この論文概要は、"Casting Characteristics of Aluminum Die Casting Alloys"(論文タイトル)と題された論文に基づいており、"US Department of Energy, Office of Industrial Technologies"にて発表されました。
1. 概要:
- タイトル:アルミニウムダイカスト合金の鋳造特性
- 著者:Makhlouf M. Makhlouf, Diran Apelian
- 発表年:2002年2月5日
- 掲載ジャーナル/学会:米国エネルギー省産業技術局
- キーワード:アルミニウム合金、ダイカスト、鋳造特性、ダイソルダー、スラッジ形成、流動性

2. 研究背景:
*研究トピックの社会的/学術的背景:
本研究は、「アルミニウムダイカスト合金における合金 - 微細組織 - 性能相互作用」と題された以前のプログラムのフォローアップです。以前のプログラムでは、10種類の元素とそれらの相互作用が、アルミニウムダイカスト合金の微細組織と特性に及ぼす影響が調査されました。以前の研究に基づいて、機械的特性と物理的特性が向上した合金の最適組成が予測されました。これらの予測された合金は優れた機械的特性または物理的特性を持つと考えられましたが、容易にダイカストできるかどうかは不明でした。その結果、本研究はこれらのアルミニウムダイカスト合金の鋳造特性を調査するために開始されました。ダイカストは重要な製造プロセスであり、高品質の部品を製造するためにはアルミニウム合金の鋳造特性を理解することが不可欠です。
*既存研究の限界:
既存の研究は、アルミニウムダイカスト合金の機械的特性と物理的特性の最適化に焦点を当てており、鋳造特性、特にダイソルダー、スラッジ形成、流動性、および被削性を十分に評価していませんでした。スラッジ形成とダイソルダーに関する既存の文献は、特にダイカスト特有の条件(高い冷却速度など)の影響に関して、矛盾があり、包括的な理解に欠けていました。さらに、ダイカスト条件を正確にシミュレートする、普遍的に受け入れられた標準化された流動性試験が不足していました。
*研究の必要性:
強化された特性を持つ合金設計と、ダイカストによる製造可能性との間のギャップを埋めるために、本研究が開始されました。新たに開発されたアルミニウムダイカスト合金の鋳造特性を調査し、それらが効果的かつ効率的にダイカストできることを保証する必要があります。ダイソルダーやスラッジ形成などの問題を理解し、軽減することは、ダイカスト業界における生産性と費用対効果にとって非常に重要です。流動性と被削性を評価することも、部品の品質と製造効率を確保するために不可欠です。
3. 研究目的と研究課題:
*研究目的:
本研究プログラムの目的は以下のとおりです。
- 選択されたアルミニウムダイカスト合金の鋳造特性を評価する。
- アルミニウムダイカスト合金の鋳造特性に影響を与える主要な要因を特定する。
このプロジェクトは、優れた特性を持つと予測された5つの実験的アルミニウムダイカスト合金のダイソルダー傾向、スラッジ形成傾向、流動性、および被削性を調査し、市販のA380.0合金と比較することを目的としています。
*主な研究課題:
- 選択されたアルミニウムダイカスト合金のダイソルダー傾向はどの程度であり、合金化学組成によってどのように影響を受けるか?
- これらの合金のスラッジ形成傾向は、異なる保持温度および冷却速度下でどの程度であり、合金化学組成および加工パラメータはスラッジ特性にどのように影響するか?
- ダイカスト条件下でのこれらの合金の流動性はどの程度であり、合金化学組成はダイカスト充填能力にどのように影響するか?
- これらの合金の被削性特性はどの程度であり、スラッジ形成に関連する潜在的な被削性の問題はあるか?
*研究仮説:
本研究は暗黙のうちに以下の仮説を立てています。
- 合金化学組成、特にFe、Mn、Ni、Cr、およびSi含有量は、ダイソルダーおよびスラッジ形成傾向に大きな影響を与える。
- 溶融金属温度、金型温度、冷却速度などの加工パラメータは、鋳造特性において重要な役割を果たす。
- スラッジ係数が高い合金は、より大きなスラッジ形成傾向を示す。
- 合金化学組成および加工パラメータの調整は、ダイソルダーおよびスラッジ形成の問題を軽減し、鋳造特性を最適化できる。
4. 研究方法
*研究デザイン:
本研究では、6種類のアルミニウム合金(5種類の実験合金と1種類の市販A380.0合金)の鋳造特性を評価するために実験的デザインを採用しています。ダイソルダーと流動性の物理シミュレーション試験、およびスラッジ形成の制御冷却実験が含まれています。被削性は、スラッジ形成の理解と文献レビューに基づいて評価され、直接試験は実現不可能でした。
*データ収集方法:
- ダイソルダー傾向: 物理シミュレーション装置を使用し、制御された条件(温度、回転速度、時間)下でH-13ピンを溶融合金に浸漬しました。ピンの金属間化合物層の厚さを、ダイソルダー傾向の指標として測定しました。
- 流動性: SPX Corporation での曲がりくねったキャビティ金型へのダイカストにより、充填長さを流動性の指標として測定しました。試験は、ゲート速度 2400 ips、金型キャビティ厚さ 0.5 mm で実施されました。
- スラッジ形成傾向: 合金を 670℃ および 720℃ で 3 時間保持し、異なる冷却速度で凝固させました。るつぼでの徐冷、パーマネント金型での中速冷却、銅ウェッジ金型での急速冷却です。微細組織分析を実施してスラッジを特性評価しました。
- 被削性: 被削性は、スラッジ形成傾向と文献レビューから推測され、試料作製の困難さから直接的な実験的測定は行いませんでした。
*分析方法:
- ダイソルダー: 顕微鏡を使用した金属間化合物層の厚さの測定。
- 流動性: 金型キャビティ内の充填長さの測定。流動長データに対する統計分析。
- スラッジ形成: 光学顕微鏡、走査型電子顕微鏡(SEM)、およびエネルギー分散型X線分析(EDX)を使用して、スラッジの量、サイズ、形態、分布、および化学組成を特性評価しました。スラッジ粒子の微小硬さ試験も実施しました。
- 被削性: スラッジ特性と文献に基づく定性的な評価。
*研究対象と範囲:
研究対象は、6種類のアルミニウムダイカスト合金です。強化された特性のために設計された5種類の実験合金(#1〜#5)と、市販のA380.0合金です。研究の範囲は、ダイソルダー傾向、スラッジ形成傾向、流動性、および被削性の評価に限定されています。この研究は、シミュレートされたダイカスト条件下でのこれらの鋳造特性に対する合金化学組成と加工パラメータの影響に焦点を当てています。
5. 主な研究結果:
*主な研究結果:
- ダイソルダー: 「合金の鉄含有量がソルダーに最も影響を与える。」合金#1(1.84% Fe)はソルダーを示しませんでした。「Mnはソルダーに有益な効果がある。」「Niはソルダーに有害である。」「Tiの欠如または不在はソルダーにとって不利である。」FeとMnが低く、Niが存在する合金#4は、A380.0合金よりも悪い、最も高いダイソルダー傾向を示しました。
- 流動性: 「すべての合金において、データ散布が大きく、合金化学組成以外の要因が、金型キャビティを充填する合金の能力に大きな役割を果たしていることを示唆している。」「合金化学組成の観点から見ると、Fe、Mn、Cr、Mgなどの高温化合物を形成する元素の量が多いほど、合金の流動性は低くなる。」合金383は最も高い平均流動長を示しましたが、合金#1と#3は、SiとCuの含有量が高いにもかかわらず、Fe、Mn、Cr、Mgの合計含有量が高いことが原因で、合金383よりも低い流動性を示しました。
- スラッジ形成: 「スラッジ係数(SF)¹は、合金のスラッジ形成傾向と形成されるスラッジの量を決定する上で最も重要である。」SFが高い合金#1と#3は、有意なスラッジを形成しました。「スラッジ粒子の形態は、合金中のFe:Mn:Crの比率によって影響を受ける。」「冷却速度はスラッジ形成において重要な役割を果たす。冷却速度が遅いほどスラッジ形成が促進される。」「スラッジは、試験した合金では、670℃または720℃のいずれかの保持温度では形成されない。」ただし、るつぼでの徐冷条件下では形成される可能性がありますが、高速冷却ダイカスト条件下では形成されません。
- 被削性: 「適切な機械加工技術と機械加工パラメータを使用すれば、合金に機械加工上の問題は発生しないはずである。」被削性は、ダイカストにおけるスラッジ形成がほとんどの試験合金で過剰ではないため、適切なパラメータ調整で管理可能であると推測されます。
*統計的/定量的分析結果:
- ダイソルダー: 金属間化合物層の厚さの測定値(表4)は、ダイソルダー傾向を定量化し、合金#4が最も高い値(44.5 µm)を示し、合金#1が0 µmを示しました。
- 流動性: 流動長測定値(表6)は、データ散布が大きいことを示しており、合金化学組成以外の要因が流動性に影響を与えていることを示唆しています。合金#1、#3、および383の平均流動長と範囲が示されています。
- スラッジ形成: スラッジ係数(SF)の計算値(表7)は、観察されたスラッジ形成と相関していました。微小硬さ測定値(表8)は、異なるスラッジ相の硬さを定量化しました。顕微鏡写真(図7〜20)は、さまざまな条件下でのスラッジの形態と分布を定性的に示しています。
*データ解釈:
- 合金#1の高いFe含有量は、Fe飽和のためにダイソルダーを最小限に抑えました。Mnは有益な効果を示しましたが、NiとTiの欠如は有害でした。
- 流動性試験の結果は、データ散布が大きいため、合金化学組成の影響に関して決定的な結論を出すことができませんでした。これは、プロセス変動が支配的であることを示唆しています。ただし、高温化合物を形成する元素(Fe、Mn、Cr、Mg)の含有量が多いほど、流動性が低下する可能性があるようです。
- スラッジ係数は、ダイカスト冷却速度下でのスラッジ形成傾向を効果的に予測しました。SFが高い合金は有意なスラッジを形成しました。冷却速度と合金化学組成は、スラッジの形態と量に大きな影響を与えました。スラッジ形成は、冷却速度が遅いほど顕著になります。
- 被削性は、ほとんどの合金でダイカストにおけるスラッジ形成が深刻ではないため、適切な機械加工パラメータで管理可能であると予想されます。
*図表名リスト:
- 図1. スラッジ係数と温度の関係 [14, 16]。
- 図2. ダイソルダーシミュレーション装置。
- 図3. ピン表面の金属間化合物層。
- 図4. ピン表面の金属間化合物層。
- 図5. 合金383の流動性試験結果、キャビティ厚さ1 mm。
- 図6. 試験合金のスラッジ係数と温度の関係。
- 図7. 合金#3を徐冷した場合のFeリッチ針状および多面体状粒子と一次Si。S-一次Si、P-多面体状、N-針状(または板状)。
- 図8. 合金#1の微細組織、溶融金属を670℃で3時間保持し、壁厚0.17インチの銅ウェッジ金型で鋳造。T-星状、N-針状(または板状)、S-一次Si。
- 図9. 合金#2の微細組織、溶融金属を670℃で3時間保持し、壁厚0.17インチの銅ウェッジ金型で鋳造。C-中国文字状。
- 図10. 合金#3の微細組織、溶融金属を670℃で3時間保持し、壁厚0.17インチの銅ウェッジ金型で鋳造。T-星状、S-一次Si。
- 図11. 合金#4の微細組織、溶融金属を670℃で3時間保持し、壁厚0.17インチの銅ウェッジ金型で鋳造。N-針状(または板状)。
- 図12. 合金#5の微細組織、溶融金属を670℃で3時間保持し、壁厚0.17インチの銅ウェッジ金型で鋳造。C-中国文字状。
- 図13. 合金A380の微細組織、溶融金属を670℃で3時間保持し、壁厚0.17インチの銅ウェッジ金型で鋳造。B-ブロック状粒子。
- 図14. 合金#2の微細組織、溶融金属を720℃で3時間保持し、るつぼ内で空冷。C-中国文字状。
- 図15. 合金#4の微細組織、溶融金属を720℃で3時間保持し、るつぼ内で空冷。P-多面体状。
- 図16. 合金A380の微細組織、溶融金属を720℃で3時間保持し、るつぼ内で空冷。C-中国文字状、N-針状(または板状)、P-多面体状。
- 図17. 合金#1の微細組織、溶融金属を670℃で3時間保持し、るつぼ内で空冷。S-一次Si、N-針状(または板状)、P-多面体状。
- 図18. 合金#3の微細組織、溶融金属を670℃で3時間保持し、るつぼ内で空冷。C-中国文字状、B-ブロック状粒子。
- 図19. 合金A380の微細組織、溶融金属を670℃で3時間保持し、壁厚0.36インチの銅ウェッジ金型で鋳造。T-星状、B-ブロック状粒子。
- 図20. 合金A380の微細組織、溶融金属を720℃で3時間保持し、壁厚0.36インチの銅ウェッジ金型で鋳造。T-星状、B-ブロック状粒子。
![Figure1. Sludge factor versus temperature [14, 16].](https://castman.co.kr/wp-content/uploads/Figure1.-Sludge-factor-versus-temperature-14-16.webp)
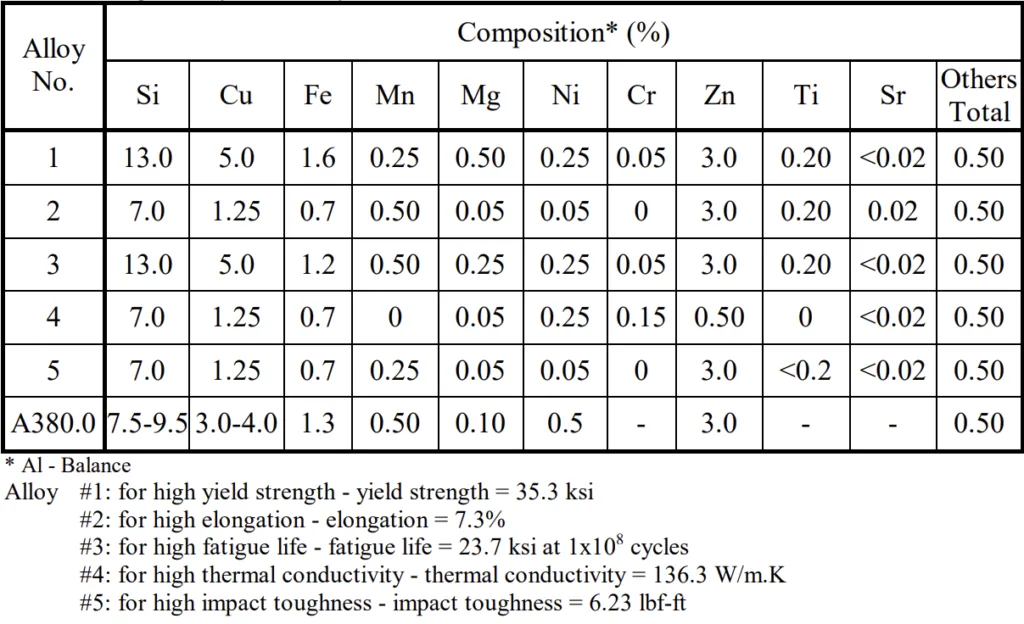
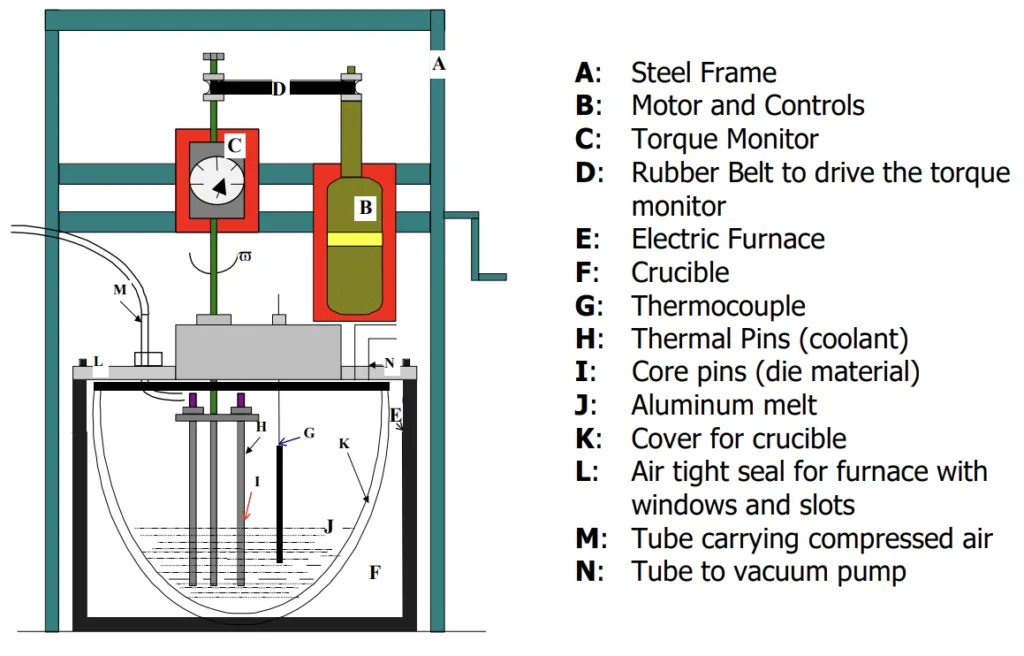
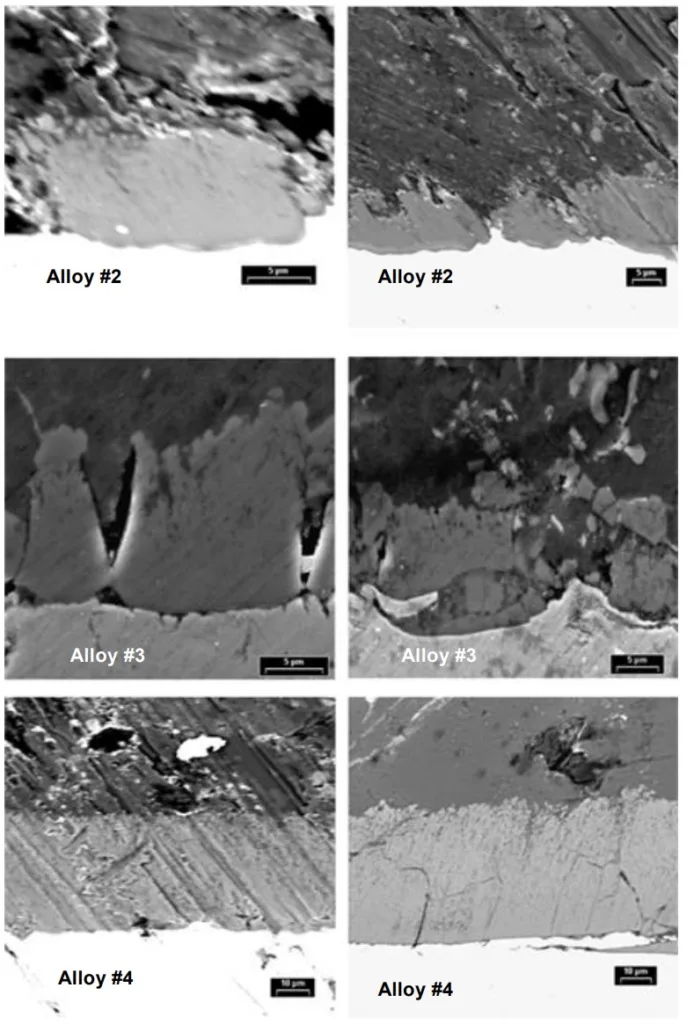
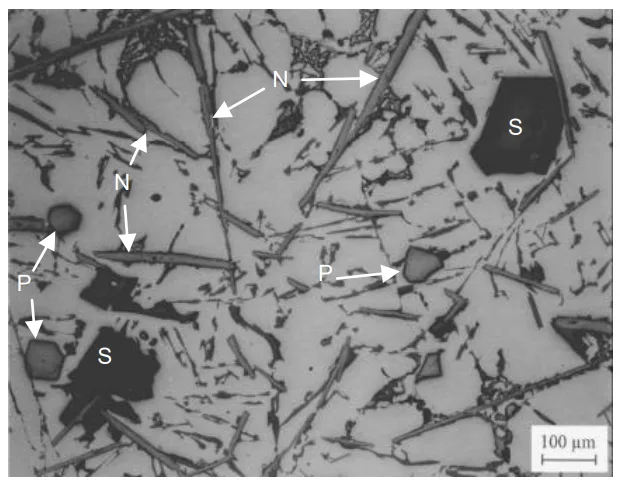
6. 結論と考察:
*主な結果の要約:
本研究では、機械的特性が向上するように設計された5つの実験合金は、ダイカスト可能であることが結論付けられました。これらの合金は、ダイソルダー、スラッジ形成、流動性、または被削性の点で、A380.0合金と比較して大きな問題を示していません。具体的な調査結果には、Fe含有量がダイソルダーの主要な要因であること、Mnが有益な効果を持つこと、Niが有害であることなどが含まれます。スラッジ形成傾向はスラッジ係数によって予測可能であり、合金化学組成と冷却速度の影響を受けます。流動性データは大きな変動を示し、プロセス要因が支配的であることを示唆していますが、Fe、Mn、Cr、およびMgの含有量が多いほど、流動性が低下する可能性があります。被削性は、ほとんどの合金でダイカストにおけるスラッジ形成が深刻ではないため、適切な技術で管理可能であると予想されます。
*研究の学術的意義:
本研究は、アルミニウムダイカスト合金の鋳造特性、特にダイソルダーとスラッジ形成に関するより深い理解に貢献しています。ダイカスト条件下でのスラッジ傾向を予測するためのスラッジ係数の概念の実験的検証を提供します。この研究は、ダイソルダーにおけるFe、Mn、Ni、Cr、およびTiの役割と、スラッジ形態に対する冷却速度の影響を明らかにしています。ダイカストにおける流動性測定の複雑さと、合金化学組成と並行してプロセスパラメータを考慮する必要性を強調しています。
*実用的な意義:
調査結果は、アルミニウムダイカストにおける合金設計とプロセス最適化に関する実用的なガイドラインを提供します。
- FeとMnの含有量が少ない合金の場合、ダイソルダーの問題に注意が必要です。Mn含有量を増やし、Niを最小限に抑えることで、これを軽減できます。たとえば、合金#4の場合、「合金#4のMn含有量を0.25〜0.5%に増やし、Ni含有量を最小限に抑える必要がある」とされています。
- スラッジ係数が高い合金、特にFeが高い合金の場合、ハードスポットの形成を防ぐために「Fe含有量を許容される下限レベルに維持し、Mn含有量を増やす必要がある」。たとえば、合金#1の場合、「Feを1.6%に減らし、Mnを0.5%に増やすことができる」とされています。
- ダイカスト充填の問題が発生した場合は、合金組成を変更する前に、プロセス調整を検討する必要があります。合金化学組成において高温化合物を形成する元素を最小限に抑えて、流動性を向上させる必要があります。
- これらの合金には適切な機械加工技術とパラメータが不可欠であり、合金の種類とスラッジによる潜在的なハードスポットに基づいて調整が必要になる場合があります。
*研究の限界:
流動性試験はデータ散布が大きく、合金化学組成の影響に関する決定的な結論を出すことができませんでした。直接的な被削性試験は実施されておらず、評価は推論に基づいています。研究は、限られた合金セットと加工条件に焦点を当てました。スラッジ形成の研究は有益ですが、工業的なダイカスト操作における複雑な溶融金属処理および冷却条件を完全に再現しているわけではありません。
7. 今後のフォローアップ研究:
*今後のフォローアップ研究の方向性:
- ダイカスト合金のより堅牢な流動性測定方法を開発するために、流動性試験におけるデータ散布の原因となる要因のさらなる調査。
- 被削性特性を定量化し、機械加工パラメータを最適化するための、さまざまな機械加工条件下でのこれらの合金の直接的な被削性試験。
- 工業的なダイカストプロセスをより厳密にシミュレートする条件下での、合金化学組成、保持温度、および冷却速度がスラッジ形成に及ぼす相互作用に関する、より詳細な研究(溶融金属の移動やショットスリーブの冷却など)。
- スラッジ粒子がダイカスト部品の機械的特性と性能に及ぼす長期的な影響の調査。
- これらの合金のダイソルダーを軽減するための、さまざまな金型コーティングと潤滑剤の有効性の調査。
*さらなる探求が必要な分野:
- MnとTiがダイソルダー傾向に影響を与える正確なメカニズム。
- ダイカスト条件下で異なる合金系でスラッジ形成を引き起こす臨界冷却速度と保持温度。
- 微量合金元素と不純物がアルミニウムダイカスト合金の鋳造特性に及ぼす影響。
- 合金化学組成と加工パラメータに基づいて、ダイソルダー、スラッジ形成、および流動性の予測モデルの開発。
8. 参考文献:
- 1 M. M. Makhlouf, D. Apelian, and L. Wang, Microstructure and Properties of Aluminum Die Casting Alloys, NADCA, 1999.
- 2 Y. L. Chu, P. S. Cheng, and R. Shivpuri, “Soldering Phenomenon in Aluminum Die Casting: Possible Causes and Cures”, NADCA Transactions, 1993, pp361-371.
- 3 Y. L. Chu, P. S. Cheng, and R. Shivpuri, “A Study of Erosive Wear in Die Casting Dies: Surface Treatments and Coatings”, NADCA Transactions, 1993, pp199-208.
- 4 R. Shivpuri, S. I. Chang, Y. I. Chu, M. Kuthirakulathu, “An Evaluation of H-13 Die Steel, Surface Treatments and Coatings for Wear in Die Casting Dies”, NADCA Transactions, 1991, p.391-397.
- 5 K. Venkatesan, R. Shivpuri, “An Investigation of the Effect of Process Parameters on the Washout in Die Casting Dies”, NADCA Transactions, 1995, pp361-371.
- 6 W. Kajoch and A. Fajkiel, “Testing the Soldering Tendencies of Aluminum Die Casting Alloys”, NADCA Transactions, 1991, pp67-74.
- 7E. K. Holz, “Trouble-Shooting Aluminum Die Casting Quality Problems” Transactions of 7th. SDCE International Die Casting Congress, 1972, Paper No. 4372.
- 8 S. Shankar and D. Apelian, “DIE SOLDERING: Mechanism Of The Interface Reaction Between Molten Aluminum Alloy And Tool Steel – Part I, Submitted to Met Trans.
- 9 S. Shankar and D. Apelian, “DIE SOLDERING: Mechanism Of The Interface Reaction Between Molten Aluminum Alloy And Tool Steel – Part II, Submitted to Met Trans.
- 10 M. Yu, Y. L. Chu, and R. Shivpuri, Ohio State University, Columbus, OH, unpublished research, 1997.
- 11 A. C. Paladino, “Die Lubricant Research Meets Die Casters' Needs”, Die Casting Engineers, May-June 1991, pp. 16-18.
- 12 H. G. Munson, T. H. Camel, “Development of a Semi-Permanent Release Coating for Die Casting”, NADCA Transactions, 1991, pp351-354.
- 13 P. N. Crepeau, B. L. Tiwari, and K. M. Rahmoeller, “ Characterization of Oxide Sludge, Dross and Inclusions in Aluminum Melting and Holding Furnaces”, Proc. Of the 3rd International Conference on Molten Aluminum Processing, Orlando, Fl, November 1992, pp 51-57.
- 14 J. L. Jarstad, "Understanding Sludge", Proc. Of the 14th SDCE International Die Casting Congress and Exposition, Toronto, Ont, Canada, May 11-14, 1987, Paper No. G-T87-011.
- 15 D. E. Groteke, “Elimination Hard Spots from Aluminum Die Castings”, Die Casting Engineer, Vol. 29, No. 5, Sept/Oct. 1985, pp 16-18, 20, 22, 24.
- 16 J. Gobrecht, “Gravity-Segregation of Iron, Manganese and Chromium in an Aluminum-Silicon Casting, Part I”, Giesserei, Vol. 61, No. 10, 1975, pp 263-265.
- 17 S. G. Shabestari, and J. E. Druzleski, “The Effecet of Solidification Condition and Chemistry on the Formation and Morphology of Complex Intermetallic Compounds in Aluminum-Silicon Alloys”, Cast Metals, Vol. 6, No. 4, 1994, pp 217-224.
- 18 A. Flores, J. C. Escobedo, M. Mendez, and J. Mendez, “Kinetics of the Formation, Growth and Sedimentation of the Al15(Fe, Mn)3Si2 Phase in Al-Si-Cu Alloys”, Trans. of International Die Casting Congress and Exposition, Drtroit, Michigan, USA, Sept. 30 – Oct. 3, 1991, pp 293-297.
- 19 M. R. Ghomashchi, “Intermetallic Compounds in an Al-Si Alloy Used in High Pressure Die-Casting”, Z Metallkunde, 78 (1987), 11, pp 784-787.
- 20 G. Gustafsson, T. Thorvaldsson, and G. L. Dunlop, “The Influence of Fe and Cr on the Microstructure of Cast Al-Si_Mg Alloys”, Met. Trans. A. 17A (1986), pp 45-52.
- 21 M. C. Flemings, “Solidification Processing", McGraw., London, 1974.
- 22 L. Arnberg, L. Backerud, and A. Dahle, “Castability of Aluminum Foundry Alloys”, An AFS Research Report, AFS, 1999, pp24-31.
- 23 J. Campbell, “Review of Fluidity Concepts in Casting”, Cast Metals, Vol. 7, No. 4, 1995, pp227-237.
- 24 M. Tiryakioglu, D. R. Askeland, and C. W. Ramsay, “Fluidity of 319 and A356: An Experimental Design Approach”, AFS Trans. Vol. 102, 1994, pp17-25.
- 25 M. C. Flemings, E. F. Niiyama, and H. F. Taylor, “Fluidity of Aluminum: An Experimental and Quantitative Evaluation”, AFS Trans. Vol. 69, 1961, pp625-635.
- 26 M. C. Flemings, F. R. Mollard, E. F. Niiyama, and H. F. Taylor, “Fluidity of Aluminum: Surface Tension, Vibration and Heat Losses in Runner Systems Effect”, AFS Trans. Vol. 70, 1962, pp1029-1039.
- 27 S. Floreen and D. V. Ragone, “The Fluidity of Some Aluminum Alloys”, AFS Trans. Vol. 65, 1957, pp391-393.
- 28 M. R. Sheshradri and A. Ramachandran, “Casting Fluidity and Fluidity of Aluminum and its Alloys”, AFS Trans. Vol. 73, 1965, pp292-304.
- 29 E. N. Pan and J. F. Hu, “Study on Fluidity of Al-Si Alloys”, AFS Trans. Vol. 105, 1997, pp413-418.
- 30 G. W. P. Rengstorff and T. R. Baruch, “Surface Energy Effect on Flow of Molten Metal in Thin Section”, AFS Trans. Vol. 70, 1962, pp920-923.
- 31 P. Bastien, J. C. Armbruster, and P. Azou, “Flowability and Viscosity”, AFS Trans. Vol. 70, 1962, pp400-409.
- 32 J. L. Jorstad, “Machinability of 380 Alloy: Effect of Minor Elements and Impurities", 10th SDCE International Die Casting Exposition & Congress, March 19-22, 1979, St. Louis, Missouri, Paper No. G-T79-072.
- 33 J. L. Jorstad, “Influence of Aluminum Casting Alloy Metallurgical Factor on Machinability", Modern Casting, December 1980, pp47-51.
- 34 R. C. Lemon, “Metallurgical Factor Related to Machining Aluminum Castings”, SAE Congress and Exposition, January 1967, Paper No. 607465.
- 35 D. L. Colwell, “Zinc in Aluminum Casting Alloys”, AFS Trans. Vol. 60, 1952, pp517-524.
- 36 R. C. Lemon, “Free Machining Aluminum Casting Alloys X310 and X335”, AFS Trans. Vol. 71, 1963, pp315-318.
- 37 C. A. Queener and W. L. Witchell, “Effect of Iron Content and Sodium Modification on the Machinability of Aluminum Alloy Die Castings”, AFS Trans. Vol. 73, 1965, pp14-19.
- 38 J. M. Fox, “Aluminum Alloy Casting Inclusions”, AFS Trans. Vol. 69, 1961, pp737-742.
- 39 G. L. Armstrong, “Metallurgical Defects Encountered in Machining Aluminum Die Castings", Trans. of the Society of Die Casting Engineers, March 1975, Paper No. G-T75-011.
9. 著作権:
*この資料は、Makhlouf M. MakhloufとDiran Apelianの論文「Casting Characteristics of Aluminum Die Casting Alloys」に基づいています。
*論文ソース:[DOI URL] (DOI URLがドキュメントに提供されていません。利用可能な場合は追加してください)
この資料は上記の論文に基づいて要約されたものであり、商業目的での無断使用は禁止されています。
Copyright © 2025 CASTMAN. All rights reserved.