この紹介論文は、[THE ROLE OF THERMAL PROCESSES IN THE FORMATION OF GALVANIC ZINC ANODES PROPERTIES]に基づいています。
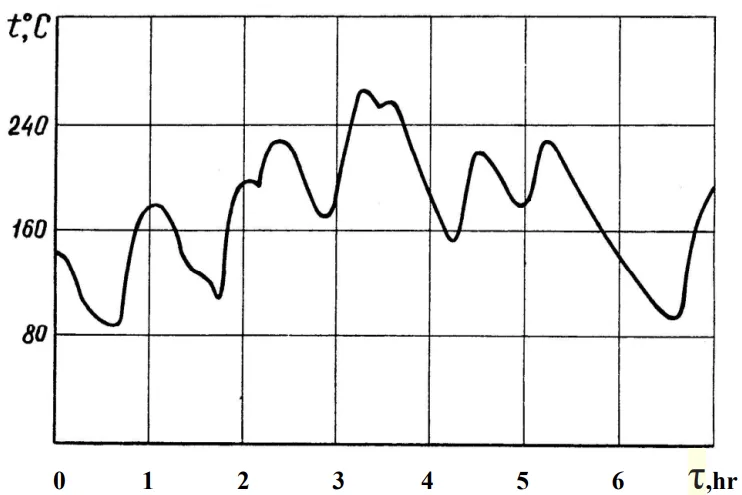
1. 概要:
- タイトル: THE ROLE OF THERMAL PROCESSES IN THE FORMATION OF GALVANIC ZINC ANODES PROPERTIES (ガルバニ亜鉛アノード特性形成における熱プロセスの役割)
- 著者: Prof. Vladimir Kechin¹, Prof. Efim Lyublinski², Phd. Evgeny Prusov¹ (¹Vladimir State University, Russia, kechin@vlsu.ru, ²COR/SCI, LLC, USA, elyublinski@gmail.com)
- 発行年: 論文に明記されていません
- 発行学術誌/学会: 論文に明記されていません
- キーワード: sacrificial anodes, structure, foundry, electrochemistry
2. 要旨:
「金属-電解質」系における鋳造犠牲ガルバニ陽極合金の電気化学的不均一性が現れる主な理由は、金属の性質、組成、構造などに関連する内部要因です。鋳造陽極の製造技術を開発する際には、合金の構造的均一性を確保することに特別な注意を払う必要があります。鋳造陽極の構造と基本特性の形成における主な役割は、鋳型内の溶湯の凝固条件に影響を与える熱プロセスによって果たされます。本論文では、冷却条件に応じた鋳造亜鉛犠牲合金(ZSA)の構造と基本電気化学的特性の研究結果を提示します。異なる冷却強度における凝固金属(金属が冷却されるとき)と形状(鋳型が加熱されるとき)の温度場の分析により、鋳造サイクルの持続時間を最適化することが可能になりました。これは、鋳型の初期温度によって決定される冷却条件を考慮し、トレッド全体の厚さにわたって均一な構造と材料の安定した電気化学的特性を保証します。例えば、18kgの亜鉛合金トレッドの鋳造では、鋳造前の鋳型温度は120-160℃であるべきであることが確立されています。これらの条件下では、鋳造犠牲陽極合金の必要な品質は、電流容量効率93-96%、腐食電位-E = 815-820 mV vs. SHEで達成されます。必要な鋳造サイクル時間は10-14分です。様々な形状とサイズの犠牲陽極についても同様のデータが得られました。数値シミュレーション法を用いた亜鉛陽極と鋳造金型(砂質-粘土質、鋳鉄、鋼製水冷式)との熱的相互作用の研究結果に基づき、水冷式金型への陽極鋳造の妥当性が示され、最も有利な熱除去条件と鋳造トレッドの均一な構造の取得が提供されます。得られた結果に基づいて、様々なサイズの亜鉛陽極の鋳造技術が開発され、これは高く安定した電気化学的特性を提供します。
3. 緒言:
熱プロセスは、溶湯の凝固中の鋳物のほとんどの特性形成において主導的な役割を果たします[1-11]。したがって、鋳型内の溶湯の凝固条件を研究することは、鋳造の熱理論の最も重要な課題です。この問題の緊急性は、犠牲陽極(SA)を鋳造する際に、金属鋳型の著しい温度変動があるという事実[12]によっても左右されます。したがって、亜鉛SA [組成 ZSA1: Zn+(0,4-0,6%)Al および ZSA2: Zn+(0,5-0,7%)Al+(0,1-0,3%Mg+0,1-0,3%Mn)、不純物 Fe-0,0015%未満、Cu-0,001%未満、Pb-0,005%未満] の鋳造中に、一連の鋳鉄鋳型の1つで温度を連続的に監視したところ、鋳型の初期温度がシフト中に80℃から260℃に変化することが注目されました(Fig.1)。明らかに、これはSA使用の初期段階で発生するZSA電気化学的特性の不安定化と低下、ならびに同じグレードの合金や同じ溶解からの個々のSAの有効性に関する矛盾したデータを説明できます[13]。
4. 研究の概要:
研究トピックの背景:
熱プロセスは、溶湯凝固中の鋳物の特性を決定する上で極めて重要です。これは特に犠牲陽極(SA)に当てはまり、金属鋳型での製造プロセスは、最終製品の性能に影響を与える可能性のある大幅な温度変動を伴います。
従来の研究状況:
従来の研究では、亜鉛犠牲陽極(ZSA)の鋳造中に金属鋳型で大幅な温度変動(シフト中に80℃から260℃、Fig.1)が観察されました。このような変動は、ZSAの電気化学的特性の不安定化と低下を引き起こし、同じ合金グレードや溶解内であっても、その有効性に関する矛盾したデータをもたらすと考えられています[13]。
研究の目的:
本研究の主な目的は、冷却の熱条件に応じたZn-Al合金[13]から作られた鋳造犠牲陽極の構造と基本的な電気化学的特性を研究することです。
研究の核心:
本研究では、鋳造中の熱プロセスが亜鉛犠牲合金(ZSA1およびZSA2)の構造および電気化学的特性に及ぼす影響を調査しました。主な側面は以下の通りです。
- 様々な初期鋳型温度(鋳鉄鋳型で20℃、160℃、310℃)における凝固中の温度場の分析。
- ポアリングアウト法を用いた凝固特性の決定、マクロ構造およびミクロ構造の検査。
- 電流容量効率(CC)および腐食電位(-E)などの電気化学的特性の評価。
- 鋳型温度と冷却条件を考慮した鋳造サイクル時間の最適化。
- 異なる鋳型材料(砂質-粘土質、鋳鉄、水冷鋼)での鋳造結果の比較。
- 鋳造温度(450℃、500℃、550℃)および凝固速度(Vs)がZSA特性に及ぼす影響の調査。
- 指向性凝固と陽極品質向上を目的とした改良鋳型設計の開発と評価。
5. 研究方法論
研究デザイン:
本研究では実験的アプローチを採用しました。これには、制御された様々な熱条件下でのZSAの鋳造、その後の熱分析、微細構造特性評価、および電気化学的性能試験が含まれます。また、ZSAと鋳型間の熱的相互作用を研究するために数値シミュレーション法も利用されました。
データ収集と分析方法:
- 測温: 凝固合金および鋳型内の温度場は熱電対(Fig. 3に示す)を用いて測定され、データは自動12点ポテンショメータによって記録されました。
- ポアリングアウト法: この方法は凝固プロセスを研究するために使用され、異なる時間間隔での凝固殻の厚さと質量を測定することができました(Table 2、Fig. 5)。
- マクロ構造およびミクロ構造分析: 異なる条件下で鋳造されたZSAのマクロ構造が検査されました(Fig. 2)。様々な温度および異なるタイプの鋳型で鋳造されたZSA1およびZSA2合金について、ミクロ構造分析(x100倍率)が実施されました(Fig. 8、Fig. 9)。
- 電気化学的特性試験: 電流容量(CC)、定常電位(-Ecまたは-φc)、および分極下電位(-Epまたは-φp)を含む主要な電気化学的特性が決定されました(Table 3)。試験は人工海水中で実施されました。
- 数値シミュレーション: これらの方法は、犠牲陽極を水冷鋳型に鋳造することの利点に関する実験結果を確認するために適用されました。
研究トピックと範囲:
- 本研究は、2つの亜鉛-アルミニウム犠牲陽極合金に焦点を当てました:ZSA1(Zn+(0.4-0.6%)Al)およびZSA2(Zn+(0.5-0.7%)Al+(0.1-0.3%Mg+0.1-0.3%Mn))。
- 初期鋳型(鋳鉄)温度(20℃、160℃、310℃)が凝固特性、微細構造、および電気化学的特性に及ぼす影響の調査。
- 一貫した注入前鋳型温度を維持するための鋳型加熱および冷却時間を考慮した鋳造サイクルの最適化。
- 異なる鋳型タイプでの鋳造性能の比較:砂質-粘土質(シャモット)、鋳鉄、および水冷鋼鋳型。
- 鋳造温度(450℃、500℃、550℃)および鋳型材料(非金属対金属)がCCおよび微細構造に及ぼす影響の評価。
- 凝固速度(Vs)がCCおよび微細構造に及ぼす影響の評価。
- 亜鉛トレッドの指向性凝固のための改良鋳型の設計と試験(Fig. 10)。
6. 主な結果:
主な結果:
- 初期鋳型温度の変動(例:シフト中の80℃から260℃、Fig. 1)は、ZSAの構造と電気化学的特性に大きな影響を与え、CCの低下(鋳型温度が20℃から300℃に変化すると96%から80%へ)を引き起こす可能性があります。
- 18kgの亜鉛合金トレッドの鋳造には、120-160℃の最適な初期鋳型温度が、93-96%の電流容量効率と815-820mV vs. SHEの腐食電位(-E)を保証し、鋳造サイクルは10-14分です。
- ZSAのマクロ構造は、皮質、柱状、および無配向の結晶ゾーンを示します。最も均一な微細粒構造は、初期鋳型温度が20℃および160℃で得られます(Fig. 2)。
- 熱除去の強度が凝固速度と特性を決定します。金属鋳型内のZSAトレッドの場合、完全凝固時間は異なりました:215秒(20℃鋳型)、255秒(160℃鋳型)、440秒(310℃鋳型)(Table 2)。
- 定常電位および分極時電位(3 A/m²)は凝固条件にほとんど依存しませんが、CCは影響を受けます:ZSA1の場合、CCは92-96%(20℃鋳型)、90-93%(160℃鋳型)、80-87%(310℃鋳型)でした(Table 3)。
- 定常状態の鋳造プロセスには、一定の初期鋳型温度を維持することが不可欠です。最適な総鋳造サイクル(tц)は、凝固/冷却時間(t1)と鋳型冷却時間(t2)のバランスによって達成されます(Fig. 6)。亜鉛トレッドには、120-160℃の鋳型温度が推奨されます。
- 鋳造温度を450℃から550℃に上げると、非金属(シャモット)および金属(鋳鉄)鋳型の両方で、ZSA1およびZSA2のCCが低下します。金属鋳型は一般的に高いCCを示します(Fig. 7)。
- 鋳造温度が高いほど、微細構造が粗くなり、第二相粒子が大きくなり、CCの低下と相関します(Fig. 8)。
- ZSA合金のCCは凝固速度(Vs)とともに増加します(Fig. 9)。ZSA1の回帰式:CC = 127-0,072tc(鋳造温度依存性)およびCC = 84,21 + 0,035 Vculing(凝固速度依存性)。
- 水冷ベース、断熱側壁、および遮熱スクリーンを備えた改良された鋳型設計(Fig. 10)は、指向性凝固を促進し、均一な結晶構造、滑らかな表面、収縮孔の排除、および96-98%のCCをもたらします。この設計により、鋳造サイクルは2-3分に短縮されます(Fig. 11)。
図の名称リスト:
- Figure 1. Change in mold temperature during the cast of ZSA
- Figure 2. Macrostructure of zinc sacrificial lloys under various conditions of solidification and cooling in-the form with initial temperature of form 20°C(a), 160°C(b) and 310°C(c)
- Figure 3. The scheme of installation of thermocouples for measure the temperature fields of a hardening alloy (1-5) and cast-iron forms (6-8)
- Figure 4. Temperature variation in the solidifying alloys and cast-iron mold at their height at a mold temperature of 20°C (I), 160° C(II), 310°C (III): a, b - cooling and heating curves, respectively; c, d - are the temperature fields in the solidifying alloy and the shape, respectively.
- Figure 5. Change in mass of metal under different cooling conditions at initial temperature of the mold 20(1), 160(2) and 310(3)°C
- Figure 6. Dependence of the cooling time of the casting in the form t1, cooling the mold to the set temperature t2 and the total casting cycle tц from the initial temperature of the mold.
- Figure 7. Influence of the casting temperature on the change of zinc alloys CC by casting into nonmetallic (a) and metallic forms (b)
- Figure 8. Microstructure (x100) of the ZSA1 (I, II, III) and ZSA2 (IV, V, VI) alloys when casting into nonmetallic and metallic (VII, VIII, IX) forms at the following casting temperatures: I, IV, VII - 450 °C; II, V, VII - 500 ° III, VI, IX - 550°C
- Figure 9. Change in CC and microstructure of ZSA1 (a) and ZSA2 (b) alloys depending on the speed of solidification(Vs)
- Figure 10. Construction of a mold for the production of zinc treads
- Figure 11. Changing the temperature of the cast tread when casting into a water-cooled mold 1-5 – the areas, where installed the thermocouples
7. 結論:
- 異なる冷却条件が、鋳造亜鉛犠牲陽極の断面全体の温度降下の変化につながり、それらの電気化学的特性を変化させることが示されています。
- インゴットの指向性凝固のための最良の条件は、より高い温度差(160℃以下の温度の鋳型での合金の凝固)で保証されます。
- 亜鉛インゴットの凝固の熱条件の調査により、強制冷却がない場合の亜鉛インゴットの充填および冷却を含む完全な鋳造サイクルの最小時間は、金属鋳型の初期温度180-200℃で達成されることが示されました。
- 金属鋳型はシフト中に何度もインゴットを製造するために使用されるため、鋳造プロセスを制御する重要な課題は、指向性ヒートシンクを備えた水冷形状に鋳造することによる強制冷却の使用を含め、次の注入前に温度を一定レベルに維持することです。
- 現在の結果は、陽極分極において最高の電流容量と安定した電位を達成することを可能にします。
8. 参考文献:
- [1] D.M. Stefanescu. Science and Engineering of Casting Solidification. 3rd ed. Springer International Publishing AG, Switzerland (2015) p.559.
- [2] J. Dantzig, M. Rappaz. Solidification. Taylor & Francis Group, CRS Press (2009) p.621
- [3] J. Campbell. Casting. 2nd ed. Butterworth-Heinemann, Elsevier (2003) p.335.
- [4] F. S. Yang, F. Ni. Effect of Cooling Rate on the Solidification of Zn-5wt%Al Alloy, Advanced Materials Research (2012) Vol. 366, pp. 502-505.
- [5] Krupiński, M., Krupińska, B., Labisz, K. et al. Influence of cooling rate on crystallization kinetics on microstructure of cast zinc alloys, Journal of Thermal Analysis and Calorimetry (2014), Volume 118, Issue 2, pp 1361–1367.
- [6] R.-N. Ma, Y.-Z. Fan, A. Du, P.-P. Zhang. Effect of cooling rate on morphology and corrosion resistance of Zn-Al-Mg alloy, Cailiao Rechuli Xuebao/Transactions of Materials and Heat Treatment. (2015) Vol. 36(4), pp. 49-55.
- [7] V.A. Kechin, E.Y. Lyublinski. New Sacrificial Anodic Alloys. NACE International, (2018) Paper C2018-11388.
- [8] Chris Jennings,. A comparison of the structure and Consumption Rate for Centrifugally Cast Anodes Compared with Die-Cast Anodes, NACE 2018, Phoenix, USA, Paper C2018-10954.
- [9] Efim Lyublinski, Vladimir Kechin. Formation of basic properties of galvanic anodes during the industrial production, EUROCORR 2017, Prague,Czhech Republic, Paper 72701.
- [10] A. Aghajani, M. Atapour, R. Alibek. Passivation of Zink Anodes in Marine Conditions. Materials Performance, Vol. 55. No. 9, p, 34.
- [11] V. Kechin, E. Lyublinski. New Sacrificial Anodic Alloys, EUROCORR 2016, Montpellier, France, Paper 0-6242.
- [12] V.A. Kechin. Theory and Technology of Cast Sacrificial Materials. Vladimir State University (2004) p. 181.
- [13] V.A. Kechin, E.Y. Lyublinski. Zinc Alloys. Moscow, Metallurgy (1986) p, 247.
- [14] V.A. Kechin , A.B.Kireev. Riser for the production of cast treads sacrificial anodes, Russian Patent Patent №2492020 (2013)
9. 著作権:
- この資料は、「Prof. Vladimir Kechin, Prof. Efim Lyublinski, Phd. Evgeny Prusov」による論文です。「THE ROLE OF THERMAL PROCESSES IN THE FORMATION OF GALVANIC ZINC ANODES PROPERTIES」に基づいています。
- 論文の出典: 論文に記載されていません。
この資料は上記の論文に基づいて要約されており、商業目的での無断使用は禁止されています。
Copyright © 2025 CASTMAN. All rights reserved.