Werkzeugkonzept für die Druckgussuntersuchungen. Gekennzeichnet sind der Formrahmen, die Entlüftung, der Werkzeugeinsatz und der 6 mm sowie 3mm Anschnitt, b) Schematische Darstellung des Druckgussumgussprozesses mit dem 6mm Anschnittsystems und prozesstechnischer Abfolge (1-3). In 2.1 – 2.3. sind zudem die neben dem Stahlrohr alternativen Einleger dargestellt.
- Abbildung 4.16: Darstellung der Versuchsergebnisse aus den Druckgussumgussversuchen, a) Verbundgussgeometrie mit 3mm-Anschnitt mit eingezeichneten Trennebenen und Zugprobenentnahmeposition, b) Verbundgussgeometrie mit 6mm-Anschnitt, c) Umguss-geometrie mit ∅ 17 Salzkern, d) Umgussgeometrie mit ∅ 30 Salzkern, e) Darstellung der Abbildungen a - d in den Seitenansicht
- Abbildung 4.17: Darstellung des Niederdruckgussprozesses für die Herstellung der Verbundgussgeometrie als CAD-Geometrie und Realbauteil. Dargestellt sind die Einlegertechnik (1) und (2) sowie die Formpakete (3) und das zentrale Anschnittsystem
- Abbildung 4.18: Darstellung der Versuchsabgüsse im Niederdruckguss: a) Darstellung der ∅ 17 und ∅ 30 Salzkerne und der Thermoelementpositionen (1) an den Stahlrohren, b) Gussrohling der Niederdruckgussversuche, c) Verputzte Versuchsgeometrie mit eingezeichneter Schnittebene
- Abbildung 4.19: a) Flow3D Modell für die Abbildung der Druckgussexperimente; Dargestellt sind die charakteristischen Modellinhalte 1-7 sowie der Übergang an der Vernetzung (8) mit unterschiedlicher Netzgröße, b) Darstellung der FEM-Vernetzung der Einlegerhülsen mit Salzkern sowie des Stahlrohrs und der Kavität
- Abbildung 4.20: Prozessablauf eines Druckgussumgussversuchs, dargestellt an dem Kolben-druck und der Kolbengeschwindigkeit über der Prozesszeit sowie an charakteristischen Zeitpunkten aus der Füllsimulation
- Abbildung 4.21: Darstellung der von Mises-Spannung im Salzkern und der Schmelze-geschwindigkeit für drei charakteristischer Zeitpunkte im Füllprozess der Umgussprinzip-geometrie, a) Umschaltpunkt von erster zur zweiten Phase, b) erstes Auftreffen der Schmelze auf den Salzkern, c) Nachdruckphase
- Abbildung 4.22: Vorgehen beim Auszugversuch zur Charakterisierung der Anbindungsqualität zwischen Stahleinleger und Aluminiumumguss, a) ungeprüfte Auszugprobe und Prüfaufnahme, b) Versuchsaufbau im CAD-Schnitt und Realbauteil, c) teilgeprüfte Probe nach 15 mm Traversenverfahrweg, d) vollständig ausgezogene Probe im CAD-Schnitt und Realbauteil
- Abbildung 4.23: a) Ausdruckversuch zur Charakterisierung der Anbindung zwischen Einleger und Umgussmaterial und Darstellung der Ringbeschriftung, b) Aufbau für die Haftzugprüfung an der geteilten Verbundguss-Ringgeometrie, exemplarisch dargestellt für eine feuerverzinkte Probe
- Abbildung 4.24: a) Schwerzugversuch für die Charakterisierung der Anbindung auf Scherung, b) exemplarische Darstellung einer geprüften Haftzug- bzw. Scherzugprobe am Beispiel eines feuerverzinkten Stahleinlegers
- Abbildung 4.25: Stahl-Aluminiumverbundgussbauteil mit Zink-Zwischenschicht, hergestellt im Druckguss: a) Lichtmikroskop-, b) Rasterelektronenmikroskopaufnahme
- Abbildung 4.26: a) Technische Zeichnung der Miniflachzugprobe mit einer Wandstärke von 2mm, b) Fließkurvenapproximation am Beispiel AlSi9MgMn-T6
- Abbildung 4.27: Auswertung der Härtemessung nach Brinell für die Zugprobe und die Umgussgeometrie mit einer linearen Ausgleichsgerade, für beide Härtewertkurven
- Abbildung 4.28: Darstellung der gemessenen Fließkurven bis 30 % plastischer Dehnung für AlSi9MgMn-F mit der Endung –a; Die approximierten Kurven nach dem Hocket-Sherby-Model sind mit der Endung –g bezeichnet
- Abbildung 4.29: Temperaturaufzeichnungen der Schmelzetemperaturen an der Rohraußen-fläche und Rohrinnenfläche mittig in axialer Richtung aus dem Druckgussumgussversuch für Schussnummer 12 und 13
- Abbildung 4.30: a) FEM-Modell für die Abkühl- und Auszugsimulation in ABAQUS dargestellt im 34 Schnittmodell und im 2D-Model, b) Schematische Darstellung der theoretischen Berechnungsvorgehensweise zur Abkühl- und Auszugsimulation in ABAQUS
- Abbildung 4.31: a) Darstellung der maximalen Auszugskraft in Abhängigkeit verschiedener Kontaktdefinitionen einer Importberechnung in Abaqus, b) Einfluss des Penalty Scale Faktors auf die maximale Auszugskraft
- Abbildung 4.32: a) Darstellung des Abkühlmodells im 34 -Schnitt für die Ausdruck-simulation, b) Ausdruckmodell im 34 -Schnitt mit Halter und Stempel, c) 2D-Darstellung des Ausdruck-modells, d) Vernetzung und Spalte an den Kontaktflächen zwischen Stahlring und Stempel sowie Aluminium und Halter
- Abbildung 4.33: a) Schematische Darstellung der Funktionsweise von kohäsiven Elementen und kohäsiven Kontaktflächen, b) Schädigungstheorie zur Beschreibung von kohäsiven Elementen und kohäsiven Flächen in Abaqus 6.13 [113]
- Abbildung 4.34: a) Darstellung eines feuerverzinkten Stahlrings nach dem Ausdruckversuch mit geschädigter intermetallischer Phase, b) Kraft- und Stoffschlussbereich im 3D-Ausdruck-modell aufgezeigt am Aluminiumumgussbereich
- Abbildung 4.35: a) Darstellung eines feuerverzinkten Stahlrings nach dem Haftzugversuch mit eingezeichneter geschädigter intermetallischer Phase, b) Darstellung des numerischen Modells zur Abbildung des Haftzugversuchs inkl. Rand-bedingungen und getrenntem Zustand
- Abbildung 4.36: a) Darstellung eines Spannungs-Dehnungs-Diagramms mit der Beschreibung eines Schadenfortschrittes und Verringerung der Elastizität ab Initiierung; Abbildung einer Kurve mit und ohne Schädigung [113], b) Abbildung der fünf verschiedenen Spannungs-zustände mit beispielhaften Probengeometrien für die Ermittlung der Triaxialitäts-zustände η von -0,666 bis + 0,666
- Abbildung 4.37: Proben zur Ermittlung des Verhaltes unter verschiedenen Spannungs-zuständen a) Druckprobe, b) Kerbzug R4, c) Scherzug 0°, d) Scherzug 45°
- Abbildung 4.38: Iterativ ermittelte Kraft-Weg-Kurven in ABAQUS für die Legierung AlSi7Mg0,15-F am Beispiel des Zug- und Kerbzugversuchs sowie der beiden Scherzugversuche bei 0° und 45. Zudem ist der jeweilige Vergleich zwischen der optischen Aramis-Messung (links) und der numerischen Simulation (rechts) dargestellt. Als Skala wird die Vergleichs-dehnung nach von Mises verwendet
- Abbildung 4.39: a) Versuchsaufbau für die Druckprüfung inkl. Darstellung der Druckprobe im Ausgangszustand und nach Ende der Verfahrweges für die AlSi7Mg0,15-Legierung im F- und T7-Zustand; b) Vergleich der numerischen Simulation und des experimentellen Kraft-Weg-Verlaufs im Druckversuch exemplarisch für AlSi7Mg0,15-T7
- Abbildung 4.40: Exemplarische Darstellung der wahren plastischen Dehnung bei Versagen über der Triaxialität η inklusive Triaxialitätsverlauf und Mittelwert bis zum Versagen im kritischen Element für die Legierung AlSi7Mg0,15-F
- Abbildung 4.41: Schematische Darstellung des zeitlichen Verlaufs der Dehnung ε und der Dehnrate ε̇ , verursacht durch primäres (1), sekundäres (2) und tertiäres (3) Kriechen bei metallischen Werkstoffen bis zum Bruch [117]
- Abbildung 4.42: a) Technische Zeichnung der Zeitstandprobe für die Untersuchung des Kriechverhaltens der verwendeten Aluminiumlegierungen, b) Versuchs-aufbau für die Zeitstandversuche
- Abbildung 4.43: Darstellung der Zugfestigkeit (a) und Streckgrenze (b) für die Aluminium-legierung AlSi7Mg0,15 über Temperatur
- Abbildung 4.44: Darstellung der Stufenzeitstandversuche für die Legierung AlSi7Mg0,15-F für a) bei der Temperatur 350 °C und b) bei der Temperatur 400 °C
- Abbildung 4.45: Ermittlung der Dehnrate ε̇ cr für die Stufenzeitstandversuche der Aluminium-legierung AlSi7Mg0,15-F a) bei der Temperatur 350 °C und b) bei der Temperatur 400 °C
- Abbildung 4.46: Parameterermittlung für das Kriechmodel nach Norton für AlSi7Mg0,15-F
- Abbildung 4.47: Vergleich zwischen der numerischen Simulation und den experimentellen Versuchen für die Stufenzeitstandversuche der Aluminiumlegierung AlSi7Mg0,15-F für a) bei der Temperatur 350 °C und b) bei der Temperatur 400 °C
- Abbildung 5.1: a) Darstellung der ermittelten 3-Punkt-Biegefestigkeiten in Abhängigkeit der Zusammensetzung; Zudem die Darstellung der ermittelten Festigkeiten nach Yaokawa [56], b) Darstellung des Bruchzeitpunkts bei der Warmrissprobe und der Randfaserdehnung in der Drei-Punkt-Biege-Prüfung in Abhängigkeit der Salzkernzusammensetzung
- Abbildung 5.2: a) Darstellung der Temperatur bei Bruch und der Zeit bis zum Erreichen der 400 °C Grenze für die untersuchten Legierungen Nr. 2 bis Nr. 7, b) Darstellung der Abkühl-raten für die Salzmischung Nr. 2, Nr. 5, Nr. 6 und Nr. 7 für den Bereich 1: Messpunkt 1 – Liquidus, Bereich 2: Liquidus – Solidus und Solidus – 400 °C
- Abbildung 5.3: Gefüge der DoE5 mittig und im Randbereich mit x300 Vergrößerung
- Abbildung 5.4: Vergleich der Abkühlraten mit der Erstarrungsmorphologie der DoE-Gießserien. Dargestellt sind drei charakteristische Proben mit den minimalen, mittleren sowie maximalen errechneten Abkühlraten.
- Abbildung 5.5: a) Gegenüberstellung der 3-Punkt-Biege-, Zug- und Druckfestigkeiten sowie des E-Moduls der ausgewählten Salzkernlegierung bei Raumtemperatur bis 400 °C, b) Darstellung der gemessenen Dehnung im 3-Punkt-Biegeversuch und Zugversuch in Abhängigkeit der Temperatur
- Abbildung 5.6: Mittlere 3-Punkt-Biegefestigkeit der mechanisch bearbeiteten Salzproben inkl. Standardabweichung und Auflageposition im Biegeversuch. Schematisch sind in der Biegeprobe im Längsquerschnitt der Ursprungsquerschnitt, die Trennebene und der durch Bearbeitung erzeugten Prüfquerschnitt eingezeichnet.
- Abbildung 5.7: Simulationsergebnis aus der Formfüll- und Erstarrungssimulation in Flow3D; dargestellt wird die Temperaturverteilung der Kokille vor dem Gießvorgang bis hin zum Zeitpunkt der Entformung des Biegestäbchens nach 90 s
- Abbildung 5.8: Darstellung des Temperatur-Zeit-Verlaufs für die Schmelzetemperatur in der Kavität und der Wandtemperatur nahe der Kavität für das Experiment und die numerische Berechnung sowie der Festkörperanteil (Solid Fraction) während des Füllvorganges bis 1,8 s Prozesszeit.
- Abbildung 5.9: Vergleich der experimentell und numerisch ermittelten Temperaturkurven; Dargestellt wird der Temperaturverlauf in der Mitte des Salzbiegestäbchens während des Gießprozesses. Als numerisches Materialmodell wird der iterativ bestimmte, finale Datensatz SFQ9V3 zugrunde gelegt.
- Abbildung 5.10: Füllvorgang beim Spiral-Kokillenguss dargestellt in acht Schritten
- Abbildung 5.11: Vergleich der Spirallängen zwischen Experiment und numerischer Simulation. Dargstellt werden der Zentralpunkt, zwei weitere Prozessparameterkombinationen mit Angabe der Gießlängen sowie einer schematischen Darstellung in der Gießspirale.
- Abbildungsqualität von Gussphänomenen in der Biegestab- und Gießspiralkokille
- Abbildung 5.14: Auswertung der Rissentstehung nach Gießtemperatur (links) und Kokillen-temperatur (rechts); Unterteilt werden die Risse in vier Kategorien.
- Abbildung 5.15: Auswertung der Rissentstehung über die Temperaturdifferenz zwischen Kokillentemperatur und Gießtemperatur; Unterteilt werden die entstehenden Risse in vier Kategorien.
- Abbildung 5.16: Darstellung der zwei Extrempunkte der Salzkerngießversuche zur Untersuchung der Warmrissfähigkeit; Worst Case: =720°C und =100°C mit dem höchsten ∆ zwischen Kokille und Schmelze; Best Case: =680°C und =300°C mit dem geringsten ∆ zwischen Kokille und Schmelze
- Abbildung 5.17: Darstellung der ersten Hauptspannung im Verlauf der Abkühlung in der Salzkernwarmrissprobe mit Schwindungsbehinderung für die Variante 1: =720°C/ =100°C und Variante 2: =680°C/ =300°C
- Abbildung 5.18: Verlauf der ersten Hauptspannung in der Randschale der Probenmitte und im Speiserübergangsbereich zur Stabkontur für die Variante 1: =720°C/ =100°C und Variante 2: =680°C/ =300°C
- Abbildung 5.19: Darstellung der ersten Hauptspannung in der Randschale der Probenmitte und im Speiserübergangsbereich zur Stabkontur für die Variante 1: =720°C/ =100°C und Variante 2: =680°C/ =300°C über der Temperatur; Zudem ist die maximal ertragbare Spannung, basierend auf den durchgeführten Zugversuchen im Diagramm, eingezeichnet.
- Abbildung 5.20: Schematische Darstellung der Funktionsweise des angepassten Solvers in Flow3D zur Darstellung der beiden Skalare „Hot Crack“ und „Hot Crack Duration“
- Abbildung 5.21: Darstellung des Hot Crack Criterions und der Hot Crack Duration für den Fall =680°C/ =300°C und =720°C/ =100°C; Abgebildet sind die Ergebnisse bei 15 s, 30 s, 45 s und 60 s Abkühlzeit.
- Abbildung 5.22: Darstellung der charakteristischen Schusskurven inkl. des dazugehörigen Bruchverhaltens der Salzkerne nach dem Druckgussumgussprozess
- Abbildung 5.23: Abbildung der von-Mises-Spannung im Salzkern und Schmelze-geschwindigkeit kurz nach dem Auftreffen der Aluminiumschmelze für die Kolbengeschwindigkeit a) 0,7 s , b) 1,0 s und c) 4,0 s
- Abbildung 5.24: Darstellung der ersten und zweiten Hauptspannung an der Zug- und Druckseite über die Prozesszeit inkl. Markierung der experimentell ermittelten Zug- und Biegefestigkeit für den Belastungfall mit der höchsten Kolbengeschwindigkeit von 4,0 s
- Abbildung 5.25: Abbildung des Kolbendrucks, der ersten drei Hauptspannungen in der Randschale des Salzkerns während des Umgussprozesses am Ende der zweiten Phase mit Übergang zur dritten Phase
- Abbildung 5.26: a) Temperaturverteilung in der Kavität und im Salzkern während der dritten Phase des Druckgussprozesses, b) Druckverteilung in der Kavität und Spannung im Salzkern während der Nachdruckphase
- Abbildung 5.27: Exemplarische Darstellung des Füllvorgangs beim Umguss des Stahleinlegers mit 1,5 mm Wandstärke mit von-Mises-Spannung im Rohr und der Geschwindigkeit der Aluminiumschmelze in der Kavität sowie der Nachdruckphase mit 480 bar und 800 bar Nachdruck
- Abbildung 5.28: Übersicht der verwendeten Stahlrohre (inkl. Wandstärke) und der Ergebnisse der Umgussversuche bei der Kolbengeschwindigkeit 2,8 ms-1 mit und ohne dem Nachdruck; Gegenüberstellung der von-Mises-Spannungen für das 1,5 mm und 2 mm Stahlrohr bei einem Nachdruck von 500 bar sowie für das 2 mm und 2,5 mm Stahlrohr bei einem Nachdruck von 780 bar
- Abbildung 5.29: Gegenüberstellung der ermittelten Maximalspannungen für die unterschiedlichen Stahleinleger, umgossen im Aluminiumdruckguss und geprüft im Ausdruckversuch
- Abbildung 5.30: Gegenüberstellung der gemittelten Energieaufnahme für die unterschiedlichen Stahleinleger, umgossen im Aluminiumdruckguss und geprüft im Ausdruckversuch
- Abbildung 5.31: Betrachtung der a) Maximalspannung und b) Energie der unbeschichteten, profilierten Einleger im Ausdruckversuch, aufgetragen über den taktil gemessenen Rz-Wert
- Abbildung 5.32: REM-Aufnahmen des feuerverzinkten Stahleinlegers, eingelegt bei Raum-temperatur und 680 °C Schmelzetemperatur; Abbgebildet ist der Anguss (Bereich1), die erste Abnahme der stoffschlüssigen Anbindung (Bereich2), das Ende der stoffschlüssigen Anbindung (Bereich3) sowie der Überlauf, der keinerlei stoffschlüssige Anbindung aufweist (Bereich4).
- Abbildung 5.33: Darstellung des Einflusses von Einlegertemperatur und Schmelzetemperatur sowie der T6-Wärmebehandlung auf die Maximalspannung und Ausdrückenergie am Beispiel des feuerverzinkten Einlegers; Die Erhöhung der Schmelzetemperatur ist von 680°C auf 700°C gewählt, die vorgewärmten Einleger sind bei 250 °C gewählt.
- Abbildung 5.34: Darstellung der a) Scherzugfestigkeit und b) Haftzugfestigkeit für ausgewählte Stahl-Aluminiumverbindungen mit stoffschlüssigen Anteilen
- Abbildung 5.35: a) Darstellung eines feuerverzinkten Stahlrings nach dem Haftzugversuch mit eingezeichneter geschädigter intermetallischer Phase, b) Darstellung des numerischen Modells zur Abbildung des Haftzugversuchs inkl. Rand-bedingungen und getrenntem Zustand
- Abbildung 5.36: Darstellung der Auszugberechnung in 20-facher Überhöhung in radialer Richtung mit Darstellung der von-Mises-Spannung
- Abbildung 5.37: a) Gegenüberstellung der Kraft-Weg-Verläufe der Auszugprüfung aus dem Experiment, der rein impliziten Simulation mit Haftreibkoeffizient und der Implizit-Explizit-Import-Simulation mit Berücksichtigung des Wechsels von Haft- auf Gleitreibung, b) Innenradius der rotationssymmetrischen Berechnung und taktilen Vermessung an drei ausgewählten Winkeln in Abhängigkeit der axialen Richtung
- Abbildung 5.38: a) Darstellung der Kontaktspannung in radialer Richtung am Distanzring mit Angabe der Maximalspannung der „direct“ und „penalty“ Kontakt-formulierung aus ABAQUS mit und ohne Kriechmodell, b) Übersicht der Spannungsverteilung in radialer Richtung über das gesamte Bauteil, c) Innenradius nach dem Auszug für die beiden Kontaktformulierungen mit und ohne Kriechmodell
- Abbildung 5.39: a) Spannungen in radialer Richtung nach dem Abkühlvorgang des Ausdruckmodells, b) Spannungszustand im ersten Inkrement der expliziten Import-Ausdruckberechnung, c) Spannungszustand am Ende des Kontaktfindungsschrittes
- Abbildung 5.40: Vergleich zwischen Experiment und numerischer Simulation im Ausdruckversuch, a) Kraft-Weg-Verlauf des 2D Ausdruckverlaufs, b) Kraft-Weg-Verlauf des 3D-Ausdruckversuchs
- Abbildung 5.41: Entstehung der radialen Spannungen 11, dargestellt in einem zylindrischen Koordinatensystem, während des Abkühlvorgangs im 3D-Verbundgussmodell
- Abbildung 5.42: Darstellung der Spannungen 11 in radialer Richtung im zylindrischen Koordinatensystem und der Kontaktspannung im Stahl-Aluminiuminterface mittig, in Umfangsrichtung zu Beginn und am Ende des Trennvorgangs
- Abbildung 5.43: Vergleich der experimentellen und numerischen Kraft-Weg-Kurve im a) Haftzugversuch und b) Scherzugversuch einer feuerverzinkten und mit AlSI10MgMn umgossenen Stahlprobe
- Abbildung 5.44: Gegenüberstellung der numerischen Kraft-Weg-Kurven mit und ohne thermischer Importberechnung für a) den Haftzugversuch und b) den Scherzugversuch
- Abbildung 5.45: Darstellung der Größe CPRESS und CSHEAR für die Simulation mit Abkühlvorgang (oben) und ohne (unten) für den Fall a) nach dem Trennvorgang, am Ende des Kontaktfindungsschrittes und für den Fall b) kurz vor dem Versagen der kohäsiven Schicht
- Abbildung 5.46: a) Darstellung des experimentell ermittelten Rz-Werts und des numerischen statischen Reibkoeffizienten über die experimentell und numerisch ermittelte maximale Ausdruckspannung, b) Gegenüberstellung des experimentellen und numerischen Kraft-Weg-Verlaufs aus dem Ausdruckversuch einer charakteristischen feuerverzinkten Verbundgussprobe
- Abbildung 5.47: Schematische Darstellung der wirkenden Parameter im FEM-Modell einer Stahl-Aluminium-Verbundgussprobe vor und nach der Schädigung der kohäsiven Schicht
- Abbildung 5.48: Vergleich zwischen numerischer Berechnung und Experiment unter Annahme erhöhter Werte für die kohäsive Schicht
- Abbildung 5.49: Schematische Darstellung der Funktionsweise der verwendeten Subroutine zur Abbildung kombinierter stoff- und kraftschlüssiger Stahl-Aluminium-Verbunde mit der ABAQUS Kontaktdefinition
- Abbildung 5.50: Aufbau der Kontaktspannung, dargestellt durch die Größe CPRESS in dem Stahl-Aluminium-Kontakt mit und ohne der Subroutine VUINTER; Der Bereich der Subroutine ist mit einer roten gestrichelten Linie verdeutlicht.
- Abbildung 5.51: a) Vergleich der Kraft-Weg-Kurve von Experiment und der numerischen Berechnung unter Verwendung der Subroutine, b) Darstellung der Größe CSHEAR2 im Zeitschritt vor und nach der Schädigung der Schicht
- Abbildung 6.1: a) Verbundguss-A-Säulenkonzept mit Darstellung der zwei verwendeten Stahlrohre, des Stahlblechs und des Aluminiumumgussbereichs; b) Sandform und Sandkern; c) Gussrohling der Verbundgusssäule mit Angusssystem und Speisern
- Abbildung 6.2: a) Realaufnahmen des Prüfaufbaus zur Umsetzung des A-Säulenersatzlastfalls mit Dateilaufnahmen der Fixierungen 1-3, b) FEM-Modell für den Roof-Crush-Test der Verbundguss-A-Säule inkl. Stempel
- Abbildung 6.3: Vergleich des Kraft-Weg-Verlaufs für den Ersatzlastfall des Dacheindrück-tests zwischen Experiment und numerischer Simulation; Dokumentiert ist der Verlauf aus dem Experiment im Gusszustand und im T7-Zustand sowie der dazugehörige Verlauf aus der numerischen Berechnung mit Schädigungsmodell. Ergänzend sind die Ergebnisse der Seriengeometrie und einer Berechnung ohne Schädigungsmodell eingezeichnet.
- Abbildung 6.4: a) Rohteil des 8-fach-Abgusses und; b) Darstellung der Füllung und Schmelze-geschwindigkeit nach 0,105 sowie der Erstarrung der Salzkernstegkü
7. まとめ、結論、今後の展望(Conclusion):
主要な調査結果の要約 (Summary of key findings):
- 鋳造ソルトコアと鋼-アルミニウム複合材のための実験的および数値的方法の開発
- ソルトコア材料およびプロセスパラメータがコア品質に及ぼす影響の特定
- 鋼-アルミニウム複合材のさまざまな結合メカニズム(力-適合、形状-適合、材料-適合)の特定とモデリング
- ダイカストプロセス中のソルトコアおよび鋼インサートの荷重と破壊挙動の予測
- 実際の適用事例(Aピラー、シリンダー冷却)による研究結果の検証
今後の研究の可能性のある分野 (Possible areas for future expansion research):
- 消失性中子技術のさらなる調査
- 鋳造部品における異種材料間の化学結合をモデリングおよび予測するための改善された方法の開発
- 長期耐久性と性能の調査
8. 参考文献 (References):
9. 著作権 (Copyright):
- この資料は、[著者]による論文「[論文タイトル]」に基づくものです。
- 論文の出典: [DOI URL]
この資料は、上記の論文を紹介するために作成されたものであり、商業目的での無断使用は禁止されています。著作権 © 2025 CASTMAN. 無断複写・転載を禁じます。
Conditions: (条件)
- Do not include any content not specified in the paper. (論文に記載されていない内容は含めないこと。)
- All figures and references must be directly cited in the paper. No translation.(すべての図表と参考文献は、論文中で直接引用すること。翻訳はしないこと。)
- Use technical terms as they are in the original text.(専門用語は原文のまま使用すること。)
- Do not include promotional content.(販促コンテンツは含めないこと。)