1. 概要:
- タイトル: 自動車軽量化のための材料 (Materials for Automotive Lightweighting)
- 著者: Alan Taub, Emmanuel De Moor, Alan Luo, David K. Matlock, John G. Speer, Uday Vaidya
- 発行年: 2019年
- 発行学術誌/学会: Annual Review of Materials Research
- キーワード:
- advanced high-strength steel (先進高張力鋼)
- aluminum (アルミニウム)
- magnesium (マグネシウム)
- polymer composites (ポリマー複合材料)
- lightweighting (軽量化)
- multimaterial joining (異種材料接合)
2. 研究背景:
- 研究テーマの社会的/学術的背景:
- 自動車の重量を削減することは、燃費向上に大きく貢献します。
- 従来の自動車製造における基本材料である低炭素鋼や鋳鉄は、より高い比強度と比剛性を持つ材料に置き換えられつつあります。
- 主要な課題は、これらの新しい軽量材料を用いた構造物の製造コストを削減することです。
- 重量削減を最大化するには、様々な形態の異種材料を利用した最適化設計が必要です。
- 混合材料の使用は、接合およびガルバニック腐食の防止において追加の課題をもたらします。
- 既存研究の限界:
- 軽量材料の既存の製造プロセスは、特定の用途のコスト要件を満たす必要があります。
- 異種材料構造における接合およびガルバニック腐食の防止は、さらなる課題です。
- 研究の必要性:
- 自動車軽量化のための先進高張力鋼、アルミニウム、マグネシウム、ポリマー複合材料などの材料システムの進歩をレビューします。
- アルミニウムとマグネシウムの使用増加を可能にする製造技術について議論します。
- 軽量材料の広範な採用のための材料特性の改善とコスト削減策を模索します。
3. 研究目的および研究質問:
- 研究目的:
- 自動車軽量化のための材料および製造技術の最先端技術をレビューし、特に先進高張力鋼、アルミニウム、マグネシウム、ポリマー複合材料に焦点を当てます。
- 核心研究質問:
- 自動車軽量化のために、鉄合金、特に先進高張力鋼とダクタイル鋳鉄の分野で最近の進歩は何ですか?
- 自動車構造におけるアルミニウムとマグネシウムの使用増加を可能にする製造技術は何ですか?また、最近の合金開発は何ですか?
- 自動車軽量化のためのポリマー複合材料の現在の応用分野と進歩は何ですか?材料開発と加工技術を含めて説明してください。
- 自動車軽量構造のための異種材料接合における課題と進歩は何ですか?
- 研究仮説: (論文では仮説として明示されていませんが、暗示されています)
- 材料科学、製造プロセス、および設計最適化の進歩は、性能と安全性、費用対効果を維持しながら、自動車の著しい軽量化を達成し、燃費を向上させるために不可欠です。
4. 研究方法論:
- 研究設計: 自動車軽量化材料および製造の分野における既存の文献および研究結果を要約するレビュー論文です。
- データ収集方法: 自動車材料、製造、および軽量化技術に関連する公開された研究論文、業界レポート、および技術刊行物の文献レビューを実施しました。
- 分析方法: レビューされた文献から得られた情報を質的に統合および要約し、当該分野における主要な傾向、進歩、課題、および将来の方向性を特定することに焦点を当てました。
- 研究対象および範囲: 自動車の車体、シャシー、および内装部品に使用される材料に焦点を当てています。主に先進高張力鋼、アルミニウム、マグネシウム、およびポリマー複合材料をレビューします。範囲は、軽量化材料の検討事項を超えたパワートレイン電動化の影響は除外します。
5. 主要研究結果:
- 核心研究結果:
- 先進高張力鋼 (AHSS) およびダクタイル鋳鉄:
- 向上した強度と成形性のために、複雑な微細構造 (マルテンサイト、ベイナイト、超微細粒フェライト、残留オーステナイト) を持つ第3世代 AHSS の開発。
- 第3世代 AHSS のための新しい加工ルートとして、Q&P (Quenching and Partitioning, 焼入れおよび分配) および TBF (TRIP-aided bainitic ferrite, TRIP 支援ベイナイトフェライト) 鋼の開発。
- 高い比強度と費用対効果を提供する薄肉オーステンパーダクタイル鋳鉄 (ADI) 鋳造。
- アルミニウムおよびマグネシウム:
- 燃費要求と製造革新によって推進されるアルミニウムとマグネシウムの使用増加。
- アルミニウムおよびマグネシウム合金の成形性を向上させるための温間成形などの板金成形技術。
- 最小限の気孔率と向上した延性を備えた部品を製造するためのアルミニウムおよびマグネシウム用高真空ダイカストプロセス (SVDC)。
- CALPHAD アプローチを使用した高温マグネシウム合金 (例: AE44) の合金開発。
- ポリマー複合材料:
- 高い比強度と設計の柔軟性により、軽量化の主要な実現要因としての繊維強化ポリマー複合材料。
- 車体外装、内装、安全、シャシー、パワートレイン、燃料システム、およびエンジン部品における様々な応用分野。
- 費用対効果の高い複合材料製造のための炭素繊維技術と加工方法 (HP-RTM、湿式圧縮、IOM、プリプレグスタンピング、押出圧縮) の進歩。
- コスト削減と持続可能性の向上のために重要性が増しているポリマー複合材料のリサイクル技術。
- 異種材料接合:
- 自動車設計において異なる軽量材料を統合するために不可欠になっている異種材料接合。
- 堅牢な設計ツール、信頼性の高い試験方法、および費用対効果の高い接合技術の必要性。
- 接合アプローチのスケールアップ、加速劣化試験の開発、および第三者データ評価に焦点を当てた研究。
- 先進高張力鋼 (AHSS) およびダクタイル鋳鉄:
- 統計的/定性的分析結果:
- 重量削減効果: 軽自動車: 重量削減価値 "$4.50/kg"。大型トラック: 重量削減価値 "$5-11/kg ドライバン専用ルート" および "$13-24/kg バルクキャリア" (表 1)。
- 材料置換効果: 軟鋼/鋳鉄と比較した様々な軽量材料の質量削減率と相対的な部品あたりコスト (表 2)。例えば、マグネシウム: 質量削減率 "60-75%"、相対的な部品あたりコスト "1.5~2.5"。炭素繊維複合材料: 質量削減率 "50-60%"、相対的な部品あたりコスト "2~10+"。
- AHSS 伸び: 図 5 は、従来の鋼種と AHSS 鋼種の引張強度と全伸びの組み合わせの特性マップを示しています。第3世代 AHSS は、このマップの特定の帯域内の特性を目指しています。
- Q&P 鋼の応力-ひずみ曲線: 図 6 および図 8 は、異なる加工条件下での Q&P 鋼の応力-ひずみ曲線を示しており、引張特性の変化を示しています。
- 中 Mn 鋼におけるオーステナイト変態: 図 10 は、異なるアニール温度における中 Mn 鋼のひずみと対応する応力-ひずみ曲線によるオーステナイトからマルテンサイトへの変態の進化を示しています。
- 疲労寿命と介在物含有量: 図 11 は、鋼の介在物含有量と疲労応力/寿命の関係を示しています。改善された製鋼法は、1980 年以降 "疲労寿命が 2 桁増加" する結果をもたらしました。
- ダクタイル鋳鉄の球状黒鉛密度: 図 12 は、薄肉と厚肉のダクタイル鋳鉄鋳物の球状黒鉛密度を比較しています。
- 炭素繊維複合材料の特性: 表 3 は、織物炭素繊維 (TCF) エポキシ複合材料の代表的な特性を示しています。例: 引張強度: "548 MPa (79.48 ksi)"、引張弾性率: "84 GPa (12.18 Msi)"。
- オーバーモールド複合材料の耐荷重能力: 図 24 は、PA6-C LFT と比較して、オーバーモールドされた PA6-C LFT の "耐荷重能力とひずみ能力が 275% 向上" していることを示しています。
- データ解釈:
- 材料置換と最適化された設計は、自動車軽量化のための重要な戦略です。
- 先進材料と製造プロセスは、より軽量で、より強く、より費用対効果の高い自動車構造の需要を満たすために継続的に進化しています。
- ポリマー複合材料と異種材料設計は、将来の軽量化の取り組みにとってますます重要になっています。
- 図の名前リスト:
- 図 1: 1975~2016年モデルイヤーにおける調整済み燃費、重量、馬力の変化。
- 図 2: (a) 従来の成形技術と比較した、少量生産におけるインクリメンタル成形と費用対効果。(b) 部品の複雑さと生産量に対するさまざまな成形プロセスのバランス。
- 図 3: 異種材料軽量自動車 Mach-II ボディ・イン・ホワイト材料分布。
- 図 4: 米国の自動車金属市場の歴史と予測。
- 図 5: さまざまな種類の従来の鋼種と AHSS 鋼種における引張強度と全伸びの組み合わせの特性マップ。
- 図 6: 300℃~500℃のさまざまな温度で200秒間オーステンパー処理された0.2 wt% C–1.5 wt% Mn–1.0 wt% Si-0.5 wt% Al 鋼の工学的応力-ひずみ曲線。
- 図 7: 完全オーステナイト組織から始まる2段階焼入れ・分配熱処理プロセスを示す模式図。
- 図 8: 焼入れ・分配処理後、炭素含有量0.2~0.4 wt%で、分配時間が10秒と300秒の400℃で分配を行ったx wt% C–1.5 wt% Mn–1.6 wt% Si 鋼で得られた工学的応力-ひずみ曲線。
- 図 9: 40 vol% オーステナイトを生成するために 620℃ で 24 時間アニールされた 7 wt% Mn 鋼の電子後方散乱回折像品質マップ。
- 図 10: (a) さまざまなアニール温度における引張変形によるマルテンサイトに変態したオーステナイト分率の進化。(b) 0.1 wt% C–7.1 wt% Mn–0.1 wt% Si サンプルの対応する引張応力-ひずみ曲線。
- 図 11: (a) 許容疲労応力と (b) 軸受疲労寿命に対する介在物含有量の影響。
- 図 12: 肉厚がノジュール数に及ぼす影響を示す、エッチングされていない試料の光学顕微鏡写真。
- 図 13: 主要なアルミニウムおよびマグネシウム自動車アプリケーションのタイムライン。
- 図 14: 成形直後のコルベット Z06 用ハイドロフォームアルミニウムレール。
- 図 15: (a) Al-8 wt% Si-0.35 wt% Mg-0.6 wt% Fe-x% Mn について計算されたアイソプレット。(b) Al-Si-Mg-Fe-Mn 合金系における β-Al5FeSi 金属間化合物の形成に対する Fe および Mn 含有量の影響。
- 図 16: 合金最適化とプロセスシミュレーションによる薄肉アルミニウムおよびマグネシウムダイカストの実現。
- 図 17: (a) 計算された Mg-Al 相図。(b) 実験的な Mg-Al-Ce 合金の計算された Mg-Al-Ce 液相線投影図と凝固経路。
- 図 18: 車両の軽量化に関連する製造プロセスを備えたポリマーおよびポリマー複合材料の包括的な機会。
- 図 19: 米国およびカナダの軽自動車におけるさまざまなプラスチックおよび複合材料の過去の平均材料使用量。
- 図 20: 米国/カナダの軽自動車で使用されている平均的なプラスチックおよびポリマー複合材料。
- 図 21: オークリッジ国立研究所の炭素繊維技術施設で製造された広幅トウ織物グレード炭素繊維。
- 図 22: (a) 高圧樹脂トランスファー成形 (RTM)。(b) 湿式圧縮成形。
- 図 23: 自動車部品のオーバーモールディング工程。
- 図 24: 炭素 PA6 とオーバーモールドされた炭素 PA6 の比較。
- 図 25: 長繊維熱可塑性押出圧縮成形プロセスの材料段階。
- 図 26: (a) サイクルタイム 45 秒で成形されたシートモールディングコンパウンド (SMC) シートバックレスト。(b) SMC 成形プラークとオーバーモールドされた SMC プラーク。
- 図 27: ニアネットシェイプにスタンプ/圧縮成形できるリサイクル炭素繊維ポリアミド 6 (PA6) マットの例。
- 図 28: オークリッジ国立研究所の製造デモンストレーション施設にある BAAM (大面積付加製造) プリンターで製造された Strati 車の六角形断面。
- 図 29: (a) プリプレグスタンピング、射出成形、圧縮成形、付加製造のための包括的な機能を備えた IACMI Purdue University のモデリングおよびシミュレーションハブ。(b) アクリロニトリルブタジエンスチレン材料の層状押出堆積で開発された局所的な熱応力のモデル。
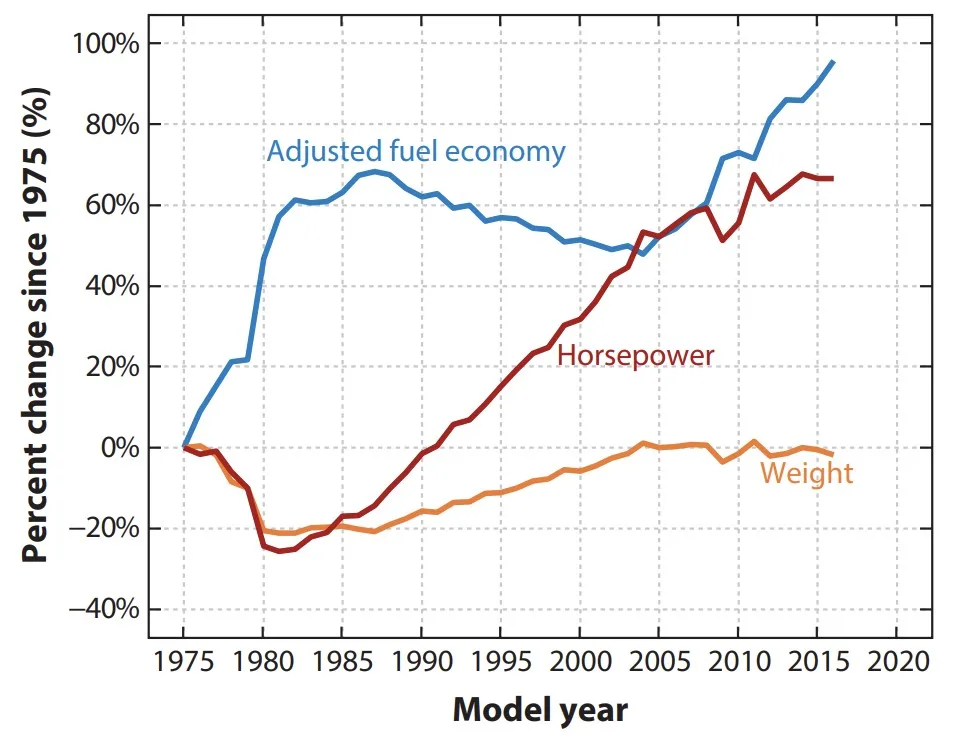
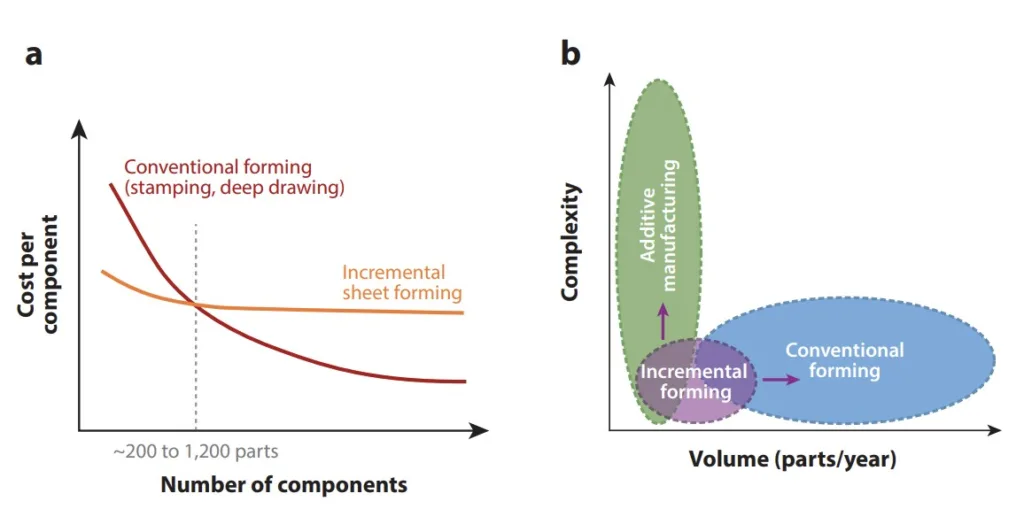
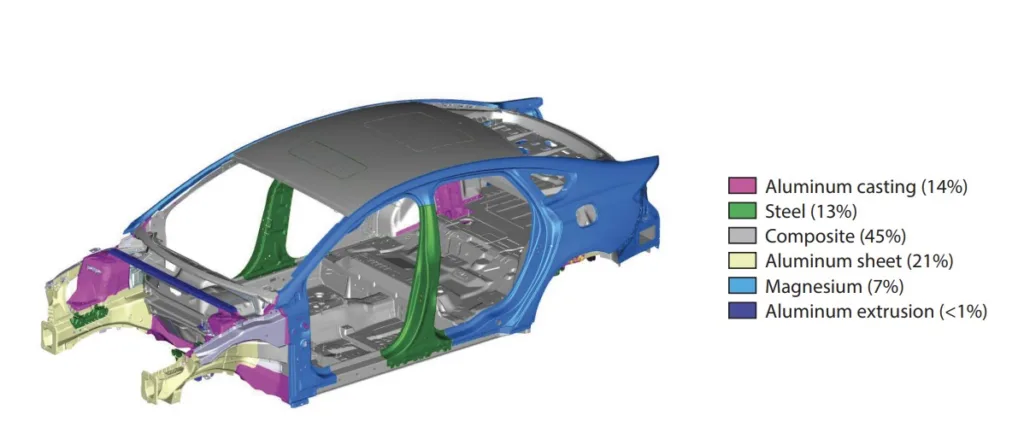
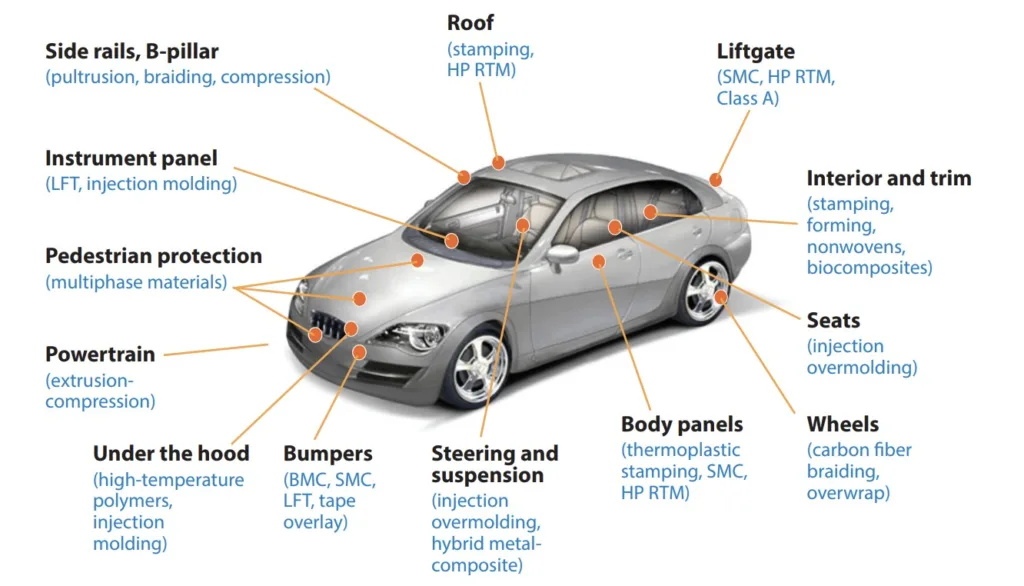
6. 結論および考察:
- 主要な結果の要約:
- 自動車産業は、AHSS、アルミニウム、マグネシウム、ポリマー複合材料などの先進材料を採用することにより、軽量化に積極的に移行しています。
- 最適化された設計と高度な製造技術は、費用対効果の高い軽量材料の実装に不可欠です。
- 性能を向上させ、重量を削減するために、各材料カテゴリの新しい合金と加工ルートの開発に大きな進歩がありました。
- 異種材料設計と接合技術は、重量削減を最大化し、望ましい性能特性を達成するために不可欠です。
- 研究の学術的意義:
- 自動車軽量化のための材料と製造における最新の進歩の包括的な概要を提供します。
- 設計最適化と材料選択のための統合計算材料工学 (ICME) の重要性を強調しています。
- 異種材料設計への移行と、それに関連する課題と機会を強調しています。
- 実務的示唆:
- 自動車エンジニアや材料科学者が軽量材料と製造プロセスを選択および実装する上で貴重な洞察を提供します。
- 自動車軽量化のさらなる進歩に必要な主要な研究分野と技術的進歩を特定します。
- 新しい軽量化技術の採用における費用対効果とリサイクル可能性の重要性を強調しています。
- 研究の限界:
- 本レビューは主に材料の側面と製造技術に焦点を当てており、ライフサイクル全体の分析や詳細なコストモデリングなどのより広範なシステムレベルへの影響に関する議論は限定的です。
- 範囲は車体、シャシー、内装部品に限定されており、材料の検討事項を超えたパワートレイン電動化が軽量化に及ぼす影響の詳細な分析は除外されています。
7. 今後のフォローアップ研究:
- 今後の研究方向:
- 低コスト炭素繊維と効率的な複合材料製造プロセスのさらなる開発。
- 異種材料接合技術とガルバニック腐食防止方法の進歩。
- 加速された材料設計とプロセス最適化のための ICME ツールの開発と改良。
- 持続可能性を高めるための複合材料のリサイクル技術の研究。
- 向上した特性とコスト削減を備えた AHSS、アルミニウム、およびマグネシウムのための新しい合金設計と加工技術の探求。
- 追加探求が必要な領域:
- さまざまな軽量化戦略と材料選択の技術経済分析。
- 複合材料衝突シミュレーションモデルの検証と堅牢な設計ガイドラインの開発。
- 異種材料接合部の標準化された試験方法とデータベースの開発。
- 軽量化戦略と車両電動化および自動運転技術の統合。
8. 参考文献:
- US Natl. Res. Counc. 2003. Materials Research to Meet 21st Century Defense Needs.Washington, DC: Natl. Acad. Press
- Roeth M. 2015. Confidence report: lightweighting. Rep., North American Council for Freight Efficiency.
https://nacfe.org/technology/lightweighting-2/. Accessed Nov. 20, 2017 - Taub AI, Krajewski PE, Luo AA, Owens JN. 2007. The evolution of technology for materials processing
over the last 50 years: the automotive example. JOM 59(2):48–57 - Schutte C, Joost WJ. 2014. Lightweight materials for cars and trucks. https://www.energy.gov/eere/
vehicles/lightweight-materials-cars-and-trucks - Joost W. 2015.Energy, materials and vehicle weight reduction. Rep., US Dep. Energy. http://www.nist.gov/
mml/acmd/structural_materials/upload/Joost-W-DOE-VTP-NIST-ASP-AHSS-WorkshopR03.pdf - Picker L. 2017. Vehicle weight and automotive fatalities. Digest, NBER. http://www.nber.org/digest/
nov11/w17170.html. Accessed Dec. 3, 2017 - Plumer B. 2014. Cars in the US are more fuel-efficient than ever. Here are 5 reasons why. Vox,
Sept. 4. https://www.vox.com/2014/9/4/6107203/cars-in-the-us-are-more-fuel-efficient-thanever-here-are-5-reasons. Accessed Dec. 3, 2017 - US Envir. Prot. Agency (EPA). 2015. Light-duty automotive technology, carbon dioxide emissions, and fuel economy trends: 1975 through 2015. Rep., US EPA
- Baron JS, Modi S. 2016. Assessing the fleet-wide material technology and costs to lightweight vehicles. Rep.,
Cent. Automot. Res. - Isenstadt A, German J, Bubna P, Wiseman M, Venkatakrishnan U, et al. 2016. Lightweighting technology development and trends in U.S. passenger vehicles. Work. Pap., Int. Counc. Clean Transp.
- US EPA. 2016. Light-duty vehicle CO2 and fuel economy trends. Rep. EPA-420-S-16-001, US EPA
- Bullis K. 2013. Automakers shed the pounds to meet fuel efficiency standards. MIT Technol. Rev., Feb. 20
- Kunkel GA, Hovanski Y. 2016. From the lab to your driveway: aluminum tailor-welded blanks. Weld. J.
95(8):36–39 - Joost WJ, Krajewski PE. 2017. Towards magnesium alloys for high-volume automotive applications. Scr. Mater. 128:107–12
- Winters J. 2014. Light vehicles’ lightweight future. Mech. Eng. CIME, Aug. 1. Accessed Nov. 28, 2017
- Hartfield-Wünsch SE, Hall JN. 2012. Manufacturing challenges for aluminum sheet in the automotive
industry. In ICAA13, ed. H Weiland, AD Rollett, WA Cassada, pp. 885–90. Cham, Switz.: Springer - Xia L. 2016. Multiscale Structural Topology Optimization. London: Elsevier
- Fiedler K, Rolfe BF, De Souza T. 2017. Integrated shape and topology optimization: applications in
automotive design and manufacturing. SAE Int. J. Mater. Manuf. 10(3):385–94 - Keough JR, Hayrynen KL. 2000. Automotive applications of austempered ductile iron (ADI): a critical
review. SAE Trans. 109:344–54 - Horstemeyer MF. 2012. Integrated Computational Materials Engineering (ICME) for Metals: Using Multiscale Modeling to Invigorate Engineering Design with Science. Hoboken, NJ: Wiley
- Pollock DGB, Tresa M, Allison JE. 2008. Integrated Computational Materials Engineering: A Transformational Discipline for Improved Competitiveness and National Security. Washington, DC: Natl. Acad. Press
- Allison J, Li M, Wolverton C, Su XM. 2006. Virtual aluminum castings: an industrial application of
ICME. JOM 58(11):28–35 - Sames WJ, List FA, Pannala S, Dehoff RR, Babu SS. 2016. The metallurgy and processing science of
metal additive manufacturing. Int. Mater. Rev. 61(5):315–60 - Daehn G. 2017. Metamorphic manufacturing. Abstract, LIFT. https://lift.technology/pillar/novelagile-processing/. Accessed Nov. 30, 2017
- Allwood JM, Utsunomiya H. 2006. A survey of flexible forming processes in Japan. Int. J. Mach. Tools
Manuf. 46(15):1939–60 - Allwood J, Houghton N, Jackson K. 2005. The design of an incremental sheet forming machine. Adv.
Mater. Res. 6–8:471–78 - Cao J, Huang Y, Reddy NV, Malhotra R, Wang Y. 2008. Incremental sheet metal forming: advances
and challenges. In Proceedings of International Conference on Technology of Plasticity (ICTP 2008). Gyeongju,
Korea: Korean Soc. Technol. Plastic. - Taub AI, Babu SS. 2018. Opportunities and challenges for introducing new lightweight metals in transportation. Int. J. Powder Metall. 54(2):27–33
- Taub AI, Luo AA. 2015. Advanced lightweight materials and manufacturing processes for automotive
applications. MRS Bull. 40(12):1045–54 - Skszek T, Conklin J, Zaluzec M,Wagner D. 2014. Multi-material lightweight vehicles: Mach-II design. Rep. for US Dep. Energy. https://energy.gov/sites/prod/files/2014/07/f17/lm088_skszek_2014_o.pdf.
Accessed Dec. 1, 2017 - Skszek T. 2015. Demonstration project for a multi-material lightweight prototype vehicle as part of the clean energy dialogue with Canada. Final Rep. for US Dep. Energy (award DE-EE0005574)
- Henriksson F. 2016. An outlook on multi material body solutions in the automotive industry: possibilities and
manufacturing challenges. Tech. Pap. 2016-01-1332, SAE - US Dep. Energy. 2010. 2010 annual progress report: lightweight material. Rep., US Dep.
Energy. https://www.energy.gov/sites/prod/files/2014/03/f8/2010_lightweighting_materials.pdf.
Accessed Sept. 1, 2015 - US EPA. 2012. Light-duty vehicle mass reduction and cost analysis—midsize crossover utility vehicle. Rep. EPA-420-R-12-026, US EPA. https://nepis.epa.gov/Exe/ZyPDF.cgi/P100EWVL.PDF?Dockey=
P100EWVL.PDF - Gehm R. 2016. Multi-material structures move mpg upward. Automot. Eng. 2016(3):18–21
- Singh H. 2012. Mass reduction for light-duty vehicles for model years 2017–2025. Rep. DOT HS 811 666,US Dep. Transp.
- US EPA. 2015. Mass reduction and cost analysis: light duty pickup model years 2020–2025. Rep. EPA-420-R15-006, US EPA
- Vasalash GS. 2017. Light vehicles and how they got that way. Automotive Design and Production, Oct. 11.
https://www.adandp.media/articles/light-vehicles-and-how-they-got-that-way - Monaghan M. 2012. Light and mighty. Automot. Eng. 2012(7):20–24
- Steven A. 2015. Mixing metals. Automot. Eng. 2015:27–29
- Wagner DA, Zaluzec MJ. 2015. Mixed materials drive lightweight vehicle design. Adv. Mater. Process.
2015(3):18–23 - Meschut G, Janzen V, Olfermann T. 2014. Innovative and highly productive joining technologies for
multi-material lightweight car body structures. J. Mater. Eng. Perform. 23(5):1515–23 - Ghosh D, Pancholi L, Sathaye A. 2014. Forming a strong bond. Automot. Eng. 2014:24–29
- Gould JE. 2012. Joining aluminum sheet in the automotive industry—a 30 year history. Weld. J. 91:23–34
- WorldAutoSteel. 2017. Advanced high-strength steels application guidelines version 6.0. https://www.
worldautosteel.org/projects/advanced-high-strength-steel-application-guidelines/. Accessed
Oct. 2018 - De Moor E, Gibbs PJ, Speer JG, Matlock DK, Schroth JG. 2010. Strategies for third-generation advanced high-strength steel development. AIST Trans. 7(3):133–44
- Matlock DK, Speer JG. 2009. Third generation of AHSS: microstructure design concepts. In Microstructure and Texture in Steels and Other Materials, ed. A Haldar, S Suwas, D Bhattacharjee, pp. 185–205. New York: Springer
- Matlock DK, Speer JG. 2006. Design considerations for the next generation of advanced high strength steels. In Proceedings of the Third International Conference on Advanced Structural Steels, ed. HC Lee, pp. 774–81. Seoul, Korea: Korean Institute of Metals and Materials
- Olson GB. 1984. Transformation plasticity and the stability of plastic flow. In Deformation, Processing and Structure, ed. G Krauss, pp. 391–424. Materials Park, OH: ASM
- Matlock DK, Speer JG, De Moor E, Gibbs PJ. 2011. TRIP steels—historical perspectives and recent
developments. In Proceedings of the 1st International Conference on High Manganese Steels, HMnS2011.
Seoul, Korea: Yonsei Univ. Press - De Cooman BC. 2004. Structure-properties relationship in TRIP steels containing carbide-free bainite.
Curr. Opin. Solid State Mater. Sci. 8(3–4):285–303 - Sugimoto K, Murata M, Song SM. 2010. Formability of A1-Nb bearing ultra high-strength TRIP-aided
sheet steels with bainite ferrite and/or martensite matrix. ISIJ Int. 50(1):162–68 - Rana R, De Moor E, Speer JG, Matlock DK. 2018. On the importance of adiabatic heating on deformation behavior of medium-manganese sheet steels. JOM 70(5):706–13
- Lee S, De Cooman BC. 2014. Tensile behavior of intercritically annealed 10 pct Mn multi-phase steel.
Metall. Mater. Trans. A 45(2):709–16 - Merwin MJ. 2007. Low-carbon manganese TRIP steels. Mater. Sci. Forum 539–543:4327–32
- Merwin MJ. 2007. Hot- and cold-rolled low-carbon manganese TRIPS steels. Tech. Pap. 2007-01-0336, SAE
- Bhadeshia HKDH. 2010. Nanostructured bainite. Proc. R. Soc. A 466(2113):3–18
- Speer JG, De Moor E, Findley KO, Matlock DK, De Cooman BC, Edmonds DV. 2011. Analysis of
microstructure evolution in quenching and partitioning automotive sheet steel. Metall. Mater. Trans. A 42(12):3591–601 - Wang L, Speer JG. 2013. Quenching and partitioning steel heat treatment. In ASM Handbook, Volume 4A: Steel Heat Treating Fundamentals and Processes, ed. GE Dossett, J Totten, pp. 317–26. Materials Park, OH:ASM Int.
- Sugimoto K, Iida T, Sakaguchi J, Kashima T. 2000. Retained austenite characteristics and tensile properties in a TRIP type bainitic sheet steel. ISIJ Int. 40(9):902–8
- Sugimoto K, Tsunezawa M, Hojo T, Ikeda S. 2004. Ductility of 0.1-0.6C-1.5Si-1.5Mn ultra highstrength TRIP-aided sheet steels with bainitic ferrite matrix. ISIJ Int. 44(9):1608–14
- Speer JG, Matlock DK, De Cooman BC, Schroth JG. 2003. Carbon partitioning into austenite after
martensite transformation. Acta Mater. 51(9):2611–22 - Matlock DK, Bräutigam VE, Speer JG. 2003. Application of the quenching and partitioning (Q&P)
process to a medium-carbon, high-Si microalloyed bar steel. Mater. Sci. Forum 426–432(1):1089–94 - Pierce DT, Coughlin DR, Williamson DL, Clarke KD, Clarke AJ, et al. 2015. Characterization of transition carbides in quench and partitioned steel microstructures by Mössbauer spectroscopy and complementary techniques. Acta Mater. 90:417–30
- Speer JG, Striecher AM, Matlock DK, Rizzo F, Krauss G. 2003. Quenching and partitioning a fundamentally new process to create high strength TRIP sheet microstructures. In Austenite Deformation and
Decomposition, ed. EB Damm, MJ Merwin, pp. 502–22. Warrendale, PA: ISS/TMS - Kahkonen MJ, De Moor E, Speer JG, Thomas GA. 2015. Carbon and manganese effects on quenching
and partitioning response of CMnSi-steels. SAE Int. J. Mater. Manuf. 8(2):419–24 - Wang L, Zhong Y, Feng W, Jin X, Speer JG. 2013. Industrial application of Q&P sheet steels. In Proceedings of the International Symposium on New Developments in Advanced High-Strength Steels, ed. E De Moor, HJ Jun, JG Speer, MJ Merwin, pp. 141–51. Warrendale, PA: AIST
- Gibbs PJ, De Moor E, Merwin MJ, Clausen N, Speer JG, Matlock DK. 2011. Austenite stability
effects on tensile behavior of manganese-enriched-austenite transformation-induced plasticity steel.
Metall. Mater. Trans. A 42(12):3691–702 - De Moor E, Matlock DK, Speer JG, Merwin MJ. 2011. Austenite stabilization through manganese enrichment. Scr. Mater. 64:185–88
- Zhang Y, Wang L, Findley KO, Speer JG. 2017. Influence of temperature and grain size on austenite
stability in medium manganese steels. Metall. Mater. Trans. A 48:2140–49 - Rana R, Lahaye C, Ray RK. 2014. Overview of lightweight ferrous materials: strategies and promises.
JOM 66(9):1734–46 - Ghanbari ZN, Speer JG. 2016. Elevated- and room-temperature mechanical behaviour of Zn-coated
steel sheet for hot stamping. AST Trans. 13(4):170–77 - Matlock DK, Speer JG. 2009. Microalloying concepts and application in long products. Mater. Sci. Technol. 25:1118–25
- Thompson RE, Matlock DK, Speer JG. 2007. The fatigue performance of high temperature vacuum
carburized Nb modified 8620 steel. SAE Trans. J. Mater. Manuf. 116(5):392–407 - Darragh CV. 2002. Engineered gear steels: a review. Gear Technol. Nov.–Dec.:33–40
- Gynther D. 2018. UltrapremiumTM and endurance steels. Presented at Great Designs in Steel, Livonia, MI. https://www.autosteel.org/-/media/files/autosteel/great-designs-in-steel/gdis-2018/track2- - -gynther- - -timkensteel.ashx. Accessed July 2018
- Findley KO, Cryderman RL, Nissan AB, Matlock DK. 2013. The effects of inclusions on fatigue performance of steel alloys. AIST Trans. 10(6):234–44
- Jhaveri K, Lewis GM, Sullivan JL, Keoleian GA. 2018. Life cycle assessment of thin-wall ductile cast
iron for automotive lightweighting applications. Sustain. Mater. Technol. 15:1–8 - Labrecque C, Gagné M, Javaid A, Sahoo M. 2003. Production and properties of thin-wall ductile iron
castings. Int. J. Cast Met. Res. 16:313–17 - Borrajo JM, Martínez RA, Boeri RE, Sikora JA. 2002. Shape and count of free graphite particles in thin
wall ductile iron castings. ISIJ Int. 42(3):257–63 - Fras E, Górny M, Lopez H. 2014. Thin wall ductile iron castings as substitutes for aluminum alloy ´
castings. Arch. Metall. Mater. 59(2):459–65 - Stefanescu DM, Dix LP, Ruxanda RE, Corbitt-Coburn C, Piwonka TS. 2002. Tensile properties of
thin-wall ductile iron. AFS Trans. 2(178):1149–61 - Górny M, Tyrała E. 2013. Effect of cooling rate on microstructure and mechanical properties of thinwalled ductile iron castings. J. Mater. Eng. Perform. 22(1):300–5
- Krajewski P, Sachdev A, Luo A, Carsley J, Schroth J. 2009. Automotive aluminum and magnesium:
innovation and opportunities. Light Met. Age 67(5):6–13 - Healey JR. 2014. 2015 Ford F-150 makes radical jump to aluminum body. USA Today, Jan. 13. https://
www.usatoday.com/story/money/cars/2014/01/13/redesigned-2015-ford-f-series-pickup-f150-aluminum/4421041/ - Ducker Worldwide. 2017.Aluminum content in North American light vehicles 2016 to 2028: summary report. Rep. for DriveAluminum
- Krajewski PE, Schroth JG. 2007. Overview of quick plastic forming technology. Mater. Sci. Forum 3:551–52
- Carter JT, Krajewski PE, Verma R. 2008. The hot blow forming of AZ31 Mg sheet: formability assessment and application development. JOM 60:77
- Shehata F, Painter MJ, Pearce R. 1978. Warm forming of aluminium/magnesium alloy sheet. J. Mech.
Work. Technol. 2:279–90 - Ayres RA. 1977. Enhanced ductility in an aluminum–4 Pct magnesium alloy at elevated temperature.
Metall. Trans. A 8:487–92- Warmed-up aluminum could beat steel to the draw. Mater. Eng. 88:52–54
- Luo AK, Sachdev AA. 2007. Development of light metals automotive structural subsystems. In Proceedings of the Light Metals Technology Conference. Ottawa, Can.: Nat. Resour. Can.
- Luo AA, Fu PH, Yu YD, Jiang HY, Peng LM, et al. 2008. Vacuum-assisted high pressure die casting of
AZ91 magnesium alloy. North Am. Die Cast. Assoc. Trans. 2008:T08–83 - Brown Z, Szymanowski B, Musser M, Saha D, Seaver S. 2009. Development of super-vacuum die casting
process for magnesium alloys. North Am. Die Cast. Assoc. Trans. - Brown Z, Szymanowski B, Musser M, Saha D, Seaver S. 2007. Manufacturing of thin wall structural automotive components through high vacuum die casting technology. Presented at International Die Casting
Congress and Exposition, Houston, TX, May 15–18 - Casarotto F, Franke AJ, Franke R. 2012.High-pressure die cast (HPDC) aluminum alloys for automotive
applications. In Advanced Materials in Automotive Engineering, ed. J Rowe, pp. 109–49. Sawston, UK:
Woodhead - Apelian D. 2009. Aluminum Cast Alloys: Enabling Tools for Improved Performance. Wheeling, IL: N. Am.Die Cast. Assoc.
- Taylor JA. 2012. Iron-containing intermetallic phases in Al-Si based casting alloys. Proc. Mater. Sci. 1:19–33
- Dinnis CM, Taylor JA, Dahle AK. 2006. Interactions between iron, manganese, and the Al-Si eutectic
in hypoeutectic Al-Si alloys. Metall. Mater. Trans. A 37:3283–91 - Ceschini L, Boromei I, Morri A, Seifeddine S, Svensson IJ. 2009. Microstructure, tensile and fatigue
properties of the Al–10% Si–2% Cu alloy with different Fe and Mn content cast under controlled conditions. J. Mater. Proc. Technol. 209:5669–79 - Cinkilic E, Sun W, Klarner AD, Luo AA. 2015. Use of CALPHAD modeling in controlling microstructure of cast aluminum alloys. Pap. 15-044, Am. Foundry Soc.
- Klarner AD, et al. 2017. A new fluidity die for castability evaluation of high pressure die cast alloys.Trans.
North Am. Die Cast. Assoc. T17–101 - Luo AA. 2013. Application of computational thermodynamics and CALPHAD in magnesium alloy development. In Proc. 2nd World Congr. Integr. Comput. Mater. Eng., ed. M Li, C Campbell, K Thornton, E Holm, P Gumbsch, pp. 3–8. Warrendale, PA: TMS
- Am. Chem. Counc. 2018. Plastics and polymer composites in light vehicles. Rep., Am. Chem. Counc.
- Institute for Advanced Composites Manufacturing Innovation (IACMI). 2017. Phase two roadmap. Feb. http://www.iacmi.org
- Vaidya U. 2017. Advanced composite materials and manufacturing in vehicles, wind and compressed gas storage. Text. World, Mar. 21
- Cedric B. 2016. New developments for mass production of epoxy automotive composites. Presented at Global Automotive Lightweight Materials Conference, Detroit. Accessed Aug. 2018
- Gardiner G. 2015. HP-RTM on the rise. Compos. World, Apr. 14
- Gardiner G. 2016. Wet compression molding. Compos. World, Jan. 2
- Rocky Mt. Inst. 2013. Kickstarting the widespread adoption of automotive carbon fiber composites: key findings and next steps. Rep., Rocky Mt. Inst.
- Thattaiparthasarathy K, Pillay S, Bansal D, Ning H, Vaidya U. 2013. Processing and characterization
of continuous fibre tapes co-moulded with long fibre reinforced thermoplastics. Polym. Polym. Compos. 21(8):483–94 - Emerson D, Grauer D, Hang B, Reif M, Henning F, et al. 2012. Using unidirectional glass tapes to improve impact performance of thermoplastic composites in automotive applications. Presented at Soc. Plast. Eng.
Automot. Compos. Conf. Exhib., Troy, MI, Sept. 11–13 - LayStitch Technology. 2018. Print technology. http://www.laystitch.com/Technology.html. Accessed
Aug. 2018 - Behrens BA, Raatz A, Hubner S, Bonk C, Bohne F, et al. 2017. Automated stamp forming of continuous
fiber reinforced thermoplastics for complex shell geometries. Proc. CIRP 66:113–18 - Vaidya UK. 2010. Composites for Automotive, Truck and Mass Transit. Lancaster, PA: DEStech
- Thattaiparthasarathy KB. 2008. Process simulation, design and manufacturing of a long fiber thermoplastic composite for mass transit application. Composites A Appl. Sci. Manuf. 39(9):1512–21
- Thomason JL, Vlug MA. 1996. Influence of fiber length and concentration on the properties of glass
fibre–reinforced polypropylene. 1. Tensile and flexural modulus.Composites A Appl. Sci.Manuf. 27(6):477–84 - IDI Compos. 2018. Structural thermoset composites. http://www.idicomposites.com/technology-stc.
php - Cabrera-Rios M, Castro JM. 2006. An economical way of using carbon fibers in sheet molding compound
compression molding for automotive applications. Polym. Compos. 27(6):718–22 - Carberry W. 2008. Airplane recycling efforts benefit Boeing operators. AERO, Quart. 4. http://www.
boeing.com/commercial/aeromagazine/articles/qtr_4_08/pdfs/AERO_Q408_article02.pdf - IACMI. 2016. Pioneering partnerships announced for composite recycling. News Release, IACMI. http://iacmi.org/2016/07/01/pioneering-partnerships-announced-composite-recycling/. Accessed Aug. 1
- Janney M, Ledger J, Vaidya U. 2012. Long fiber thermoplastic composites from recycled carbon fiber. Presented at ISTC, 44th, Charleston, SC, Oct. 22–25
- Janney M, Vaidya U, Sutton R, Ning H. 2014.Re-grind study of PPS-based long fiber thermoplastic composites. Presented at SAMPE, Seattle
- Okine RK, Edison DH, Little NK. 1990. Properties and formability of an aligned discontinuous fiber
thermoplastic composite sheet. J. Reinf. Plast. Compos. 9(1):70–90 - Sloan J, ed. 2016. Composites recycling becomes a necessity. Compos. World, May 16. https://www.
compositesworld.com/articles/composites-recycling-becomes-a-necessity - Blackman B, Kinloch A, Watts J. 1994. The plasma treatment of thermoplastic fibre composites for
adhesive bonding. Composites 25(5):332–41 - Brosius D, Armstrong K. 2017. IACMI baseline cost and energy metrics. Presentation, Mar.
- Das S, Armstrong K. 2018. FRPC energy use estimation tool. https://ornlenergyestimatortools.
shinyapps.io/frpc-energy-estimator2/ - USDRIVE. 2015. Materials technical team roadmap. Rep. https://www.energy.gov/…/MTT%
20Roadmap%20UPDATE%20Apprvd%2003-11-1 - Baldan A. 2004. Adhesively-bonded joints and repairs in metallic alloys, polymers and composite materials: adhesives, adhesion theories and surface pretreatment. J. Mater. Sci. 39(1):1–49
9. 著作権:
本資料は、[Alan Taub ら] による論文: [Materials for Automotive Lightweighting] に基づいて作成されました。
論文出典: [https://doi.org/10.1146/annurev-matsci-070218-010134]
本資料は上記の論文に基づいて要約作成されたものであり、情報提供のみを目的としています。無断での商業利用は禁止されています。
Copyright © 2025 CASTMAN. All rights reserved.