1.概要:
- タイトル: Aluminum High Pressure Vacuum Die Casting Applications for the Multi Material Lightweight Vehicle Program (MMLV) Body Structure
- 著者: Randy Beals¹, Jeff Conklin¹, Tim Skszek¹, Matt Zaluzec², David Wagner²
- 発行年: 2015年
- 発行誌/学会: Light Metals 2015, TMS (The Minerals, Metals & Materials Society)
- キーワード: アルミニウム、高圧真空ダイカスト、車体構造
2. 研究背景:
この研究は、2012年にマグナ・インターナショナル、米国エネルギー省、フォード・モーター・カンパニーが共同で開始した多材料軽量車両(MMLV)プロジェクトの一環として行われました。社会的な背景としては、車両軽量化による燃費向上と排出ガス削減のニーズがあります。研究の必要性は、従来の単一材料(鋼、高強度鋼、またはアルミニウム)車体設計の限界(高コスト、既存プロセスとの非互換性、グローバル生産能力の不足)を克服することにあります。従来の研究は単一材料ソリューションに焦点を当てていましたが、多材料アプローチはコンポーネントレベルの統合に限定されていました。
3. 研究目的と研究課題:
- 研究目的: CセグメントとDセグメントの車両の軽量化された車体構造設計において、アルミニウム高圧真空ダイカスト(hpvdc)部品による重量削減効果と性能を評価すること。
- 主要な研究課題: アルミニウムhpvdc部品を統合した多材料車体構造は、基準車両と比べてどれだけ軽量化され、剛性、耐久性、衝突安全性はどのように維持されるか?
- 研究仮説: アルミニウムhpvdc部品を戦略的に使用することで、従来の鋼製車体と比較して重量を削減し、同時に衝突性能と組立コスト(部品点数削減)を改善できる。
4. 研究方法:
- 研究設計: MMLVプロジェクトで製造された試作車両を用いて、車体構造におけるアルミニウムhpvdc部品の重量削減効果と性能を分析する実証研究。
- データ収集方法: MMLV車両の車体構造設計、製造プロセス、性能試験結果(剛性、耐久性、衝突安全性)のデータを収集。
- 分析方法: アルミニウムhpvdc部品を含むMMLV車体構造の重量、剛性、耐久性、衝突性能を定量的に分析し、基準車両と比較。MAGMASOFT®ソフトウェアを用いた鋳造シミュレーションによる鋳造プロセスの最適化。
- 研究対象と範囲: MMLVプロジェクトで製造された試作車両の車体構造(BIW)。8個のhpvdcアルミニウム鋳造部品、6個のアルミニウム押出材、12個の主要な鋼鉄スタンピング、多数のアルミニウムスタンピングなどが含まれる。
5. 主要な研究結果:
- 主要な発見: MMLV車両は、2013年型フォード・フュージョンモデルと比べて23.5%(1170kg対1559kg)の軽量化を実現しました。これは、アルミニウムhpvdc部品の使用が大きく貢献しています。
- 定量的/定性的分析結果: BIW構造の63%がアルミニウム、37%が鋼鉄で構成されています。8個のhpvdc部品を使用することで、部品点数を32個削減し、剛性を向上させました。衝突シミュレーションの結果、基準車両と比べて衝突安全性が向上していることが確認されました。
- データ解釈: アルミニウムhpvdc鋳造技術は、軽量化、部品統合、組立工程の簡素化などを通じて、車体構造の軽量化と性能向上に貢献しています。低圧精密砂型鋳造技術を用いて、hpvdc部品と同様の性能を確保しています。様々な接合技術(SPR、CMT溶接、接着剤)を用いて、多材料車体構造を実現しています。
- Figure List:
- Figure 1. MMLV concept vehicle
- Figure 2. MMLV BIW Design
- Figure 3. MMLV BIW concept prototype
- Figure 4. MMLV BIW showing hpvdc castings
- Figure 5. MMLV vacuum die cast shock tower casting x-ray
- Figure 6. MMLV kick down rail, Magmasoft Casting Fill Simulation
- Figure 7. MMLV aluminum shock tower casting
- Figure 8. MMLV aluminum shock tower casting joined to the front end assembly by SPR and CMT methods
- Figure 9. MMLV kick down rail
- Figure 10. MMLV Frontal 40% off-set impact FEA with improved intrusion over baseline
- Figure 11. MMLV hinge pillar
- Figure 12. MMLV hinge pillar casting one sided joining with flow drill screws
- Figure 13. MMLV mid rear rail
- Figure 14. MMLV mid rear rail assembly
- Figure 15. SPR of MMLV shock tower casting to front rail
- Figure 16. MMLV cast aluminum hinge pillar to cast aluminum extruded rail TIG weld.
- Figure 17. MMLV TIG weld detail
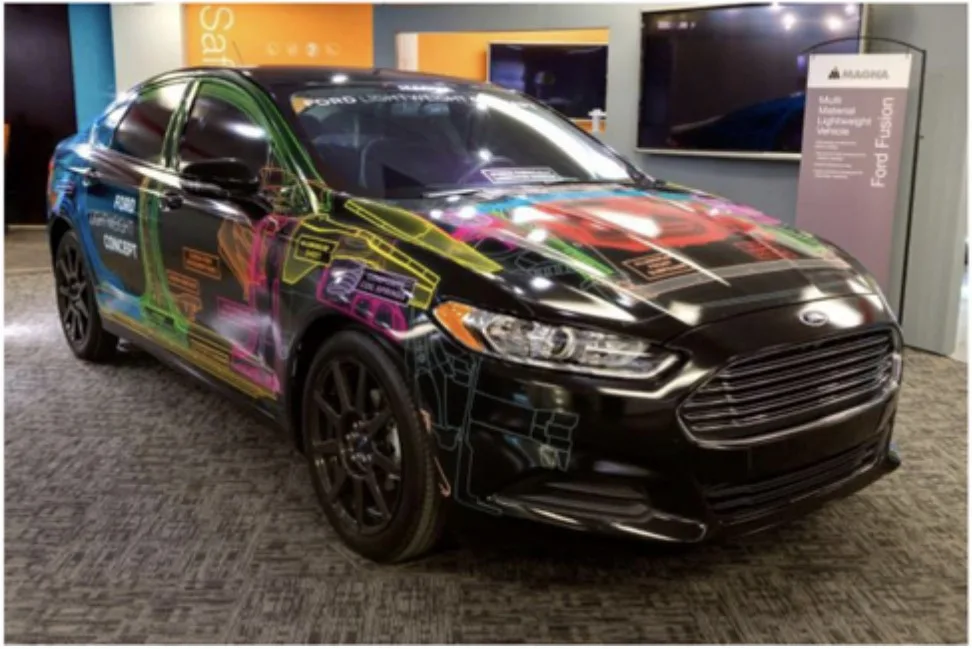
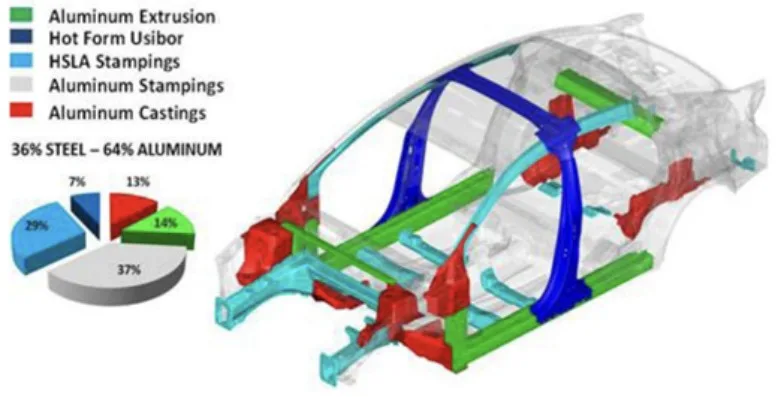
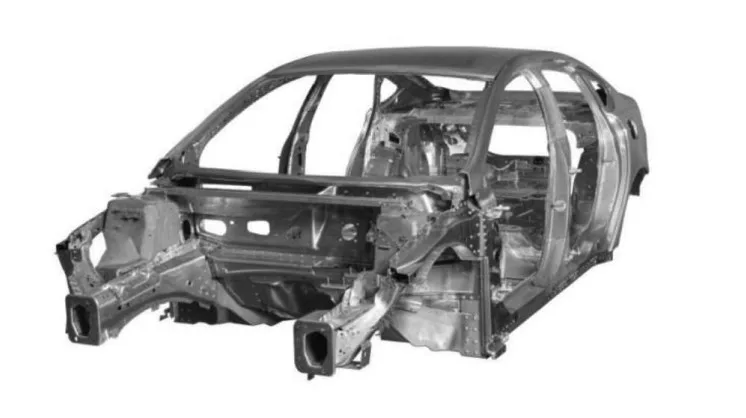
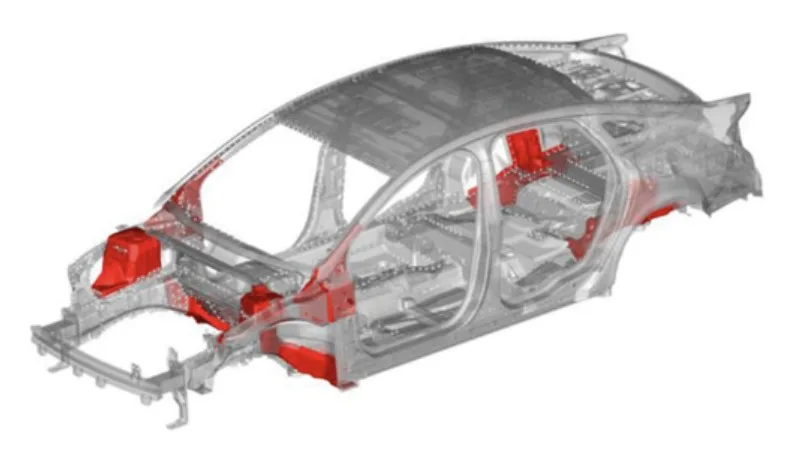
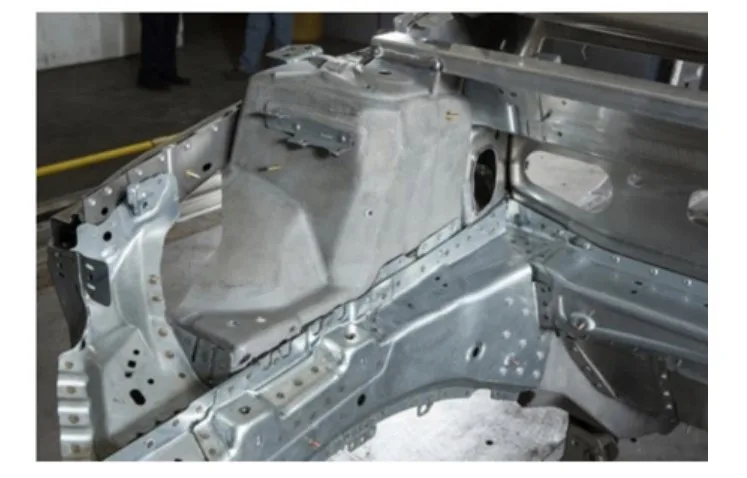
6.結論と考察:
MMLVプロジェクトは、アルミニウムhpvdc部品を活用した多材料車体構造設計の有効性を実証しました。軽量化と同時に、剛性、耐久性、衝突安全性を確保し、部品点数削減による組立コストの削減効果も得られました。ただし、低圧精密砂型鋳造技術の活用や少量生産に伴うコスト面は、今後の研究課題となります。
7. 今後の研究方向:
アルミニウムhpvdc技術と高強度鋼やその他の高性能材料との組み合わせによる軽量化研究、大量生産に向けた工程最適化研究、様々な接合技術の性能と経済性の分析、そして様々な車体形状やサイズへの拡張適用に向けた更なる研究が必要です。
8.参考文献:
- Aluminum Alloys and Manufacturing Processes for Automotive Structural Applications, Alan Luo, The Ohio State University, TMS 2014
- The Aluminum Advantage Commercial Vehicle Applications, Todd Summe, Technical Committee, The Aluminum Association's Aluminum Transportation Group Division, SAE 2012
- Cost Effectiveness of a Lightweight Design for 2017- 2020: An Assessment of a Midsize Crossover Utility Vehicle, Cheryl Caffrey, Kevin Bolon, Hugh Harris (EPA), Greg Kolwich (FEV Inc.), Robert Johnston (EDAGInc.), SAE 2012
- Cost-Effectiveness of a Lightweight BIW Design for 2020-2025: An Assessment of a Midsize Crossover Utility Vehicle Body Structure; Gregory Peterson, Andrew Peterson, Lotas Engineering Inc, SAE 2013
- The Past, Present and Future of Aluminum in North American Light Vehicles, Dick Schultz, Ducker, October 2012
- Heat Treating of High Pressure Die Castings; Challenges and Possibilities: Salem Seifeddine, Swerea SWECAST and Darya Poletaeva, Jönköping University, TMS 2014.
- The application of multiphase steel in tlie Body-inWliite, Markus Pfestorf, BMW AgH
- A Lightweight Automobile Body Concept Featuring Ultra-Large, Ήιίη-Wall Structural Magnesium Castings, Steve Logan, Chrysler, SAE 2007.
- A Process of Decoupling and Developing Body Structare for Safety Performance, John Madakacherry, Martin Isaac, General Motors, 5th European LS-DYNA Users Conference, 2005.
- Recent Advancements on Porosity Simulation in High Pressure Die Casting, Chung Wliee Kim, Kimio Kubo, EKK Inc., AFS 2005.
- Light-Weighting the 2013 Cadillac ATS Body Structare, Warren J. Parsons, General Motors, Great Designs in Steel 2012.
- High Integrity Diecasting for Structural Applications, Martin Hartlieb, Viami International Inc, iMdc meeting, WPI, Worcester Mass, 2013.
- 2013 Ford Fusion, Shawn Morgans, Ford Motor co., Euro Car Body Conference 2012.
- Challenges and opportunities relative to increased usage of aluminum within the automotive industry, Blair Carlson, Paul Krajewski, Anil Sachdev, Jim Schroth, David Sigler, Mark Verbrugge, General Motors R&D, Warren, MI, TMS 2010
- Trends in Automotive - Aluminum, Doug Richman, Aluminum Association's Transportation Group (ATG), OPC Meeting, Aim Arbor, MI, July 16, 2013
- The Future of Aluminum Use in tlie Auto Industry, Alcoa, October 31,2013
- Future Material Opportunities and Direction for Lightweighting Automotive Body Structures, Marcel Camion, General Motors, February 9, 2012
- The Increasing Use of Aluminum: Prospects and Implications, John Hartley, European Commission Institute for Prospective Technological Studies, Nov 1996
著作権
本資料は[Randy Beals¹, Jeff Conklin¹, Tim Skszek¹, Matt Zaluzec², David Wagner²]の論文:[Aluminum High Pressure Vacuum Die Casting Applications for the Multi Material Lightweight Vehicle Program (MMLV) Body Structure]に基づいて作成されました。
商業目的での無断使用を禁じます。
Copyright © 2025 CASTMAN. All rights reserved.