この論文要約は、['Int J Adv Manuf Technol'] に発表された論文 ['高圧ダイカストによるアルミニウム自動車クラッチハウジング製造のための金型構造設計と鋳造シミュレーション'] に基づいて作成されています。
1. 概要:
- タイトル: 高圧ダイカストによるアルミニウム自動車クラッチハウジング製造のための金型構造設計と鋳造シミュレーション (Mold structure design and casting simulation of the high-pressure die casting for aluminum automotive clutch housing manufacturing)
- 著者: 鄭 聖一, 陳 哲奎, 徐 亨允, 金 鍾德, 姜 忠吉 (Seong Il Jeong, Chul Kyu Jin, Hyung Yoon Seo, Jong Deok Kim, Chung Gil Kang)
- 出版年: 2015年
- 出版ジャーナル/学会: Int J Adv Manuf Technol
- キーワード: 高圧ダイカスト, 金型構造, 鋳造シミュレーション, 鋳造欠陥, アルミニウム合金 (High-pressure die casting, Mold structure, Casting simulation, Casting defects, Aluminum alloy)
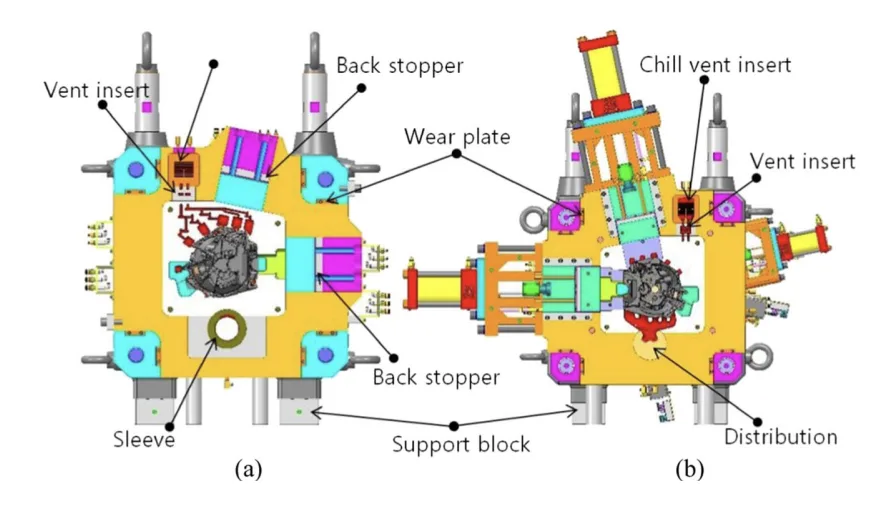
2. 研究背景:
研究テーマの背景:
1915年に Doeher die-casting co がアルミニウム合金を用いたダイカスト製品の製造を開始して以来、特に自動車産業の発展に伴い、ダイカスト製品の需要は着実に増加しています [1]。アルミニウム自動車部品の鋳造方法の中でも、高圧ダイカスト (HPDC)、重力ダイカスト、低圧ダイカストが最も一般的に用いられています。低圧ダイカストと重力ダイカストは、シリンダーヘッドのように内部構造が複雑な自動車部品に適用できますが、HPDC は、従来、低圧または重力鋳造法で製造されていた軽量自動車部品の大量生産に徐々に適用され始めています [2-7]。HPDC は、数十秒から 100~180 秒の短時間で複雑かつ精密な形状を大量生産できるという利点があります。
既存研究の現状:
従来、ダイカスト金型の設計は、金型設計者と現場技術者の試行錯誤法に依存する傾向がありました。しかし、高圧ダイカスト金型の設計プロセスは、コンピュータ支援エンジニアリング (CAE) を採用し、初期開発段階から充填および凝固プロセスシミュレーションを取り入れています。この CAE ベースのアプローチにより、品質予測と評価が可能になり、最適化された金型設計が確立されます [5, 8-10]。今日、多くの設計者が CAE と実務経験を組み合わせた金型設計手法を採用し、不良率を低減し、コストを削減し、開発期間を短縮しています。さらに、金型の固着や変形を予測できるため、金型の構造設計にも非常に役立ちます。
研究の必要性:
本研究は、特にクラッチハウジングのような複雑な自動車部品の HPDC において、堅牢な金型設計の必要性を強調しています。本研究では、充填および凝固段階で発生する可能性のある潜在的な鋳造欠陥を予測および軽減するために、鋳造シミュレーションの適用を重視しています。また、最小限の鋳造欠陥で最適化された品質の製品を製造することを目的として、ゲートシステムの設計と製品形状の最適化を目指し、金型設計段階から潜在的な金型損傷を予測し、実験回数を最小限に抑えることで、製造コストと時間を削減するために、金型ベースの構造シミュレーションを実施します。
3. 研究目的と研究課題:
研究目的:
本研究の目的は、高圧ダイカストプロセスにおいてアルミニウム自動車クラッチハウジング部品を製造するための金型設計を開発することです。これは、効率的で欠陥のない生産を保証するために、鋳造シミュレーションと金型構造シミュレーションを通じて達成されます。
主要な研究課題:
- 溶融金属が金型に流れ込み、製品セクションを均一に充填するように、5つのゲートを備えたゲートシステムを設計する方法は何か?
- 充填プロセスおよび凝固プロセスで発生する可能性のある鋳造欠陥の可能性を予測または防止するために、鋳造シミュレーションプログラムである MAGMAsoft を使用する方法は何か?
- クラッチハウジング製品の製造に適した鋳造装置を選定する方法は何か?
- 金型設計段階から脆弱な金型部分への潜在的な損傷を予測するために、ANSYS Workbench を使用して金型ベースの構造シミュレーションを実施する方法は何か?
研究仮説:
明示的に仮説として述べられてはいませんが、本研究は以下の前提の下に進められています。
- 鋳造解析と構造解析の両方を組み込んだシミュレーションベースの金型設計は、鋳造欠陥を最小限に抑えたアルミニウム自動車クラッチハウジングを製造できる堅牢な金型を作成するだろう。
- シミュレーション結果に基づいて最適化されたゲートシステム設計と金型構造は、製品品質を向上させ、製造コストと時間を削減するだろう。
4. 研究方法
研究デザイン:
本研究では、鋳造シミュレーションと構造シミュレーションを統合したシミュレーションベースの設計手法を採用し、実際のショットテストによる実験的検証を実施します。
データ収集方法:
- 鋳造シミュレーション: MAGMAsoft を活用して、充填および凝固プロセスをシミュレーションし、潜在的な鋳造欠陥を予測しました。
- 構造シミュレーション: ANSYS Workbench を使用して、金型ベースの構造解析を実施し、潜在的な損傷を予測しました。
- 実験的検証: 実際のショットテストを実施し、5 つのクラッチハウジング製品を製造しました。鋳造後の分析には、表面欠陥の目視検査、引け巣評価、ビッカース硬さ測定が含まれていました。
- 温度測定: 予熱および鋳造中の金型温度を非接触式熱画像カメラを使用して測定しました。
分析方法:
- シミュレーション分析: MAGMAsoft シミュレーション結果を分析して、ゲートシステムを最適化し、引け巣などの鋳造欠陥を予測しました。ANSYS Workbench の結果を分析して、金型ベース構造を最適化し、構造的完全性を確保しました。
- 実験データ分析: MAGMAsoft で予測された引け巣の位置と、ショットテストサンプルで観察された実際の引け巣を比較しました。鋳造部品の表面品質を評価しました。クラッチハウジングのさまざまな位置でビッカース硬さを測定し、分析しました。シミュレーションされた金型温度分布と熱画像測定値を比較しました。
研究対象と範囲:
本研究は、高圧ダイカストによって製造されるアルミニウム自動車クラッチハウジングの金型設計と製造プロセスに焦点を当てています。範囲は以下を含みます。
- アルミニウム自動車クラッチハウジングの HPDC 用金型設計。
- 充填および凝固を含む鋳造プロセスのシミュレーション。
- 金型ベースの構造シミュレーション。
- ショットテストおよびクラッチハウジング製品の鋳造後分析による実験的検証。
- 材料: クラッチハウジング用 ALDC12 アルミニウム合金、金型ベース用 GCD500 ダクタイル鋳鉄。
5. 主な研究結果:
主要な研究結果:
- ゲートシステム設計: 5 ゲートゲートシステムは、溶融金属の均一な流れとクラッチハウジング金型キャビティの完全な充填を促進するように、首尾よく設計されました (Fig. 1)。
- 鋳造シミュレーションと欠陥予測: MAGMAsoft シミュレーションは、鋳造内の引け巣の可能性を効果的に予測しました。予測された引け巣の位置は、製造された部品で観察された実際の発生位置と密接な相関関係を示しました。
- 金型構造シミュレーションと最適化: ANSYS Workbench を使用した構造シミュレーションは、金型ベースの厚さを最適化する上で非常に重要でした。23 cm の金型ベース厚さが、追加の支持なしでも十分であり安全であることが判明しました (Fig. 7d)。
- ショットテスト検証: 実際のショットテストでは、5 つのアルミニウムクラッチハウジング部品が首尾よく製造されました。すべての部品は完全に充填され、表面欠陥は見られませんでした。製造されたクラッチハウジングの硬度は、場所に関係なく約 84 HV で一貫して測定されました。
- 温度分布解析: 熱画像カメラを使用した温度測定の結果、鋳造シミュレーションで予測された温度分布と妥当な一致が見られました (Fig. 15)。
データ解釈:
結果は、シミュレーション予測と実験結果の間に強い相関関係があることを示しています。鋳造シミュレーションは、潜在的な引け巣領域を正確に特定し、構造シミュレーションは、金型ベースの厚さの最適化を効果的に導きました。欠陥のないクラッチハウジングを製造した成功したショットテストは、本研究で採用されたシミュレーションベースの金型設計アプローチの有効性を検証しています。部品全体で一貫した硬度値は、プロセス安定性と製品の均一性を示しています。
図のリスト:
- Fig. 1 クラッチハウジングのゲートシステム設計 (Gating system design of clutch housing)
- Fig. 2 3D 金型モデリング: a 固定金型と b 可動金型 (3D mold modeling: a fixed mold and b movable mold)
- Fig. 3 金型冷却ライン (Cooling line of mold)
- Fig. 4 可動金型の各象限における締結力 (Locking force in each quadrant of movable mold)
- Fig. 5 構造解析のための可動金型ベースの形状条件 (Shape condition of movable mold base for structural analysis)
- Fig. 6 組み立てられた高圧ダイカストマシン金型: a 固定金型と b 可動金型 (Molds assembled high-pressure die casting machine: a fixed mold and b movable mold)
- Fig. 7 可動金型ベースの構造解析結果: a h=20 cm, b h=22 cm, c h=24 cm, および d h=23 cm (Results of structural analysis for movable mold base: a h=20 cm, b h=22 cm, c h=24 cm, and d h=23 cm)
- Fig. 8 金型キャビティ内の充填挙動 (Filling behavior in mold cavity)
- Fig. 9 金型キャビティ内の空気圧とエア巻き込み (Air pressure and air entrapment in mold cavity)
- Fig. 10 金型キャビティ内の速度分布 (Velocity distribution in mold cavity)
- Fig. 11 充填完了後の金型キャビティ内の凝固挙動 (Solidification behavior in mold cavity after filling finish)
- Fig. 12 凝固完了後の引け巣 (Shrinkage porosity after solidification finish)
- Fig. 13 凝固完了後の金型半田付け: a 固定金型と b 可動金型 (Mold soldering after solidification finish: a fixed mold and b movable mold)
- Fig. 14 予熱後の金型温度分布 (熱画像カメラで測定): a 固定金型と b 可動金型 (Temperature distribution of molds after pre-heating measured by thermo-graphic camera: a fixed mold and b movable mold)
- Fig. 15 シミュレーションと実ショットテスト間の金型温度の比較: a シミュレーション結果と b 実ショットテスト (Comparison of mold temperature between simulation and real shot test: a simulation result and b real shot test)
- Fig. 16 製造されたクラッチハウジング鋳物: a 1 ショット目, b 2 ショット目, c 3 ショット目, d 4 ショット目, および e 5 ショット目 (Fabricated clutch housing castings: a first shot, b second shot, c third shot, d fourth shot, and e fifth shot)
- Fig. 17 シミュレーションと実ショットテスト間の気孔率分布の比較 (Comparison of porosity distribution between simulation and real shot test)
- Fig. 18 異なる位置におけるクラッチハウジングの微細構造: a 通常の厚さと b 厚い厚さ (Microstructures of clutch housing in different positions: a normal thickness and b thick thickness)
- Fig. 19 異なる位置におけるビッカース硬さ (Vickers hardness at different positions)
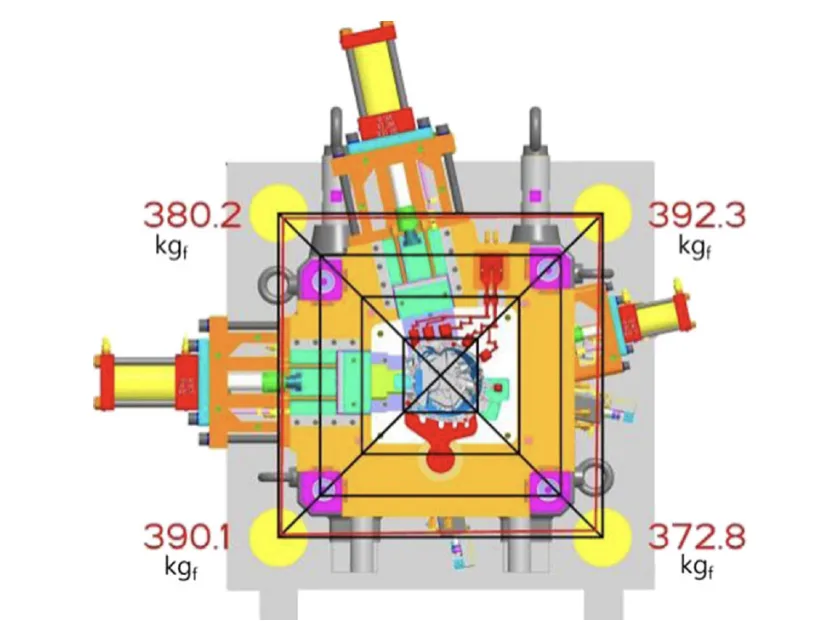
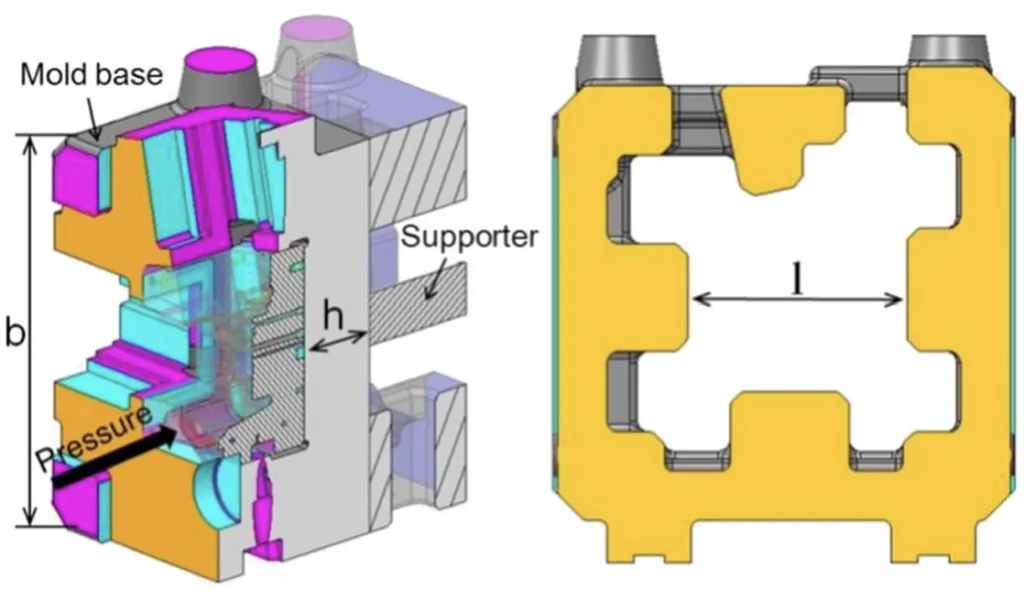
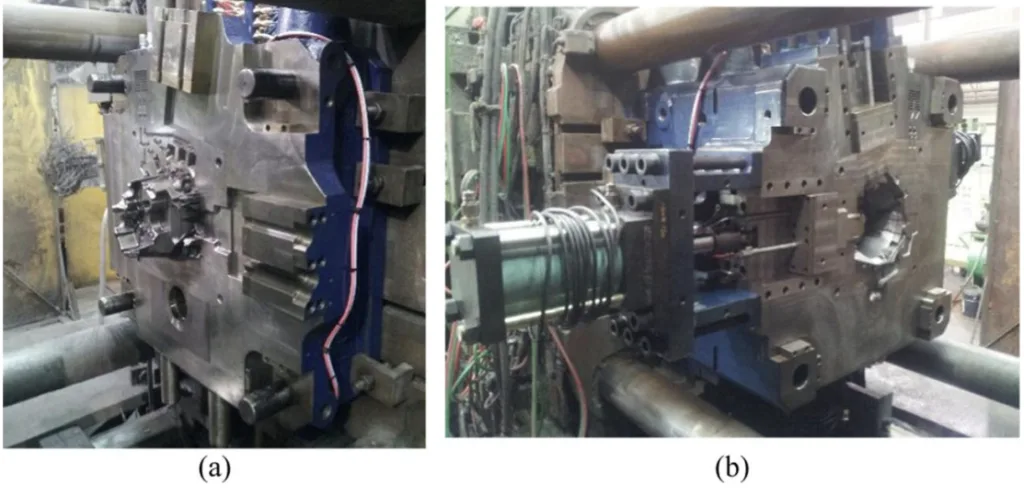
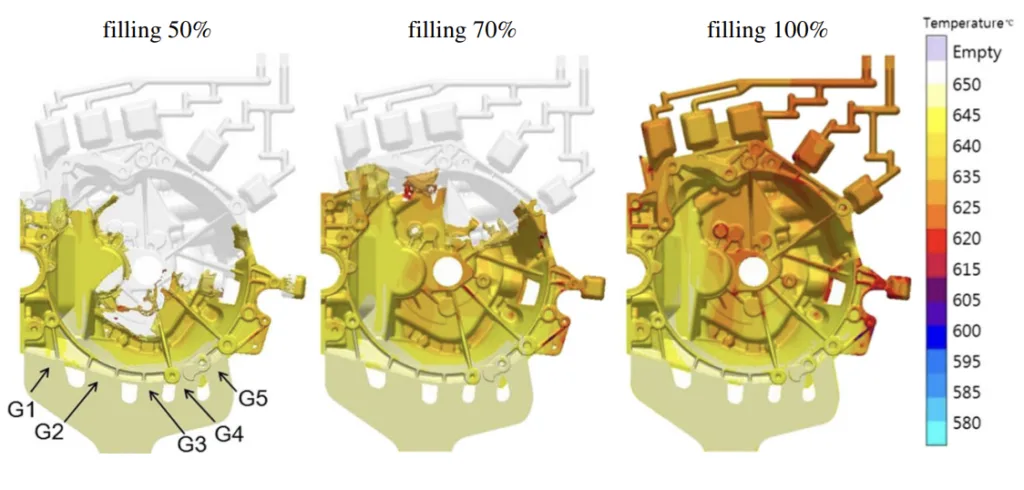
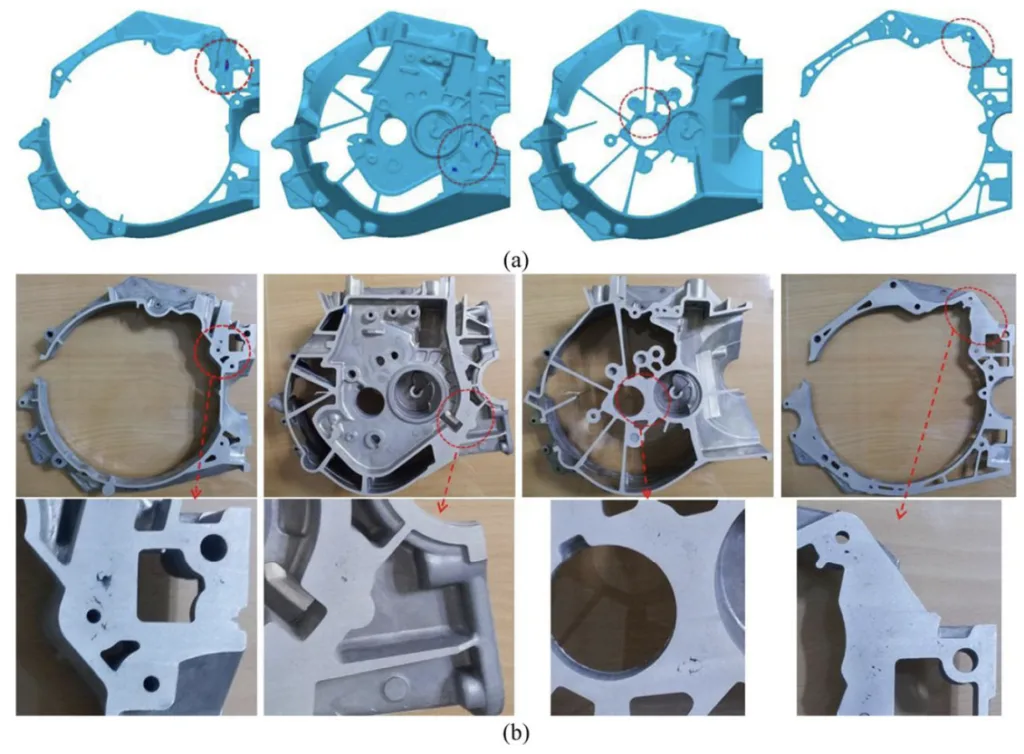
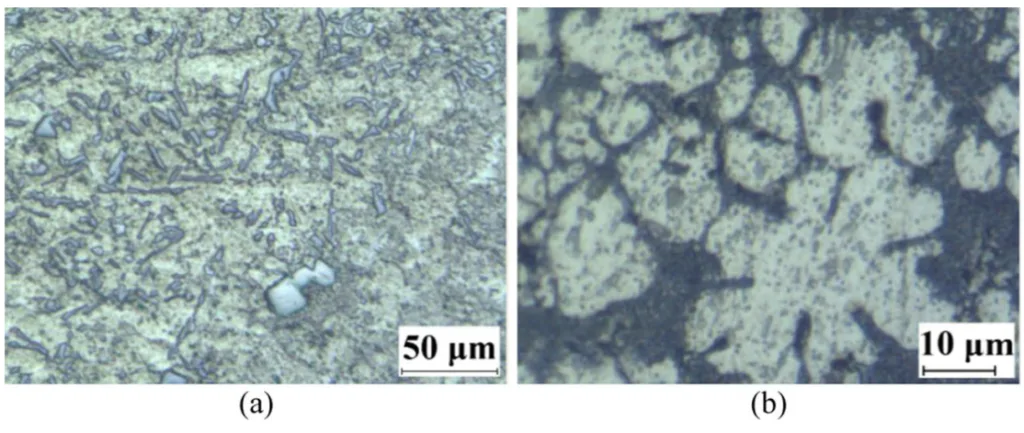
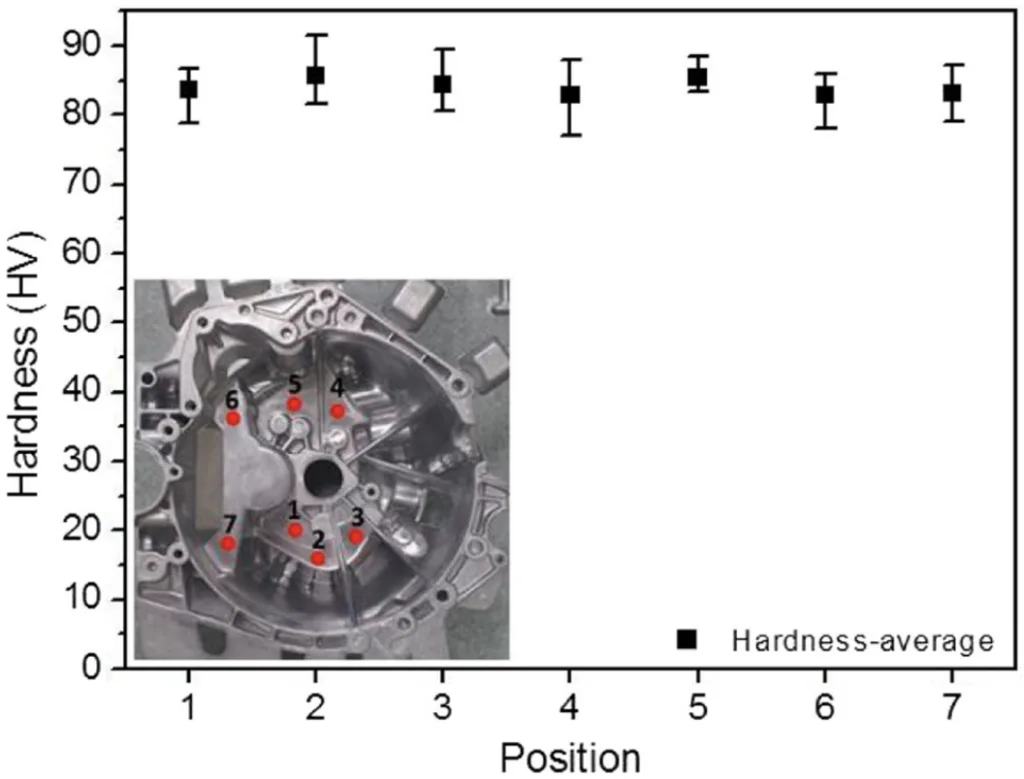
6. 結論:
主な結果の要約:
本研究では、アルミニウム自動車クラッチハウジングの高圧ダイカストのための金型設計へのシミュレーションベースのアプローチを首尾よく実証しました。MAGMAsoft と ANSYS Workbench をそれぞれ使用して鋳造シミュレーションと構造シミュレーションを統合することにより、5 ゲートゲートシステムと 23 cm 厚の金型ベースを最適化しました。ショットテストによる実験的検証により、シミュレーション予測が確認され、一貫した硬度を持つ欠陥のないクラッチハウジングの製造につながりました。
研究の学術的意義:
本研究は、ダイカスト金型設計における CAE ツールの使用の学術的意義を強調しています。複雑な HPDC 部品用の金型を設計するための詳細で検証済みの方法論を提供します。本研究は、鋳造欠陥予測、HPDC 条件下での金型構造挙動、および製造プロセスにおけるシミュレーションベースの最適化の有効性に関する知識体系に貢献します。
実用的な意義:
本研究の実用的な意義は、ダイカスト業界にとって非常に大きいです。提示された方法論は、コストがかかり時間がかかる試行錯誤のアプローチへの依存を最小限に抑えながら、複雑な自動車部品用の堅牢な金型を設計するための道筋を提供します。鋳造シミュレーションと構造シミュレーションを活用することで、製造業者は生産コストを削減し、開発サイクルを短縮し、HPDC 部品の品質と信頼性を向上させることができます。
研究の限界
本研究の限界には、単一の部品 (クラッチハウジング) と材料 (ALDC12) に焦点を当てていることが含まれます。方法論は堅牢ですが、大幅に異なる部品形状または合金システムへの直接的な一般化には、さらなる調査が必要です。また、引け巣予測は妥当な精度でしたが、シミュレーションされた位置と実際の位置との間の不一致は、シミュレーションモデルの改良または将来の研究における追加の影響要因の考慮が必要な領域を示唆しています。
7. 今後のフォローアップ研究:
- 今後のフォローアップ研究の方向性
今後の研究は、特に引け巣の正確な位置と範囲に関して、欠陥予測の精度を高めるためにシミュレーションモデルを改良することに焦点を当てる必要があります。射出速度プロファイルや冷却戦略などのさまざまなプロセスパラメータや、鋳造品質に対する材料のばらつきの影響に関する追加調査が必要です。 - さらなる探求が必要な領域
さらなる探求が必要な領域には、本研究で予測されましたが、実験的に広範囲に検証されていない金型侵食および金型固着現象に関するより詳細な分析が含まれます。開発された方法論を、より広範囲の複雑な HPDC 部品とさまざまなアルミニウム合金に適用することで、その汎用性と産業的適用性をさらに検証することができます。
8. 参考文献:
- [1] Doehler die-casting co (1916) Creating and industry. Brooklyn, New York
- [2] Jin CK, Bae JW, Kang CG (2014) Development of rheology vacuum low-pressure die casting with electromagnetic stirrer and vacuum system. Proc IMechE Part B J Eng Manuf 228(12):1599-1610
- [3] Zhang L, Wang R (2013) An intelligent system for low-pressure die-cast process parameters optimization. Int J Adv Manuf Technol 65:517-524
- [4] Hsu FY, Jolly MR, Campbell J (2009) A multiple-gate runner system for gravity casting. J Mater Process Technol 209:5736–5750
- [5] Jin CK, Kang CG (2011) Fabrication process analysis and experimental verification for aluminum bipolar plates in fuel cells by vacuum die-casting. J Power Sources 196:8241-8249
- [6] Kim ES, Lee KH, Moon YH (2000) A feasibility study of the partial squeeze and vacuum die casting process. J Mater Process Technol 105:42-48
- [7] Jin CK, Kang CG (2012) Fabrication by vacuum die casting and simulation of aluminum bipolar plates with micro-channels on both sides for proton exchange membrane (PEM) fuel cells. Int J Hydrog Energy 37:1661-1676
- [8] Chang QM, Chen CJ, Zhang SC, Schwam D, Wallace JF (2010) Effects of process parameters on quality of squeeze casting A356 alloy. Int J Cast Met Res 23:30-36
- [9] Hu BH, Tong KK, Niu XP, Pinwill I (2000) Design and optimisation of runner and gating systems for the die casting of thin-walled magnesium telecommunication parts through numerical simulation. J Mater Process Technol 105:128-133
- [10] Chen JH, Hwang WS, Wu CH, Lu SS (2011) Design of die casting process of top cover of automobile generator through numerical simulations and its experimental validation. Int J Cast Met Res 24:163-169
- [11] Jang JCH (1994) Casting plan of aluminum die castings. J Korean Foundry Soc 14(4):294-304
- [12] Kim ES, Lee KH (1998) High casting technology for aluminum alloy die casting (I). J Korean Foundry Soc 18(3):211-221
9. 著作権:
- この資料は、"鄭 聖一, 陳 哲奎, 徐 亨允, 金 鍾德, 姜 忠吉" の論文: "高圧ダイカストによるアルミニウム自動車クラッチハウジング製造のための金型構造設計と鋳造シミュレーション" に基づいています。
- 論文ソース: https://doi.org/10.1007/s00170-015-7566-4
この資料は上記の論文を要約したものであり、商業目的での無断使用は禁止されています。
Copyright © 2025 CASTMAN. All rights reserved.