論文概要:
この論文の紹介文は、['埼玉大学'が発行した ['Effects of Casting Defects on Mechanical Properties of Aluminum Alloy Die-Casts'] という論文に基づいて作成されました。
1. 概要:
- タイトル: アルミニウム合金ダイカストの機械的性質に及ぼす鋳造欠陥の影響 (Effects of Casting Defects on Mechanical Properties of Aluminum Alloy Die-Casts)
- 著者: A.K.M. アジズ アハメド (A.K.M. Aziz Ahamed)
- 発行年: 2008年3月
- 発行学術誌/学会: 埼玉大学大学院理工学研究科 (Graduate School of Science and Engineering, Saitama University)
- キーワード: 論文に明記されていません。
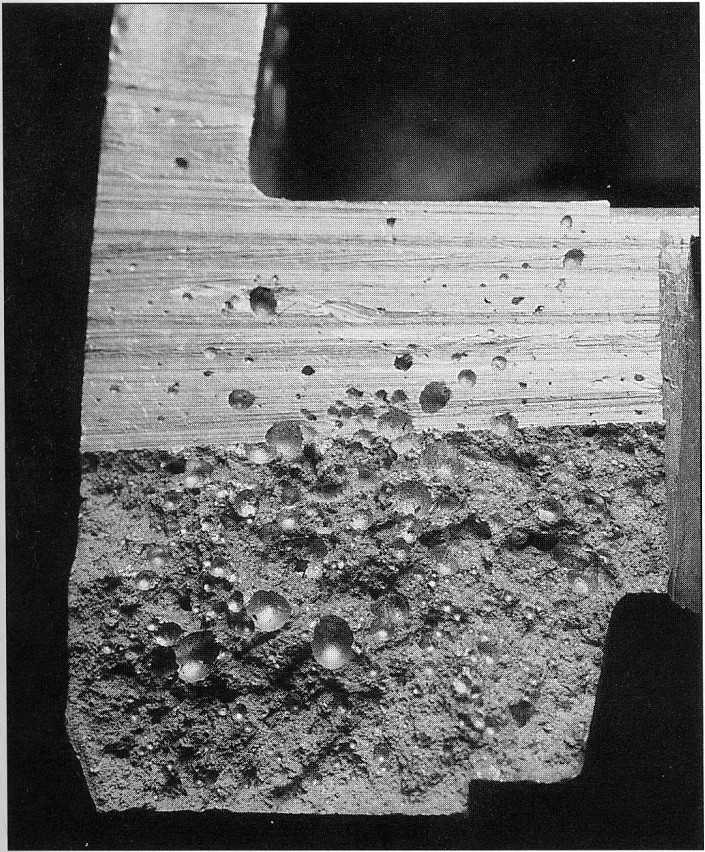
2. 抄録または序論
第1章では、ダイカスト合金の重要性と欠陥、音響顕微鏡技術の開発、非破壊評価、および本論文の目的を紹介しています。アルミニウム合金は、軽量特性により、自動車、航空宇宙、輸送産業で認められている金属です。高圧ダイカストは、最小限の機械加工で複雑な形状を製造する費用対効果の高い方法です。自動車産業は、自動車のトランスミッションハウジングやシリンダーヘッドなどの部品製造に、強力な地域アルミニウムダイカスト産業を活用しています。ダイカストは、高い初期設備投資にもかかわらず、厳しい公差と迅速な生産速度を提供する、大量精密鋳造に最も効率的なプロセスです。
自動車用アルミニウム合金鋳物の欠陥は、製品の品質と生産コストがますます重視されるようになるにつれて、冶金学者や生産技術者にとって依然として課題となっています。アルミニウム合金ダイカストは、自動車製品において繰り返し荷重と熱サイクルにさらされて使用されます。したがって、信頼性が重要であり、機械的特性に影響を与える要因を認識し、保証する必要があります。多孔性 [1.1-1.7]、引け巣 [1.8-1.9]、酸化物介在物 [1.10-1.12]、微細組織 [1.13-1.15]、その他の鋳造欠陥 [1.16-1.25] がダイカストの引張特性および疲労特性に及ぼす影響に関する研究が行われてきました。
鋳造欠陥の中でも、不規則な構造であるコールドフレーク [1.21-1.25] の影響に関心が集中しています。コールドフレークは、溶融金属を射出スリーブに注入し、プランジャーで押し出す際に、初期に凝固した溶融層が鋳造中に小さな破片に砕けて生成されます。これらの小さな破片はコールドフレークと呼ばれ、一般的に酸化物層で覆われています。酸化物層は、多くの場合、潤滑剤や気孔 [1.26] によって汚染され、母材との濡れ性を低下させます。したがって、ダイカスト合金の機械的特性と信頼性は、コールドフレークの量によって低下します [1.27]。コールドフレークを除去するための多くの研究が行われてきましたが、製造技術 [1.28] が進歩しても、ダイカスト製品からコールドフレークを完全に取り除くことは達成されていません。非破壊評価は、鋳造製品 [1.29] の欠陥を調査するためにも使用されています。
3. 研究背景:
研究テーマの背景:
アルミニウム合金ダイカストは、軽量かつ複雑な形状の部品を費用対効果よく製造できるため、自動車部品に広く使用されています。しかし、鋳造欠陥、特にコールドフレークは、自動車用途で繰り返し荷重と熱サイクルを受けるこれらの部品の機械的特性と信頼性に大きな影響を与えます。
既存研究の現状:
既存の研究では、多孔性 [1.1-1.7]、引け巣 [1.8-1.9]、酸化物介在物 [1.10-1.12]、微細組織 [1.13-1.15]、その他の鋳造欠陥 [1.16-1.25] など、さまざまな鋳造欠陥と、それらがダイカストの引張特性および疲労特性に及ぼす影響に焦点が当てられてきました。これらの欠陥の中でも、コールドフレーク [1.21-1.25] は重大な欠陥として認識されています。非破壊評価法は、これらの欠陥を検出するために用いられていますが [1.29]、コールドフレークを完全に除去することは依然として課題です [1.28]。
研究の必要性:
鋳造欠陥に関する数多くの研究にもかかわらず、アルミニウムダイカストの機械的特性に及ぼすコールドフレークの影響、特に非破壊検出とサイズおよび位置の評価に関する影響については、さらなる調査が必要です。特にコールドフレークからの亀裂の発生と伝播に関して、ダイカスト部品の信頼性を確保するための効果的な評価方法が必要です。
4. 研究目的と研究課題:
研究目的:
本論文の目的は、鋳造欠陥、特にコールドフレークがアルミニウム合金ダイカストの機械的特性に及ぼす影響を評価することです。これには、コールドフレークを検出および特性評価するための効果的な超音波法を開発し、引張特性および疲労特性に及ぼす影響を調査し、これらの欠陥からの亀裂の発生と伝播を評価することが含まれます。
主要な研究内容:
- コールドフレークの調査による超音波測定による亀裂開口検出法の開発。
- コールドフレークのサイズと位置が異なるADC12の引張特性の測定。
- コールドフレークのサイズと位置が異なるADC12の疲労特性の調査。
- 音響顕微鏡技術と局所浸漬超音波法を用いた欠陥のサイズと位置の評価。
- 音響顕微鏡と超音波測定を用いたコールドフレークからの亀裂発生の観察。
- 線形弾性破壊力学的手法を用いたADC12合金の破壊基準の検討。
- コールドフレークの領域、サイズ、形状、および方向による疲労特性の調査、および疲労試験中のコールドフレークからの亀裂発生と伝播の決定、およびプロセス内超音波測定による不安定な亀裂伝播の調査。
研究仮説:
論文では研究仮説は明示的に述べられていません。
5. 研究方法
研究デザイン:
本研究では、以下の実験計画法を採用しました。
- 超音波試験と音響顕微鏡検査(SAM): アルミニウム合金ダイカスト板(ADC12)中のコールドフレークを検出し、可視化します。
- 引張試験: ADC12合金の引張強度に及ぼすコールドフレークの影響を評価します。
- 曲げ試験: 曲げ条件下でのコールドフレークからの亀裂発生と伝播を観察します。
- 疲労試験: ADC12合金の疲労特性に及ぼすコールドフレークの影響を調査します。
- プロセス内超音波測定: 引張試験および疲労試験中にコールドフレークからの亀裂開口と伝播をモニタリングします。
データ収集方法:
- 音響顕微鏡検査(SAM): ダイカスト板内部のコールドフレークの高解像度画像を取得するために使用されました。画像取得条件は、ゲイン-60 dB、ゲート-0.075 μm、Fトリガー-50 %に設定されました。
- 超音波測定: 20 MHzの縦波を生成するトランスデューサを使用して、コールドフレークと亀裂伝播を検出およびモニタリングしました。
- 引張試験: 引張強度を測定するために、クロスヘッド速度0.5 mm/minの試験機を使用して実施しました。破断荷重(Pf)と初期断面積(A0)を記録しました。
- 疲労試験: S-N曲線と疲労寿命データを得るために、応力比R= 0.05(引張-引張タイプ)および周波数10 MHzで実施しました。
- 破面解析: 破断面を光学顕微鏡および走査型電子顕微鏡(SEM)を使用して観察し、亀裂発生位置と伝播経路を分析しました。
分析方法:
- 音響画像解析: AVSソフトウェアを使用して、3次元コールドフレークの可視化のために間隔音響画像を結合しました。
- 応力拡大係数解析: 線形弾性破壊力学的手法を用いて、村上ら [3.12,3.13]、ニューマンら [3.14,3.15]、石田ら [3.16] の式を用いて、破壊時の臨界応力拡大係数(Kc)を評価しました。
- S-N曲線解析: 疲労試験データを用いて、コールドフレークを有するADC12合金の疲労寿命を評価するためにS-N曲線を作成しました。
- 破面解析: SEM破断面画像を分析して、コールドフレークに関連する亀裂発生点と伝播メカニズムを特定しました。
研究対象と範囲:
- 材料: アルミニウム合金ダイカスト板(ADC12、公称組成 Al-11 mass% Si-2.5 mass% Cu)。
- 欠陥: コールドフレーク、サイズ、位置(内包型、露出型)、および荷重方向に対する配向によって特徴付けられます。
- 試験片: 引張試験、曲げ試験、および疲労試験用に、制御されたコールドフレークのサイズと位置でダイカスト板から機械加工された長方形の試験片。
- 範囲: ADC12合金の引張強度、疲労寿命、および亀裂伝播に対するコールドフレークの影響の調査。コールドフレークの非破壊評価のための超音波および音響顕微鏡技術の開発と応用。
6. 主な研究成果:
主要な研究成果:
- 亀裂開口の超音波検出: コールドフレークからの亀裂開口を検出するために、ウォーターバッグを用いた局所浸漬超音波法を開発しました。音響顕微鏡検査(SAM)は、コールドフレークを明るい部分として効果的に可視化しました。引張試験中のプロセス内超音波測定では、コールドフレークから反射された波形の位相変化が示され、亀裂の発生と伝播を示唆しました。
- 鋳造欠陥が引張強度に及ぼす影響: ADC12合金の引張強度は、コールドフレークの酸化物層面積の増加とともに線形的に減少しました。引張方向に対して垂直に露出したコールドフレークは、内包型コールドフレークと比較して引張強度を大幅に低下させました。引張方向と平行な酸化物層は、最小限の影響しか与えませんでした。臨界応力拡大係数(Kc*)を評価し、酸化物層面積への依存性を示しました。
- コールドフレークが疲労特性に及ぼす影響: ADC12合金の疲労寿命は、コールドフレークによって大きく影響を受け、コールドフレークのサイズと位置のばらつきにより、S-N曲線に大きなばらつきが見られました。疲労寿命は、コールドフレーク面積の増加とともに減少しました。荷重方向に対して垂直に露出したコールドフレークは、内包型コールドフレークよりも疲労寿命に悪影響を及ぼしました。プロセス内超音波測定により、疲労プロセス中にコールドフレークが剥離し、亀裂が形成されることが確認されました。疲労亀裂サイズから評価された最大応力拡大係数(KImax)は、引張試験の結果と一致していました。
提示されたデータの分析:
- 引張強度の低下: コールドフレーク、特に露出したフレークの存在は、応力集中部として機能し、早期破壊と引張強度の低下につながります。コールドフレークを囲む酸化物層のサイズは、引張強度低下の程度と直接相関しています。
- 亀裂の発生と伝播: コールドフレーク、特に酸化物層を有するコールドフレークは、引張荷重と疲労荷重の両方において、亀裂発生の優先的な位置として機能します。超音波測定は、これらの欠陥からの亀裂開口と伝播を効果的に追跡しました。
- 疲労寿命の低下: コールドフレークは、疲労寿命を大幅に短縮します。S-N曲線は大きなばらつきを示しており、欠陥特性の変動性と疲労性能への影響を強調しています。露出したコールドフレークの構成は、内包型コールドフレークよりも疲労においてより重要です。
- 破壊力学解析: 線形弾性破壊力学は、応力拡大係数アプローチを使用することで、応力-ひずみ曲線で観察されたいくつかの非線形性にもかかわらず、コールドフレークを含むダイカストの破壊挙動を特徴付けるための妥当なフレームワークを提供します。
図のリスト:
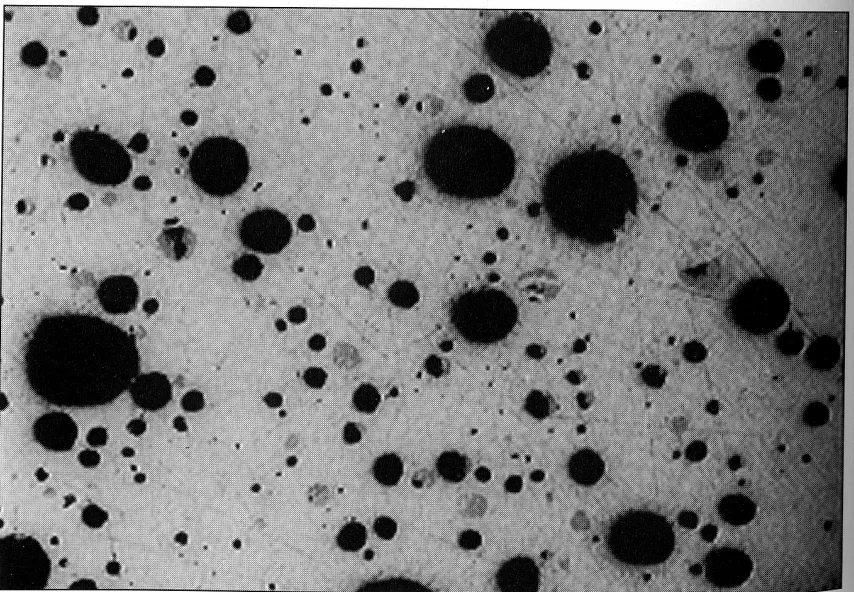
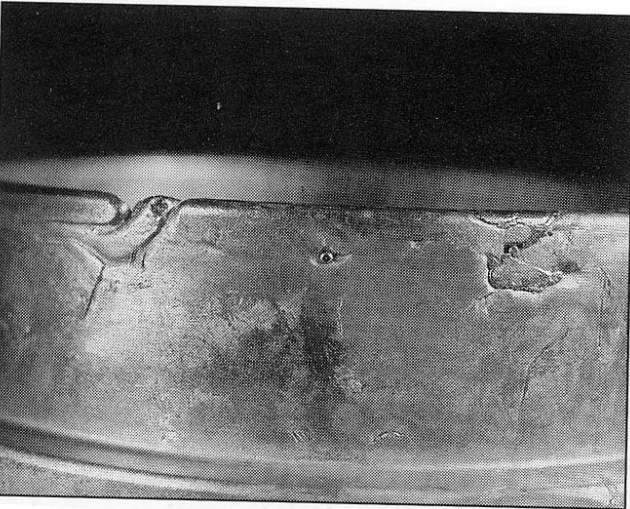
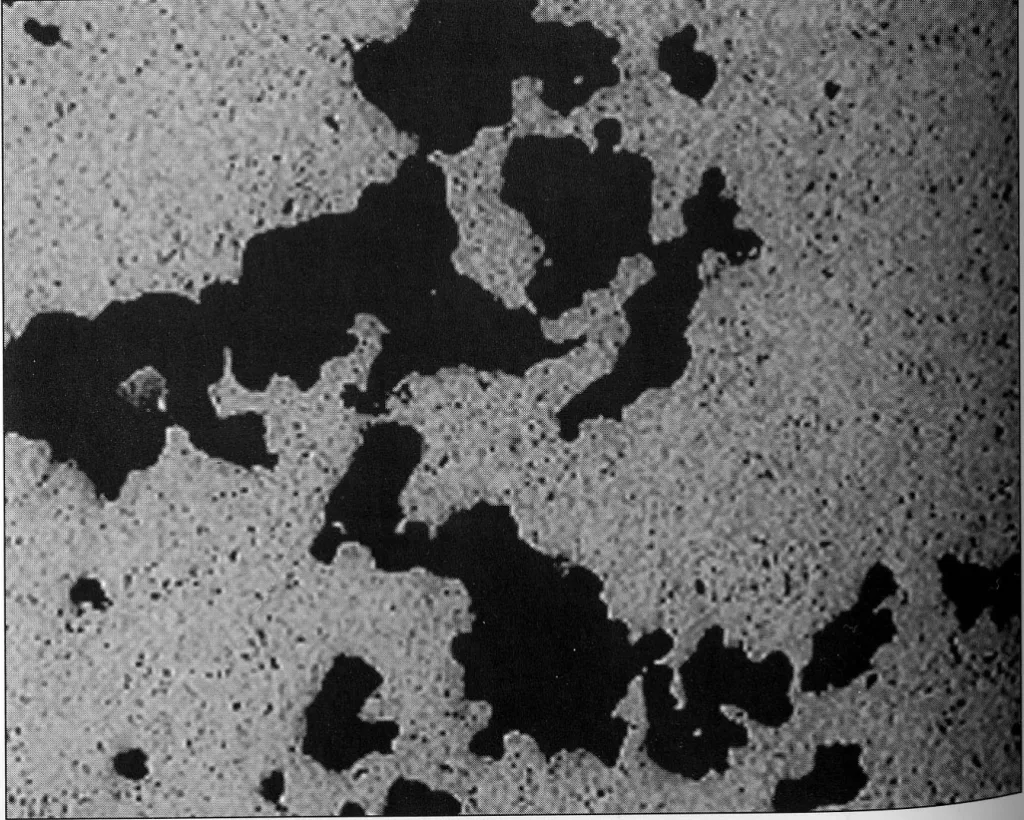
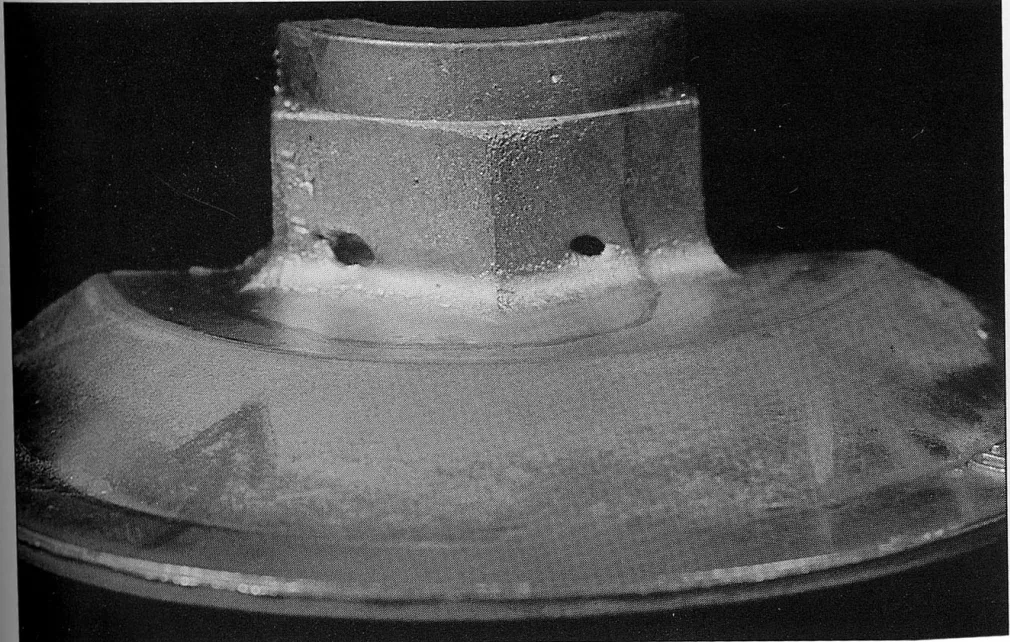
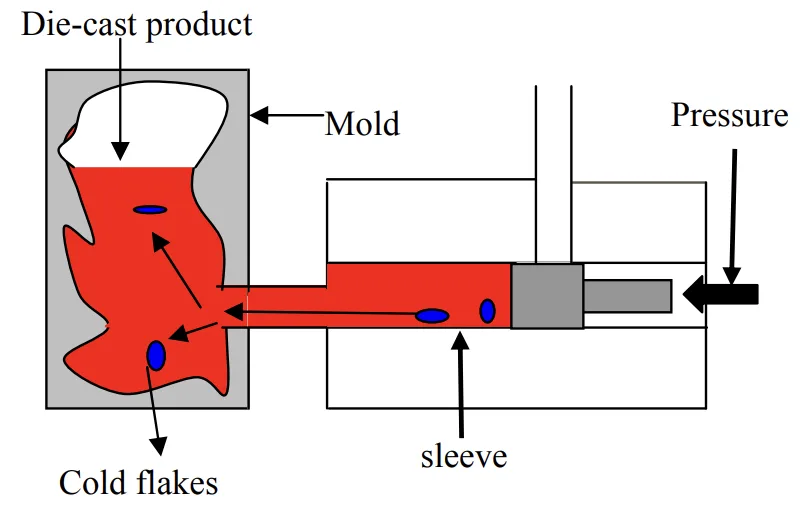
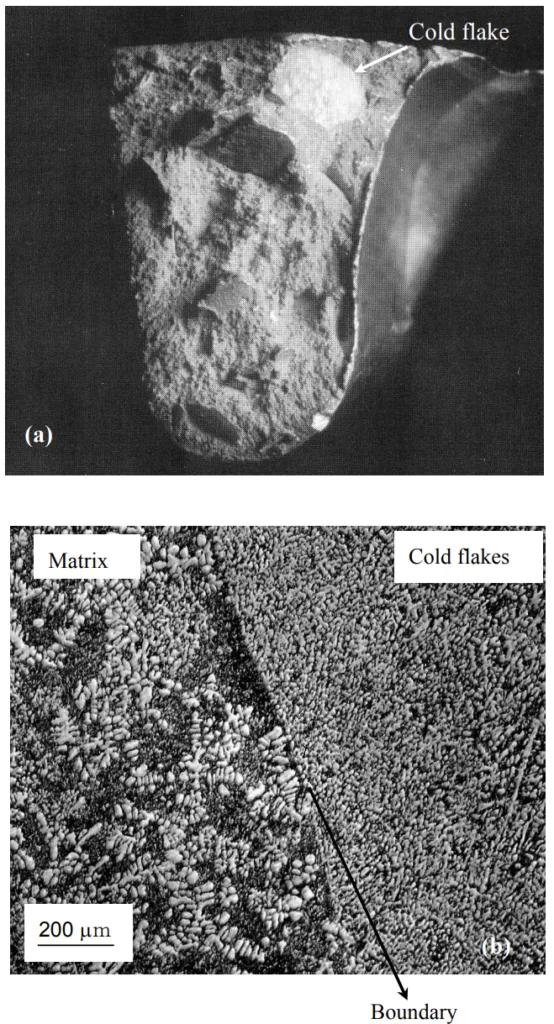
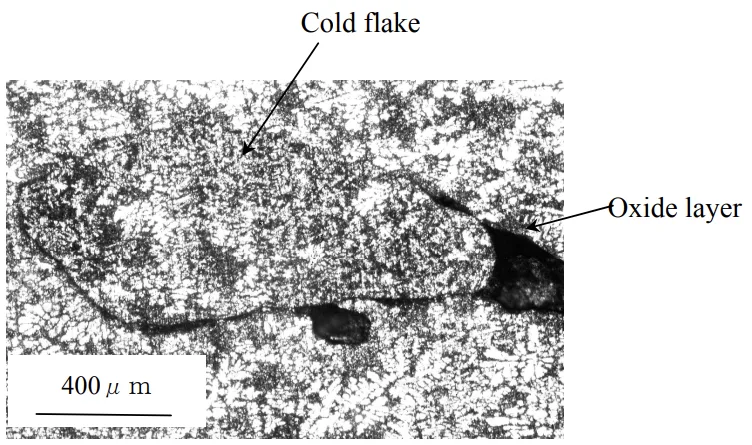

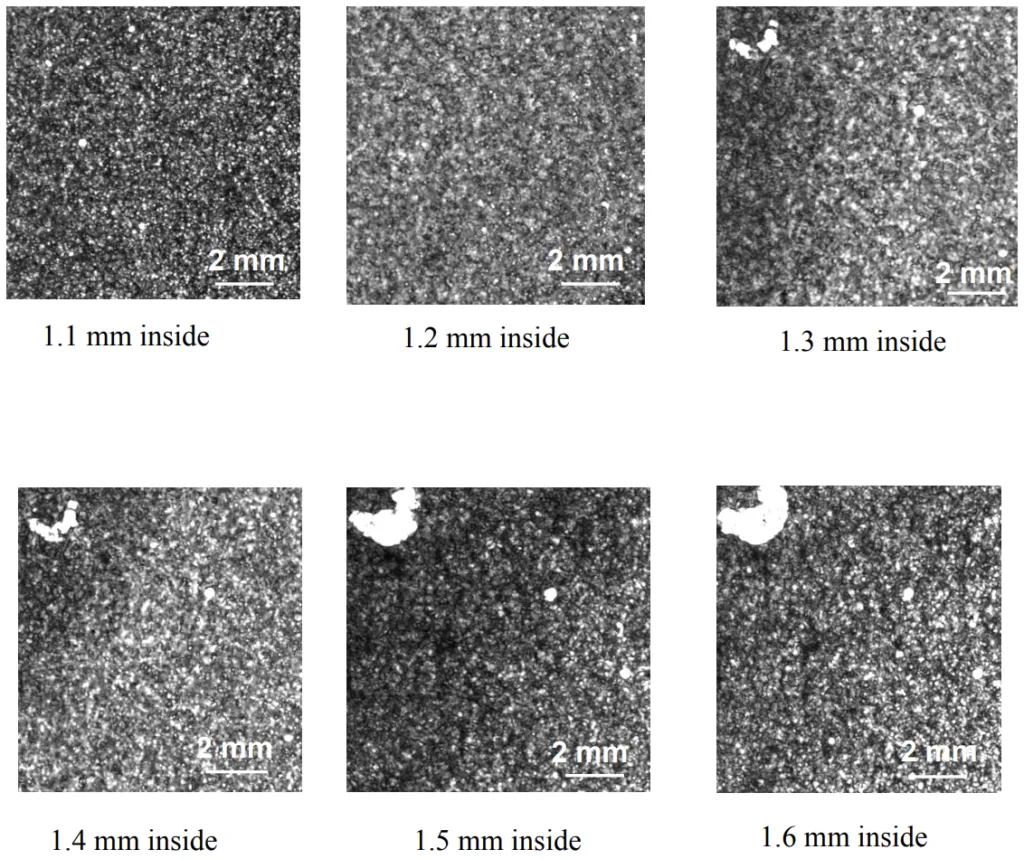
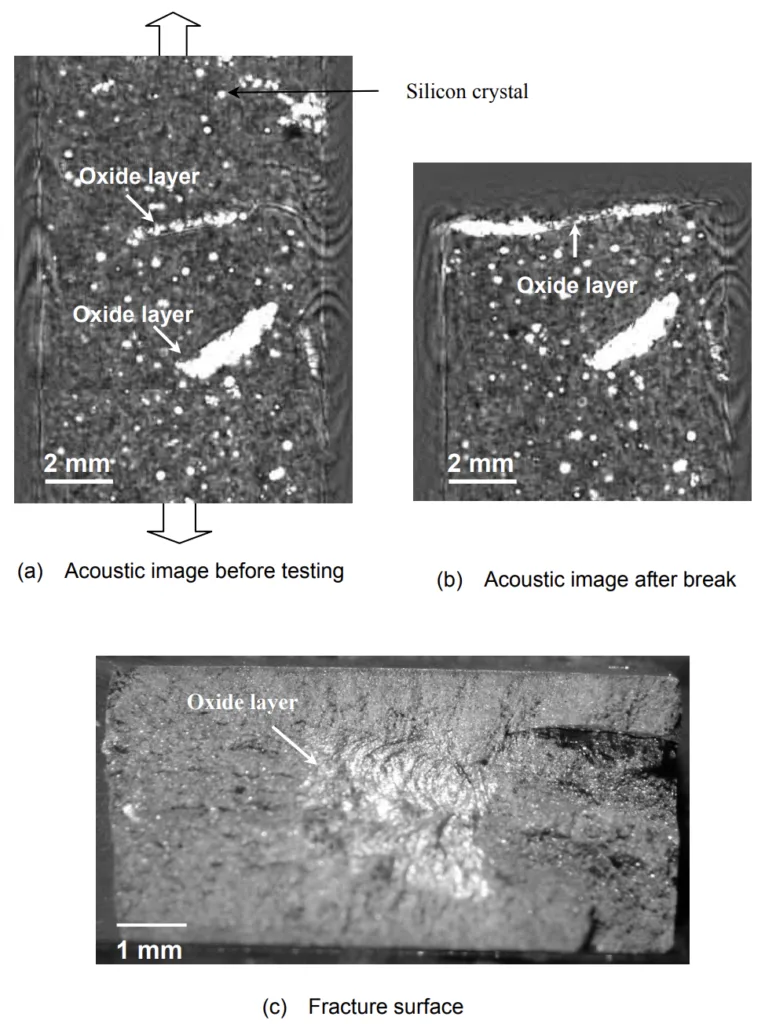
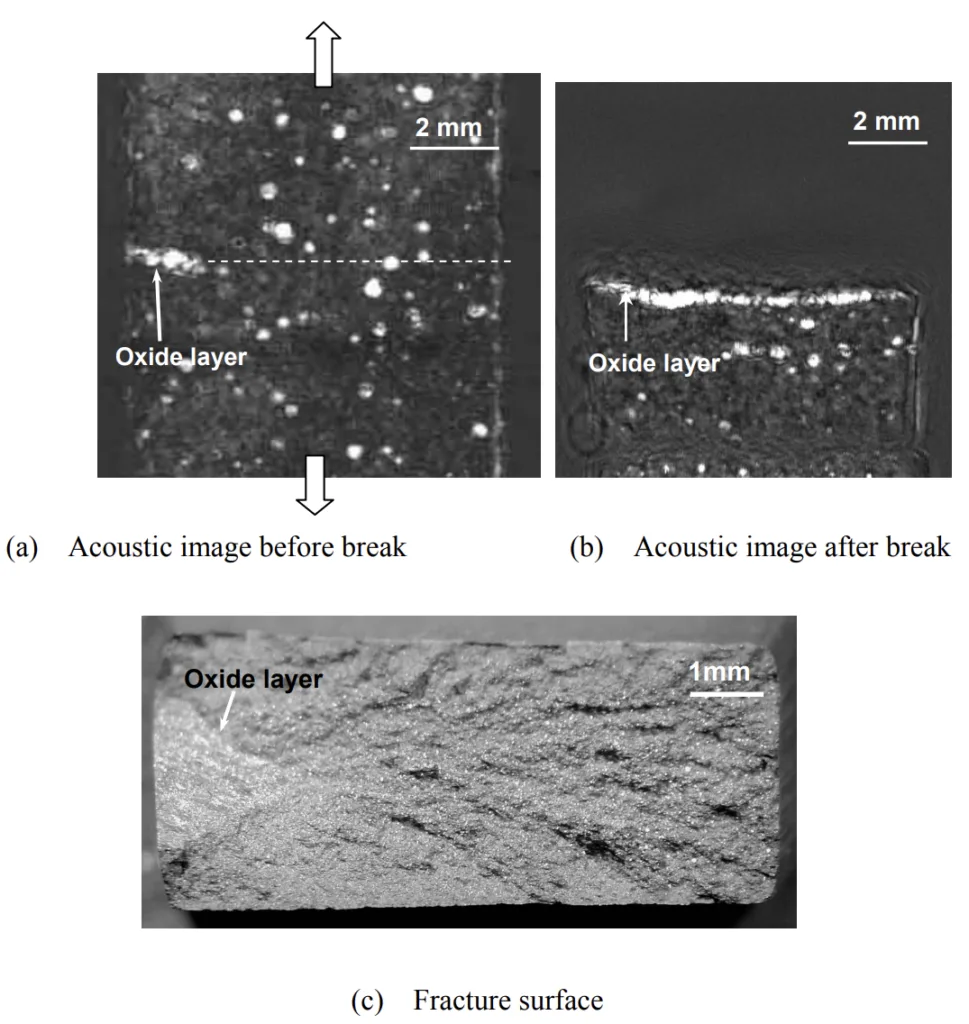
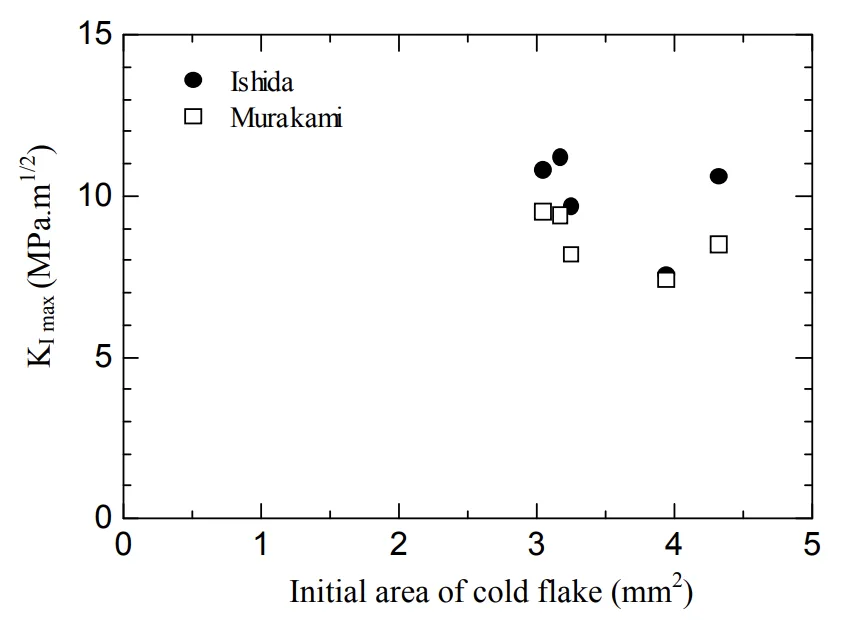
- Fig. 1.1 圧力によって平坦化された気泡があるガス気孔。
- Fig. 1.2 鋳造品中の丸いガス気孔の顕微鏡写真。
- Fig. 1.3 コールドフロー表面欠陥の一般的な例
- Fig. 1.4 これは、収縮気孔の典型的な外観を示しています。
- Fig. 1.5 表面まで伸びる典型的なフロー気孔。
- Fig. 1.6 機械的亀裂
- Fig. 1.7 典型的なブリスター
- Fig. 1.8 ポットの上部からのより柔らかい酸化物のスキミング
- Fig. 1.9 ラドルディップアウトウェルからドロスが含まれている鋳造
- Fig. 1.10 ダイカストマシン (a) 従来のダイカストマシン、 (b) スリーブと圧力システムの拡張ビュー
- Fig. 1.11 製品にコールドフレークを示すダイカストマシンのスリーブと圧力システム。
- Fig. 1. 12 典型的なコールドフレーク (a) 試験片中のコールドフレーク (b) 薄い酸化物境界で分離されたコールドフレークとマトリックス
- Fig. 1.13 酸化物層を有する典型的なコールドフレーク
- Fig. 1.14 音響測定 (a) 音響顕微鏡、 (b) スキャナー (c) 水中の試験片とプローブの距離、 (d) いくつかのセグメントを持つ総画像領域
- Fig. 1.15 走査音響顕微鏡によるCスキャン測定システムの概略図。
- Fig. 1.16 表面波とゲート位置。
- Fig.2.1 試験片の準備。 (a) 引張試験片を選択するためのダイカストプレート。 (b) ダイカストプレートの表面下2mmでの音響画像。明るい部分はコールドフレークです。
- Fig. 2.2 引張試験用試験片の形状とサイズ。
- Fig.2.3 選択されたコールドフレークを有する曲げ試験用試験片。
- Fig. 2.4 単調荷重を印加すると、この装置で音響画像が撮影されました。
- Fig. 2.5 引張試験用の実験設定。
- Fig.2.6 超音波測定の実験設定
- Fig. 2.7 局所浸漬法の概略図。
- Fig. 2.8 引張試験中のプロセス内超音波測定の設定。
- Fig. 2.9 引張試験中のプロセス内超音波測定の概略図。
- Fig.2.10 表面からの深さが異なる音響画像
- Fig. 2.11 AVSソフトウェアで2.9から取得した画像による3D画像。
- Fig.2.12 コールドフレークからの亀裂発生を示す音響画像。
- Fig.2.13 コールドフレークからの亀裂発生を示す音響画像。
- Fig. 2.14 引張試験前の試験片の音響画像。
- Fig. 2.15 浸漬法による引張試験前のFig. 4のコールドフレークの酸化物層から反射された超音波(RCF)。SとBは、それぞれ試験片の表面と底面から反射されたエコーです。(a) 標準スケール (b) 縦座標拡大スケール。
- Fig. 2.16 試験片の表面、底面、およびコールドフレークから反射されたエコーの概略図。
- Fig. 2.17 コールドフレークとマトリックス間の典型的な境界。
- Fig. 2.18 引張試験で得られた2つの典型的な曲線 (a) 機械を停止せずに、 (b) 異なる段階で機械を停止して。
- Fig. 2.19 粗いコールドフレークを含む試験片の破断面。
- Fig. 2.20 引張試験中のコールドフレークの酸化物層から反射されたエコーの変化。
- Fig. 2.21 コールドフレークの酸化物層から反射された超音波(RCF)の典型的な変化。SとBは表面と底面から反射されたエコーを示しています。
- Fig. 2.22 引張試験用試験片の音響画像
- Fig. 2.23 Fig. 2.22のターゲットコールドフレークの破断面
- Fig.2.24 ウォーターバッグ法で得られた小型コールドフレークからの波形変化。
- Fig.2.25 小型コールドフレークを含む試験片の破断面。
- Fig. 3.1 ダイカストプレートの音響画像の実験設定 (a) 音響顕微鏡 (b) 画像の選択領域
- Fig. 3.2 引張試験片の準備のためのダイカストプレートの音響画像。明るい部分と点はコールドフレークの酸化物層を示し、細かい点はマトリックス中のシリコン結晶です。
- Fig. 3.3 引張試験用試験片の形状と寸法。
- Fig. 3.4 引張試験用の実験設定。
- Fig. 3.5 冷間フレークの有無による試験片の典型的な応力-ひずみ曲線。
- Fig. 3.6 引張方向に垂直に方向付けられた内包型コールドフレークの酸化物層を有する試験片の音響画像と破断面の比較。
- Fig. 3.7 内包型コールドフレークから放射状の尾根を示す破断面
- Fig. 3.8 表面に露出するように配置されたコールドフレークの酸化物層の音響画像と破断面の比較。
- Fig. 3.9 コールドフレークの酸化物層の面積による公称引張強さの変化。
- Fig. 3.10 コールドフレークの酸化物層の面積による公称引張強さの変化。
- Fig. 3.11 コールドフレークの酸化物層の面積による有効引張強さの変化。
- Fig. 3.12 表面からのコールドフレークの酸化物層の距離と有効引張強度の関係。
- Fig. 3.13 酸化物層の露出長が異なるコールドフレークの試験片の破断面の比較。
- Fig. 3.14 コールドフレークの露出表面長と有効引張強度の関係。
- Fig. 3.15 村上(32)と石田(36)の式で計算された内包型コールドフレークを有する試験片の見かけの臨界応力拡大係数Kc*の比較。
- Fig. 3.16 村上(32)とニューマン(34)の式で計算された露出型コールドフレークを有する試験片の見かけの臨界応力拡大係数Kc*の比較。
- Fig. 3.17 村上式(32, 33)で計算された内包型および露出型コールドフレークを有する試験片の見かけの応力拡大係数Kc*の比較。
7. 結論:
主要な研究結果の要約:
本研究では、コールドフレークがアルミニウム合金ダイカスト(ADC12)の機械的特性に大きな影響を与えることを結論付けました。引張強度は、コールドフレークに関連する酸化物層の面積が増加するにつれて線形的に減少します。特に引張方向に対して垂直に配向された露出型コールドフレークは、内包型コールドフレークと比較して亀裂発生の影響を受けやすく、引張強度と疲労寿命をより大きく低下させます。プロセス内超音波測定は、引張試験と疲労試験の両方で、コールドフレークからの亀裂発生と伝播を効果的に検出します。線形破壊力学を用いて評価された臨界応力拡大係数は、破壊特性の尺度を提供し、コールドフレークのサイズと位置によって影響を受けます。疲労寿命もコールドフレークの存在によって短縮され、露出型フレークがより深刻な影響を与えます。
研究の学術的意義:
本研究は、一般的な鋳造欠陥であるコールドフレークがアルミニウム合金ダイカストの機械的挙動に及ぼす影響に関する基礎的な理解に貢献します。非破壊超音波技術と音響顕微鏡検査がこれらの欠陥を検出および特性評価するのに効果的であることを示しています。本研究は、コールドフレークの特性(サイズ、位置)と機械的特性(引張強度、疲労寿命)の間の関係に関する定量的なデータを提供し、これは材料科学およびダイカスト工学にとって貴重です。
実用的な意味合い:
本研究の知見は、ダイカスト産業に実用的な意味合いを持ち、部品の信頼性を向上させるためにダイカストプロセス中のコールドフレークの形成を最小限に抑えることの重要性を強調しています。開発された超音波測定法は、ダイカスト部品の品質管理および非破壊評価のための貴重なツールを提供し、コールドフレークのような重大な欠陥を検出し、機械的性能への影響を予測することを可能にします。これにより、プロセス制御の改善、スクラップ率の低減、および自動車やその他の用途におけるアルミニウムダイカスト部品の信頼性向上が期待できます。
研究の限界と今後の研究分野:
本研究では、特に小型コールドフレークを有する試験片の場合、応力-ひずみ曲線の非線形性に関連する限界を認め、これが臨界応力拡大係数の過小評価につながる可能性があります。今後の研究では、より包括的な分析のために、J積分などの非線形破壊力学的手法を探求することができます。さらに、今後の研究では、コールドフレークの形状と配向の影響をより詳細に調査し、ダイカスト中のコールドフレークの形成を軽減する方法を検討し、調査を他のアルミニウム合金およびダイカストプロセスに拡張することができます。疲労亀裂の進展は超音波測定では確認されておらず、今後の研究で改善できる領域となる可能性があります。
8. 参考文献:
- [1.1] RL Edwards. CR Manning. JK Magor. Effects of porosity on Strength of Aluminum Die-castings. Foundry Management & Technology, 1981; 109(7): 84-91.
- [1.2] JA Eady. DM Smith. The effect of porosity on the Tensile Properties of Aluminum Casting. Materials Forum, 1986; 9(4): 217-223.
- [1.3] M Okayasu. K Kanazawa and N Nishi. Effects of Porosity and Microstructures on Tensile properties of Slow Filling Rate Die Castings. J. JFS 1999; 71: 301-306. (in Japanese)
- [1.4] H Mayer. M Papakyriacou. B Zettl. SE Stanzl-Tschegg. Influence of porosity on the fatigue limit of die cast magnesium and aluminium alloys. Int. J. Fatigue 2003; 25: 245-256.
- [1.5] JZ Yi. YX Gao. PD Lee. HM Flower and TC Lindley. Scatter in fatigue life due to effects of porocity in cast A356-T6 aluminum–silicon alloys. Metallurgical and Materials Transactions A 2003; 34A (9): 1879-1890.
- [1.6] J Linder. M Axelsson. H Nilsson. The influence of porocity on the fatigue life for sand and permanent mould cast aluminum. Int J of Fatigue 2006; 28(12): 1752-1758.
- [1.7] J Linder. A Arvidsson. J Kron. The influence of porosity on the fatigue strength of high-pressure die cast aluminum. Fatigue and Fracture of Engng Mat and Structures 2006; 29 (5): 357-363.
- [1.8] MJ Couper. AE Neeson. JR Griffiths. Casting defects and the fatigue behaviour of an aluminum casting alloy. Fatigue & Fracture of Engng Materials & Structure 1990; 13(3): 213-227
- [1.9] B. Skallerud. T Iveland. G Härkegård. Fatigue life assessment of aluminum-alloys with casting defects. Engng Fracture Mech 1993; 44(6): 857-874
- [1.10] X Cao. J Campbell. Oxide inclusion defects in Al-Si-Mg cast alloys. Canadian Metallurgical Quarterly. 2005; 44 (4): 435-447
- [1.11] X Dai. X Yang. J Campbell. J Wood. Influence of oxide film defects generated in filling on mechanical strength of aluminum alloy castings. Materials Science and Technology, 2004; 20(4): 505-513
- [1.12] X Cao. J Campbell. The solidification characteristics of Fe-Rich Intermetallics in Al-11.5Si-0.4Mg Cast Alloys. Metallurgical and Materials Transactions A, 2004; 35A(5):1425-1435
- [1.13] N Nishi. T Komazaki. Y Takahashi. Formation Mechanisms of Aluminum Die Castings Microstructures. IMONO 1991; 63(4): 347-352. (in Japanese)
- [1.14] T Komazaki. K. Matsuura. N Nishi. Influence of Microstructures on Mechanical Properties of ADC 10 Alloy Die Castings. IMONO 1993; 65(3): 191-196. (in Japanese)
- [1.15] JZ Yi. YX Gao. PD Lee. TC Lindley. Microstructure-based fatigue life prediction for cast A356-T6 aluminum–silicon alloys. Metallurgical and Maerials Transactions B 2006; 37 (2): 301-311
- [1.16 ] A Herrera. V Kondic. The effect of artificial flaws on the tensile properties of Al-Si12 alloy. Brit. Foundryman. 1984; 77(1): 31-34,
- [1.17] K Shiozawa. Y Tohda. SM Sun. Crack initiation and small fatigue crack growth behaviour of squeeze-cast Al-Si aluminum alloys. Fatigue & Fracture of Engng Mat and Structures 1997; 20 (2): 237-247
- [1.18] M Avalle. G Belingardi. MP Cavatorta. R Doglione. Casting defects and fatigue strength of a die cast aluminum alloy: a comparison between standard specimens and production components. Int. J. Fatigue 2002; 24: 1-9
- [1.19] YX Gao. JZ Yi. PD Lee. TC Lindley. A micro-cell model of the effect of microstructure and defects on fatigue resistance in cast aluminum alloys. Acta Materialia 2004; 52 (19): 5435-5449
- [1.20] A Shyam. JE Allison. JW Jones. A small fatigue crack growth relationship and its application to cast aluminum. Acta Materialia 2005; 53: 1499-1509
- [1.21] T Komazaki. Y Maruyama. N Nishi. Effects of Silicon Contents on Formation of Abnormal Structures of Aluminum Alloy Die Castings. IMONO 1995; 67: 258-264. (in Japanese)
- [1.22] H Iwahori. K Tozawa. Y Yamamoto. M Nakamura. Formation of scattered structures in aluminum alloy die-castings. J. Japan Inst. Light Metals 1984; 34: 389-394. (in Japanese)
- [1.23] H Nomura. E Kato. Y Maeda. S Okubo. Melt Cooling and Formation of Solidification Phase in Die Casting Sleeve. J. JFS 2001; 73(10): 656-661. (in Japanese)
- [1.24] H Iwahori. K Tozawa. Y Yamamoto. M Nakamura. Properties of scattered struecures included in aluminum die castings. J. Japan Inst. Light Metals 1984; 34 (9) 389-394. (in Japanese)
- [1.25] M Okayasu. K Kanazawa. N Nishi. Effects of Internal Defects on Tensile Properties of ADC10 Die Castings. J. JFS 1998; 70(11): 779-785. (in Japanese)
- [1.26] C H Caceres.B I Selling. Casting defects and the tensile properties of an Al-Si-Mg alloy. Materials Science and Engg A 1996; 220: 109-116
- [1.27] R Kimura. M Yoshida. G Sasaki. J Pan. H. Fukunaga. Influence of abnormal structure on the reliability of squeeze castings. Journal of Materials Processing Technology 2002; 130-131: 299-303
- [1.28] William G. Walkington. Causes and solutions die-casting defects, North American Die-casting Association Publication, p 155-158, 1997
- [1.29] H Kato. T Suzuki. Y Annou. K Kageyama. Nondestructive detection of Cold Flakes in Aluminum Alloy Die-Cast Plate with Ultrasonic Measurement. Mater. Trans. 2004; 45 (7): 2403-2409.
- [1.30] J. Krautkramer and H. Krautkramer,” Ultrasonic Testing of Material, 4th edition, Springer Verlag, pp 13-14, New York, 1990
- [2.1] H. Iwahori, K. Tozawa, Y. Yamamoto and M. Nakamura : “ Formation of scattered structures in aluminum alloy die-castings”. J. Japan Inst. Light Metals 34 (1984) 389
- [2.2] N. Nishi, T. Komazaki and Y. Takahashi : “Formation mechanism of aluminum die-castings Microstructures” IMONO 63 (1991) 347
- [2.3] T. Komazaki, Y. Maruyama and N. Nishi : “ Effect of Silicon contents on formation of abnormal structures of aluminum alloy die-castings”. IMONO 67 (1995) 258
- [2.4] X Cao. J Campbell. Oxide inclusion defects in Al-Si-Mg cast alloys. Canadian Metallurgical Quarterly. 2005; 44 (4): 435-447
- [2.5] X Dai. X Yang. J Campbell. J Wood. Influence of oxide film defects generated in filling on mechanical strength of aluminum alloy castings. Materials Science and Technology, 2004; 20(4): 505-513
- [2.6] K. Konagaya, S. Aoyama, M. Tachikawa and K. Kanazawa : ”Effect of casting defects on fatigue life of aluminum alloy die-castings”. Japan Die Castings Cong. (1998) 171
- [2.7] M. Okayasu, K. Kanazawa and N. Nishi : “ Effects of internal defects on tensile properties of ADC 10 die-castings” J. JFS 70 (1998) 779
- [2.8] T. Komazaki, K. Matsuura and N. Nishi: “Influence of Microstructures on mechanical properties of ADC10 alloy die-castings” IMONO 65 (1993) 191
- [2.9] H. Iwahori, K. Tozawa, T. Asano,Y. Yamamoto, M. Nakamura, M. Hashimoto and S. Uenishi : J. Japan Inst. Light Metals 34 (1984) 525
- [2.10] Naomi Nishi : Material processing technical seminar ( Japan Material
- [2.11] William G. Walkington. Causes and solutions die-casting defects, North American Die-casting Association Publication, p 155-158, 1997
- [2.12] H. Kato, T. Suzuki, Y. Annou and K. Kageyama : “Nondestructive detection of Cold Flakes in Aluminum Alloy Die-Cast Plate with Ultrasonic Measurement”Mater. Trans. 45 (2004) 2403
- [2.13] J. Krautkrämer and H. Krautkrämer: Ultrasonic Testing of Materials, 4th ed. (Springer-Verlag) (1990) 16
- [2.14] X Cao. J Campbell. Oxide inclusion defects in Al-Si-Mg cast alloys. Canadian Metallurgical Quarterly. 2005; 44 (4): 435-447
- [3.1] X Cao. J Campbell. Oxide inclusion defects in Al-Si-Mg cast alloys. Canadian Metallurgical Quarterly. 2005; 44 (4): 435-447
- [3.2] X Dai. X Yang. J Campbell. J Wood. Influence of oxide film defects generated in filling on mechanical strength of aluminum alloy castings. Materials Science and Technology, 2004; 20(4): 505-513
- [3.3] X Cao. J Campbell. The solidification characteristics of Fe-Rich Intermetallics in Al-11.5Si-0.4Mg Cast Alloys. Metallurgical and Materials Transactions A, 2004; 35A(5):1425-1435
- [3.4] T Komazaki. Y Maruyama. N Nishi. Effects of Silicon Contents on Formation of Abnormal Structures of Aluminum Alloy Die Castings. IMONO 1995; 67: 258-264. (in Japanese)
- [3.5] H Iwahori. K Tozawa. Y Yamamoto. M Nakamura. Formation of scattered structures in aluminum alloy die-castings. J. Japan Inst. Light Metals 1984; 34: 389-394. (in Japanese)
- [3.6] H Nomura. E Kato. Y Maeda. S Okubo. Melt Cooling and Formation of Solidification Phase in Die Casting Sleeve. J. JFS 2001; 73(10): 656-661. (in Japanese)
- [3.7] H Iwahori. K Tozawa. Y Yamamoto. M Nakamura. Properties of scattered struecures included in aluminum die castings. J. Japan Inst. Light Metals 1984; 34 (9) 389-394. (in Japanese)
- [3.8] M Okayasu. K Kanazawa. N Nishi. Effects of Internal Defects on Tensile Properties of ADC10 Die Castings. J. JFS 1998; 70(11): 779-785. (in Japanese)
- [3.9] William G. Walkington. Causes and solutions die-casting defects, North American Die-casting Association Publication, p 155-158, 1997
- [3.10] H Kato. T Suzuki. Y Annou. K Kageyama. Nondestructive detection of Cold Flakes in Aluminum Alloy Die-Cast Plate with Ultrasonic Measurement. Mater. Trans. 2004; 45 (7): 2403-2409.
- [3.11] AKMA Ahamed. H Kato. K Kageyama. T Komazaki. Acoustic Visualization of Cold Flakes and Crack propagation in Aluminum Alloy Die-Cast Plate. Materials Science and Eng A 2006; 423: 313-323.
- [3.12] Y Murakami. H Usuki. Prediction of fatigue strength of high strength steels based on statistical evaluation of inclusion size. Japan Mech. Eng. Soc. 1989; 55 (510): 213-221. (in Japanese)
- [3.13] Y Murakami. Analysis of stress intensity factors of models Ι ΙΙ and ΙΙΙ for inclined surface cracks of arbitrary shape. Engng Fracture Mech. 1985; 22: 101-114.
- [3.14] JC Newman. Jr. IS Raju. An empirical Stress intensity factor equation for the surface crack. Eng. Frac. Mech. 1981; 15(1-2): 185-192.
- [3.15] Y Murakami. Stress Intensity Factor Handbook. Pergamon Press, oxford, 1987
- [3.16] M Ishida. H Noguchi. Tension of a plate containing an embedded elliptical crack. Eng. Frac. Mech. 1984; 20(3): 387-408.
- [3.17] TL Anderson. Fracture Mechanics fundamentals and applications. CRC press, 1995, p.117 p. 142 p. 541
- [3.18] K Kanazawa. K Chijiiwa. H Kubota. K Nakamura. Fracture toughness of Aluminum Alloy Die-Castings. Japan Die-Casting Association 1994; JD94-20: 170-177. (in Japanese)
- [3.19] JM McNaney. RM Cannon. RO Ritchie. Fracture and fatigue-crack growth along aluminum-alumina interfaces. Acta mater. 1996; 44(12): 4713-4728
- [4.1] K. Konagaya, S. Aoyama, M. Tachikawa, K. Kanazawa “ Effect of casting defects on fatigue life of aluminum alloy die-casting” Japan Die Cast Cong., JD98-27, pp 171-179
- [4.2] Y. Ninomiya, K. Kanazawa, K. Konagaya, S. Aoyama, H. Hirokawa, E. Soichi, “ Analytical prediction of fatigue life on aluminum alloy die-castings for high performance parts” Japan Die Cast Cong. JD04-30, pp. 175-180
- [4.3] K. Kanazawa, K. Chijiwa, T. Fukita,” Influence of casting method on properties of fatigue fracture in aluminum alloy die castings” Japan Die Cast Cong. JD92-20
- [4.4] Y. Murakami and H. Usuki: Trans. Japan Mech. Eng. Soc., 1989, 55, 213-221. (in Japanese)
- [4.5] M. Ishida and H. Noguchi: Eng. Frac. Mech., 1984, 20, 387-408.
- [4.6] K. Kanazawa, K. Chijiiwa, H. Kubota and K. Nakamura: Trans. 1994 Japan Die Cast. Cong., Dec. 1994, Japan Die Casting Association, 170-177. (In Japanese)
9. 著作権:
- この資料は、"[A.K.M. Aziz Ahamed]"氏の論文:「"Effects of Casting Defects on Mechanical Properties of Aluminum Alloy Die-Casts"」に基づいています。
- 論文ソース: [DOI URL] (DOI URLは論文に記載されていません)
この資料は上記の論文に基づいて要約されたものであり、商業目的での無断使用は禁止されています。
Copyright © 2025 CASTMAN. All rights reserved.