高整合性ダイカストにおけるプロセス・金型設計:アルミニウム・マグネシウム合金の鋳造欠陥を克服する
本テクニカルブリーフは、Varun Nandakumar氏が2014年にオハイオ州立大学大学院に提出した修士論文「Process and Tool Design for the High Integrity Die Casting of Aluminum and Magnesium Alloys」に基づいています。ハイプレッシャーダイカスト(HPDC)の専門家のために、CASTMANのエキスパートが要約・分析しました。

キーワード
- 主要キーワード: 高整合性ダイカスト
- 副次キーワード: 真空ダイカスト, アルミニウム合金, マグネシウム合金, 鋳造欠陥対策, チルブロック, 溶湯品質, ロータリー脱ガス
エグゼクティブサマリー
- 課題: 従来のハイプレッシャーダイカスト(HPDC)では、ガス巻き込みや溶存水素に起因する内部鋳巣が避けられず、自動車の構造部品のような高い信頼性が求められる用途への適用が困難でした。
- 手法: 本研究では、この課題を克服するため、2つのアプローチを統合しました。1) ロータリー脱ガス装置による溶湯品質の向上(水素除去)、2) 真空アシストシステムと独自設計のチルブロックを用いた金型内からの空気排気。
- 重要なブレークスルー: シミュレーション(MAGMA, ANSYS)と実験計画法(DOE)を駆使し、真空引き用のチルブロックをゼロから設計・検証する体系的なプロセスを確立。これにより、勘や試行錯誤に頼らない、データに基づいた金型設計が可能になりました。
- 結論: 適切な溶湯処理と、科学的に設計された真空アシストシステムを組み合わせることで、従来のHPDCプロセスをアップグレードし、熱処理可能で高品質な構造用部品の製造が実現可能であることを示しました。
課題:なぜこの研究がHPDC専門家にとって重要なのか
自動車業界では、燃費向上と排出ガス規制の強化という大きな流れの中で、車体の軽量化が最重要課題の一つとなっています。このため、従来の鉄鋼部品をアルミニウムやマグネシウムといった軽量合金に置き換える動きが加速しています。しかし、これらの軽量合金を構造部品に適用する際、製造プロセスが大きな壁となります。
特に、高い生産性を誇るHPDCは、そのプロセス特性上、溶融金属が高速で金型キャビティに射出されるため、空気の巻き込みや、アルミニウム溶湯に溶け込んだ水素ガスに起因する鋳巣(ポロシティ)の発生が避けられませんでした(Figure 11)。これらの内部欠陥は、部品の機械的特性(特に伸び)を著しく低下させ、熱処理時に「膨れ」を引き起こす原因となるため、HPDC製の部品はこれまで、高い強度や延性が求められる安全・構造部品への採用が見送られてきました。
本研究は、この根本的な課題に正面から取り組み、「どうすれば従来のHPDCプロセスで、構造部品に求められる高い品質(高整合性)を達成できるか」という問いに答えることを目指しています。
アプローチ:研究手法の解明
本研究では、高整合性鋳造を実現するために、鋳巣の2大要因である「溶存水素」と「巻き込み空気」をそれぞれターゲットとした、包括的なアプローチを採用しました。
溶湯品質の改善(水素除去):
アルミニウム溶湯中の溶存水素を除去するため、PYROTEK®製のロータリー脱ガス装置(Figure 29)を導入。パージガスとしてアルゴンを使用し、最適な脱ガス処理時間や条件を実験的に検証しました。その効果は、減圧凝固試験(RPT、Figure 31)とアルキメデス法による密度測定によって定量的に評価されました。真空アシスト用金型設計(空気除去):
金型キャビティ内の空気を射出前に排気するため、真空アシストシステムを導入することを決定。特に、メンテナンス性とコストの観点から、可動部品のない「チルブロック(バルブレスシステム)」方式(Figure 25)を採用しました。チルブロックの最適な形状(ギャップ、材質、熱伝達係数)を決定するため、以下の体系的な設計プロセスを実行しました。- MAGMAによる流動解析: 鋳造方案の出口における溶湯の温度と速度を算出。
- 実験計画法(DOE)とANSYSによる熱解析: チルブロックの材質(H13鋼 vs. 銅)、ギャップ(0.02インチ vs. 0.04インチ)、熱伝達係数をパラメータとし、溶湯がチルブロック内で凝固するまでの時間をシミュレーション。これにより、最も効果的な設計を科学的に特定しました。
- 3D CAD設計と製作: 最適化された結果に基づき、最終的なチルブロックを設計し、実物を製作しました(Figure 44)。
ブレークスルー:主要な研究結果とデータ
本研究により、高整合性ダイカスト部品の製造に向けた、具体的かつ実践的な知見が得られました。
発見1:最適な脱ガス処理による品質向上
A380合金を用いた実験では、10~15分間のロータリー脱ガス処理を行うことで、溶湯の水素レベルを大幅に低減できることが確認されました。これにより製造された試験片は、熱処理(485℃で3時間)後も「膨れ」が一切発生せず(Figure 34)、高整合性部品に不可欠な熱処理耐性を有することが実証されました。発見2:チルブロック設計における重要因子の特定
実験計画法(DOE)とシミュレーションの結果、チルブロックの性能(溶湯を素早く凝固させる能力)に最も影響を与えるのは「材質」と「ギャップの寸法」であることが明らかになりました。予想に反し、特定の条件下では熱伝達係数(HTC)の影響は比較的小さいという、興味深い結果も得られました(Table 6, Figure 43)。発見3:銅製チルブロックの優位性
熱伝導率の高い銅をチルブロックの材質として使用することで、金型材料であるH13鋼に比べて、溶湯の凝固時間を大幅に短縮できることがデータで示されました。また、ギャップは狭いほど凝固が速く、真空を遮断する効果が高いことが確認されました。最終的に、製造の容易さと性能のバランスから「銅製、ギャップ0.03インチ」が最適設計として選定されました。
HPDC製品への実践的な示唆
本研究の成果は、理論に留まらず、実際の製造現場に直接応用できる多くのヒントを提供します。
プロセスエンジニア向け:
本研究(Chapter 3)は、ロータリー脱ガスを導入し、その運転パラメータ(処理時間、ガス流量など)を最適化することで、溶湯品質を安定的に管理し、後工程の熱処理を可能にするための具体的な指針を示しています。これにより、付加価値の高い製品の製造が可能になります。品質管理担当者向け:
減圧凝固試験(RPT)と密度測定を組み合わせる方法は、製造現場で溶湯のガス量を迅速かつ定量的に評価するための有効なツールとなります。Figure 33に示されるように、これらの測定値を時系列で追跡することで、脱ガスプロセスの有効性をリアルタイムで監視し、品質の安定化に貢献できます。金型設計者向け:
本論文(Chapter 4)で詳述されている「シミュレーションと実験計画法(DOE)を統合したチルブロックの設計手法」は、真空ダイカスト用金型の開発プロセスを大幅に効率化する可能性を秘めています。これにより、試作と修正の繰り返しを減らし、開発期間の短縮とコスト削減が期待できます。
論文詳細
Process and Tool Design for the High Integrity Die Casting of Aluminum and Magnesium Alloys
1. 概要:
- 論文名: Process and Tool Design for the High Integrity Die Casting of Aluminum and Magnesium Alloys
- 著者: Varun Nandakumar
- 発表年: 2014
- 発表機関: The Ohio State University
- キーワード: High Integrity Die Casting, Aluminum Alloys, Magnesium Alloys, Porosity, Vacuum Die Casting, Melt Quality, Degassing, Chill Block
2. 要旨:
現代の自動車における高効率化と低排出ガス化の要求は、従来の鉄鋼部品をアルミニウムやマグネシウムのような軽合金に置き換える大きな需要を生み出しています。これらの多くは構造的な荷重を受ける部品です。通常、これは従来のハイプレッシャーダイカスト(HPDC)のようなプロセスが、固有の空気および水素巻き込み問題のために参入できないことを意味していました。しかし、従来プロセスの品質管理を全体的に向上させることで、構造用途に使用可能な高整合性部品を製造することが可能です。本論文では、アルミニウムおよびマグネシウム合金用の高整合性鋳造品を製造可能にするために、従来のHPDCプロセスを改善するいくつかの手法を記述し、テストします。高品質な溶湯を得るための手法が研究され、ロータリー脱ガス装置が同様のアルミニウム合金の2つの実験試行に使用されます。同様に、既存の設備に真空を統合する手法が研究され、チルブロックを備えた真空アシストシステムの金型部分が完全に設計されます。チルブロックの設計は、統合システム工学研究室で利用可能なMAGMAおよびANSYSシミュレーションツールを使用してゼロから行われます。設計パラメータの変更効果を理解するために実験計画が完了します。最後に、最適な設計が3D CADソフトウェアで完成され、その後、自社で製造されます。
3. 緒言:
ハイプレッシャーダイカスト(HPDC)は、溶融金属を精密に加工された鋼鉄の金型に射出し、凝固が完了するまで圧力を維持するプロセスです。このプロセスは「原材料から完成品までの最短距離」と呼ばれてきました。HPDCを他の鋳造プロセスと区別する主な要因は、射出される金属の圧力と速度です(Figure 1)。自動車産業の軽量化への強い要求により、アルミニウムやマグネシウム合金を用いた構造用ダイカスト部品の需要が高まっています。これらの部品は、高い機械的特性(特に伸び)と、熱処理への適合性が求められます。しかし、従来のHPDCプロセスでは、鋳巣の発生が避けられず、これらの要求を満たすことが困難でした。本研究の目的は、既存のHPDC設備に、溶湯品質管理技術と真空アシスト技術を導入し、高整合性ダイカスト部品を製造するためのプロセスと金型を設計することです。
4. 研究の概要:
研究トピックの背景:
HPDCにおける主要な欠陥は鋳巣(ポロシティ)であり、これは主にガス鋳巣(溶存水素、巻き込み空気、潤滑剤の蒸発)と凝固収縮鋳巣に分類されます(Figure 11)。特に、アルミニウムは液体状態では固体状態よりもはるかに多くの水素を溶解するため、凝固時に水素ガスが放出され、鋳巣の原因となります(Figure 12)。また、高速射出はキャビティ内の空気を巻き込み、これも重大な欠陥要因となります。これらの欠陥は、部品を構造用途に用いる際の大きな障害となります。
従来の研究の状況:
鋳巣を低減する技術として、スクイズキャスティング、半溶融鋳造、そして真空ダイカストなどの高整合性プロセスが存在します。真空ダイカストは、金型キャビティ内のガスを排気することで鋳巣を大幅に削減する技術であり、その実現方法には、真空バルブを用いる方法と、チルブロックのようなバルブレスシステムを用いる方法があります。また、溶湯品質の改善策として、ロータリーインペラによる脱ガスが最も効率的な手法の一つとして知られています(Figure 15)。
研究の目的:
本研究の目的は、オハイオ州立大学のダイカスト研究室にある既存のHPDC設備を、高整合性部品の製造が可能なセルにアップグレードすることです。具体的には、以下の2点を達成します。
1. 溶湯中の水素鋳巣を低減するためのシステムを理解し、開発する。
2. 金型キャビティ内に低レベルの真空を生成・維持できる真空対応金型を設計する。
研究の核心:
本研究の核心は、2つの主要技術を体系的に統合し、その設計プロセスをデータに基づいて検証した点にあります。
1. 溶湯品質管理: ロータリー脱ガス装置を導入し、実際の鋳造キャンペーンを通じて最適な運転条件(脱ガス時間、ガス流量など)を特定しました。
2. 真空用金型設計: 市販品に頼らず、チルブロックをゼロから設計。MAGMAとANSYSを用いたシミュレーションと実験計画法(DOE)を組み合わせることで、チルブロックの形状、材質、ギャップなどの重要パラメータを科学的に最適化し、その設計プロセス全体を確立しました。
5. 研究方法
研究デザイン:
本研究は、実験的アプローチとシミュレーションベースの設計アプローチを組み合わせています。
- 溶湯品質改善: 2種類のアルミニウム合金(A380および企業独自の合金B)を用いて、ロータリー脱ガス装置の効果を検証する観察研究を実施。
- 真空用金型設計: 既存の金型寸法を調査し、設計制約を特定。その後、チルブロックの概念設計、シミュレーションによる性能評価、実験計画法(DOE)によるパラメータ最適化、最終的なCAD設計と製作という一連の設計プロセスを実行。
データ収集と分析方法:
- 溶湯のガスレベルは、減圧凝固試験(RPT)による定性的評価と、アルキメデス法による密度測定という定量的評価の両方で収集されました。
- チルブロックの性能評価は、MAGMAによる流動解析で得られた境界条件(溶湯温度、速度)を用い、ANSYSによる2次元熱伝達過渡解析によって行われました。
- DOEの結果は、分散分析(ANOVA)を用いて統計的に分析され、各設計因子(材質、ギャップ、HTC)の有意性が評価されました。
研究のトピックと範囲:
本研究は、HPDCにおける高整合性鋳造の実現に焦点を当て、特に「溶湯品質の改善」と「真空アシストシステムのツール設計」という2つのトピックを深く掘り下げています。溶湯品質改善はアルミニウム合金を対象とし、真空用金型設計はマグネシウム合金(AZ91)の物性値を用いたシミュレーションに基づいています。
6. 主要な結果:
主要な結果:
- ロータリー脱ガスを10~15分間行うことで、溶湯密度が大幅に向上し(Figure 33)、熱処理可能なレベルまでガス含有量を低減できることが実証されました。
- チルブロックの設計に関する実験計画法(DOE)の結果、凝固時間に最も大きな影響を与える因子は「材質(銅 > H13鋼)」と「ギャップの寸法(狭い方が速い)」であることが統計的に示されました(Table 6)。
- 熱伝達係数(HTC)は、本研究で評価した範囲と形状においては、凝固時間に対する影響が統計的に有意ではないという、非自明な結果が得られました(Figure 43)。
- これらの結果に基づき、銅を材質とし、ギャップを0.030インチとする最適なチルブロックの設計が決定され、3D CADモデル(Figure 44)が作成され、実物が製作されました。
図の名称リスト:
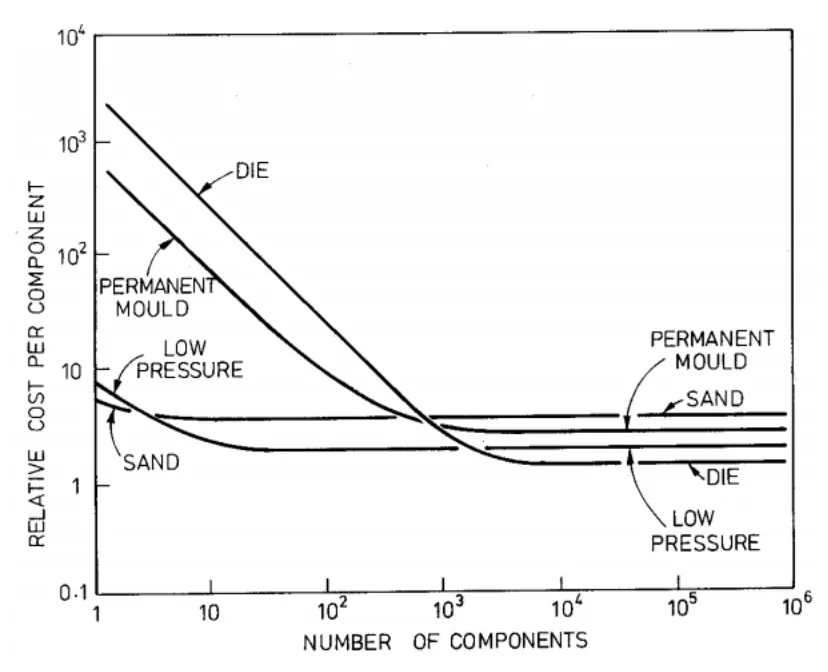
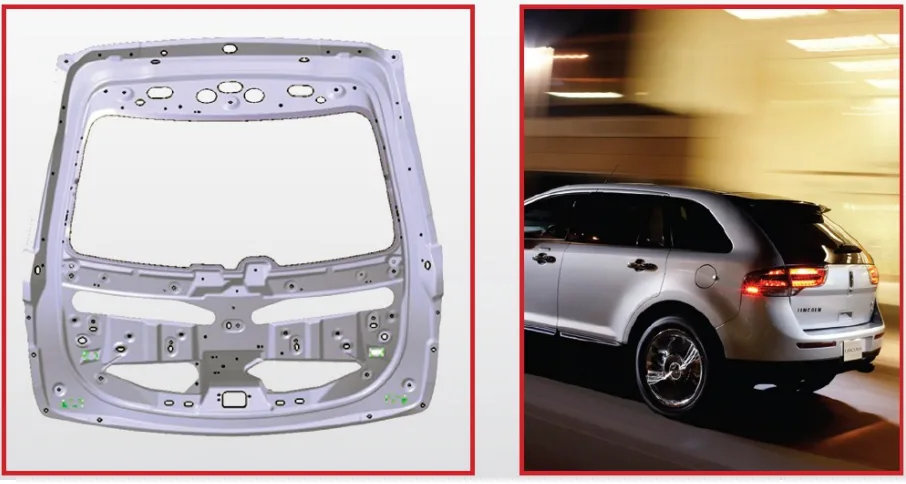
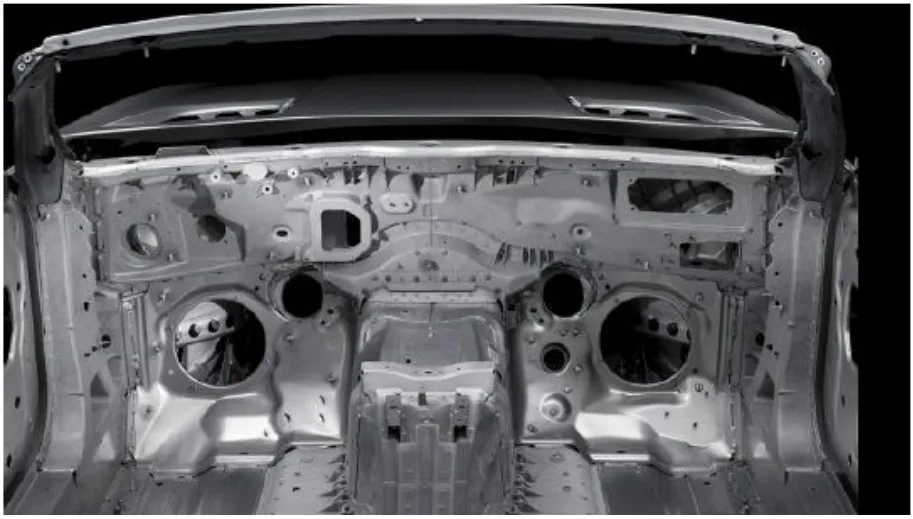
- Figure 1. Relationship of various casting processes to pressure and velocity
- Figure 2. Steps in a HPDC process
- Figure 3, Advantages of High Pressure Die Casting
- Figure 4. Cold Chamber Process
- Figure 5. The Hot Chamber Process
- Figure 6, Graph howing the relative cost of a component manufactured by different casting processes
- Figure 7, Magnesium Lincoln MKT lift gate
- Figure 8, Upper Fire wall
- Figure 9, Audi Space frame, Showing Structural Die Castings in Red
- Figure 10, Fe rich needle like phase that causes low elongation and flow capabilities
- Figure 11, Major sources of defects in a HPDC product
- Figure 12, Solubility of Hydrogen drops drastically as the aluminum solidifies, not so much a problem with Magnesium
- Figure 13, Protection of the surface of the melt by the addition of liquid Argon
- Figure 14, Surface protection by delivery of argon gas parallel to the surface of the melt
- Figure 15, Efficiencies of three different techniques to degassing
- Figure 16, Coupling flux injection with rotor degassing
- Figure 17, For a given size of a bubble, (a) larger oxides are easily floated out while (b) smaller ones follow the streamlines of the rising bubble and so do not collect the bubble
- Figure 18 Vss- Critial Slow Shot Velocities
- Figure 19, Illustration showing Atomized flow that is typical in a conventional HPDC
- Figure 20, Left - Close to eutectic with a small mushy zone, Right - bigger mushy zone
- Figure 21 Conventional Vacuum Die Casting Process
- Figure 22, Difference time in vacuum application for Vacural vs. others
- Figure 23, Vacuural Process schematic
- Figure 24, Residual gas content a seen on X-ray
- Figure 25, Valve and Valve less technology for creating vacuum inside the die cavity
- Figure 26, Erroneous Cavity vacuum reading in case of chill blocks
- Figure 27, Comparison between Chill Blocks and Valves
- Figure 28, 250 T Cold Chamber die casting Machine at OSU
- Figure 29, PYROTEK® STAR 300® Rotary Degasser
- Figure 30, Specially designed mounts on the furnace to receive the Rotary degasser
- Figure 31, Palmers® Reduced Pressure Tester
- Figure 33, Density measurement after degassing, yellow points indicate that degassing was done
- Figure 34, Four Heat treated samples and one as cast on the extreme right, no blistering observed
- Figure 35, Ejector and cover die with inserts
- Figure 36, Available design space on the cover die half was 4X2X.5 in
- Figure 37, Outer envelope of chill block and initial concept design
- Figure 38, ISO view and section view of entire chill block assembly showing internal trapezoidal passages and required area for venting into vacuum tank
- Figure 39, Initial geometry for chill profile with a cut away (.52X.40in) for consistent vent area
- Figure 40, MAGMA simulation Parameters
- Figure 41, Temperature and Flow lengths at an arbitrary 84% fill, Stars showing location of control points
- Figure 42, Boundary Conditions (BC1 and BC2) & Thermal loads for the 2D Model
- Figure 43, Main effect plots for the factors
- Figure 44, Chill Block design process
- Figure 45, CAD model section view showing the vent passage in the ejector die and hole on the cover die
- Figure 46, Ejector die vent cutout area
- Figure 47, Design criteria for Sealant; to determine optimal sealing.
- Figure 48, Sealant Path on the cover die
7. 結論:
本研究は、アルミニウムおよびマグネシウムを用いた高整合性鋳造品を製造するための全体的なフレームワークを構築することを試みました。溶湯品質の維持と真空ダイカストという2つの主要なトピックがカバーされました。ロータリー脱ガス装置、減圧凝固試験機、アルキメデス法密度測定装置がすべて使用され、最良の実践方法と学習が記録されました。
真空アシストとチルブロックによる排気という手法が、制約条件を考慮した上で最良の選択であると決定されました。チルブロックは、MAGMA、ANSYSでのシミュレーションとSOLIDWORKSでの設計を用いてゼロから設計されました。ギャップ厚、材質、熱伝達係数という3つの因子の影響を理解するために、2³の実験計画が実施されました。分散分析(ANOVA)の結果、HTCの影響はほとんどなく、銅とより小さなギャップが最良の凝固時間をもたらすことが明らかになりました。この演習は、チルブロックの設計を検証するのに役立ちました。チルブロックはその後製造され、金型も機械加工の過程にあります。
8. 参考文献:
- [List of references from the paper is omitted for brevity but is available in the original document.]
専門家Q&A:あなたの疑問に答えます
Q1: この研究で、高整合性鋳造の品質を向上させるために最も重要だと特定された単一の要因は何ですか?
A1: 本研究では、単一の要因ではなく、2つの重要な技術領域の統合が重要であると結論付けています。1つはロータリー脱ガスによる「溶湯品質の向上(水素除去)」、もう1つは真空アシストシステムによる「金型キャビティからの空気除去」です。チルブロック自体の設計においては、「材質(銅)」と「ギャップの寸法」が最も影響力のある要因であると特定されました。これは「Chapter 4」の結論部分で詳述され、Table 6のデータで裏付けられています。
Q2: この研究は、鋳巣問題に対処する従来の方法とどう比較されますか?
A2: 論文の「Chapter 1」で述べられているように、従来のHPDCではある程度の鋳巣の存在が許容され、それが熱処理や構造用途への適用を妨げていました。本研究は、脱ガスによる「溶湯の前処理」と真空引きによる「鋳造環境の制御」という、より積極的なアプローチを導入し、これらの限界を克服する道筋を示した点で異なります。
Q3: この研究結果は、すべての合金に適用可能ですか、それとも特定の合金に限定されますか?
A3: 「Chapter 3」で記述されているように、溶湯品質の実験はアルミニウム合金A380およびそれに類似した合金で行われました。一方、「Chapter 4」の真空用金型のシミュレーションは、マグネシウム合金AZ91の物性値を用いて行われています。したがって、研究は特定の合金に基づいていますが、その背後にある物理的原則(脱ガスの原理や熱伝導による凝固制御)は、他の多くのアルミニウム・マグネシウム合金にも広く応用可能と考えられます。
Q4: 研究者たちは、この結論に至るために具体的にどのような測定・シミュレーション技術を使用しましたか?
A4: 研究者たちは、「Chapter 3」および「Chapter 4」で説明されているように、複数の技術を組み合わせて使用しました。溶湯品質の評価には「ロータリー脱ガス装置」と「減圧凝固試験(RPT)」を、チルブロックの設計と検証には「MAGMAによる流動解析」と「ANSYSによる熱伝達過渡解析」を活用しました。
Q5: 論文によると、主な限界や今後の研究課題は何ですか?
A5: 著者は「Chapter 5, Future Work」セクションで、今後の課題を明確に述べています。主な課題として、真空システムの残りの部分(トラップ、制御システム)の製作、真空の有無による効果を比較するための鋳造試験の実施、そしてANSYSによる近似計算をMAGMAを用いて検証することなどを挙げています。
Q6: この論文から、ダイカスト工場が直接得られる実践的な教訓は何ですか?
A6: 最も重要な教訓は、体系的なアプローチにより、既存の設備でも高整合性部品の製造能力を獲得できるということです。具体的には、「溶湯のロータリー脱ガス」と「シミュレーションで最適化したカスタム設計のチルブロックを用いた真空アシスト」という2つの技術を導入することで、品質を大幅に向上させることが可能であるという結論が、論文「Process and Tool Design for the High Integrity Die Casting of Aluminum and Magnesium Alloys」の全体的な結果によって強く支持されています。
結論と次のステップ
本研究は、HPDCにおける鋳巣という長年の課題に対し、溶湯品質管理と真空技術を統合するという、データに基づいた明確な解決策を提示しています。その成果は、品質の向上、欠陥の削減、そして生産の最適化に向けた貴重なロードマップとなります。
私たちCASTMANは、最新の業界研究を応用し、お客様の最も困難なダイカストの課題を解決することに専念しています。もし、この論文で議論された課題が貴社の目標と共鳴するものであれば、私たちのエンジニアリングチームにご連絡ください。これらの先進的な原則を貴社の部品にどのように実装できるか、共に検討させていただきます。
著作権
- 本資料は、"Varun Nandakumar"氏の論文"Process and Tool Design for the High Integrity Die Casting of Aluminum and Magnesium Alloys"に基づいています。
- 論文の出典: The Ohio State University (2014)
本資料は情報提供のみを目的としています。無断での商業利用は禁じられています。
Copyright © 2025 CASTMAN. All rights reserved.