- 研究の核心目的: 電子機器の高性能化、小型化に伴う高度な熱管理ニーズに対応するため、従来のダイカスト法および押出成形法の限界を超える高密度ダイカスト(HDDC)法を開発し、高性能ヒートシンクの製造における新たな可能性を示すこと。
- 主要な方法論: 高熱伝導率アルミニウム合金を用いたHDDCプロセスを開発し、様々なフィン形状を持つヒートシンクを試作。計算流体力学(CFD)シミュレーションと実験的手法を用いて、HDDCプロセスの性能評価を実施。異なる材料(例:銅)をHDDCプロセスに統合する可能性についても調査。
- 重要な結果: HDDCプロセスは、従来のダイカスト法に比べて熱放散効率を大幅に向上。3次元形状設計の柔軟性を提供し、押出成形法では実現不可能な複雑なフィン形状のヒートシンクの製造を可能にする。高熱伝導率アルミニウム合金の使用と、他の高熱伝導率材料の統合により、多孔性がなく、高強度で熱伝導率の高い部品の製造が可能となる。
研究者情報
- 所属機関: Aavid Thermalloy S.r.l.
- 著者: Andrea Sce, Lorenzo Caporale
- 主要研究分野: 熱管理、ダイカストプロセス
研究背景と目的
- 研究が必要な産業的背景: 電子機器の高性能化と小型化のトレンドにより、熱管理の重要性が増大。大量生産に適したコスト効率の良い、拡張性の高いヒートシンク製造技術が必要。
- 具体的な技術的問題・課題: 従来の押出成形プロセスは2次元設計に限定され、使用可能なアルミニウム合金の種類(6xxx系など)やフィン形状、フィン密度に制約がある。従来のダイカストプロセスは、使用合金の熱伝導率が低いため熱放散性能が低く、また多孔性の問題により機械的強度や表面仕上げに課題がある。異なる材料を組み合わせることが困難。
- 研究目標: 押出成形法と従来のダイカスト法の限界を克服する、革新的な高密度ダイカスト(HDDC)プロセスを開発すること。高熱伝導率アルミニウム合金を用いて熱放散性能を向上させる。3次元形状設計の自由度を高める。異なる材料を組み合わせることで熱管理性能を向上させる。
論文の主要な目的と研究内容
- 論文の主要な目的と研究内容: 高密度ダイカスト(HDDC)プロセスを用いた高性能ヒートシンク製造技術の開発。既存の押出成形法およびダイカスト法との性能比較分析。
- 解決すべき問題点: 従来の押出成形法およびダイカスト法における熱伝導率の低さ、設計の自由度の低さ、様々な材料の組み合わせの困難さといった問題点を解決する。
- 問題解決のための段階的アプローチ:
- 高熱伝導率アルミニウム合金(Al 6063またはAl 11070)を用いたHDDCプロセスの開発。
- 高圧注入により多孔性のない高強度ヒートシンクの製造。
- 3次元形状設計により、様々なフィン形状(平板フィン、傾斜フィン、楕円形ピン、円形ピン、放射状プレートなど)を実現。
- 計算流体力学(CFD)シミュレーションと実験により、HDDCプロセスの熱伝達性能を従来のダイカストプロセスと比較評価。
- 異なる材料(アルミニウム、銅など)を組み合わせることで熱伝達性能の向上と新たな製品開発。
- 耐久性向上のための表面処理技術の適用。
- 主要な図表: 図1、図2、図3、図4、図5、図6、図7、図8、図9、図10、図11は、押出成形法とダイカスト法の限界、HDDCプロセスの工程、CFDシミュレーション、組織解析、機械的特性、開発ロードマップ、製品例、材料の統合、大型HDDC部品などを示している。(図表の詳細な説明は下記参照)
図表の詳細な説明:
(注記: 以下の説明は、解釈を避けるため、論文のキャプションおよび周辺テキストからの直接引用に大きく依存しています。完全な説明には、図表自体の再現が必要となります。)
- 図1. 押出成形法の限界: フィン形状、フィン密度、使用可能なアルミニウム合金の種類に関する押出成形法の限界を示す図。隣接するセクション間の急激な形状変化は許容されず、フィン高さ対ギャップ比にも上限がある。6xxx系アルミニウム合金しか使用できない。
- 図2. ダイカスト法の限界: キャストプロセスによる形状制限、合金選択の制限(容易に鋳造できる合金には銅含有量が高く、屋外用途での耐食性が低い)、固有の多孔性、表面処理の困難さなどを示す図。
- 図3. HDDCプロセスの工程: 溶湯の注入、パンチの降下、溶湯への加圧、固化部品の排出というHDDCプロセスの段階的工程を示す図。
- 図4. 従来のダイカスト法(左)とHDDC法(右)のCFD比較;HDDCはより多くのフィンを許容: 従来のダイカスト法とHDDC法を比較したCFDシミュレーション結果を示す図。HDDC法は熱抵抗(Rth)が低く、より多くのフィンを配置できることを示す。各プロセスのTmax、Rth、APなどの数値データが示されている。
- 図5. HDDC組織とダイカスト組織の組織解析: HDDC法と従来のダイカスト法による部品の微細組織を比較した顕微鏡写真。HDDC法では多孔性が無いことが分かる。
- 図6. Al 6xxx-T4系に関する機械的特性:HDDCと押出材の比較試験結果: 同一のアルミニウム合金を用いて製造されたHDDC部品と押出部品の機械的特性(降伏強度、引張強度)を比較したグラフ。
- 図7. 機能開発の進捗パス: 大型部品や統合機能を含むHDDCプロセスの段階的開発ロードマップを示す図。
- 図8. HDDC製品の例: HDDCプロセスで製造可能な様々な部品の例を示す画像。多様な形状と設計の柔軟性を示している。
- 図9. AlとCuを用いたHDDC製品の例(断面図-60x17x40 mm): アルミニウムと銅を組み合わせたHDDC部品の断面図。
- 図10. AlとCuを用いたHDDCに関する顕微鏡観察と超音波検査: アルミニウムと銅を組み合わせたHDDC部品の界面の微細組織と超音波検査結果。
- 図11. AlとCuを用いた大型HDDC部品: HDDCプロセスで製造された大型部品の画像。
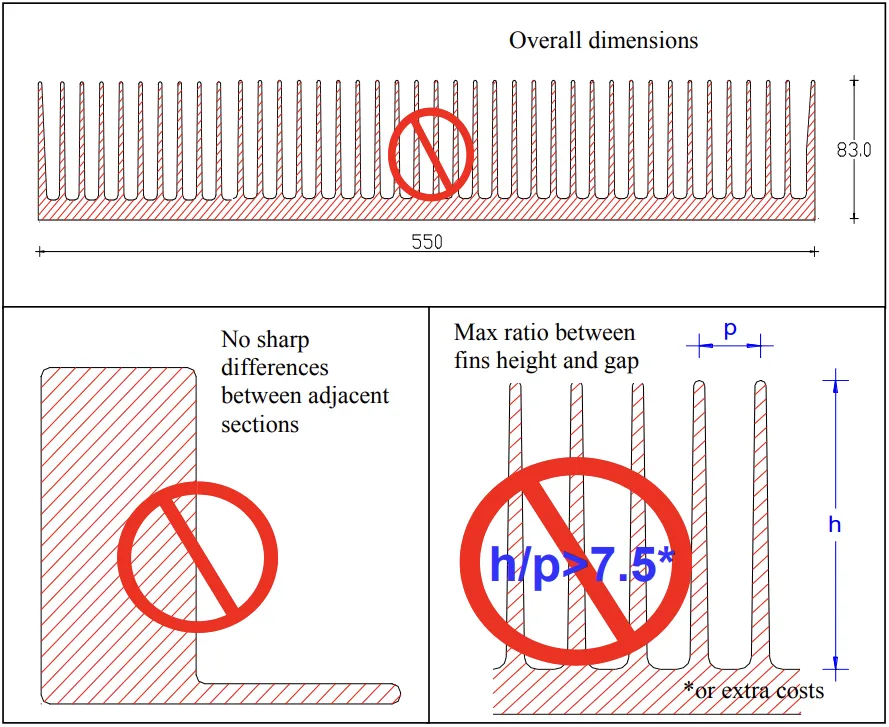
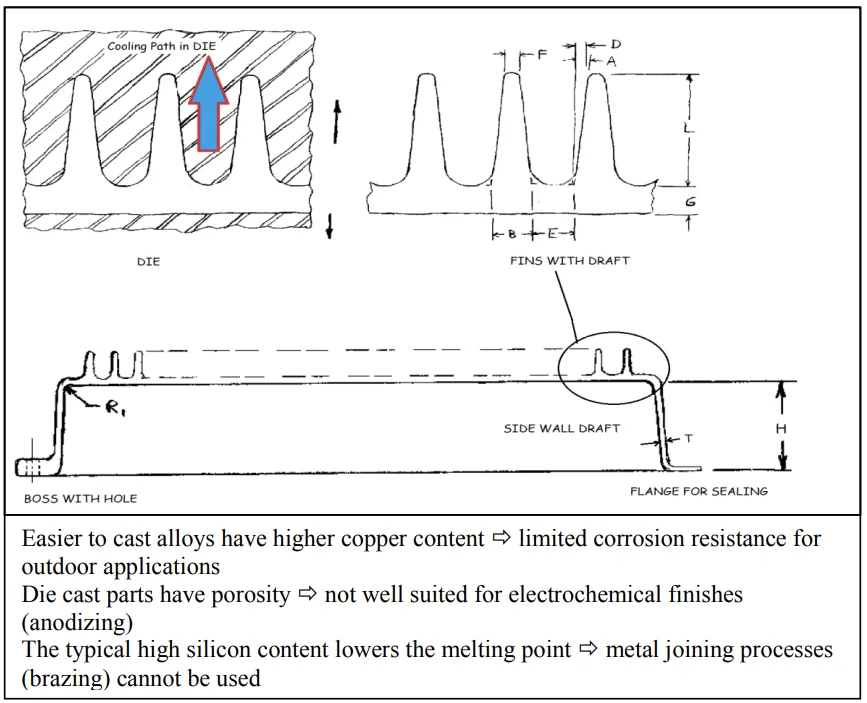
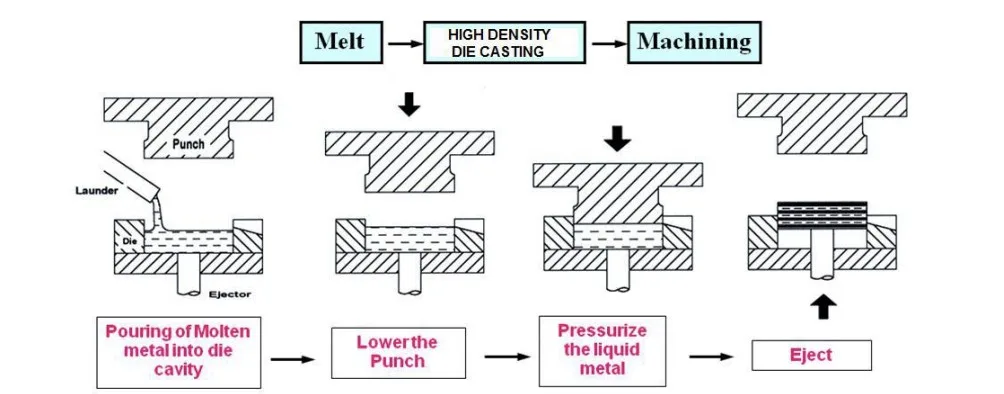
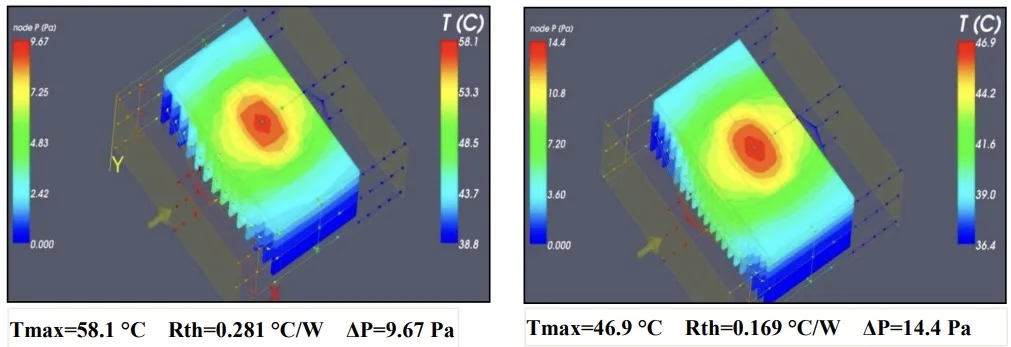
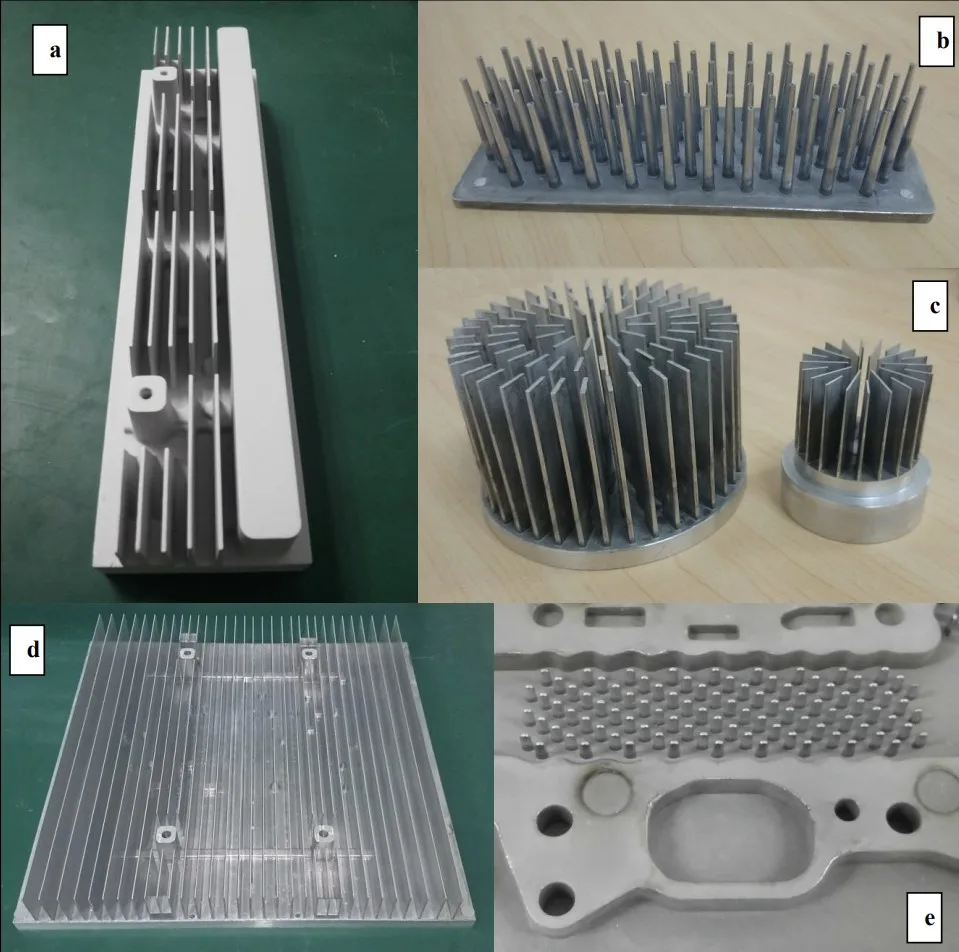
結果と成果
- 定量的結果: CFDシミュレーションでは、HDDC法による熱抵抗が従来のダイカスト法に比べて約40%低減。機械試験では、HDDC部品の引張強度と降伏強度は、従来の押出部品と同等かそれ以上であることが示された。
- 定性的結果: HDDCプロセスは、多孔性がなく、高強度で、複雑な3次元形状を持つヒートシンクの製造を可能にし、押出成形法では実現不可能な設計柔軟性を提供する。銅などの異なる材料を統合することも可能。
- 技術的成果: 高密度ダイカスト(HDDC)プロセスの開発により、高性能ヒートシンク製造技術を確立。従来技術の限界を超え、熱管理技術の向上に貢献。埋め込み式ヒートパイプの統合など、更なる技術向上も期待できる。
著作権と参考文献
この文書は、Andrea SceとLorenzo Caporaleによる論文「High Density Die Casting (HDDC): new frontiers in the manufacturing of heat sinks」を要約したものです。
DOI: 10.1088/1742-6596/525/1/012020
この要約は情報提供のみを目的としており、著作権者の許可なく商業目的で使用することはできません。