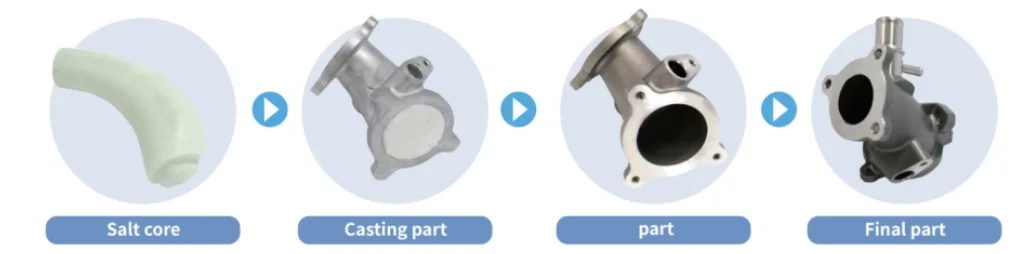
アルミ高圧ダイカストにおけるアンダーカット形状製品へのソルトコア技術の適用
アルミ高圧ダイカストは、その高い生産効率と精度で広く利用されている製造プロセスです。しかし、アンダーカット形状(金型の開閉方向と干渉する形状)を持つ部品を製造する際には、大きな課題があります。従来の解決策としては、スライドコアや分割金型を使用する方法がありますが、これらは製造プロセスを複雑化させ、コストを増加させるだけでなく、設計の自由度を制限します。
ソルトコア技術によるアンダーカット形状の解決
ソルトコア技術は、アルミダイカストにおけるアンダーカット形状の課題を解決する革新的な方法です。このプロセスでは、溶解可能な塩を素材として使用し、アンダーカット形状や複雑な内部構造を形成します。
技術的なプロセス
- ソルトコアの製造:
- ソルトコアは、特殊なダイカスト技術を使用して製造され、耐熱性があり、正確な形状が可能です。
- 塩素材を用いることで、複雑で精密な形状を成形できます。
- コアの挿入と鋳造:
- ソルトコアをダイカスト金型内に配置します。
- 溶融したアルミ合金を高圧で射出し、ソルトコアを包み込む形で部品を成形します。
- ソルトコアの除去:
- ダイカスト後、部品を水や溶剤に浸し、ソルトコアを溶解します。
- これにより、アンダーカット形状や複雑な内部構造が完成します。
ソルトコア技術の利点
- 複雑なアンダーカット形状の実現:
- 従来のダイカスト金型設計の制約を克服し、複雑な内部構造やアンダーカット形状の製造が可能です。
- 後加工の最小化:
- 追加の機械加工や組み立て作業を削減し、生産時間とコストを削減します。
- 設計の自由度向上:
- 金型設計の制約を気にせず、部品の機能や軽量化に重点を置いた設計が可能になります。
- 高精度・高一貫性:
- ソルトコアは高い寸法精度を持つため、生産された部品の品質と性能が向上します。
- リバースエンジニアリングの防止:
- ソルトコアは鋳造後に溶解して消失するため、競合他社が内部構造を解析または模倣することが困難です。
結論
ソルトコア技術は、アンダーカット形状を持つアルミダイカスト部品の製造における課題を解決する革新的なソリューションです。この技術は設計の自由度、生産効率、精密性を同時に向上させ、自動車、航空宇宙、その他の業界で重要な役割を果たしています。
ソルトコア技術の主な応用分野
- 自動車部品:
- ターボチャージャーハウジング、デファレンシャルハウジング、エキゾーストマニホールド、トランスミッション内部チャネルなど。
- 航空宇宙部品:
- 軽量化と高精度が求められるジェットエンジン内部や冷却システムのチャネル。
- 電子機器や冷却システム:
- 熱管理性能を最適化するための複雑な設計を持つヒートシンクや冷却チャネル。
Automotive Components
1. ターボチャージャーハウジング内部構造
従来のアルミニウム高圧ダイカスト法:
- ターボチャージャーの内部流路は複雑な形状で、アンダーカットが多く、金型の設計や加工が難しいため、分割パーツを組み立てる方法が採用されていました。
- 組み立て部で気密性の問題や強度の低下が発生する可能性がありました。
ソルトコア工法適用の特徴:
- 一体成型: ソルトコアを使用することで、組み立てなしで複雑な内部構造を一体化して成型可能。
- ガス流路の最適化: 精密な内部形状により、空気や排気ガスの流れが最適化され、ターボ効率が向上します。
- 軽量化: 内部の空洞設計により、重量を削減し、エンジン全体の性能を向上。
2. 排気マニホールド(エキゾーストマニホールド)
従来のアルミニウム高圧ダイカスト法:
- アンダーカット部分が多いため、複数パーツで構成し、溶接やボルトで接続する手法が一般的でした。
- 高温環境下で溶接部が劣化しやすく、信頼性の問題が発生することがありました。
ソルトコア工法適用の特徴:
- 高温耐久性の向上: 組み立てなしの一体成型により、接続部の劣化を防止。
- 複雑形状の実現: 排気ガス流路を精密に設計し、エンジン性能を向上。
- 製造効率: 溶接や追加工程を削減し、大量生産が容易に。
3. エンジンブロック内部のオイルチャンネル
従来のアルミニウム高圧ダイカスト法:
- 複雑なオイルチャンネルを形成するためには、追加の機械加工や組み立てが必要で、コストと製造時間が増加しました。
ソルトコア工法適用の特徴:
- 高精度な内部構造: ソルトコアを使用してオイルチャンネルを一体化して製造可能。
- エンジン寿命の延長: 高精度なオイル流路が潤滑効率を最大化し、エンジンの耐久性を向上。
- 軽量化: 不要な材料を削減し、軽量化と強度を両立。
4. トランスミッションハウジング
従来のアルミニウム高圧ダイカスト法:
- アンダーカット形状を持つ内部流路を追加加工または分割部品として製造し、最終的に組み立てていました。
ソルトコア工法適用の特徴:
- 内部流路の一体成型: ソルトコアで内部流路を直接形成し、追加加工を省略。
- 密閉性の向上: 組み立てが不要となり、流体漏れのリスクを最小化。
- 軽量化: 内部空洞の設計を最適化し、重量削減と強度維持を両立。
5. 冷却システム部品
従来のアルミニウム高圧ダイカスト法:
- シンプルな冷却チャンネルしか製造できず、複雑な冷却構造は追加加工や組み立てが必要でした。
ソルトコア工法適用の特徴:
- 効率的な冷却チャンネル設計: ソルトコアを用いることで熱交換効率を最大化する冷却チャンネルが可能。
- 信頼性の向上: 組み立てなしで一体化されるため、部品寿命が向上。
- 軽量化: 内部形状を最適化して重量を削減。
6. サスペンション部品
従来のアルミニウム高圧ダイカスト法:
- アンダーカット形状の製造が難しく、強度を保つために部品を厚く設計する必要がありました。
ソルトコア工法適用の特徴:
- 軽量かつ高強度: 内部空洞を形成して重量を削減しながら、強度と耐久性を向上。
- 自由度の高い設計: 複雑な形状設計が可能になり、サスペンション性能が向上。
- 製造効率: 単一工程で精密部品を製造可能。
7. ブレーキキャリパー
従来のアルミニウム高圧ダイカスト法:
- 内部の油圧通路を加工または組み立てる必要があり、製造工程が増加しました。
ソルトコア工法適用の特徴:
- 内部油圧通路の統合: 一体成型で油圧効率を向上し、ブレーキ性能を最適化。
- 軽量化: 内部形状を最適化することで、強度を保ちながら軽量化を実現。
- 製造効率: 高精度で一貫した品質を提供。
8. 燃料噴射器ハウジング
従来のアルミニウム高圧ダイカスト法:
- 燃料通路の形成には、追加加工や部品の組み立てが必要でした。
ソルトコア工法適用の特徴:
- 精密な燃料通路設計: ソルトコアにより燃料効率を最大化する内部構造を実現。
- 信頼性の向上: 組み立てが不要で漏れのリスクを軽減。
- 軽量化: 内部空洞を適切に設計して軽量化。
9. ディファレンシャルハウジング
従来のアルミニウム高圧ダイカスト法:
- 複雑な内部形状の作成に追加加工が必要で、組み立てコストが発生していました。
ソルトコア工法適用の特徴:
- 複雑内部形状の実現: 内部ギアや流体通路を一体成型で作成可能。
- 耐久性の向上: 一体設計により構造強度が向上。
- 軽量化: 内部構造の最適化による重量削減。
10. 電気自動車バッテリーモジュールケース
従来のアルミニウム高圧ダイカスト法:
- 冷却チャンネルを追加加工で形成するか、別部品として組み立てていました。
ソルトコア工法適用の特徴:
- 効率的な熱管理: ソルトコアを活用した複雑な冷却チャンネルで熱分散性能を向上。
- 軽量化: 内部形状の最適化により軽量化を実現。
- 構造的安定性: 一体成型により信頼性が向上。
まとめ:
ソルトコア工法は、アンダーカット形状を持つ部品の製造において、従来のダイカスト法の限界を克服し、軽量化、信頼性向上、製造効率の向上を可能にする画期的な技