マグネシウムダイカスト:ホットチャンバー vs. コールドチャンバー、あなたの用途に最適なプロセスは?
本技術概要は、Dr. Ing Norbert Erhard氏およびBob Tracy氏による論文「Properties of Diecasting Alloys and a Comparison of Hot and Cold Chamber Processes for Magnesium Die Casting」に基づいています。HPDC製品のリーディングメーカーである株式会社CASTMANの専門家が、ダイカスト専門家向けに要約・分析したものです。
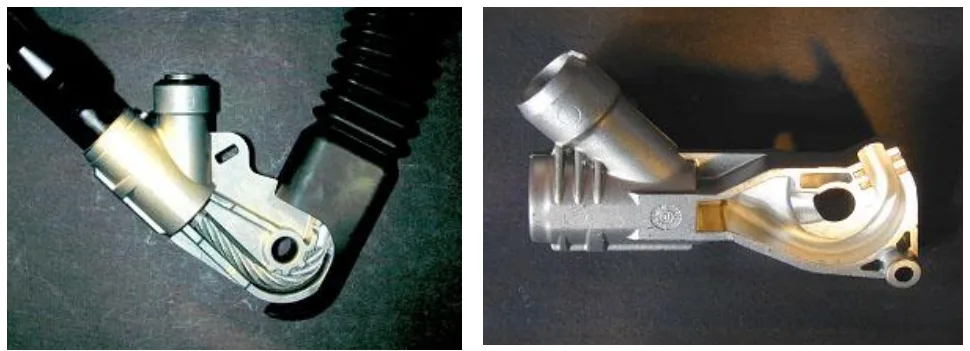
キーワード
- 主要キーワード: マグネシウムダイカスト ホットチャンバー コールドチャンバー 比較
- 副次キーワード: ダイカスト合金特性, 薄肉鋳造, 鋳造品質, 鋳造プロセス, 金型寿命, ガス気孔, 鋳造方案
エグゼクティブサマリー
(本論文の核心をなす問題、アプローチ、そして最も重要な発見を3~4つの箇条書きで要約します。)
- 課題: 自動車産業を中心に需要が拡大するマグネシウムダイカストにおいて、ホットチャンバーとコールドチャンバーのどちらのプロセスが特定の用途に対してコスト、品質、性能の面で最適なのかを判断すること。
- 手法: 本論文では、機械サイズ、サイクルタイム、鋳造圧力、温度管理、金型設計、最終製品の特性など、多岐にわたる技術的パラメータにわたって、マグネシウムダイカストにおけるホットチャンバープロセスとコールドチャンバープロセスを包括的に比較・分析しています。
- 重要な発見: ホットチャンバープロセスは、薄肉品(1.2mm未満)の鋳造において、より経済的で高品質な製品を製造するのに優れています。一方、コールドチャンバープロセスは、優れた機械的特性が求められる厚肉品や、より高い鋳造性が要求される場合に適しています。
- 結論: 最適なプロセスの選択は、最終製品に要求される特性(肉厚、機械的強度、気孔率など)に大きく依存します。この比較は、ダイカストメーカーが情報に基づいた意思決定を行うための重要な指針となります。
課題:なぜこの研究がHPDC専門家にとって重要なのか
亜鉛(Zn)、アルミニウム(Al)、マグネシウム(Mg)の消費量が世界的に増加する中、特に軽量なアルミニウムとマグネシウムは自動車産業で70%以上を占めるなど、その重要性を増しています。マグネシウムはアルミニウムより約50%も軽量であり、軽量化が求められるコンポーネントにとって非常に魅力的な材料です。
しかし、マグネシウムダイカストを成功させるには、単に材料を選ぶだけでは不十分です。ホットチャンバーとコールドチャンバーという2つの主要な製造プロセスが存在し、それぞれに明確な長所と短所があります。プロセスの選択を誤ると、サイクルタイムの悪化、品質のばらつき(特にガス気孔)、金型寿命の低下、そして最終的にはコストの増大につながる可能性があります。多くのエンジニアや製造管理者は、「我々の製品にとって、どちらのプロセスが本当に最適なのか?」という根本的な問いに直面しています。この論文は、その問いにデータに基づいた明確な答えを提供します。
アプローチ:方法論の解明
この研究は、実験室での単一の実験ではなく、長年の経験と実用データに基づいた包括的な比較分析を採用しています。研究者たちは、ホットチャンバーとコールドチャンバープロセスを以下の複数の側面から徹底的に比較しました。
- 機械とプロセスパラメータ: ロック力、鋳造能力、サイクルタイム、射出速度、鋳造圧力などを比較(Table 2)。
- 熱管理: 炉内の金属湯温(Table 3)や金型温度の違いがプロセスに与える影響を分析。
- 鋳造システム: スリーブ内の空気混入(Figure 7, 8)、酸化物の生成、潤滑剤の影響など、鋳造品質に直接関わる要因を評価。
- 金型設計: 金型寿命、ゲート設計(Figure 9)、エアベントの要件など、金型に関する考慮事項を比較。
- 製品特性: 最小肉厚、強度と伸び、ガス気孔、表面硬度など、最終製品の品質に与える影響を分析。
この多角的なアプローチにより、両プロセスの技術的なトレードオフが明確に示されています。
発見:主要な結果とデータ
本論文は、両プロセスの優位性と劣位性を具体的なデータと共に明らかにしています。
発見1:プロセス能力と機械サイズ
Table 2が示すように、ホットチャンバーは低い鋳造圧力(160-250 bar)で済むため、より小さなロック力(最大10000 kN)の機械で対応可能です。一方、コールドチャンバーは高い圧力(400-1400 bar)を必要とし、より大きな機械(最大40000 kN)が求められます。これにより、ホットチャンバーの方がサイクルタイムが短く(10秒から)、生産性が高いことが示唆されます。発見2:鋳造品質と空気混入
コールドチャンバープロセスでは、スリーブが平均50%(最大でも2/3)しか充填されないため、大量の空気が金型内に巻き込まれます(Figure 8)。対照的に、ホットチャンバーではスリーブが常に100%充填されているため、空気の混入が大幅に少なく、ガス気孔の少ない高品質な鋳物が得られます(Figure 7)。発見3:薄肉鋳造の可能性
ホットチャンバープロセスは、より薄い肉厚の鋳造を可能にします。論文では、FisherCast社の事例として、0.5mmという極薄肉厚の鋳造が可能であることが示されています。これは、ホットチャンバーの優れた湯流れ性と低い凝固速度によるものです。発見4:合金と温度管理
ホットチャンバープロセスは、鋳造ユニット(グースネック、プランジャー等)が溶湯に浸漬しているため、使用できる合金と湯温に制限があります。Table 3によると、湯温が650°Cを超えると部品のリークが増加するため、AZ91 HPやAM60 HPといった合金が推奨されます。一方、コールドチャンバーはより高い湯温(例:AM50 HPで680°C)に対応できます。発見5:金型設計への影響
ホットチャンバーは、中央からのゲート設定(セントラルゲーティング)が可能であり、溶湯を内側から外側へ充填することで高品質な鋳造を実現します(Figure 9)。一方、コールドチャンバーは凝固が速いため、より短い充填時間と、それに伴いより厚いゲートと広いゲート面積が必要となります。
あなたのHPDC業務への実践的示唆
この研究結果は、現場の製造プロセスを改善するための具体的なヒントを提供します。
プロセスエンジニアへ: 論文のConclusionで述べられているように、1.2mm未満の薄肉部品を製造する場合、ホットチャンバープロセスを選択することで、経済性と品質の両方を向上させられる可能性があります。サイクルタイムの短縮と不良率の低減が期待できます。
品質管理担当者へ: Figure 8で示されているように、コールドチャンバープロセスは本質的に空気の巻き込みが多いです。したがって、コールドチャンバーで製造された部品については、ガス気孔に関連する品質検査(X線検査など)をより重点的に行うことが賢明です。
金型設計者へ: この研究は、プロセス選択が金型設計に直接影響することを示唆しています。ホットチャンバーを選択する場合、Figure 9にあるようなセントラルゲート方式を採用することで充填性を最適化できます。また、ホットチャンバーの穏やかな鋳造条件は、金型の熱的・機械的ストレスを低減し、金型寿命の延長に貢献する可能性があります(Die Casting Die, 1. Life of dieの項より)。
論文詳細
[論文タイトル]
1. 概要:
- タイトル: Properties of Diecasting Alloys and a Comparison of Hot and Cold Chamber Processes for Magnesium Die Casting
- 著者: Dr. Ing Norbert Erhard, Bob Tracy
- 発行年: (論文に記載なし)
- ジャーナル/学会: (論文に記載なし、FRECH社内資料)
- キーワード: Magnesium, Diecasting, Hot Chamber, Cold Chamber, Zinc, Aluminium
2. 要旨:
本論文は、ダイカストで一般的に使用される亜鉛、アルミニウム、マグネシウム合金の物理的・機械的特性を概観し、特にマグネシウムダイカストにおけるホットチャンバープロセスとコールドチャンバープロセスの包括的な比較を行う。両プロセスの長所と短所を、機械サイズ、サイクルタイム、鋳造パラメータ、金型設計、最終製品の品質など、さまざまな観点から分析する。結論として、薄肉部品にはホットチャンバーが、厚肉で高い機械的特性が要求される部品にはコールドチャンバーが適していることを示し、ダイカストメーカーが用途に応じて最適なプロセスを選択するための指針を提供する。
3. 序論:
亜鉛(Zn)、アルミニウム(Al)、マグネシウム(Mg)合金の世界的な消費量は近年増加している。特にAlとMgの軽金属鋳物の70%は自動車産業で使用されている。AlはMgより約50%重く、ZnはMgの約4倍重い。しかし、特定の機械的特性が求められる用途では、それぞれの材料が好まれる。本稿では、これらの合金の特性を比較し、マグネシウムダイカストにおけるホットチャンバーとコールドチャンバーのプロセスを詳細に比較検討する。
4. 研究の要約:
研究トピックの背景:
軽量化の要求が高まる自動車産業やエレクトロニクス産業において、マグネシウムは非常に重要な材料となっている。その製造方法であるダイカストには、主にホットチャンバーとコールドチャンバーの2つのプロセスがあり、それぞれが異なる特性を持つため、適切なプロセス選択が製品の品質とコストを左右する。
従来の研究状況:
従来、各プロセスは個別に議論されることが多かったが、本稿のように機械、プロセス、金型、製品品質といった多角的な視点から両者を直接比較する包括的な分析は、現場の技術者にとって非常に有益である。
研究の目的:
マグネシウムダイカストにおいて、ホットチャンバープロセスとコールドチャンバープロセスのどちらがどのような条件下で優れているかを明確にすること。これにより、ダイカストメーカーが製品の要求仕様に基づいて最適な製造プロセスを選択できるよう支援することを目的とする。
研究の核心:
研究の核心は、両プロセスの直接比較にある。鋳造圧力、サイクルタイム、湯温管理、空気混入、金型への影響、そして最終製品の特性(肉厚、気孔、強度)といった具体的な技術項目を比較し、それぞれのプロセスの適用範囲と限界を明らかにしている。
5. 研究方法
研究デザイン:
本研究は、特定の実験計画に基づくものではなく、FRECH社が持つ長年の経験、実世界の操業データ、および顧客事例(例:Foehl社、Honsel社、Fishercast社)に基づいた比較分析である。
データ収集と分析方法:
データは、実際の機械仕様(Table 2)、合金メーカーの推奨する湯温(Table 3)、および理論的なプロセスモデル(Figure 7, 8, 9)から収集されている。これらのデータを基に、両プロセスの定性的および定量的な比較分析が行われている。
研究トピックと範囲:
研究はマグネシウムダイカストに焦点を当て、ホットチャンバープロセスとコールドチャンバープロセスを比較する。比較項目は、機械、プロセスパラメータ、鋳造品質、金型、製品特性に及ぶ。
6. 主要な結果:
主要な結果:
- ホットチャンバーは低圧・高速サイクルで、薄肉品の生産性に優れる。
- コールドチャンバーは高圧で、厚肉品や高い機械的強度が求められる部品に適している。
- ホットチャンバーは空気の巻き込みが少なく、ガス気孔の少ない高品質な鋳物を生産できる。
- コールドチャンバーはスリーブ内の空気混入が多く、酸化物や潤滑剤による汚染のリスクがある。
- ホットチャンバーは湯温に制限があり(約650°C)、使用できるマグネシウム合金が限られる。
- ホットチャンバーは金型への熱的・機械的負荷が少なく、金型寿命に有利である。
図の名称リスト:
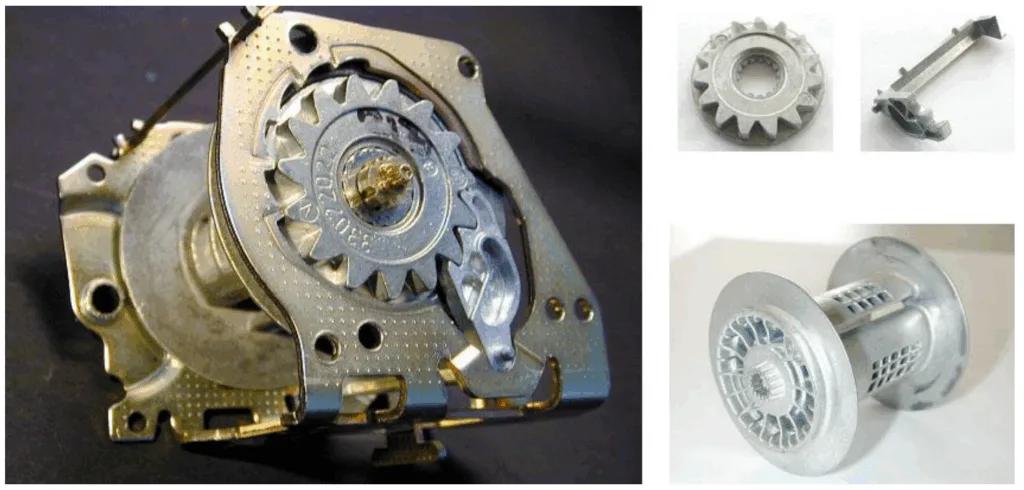
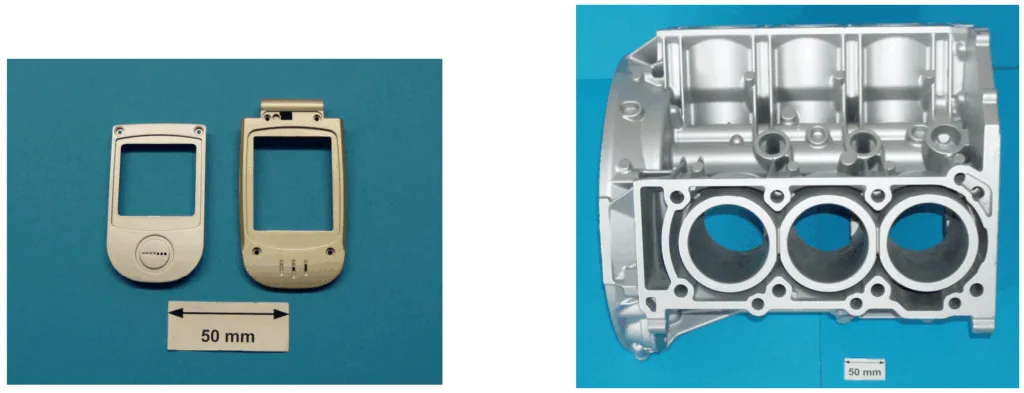
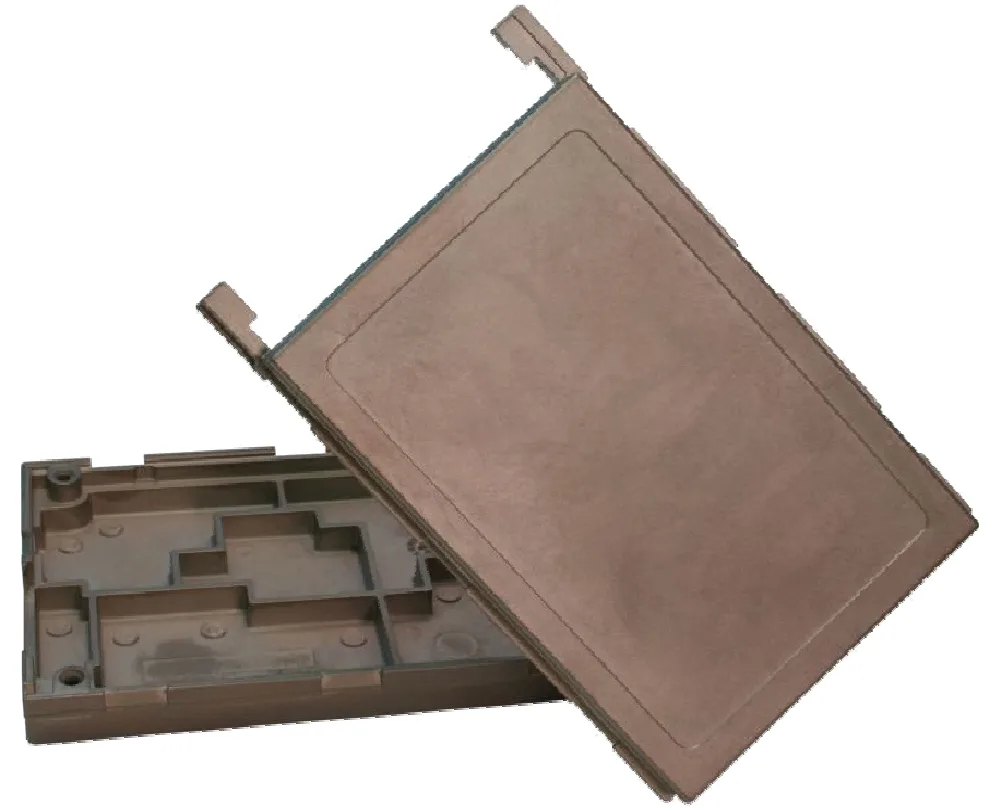
- Figure 1 - Casting „Belt-taut“ (Zinc) (source: Foehl, Germany)
- Figure 2 - Supporting Frame with wall thickness up to 0.6mm (project Fohl, Germany)
- Figure 3 - Belt roll (Zinc) (source: Foehl, Germany)
- Figure 4 - Mobile phone (Mg)
- Figure 5 - Zylinder crank housing (Al) (source: Honsel, Germany)
- Figure 6 - Electronic Device (Mg), Fishercast, CANADA
- Figure 7 - Ventilation of die in hot chamber process
- Figure 8 - Ventilation of die in cold chamber process
- Figure 9 - Gating for the hot chamber process
- Figures 9 - Gating for the cold chamber processes
7. 結論:
提示された結果と経験値は、薄肉部品(1.2 mm未満)はホットチャンバーマシンで鋳造する方が良いことを示している。これはより経済的で、鋳物の品質も高い。厚肉部品で明確な機械的特性が要求される場合や、気孔の少ない鋳造品質が求められる場合は、コールドチャンバーマシンで鋳造する方が良い。ホットチャンバーとコールドチャンバープロセスの比較は、ダイカストメーカーが要求される鋳造特性に応じて適切なプロセスを選択するのに役立つはずである。
8. 参考文献:
(本論文には参考文献リストの記載はありません。)
結論と次のステップ
この研究は、HPDCにおける品質と生産性を向上させるための貴重なロードマップを提供します。その発見は、品質改善、欠陥削減、そして生産最適化に向けた、データに基づいた明確な道筋を示しています。
株式会社CASTMANでは、最新の業界研究を応用し、お客様の最も困難なダイカストの課題を解決することに専念しています。もしこの論文で議論された課題が、貴社の事業目標と共鳴するようでしたら、ぜひ当社の技術チームにご連絡ください。これらの先進的な原理を貴社のコンポーネントにどのように実装できるか、ご相談させていただきます。
専門家Q&A:あなたの疑問に答えます
(注:回答は論文内の特定の出典を引用しなければなりません。例:「[論文名]、結論部より」または「図4に示されるように」)
Q1: この研究で特定された、鋳造品質を向上させるための最も重要な要素は何ですか?
A1: この研究では、鋳造品質、特にガス気孔の観点から、スリーブ内の空気の量をコントロールすることが最も重要であると示唆しています。これは、ホットチャンバープロセス(スリーブ充填率100%)とコールドチャンバープロセス(最大充填率2/3)の比較(Air Ventsの項)およびFigure 7とFigure 8の図解から明らかです。
Q2: 薄肉部品の鋳造において、なぜホットチャンバーが有利なのですか?
A2: 論文のParts Properties, 1. Minimum wall-thicknessの項によると、ホットチャンバープロセスはより薄い壁を鋳造することが可能です。これは、溶湯がノズルまで加熱されており、湯流れ性が良く、低い鋳造圧力で穏やかに充填できるためです。結論部では、1.2mm未満の薄肉品にはホットチャンバーが推奨されています。
Q3: この研究結果はすべての合金に適用できますか、それとも特定の合金に限定されますか?
A3: この研究は主にマグネシウム合金に焦点を当てています。さらに、Parts Properties, 8. Magnesium alloyの項で述べられているように、ホットチャンバープロセスは湯温が650°Cを超えるとリークの問題が発生するため、AZ91やAM60といった特定の合金が推奨されます。したがって、結果はすべての合金に普遍的に適用できるわけではありません。
Q4: プロセス選択は金型寿命にどのような影響を与えますか?
A4: 論文のDie Casting Die, 1. Life of dieの項によると、「ホットチャンバープロセスの有益な鋳造パラメータは、金型に熱的および機械的なストレスを与えない」と述べられています。これは、コールドチャンバーの高圧で急激な充填に比べ、ホットチャンバーの穏やかなプロセスが金型寿命の延長に貢献することを示唆しています。
Q5: コールドチャンバーで高い機械的特性が得られるのはなぜですか?
A5: 論文では、コールドチャンバーの方が高い機械的特性が得られると直接的に述べている箇所は限定的ですが、Parts Properties, 2. Strength and elongationの項で「肉厚が2mmを超える部品では、コールドチャンバープロセスでより高い強度と伸びの値が達成できる」とされています。これは、より高い鋳造圧力(400-1400 bar)による高い緻密化効果に起因すると考えられます。
Q6: この論文からダイカスト工場が得られる、直接的で実用的な教訓は何ですか?
A6: 論文「Properties of Diecasting Alloys and a Comparison of Hot and Cold Chamber Processes for Magnesium Die Casting」からの最も直接的な教訓は、製品の要求仕様(特に肉厚)に基づいてプロセスを戦略的に選択することの重要性です。Conclusionで明確に述べられているように、薄肉品にはホットチャンバーを、厚肉・高強度品にはコールドチャンバーを選択することで、品質と経済性の最適なバランスを達成できます。
著作権
- 本資料は、Dr. Ing Norbert Erhard氏およびBob Tracy氏による論文「Properties of Diecasting Alloys and a Comparison of Hot and Cold Chamber Processes for Magnesium Die Casting」を分析したものです。
- 論文の出典: FRECH
- 本資料は情報提供のみを目的としています。無断での商業利用は禁じられています。
- Copyright © 2025 CASTMAN. All rights reserved.