この文書は、「Experimental and Theoretical Studies on the Effect of Die Temperature on the Quality of the Products in High-Pressure Die-Casting Process」論文を要約したものです。
1. 概要:
- タイトル: 高圧ダイカストプロセスにおける製品品質に及ぼす金型温度の影響に関する実験的および理論的研究 (Experimental and Theoretical Studies on the Effect of Die Temperature on the Quality of the Products in High-Pressure Die-Casting Process)
- 著者: Mohammad Sadeghi, Jafar Mahmoudi
- 発行年: 2012年
- 発行学術誌/学会: Advances in Materials Science and Engineering
- キーワード:
- 金型温度 (Die temperature)
- 高圧ダイカスト (High-pressure die-casting, HPDC)
- A380合金 (A380 alloy)
- 数値シミュレーション (Numerical simulation)
- 実験的観察 (Experimental observation)
- ProCASTソフトウェア (ProCAST software)
- ラダーフレーム (Ladder frame)
2. 研究背景:
- 社会的/学術的背景:
- 高圧ダイカスト(HPDC)プロセスは、高い寸法精度と生産性で多種多様な製品を製造するために広く使用されています。
- HPDCは、他の方法と比較して生産速度がはるかに速く、表面粗さが低く、寸法精度が高い部品を製造するための経済的かつ効率的な方法です。
- 主要なアルミニウム自動車部品は、この技術で加工できます [1-7]。
- HPDCは他の金属成形プロセスよりも速度が大幅に速いですが、プロセスの複雑さと変数の数により、プロセスの最適化が不可欠です。
- 特に、以下に関連する問題があります。
- 金型温度の制御
- 部品の凝固
- 鋳造品の品質管理
- 一貫性のある統合されたシステムの開発または使用
- ダイカスト製品の機械的特性は、主に以下の要素に関連しています。
- 金型温度
- ゲートでの金属速度
- 印加された鋳造圧力 [4]
- 鋳造部品の完全性は、以下の組み合わせによって影響を受けます。
- 金型温度
- 溶融金属の流動性
- 部品の幾何学的複雑さ
- ダイカスト中の冷却速度
- 運転中の金型の熱プロファイルは、高品質部品の製造におけるもう1つの重要な要素です。
- 金型温度が高すぎると、凝固時間が長くなり、サイクル時間が長くなります。
- 金型が冷たすぎると、表面欠陥が発生する可能性があります [3, 8, 9]。
- 既存研究の限界:
- これらの研究の多くでは、部品の形状が単純であり、産業現場で非常に複雑な部品に関する研究はほとんどありません。
- 研究の必要性:
- 本研究の目的は、シミュレーションを通じて、複雑な自動車部品であるラダーフレームのダイカストプロセスパラメータを最適化することです。
3. 研究目的および研究質問:
- 研究目的:
- 実験的観察および数値シミュレーションを通じて、A380合金の高圧ダイカストにおける金型温度を最適化します。
- 核心研究質問:
- 高圧ダイカストプロセスにおける製品品質に及ぼす金型温度の影響は何ですか?
- この合金に適切な金型温度は何ですか?
- 研究仮説:
- この合金に適切な金型温度は200℃以上であることが示されています。
4. 研究方法論:
- 研究設計:
- 実験的観察と数値シミュレーションの組み合わせ。
- 金型温度および溶融金属温度の実験的測定。
- ProCASTソフトウェアを使用した数値シミュレーション。
- 実験的測定によるシミュレーション結果の検証。
- データ収集方法:
- 実験データ:
- 初期段階と最終充填位置で金型温度を測定しました。
- これらの値の差を計算しました。
- ダイ表面で熱電対およびレーザー高温計(モデルchy 110)で溶融金属温度を測定しました。
- 「150℃、200℃、250℃」の金型温度で実験を実施しました。
- シミュレーションデータ:
- ProCASTソフトウェアを使用して、流体流れと部品凝固段階をシミュレーションしました。
- 合金の材料特性は、ソフトウェアデータベースから抽出して表1に示しました。
- シミュレーションで使用された初期条件と境界条件を表2に示します。
- 実験データ:
- 分析方法:
- 数値シミュレーション:
- ProCASTソフトウェアを使用して、質量保存、運動量保存、およびエネルギー保存(エンタルピー定式化)に関する支配方程式を解きました。
- 自由表面モデリングは、スカラー変数Φを使用して達成しました。
- 結果がメッシュに依存しないことを確認するために、異なる2つのメッシュサイズを使用し、シミュレーション結果を比較しました。
- 実験的検証:
- 結果は実験的測定によって検証されました。
- 数値シミュレーション:
- 研究対象および範囲:
- 材料: A380材料。
- 部品形状: 非常に複雑な形状のラダーフレーム(新しいモーターEF7の部品の1つ)(図1)。
- プロセス: 高圧ダイカスト(HPDC)。
- 金型温度: 「150℃、200℃、250℃」。
- 溶融金属温度: ラダーフレームについて、「680℃」の初期溶融金属温度、「3m/s」のショットスリーブ速度、「55m/s」のゲート溶融速度を仮定しました。
- 機械: IDRA1600ダイカスト機。
5. 主要研究結果:
- 核心研究結果:
- この合金に適切な金型温度は200℃以上であることが示されています。
- 「150℃」の金型温度で、ソフトウェアで予測された最終充填位置でコールドフロー表面欠陥が発生します(図5)。
- 最終凝固位置で収縮欠陥が発生し、これはソフトウェアで予測されたものです(図12)。
- 検証されたモデルは、鋳造品における多孔質欠陥の正確な位置を興味深く示しました。
- 統計的/定性的分析結果:
- 溶融金属温度変化:
- 結果は、金型温度が「150〜250℃」に変化するのに対し、溶融金属温度は「660℃〜680℃」の間で変化することを示しています(図2)。
- 表3は、ショットスリーブの初期注入時の溶融金属温度と、最終充填位置の最終注入時の溶融金属温度を示しています。
- 金型温度「150℃」で、初期注入時の溶融金属温度°Cは「670、669、671」であり、最終注入時の溶融金属温度°Cは「650、649、652」でした。
- 金型温度「200℃」で、初期注入時の溶融金属温度°Cは「675、676、674」であり、最終注入時の溶融金属温度°Cは「664、666、663」でした。
- 金型温度「250℃」で、初期注入時の溶融金属温度°Cは「679、680、679」であり、最終注入時の溶融金属温度°Cは「671、670、668」でした。
- 溶融金属温度の低下:
- 初期および最終工程における「250℃、200℃、150℃での2つの溶融金属温度曲線の差は、それぞれ9.5℃、10℃、19.5℃です」(図3)。
- 欠陥観察:
- 図5は、「150℃」の金型温度で製造された部品におけるコールドフロー表面欠陥の一般的な例を示しています。
- 金属注入中に閉じ込められた空気によって引き起こされるガス気孔が図7に示されています。
- 最終凝固位置で収縮欠陥が発生し、これは図12に示されています。
- 溶融金属温度変化:
- データ解釈:
- 最終注入曲線には、「200℃」の金型温度で分岐点があります。
- 欠陥は、「200℃」未満の金型温度で発生する可能性が高くなります。
- この分岐点を考慮すると、この合金の通常の金型温度は「200℃」であると見なすことができます。
- 最高温度は、特定の部品生産のための金型冷却システムと最適化されたサイクルタイムによって異なります。
- 実験結果とシミュレーション結果を比較すると、部品の欠陥はシミュレーションで予測された位置にあることが示されています。
- Figure Name List:
- FIGURE 1: ラダーフレーム製品の形状。
- FIGURE 2: 金型入口および初期注入時の溶融金属温度対金型温度。
- FIGURE 3: 金型末端および最終注入時の溶融金属温度対金型温度。
- FIGURE 4: 初期および最終注入時のさまざまな金型温度での溶融金属温度の低下。
- FIGURE 5: 最終充填位置でのコールドフロー表面欠陥。
- FIGURE 6: 金型に追加されたオーバーフローの位置。
- FIGURE 7: 一部の多孔質欠陥。
- FIGURE 8: ゲート前面の3つの穴における溶融金属の速度ベクトル。
- FIGURE 9: 溶融金属で満たされたステップと終点を示す。
- FIGURE 10: 同一時間における金型温度(a)150℃および(b)250℃での溶融金属の流れパターン。時間al = b1、a2 = b2、およびa3 = b3。
- FIGURE 11: 鋳造欠陥の影響を受けやすい凝固段階末期のホットスポット。
- FIGURE 12: 最終凝固位置で発生した欠陥。
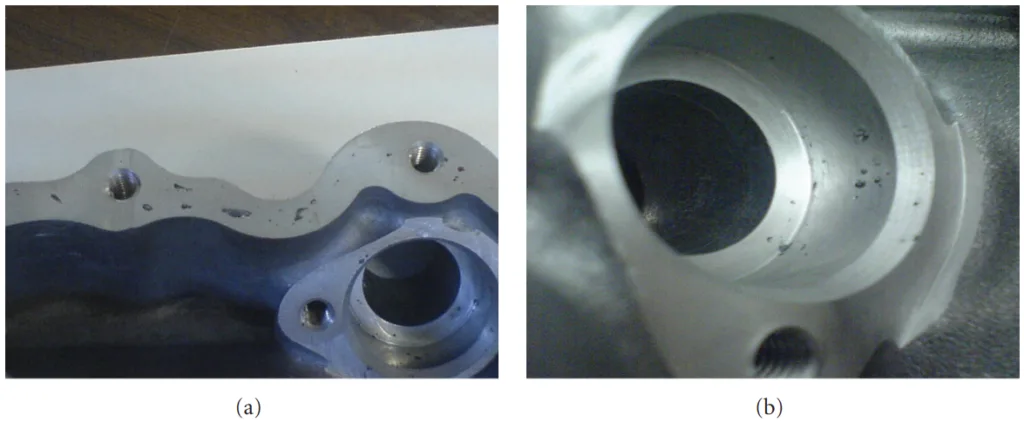
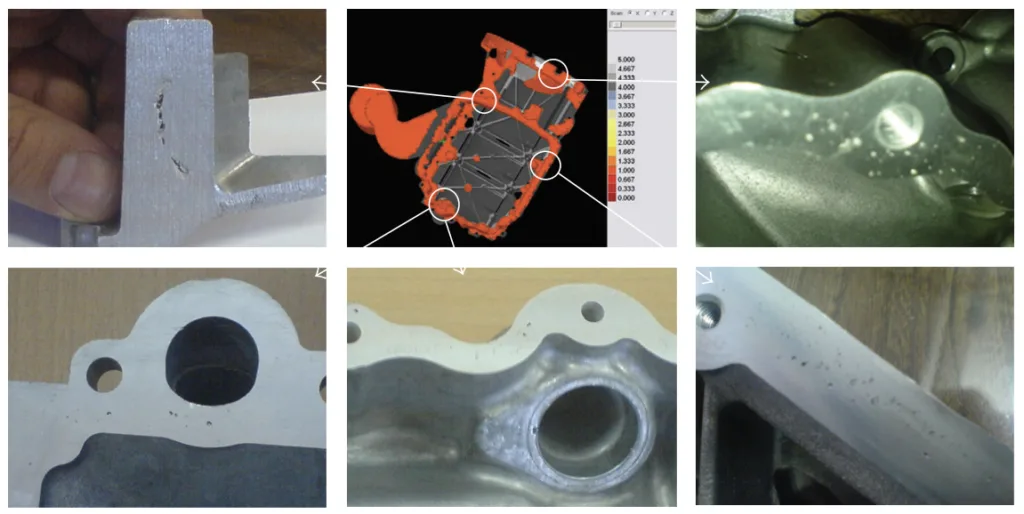
6. 結論および考察:
- 主要結果の要約:
- 実験結果とシミュレーション結果を比較すると、部品の欠陥はシミュレーションで予測された位置にあることが示されています。
- H13金型材料に対するA380合金の最適金型温度は約「200℃」です。
- 金型温度を最適温度範囲から下げると、コールドフロー欠陥および気孔が発生する可能性が高まります。
- シミュレーションによって最適化されたオーバーフローの位置を決定することにより、コールドショットや気孔などの一部の鋳造欠陥を減らすことができました。
- 学術的意義:
- 本研究では、A380合金の高圧ダイカストにおける最適な金型温度を実験的および理論的に決定しました。
- 本研究は、高品質のダイカスト製品を達成するための金型温度制御の重要性を強調しています。
- 数値シミュレーション(ProCASTソフトウェア)の使用は、ダイカストプロセスを最適化し、欠陥位置を予測するための効果的なツールとして検証されています。
- 実務的示唆:
- HPDCでA380合金およびH13金型材料を使用して部品を製造する場合、欠陥を最小限に抑え、製品品質を確保するために、約「200℃」の金型温度を維持することをお勧めします。
- 調査結果は、ダイカスターが、特に200℃未満の金型温度を使用する場合、コールドフロー欠陥や気孔を回避するために金型温度を注意深く制御および監視する必要があることを示唆しています。
- 数値シミュレーションを使用して、ダイ設計とプロセスパラメータを最適化できます。特に、欠陥を軽減するためのオーバーフローの効果的な位置を決定するのに役立ちます。
- 研究の限界:
- 本研究は、特定の合金(A380)と部品形状(ラダーフレーム)に焦点を当てています。
- 最適な金型温度は、合金、金型材料、および部品設計によって異なる場合があります。
- 他のプロセスパラメータや金型冷却システム設計の影響を調査するには、さらなる研究が必要になる場合があります。
7. 今後の研究:
- 今後の研究方向:
- HPDCにおける他のアルミニウム合金および異なる部品形状に対する金型温度の影響を調査するために、さらなる研究が推奨されます。
- 均一な金型温度を維持し、サイクルタイムを改善するための金型冷却システムの最適化を検討することができます。
- さらなる研究では、金型温度と組み合わせて、射出速度や圧力などの他のプロセスパラメータの影響を調査することができます。
- 追加探求が必要な領域:
- 最適な金型温度に対する異なる金型材料の影響の調査。
- 他のタイプの鋳造欠陥を予測および軽減するための高度なシミュレーション技術の探求。
- HPDCにおける金型温度、サイクルタイム、および製品品質の間の最適なバランスを決定するための経済分析の実施。
8. 参考文献:
- [1] M. S. Dargusch, G. Dour, N. Schauer, C. M. Dinnis, and G. Savage, "The influence of pressure during solidification of high pressure die cast aluminium telecommunications components," Journal of Materials Processing Technology, vol. 180, no. 1-3, pp. 37-43, 2006.
- [2] Z. W. Chen and M. Z. Jahedi, "Die erosion and its effect on soldering formation in high pressure die casting of aluminium alloys," Materials and Design, vol. 20, no. 6, pp. 303-309, 1999.
- [3] P. W. Cleary, J. Ha, M. Prakash, and T. Nguyen, "3D SPH flow predictions and validation for high pressure die casting of automotive components," Applied Mathematical Modelling, vol. 30, no. 11, pp. 1406-1427, 2006.
- [4] K. J. Laws, B. Gun, and M. Ferry, "Effect of die-casting parameters on the production of high quality bulk metallic glass samples," Materials Science and Engineering A, vol. 425, no. 1-2, pp. 114-120, 2006.
- [5] D. McBride, T. N. Croft, and M. Cross, "A coupled finite volume method for the computational modelling of mould filling in very complex geometries," Computers & Fluids, vol. 37, no. 2, pp. 170–180, 2008.
- [6] C. C. Tai and J. C. Lin, “The optimal position for the injection gate of a die-casting die," Journal of Materials Processing Technology, vol. 86, no. 1-3, pp. 87–100, 1998.
- [7] S. W. Youn, C. G. Kang, and P. K. Seo, "Thermal fluid/solidification analysis of automobile part by horizontal squeeze casting process and experimental evaluation," Journal of Materials Processing Technology, vol. 146, no. 3, pp. 294-302, 2004.
- [8] J. X. Zhou, L. L. Chen, D. M. Liao, and R. X. Liu, "High pressure diecasting module of InteCAST software and its applications," Journal of Materials Processing Technology, vol. 192-193, pp. 249-254, 2007.
- [9] S. Yue, G. Wang, F. Yin, Y. Wang, and J. Yang, “Application of an integrated CAD/CAE/CAM system for die casting dies," Journal of Materials Processing Technology, vol. 139, no. 1-3, pp. 465-468, 2003.
- [10] A. Kermanpur, S. Mahmoudi, and A. Hajipour, "Numerical simulation of metal flow and solidification in the multi-cavity casting moulds of automotive components," Journal of Materials Processing Technology, vol. 206, no. 1-3, pp. 62-68, 2008.
- [11] S. Schneiderbauer, S. Pirker, C. Chimani, and R. Kretz, "Studies on flow characteristics at high-pressure die-casting," in Proceedings of the 3rd International Conference on Advances in Solidification Processes.
- [12] M. F. V. T. Pereira, M. Williams, and W. B. du Preez, "Reducing non value adding aluminium alloy in production of parts through high pressure die casting," in Proceedings of the Light Metals Conference, 2010.
- [13] J. K. Rai, A. M. Lajimi, and P. Xirouchakis, "An intelligent system for predicting HPDC process variables in interactive environment," Journal of Materials Processing Technology, vol. 203, no. 1-3, pp. 72-79, 2008.
- [14] B. S. Sung and I. S. Kim, "The molding analysis of automobile parts using the die-casting system," Journal of Materials Processing Technology, vol. 201, pp. 635-639, 2008.
- [15] V. Ilotte, "Die casting for chassis components," in Proceedings of the 4th International High Tech Die Casting Conference, Montichiari, Italy, April 2008.
- [16] Z. Brown, C. Barnes, J. Bigelow, and U. S. Contech, "Squeeze cast automotive applications and design considerations," in Proceedings of the 4th International High Tech Die Casting Conference, Montichiari, Italy, April 2008.
- [17] J. P. Papai, Contact heat transfer coefficients in aluminum alloy die casting: an experimental and numerical investigation? [Ph.D. thesis], The Ohio State University, 1994.
9. 著作権:
- 本資料は、Mohammad SadeghiおよびJafar Mahmoudiの論文:「高圧ダイカストプロセスにおける製品品質に及ぼす金型温度の影響に関する実験的および理論的研究」に基づいて作成されました。
- 論文出典: https://doi.org/10.1155/2012/434605
本資料は上記の論文に基づいて要約作成されたものであり、商業目的での無断使用は禁止されています。
Copyright © 2025 CASTMAN. All rights reserved.