本論文概要は、['Università di Bologna' が発行した 'DESIGNING AN INNOVATIVE MODULAR PLATFORM FOR SPORTS CARS USING THE GENERATIVE DESIGN METHOD'] の論文に基づいて作成されました。
1. 概要:
- タイトル: ジェネレーティブデザイン手法を用いたスポーツカー用革新的モジュラープラットフォームの設計 (DESIGNING AN INNOVATIVE MODULAR PLATFORM FOR SPORTS CARS USING THE GENERATIVE DESIGN METHOD)
- 著者: メルヴェ・サリ (Merve Sali)
- 発行年: 2024年
- 発行ジャーナル/学会: ボローニャ大学 (Università di Bologna) 機械工学・先端科学博士課程 (DOTTORATO DI RICERCA IN MECCANICA E SCIENZE AVANZATE DELL'INGEGNERIA)
- キーワード: 提供された文書に明示的なリストはありませんが、タイトルと要約から推測されるキーワードは以下の通りです: モジュラープラットフォーム (Modular Platform), スポーツカー (Sports Cars), ジェネレーティブデザイン手法 (Generative Design Method), 自動車シャシー (Automotive Chassis), 軽量設計 (Lightweight Design), アジャイル手法 (Agile Method), スクラム (Scrum).
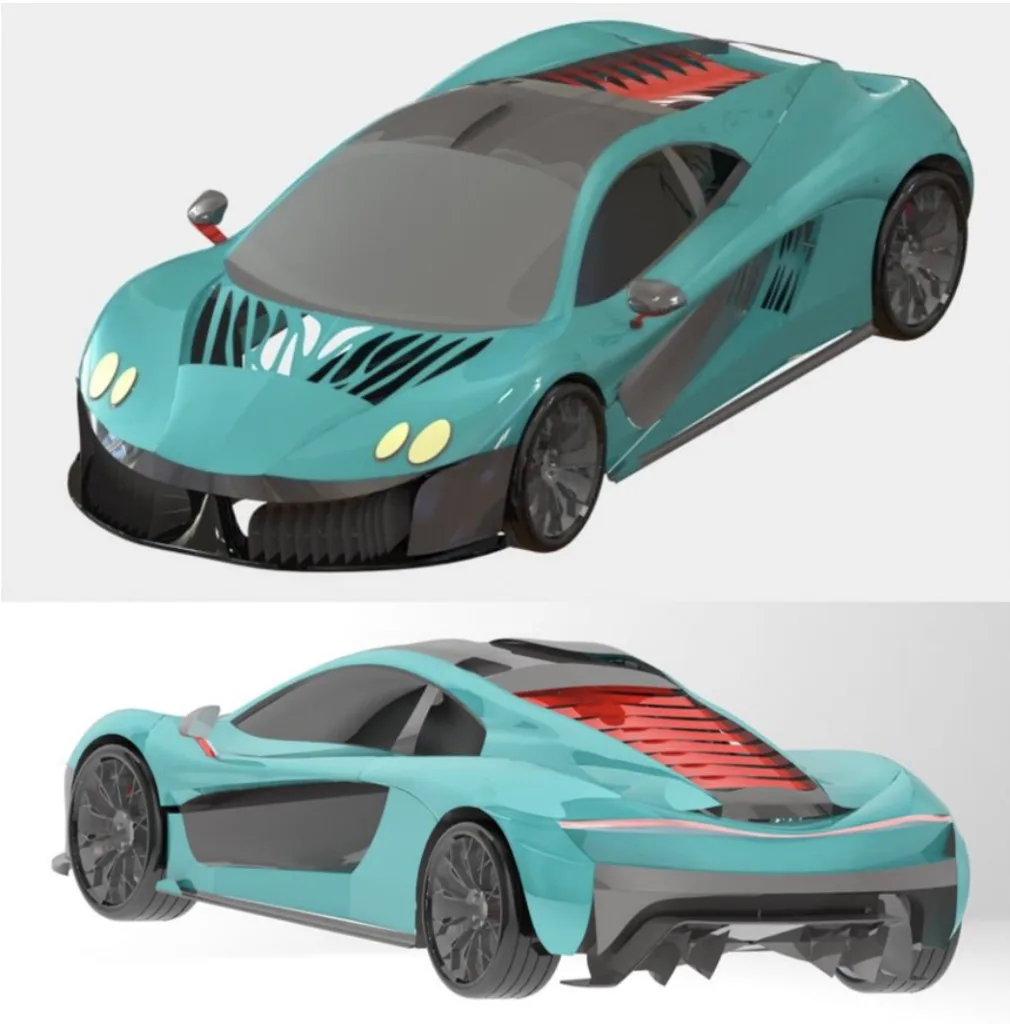
2. 抄録
従来の製造方法では、シャシー部品は車種ごとに特注で製造されるため、柔軟性と効率性に欠けていました。現在のモジュラープラットフォームの概念は、異なるモデル間で部品を再利用することを可能にし、生産コストを削減し、適応性を向上させます。しかし、現状では、これらのソリューションはスポーツカーセグメントでは一般的ではありません。本研究は、スポーツカーのコンテキストにおけるモジュラープラットフォームがもたらす課題と機会を掘り下げ、ドライビングダイナミクス、デザイン美学、将来のイノベーションに対する潜在的な影響を強調しています。本プロジェクトは、標準化された設計セクションを維持しながら多様性を提供し、柔軟性に加えて部品の互換性を重視し、最先端の設計手法を使用するモジュラープラットフォームアプローチに焦点を当てています。本研究は、ジェネレーティブデザイン手法を使用することにより、軽量かつ高剛性の設計を目標とする反復的なスプリントを用いて、異なるドライブトレインおよびパワートレイン構成に適したモジュラープラットフォームを作成することを目的としています。設計成果の改善に加えて、既存のワークフロー(IDeS)内でジェネレーティブデザイン手法のステップを採用し、アジャイル手法のバリアントであるスクラムとの連携を確立して、プロジェクト開発に不可欠な結果のフィルタリングを確立することにより、創造性を高めるための努力が払われています。さらに、ジェネレーティブデザインアプリケーションを通じて得られた新しい部品で作成された代替モジュラープラットフォームに適用されています。得られた結果は、モデルの機械的特性の観点から評価されました。これらの新しい部品は、幾何学的に効率的であるだけでなく、異なる材料を使用した場合でも同じ機械的結果を生み出すことができます。シミュレーションの数値結果は、生成された部品(パート1、パート3、パート4)と初期部品で作成された最終アセンブリについて比較されます。特に、ジェネレーティブデザイン手法を採用することにより、パート3(アウトカム7)の部品に鋼合金の代わりにアルミニウム合金を使用することで、同等の強度値を達成できることが実証されました。ねじりおよび曲げ剛性試験は、ジェネレーティブデザインプロセス前後の各モデルに対して実施されました。生成するために定義された部品は、リアミッドおよびフロントモジュラープラットフォームレイアウトでの衝突試験によって決定されました。結果を比較したところ、応力分布が類似していることがわかりました。これは、私たちが生成した部品が、形状、重量、機械的特性などの新しい設計に十分であることを意味します。
3. 研究背景:
研究テーマの背景:
従来の自動車シャシーの設計手法は、各車種に合わせて部品を特注で製造するため、柔軟性と効率性に欠けています。現在のモジュラープラットフォームは、モデル間で部品を再利用できるため、生産コストを削減し、適応性を向上させることができます。しかし、これらのソリューションはスポーツカーセグメントでは一般的ではありません。本研究は、スポーツカーにおけるモジュラープラットフォームの課題と機会に取り組み、ドライビングダイナミクス、デザイン美学、イノベーションへの潜在的な影響を検討します。このプロジェクトは、スポーツカー用のモジュラープラットフォームを作成することを目的としており、最先端の設計手法を用いて多様性、標準化された設計、部品の互換性、および柔軟性を重視しています。
既存研究の現状:
既存の研究では、自動車産業におけるモジュラープラットフォームの利点、すなわちコスト削減と柔軟性の向上を認識しています (Florea et al., 2016; Lampón et al., 2015)。文献レビューでは、三菱自動車が先駆けた共有プラットフォーム (Cusumano & Nobeoka, 1998) から PSA グループによる標準化の取り組み (Holweg, 2008; Patchong et al., 2003) まで、プラットフォーム戦略の進化を強調しています。また、軽量自動車部品のためのジェネレーティブデザインとアディティブマニュファクチャリングの応用 (Junk & Rothe, 2022; Fenoon et al., 2021; Dalpadulo et al., 2020) を探求し、シャシー開発における革新的な設計と材料利用の傾向を示しています。
研究の必要性:
本研究は、モジュラープラットフォームの潜在的な利点にもかかわらず、スポーツカーセグメントでの適用が限定的であるため、その必要性があります。自動車製造における柔軟性、効率性、適応性に対する要求の高まりと、軽量設計および持続可能な慣行の必要性が相まって、モジュラー型スポーツカープラットフォームのためのジェネレーティブデザインのような革新的なアプローチを模索する必要があります。さらに、気候変動に対処し、CO2 排出量を削減する必要性 (European Parliament and the Council of the European Union, 2019) が、自動車産業をモジュール式で持続可能なソリューションへと推進しています。
4. 研究目的と研究課題:
研究目的:
本研究は、ジェネレーティブデザイン手法を使用することにより、軽量かつ高剛性の設計を目標とする反復的なスプリントを用いて、異なるドライブトレインおよびパワートレイン構成に適したモジュラープラットフォームを作成することを目的としています。設計成果の改善に加えて、既存のワークフロー(IDeS)内でジェネレーティブデザイン手法のステップを採用し、アジャイル手法のバリアントであるスクラムとの連携を確立して、プロジェクト開発に不可欠な結果のフィルタリングを確立することにより、創造性を高めるための努力が払われています。
主要な研究課題:
- さまざまなドライブトレインおよびパワートレイン構成に適応可能なスポーツカー用モジュラープラットフォームの作成。
- 軽量かつ高剛性設計を実現するためのジェネレーティブデザイン手法の適用。
- インダストリアルデザインストラクチャー(IDeS)ワークフロー内へのジェネレーティブデザインの統合。
- 生成されたデザイン出力を管理およびフィルタリングするためのスクラム方法論の実装。
- モジュラープラットフォームの機械的特性と性能の評価。
研究仮説:
本論文では、研究仮説は明示的に述べられていません。しかし、研究目的と主要な研究課題に基づいて、暗黙の仮説は次のとおりです。
- ジェネレーティブデザイン手法は、モジュラー型スポーツカープラットフォーム用の幾何学的に効率的で軽量な部品を作成できます。
- ジェネレーティブデザインで設計されたモジュラープラットフォームは、従来の方法で設計されたプラットフォームと比較して、同等または改善された機械的特性を達成できます。
- スクラム方法論を IDeS ワークフローおよびジェネレーティブデザインと統合することで、モジュラープラットフォームの設計プロセスの効率と創造性を高めることができます。
- ジェネレーティブデザインされた部品にアルミニウム合金を使用すると、重量を削減しながら鋼合金部品と同等の強度を達成できます。
5. 研究方法論
研究デザイン:
本研究では、ジェネレーティブデザインを用いた革新的なモジュラープラットフォームの開発に焦点を当てたデザインベースの研究アプローチを採用しています。インダストリアルデザインストラクチャー(IDeS)ワークフローとスクラム方法論およびジェネレーティブデザイン技術を統合しています。設計プロセスは反復的であり、分析とテストに基づいてスプリントと適応を含みます。
データ収集方法:
データ収集方法は、この要約では明示的に詳述されていませんが、次のように推測できます。
- 文献調査: モジュラープラットフォーム、ジェネレーティブデザイン、自動車シャシー設計に関する既存の研究を理解します。
- 市場分析データ: 市場動向、顧客要件、競合分析を理解します。
- シミュレーションデータ: 機械的特性を評価するためのシミュレーション(ねじり、曲げ、衝突試験)からの数値結果。
- 専門家インタビュー: 業界専門家のプロフィールの分析 (図 3.1 参照)。
分析手法:
- 品質機能展開 (Quality Function Deployment, QFD): 顧客要件を分析し、設計パラメータに変換します。
- 依存性/独立性マトリックスと相対的重要度マトリックス: 顧客要件の優先順位を付けます。
- ベンチマーキング: 既存のスポーツカーモデルを比較し、設計パラメータを特定します。
- 有限要素解析 (Finite Element Analysis, FEA): SolidWorks Simulation を使用して、機械的応力解析 (ねじり剛性、曲げ剛性、正面衝突解析) を実行し、モジュラープラットフォームとジェネレーティブデザインされた部品の性能を評価します。
- 比較分析: 初期部品とジェネレーティブデザインされた部品、および異なる構成と材料のプラットフォームのシミュレーション結果を比較します。
研究対象と範囲:
- 研究対象: スポーツカー用モジュラープラットフォームの設計と解析。エンジン室(パート1)、コックピット下部(パート3)、電気モーター室(パート4)用に生成的に設計された部品。
- 研究範囲: モジュラープラットフォームの構造設計と機械的性能、特にシャシー部品に焦点を当てています。スタイリングとより広範な車両開発の側面も考慮されますが、構造的およびモジュラー設計の側面が優先されます。材料範囲は主に鋼鉄とアルミニウム合金です。
6. 主な研究成果:
主要な研究成果:
- ジェネレーティブデザイン手法は、モジュラープラットフォーム用の軽量部品(パート1、パート3、パート4)を作成するために成功裏に適用されました。
- アルミニウム合金を使用したジェネレーティブデザイン部品は、特にパート3(アウトカム7)で大幅な軽量化を実現しながら、初期の鋼合金部品と同等の強度値を達成しました。
- 初期モジュラープラットフォームとジェネレーティブデザインされたモジュラープラットフォームについて、ねじりおよび曲げ剛性試験を実施し、比較し、新しい設計の実現可能性を実証しました。
- ジェネレーティブデザイン手法と IDeS ワークフローを統合した新しいスクラムワークフローモデルが開発され、適用されました。
- モジュラープラットフォーム設計により、異なるエンジンレイアウト(リアミッドおよびフロントエンジン)とパワートレイン構成への適応が可能になります。
提示されたデータの分析:
- ねじり剛性: 初期プラットフォームとジェネレーティブデザインされたプラットフォームの両方のねじり剛性値は同等の範囲内ですが、ジェネレーティブデザインされたリアミッドエンジンプラットフォーム(9179.317 Nm/deg)は、初期リアミッドエンジンプラットフォーム(9705.0857 Nm/deg)と比較してわずかに低くなっています。
- 曲げ剛性: 曲げ剛性値も初期プラットフォームとジェネレーティブデザインされたプラットフォーム間で同等であり、ジェネレーティブデザインされたリアミッドプラットフォームは、初期リアミッドプラットフォーム(25786.02 Nm/deg)よりもわずかに低い値(21773.6 Nm/deg)を示しています。
- 質量削減: ジェネレーティブデザインとアルミニウム合金の使用により、部品の質量が大幅に削減され (表 3.14)、特にパート 3 では、アルミニウム合金アウトカム 7 が初期鋼合金部品と比較して 3.932 kg の質量を達成しました。
- 応力分布: 応力分布解析の結果、最大応力位置は初期プラットフォームとジェネレーティブデザインされたプラットフォームの両方で類似しており、主に接続点と荷重集中領域で発生しています。
図のリスト:
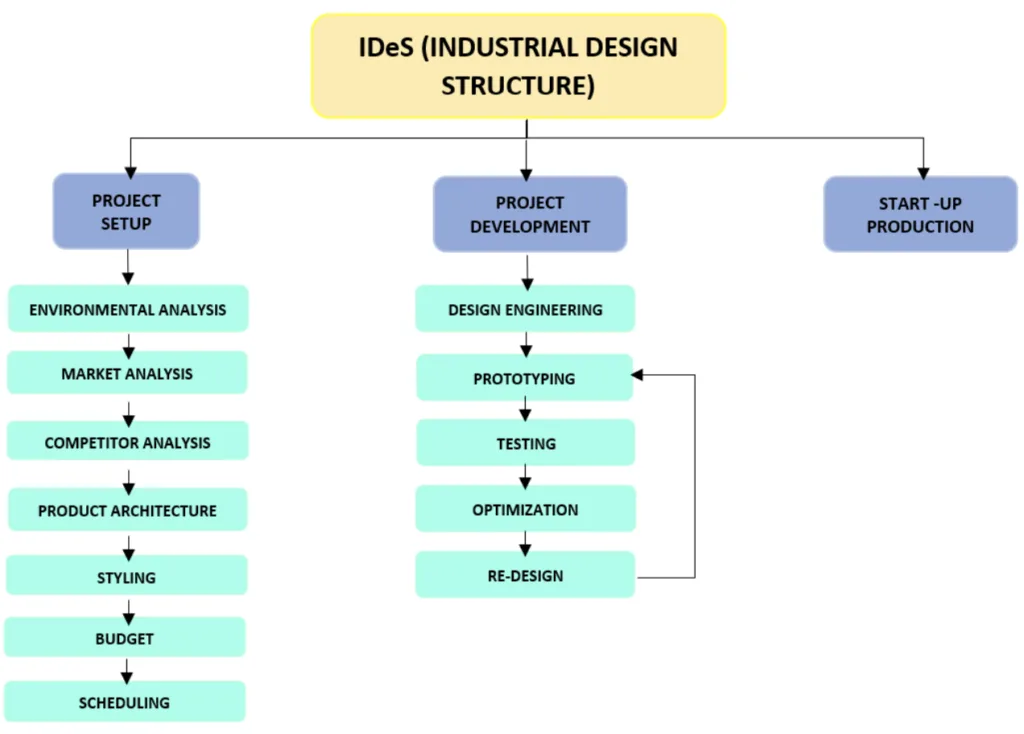
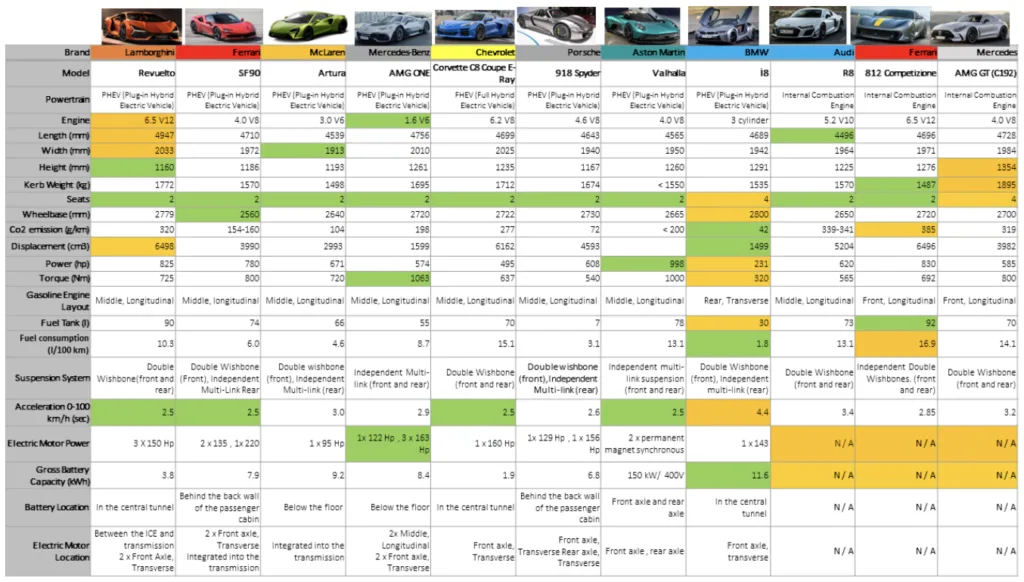
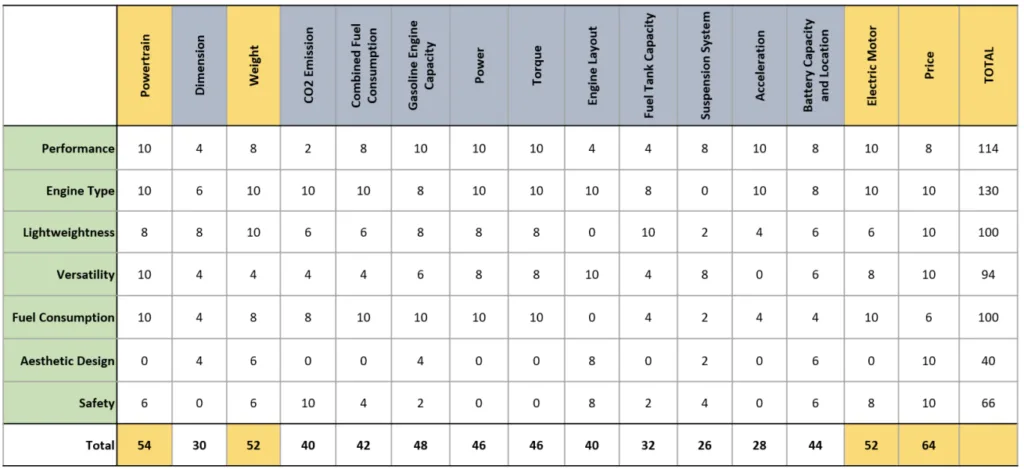
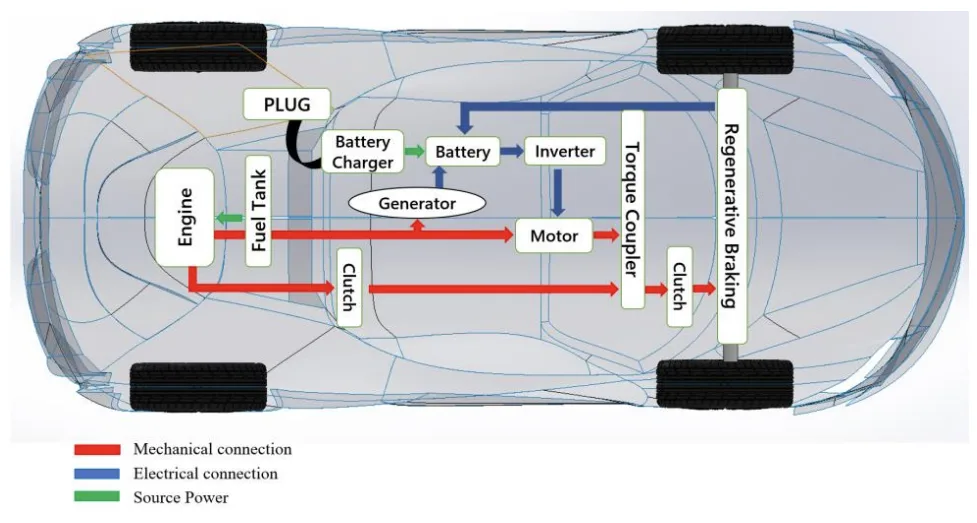
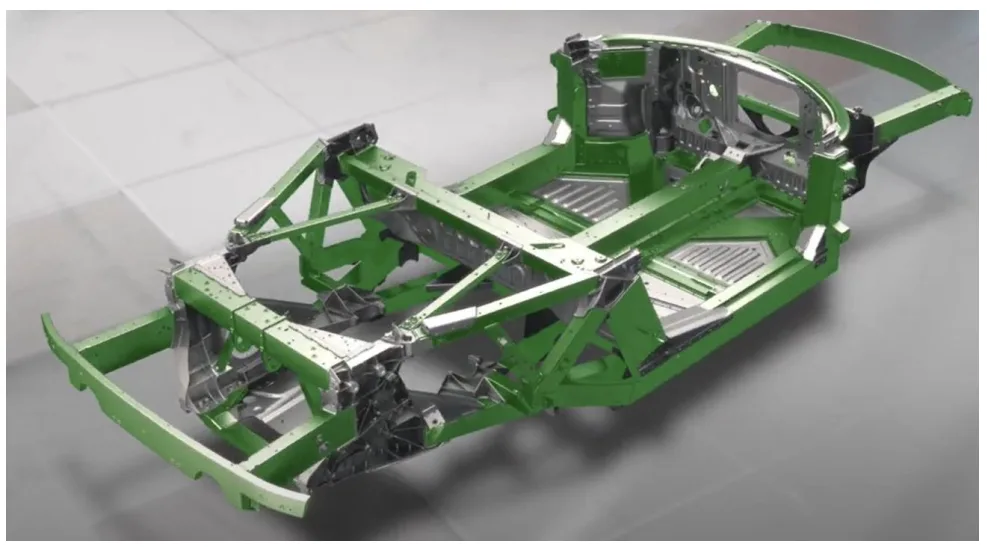
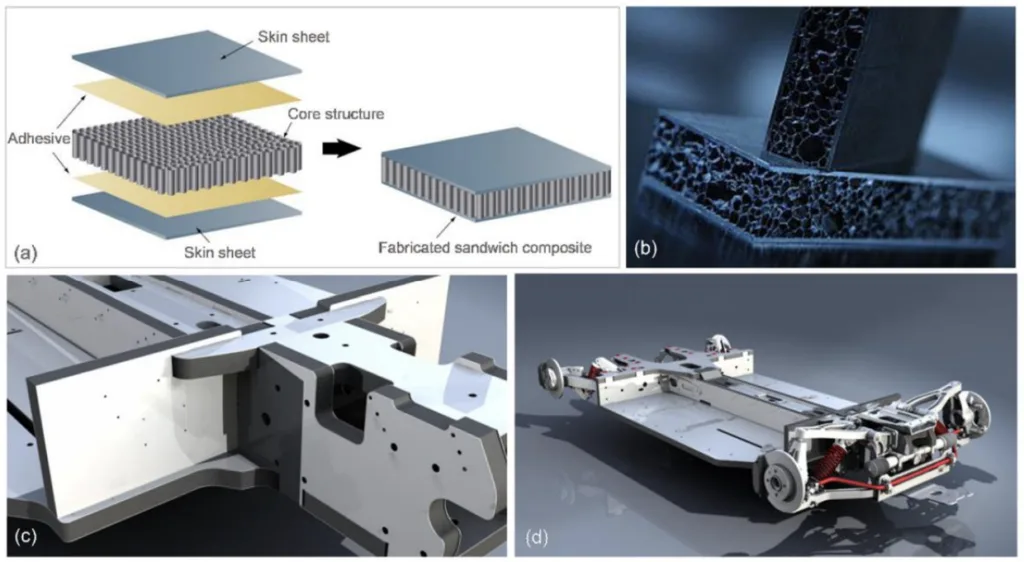
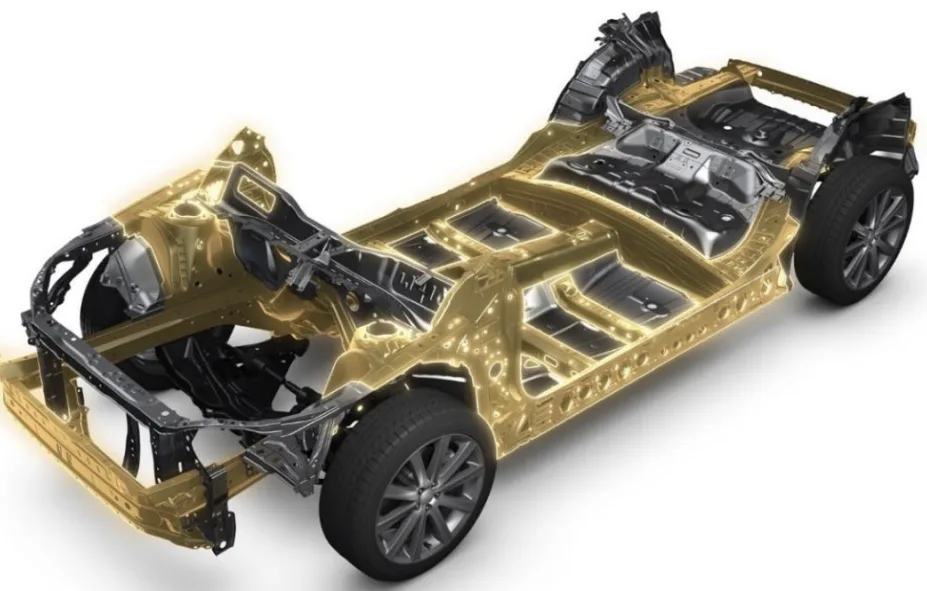
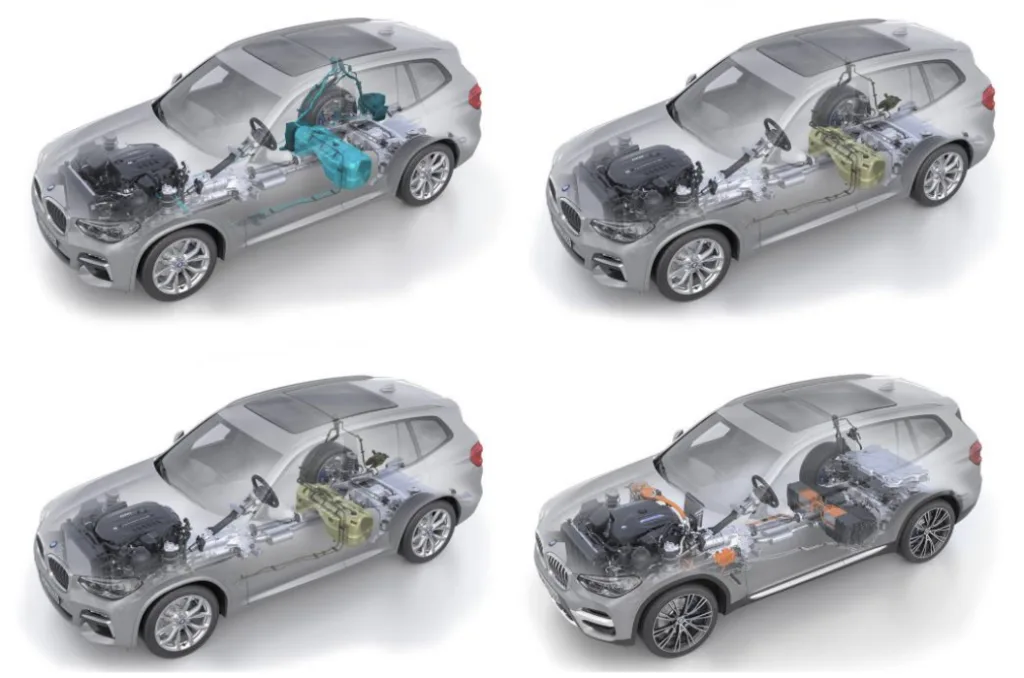
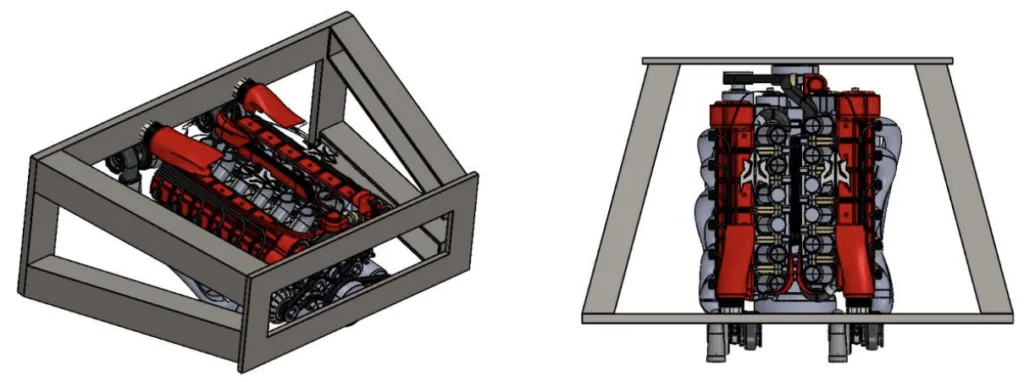
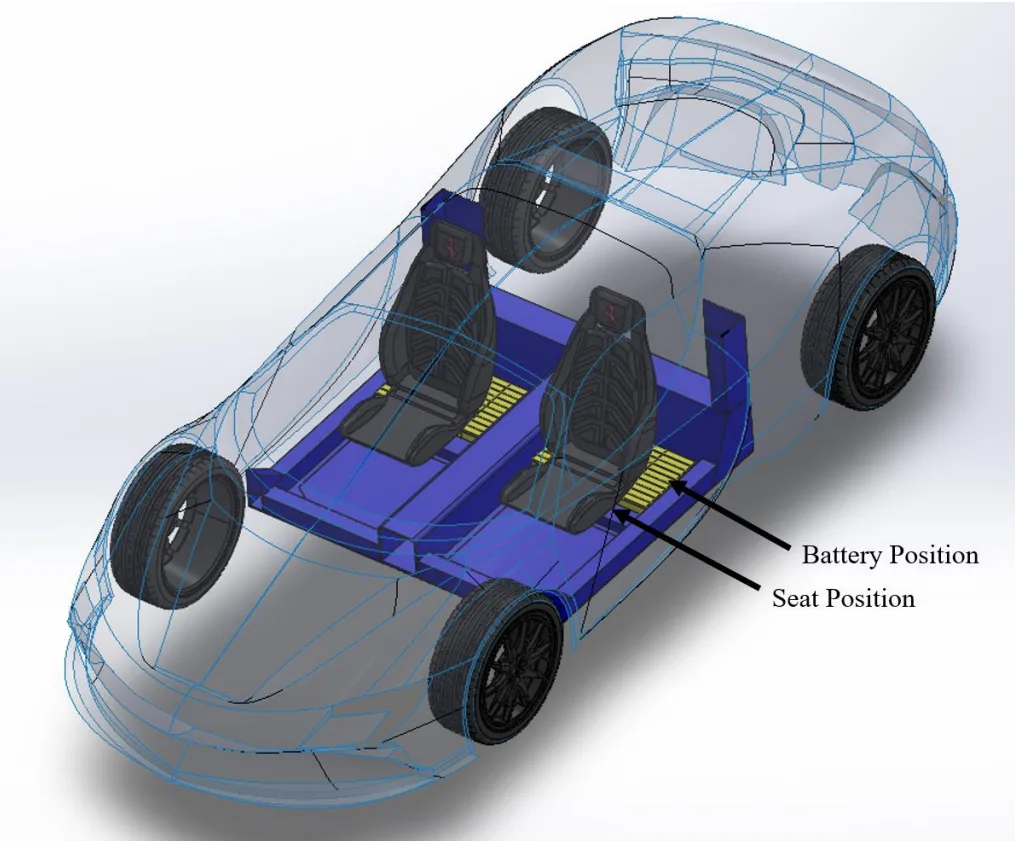
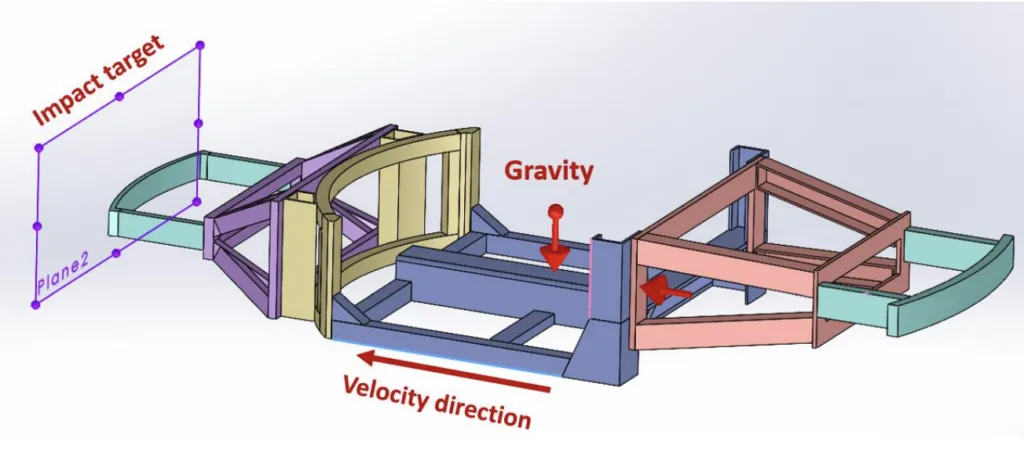
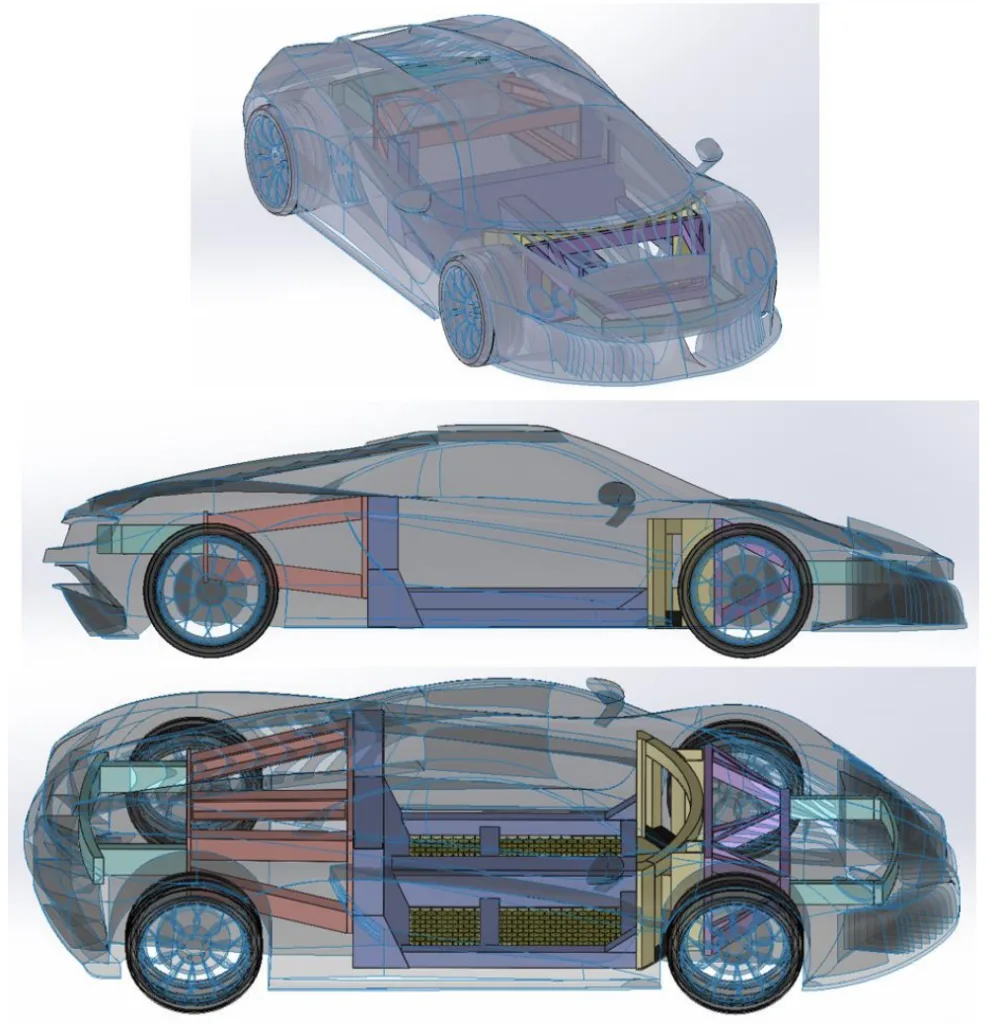
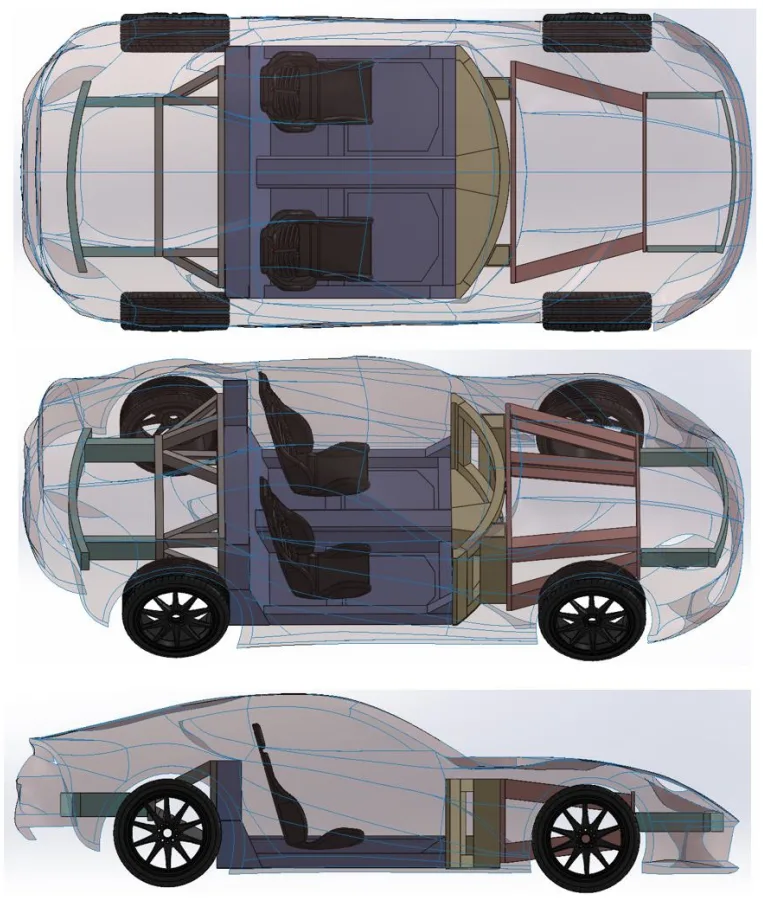
- Figure 1.1: 産業デザイン構造 (Industrial Design Structure)
- Figure 3.1: 業界専門家のプロフィールの内訳 (Break-up of the profiles of industry experts)
- Figure 3.2: アジア太平洋地域の自動車シャシーの市場規模、2019-2030年 (10億米ドル) (The market size of the Automotive Chassis in the Asia Pacific, 2019-2030(USD Billion))
- Figure 3.3: シャシータイプ別の世界の自動車シャシー市場シェア、2022年 (Global automotive chassis market share by chassis type, 2022)
- Figure 3.4: 品質機能展開 (QFD) テンプレート (House of quality template)
- Figure 3.5: QFD - 6つの質問 (QFD- Six Questions)
- Figure 3.6: 依存/独立マトリックス (Dependence / Independence matrix)
- Figure 3.7: 相対的重要度マトリックス (Relative importance matrix)
- Figure 3.8: What-How マトリックス (What-How matrix)
- Figure 3.9: さまざまなドライブトレイン構成のフロントエンジンレイアウト (Front Engine layouts with different drivetrain configurations)
- Figure 3.10: 全輪駆動構成のフロントエンジンレイアウト (Front Engine layout with all wheel drive configuration)
- Figure 3.11: さまざまなドライブトレイン構成のリアエンジンレイアウト (Rear Engine layouts with different drivetrain configurations)
- Figure 3.12: シリーズ HEV 構成 (Series HEV configuration)
- Figure 3.13: パラレルハイブリッドパワートレイン構成 (Parallel hybrid powertrain configuration)
- Figure 3.14. シリーズ-パラレルスプリットハイブリッドパワートレイン構成 (Series-Parallel split hybrid powertrain configuration)
- Figure 3.15: プラグインシリーズハイブリッド電気自動車構成 (Plug-in series hybrid electric vehicle configuration)
- Figure 3.16: プラグインパラレルハイブリッド電気自動車構成 (Plug-in parallel hybrid electric vehicle configuration)
- Figure 3.17: プラグインシリーズ/パラレルハイブリッド電気自動車構成 (Plug-in series / Parallel hybrid electric vehicle configuration)
- Figure 3.18: ジェネレーティブデザイン反復プロセス例 (Generative design iterative process example)
- Figure 3.19: CAD および生成されたモジュール使用モデルの例 (Example of CAD and generated module used model)
- Figure 3.20: 押し出し成形で製造された部品 (Parts produced through extrusion)
- Figure 3.21: 従来の高張力鋼における極限引張強度と全伸び率の関係 (The relationship between ultimate tensile strength and total elongation in traditional high-strength steels)
- Figure 3.22: 自動車サブフレームにおけるサンドイッチ構造複合材の応用 (Sandwich structured composite application in automotive sub-frame)
- Figure 3.23: PSA 共通モジュラープラットフォーム (PSA Common modular platform)
- Figure 3.24: フォルクスワーゲン MQB モジュラープラットフォーム (Volkswagen MQB modular platform)
- Figure 3.25: トヨタ (TNGA) モジュラープラットフォーム (Toyota (TNGA) modular platform)
- Figure 3.26: スバル (SGP) モジュラープラットフォーム (Subaru (SGP) modular platform)
- Figure 3.27: ルノー-日産 CMF モジュラープラットフォーム (Renault-Nissan CMF modular platform)
- Figure 3.28: BMW (CLAR) モジュラープラットフォーム (BMW (CLAR) modular platform)
- Figure 3.29: モジュラー車両プラットフォーム (Modular vehicle platform)
- Figure 3.30: パート 1: エンジンコンパートメントの寸法 (Part 1: Engine compartment dimensions)
- Figure 3.31: 縦方向位置の V6 シボレーエンジン (V6 Chevrolet engine for longitudinal position)
- Figure 3.32: 縦方向位置の V6 ジャガーエンジン (V6 Jaguar engine for longitudinal position)
- Figure 3.33: 縦方向位置の V8 エンジン (V8 Engine for longitudinal position)
- Figure 3.34: 横方向位置の V8 エンジン (V8 Engine for transverse position)
- Figure 3.35: トランスミッション付き縦方向配置の V12 エンジン (V12 Engine for longitudinal positioning with transmission)
- Figure 3.36: 縦方向位置の V12 エンジン (V12 Engine for longitudinal position)
- Figure 3.37: 車に図示されたシート配置の寸法パラメータ (Dimensional parameters of seat arrangement illustrated on a car)
- Figure 3.38: スポーツカーシートの適合パラメータの寸法 (Sports car seat dimensions of fit parameters)
- Figure 3.39: モジュラープラットフォーム上のバッテリー配置 (Battery positioning on modular platform)
- Figure 3.40: パート 2: 乗員ゾーンの寸法 (Part 2: Passenger zone dimensions)
- Figure 3.41: パート 3: a) リアミッドエンジン構成 b) フロントエンジン構成アセンブリ (Part 3: Assembly with a) Rear-Mid engine configuration b) Front engine configuration)
- Figure 3.42: パート 3: コックピット下部の寸法 (Part 3: Cockpit underbody dimensions)
- Figure 3.43: パート 4: ダブル電気モーターアセンブリ (Part 4: Assembly with double electric motor)
- Figure 3.44: パート 4: 電気モーター室の寸法 (Part 4: Electric motor compartment dimensions)
- Figure 3.45: モジュラープラットフォーム設計の最終モデルと寸法 (Modular platform design final model and dimensions)
- Figure 3.46: 車両の動きの間の力 (Forces during the car motion)
- Figure 3.47: 縦ねじり (Longitudinal torsion)
- Figure 3.48: ねじり剛性荷重ケース (Torsional stiffness load case)
- Figure 3.49: 垂直曲げ (Vertical bending)
- Figure 3.50: 曲げ剛性荷重ケース (Bending stiffness load case)
- Figure 3.51: 横曲げ (Lateral bending)
- Figure 3.52: 水平ひし形 (Horizontal lozenging)
- Figure 3.53: リアミッドモジュラープラットフォームの境界条件 (Boundary conditions on rear-mid modular platform)
- Figure 3.54. リアミッドモジュラープラットフォームのねじり試験の変位結果 (Displacement results of torsional test for rear-mid modular platform)
- Figure 3.55. リアミッドモジュラープラットフォームのねじり応力分布 (Torsional stress distribution of rear-mid modular platform)
- Figure 3.56: フロントモジュラープラットフォームの境界条件 (Boundary conditions on front modular platform)
- Figure 3.57: フロントモジュラープラットフォームのねじり試験の変位結果 (Displacement results of torsional test for front modular platform)
- Figure 3.58: フロントモジュラープラットフォームのねじり応力分布 (Torsional stress distribution of front modular platform)
- Figure 3.59: 曲げ試験用のリアミッドモジュラープラットフォームの境界条件 (Boundary conditions on rear-mid modular platform for bending test)
- Figure 3.60: 曲げ試験用のリアミッドモジュラープラットフォームの変位結果 (Displacement results of bending test for rear-mid modular platform)
- Figure 3.61: リアミッドモジュラープラットフォームの曲げ応力分布結果 (Bending stress distribution results of rear-mid modular platform)
- Figure 3.62: 曲げ試験用のフロントモジュラープラットフォームの境界条件 (Boundary conditions on front modular platform for bending test)
- Figure 3.63: 曲げ試験用のフロントモジュラープラットフォームの変位結果 (Displacement results of bending test for front modular platform)
- Figure 3.64: フロントモジュラープラットフォームの曲げ応力分布結果 (Bending stress distribution results of front modular platform)
- Figure 3.65: リアミッドモジュラープラットフォームの衝撃試験設定 (Impact test settings for rear-mid modular platform)
- Figure 3.66: 衝撃試験結果 (a) 変位結果、 (b) 変形分布結果 (Impact test results (a) Displacement results, (b) Deformation distribution results)
- Figure 3.67: パート 3 およびパート 4 の部品開発用に定義されたセクション (Defined sections for part development on Part 3 and Part 4)
- Figure 3.68: フロントモジュラープラットフォームの衝撃試験設定 (Impact test settings for front modular platform)
- Figure 3.69: 衝撃試験結果 (a) 変位結果、 (b) 変形分布結果 (Impact test results (a) Displacement results, (b) Deformation distribution results)
- Figure 3.70: パート 1 の部品開発用に定義されたセクション (Defined section for the part development on Part 1)
- Figure 3.71: レトロデザイン (Retro design)
- Figure 3.72: ストーンデザイン (Stone design)
- Figure 3.73: メカジキの背びれからインスピレーションを得たナチュラルデザイン (Natural design inspired from the dorsal lines of the sailfish)
- Figure 3.74: ナチュラルデザイン (Natural design)
- Figure 3.75: アドバンストデザイン (Advanced design)
- Figure 3.76: 最終デザインのために選択された詳細の表現 (Representation of the details selected for the final design)
- Figure 3.77: 最終デザインスケッチ (Final design sketching)
- Figure 3.78: 最終スケッチのブループリント (Blueprint of final sketch)
- Figure 3.79: 最終スケッチのローデザイン (Raw design of final sketch)
- Figure 3.80: 最終 3D デザイン (Final 3D design)
- Figure 3.81: レンダリングされた最終デザイン (Rendered final design)
- Figure 3.82: モジュラープラットフォームと最終デザインアセンブリ (Modular platform and final design assembly)
- Figure 3.83: スクラムプロセス (Scrum process)
- Figure 3.84: ジェネレーティブデザインワークフロー (Generative design workflow)
- Figure 3.85: 方法の比較 a) スプリントステップ (Srivastava et al., 2017) b) ジェネレーティブデザインプロセスステップ (Comparison of methods a) Sprint steps (Srivastava et al., 2017) b) Generative design process steps)
- Figure 3.86: ジェネレーティブデザイン手法を用いた新しいスクラムワークフローモデル (New scrum workflow model with generative design method)
- Figure 3.87: スクラムとジェネレーティブデザイン手法を用いた修正された IDeS ワークフロー (Modified IDeS workflow using Scrum and Generative Design method)
- Figure 3.88: 材料の詳細を含むフォルクスワーゲン MQB プラットフォーム (Volkswagen MQB platform with material details)
- Figure 3.89: プラットフォームセクションの境界 (Boundaries of platform sections)
- Figure 3.90: モジュラープラットフォームアセンブリの分解図 (Exploded view of the modular platform assembly)
- Figure 3.91: リアミッドエンジン用モジュラープラットフォーム (Modular platform for rear-mid engine)
- Figure 3.92: フロントエンジン用モジュラープラットフォーム (Modular platform for front engine)
- Figure 3.93: モジュラープラットフォームのボルト締めジョイント (Bolted joints of the modular platform)
- Figure 3.94: ジェネレーティブデザイン用に定義された領域 (Areas defined for generative design)
- Figure 3.95: エンジンコンパートメントの境界条件 (パート 1) (Boundary conditions of engine compartment (Part1))
- Figure 3.96: コックピット下部の境界条件 (パート 3) (Boundary conditions of cockpit underbody (Part3))
- Figure 3.97: 電気モーター室の境界条件 (パート 4) (Boundary conditions for electric motor compartment (Part 4))
- Figure 3.98: パート 1 の構造的制約と荷重 (Structural constraints and loads on Part 1)
- Figure 3.99: パート 3 の構造的制約と荷重 (Structural constraints and loads on Part 3)
- Figure 3.100: パート 4 の構造的制約と荷重 (Structural constraints and loads on Part 4)
- Figure 3.101: 生成設計結果鋼合金適用パート 1 (Generative design results steel alloys applied Part 1)
- Figure 3.102: 生成設計結果鋼合金適用パート 3 (Generative design results steel alloys applied Part 3)
- Figure 3.103: 生成設計結果鋼合金適用パート 4 (Generative design results steel alloys applied Part 4)
- Figure 3.104: 生成設計結果アルミニウム合金適用パート 1 (Generative design results aluminium alloys applied Part 1)
- Figure 3.105: 生成設計結果アルミニウム合金適用パート 3 (Generative design results aluminium alloys applied Part 3)
- Figure 3.106: 生成設計結果アルミニウム合金適用パート 4 (Generative design results aluminium alloys applied Part 4)
- Figure 3.107: 生成設計適用「理想的なモジュラープラットフォーム」 (Generative design applied “Ideal Modular Platform”)
- Figure 3.108: 理想的なモジュラープラットフォームのビームモデル (Beam model of ideal modular platform)
- Figure 3.109: リアミッドエンジンレイアウトの理想的なモジュラープラットフォームの変位結果 (Displacement results of ideal modular platform for rear-mid engine layout)
- Figure 3.110: リアミッドエンジンレイアウトの理想的なモジュラープラットフォームのねじり応力分布 (Torsional stress distribution of ideal modular platform for rear-mid engine layout)
- Figure 3.111: フロント理想的なモジュラープラットフォームの境界条件 (Boundary conditions on front ideal modular platform)
- Figure 3.112: フロントエンジンレイアウトの理想的なモジュラープラットフォームの変位結果 (Displacement results of ideal modular platform for front engine layout)
- Figure 3.113: フロントエンジンレイアウトの理想的なモジュラープラットフォームのねじり応力分布 (Torsional stress distribution of ideal modular platform for front engine layout)
- Figure 3.114: 曲げ試験用のリアミッド理想的なモジュラープラットフォームの境界条件 (Boundary conditions on rear-mid ideal modular platform for bending test)
- Figure 3.115: 曲げ試験用のリアミッド理想的なモジュラープラットフォームの変位結果 (Displacement results of bending test for rear-mid ideal modular platform)
- Figure 3.116: リアミッド理想的なモジュラープラットフォームの曲げ応力分布結果 (Bending stress distribution results of rear-mid ideal modular platform)
- Figure 3.117: 曲げ試験用のフロント理想的なモジュラープラットフォームの境界条件 (Boundary conditions on front ideal modular platform for bending test)
- Figure 3.118: 曲げ試験用のフロント理想的なモジュラープラットフォームの変位結果 (Displacement results of bending test for front ideal modular platform)
- Figure 3.119: 曲げ試験用のフロント理想的なモジュラープラットフォームの曲げ応力分布結果 (Bending stress distribution results of front ideal modular platform)
7. 結論:
主な調査結果の要約:
本研究では、スクラムを組み込んだ修正された IDeS ワークフロー内で、ジェネレーティブデザイン手法を用いてスポーツカー用の適切なモジュラープラットフォームを設計することに成功しました。ジェネレーティブデザインにより、特にアルミニウム合金を使用した場合に、軽量部品を作成することが可能になり、機械的性能を維持または向上させることができました。モジュラープラットフォームは、異なるエンジンレイアウトとパワートレイン構成に適応可能であり、その汎用性を示しています。スクラム方法論の統合により、反復的で効率的な設計プロセスが促進されました。
研究の学術的意義:
本研究は、自動車シャシー設計、特にスポーツカーのモジュラープラットフォームにおけるジェネレーティブデザインとアジャイル方法論(スクラム)の効果的な応用を実証することにより、学術分野に貢献しています。これらの最先端技術を構造化された設計ワークフロー(IDeS)に統合するための詳細な方法論を提供します。また、本研究は、軽量かつ高性能な自動車構造を達成するためのジェネレーティブデザインにおける材料選択と最適化の理解を深めます。
実用的な意味合い:
本研究の実用的な意味合いは、自動車産業、特にスポーツカーメーカーにとって重要です。開発されたモジュラープラットフォーム設計は、生産コストの削減、車両の適応性向上、軽量化による燃費向上を実現するための実行可能なソリューションを提供します。ジェネレーティブデザインとアディティブマニュファクチャリング技術を使用すると、より革新的で効率的なシャシー設計につながる可能性があります。スクラム方法論の統合は、製品開発プロセスを合理化し、変化する市場の要求に、よりアジャイルかつ対応できるようにします。
研究の限界と今後の研究分野:
本研究は、シャシーの下部とビームモデルシミュレーションに焦点を当てているため、完全な車両シャシーを単純化しているという点で限界があります。得られたねじり剛性値は、既存のスポーツカーのフルシャシー値と直接比較することはできません。今後の研究では、以下に焦点を当てる必要があります。
- フルビークルシミュレーションと物理プロトタイピングによるモジュラープラットフォーム設計の検証。
- ジェネレーティブデザインにおける、より広範囲な材料と製造プロセスの探求。
- 性能と持続可能性を向上させるための多目的最適化とジェネレーティブデザインの統合の調査。
- さまざまな自動車設計プロジェクトに対応するためのスクラム-IDeS ワークフローのさらなる改良と、その幅広い適用可能性の評価。
- 生成的に設計された部品とモジュラープラットフォームの機械的特性の実験的検証の実施。
8. 参考文献:
- [参考文献リストは、英語の要約の 8 番目の項目を参照してください。]
9. 著作権:
- 本資料は "Merve Sali" の論文: "DESIGNING AN INNOVATIVE MODULAR PLATFORM FOR SPORTS CARS USING THE GENERATIVE DESIGN METHOD" に基づいています。
- 論文ソース: DOI URL はドキュメントで利用できません。
本資料は上記の論文に基づいて要約されたものであり、商業目的での無断使用は禁止されています。
Copyright © 2025 CASTMAN. All rights reserved.