本紹介資料は、【NADCA】が発行した【"アルミニウム高圧ダイカストにおけるプロセスパラメータと品質特性の相関関係"】論文の研究内容です。
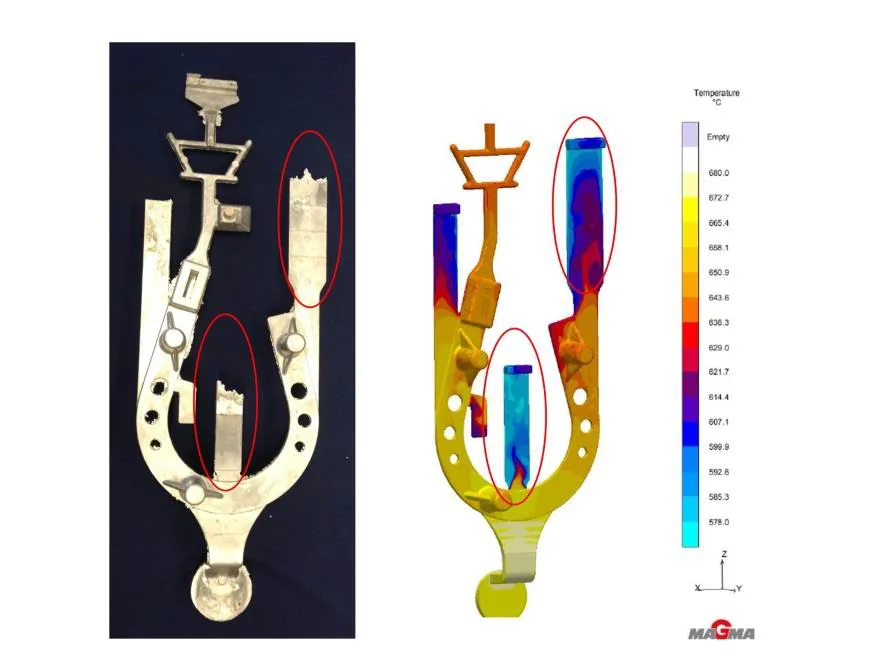
1. 概要:
- タイトル: アルミニウム高圧ダイカストにおけるプロセスパラメータと品質特性の相関関係 (Correlation between process parameters and quality characteristics in aluminum high pressure die casting)
- 著者: M. Winkler, L. Kallien, T. Feyertag
- 出版年: 2015
- 発表ジャーナル/学会: DIE CASTING CONGRESS & EXPOSITION, NORTH AMERICAN DIE CASTING ASSOCIATION
- キーワード: (論文に明示的なキーワードがないため、提供されたドキュメントに基づいてこのセクションを埋めることはできません。)
2. 概要 (Abstract)
アルミニウム高圧ダイカストは、最も生産性の高い製造プロセスの1つです。 部品の複雑さが増し、品質要件が高まっています。 高圧ダイカストの課題は、多数の品質に影響を与えるプロセスパラメータにもかかわらず、高い品質基準を達成することです。 すべての品質影響パラメータの相互作用は、最大10〜25%の非常に高いスクラップ率につながります。 これらのパラメータは、ダイカストマシン、炉、温度調節システムなど、プロセスのさまざまなシステムによって一元的に監視されていません。 現在、プロセスで測定されている典型的なパラメータは、第1段階と第2段階のピストン速度、強化圧力などです。 しかし、排気された空気の湿度など、部品の品質を制御する多くのパラメータがあります。
欧州の研究プロジェクトMUSIC(MUlti-layers control and cognitive System to drive metal and plastic production line for Injected Components)は、すべての品質管理パラメータを考慮したインテリジェントな認知システムを開発することにより、高圧ダイカストのスクラップ率を削減することを目的としています。 このプロジェクトの枠組みの中で、収縮気孔率、コールドシャット、歪みなどのいくつかの欠陥を持つ部品の製造を可能にする特別な鋳造形状が開発されました。 ダイには、ショット音など、これまで適用されていなかった新しいプロセスパラメータを監視するために、多くの新しい革新的なセンサーが装備されています。 センサーデータ、機械および周辺機器のプロセスパラメータは、鋳物の品質指数とともに1つの共通データベースに保存されます。 その後、認知ネットワークは、測定されたセンサーデータに基づいて将来の部品の品質指数を計算できるようになります。
3. 研究背景:
研究テーマの背景:
革新的な自動車の車体構造において、高圧ダイカスト部品の数が増加しています。 構造要素としてアルミニウム部品を使用する理由は、軽量化です。
先行研究の状況:
高圧ダイカスト(HPDC)は、良好な表面品質、高い寸法精度、および高い引張強度を備えた部品を製造する生産性の高い製造方法です。 ただし、多数のパラメータが部品の品質に影響します。 従来のデータ収集(図2)には、ピストン速度、切り替えポイント、昇圧圧力、加熱油温度、炉温度、スプレーユニットパラメータなどのパラメータが含まれます。 これらは通常、個々のユニットによって制御および測定されます。 他の影響パラメータ(湿度、排気空気量、プランジャー加速度、合金組成の変動など)は、通常、測定または保存されません。
研究の必要性:
すべての品質影響パラメータ間の相互作用により、10〜25%の高いスクラップ率が発生します。 この値は、他の製造プロセスのスクラップ率の10倍、あるいは1000倍を超えています。
4. 研究目的と研究課題:
研究目的:
欧州の研究プロジェクトMUSIC(MUlti-layers control and cognitive System to drive metal and plastic production line for Injected Components)は、高圧ダイカストのスクラップ率を削減することを目的としています。
コア研究:
すべての品質管理パラメータを考慮したインテリジェントな認知システムを開発することにより、スクラップ率を削減します。
5. 研究方法論
この研究では、センサーネットワークと認知システムを活用しています(図3)。 高圧ダイカストマシンと周辺機器にはセンサーが装備されています。 すべてのデバイスは、1つの共通データベースに接続されたネットワークに接続されています。 このデータベースには、すべてのセンサーデータと、機械および周辺機器の制御されたプロセスパラメータが保存されます。
欠陥(収縮気孔、コールドシャット、歪み)を意図的に生成するために、特別な鋳造形状(図4)が設計されました。 ダイには、さまざまなプロセスパラメータを監視するためのセンサーが装備されています。
鋳造部品の最終設計を検証するために、MAGMAを使用して充填および凝固シミュレーションが実行されました。
認知モデルのトレーニングは、鋳造欠陥を予測するための最初のステップです。 このための基礎は、プロセスおよび品質データの可用性です。 データは、実験計画法(DoE)中に取得されます。
すべての鋳物の同じ基準を分析するために、品質管理手順が定義されました。
6. 主要な研究結果:
主要な研究結果と提示されたデータ分析:
- さまざまなキャビティ圧力信号の比較を図8に示します。
- 真空システムと組み合わせた空気質量センサー信号が提示されます。 図10は通常のショットを示し、図11は真空チャネルに漏れがあるショットを示しています。
- 長いスプレーサイクルと短いスプレーサイクルの後の湿度センサー信号を図12に示します。
- パラメータ、センサーデータ、および品質結果の間の依存関係を示すために、相関行列(表1)が生成されました。
- Design-Expert®ソフトウェアからの、品質指数、温度、およびピストン速度の間の相互作用を示す3Dダイアグラムの例を図13に示します。
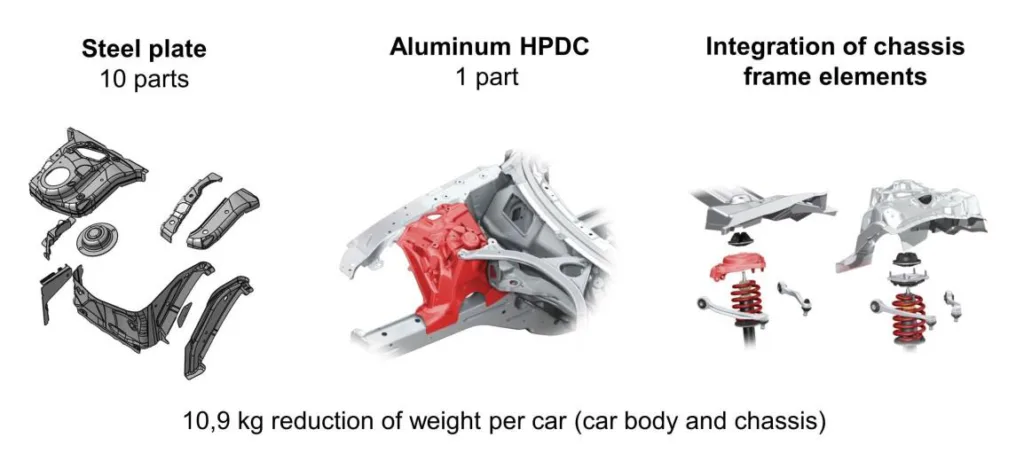
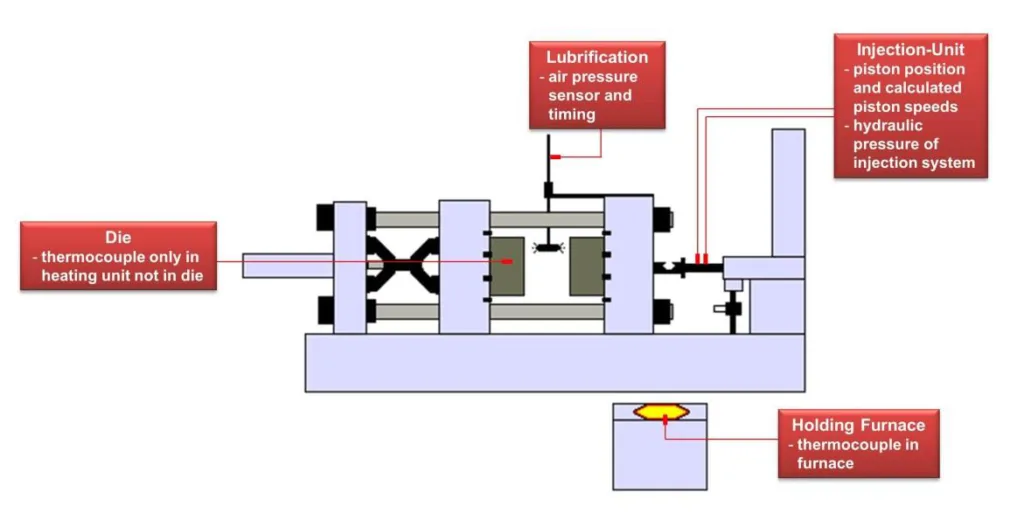

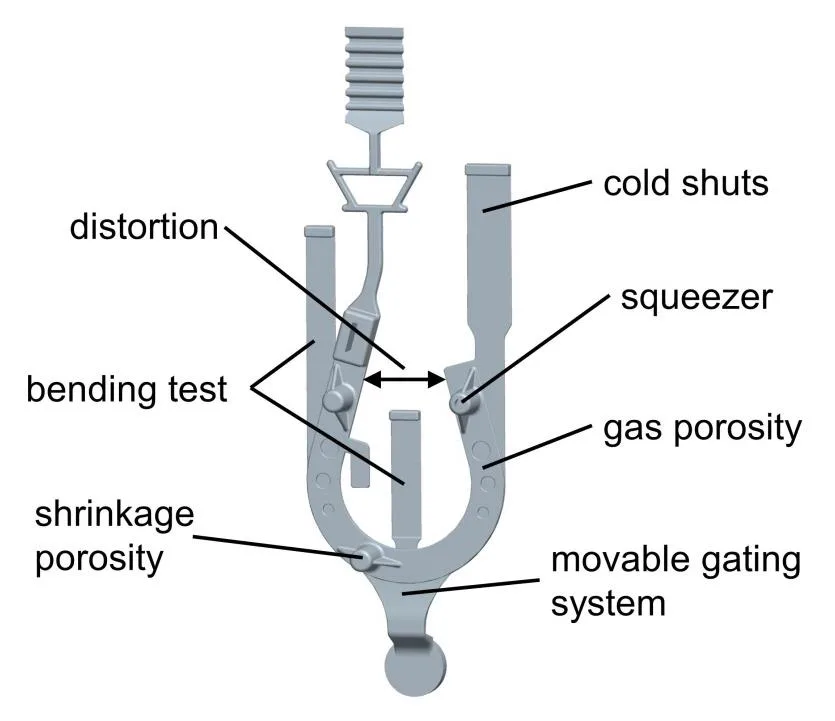
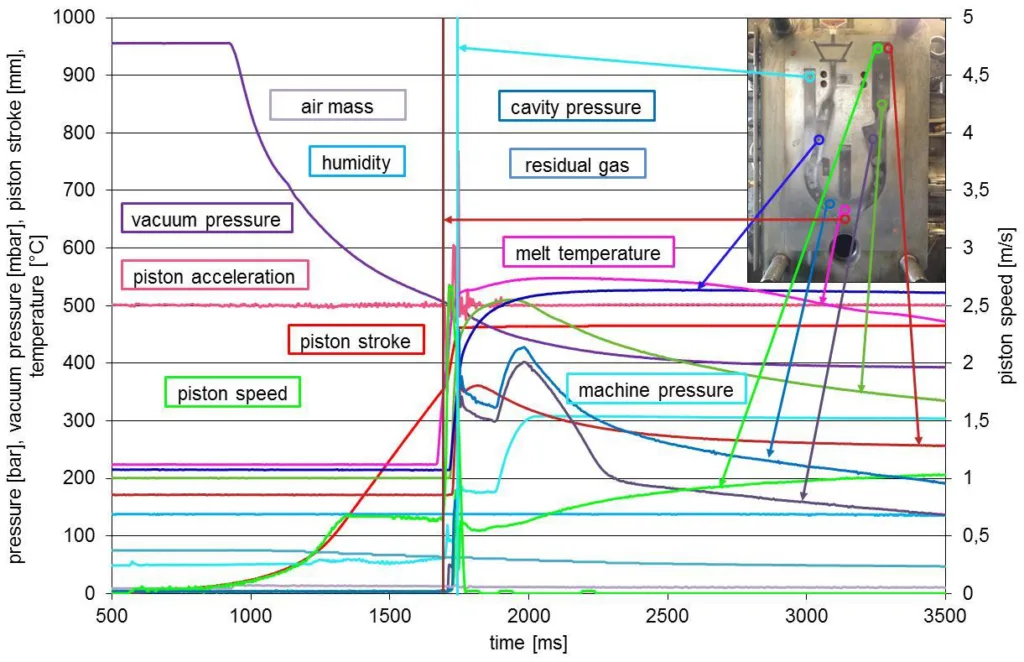
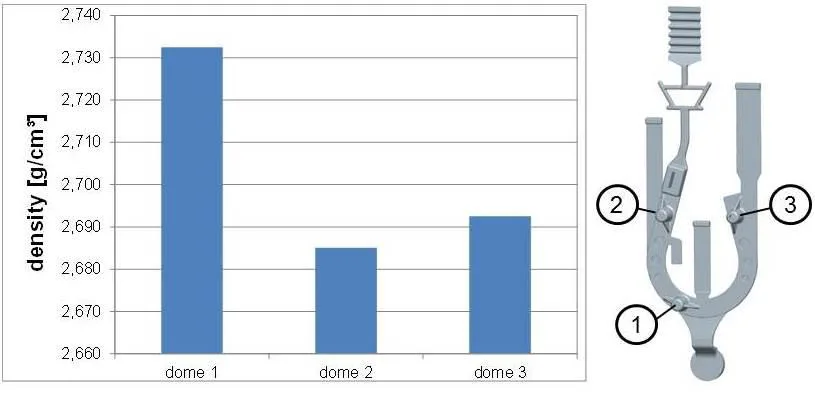
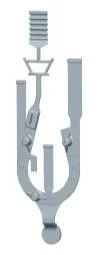
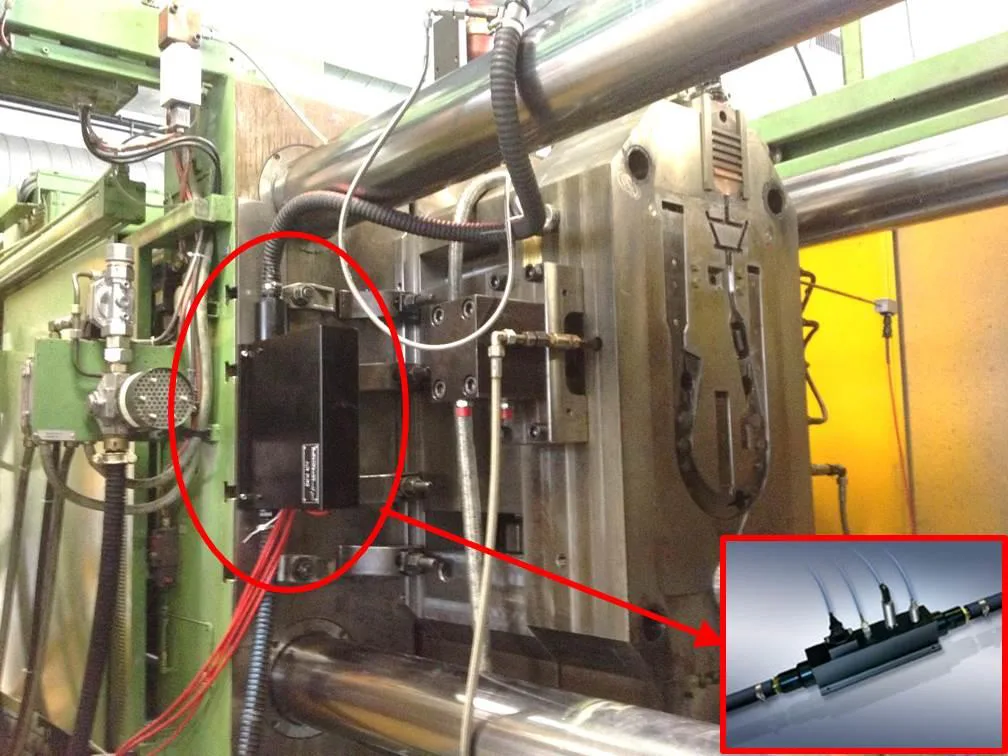
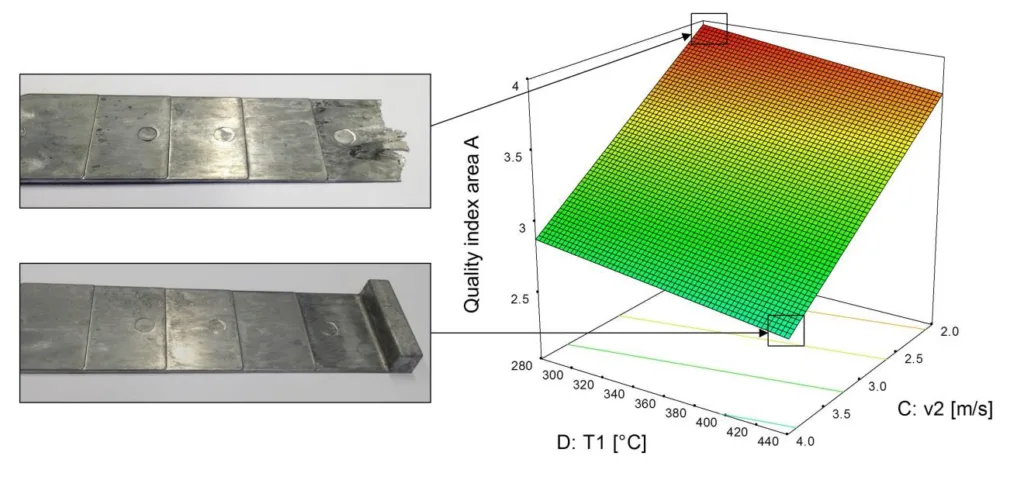
図の名称リスト:
- 図1:接合された鋼部品の代わりに構造用アルミニウム高圧ダイカスト部品を使用して軽量化[1]
- 図2:HPDCプロセス中の従来のデータ収集
- 図3:革新的なセンサーネットワークと認知システム
- 図4:欠陥を生成するための特別な鋳造形状
- 図5:実際の鋳造部品とコールドシャットに関するシミュレーション結果の比較[2]
- 図6:追加のセンサー信号を含むショットカーブ
- 図7:ドーム領域の密度の比較
- 図8:昇圧あり(センサー信号のオレンジ色)および昇圧なし(センサー信号の緑色)のキャビティ圧力センサー信号を含むショットカーブ
- 図9:アーレンの鋳造研究所の750tコールドチャンバーマシンに組み立てられたマルチエアパイプセンサーシステム[4]
- 図10:真空チャネルに漏れがない真空および空気質量信号を示すショットカーブ
- 図11:真空チャネルに漏れがある真空および空気質量信号を示すショットカーブ
- 図12:長い(青)および短い(黄)スプレーサイクルの後に測定された真空および湿度センサー信号を示すショットカーブ
- 図13:領域「A」の品質指数、第2段階のピストン速度、および温度センサー信号T1の相互関係
7. 結論:
主要な調査結果の要約:
キャビティ圧力センサーは、鋳造のさまざまな領域の圧力を監視しています。 これらは、供給効率に関する情報を提供し、特に鋳造部品の厚い領域で密度を予測するのに役立ちます。
空気質量センサーを使用すると、排気された空気の量を測定し、真空チャネルの漏れを検出できます。 不十分な排気による閉じ込められた空気に関して、鋳造部品の密度を予測するのに役立ちます。
湿度センサーを使用すると、ダイに残っている湿度を最小限に抑えて、スプレーサイクルを改善できます。
相関関係は、認知モデルをトレーニングし、品質検査なしで鋳造部品の品質を予測するのに役立ちます。 これは、品質管理の労力を削減し、スクラップ率を削減する絶好の機会です。
OPC-UAを介したすべてのデバイスの接続により、データの取得だけでなく、HPDCマシンおよび周辺機器の制御に入力変数を送信することもできます。 つまり、システムは、定義されたしきい値内で特定の品質影響パラメータを調整することにより、プロセスを最適化できます。
8. 参考文献:
- [1] Wanke, P., Innovative Strukturgusskonzepte bei AUDI, AUDI AG, Gießereikolloquium Hochschule Aalen, (2012年5月9日)
- [2] Kallien, L., Winkler, M., Kognitives System zur Reduzierung der Ausschussrate im Druckguss, Horizonte, (2015年4月/5月)
- [3] Bonollo, F., Gramegna, N., et al., The MUSIC guide to key-parameters in High Pressure Die Casting, MUSIC Consortium (2014)
- [4] http://www.electronics-gmbh.de/electronics/english/produkt_multisensor.htm
9. 著作権:
- この資料は、"[M. Winkler, L. Kallien, T. Feyertag]"による"[アルミニウム高圧ダイカストにおけるプロセスパラメータと品質特性の相関]"論文に基づいています。
- 論文の出典: [元のドキュメントにDOI URLが含まれていません。 ]
この資料は、上記の論文を紹介するために作成されたものであり、商業目的での無断使用を禁じます。 Copyright © 2025 CASTMAN. All rights reserved.