この資料は、[Hanxue Cao, Qiang Zhang, Weikai Zhu, Sheng Cui, Qin Yang, Zhibai Wang, Bin Jiang]の論文:[Study on the Influence of Injection Velocity on the Evolution of Hole Defects in Die-Cast Aluminum Alloy] に基づいています。
1. 概要:
- タイトル: ダイカストアルミニウム合金における穴欠陥の進化に対する射出速度の影響に関する研究 (Study on the Influence of Injection Velocity on the Evolution of Hole Defects in Die-Cast Aluminum Alloy)
- 著者: Hanxue Cao, Qiang Zhang, Weikai Zhu, Sheng Cui, Qin Yang, Zhibai Wang, Bin Jiang
- 出版年: 2024年
- 出版ジャーナル/学会: Materials (MDPI)
- キーワード: アルミニウム合金ダイカスト (aluminum alloy die-casting); 可視化 (visualization); 射出速度 (injection rate); 穴欠陥 (hole defects)
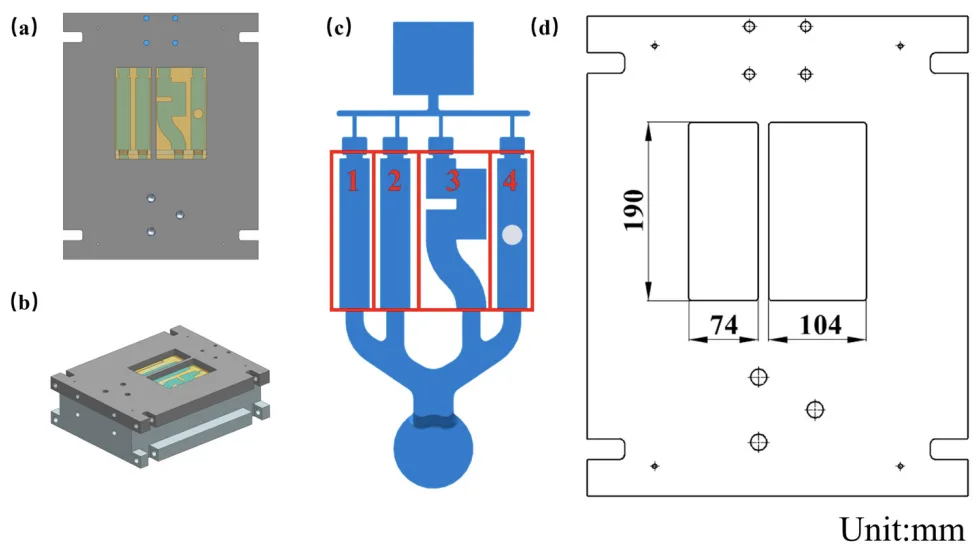
2. 研究背景:
- 研究テーマの社会的/学術的背景: アルミニウム合金ダイカストは、その効率性と寸法精度により、産業界全体で急速に発展し、広く使用されている技術です。しかし、気孔欠陥、すなわち穴欠陥は、ダイカストで一般的に見られる課題であり、部品の機械的特性および加工特性に悪影響を及ぼします。これらの欠陥を理解し、軽減することは、ダイカスト製品の品質と信頼性を向上させるために非常に重要です。
- 既存研究の限界: 既存の研究では、プロセスパラメータと金型構造が気孔に及ぼす影響を調査してきましたが、高圧ダイカスト中の金型キャビティ内の溶融金属の流れ挙動を直接観察し、特性評価することには限界がありました。水シミュレーションや数値シミュレーションなどの既存の方法は、液体金属の流れの複雑なダイナミクスと欠陥形成を正確に表現するには限界があります。
- 研究の必要性: 穴欠陥を効果的に低減または排除するためには、ダイカストプロセス中のガス挙動に関するより深い理解が不可欠です。本研究は、一般的な合金であるADC12アルミニウム合金のダイカストプロセス中に、射出速度が合金の流れパターンとガス誘起欠陥に及ぼす影響をリアルタイムで直接観察および分析する方法の必要性に対処します。
3. 研究目的と研究課題:
- 研究目的: 本研究の主な目的は、充填プロセスを直接可視化することにより、ダイカストアルミニウム合金における穴欠陥の形成と進化に対するさまざまな射出速度の影響を調査することです。
- 主要な研究課題:
- ダイカスト中の射出速度の変化は、溶融アルミニウム合金の流れパターンにどのような影響を与えるか?
- 射出速度とガス誘起穴欠陥の形成および進化の間にはどのような関係があるか?
- さまざまな射出速度での穴欠陥の形成に寄与するメカニズムは何か?
- 研究仮説: 本研究では、射出速度を上げると、溶融金属の流れパターンが変化し、空気の巻き込みが増加し、その結果、ダイカストアルミニウム合金部品において、より高い気孔率とより大きな穴欠陥が発生するという仮説を立てました。
4. 研究方法
- 研究デザイン: 本研究では、水平コールドチャンバーダイカストマシン(DCC630M)に取り付けられたガラス窓を備えた特別に設計された金型を使用した革新的な動的可視化実験を採用しました。この設定により、アルミニウム合金の充填プロセスを直接観察できます。
- データ収集方法: 高速カメラ(1000フレーム/秒、1024×1024解像度)を使用して、さまざまな射出速度(1.0 m/sおよび1.5 m/s)でのダイカスト中の溶融金属の流れを記録しました。鋳造サンプルを作成し、静水圧法と密度バランス(MH-110E)を使用して気孔率を定量化しました。
- 分析方法: 記録されたビデオを分析して、流れパターンと欠陥形成の動的な進化を特性評価しました。 Image-Pro Plusソフトウェアを使用して、鋳造サンプルの断面における穴欠陥を測定および分析しました。 Anycastingソフトウェアを使用した数値シミュレーションを実施し、実験的観察結果と比較しました。
- 研究対象と範囲: 本研究は、ADC12アルミニウム合金ダイカストに焦点を当てています。この研究では、ザグリ穴、段付きボス、弓形、および貫通穴構造の4つの一般的なキャビティ構造を持つ金型における穴欠陥形成に対する2つの異なる射出速度(1.0 m/sおよび1.5 m/s)の影響を調査します。気孔率分析のために、これらのキャビティ構造内の4つの位置(S1、S2、S3、S4)からサンプルを採取しました。
5. 主な研究成果:
- 主な研究成果:
- 射出速度を1.0 m/sから1.5 m/sに増加させると、平均気孔率が7.49%から9.57%に増加しました。これは、射出速度が速くなるにつれて、気孔の数とサイズの両方が大幅に増加したことを示しています。
- 可視化とシミュレーションにより、1.5 m/sの射出速度では、流れの先端が1.0 m/sと比較して、より顕著な破断と飛沫を示しました。
- 流れの先端での破断飛沫の程度は、射出速度が高いほど深刻であり、これは壁付着ジェット効果によるものと分析されました。
- 射出速度の増加は、液体破壊によって形成されるマイクログループの体積の減少につながり、空気の巻き込みとキャビティ欠陥が増加しました。
- 統計的/定性的分析結果: 定量的な気孔率測定により、射出速度が高いほど気孔率が統計的に有意に増加することが確認されました。定性的な可視化ビデオ分析により、より高い射出速度で明確な流れパターンと増加した乱流および飛沫が明らかになりました。
- データ解釈: より高い射出速度での気孔率の増加は、強化された壁付着ジェット効果と流れの先端の破断に起因すると考えられます。この現象により、後続の液体金属が初期の流れと融合することが困難になり、空気が閉じ込められ、キャビティ欠陥につながります。
- 図のリスト名:
- 図5. さまざまな射出速度での流れ特性 (Flow characteristics at different velocities of injection)
- 図6. さまざまな速度での充填流れのシミュレーション結果 (Simulation results of filling flow at different speeds)
- 図7. 内部ゲート厚さ3.0 mmおよび射出速度1.0 m/sの試験片の断面形態 (Cross-sectional morphology of specimens with an inner gate thickness of 3.0 mm and an injection velocity of 1.0 m/s)
- 図8. 内部ゲート厚さ3.0 mmおよび射出速度1.5 m/sの試験片の断面形態 (Cross-sectional morphology of specimens with an inner gate thickness of 3.0 mm and an injection velocity of 1.5 m/s)
- 図9. 3.0 mm内部ゲートにおけるさまざまな射出速度での気孔率 (Porosity at different injection velocities at a 3.0 mm inner gate)
- 図10. 射出速度1.0 m/sでのS2位置における液体金属の流れパターン (Flow pattern of liquid metal at S2 position at injection velocity of 1.0 m/s)
- 図11. 射出速度1.5 m/sでのS2位置における液体金属の流れパターン (Flow pattern of liquid metal at S2 position at injection velocity of 1.5 m/s)
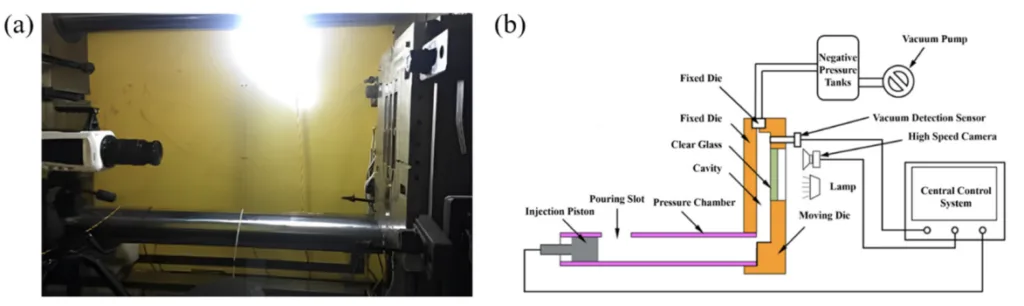
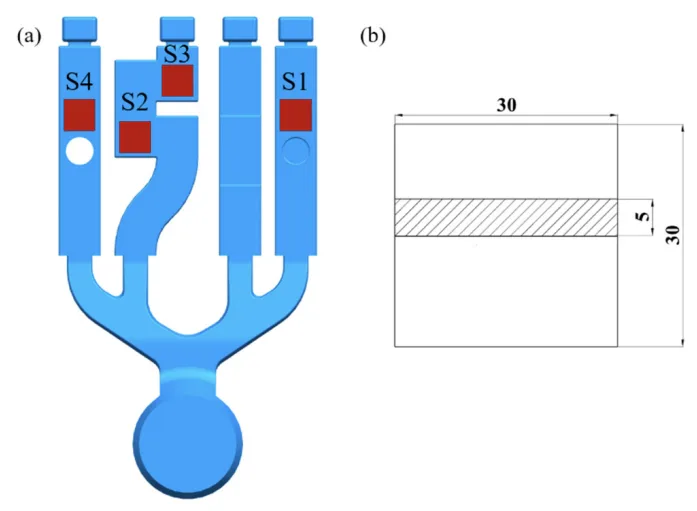
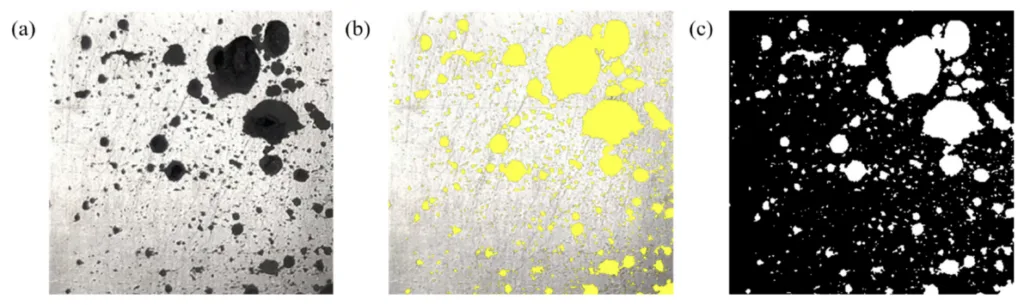
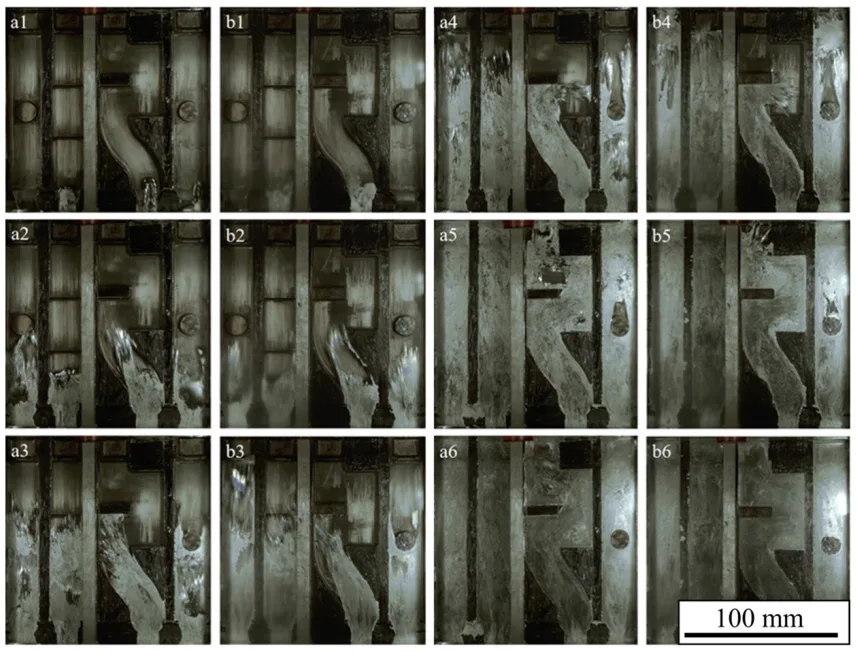
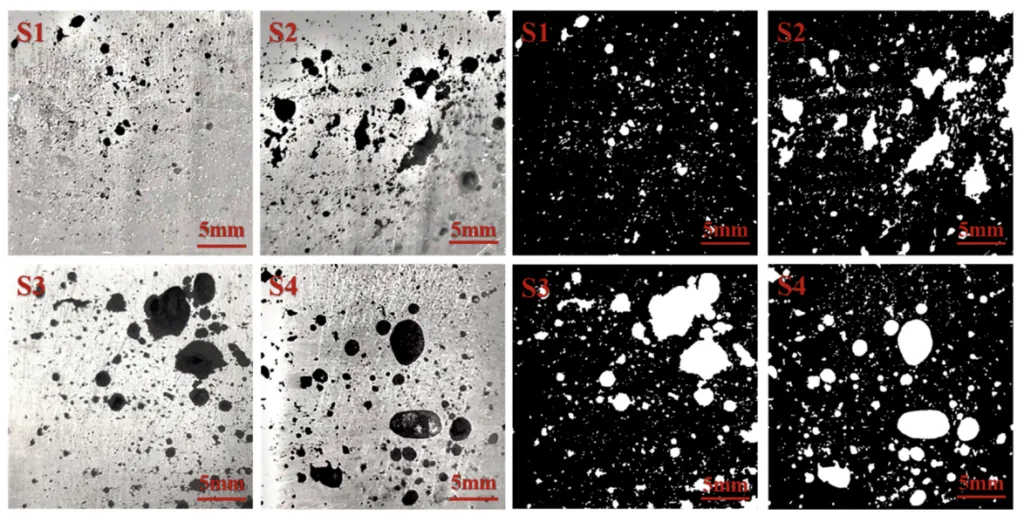
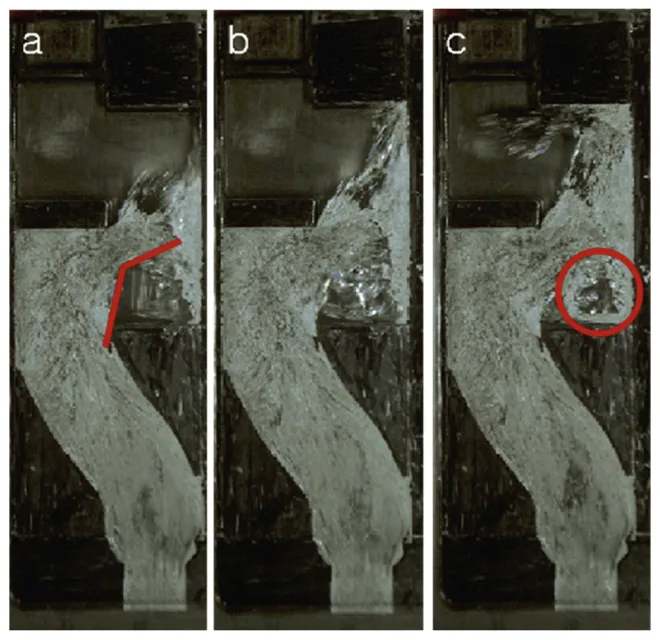
6. 結論と考察:
- 主な結果の要約: 本研究では、アルミニウム合金ダイカストにおいて射出速度を上げると、気孔率と穴欠陥が大幅に増加することが実証されました。これは主に、より高い射出速度によって引き起こされる、強化された流れの先端の破断、壁付着ジェット効果、および空気の巻き込みの増加によるものです。
- 研究の学術的意義: 革新的な動的可視化法は、ダイカストにおける溶融金属の流れ挙動と欠陥形成を直接観察し、理解するための貴重なツールを提供します。この研究結果は、ガス誘起欠陥のメカニズムと射出速度の影響に関するより深い理解に貢献します。
- 実用的な意義: 本研究は、気孔率を最小限に抑えるための金型設計に関する実用的な対策を示唆しています。
- 流れの方向を変え、壁ジェット効果を低減するために、広い平面を避けてください。
- 広い平面が必要な場合は、表面に小さな突起または窪みを追加して、下部溶融金属の安定した流れを妨げ、金型壁に付着した溶融金属の統合を促進します。
- 金型内に流れ誘導板またはチューブを組み込んで、流体の流れ方向を変更し、壁の近くでより均一な流れパターンを可能にします。
- 金型設計時に流体流れ特性を考慮して、流線形または曲線形状を選択し、壁の近くでの流体よどみと不均一な流れを最小限に抑えます。
- 研究の限界: 本研究は、主に射出速度の影響に焦点を当てました。論文では、温度分布などの要因も流れや気孔形成に重要な役割を果たしますが、本研究の主な焦点ではなかったことを認めています。
7. 今後のフォローアップ研究:
- 今後のフォローアップ研究の方向性: 今後の研究では、温度分布がダイカストにおける溶融金属の流れと気孔形成に及ぼす影響を調査する必要があります。
- さらなる探求が必要な分野: シミュレーションの精度を高めて、流れ挙動と欠陥形成を予測するために、数値シミュレーションの境界条件を最適化し、より現実的な物理モデルを開発するための追加調査が必要です。潜在的に温度効果を組み込む必要があります。
8. 参考文献:
- [1] Wang, G.G.; Weiler, J.P. Recent developments in high-pressure die-cast magnesium alloys for automotive and future applications. J. Magnes. Alloys 2023, 11, 78–87.
- [2] Yang, Y.-T.; Qiu, Z.-Y.; Zheng, Z.; Pu, L.-X.; Chen, D.-D.; Zheng, J.; Zhang, R.-J.; Zhang, B.; Huang, S.-Y. Al-enabled properties distribution prediction for high-pressure die casting Al-Si alloy. Adv. Manuf. 2024, 12, 591-602.
- [3] Cleary, P.; Ha, J.; Alguine, V.; Nguyen, T. Flow modelling in casting processes. Appl. Math. Model. 2002, 26, 171-190.
- [4] Kang, H.J.; Yoon, P.H.; Lee, G.H.; Park, J.Y.; Jung, B.J.; Lee, J.Y.; Lee, C.U.; Kim, E.S.; Choi, Y.S. Evaluation of the gas porosity and mechanical properties of vacuum assisted pore-free die-cast Al-Si-Cu alloy. Vacuum 2021, 184, 109917.
- [5] Hu, Q.; Guo, W.; Xiao, P.; Zhao, H. Effects of Fast Shot Speed and Wall Thickness on the Microstructures and Mechanical Properties of the High Pressure Die-casting 6061-SiC Composites. Metall. Mater. Trans. B-Process Metall. Mater. Process. Sci. 2021, 52, 2283–2293.
- [6] Ma, Y.-H.; Yu, W.-B.; Zhou, Y.-Q.; Xiong, S.-M. Influence of different high pressure die casting processes on 3D porosity distribution of Mg-3.0Nd-0.3Zn-0.6Zr alloy. China Foundry 2021, 18, 521–528.
- [7] Majerník, J.; Gašpár, S.; Husár, J.; Paško, J.; Kolínský, J. Research and Evaluation of the Influence of the Construction of the Gate and the Influence of the Piston Velocity on the Distribution of Gases into the Volume of the Casting. Materals 2021, 14, 2264.
- [8] Ibrahim, M.D.; Mohamad, M.R.; Roslan, L.; Sunami, Y.; Lam, S.S. High Pressure Die Casting Porosity Defect Analysis and Experimental Validation for Power Steering Columns and DVVTs. In Lecture Notes in Mechanical Engineering; Springer: Singapore, 2018; pp. 187–196.
- [9] Gautam, S.K.; Roy, H.; Lohar, A.K.; Samanta, S.K. Studies on Mold Filling Behavior of Al-10.5Si-1.7Cu Al Alloy during Rheo Pressure Die Casting System. Int. J. Met. 2023, 17, 2868–2877.
- [10] Haghniaz, F.; Delbergue, D.; Côté, R.; Demers, V. Mold filling behaviour of LPIM feedstocks using numerical simulations and real-scale injections. Powder Metall. 2023, 66, 436-449.
- [11] Hu, M.Y.; Cai, J.J.; Li, N.; Yu, H.L.; Zhang, Y.; Sun, B.; Sun, W.L. Flow Modeling in High-Pressure Die-Casting Processes Using SPH Model. Int. J. Met. 2018, 12, 97-105.
- [12] Ren, M.; Gu, J.; Li, Z.; Ruan, S.; Shen, C. Simulation of Polymer Melt Injection Molding Filling Flow Based on an Improved SPH Method with Modified Low-Dissipation Riemann Solver. Macromol. Theory Simul. 2022, 31, 2100029.
- [13] Niu, X.F.; Zhao, J.Y.; Wang, B.J. Application of smooth particle hydrodynamics (SPH) method in gravity casting shrinkage cavity prediction. Comput. Part. Mech. 2019, 6, 803–810.
- [14] Zarbini Seydani, M.; Krimi, A.; Bedel, M.; Khelladi, S.; El Mansori, M. A 2D filling and solidification benchmark test: Validating smoothed particle hydrodynamics (SPH) simulations for sand gravity casting. Int. J. Adv. Manuf. Technol. 2023, 128, 801–821.
- [15] Saeedipour, M.; Schneiderbauer, S.; Pirker, S.; Bozorgi, S. A Numerical and Experimental Study of Flow Behavior in High Pressure Die Casting. In Magnesium Technology, Proceedings of the 2014—TMS 2014 143rd Annual Meeting and Exhibition, San Diego, CA, USA, 16–20 February 2014; Springer: Berlin/Heidelberg, Germany, 2014.
- [16] Kulasegaram, S.; Bonet, J.; Lewis, R.W.; Profit, M. High pressure die casting simulation using a Lagrangian particle method. Commun. Numer. Methods Eng. 2003, 19, 679-687.
- [17] Homayonifar, P.; Babaei, R.; Attar, E.; Shahinfar, S.; Davami, P. Numerical modeling of splashing and air entrapment in high-pressure die casting. Int. J. Adv. Manuf. Technol. 2008, 39, 219-228.
- [18] Bi, C.; Xiong, S. Development of a Full PLIC-VOF Method for Mold Filling Simulation of High Pressure Die Casting Process. In Proceedings of the 8th Pacific Rim International Congress on Advanced Materials and Processing, Waikoloa, HI, USA, 4–9 August 2013; Marquis, F., Ed.; Springer International Publishing: Cham, Switzerland, 2016; pp. 2867–2874.
- [19] Sakuragi, T. Mould filling simulation with consideration of surface tension and its application to a practical casting problem. Cast Metals 2013, 18, 202-208.
- [20] Niida, A.; Maeda, Y. Observation of Air Entrapment during Mold Filling of Die Casting Using Water Model Experiment for Mold Filling Simulation. Mater. Trans. 2020, 61, 1364-1368.
- [21] Liu, J.; Zhou, P.; Zuo, X.; Wu, D.; Wu, D. Optimization of the Liquid Steel Flow Behavior in the Tundish through Water Model Experiment, Numerical Simulation and Industrial Trial. Metals 2022, 12, 1480.
- [22] Lin, S.P.; Reitz, R.D. Drop and spray formation from a liquid jet. Annu. Rev. Fluid Mech. 1998, 30, 85–105.
9. 著作権:
この資料は、Hanxue Caoらの論文:「ダイカストアルミニウム合金における穴欠陥の進化に対する射出速度の影響に関する研究」に基づいています。
論文ソース: https://doi.org/10.3390/ma17204990
この資料は上記の論文に基づいて要約したものであり、商業目的での無断使用は禁止されています。
Copyright © 2025 CASTMAN. All rights reserved.