1. 概要:
- タイトル: Effects of die-casting defects on the blister formation in high-pressure die-casting aluminum structural components (高圧ダイカストアルミニウム構造部品におけるブリスター形成に対するダイカスト欠陥の影響)
- 著者:
- Bartłomiej Dybowski (バルトロミエイ・ディボフスキ)
- Andrzej Kiełbus (アンジェイ・キェウブス)
- Łukasz Poloczek (ウカシュ・ポロチェク)
- 発行年: 2023年
- 発行学術誌/学会: Engineering Failure Analysis (工学破壊解析)
- キーワード:
- Blistering (ブリスター)
- High pressure die casting (高圧ダイカスト)
- Aluminum Alloys (アルミニウム合金)
- Heat treatment (熱処理)
- Microscopic characterization (顕微鏡観察)
2. 研究背景:
- 研究テーマの社会的/学術的背景:
- 高圧ダイカスト (HPDC) は、薄肉非鉄金属部品の大量生産に広く使用されており、特に自動車構造部品 (ショックタワー、A、B、Cピラーなど) に不可欠であり、高い機械的特性 (UTS > 180 MPa、YS > 130 MPa、A5 > 10%) が要求されます。
- 熱処理は、HPDC アルミニウム構造部品に必要な延性を確保するためにしばしば必要です。
- しかし、熱処理は表面にブリスターを引き起こす可能性があり、最終製品では許容されず、部品の廃棄につながり、生産効率を低下させます [15]。
- 既存研究の限界:
- 新しい Al-Si-Cu-Mn-Fe HPDC 合金に関する以前の研究では、強度特性は要件を満たしていますが、塑性特性は構造要素には不十分であることが示されています。
- 最適な合金化学組成と初期表面ブリスターがない場合でも、熱処理によって強度特性が向上するとは限りません [7]。
- 既存の研究では、特定のダイカスト欠陥とブリスター形成との関係をさらに詳しく調査し、この問題を効果的に軽減する必要があります。
- 研究の必要性:
- HPDC アルミニウム部品の熱処理中のブリスターは、自動車産業における重大な問題であり、生産損失と品質上の懸念を引き起こしています [15]。
- 特定の鋳造欠陥がブリスター形成に及ぼす影響を理解することは、ブリスターを最小限に抑えるか排除し、構造部品用の HPDC プロセスの信頼性と効率を向上させるための戦略を開発するために非常に重要です。
- 本研究は、ブリスターを引き起こす鋳造欠陥の種類を特定し、これらの欠陥を減らすためのプロセス最適化に関する洞察を提供するために必要です。
3. 研究目的および研究質問:
- 研究目的:
- AlSi10MnMg 合金構造部品におけるダイカスト欠陥が、熱処理中のブリスター形成の可能性に及ぼす影響を提示すること。
- HPDC アルミニウム構造部品において、ブリスターの開始点として作用する鋳造欠陥の種類を特定すること。
- 核心研究質問:
- AlSi10MnMg 合金構造部品におけるさまざまな種類のダイカスト欠陥は、熱処理中のブリスター形成にどのような影響を与えますか?
- HPDC 部品のホットエリアとコールドエリアでブリスター形成を開始する鋳造欠陥の特徴は何ですか?
- 研究仮説:
- 熱処理された HPDC AlSi10MnMg 合金構造部品のブリスター形成は、微細構造の不連続性を生成する鋳造欠陥から開始されます。
- コールドフレーク、気孔、コールドドロップ、コールドショット、酸化膜などのさまざまな種類の鋳造欠陥は、位置と特性に応じてブリスター形成にさまざまな影響を与えます。
4. 研究方法論
- 研究設計:
- 市販の 9.5 kg ショックタワー AlSi10MnMg HPDC 合金鋳造のケーススタディ。
- 鋳造のホットエリア (ゲートシステム付近) とコールドエリア (ゲートシステムから離れたエリア) のサンプル比較。
- 鋳造状態および T7 熱処理 (溶体化熱処理および時効) 後のサンプル分析。
- データ収集方法:
- 微細構造観察:
- 構造研究のための光学顕微鏡 (LM) および走査型電子顕微鏡 (SEM) の使用。
- 微細構造成分の微量分析のためのエネルギー分散型 X 線分光法 (EDS) の使用。
- 非エッチング微小断面における一般的な手順を使用して調製された金属組織試験片。
- ブリスターを半分に切断して検査するために EDM (放電加工) を使用。
- 鋳造プロセスシミュレーション:
- MAGMAsoft 商用ソフトウェアを使用して、ダイ内の液体合金注入シミュレーションと流れ解析を実施。
- 金型充填中の溶融速度と温度のシミュレーション。
- 鋳造表面観察:
- 熱処理後の鋳造表面の目視検査により、ブリスターの位置と特性を特定。
- 微細構造観察:
- 分析方法:
- ブリスター形成に関連する鋳造欠陥とその特性を特定するための微細構造の定性分析。
- 鋳造のホットエリアとコールドエリアにおける欠陥の種類とブリスター形成の比較。
- 鋳造欠陥とブリスターの位置およびサイズの相関関係分析。
- 鋳造中の溶融流れと温度分布を理解するためのシミュレーション結果の分析。
- 研究対象および範囲:
- 材料: 市販の AlSi10MnMg HPDC 合金。
- 部品: ITALPRESSE 2700 機械で製造された 9.5 kg ショックタワー鋳造。
- 焦点: ダイカスト欠陥 (コールドフレーク、気孔、コールドドロップ、コールドショット、酸化膜) および T7 熱処理中のブリスター形成への影響。
- 調査領域: 鋳造のホットエリア (ゲートシステム付近) およびコールドエリア (ゲートシステムから離れたエリア)。
5. 主な研究結果:
- 核心研究結果:
- ブリスター形成プロセスは、微細構造の不連続性を生成する鋳造欠陥から開始されます。
- 不連続性にガスが存在する場合、溶体化処理中に膨張して表面ブリスターを形成します。
- さまざまな鋳造欠陥が、さまざまな重症度と位置依存性でブリスター形成に寄与します。
- 最大のブリスターはコールドフレークに形成され、主にゲートシステム付近の鋳造領域 (ホットエリア) で発生します。
- より小さなブリスターは気孔 (ガス気孔と収縮気孔の両方) に形成され、ホットエリアとコールドエリアの両方で発見されます。
- コールドドロップ、コールドショット、および薄い酸化膜は、主にゲートシステムから離れた領域 (コールドエリア) でブリスター発生部位として作用します。
- 統計的/定性的分析結果:
- ブリスター位置: ほとんどのブリスターはホットエリアであるゲートシステム付近で発生します [Fig. 3]。対照的に、コールドエリアではブリスターはほとんど発生しません [Fig. 4a]。
- ブリスターサイズ: ホットエリアに存在するブリスターは、コールドエリアのブリスターよりも分離しており、大きいです [Fig. 4b]。ホットエリアの大きなブリスターはサイズが 5 mm を超える場合がありますが、コールドエリアの小さなブリスターは 2 mm 未満です。
- 欠陥の種類と位置:
- ホットエリア: 周囲の合金とは異なる微細構造を持つ大きな粒子 (コールドフレーク) によって特徴付けられます [Fig. 8c, Fig. 9]。また、少数の単一気孔 [Fig. 8a]、Si 共晶相の単一の大きな分離、金属間化合物、および厚い α-Al デンドライトも存在します [Fig. 8b]。
- コールドエリア: ガス気孔と収縮気孔はホットエリアよりも高いです [Fig. 10a]。長い不連続性と薄い層が鋳造壁の端部付近に存在します。微細で円形および細長い粒子 (コールドドロップ) [Fig. 11a, b]。酸化膜も発見されています [Fig. 11c, d]。
- ブリスター下の微細構造: ブリスター中心下の AlSi10MnMg 合金微細構造は、それより遠い合金とは異なり [Fig. 16a]、ブリスターリングが広く平坦な合金微細構造の不連続性から始まることを示しています。
- データ解釈:
- コールドフレーク: 平坦な形状、大きなサイズ、およびマトリックスとの不連続性により、ガスを閉じ込めてホットエリアで大きなブリスター形成の主要部位として作用します。
- 気孔: ホットエリアとコールドエリアの両方で、より小さなブリスター形成に寄与します。球状気孔はブリスターを形成するために高い圧力が必要ですが [10]、相互接続された細長い微小収縮気孔はブリスターのリスクを高めます。
- コールドドロップ、コールドショット、酸化膜: 低い合金温度と半固体流動により、しばしば気孔やラミネーションに関連して、コールドエリアでより小さなブリスターを開始します。
- ブリスター形状: ホットエリアのブリスターは、多くの場合半円形で、鋳造壁と平行な平坦な底端を持っています [Fig. 13]。これは、コールドフレークのような平坦な不連続性で形成が開始されることを示しています。
- 図表名リスト:
- Fig. 1. ショックタワー鋳造スキーム。
- Fig. 2. さまざまな金型充填段階 (a、b) における液体合金温度。
- Fig. 3. ショックタワー鋳造表面のブリスター分布。
- Fig. 4. (a) コールドエリア (Fig. 3 のエリア 2E) および (b) ホットエリア (Fig. 3 のエリア 10G) における熱処理された鋳造表面のブリスター。
- Fig. 5. 鋳造された AlSi10MnMg 合金微細構造、LM: (a) コールドエリア、(b) ホットエリア。
- Fig. 6. 鋳造された AlSi10MnMg 合金の金属間化合物、SEM: (a) 板状および (b) 多角形。
- Fig. 7. 熱処理された AlSi10MnMg 合金微細構造、SEM: (a) 球状化された Si および (b) 金属間化合物。
- Fig. 8. ショックタワー鋳造ホットエリアの鋳造欠陥、LM: (a) 気孔、(b) 外部凝固結晶 (ESC)、(c) コールドフレーク、および (d) フレークエッジの不連続性。
- Fig. 9. AlSi10MnMg 合金微細構造のコールドフレーク、LM。
- Fig. 10. ショックタワー鋳造コールドエリアの鋳造欠陥、SEM: (a) 気孔、(b) コールドシャットおよびラミネーション (b-d)。
- Fig. 11. 鋳造されたショックタワー鋳造コールドエリアの鋳造欠陥、SEM: コールドドロップ (a、b)、薄い酸化膜 (c、d)。
- Fig. 12. Fig. 11c に示されている薄膜から得られた EDS チャート。
- Fig. 13. 鋳造壁エッジに平行な不連続性で形成されたブリスター、LM。
- Fig. 14. 鋳造壁エッジに角度を付けて配置された不連続性で形成されたブリスター、LM。
- Fig. 15. ブリスターで観察された表面特性、SEM: (a) 中央の平坦な表面、(b) エッジの粗い表面。
- Fig. 16. さまざまな合金微細構造、LM: (a) Fig. 13 に示されているブリスターの中心、(b) Fig. 14 に示されているブリスター下の二次亀裂。
- Fig. 17. 非拡張不連続性、LM: (a) ブリスターエッジ、(b) 鋳造エッジから遠く離れたコールドフレーク。
- Fig. 18. コールドドロップ、SEM: (a) ブリスターエッジ、(b) 合金気孔によって形成されたブリスター。
- Fig. 19. ショックタワーコールドエリアの大きなブリスター、LM。
- Fig. 20. AlSi10MnMg 合金気孔で形成されたブリスター、SEM: a) 分離されたガス気孔、b) 接続されたガス気孔、c) 収縮気孔。
- Fig. 21. ショックタワー鋳造のコールドエリア、SEM: (a) 半球状ブリスター、(b) 拡張された薄い不連続性。
- Fig. 22. 拡張された不連続性、SEM: (a) 平坦なコールドドロップで形成、(b) 球状コールドドロップで形成。
- Fig. 23. ショックタワーコールドエリアの針状コールドドロップ、SEM: (a) 鋳造状態、(b) 熱処理状態。
- Fig. 24. 薄い酸化膜によって形成されたブリスター、SEM。
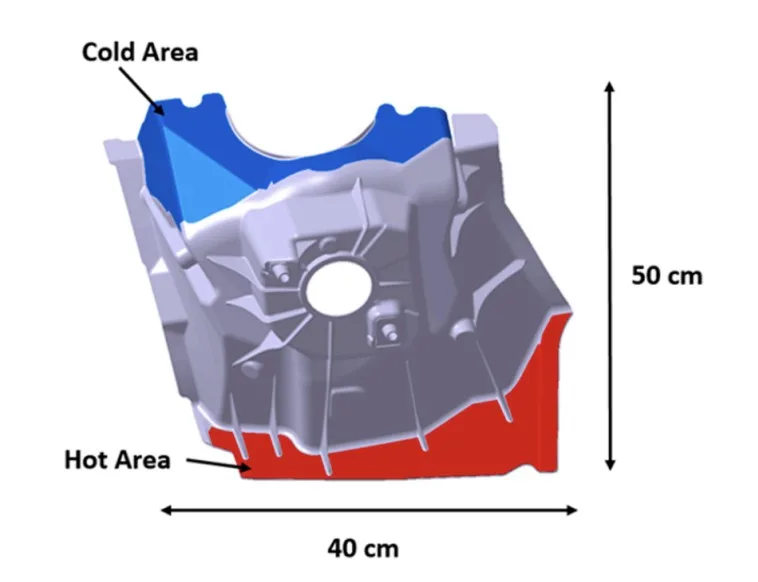
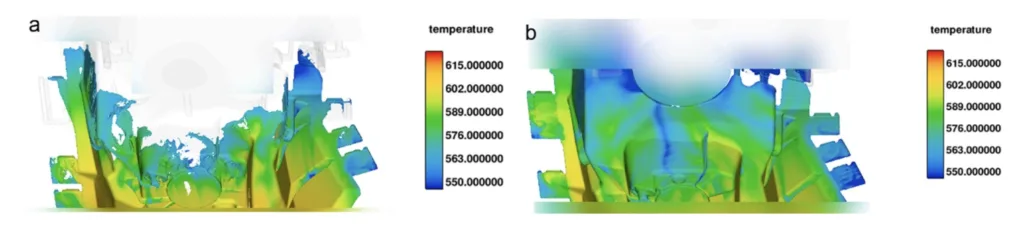
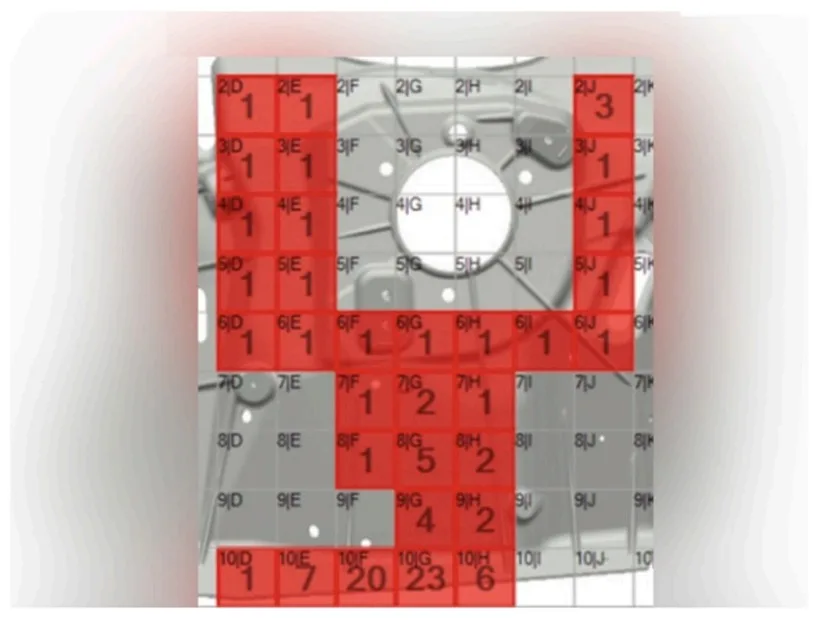
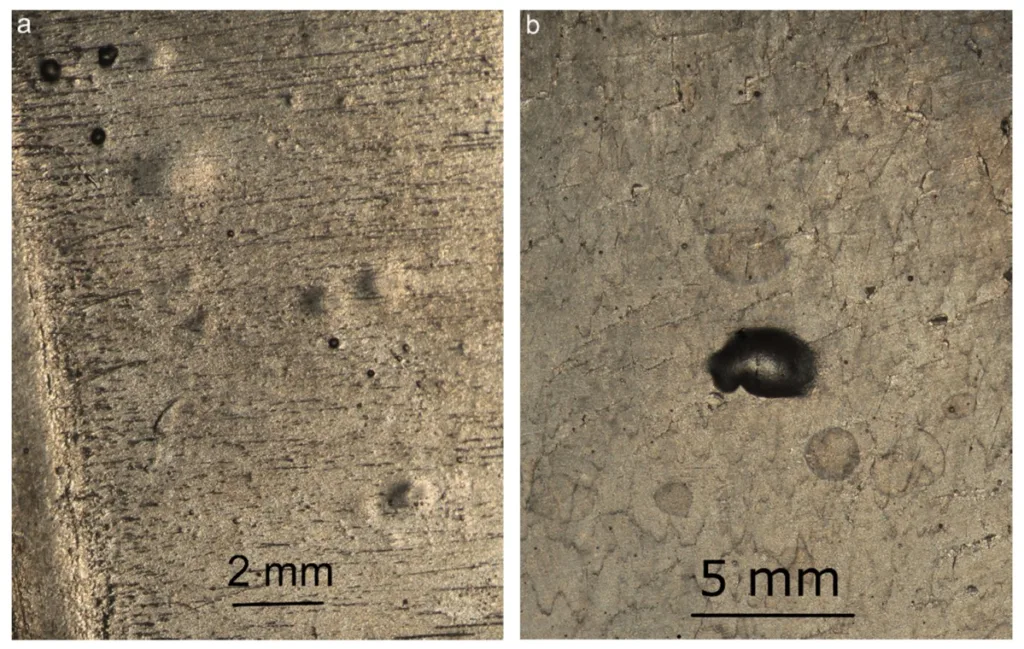
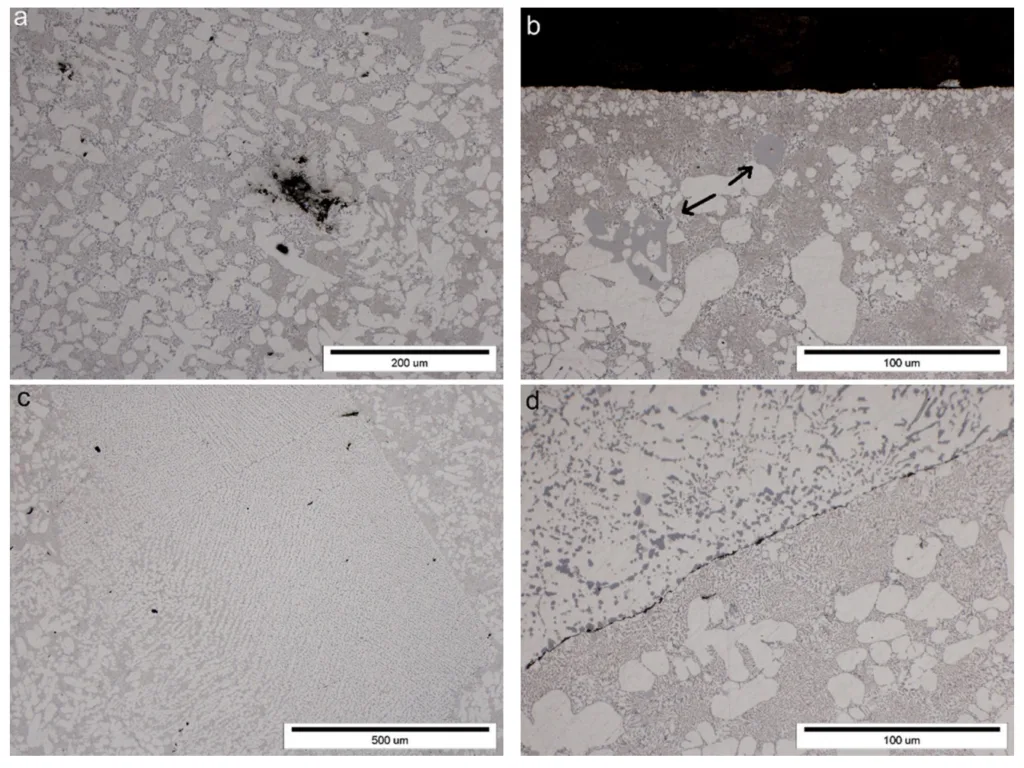
6. 結論および考察:
- 主な結果の要約:
- HPDC AlSi10MnMg 合金のブリスター形成は、微細構造の不連続性を生成する鋳造欠陥によって開始されます。
- コールドフレークは最も有害な欠陥であり、ホットエリアで大きなブリスターを引き起こし、合金の延性を低下させます。
- 気孔、コールドドロップ、コールドショット、酸化膜もブリスターリングに寄与し、特にコールドエリアではより小さなブリスターを引き起こします。
- ブリスターリングは、大きなコールドフレークの有病率により、ゲートシステム付近のホットエリアでより顕著です。
- 研究の学術的意義:
- 本研究は、HPDC アルミニウム構造部品における特定のダイカスト欠陥とブリスター形成との関係の詳細な分析を提供します。
- コールドフレークを大きなブリスターの主な原因として特定し、気孔、コールドドロップ、酸化膜などの他の欠陥がブリスター開始に果たす役割を強調しています。
- 研究結果は、HPDC 合金のブリスターリングメカニズムと、この現象における鋳造欠陥の重要な役割についてのより良い理解に貢献します。
- 実務上の意義:
- コールドフレークの形成を最小限に抑えることは、HPDC AlSi10MnMg 合金構造部品、特にホットエリアでのブリスターリングを減らすために非常に重要です。
- プロセス最適化戦略は、以下に焦点を当てる必要があります。
- コールドフレークの形成を減らすために、高いショットスリーブ温度を維持し、合金の滞留時間を最小限に抑えます。
- 大きなフレークを分解するために、ゲートシステムに障害物を実装します [17]。
- コールドフレークを減らすために、定期的な炉のメンテナンスとドージングタップの清掃を実施します。
- ガス巻き込みと気孔を最小限に抑えるために、潤滑システム、真空システム、およびショットプロファイル設定を最適化します [19]。
- コールドエリアでの凝固速度を遅くし、コールドドロップとコールドシャットを最小限に抑えるために、金型冷却を制御します。
- 研究の限界:
- 本研究は、ショックタワー鋳造の単一のケーススタディに基づいており、調査結果はこの部品形状と製造プロセスに固有である可能性があります。
- 研究は主に定性的であり、ブリスター形成と欠陥頻度の定量的統計分析ではなく、顕微鏡観察と欠陥特性評価に焦点を当てています。
- さまざまな HPDC 部品および合金にわたる欠陥サイズ、タイプ、およびブリスターの重症度の関係を定量化するには、さらなる研究が必要です。
7. 今後のフォローアップ研究:
- 今後の研究の方向性:
- さまざまな種類とサイズの鋳造欠陥と、ブリスター形成の確率とサイズとの間の相関関係の定量的分析。
- さまざまな鋳造欠陥タイプに関連するブリスター形成に対するさまざまな熱処理パラメータ (温度、時間) の影響の調査。
- HPDC におけるコールドフレークおよびその他のブリスター誘発欠陥の形成を具体的にターゲットにして削減するためのプロセス最適化戦略の開発と検証。
- さまざまな合金組成と、鋳造欠陥に関連するブリスター形成感受性の研究。
- さらなる探求が必要な領域:
- 熱処理中のさまざまな種類の鋳造欠陥内でのガス巻き込みと膨張の正確なメカニズム。
- コールドフレークおよびその他の欠陥の形成と分布に対する金型設計とゲートシステムの影響。
- HPDC 生産におけるブリスター形成を低減するためのリアルタイム欠陥検出およびプロセス制御方法の有効性。
8. 参考文献:
- [1] F. Bonollo, N. Gramegna, G. Timelli, High-pressure die-casting: contradictions and challenges, JOM 67 (2015) 901-908, https://doi.org/10.1007/s11837-015-1333-8.
- [2] S. Ji, Y. Wang, D. Watson, Z. Fan, Microstructural evolution and solidification behavior of Al-Mg-Si alloy in high-pressure die casting, Metall. Mater. Trans. A 44 (2013) 3185-3197, https://doi.org/10.1007/s11661-013-1663-5.
- [3] M. Jolly, L. Katgerman, Modelling of defects in aluminium cast products, Prog Mater Sci. 123 (2022), 100824, https://doi.org/10.1016/j.pmatsci.2021.100824.
- [4] A. Zhang, Z. Guo, Q. Wang, S. Xiong, Multiphase-field modelling of hydrogen pore evolution during alloy solidification, IOP Conf Ser Mater Sci Eng. 861 (2020), 012021, https://doi.org/10.1088/1757-899X/861/1/012021.
- [5] P. Zhang, Z. Li, B. Liu, W. Ding, Effect of chemical compositions on tensile behaviors of high pressure die-casting alloys Al-10Si-yCu-xMn-zFe, Mater. Sci. Eng. A 661 (2016) 198-210, https://doi.org/10.1016/j.msea.2016.03.032.
- [6] P. Zhang, Z. Li, B. Liu, W. Ding, Tensile properties and deformation behaviors of a new aluminum alloy for high pressure die casting, J Mater Sci Technol. 33 (2017) 367-378, https://doi.org/10.1016/j.jmst.2016.02.013.
- [7] S. Seifeddine, D. Poletaeva, M. Ghorbani, A. Jarfors, Heat treating of high pressure die cast components: challenges and possibilities, in: Light Metals 2014, Springer International Publishing, Cham, 2014, pp. 183-188, https://doi.org/10.1007/978-3-319-48144-9_32.
- [8] X.G. Hu, Q. Zhu, S.P. Midson, H.V. Atkinson, H.B. Dong, F. Zhang, Y.L. Kang, Blistering in semi-solid die casting of aluminium alloys and its avoidance, Acta Mater. 124 (2017) 446-455, https://doi.org/10.1016/j.actamat.2016.11.032.
- [9] H. Zhao, Y. Bai, X. Ouyang, P. Dong, Simulation of mold filling and prediction of gas entrapment on practical high pressure die castings, Trans. Nonferrous Met. Soc. Chin. 20 (2010) 2064-2070, https://doi.org/10.1016/S1003-6326(09)60418-0.
- [10] O. Ozhoga-Maslovskaja, E. Gariboldi, J.N. Lemke, Conditions for blister formation during thermal cycles of Al-Si-Cu-Fe alloys for high pressure die-casting, Mater Des. 92 (2016) 151-159, https://doi.org/10.1016/j.matdes.2015.12.003.
- [11] H. Toda, P.C. Qu, S. Ito, K. Shimizu, K. Uesugi, A. Takeuchi, Y. Suzuki, M. Kobayashi, Formation behaviour of blister in cast aluminium alloy, Int. J. Cast Met. Res. 27 (2014) 369-377, https://doi.org/10.1179/1743133614Y.0000000123.
- [12] H. Kang, H. Jang, S. Oh, P. Yoon, G. Lee, J. Park, E. Kim, Y. Choi, Effects of solution treatment temperature and time on the porosities and mechanical properties of vacuum die-casted and T6 heat-treated Al-Si-Mg alloy, Vacuum 193 (2021), 110536, https://doi.org/10.1016/j.vacuum.2021.110536.
- [13] H. Cao, Q. Sun, Q. Pu, L. Wang, M. Huang, Z. Luo, J. Che, Effect of vacuum degree and T6 treatment on the microstructure and mechanical properties of Al-Si-Cu alloy die castings, Vacuum 172 (2020), 109063, https://doi.org/10.1016/j.vacuum.2019.109063.
- [14] H.J. Kang, P.H. Yoon, G.H. Lee, J.Y. Park, B.J. Jung, J.Y. Lee, C.U. Lee, E.S. Kim, Y.S. Choi, Evaluation of the gas porosity and mechanical properties of vacuum assisted pore-free die-cast Al-Si-Cu alloy, Vacuum 184 (2021), 109917, https://doi.org/10.1016/j.vacuum.2020.109917.
- [15] R.N. Lumley, R.G. O'Donnell, D.R. Gunasegaram, M. Givord, Heat treatment of high-pressure die castings, Metall. Mater. Trans. A 38 (2007) 2564-2574, https://doi.org/10.1007/s11661-007-9285-4.
- [16] P.W. Cleary, J. Ha, M. Prakash, T. Nguyen, Short shots and industrial case studies: understanding fluid flow and solidification in high pressure die casting, Appl Math Model. 34 (2010) 2018-2033, https://doi.org/10.1016/j.apm.2009.10.015.
- [17] D.R. Gunasegaram, M. Givord, R.G. O'Donnell, B.R. Finnin, Improvements engineered in UTS and elongation of aluminum alloy high pressure die castings through the alteration of runner geometry and plunger velocity, Mater. Sci. Eng. A 559 (2013) 276-286, https://doi.org/10.1016/j.msea.2012.08.098.
- [18] W.G. Walkington, Die casting defects: causes and solutions, NADCA, 1997.
- [19] X.P. Niu, B.H. Hu, I. Pinwill, H. Li, Vacuum assisted high pressure die casting of aluminium alloys, J. Mater. Process Technol. 105 (2000) 119-127, https://doi.org/10.1016/S0924-0136(00)00545-8.
9. 著作権:
*本資料は、Bartłomiej Dybowski、Andrzej Kiełbus、Łukasz Poloczek による論文「Effects of die-casting defects on the blister formation in high-pressure die-casting aluminum structural components」に基づいて作成されました。
*論文出典: https://doi.org/10.1016/j.engfailanal.2023.107223
本資料は上記の論文に基づいて要約作成されており、商業目的での無断使用は禁止されています。
Copyright © 2025 CASTMAN. All rights reserved.