本稿は、「NADCA Transactions」に掲載された論文「The coating failure of coated core pin for die casting process」に基づいています。
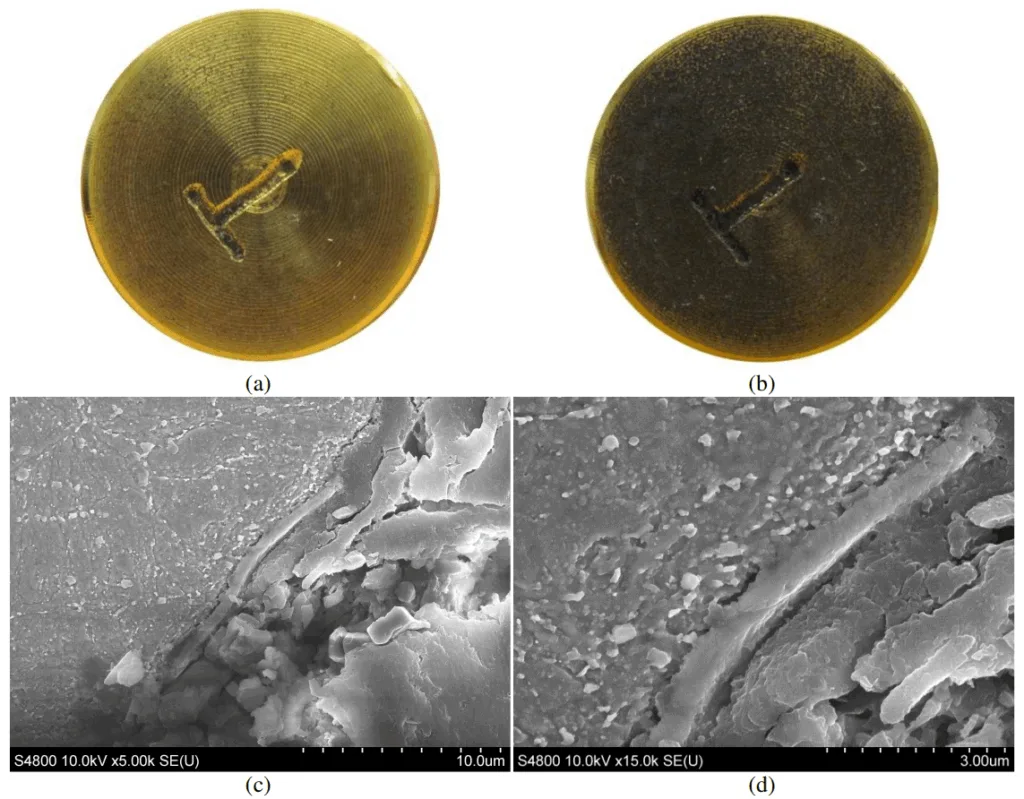
1. 概要:
- タイトル: The coating failure of coated core pin for die casting process
- 著者: J. Song, T. DenOuden, Q. Han
- 発行年: 2012
- 発行学術誌/学会: NADCA Transactions (T12-081)
- キーワード: die soldering, coating failure, mechanism, ultrasonic vibration
2. 抄録:
コアピンのソルダリングは、高圧ダイカストプロセスを用いたアルミニウム鋳物の生産性を制限する問題の一つです。ダイソルダリングを低減するために、通常、コアピンにはセラミックコーティングが施されます。その結果、コーティングの寿命がソルダリングプロセスとコアピンの寿命を左右します。本研究は、ダイカスト条件と同様の条件下におけるコアピン上のコーティングの破損メカニズムを分析するために設計されました。実験を加速するために、コーティングされたコアピンに高強度超音波振動を加えました。コーティングされたコアピンは、様々な温度の水、オイルソルトバス、溶融亜鉛、および溶融A380合金中で一定時間振動させました。試験したコアピンのコーティング破損を特徴付けるために、SEMおよびXRDが使用されました。実験結果は、水、オイル、溶融塩、および溶融亜鉛中の低温で試験されたコーティングの主な破損メカニズムが、鋼マトリックスからのコーティング剥離であることを示しています。溶湯の温度が上昇するにつれて、コーティングの破損は加速します。高温では、溶融亜鉛およびA380合金で試験されたコアピンにおいて、コーティングの断片化および剥離が発生します。コーティング破損箇所における亜鉛またはアルミニウムと鋼との反応は、コーティングの断片化を引き起こし、高温でのコーティング破損を加速させます。
3. 緒言:
高圧ダイカスト(HPDC)は、軽量金属および合金の部品を製造するための最も効率的で費用効果の高い方法です。コアピンのような、質量が小さく表面積対体積比が大きい小さな金型部品は、容易に加熱され、アルミニウムが金型材料(鋼)に「はんだ付け」されてコア上に堆積する状態、一般にソルダリングと呼ばれる状態を引き起こす可能性があります[1-6]。過酷な条件下では、ソルダリングはわずか数回の鋳造サイクル後に発生します[2, 5]。これにより、金型は一般的に高価であり、ダウンタイムは生産損失につながるため、コストが増加します[2]。鋳肌の損傷は、特に耐圧性において製品の品質を低下させます[7]。
高圧ダイカストにおいて、ソルダリングは金型表面の保護膜の「ウォッシュアウト」と密接に関連していることがよく知られています。ウォッシュアウトは、溶融合金が金型上の保護膜を破壊するときに発生します[1-2]。保護膜がないと、溶融合金は金型表面と直接接触する可能性があります。金型材料中の鉄は溶湯に溶解し、溶湯中の材料やその他の元素は金型表面に拡散します[2]。その結果、金型表面に金属間化合物層が形成されます[1, 2-11]。Hanらは、ダイソルダリングは溶融アルミニウム合金と金型表面の鋼との反応によって引き起こされ、反応温度で液体である相が形成されることを見出しました。この液体は、凝固時に金型と鋳物を接合する接着剤として機能し、その結果、金型にソルダリングが発生します[5, 7, 9, 11-12]。ShankarとApelianは、ソルダリングが起こり始めるコアピン上の場所にピラミッド型の金属間化合物層が形成されることを報告しています[6, 8, 10]。我々の以前の論文では、コーティングされたコアピン上のソルダリング形成のメカニズムを提案し[2, 12]、ソルダリング手順を5つのステップで説明しています。ステップ1では、局所的なコーティング破損が発生します。次に、ステップ2では、コーティング破損領域における溶融アルミニウムと鋼マトリックスとの反応によりピットが形成されます。金属間化合物相がピット内に形成されます。ステップ3では、ピットは鋼マトリックスの深部(アルミニウム中の鋼の溶解による)とコーティングの下側の両方に成長し、コーティングの断片化と剥離を引き起こします。ステップ4では、成長する隣接するピットが結合してはるかに大きなピットを形成します。ステップ5では、鋼の局所的な溶解によるアンダーカットが大きくなりすぎるため、鋳肌が著しく損傷するか、鋳型からの鋳物の突き出し中にコアピンが破損します。以前の研究結果に基づくと、ソルダリングプロセスはコーティングの破損と鋼マトリックスと溶融材料との間の反応によって決定されることは明らかです。しかし、局所的なコーティング破損がどのように発生し、熱疲労と溶融金属中の鋼マトリックスの溶解速度がコーティング破損にどのように影響するかは不明です。
4. 研究の概要:
研究テーマの背景:
コアピンのソルダリングは、アルミニウム合金の高圧ダイカスト(HPDC)における生産性とコアピン寿命を制限する重要な問題です。セラミックコーティングはソルダリングを軽減するために適用され、コーティング寿命が重要な要素となります。これらのコーティングの破損メカニズムを理解することは、ダイカスト作業を改善するために不可欠です。
従来の研究状況:
これまでの研究により、ソルダリングは保護膜のウォッシュアウトと金属間化合物層の形成に関連していることが確立されています[1-11]。Hanらは、溶融アルミニウムと鋼との反応がソルダリングの原因であることを特定しました[5, 7, 9, 11-12]。ShankarとApelianは、初期のソルダリング箇所の形態を記述しました[6, 8, 10]。著者らの以前の研究[2, 12]では、局所的なコーティング破損から始まる、コーティングされたコアピン上の多段階ソルダリングメカニズムが詳述されています。ソルダリングプロセスは、コーティングの破損と鋼と溶融金属の反応によって支配されることが知られていました。
研究の目的:
本研究は、1) 鋼マトリックスの微細構造変化を引き起こす加熱効果、2) セラミックコーティングと鋼ピン間の結合を弱める可能性のある温度効果、および3) 溶融材料と鋼との間の化学反応の効果の結果としての、コーティングされたコアピンのコーティング破損を理解することに焦点を当てました。コーティングプロセス中に発生するセラミックコーティングの欠陥は、本研究では考慮されていません。コーティングされたコアピンの寿命は、最近開発された加速試験法[9]を用いて評価されました。
核心研究:
本研究では、様々な熱処理(270°C、450°C、700°C)を受けたH-13鋼の微細構造変化を調査しました。TiNおよびLumenaコーティングされたH-13コアピンの寿命を評価するために、高強度超音波振動を用いた加速試験法が採用されました。これらのピンは、水(室温)、オイル(270°C)、溶融塩(700°C)、溶融亜鉛(450°Cおよび700°C)、および溶融A380アルミニウム合金(700°C)の様々な媒体で試験されました。本研究では、コーティング破損メカニズム、溶融金属中のH-13鋼の溶解速度、および温度と化学反応の影響を分析しました。特性評価にはSEMおよびXRDが使用されました。
5. 研究方法論
研究設計:
本研究は、熱サイクルによるH-13鋼の微細構造変化を調査し、模擬ダイカスト条件下でのコーティング破損メカニズムを評価するように設計されました。これには以下が含まれます。
- 異なる温度での微細構造変化を研究するためのH-13鋼サンプルの熱処理。
- コーティング寿命と破損モードを評価するための、様々な液体媒体中の異なる温度での超音波振動を用いたコーティング(TiNおよびLumena)H-13コアピンの加速試験。
- 反応性溶融金属(亜鉛およびA380合金)中のH-13鋼の溶解速度の測定。
データ収集及び分析方法:
- H-13鋼の微細構造変化: H-13試験片を270°C、450°C、および700°Cで20時間熱処理した後、水焼入れしました。硬度(HRCスケール)を測定しました。微細構造は、エネルギー分散型X線分光法(EDS)を備えた走査型電子顕微鏡(SEM)を用いて調べました。分析には、相図(ThermoCalcTMを用いて計算し、ASMハンドブック[13]から引用)を使用しました。
- 加速コーティング破損試験: コーティングされたコアピンを、以下の条件下で高強度超音波振動にかけました。
- 水(室温)およびオイル(270°C)中で15分間(TiNコーティング)。
- 溶融NaCl+KCl塩(700°C)中で120秒間(TiNコーティング)。
- 溶融亜鉛(450°Cおよび700°C)および溶融A380アルミニウム合金(700°C)中で、段階的な暴露時間で(Lumenaコーティング)。
- 溶解速度測定: 溶融亜鉛およびA380での試験では、試験片を特定の時間間隔で取り出し、NaOH溶液で洗浄し、重量変化を測定して溶解速度を計算しました。
- 特性評価: コーティング破損およびソルダリング形態は、EDSを備えたSEMを用いて調べました。X線回折(XRD)は、溶融亜鉛との反応中に形成された金属間化合物を特定するために使用しました。
研究テーマ及び範囲:
- ダイカストに関連する温度(270°C、450°C、700°C)におけるH-13工具鋼の微細構造変化と、相変態(例:オーステナイト形成とそれに続くマルテンサイト変態)によるコーティング接着性への潜在的な影響。
- 熱的および機械的影響を分離するための、非反応性媒体(水、オイル、溶融塩)におけるTiNコーティングの破損に対する温度の影響。
- 溶融亜鉛および溶融A380合金におけるLumenaコーティングの破損およびH-13鋼のソルダリングに対する温度と化学反応の複合効果。
- 異なる温度での溶融亜鉛およびA380合金中のH-13鋼の溶解速度の決定。
- コーティング剥離、断片化、結合強度の役割などの破損メカニズムの特定。
6. 主要な結果:
主要な結果:
- H-13鋼の微細構造変化:
- H-13鋼は700°Cで著しい微細構造変化を起こし、部分的にオーステナイトに変態し、その後保持するとフェライトと炭化物に変態するか、冷却するとマルテンサイトに戻ります。この変態には約4%の体積変化が伴い、コーティングに応力を与える可能性があります。
- H-13鋼の硬度は700°Cでの熱処理後に著しく低下し(約45 HRCから22.7 HRCへ)、これは実質的な微細構造変化を示しています。270°Cおよび450°Cではほとんど変化は見られませんでした。
- 非反応性媒体におけるコーティング性能(TiNコーティング):
- 低温(室温の水、270°Cのオイル)では、TiNコーティングは15分間の超音波振動後も良好に付着していました。
- 700°Cの溶融塩中では、TiNコーティングは60秒後に部分的な破損を示し、2分後にはほぼ完全に剥離しました。これは、化学反応がなくても温度がコーティングの破損を著しく加速することを示しています。
- 反応性媒体におけるコーティング性能(Lumenaコーティング):
- 450°Cの溶融亜鉛中では、Lumenaコーティングは20秒間の超音波振動後に亀裂と剥離を示しましたが、H-13鋼の著しいソルダリングは観察されませんでした。450°Cの亜鉛中でのH-13の溶解速度はほぼゼロでした。
- 700°Cの溶融亜鉛中では、Lumenaコーティングは急速に破損しました(5秒後に斑点、10秒後に約90%が破損、15秒までに完全に破損)。H-13鋼の激しい反応とソルダリングが発生しました。700°Cの亜鉛中でのH-13の溶解速度は高かった(1.395 mm/min)。金属間化合物相FeZn13およびFe3Zn10(主)が形成されました。
- 700°CでのH-13と溶融亜鉛との間の反応層の厚さは約10~20ミクロンであり、A380合金(<1.5ミクロン)よりもはるかに厚かった。
- 700°CでのA380合金中のH-13の溶解速度は0.585 mm/minでした。
- 破損メカニズム:
- 鋼マトリックスからのコーティング剥離は、低温での主な破損メカニズムです。
- 高温では、コーティングの断片化と剥離の両方が発生します。
- コーティング破損箇所での亜鉛/アルミニウムと鋼との反応は、さらなるコーティングの断片化と破損を加速します。
- H-13マトリックスが溶融材料と反応しない場合(例:450°Cの亜鉛)でもコーティング破損が発生する可能性があり、これは高温での結合強度の低下が破損に寄与することを示唆しています。
- H-13の相変態応力と高温でのコーティングとマトリックスの結合強度低下の組み合わせは、コーティングの寿命を劇的に短縮します。
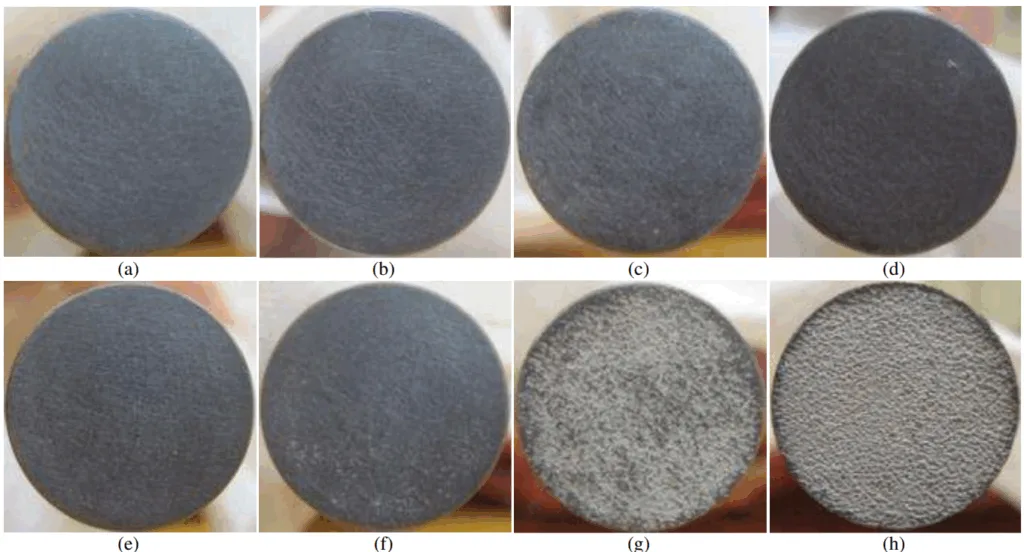
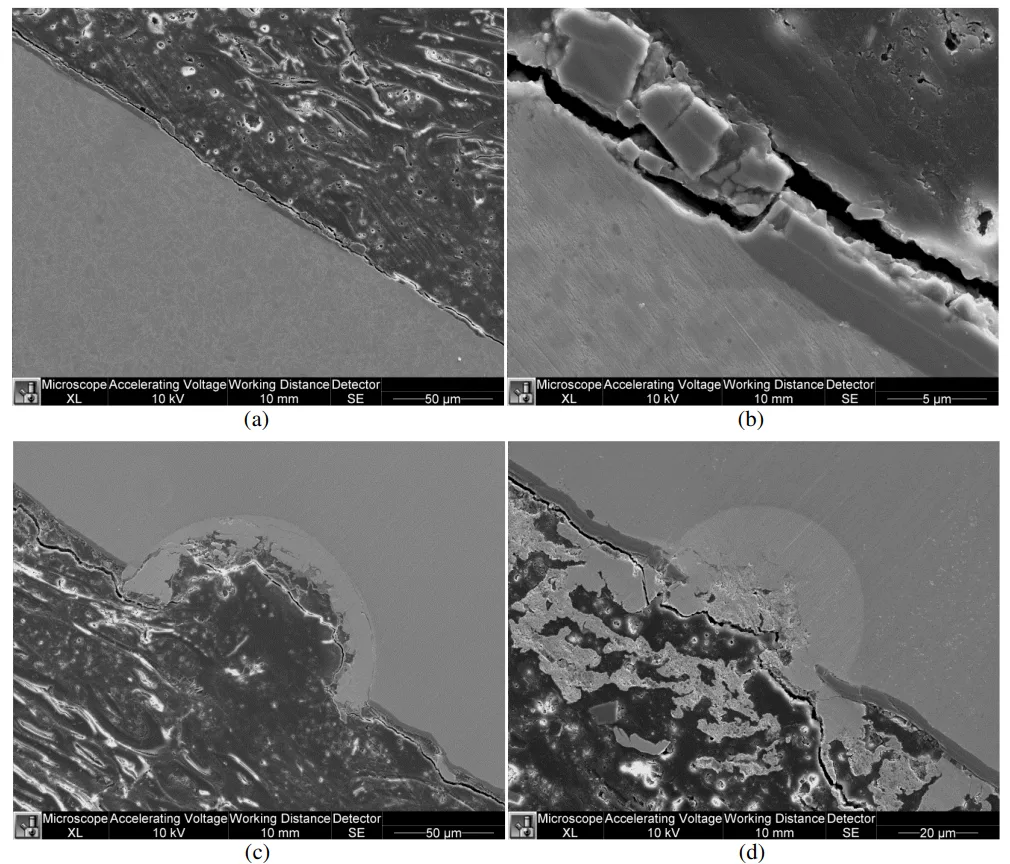
図の名称リスト:
- Figure 1: The test bars used for accelerated soldering testing. The core pins with 128 mm long by 18mm in diameter were coated with a layer of Lumena (left), and TiN (right).
- Figure 2: Phase diagram (a) and Isothermal transformation diagram (b) of the H-13 tool steel.
- Figure 3: Microstructure of the H-13 bar at different heat treatment temperatures. a) room temperature with 1000X; b) 700 degree C with 1000X; c) room temperature; d) 270 degree C; e) 450 degree C and f) 700 degree C. c-f) are in 5000X
- Figure 4: The hardness data of the H-13 matrix at different heat treatment temperatures.
- Figure 5: Accelerated test results on H-13 at 270 degree C oil after 15 minutes tested (a) and at 700 degree C molten salt after 2 minutes ultrasonic vibration (b) with the TiN coating Coating; SEM morphologies at 700 degree C molten salt (c and d).
- Figure 6: Accelerated test results on H-13 in 450 degree C zinc molten (a-d) and in 700 degree C zinc molten (e-h) with the Lumena coating at a) and e) 0 seconds, b) and f) 5 seconds, c) and g) 10 seconds, and d) and h) 15 seconds;
- Figure 7: The XRD pattern of the H-13 bar under the ultrasonic vibration in 700 degree C zinc molten (a); the zinc iron phase diagram (b).
- Figure 8: SEM graphs of the H-13 bar under ultrasonic vibration with Lumena coating in zinc molten. (a-b) 450 degree C (20 seconds) and (c-d) 700 degree C (5 seconds).
- Figure 9: The dissolution depth verses ultrasonic vibration applied time of zinc and A380 molten alloy.
7. 結論:
700°CにおけるH-13マトリックスの微細構造変化は、熱膨張係数を超える追加の4%の変形をもたらす可能性があり、これはコーティングに応力を与える可能性があります。本研究は、マトリックスの微細構造が大きく変化せず、溶融材料と反応しない450°Cでもコーティング破損が発生することを示しました。これらの結果は、マトリックスの微細構造が大きく変化しなくてもコーティングが破損する可能性があることを示しています。コーティングとマトリックス間の結合強度が温度上昇とともに低下することが、この結果のもう一つの説明となり得ます。高温では、相変態によってもたらされる応力またはひずみと、低下した結合強度が組み合わさって、コーティングの寿命を劇的に低下させます。
ソルダリングは初期のコーティング破損の直後に発生するため、溶解速度はソルダリング速度を反映する可能性があります。試験温度は溶解速度に大きく影響し、亜鉛合金では450°Cでほぼゼロから700°Cで1.395mm/minに変化しました。反応速度と溶融材料の溶解度が溶解速度を決定する可能性があります。450°Cでの最大溶解度(ほぼゼロ)は、鉄が溶融材料に溶解するのを制限しました。H-13マトリックスと溶融材料との間の遅い反応速度もソルダリングプロセスを決定し、これは溶解速度によって予測できます。亜鉛中の溶解速度はA380合金の2倍以上であり、ソルダリングプロセスもA380よりも亜鉛の方が速いです。
8. 参考文献:
- [1] Chu, Y., Cheng, P., Shivpuri, R., "A Study of Erosive Wear in Die Casting Dies: Surface Treatments and Coatings," NADCA Transactions 1993.
- [2] Song, J., DenOuden, T., and Han, Q., "Soldering analysis of core pin", NADCA Transactions 2011
- [3] Tentardini, E. K., Kunrath, A. O., Aguzzoli, C., Castro, M. J., Moore, J., Baumvol, I. J. R., Soldering mechanisms in materials and coatings for aluminum die casting, Surface & Coatings Technology, vol 202, No 16 (2008) .
- [4] Chen, Z. W., Jahedi, M. Z., Mechanisms of die failure caused by die/casting soldering during high pressure die casting of aluminium alloys, vol 20, No 6 (2001)
- [5] Han, Q., Viswanathan, S., Analysis of the mechanism of die soldering in aluminum die casting, Metallurgical and Materials Transactions a-Physical Metallurgy and Materials Science, vol 34, No 1 (2003).
- [6] Shankar, S., Apelian, D., Metallurgical and Material Die soldering: Mechanism of the interface reaction between molten aluminum alloy and tool steel, Transactions B-Process Metallurgy and Materials Processing Science, vol 33, No 3 (2002).
- [7] Han, Q., and Jian, X., "Ultrasound Assisted Die Casting Process," NADCA Transactions 2009,.
- [8] Shankar, S., Apelian, D., Die soldering: Effect of process parameters and alloy characteristics on soldering in the pressure die casting process, International Journal of Cast Metals Research, vol 15, No 2 (2002).
- [9] Han, Q., Xu, H., Ried, P. P., Olson, P., Accelerated method for testing soldering tendency of core pins, International Journal of Cast Metals Research, vol 23, No 5 (2010)
- [10] Shankar, S., Apelian, D., Mechanism and preventive measures for die soldering during Al casting in a ferrous mold, Jom-Journal of the Minerals Metals & Materials Society, vol 54, No 8 (2002)
- [11] Han, Q., Kenik, E. A., Viswanathan, S., "Die soldering in aluminum die casting", Light Metals: Proceedings of Sessions, TMS Annual Meeting, pp 765-770, (2000)
- [12] Song, J., DenOuden, T., and Han, Q., “Mechanisms of soldering formation on coated core pin", Materials and metallurgical transactions A. vol 43 pp415-421 (2012)
9. 著作権:
- 本資料は、「J. Song, T. DenOuden, Q. Han」による論文です。「The coating failure of coated core pin for die casting process」に基づいています。
- 論文の出典: [提供された文書にDOI URLなし]
本資料は上記論文に基づいて要約したものであり、商業目的での無断使用を禁じます。
Copyright © 2025 CASTMAN. All rights reserved.