この入門論文は、[Acta Mechanica Slovaca]によって発行された論文「"Use of Duplex PVD Coatings to Increase the Life of Moulds and Cores for die Casting of Aluminium Alloys in the Automotive Industry"」の研究内容を紹介するものです。
1. 概要:
- タイトル: Use of Duplex PVD Coatings to Increase the Life of Moulds and Cores for die Casting of Aluminium Alloys in the Automotive Industry
- 著者: Janette Brezinová, Ján Viňáš, Miroslav Džupon, Dagmar Jakubeczyová, Jakub Brezina, Henrich Sailer, Ján Hašuľ, Michal Považan
- 発行年: 2022年
- 発行ジャーナル/学会: Acta Mechanica Slovaca
- キーワード: PVD coatings, laser surface remelting, die casting of aluminium, tribology
![Table 1: Chemical composition of Uddeholm Dievar [15]](https://castman.co.kr/wp-content/uploads/image-1323-png.webp)
![Table 2: Mechanical properties of Uddeholm Dievar [15]](https://castman.co.kr/wp-content/uploads/image-1324-png.webp)
2. 概要または序論
本稿では、自動車産業向け部品を対象とした高圧アルミニウムダイカストにおける金型およびコアの寿命延長を目的とした研究成果を詳述する。手法としては、Uddeholm Dievar金型鋼の表面に局所的なインパルス加熱を3段階の加熱速度で適用した。表面処理後、構造解析を実施し、続いてLarc技術を用いてPVD nACRo³コーティングを施した。コーティング品質の評価は、スクラッチ試験およびメルセデス試験によって行った。レーザー処理とnACRo³コーティングを施した後の表面微細形状は、ISO 25 178に準拠して評価した。その後、コーティングされた表面を680 ± 20℃の温度でAl-Si系合金溶融液に120分および300分間浸漬した。実験の結果、金型表面の耐性が著しく向上したことが確認された。
序論では、自動車産業におけるアルミニウムおよびプラスチック鋳造品の重要性を強調しており、これらは主にダイカストおよび射出成形用の金属金型を用いて製造されている。ダイカスト金型は、通常、クロムまたは工具鋼でできており、29~48 HRCの硬度に熱処理されており、金型の寿命は大量生産の生産性に大きく影響する重要な要素である。金型の損傷は、用途によって異なり、一般的な損傷として、工具表面に微細な亀裂のネットワークまたは個別の亀裂として観察される熱疲労亀裂がある。熱疲労亀裂の発生は、表面材料が小さな破片の形で失われる原因となる。その他の一般的な損傷原因としては、構造的なノッチによる引張亀裂、工具への鋳造合金の局所的な凝着(はんだ付け)、溶融金属またはプラスチックの鋳造によって助長される鋼のエロージョンなどがある。プラスチック射出成形金型は、より低い運転温度にさらされるが、圧力サイクルはより厳しく、そのため機械疲労損傷や過負荷による破損が発生する可能性がある [1]。アルミニウム合金鋳造用の金型部品およびコアは、高温下で適切な物理的および機械的特性を備えている必要があり、これらの特性は、熱的および機械的応力、ならびに金型とアルミニウム合金溶融液との界面での相互作用によって基本的に定義される。特に、アルミニウム合金溶融液による金型キャビティの乱流から分散充填への高速性、溶融液によって金型部品に発生する高い流体力学的圧力、および金型部品表面の比較的高温は、金型およびコアの寿命を著しく短縮する可能性がある。これらの現象はすべて、エロージョン、アブレーション、腐食、および金型の熱疲労のメカニズムによって、成形部品の表面劣化を引き起こし、それぞれが同時に作用する。
3. 研究背景:
研究課題の背景:
アルミニウムおよびプラスチック鋳造品は自動車産業において極めて重要であり、主にダイカストおよび射出成形によって金属金型を用いて製造されている。ダイカスト金型は、通常、クロムまたは工具鋼でできており、29~48 HRCに熱処理されており、その寿命と生産効率に影響を与える重大な課題に直面している。金型寿命はダイカストの生産性における重要な要素であり、鋳造品または金型の用途に応じてさまざまな種類の金型損傷によって大きく影響を受ける。熱疲労亀裂は一般的な破損モードであり、工具表面に微細な亀裂のネットワークまたは個別の亀裂として現れ、材料の損失につながる。その他の損傷原因としては、構造的不規則性による引張亀裂、はんだ付け(鋳造合金の局所的な凝着)、および鋼のエロージョンなどがある。これらの劣化メカニズムは、アルミニウム溶融液射出中の高い流体力学的圧力と温度によって悪化し、エロージョン、アブレーション、腐食、および熱疲労を引き起こす [2]。
既存研究の現状:
現在の産業界では、工具や機械部品の表面保護と処理に重点が置かれている。しかし、最終表面仕上げ方法の進歩は遅れている。最終表面処理方法の研究開発は、主に学術機関や専門の研究室に集中している [6]。より優れた特性を実現し、新たな応用を可能にする革新的な表面仕上げ技術が開発されている。表面の前処理は、適切なコーティングの堆積を保証し、望ましい耐用年数と耐久性を達成するために不可欠である [7]。金属の加圧鋳造用工具および金型の摩耗は、主に熱疲労、研磨、浸食、および溶融金属の金型機能表面への腐食作用に起因し、表面形状の変化や溶融物の固着を引き起こす [8]。
研究の必要性:
金型表面の劣化を軽減するための潜在的な解決策として、溶融アルミニウムと接触する部品の表面処理が挙げられる。過酷な鋳造条件(熱的および化学的作用)により、金型表面は損傷を受けやすく、金型寿命は重要な懸念事項となっている。PVDコーティングの堆積に続いて、熱処理された工具のレーザー硬化は、耐性を高めるための有望なアプローチである。この方法は、コーティング前のレーザー前処理を利用して、より優れた表面接着特性を実現する [9]。ヨーロッパの自動車生産のかなりの部分を占めるスロバキア共和国の自動車産業は、より軽量で経済的、かつ環境に優しい車両に戦略的に焦点を当てている。鋼鉄部品を軽金属合金、特に費用対効果の高いダイカスト技術 [10] によって製造されたアルミニウム鋳造品に置き換えることが、重要な戦略となっている。合金特性、金型設計、および運転パラメータを含むダイカスト技術の最適化は、生産効率と鋳造品質にとって不可欠である。金型設計と技術寿命は決定的な要因であり、鋳造品質の要件と技術パラメータの許容範囲によって制限される [11]。
4. 研究目的と研究課題:
研究目的:
主な研究目的は、自動車産業向けアルミニウム合金の高圧ダイカストで使用される金型およびコアの耐用年数を延長することである。これは、レーザー表面再溶融技術と組み合わせて、二重PVDコーティングを適用することによって達成される。
主な研究課題:
主な研究課題は、レーザー処理されたUddeholm Dievar鋼表面における二重PVDコーティング、特にAIXN³およびnACRo³の有効性を評価することに焦点を当てている。本研究では、熱疲労、エロージョン、アブレーションなど、アルミニウムダイカストで一般的な劣化メカニズムに対する金型表面の耐性向上を調査する。また、適用されたコーティングの密着性と微細形状、およびダイカスト条件をシミュレートした条件下での性能を特性評価することを目的としている。
5. 研究方法
研究デザイン:
本研究では、局所的な高強度レーザー加熱を用いたUddeholm Dievar鋼サンプル表面の表面処理、続いてLarc技術を用いた二重PVDコーティング(AIXN³およびnACRo³)の堆積を含む実験的デザインを採用している。レーザー処理なしの対照サンプルも作成した。処理およびコーティングされたサンプルを、コーティング品質および表面特性を評価するためのさまざまな評価方法に供した。これらの方法には、スクラッチ試験、メルセデス試験、ISO 25 178に準拠した表面微細形状解析、およびダイカスト条件をシミュレートするための溶融Al-Si合金への浸漬が含まれる。
データ収集方法:
データは、いくつかの実験的手法を通じて収集された。
- スクラッチ試験およびメルセデス試験: コーティングの密着性-凝集挙動を評価するため。メルセデス試験は、1500 Nの荷重でロックウェル圧子を使用し、DIN EN ISO 18265に従って評価し、密着性番号HF1~HF6を使用して分類した [19]。
- 表面微細形状解析: ISO 25 178規格に従って評価し、レーザー処理およびコーティング後の表面粗さとトポグラフィーパラメータを定量化した。
- 浸漬試験: サンプルを680 ± 20℃のAl-Si合金溶融液に120分および300分間浸漬し、溶融金属の攻撃に対するコーティングの耐性を評価した。
- 顕微鏡観察(光学およびSEM): 表面欠陥、コーティング断面、および圧痕形状の目視検査に使用した。
- EDX微量分析: 局所的な化学組成を決定するため。
- 微小硬さ試験: コーティングおよび基板全体の硬さプロファイルを評価するため。
- 毛細管試験: 摩耗した金型インサートの表面および表面下の欠陥を特定するため。
分析方法:
- 定性分析: 表面欠陥、亀裂伝播、およびコーティングの完全性の目視検査および顕微鏡観察。HFスケールに基づくメルセデス試験圧痕の評価。
- 定量分析: スクラッチ試験の臨界荷重、ISO 25 178解析からの表面粗さパラメータ(Sa、Sq、Ssk、Sku、Sp、Sv、Sz)、および微小硬さ値の測定。異なる処理条件を比較するための表面パラメータデータの統計分析。
- 比較分析: AIXN³コーティングとnACRo³コーティングの間、およびレーザー処理サンプルと非レーザー処理サンプルの間の結果を比較し、複合表面処理アプローチの有効性を判断した。
研究対象と範囲:
研究対象は、ダイカスト金型およびコアに一般的に使用されるクロム-モリブデン工具鋼であるUddeholm Dievar鋼製のサンプルであった。研究の範囲は、これらの鋼サンプルに適用された二重PVDコーティング(AIXN³およびnACRo³)の調査に限定され、自動車産業におけるアルミニウムダイカスト用途での性能に焦点を当てている。本研究では、コーティングの密着性と性能を向上させるための前処理としてのレーザー表面再溶融の効果を特に検証する。
6. 主な研究成果:
主な研究成果:
- 金型表面耐性の向上: 実験の結果、レーザー表面再溶融と二重PVDコーティング(AIXN³およびnACRo³)の適用後、金型表面の耐性が著しく向上したことが確認された。
- 良好なコーティング密着性: スクラッチ試験およびメルセデス試験の結果、AIXN³およびnACRo³コーティングはいずれも良好な密着性を示した。メルセデス試験では、密着性はHF 1~2に分類され、圧痕周辺の亀裂が最小限であり、良好から満足のいく密着性を示した。
- 表面微細形状: ISO 25 178に準拠して評価された表面微細形状パラメータは、レーザー表面前処理および研削が、研削された表面と比較して、二重PVDコーティングの表面パラメータに有意な影響を与えなかったことを示した。
- 硬さの向上: 微小硬さ測定では、レーザー処理された基板上のコーティング領域で、基板材料と比較して18.6~25% HV0.025の硬さの増加が示された。
- 溶融アルミニウムに対する耐性: 680 ± 20℃の溶融Al-Si合金に浸漬した後、コーティングはコンパクトで無傷のままであり、母材と溶融液の間にバリアを形成し、高温腐食に対する耐性を示した。
- レーザー硬化パラメータ: レーザー表面硬化は、400 Wレーザーと3 mmビーム径を使用して、走査速度20 mm/s、30 mm/s、40 mm/s、および60 mm/sで、それぞれ160 μm、90 μm、80 μm、および75 μmの加熱深さを達成した。
提示されたデータの分析:
- 硬さプロファイル(図10): 図10は、nACRo³およびAIXN³コーティングの両方について、表面から基板に向かう硬さプロファイルHV0.025を示している。両方のコーティングで表面の硬さ値が高く、基板に向かって減少し、基板硬さ(W300)に近づいていることがわかる。nACRoコーティングされたサンプルの0.025 HVmの圧痕は、レーザーゾーンとW300基板の界面に示されている。
- 表面パラメータ(表4): 表4は、ISO 25 178に準拠したPVDコーティングの表面パラメータを示している。PVDコーティング二重nACRo³、PVDコーティング二重AIXN³、レーザー処理表面上のPVDコーティング二重nACRo³、およびレーザー処理表面上のPVDコーティング二重AIXN³のSq、Ssk、Sku、Sp、Sv、Sz、およびSa値を比較している。データは、レーザー前処理が表面微細形状パラメータを大きく変化させなかったことを示している。
- メルセデス試験(図12および13): 図12および図13は、AIXN³およびnACRo³コーティングのメルセデス試験からの圧痕形状を示している。画像は、孤立した放射状の亀裂のみを示しており、良好なコーティング品質と密着性を確認しており、HF 1-2の密着性度に対応している。
図のリスト:
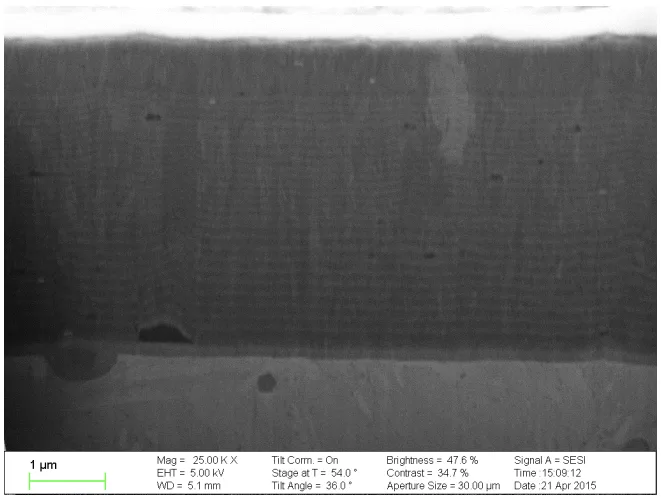
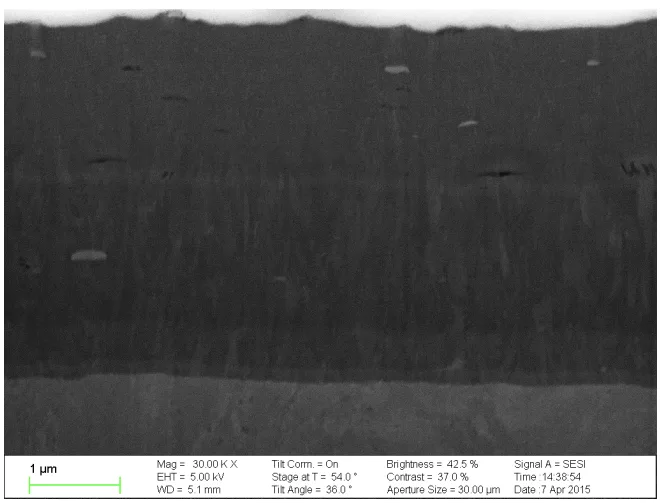
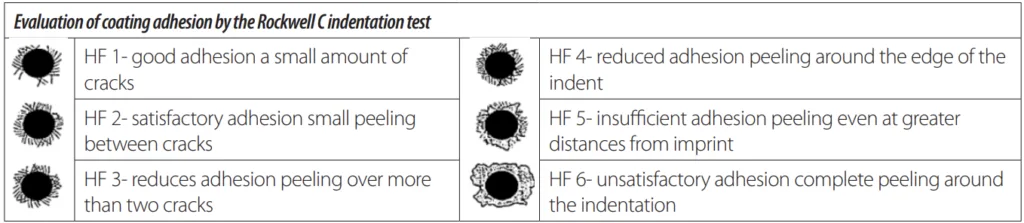
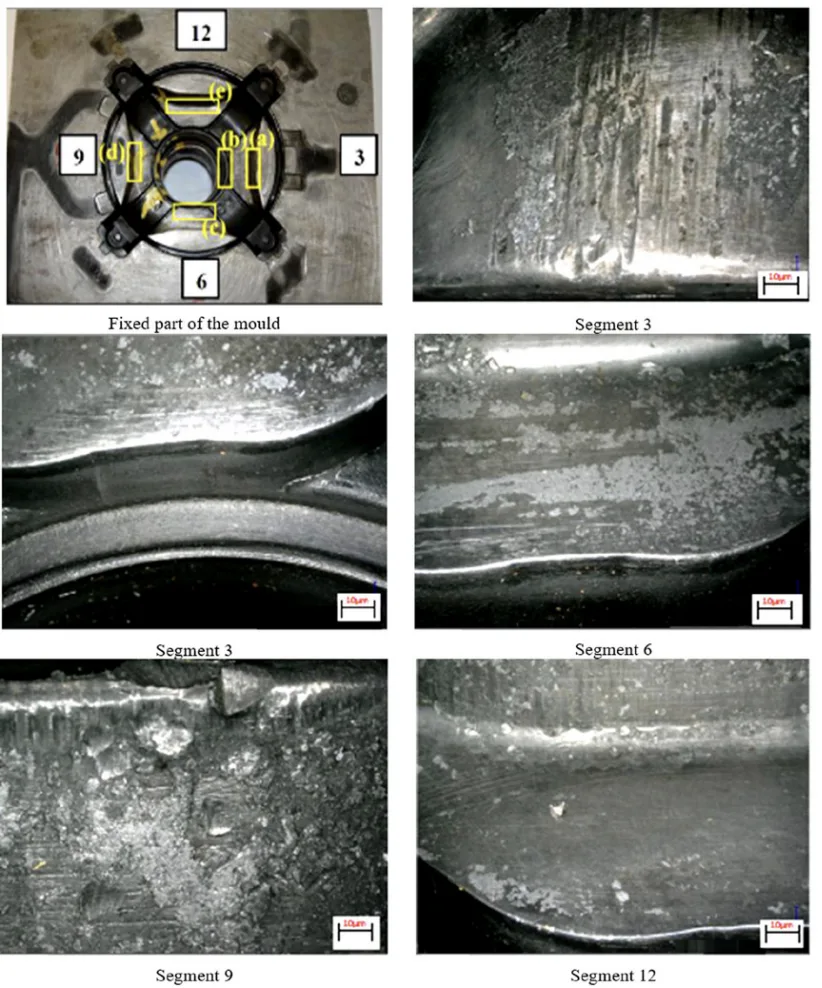
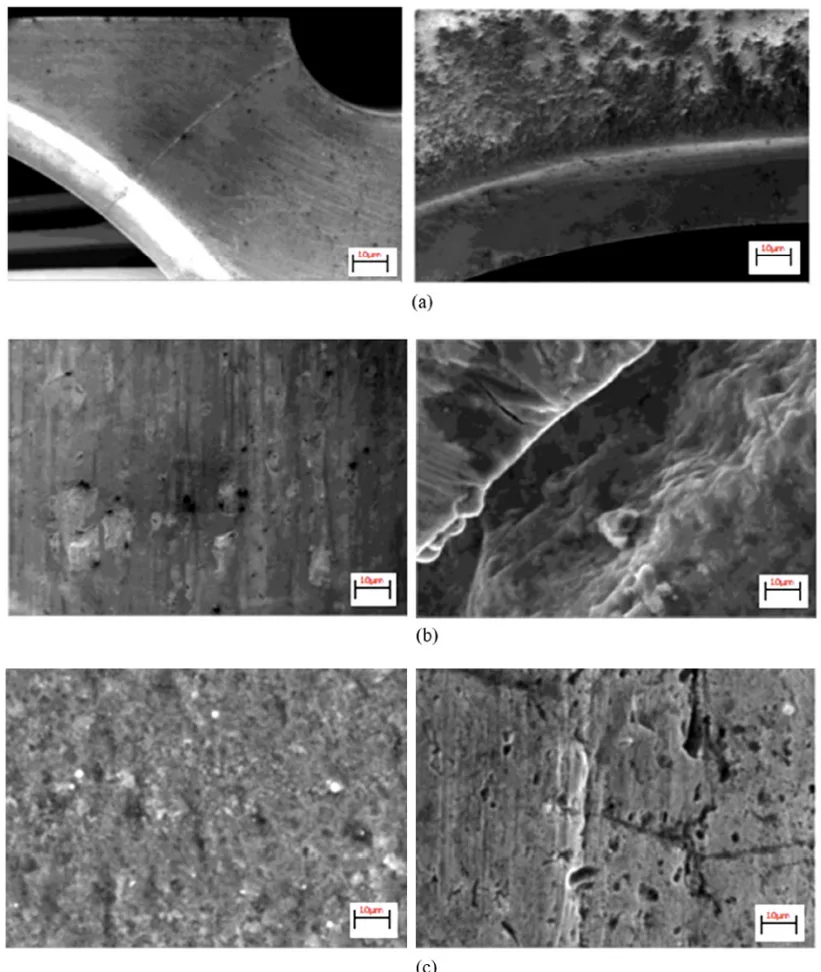
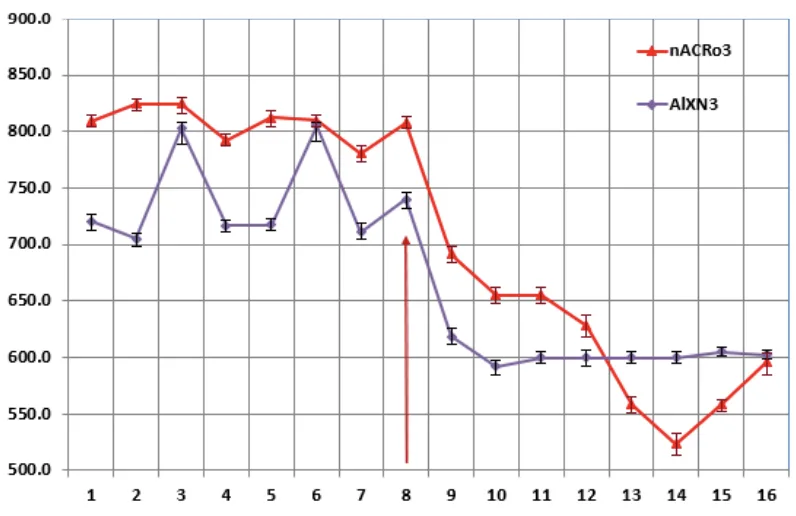
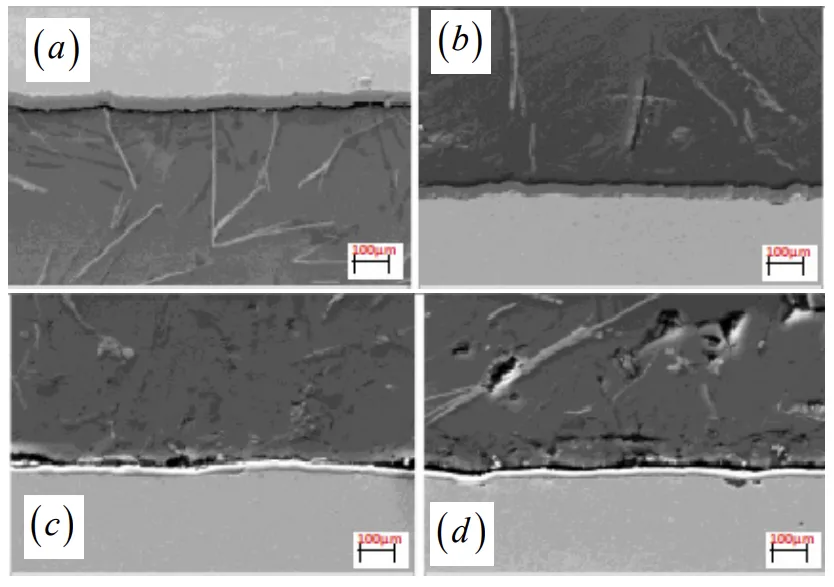
- 図 1: FIB(集束イオンビーム)装置で作製されたAIXN³コーティングの断面
- 図 2: FIB装置で実施されたnACRo³コーティングの断面
- 図 3: 摩耗した金型部品のソリッドハーフ - 金型インサート
- 図 4: 毛細管試験後の金型成形部品
- 図 5: 金型底部における亀裂の外観
- 図 6: 摩耗形態の詳細; a) エジェクタとコアキャビティ周辺の亀裂 b) 成形部品表面の分離手段 c) 可動コアと成形部品の接触部
- 図 7: レーザー表面硬化
- 図 8: 対照サンプルおよびレーザー処理とコーティング堆積後のサンプルのPVDコーティング表面
- 図 9: nACRoコーティングされたサンプルの圧痕
- 図 10: 表面から基板に向かう硬さ試験HV0.025
- 図 11: スクラッチ試験システム o PVDコーティング - レーザー熱処理基板; a) PVDコーティング二重AIXN³; b) PVDコーティング二重nACRo³; c) レーザー処理表面上のPVDコーティング二重AIXN³; d) レーザー処理表面上のPVDコーティング二重nACRo3
- 図 12: AIXN3コーティング(X = Cr)における圧痕形状
- 図 13: nACR03、LMコーティングへの圧痕形状
- 図 14: Al溶融液に曝露後のレーザー処理および研削表面上のPVDコーティング二重層; a) 二重AIXN³/120分/680+/-20℃/Al-Si; b) 二重AIXN³/300分/680+/-20℃/Al-Si; c) 二重nACRo³/120分/680+/-20℃/Al-Si; d) 二重nACRo³/300分/680+/-20℃/Al-Si
7. 結論:
主な調査結果の要約:
本研究では、局所的なレーザー表面再溶融と二重PVDコーティング(AIXN³およびnACRo³)を組み合わせた、ダイカスト金型およびコア用の革新的な表面処理方法を実証した。このアプローチにより、アルミニウムダイカスト環境における劣化に対する金型表面の耐性が大幅に向上した。適用されたPVDコーティングは、高品質で強力な密着性を示し、溶融アルミニウムおよび高温腐食に対する効果的なバリアとして機能した。表面微細形状は、レーザー前処理および研削によって大きく変化しなかった。
研究の学術的意義:
本研究は、ダイカスト金型の劣化メカニズムの基本的な理解に貢献し、高度な表面工学技術を通じて金型寿命を延ばすための検証済みの方法論を提供する。本研究は、過酷なダイカスト条件下での工具鋼の性能を向上させるにおけるレーザー表面再溶融と二重PVDコーティングの相乗効果を強調している。
実際的な意義:
本研究の知見は、自動車産業およびダイカスト産業にとって大きな実際的な意義を持つ。開発された表面処理方法は、ダイカスト金型およびコアの耐用年数を延長するための実行可能なソリューションを提供し、工具コストの削減、生産効率の向上、および鋳造品質の向上につながる。これは、自動車分野における軽量アルミニウム部品の製造、より経済的で環境に優しい車両の開発に特に重要である。
研究の限界と今後の研究分野:
本研究は、実験室規模の実験とシミュレートされたダイカスト条件に焦点を当てた。今後の研究は、以下に焦点を当てる必要がある。
- 産業規模での検証: 開発された表面処理方法を産業用ダイカスト作業でテストし、実際の生産環境での性能とスケーラビリティを評価する。
- 長期性能評価: 連続ダイカストサイクル下での処理された金型およびコアの寿命延長を評価するために、長期耐久性試験を実施する。
- レーザーおよびコーティングパラメータの最適化: コーティング性能と効率を最大化するために、レーザー表面再溶融およびPVDコーティングパラメータをさらに最適化する。
- 経済分析: 従来の金型メンテナンスおよび交換戦略と比較して、提案された表面処理方法の費用対効果を定量化するために、包括的な経済分析を実施する。
- 他のコーティング材料の調査: 金型表面特性と特定の劣化メカニズムに対する耐性をさらに向上させるために、他の高度なPVDコーティング材料と組成を調査する。
8. 参考文献:
- [1] Changrong Chen et al.: Energy based approach to thermal fatigue life of tool steels for die casting dies. In: International Journal of Fatigue Volume 92, Part 1, November 2016, Pages 166-178.
- [2] J. Lin et al.: Design methodology for optimized die coatings: The case for aluminium pressure die-casting In: Surface and Coatings Technology 201 (2006) pp. 2930-2941.
- [3] K. Domkin, J.H. Hattel, J. Thorborg, Modeling of high temperature- and diffusion-controlled die soldering in aluminium high pressure die casting, J. Mater. Process. Technol. 209 (8) (2009) 4051-4061.
- [4] Sundqvist M., Hogmark S.: Effects of liquid aluminium on hot-work tool steel Tribol. Int. 26 (1993) in International Journal of Fatigue p. 129.
- [5] H. Zhu, J. Guo, J. Jia, Experimental study and theoretical analysis on die soldering in aluminium die casting, J. Mater. Process. Technol. 123 (2) (2002) 229-235.
- [6] Z.W. Chen, M.Z. Jahedi, Die erosion and its effect on soldering formation in high pressure die casting of aluminium alloys, Mater. Des. 20 (6) (1999) 303-309.
- [7] K. Venkatesan, R. Shivpuri, Experimental and numerical investigation of the effect of process parameters on the erosive wear of die casting dies, J. Mater. Eng. Perform. 4 (2) (1995) 166-174. R. Markežič et al. Engineering Failure Analysis 95 (2019) 171-180179.
- [8] A Mohammed, M.B. Marshall, R. Lewis, Development of a method for assessing erosive wear damage on dies used in aluminium casting, Wear 332-333 (2015)1215-1224.
- [9] LF. Hou, Y.H. Wei, Y.G. Li, B.S. Liu, H.Y. Du, C.L. Guo, Erosion process analysis of die-casting inserts for magnesium alloy components, Eng. Fail. Anal. 33 (2013)457-564.
- [10] D.W.C. Baker, K.H. Jolliffe, D. Pearson, The resistance of materials to impact erosion damage, Philos. Trans. R. Soc. A Math. Phys. Eng. Sci. 260 (1110) (1966) 193-203.
- [11] A. Persson, S. Hogmark, J. Bergström, Temperature profiles and conditions for thermal fatigue cracking in brass die casting dies, J. Mater. Process. Technol. 152(2) (2004) 228-236.
- [12] C. Rosbrook, Analysis of Thermal Fatigue and Heat Checking in Die-Casting Dies: A Finite Element Approach, PhD thesis Ohio State University, 1992.
- [13] F. Medjedoub, G. Dour, S. Le Roux, P. Lamesle, M. Salem, P. Hairy, F. Rézaï-Aria, Experimental conditions and environment effects on thermal fatigue damage accumulation and life of die-casting steel X38CrMoV5 (AISI H11), Int. J. Microstruct. Mater. Propert. 3 (2-3) (2008).
- [14] P. Hansson, "Modern prehardened tool steels in die-casting applications," Materials and Manufacturing Processes, vol. 24, no. 7-8, pp. 824-827, 2009.
- [15] Uddeholm, "Dievar," 2014, (18.10.2021) internet: http://www.uddeholm.com
- [16] D. Klobčar, J. Tušek, B. Taljat, Thermal fatigue of materials for die-casting tooling, Mater. Sci. Eng. A 472 (1) (2008) 198-207.
- [17] D. Schwam, J. F. Wallace, and S. Birceanu, "Die Materials for Critical Applications and Increased Production Rates," Case Western Reserve University, 2002.
- [18] Methodical measurement and evaluation of adhesive cohesive behavior of thin film - substrate systems, 2005, (19.10.2021) internet: https://www.opi.zcu.cz/adheze.html
- [19] J. Tkáčová, E. Zdravecká, E. Evin, M. Tomáš, D. Jakubéczyová: Koroze a ochrana materiálu 63(4) 159-166 (2019).
- [20] D. Klobčar, et al.: Thermo fatigue cracking of die casting dies. In: Engineering Faliure Analysis Volume 20, March 2012, pp. 43-53.
- [21] D. Jakubéczyová, M. Džupon: Effect of the roughness on the adhesive properties of nanocomposite PVD coatings. In Vrstvy a povlaky 2016: 15. ročník konferencie. Rožnov pod Radhoštěm, 17.-18.10.2016. - Plzeň: Západočeská univerzita, 2016, p. . 49-55.(Layers and coatings 2016)
9. 著作権:
- この資料は、"Janette Brezinová et al."の論文:「"Use of Duplex PVD Coatings to Increase the Life of Moulds and Cores for die Casting of Aluminium Alloys in the Automotive Industry"」に基づいています。
- 論文ソース: https://doi.org/10.21496/ams.2022.003
この資料は上記の論文を紹介するために作成されたものであり、商業目的での無断使用は禁止されています。
Copyright © 2025 CASTMAN. All rights reserved.