この技術概要は、Piyush Shukla氏によって執筆され、International Journal for Multidisciplinary Research (IJFMR)に掲載された学術論文「Process Selection on the Basis of Time Cost and Quality for Development Components of Aluminium Bracket」(2024年)に基づいています。HPDC(ハイプレッシャーダイカスト)の専門家のために、株式会社CASTMANのエキスパートが要約・分析しました。
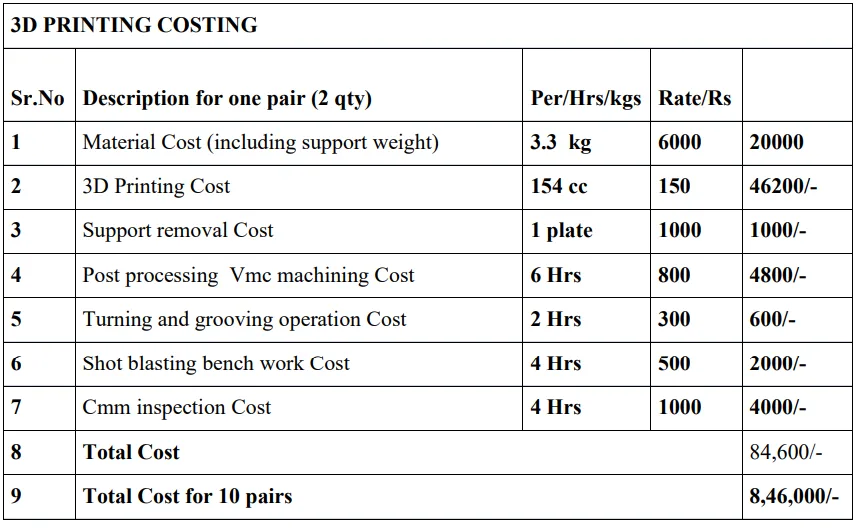
キーワード
- プライマリーキーワード: アルミニウムブラケット プロトタイプ製造
- セカンダリーキーワード: ダイカスト試作, ソフトツール, 3Dプリンティング 金属, VMC加工, コスト比較 製造方法, 品質 時間 コスト
エグゼクティブサマリー
- 課題: 製品開発の初期段階、特に組立性検証やトライアル用のアルミニウム部品を製造する際、どの製造プロセス(3Dプリンティング、切削加工、ダイカスト)を選択すべきかという問題。特に10個以上の試作品が必要な場合に、コスト、時間、品質のバランスを最適化することが困難でした。
- 手法: 本研究では、自動車用オルタネーターブラケットを対象に、3つの異なる製造プロセス(金属3Dプリンティング(DMLS)、VMC(立形マシニングセンタ)による切削加工、ソフトツールを用いたプロトダイカスト(Proto DCD))を実用的に比較。10ペア(20個)の部品を製造し、それぞれの時間、コスト、品質(寸法精度、材料特性)を詳細に評価しました。
- 重要な発見: 1~2個の試作では3Dプリンティングが有効ですが、10個以上の試作品を必要とする場合、ソフトツールを用いたプロトダイカストが、VMC加工や3Dプリンティングと比較して最もコスト効率が高いことが実証されました。時間はVMC加工と同等でありながら、コストは大幅に低減可能です。
- 結論: プロトダイカスト(ソフトツール)は、試作段階から量産への移行をスムーズにするための、非常に有効で経済的な選択肢です。特に、最終的な量産プロセスがダイカストである場合、設計変更のリスクを低減しつつ、開発全体のコストと時間を削減する上で大きな利点があります。
課題:なぜこの研究がHPDC専門家にとって重要なのか
製品開発において、特に量産用の金型を製作する前の段階で、設計の妥当性や組立性を確認するための試作品は不可欠です。しかし、アルミニウム部品のプロトタイプを製造するプロセス選択は、これまで明確な基準がありませんでした(Abstract)。多くのエンジニアは、設計プロセスの最終段階で製造方法を検討しますが、最適なアプローチは設計の初期段階から製造上の懸念を考慮に入れることです。これにより、製造が容易でコスト効率の高い設計が実現します(1.1 DEVELOPMENT PROCESS SELECTION)。
特に、自動車部品のようなコンポーネントでは、フィット感や機能テストのために最低でも10個程度の試作品が必要になるケースが多くあります。この「試運転数量(commissioning quantity)」に対して、従来の3Dプリンティングや切削加工は、コストが高すぎるか、あるいは最終製品の材料特性と乖離するという課題を抱えていました。本研究は、このギャップを埋めるための最適なプロセスを特定することを目的としています。
アプローチ:研究手法の解明
この課題を解決するため、研究者たちはアルミニウム製オルタネーターブラケットを対象に、3つの異なる製造プロセスを実用的に比較検証しました。
- 3Dプリンティング(DMLS): ダイレクトメタルレーザー焼結(DMLS)法を用いて、CADデータから直接部品を積層造形しました(4.2.1 3D PRINTING PROCESS)。
- VMC切削加工: アルミニウムのブロック材から、VMC(立形マシニングセンタ)を用いて部品を削り出しました(4.3.1 MILLING OF PART)。
- プロトダイカスト(Proto DCD): 熱処理や表面コーティングを施さない「ソフト」な状態の金型(ソフトツール)を製作し、ダイカストマシンで部品を鋳造しました。これは、量産金型に比べて低コストかつ短納期で製作できるのが特徴です(4.4.3 PROTO TOOLING DIE CASTING PROCESS)。
これらのプロセスでそれぞれ10ペア(20個)のブラケットを製造し、製造に要した総時間、総コスト、そして完成品の寸法精度(CMM測定)と材料特性(硬度、機械的性質)を詳細に比較分析しました。
重要な発見:主要な結果とデータ
本研究から得られた比較結果は、プロトタイプ製造のプロセス選択において非常に明確な指針を示しています。
発見1:コストの劇的な違い
10ペアの部品を製造するための総コストは、プロトダイカストが375,900 INRと最も低コストでした。一方、VMC加工は398,300 INR、3Dプリンティングは8,500,000 INRと非常に高価であることが明らかになりました。この結果は、10個以上の試作において、3Dプリンティングが経済的に非現実的であることを示しています(Table 2.2, Graph 1.3)。発見2:製造時間の比較
製造に要した時間は、3Dプリンティングが15日と最も短かったものの、プロトダイカストとVMC加工は共に17日であり、実用上大きな差はありませんでした。法外なコストを考慮すると、3Dプリンティングの2日間のリードタイム短縮は、その優位性を正当化できません(Table 2.2, Graph 1.3)。発見3:品質と材料特性の優位性
寸法精度については、3つのプロセスすべてが要求公差内に収まり、実用上の差は見られませんでした(Table 2.0)。しかし、材料特性には顕著な差が現れました。プロトダイカスト品の硬度(97 HB)は、目標範囲(95-100 HB)に完全に合致していました。一方、VMC加工品(Al6061)は81 HBと柔らかすぎ、3Dプリンティング品(AlSi10Mg)は121 HBと硬すぎる結果となりました。これは、プロトダイカストが最終量産品に最も近い材料特性を実現できることを示唆しています(Table 2.1, Table 2.2)。発見4:プロトダイカストの拡張性
本研究で使用されたソフトツールは、5000個の部品製造後でも、硬化処理されたインサートに交換することで、10万ショットの通常ダイカスト金型として使用できる可能性があると指摘されています。これにより、試作から量産への移行が非常にスムーズかつ低コストになる可能性があります(6.2 FUTURE SCOPE)。
HPDC製品への実用的な示唆
この研究結果は、実際の製造現場、特に製品開発の初期段階において、具体的かつ実践的なメリットをもたらします。
プロセスエンジニア向け: 「5.3 Result on time cost and quality」の知見は、10個以上の試作品が必要な場合、VMC加工や3Dプリンティングの代わりにプロトダイカスト(ソフトツール)を選択することで、コストを大幅に削減しつつ、量産品に近い品質を確保できることを示唆しています。
品質管理向け: Table 2.0が示すように、プロトダイカストは要求される寸法精度を十分に満たすことができます。さらにTable 2.1の結果は、最終製品と同じ合金を使用することで、機械的特性の検証を試作段階で正確に行える可能性を示しており、手戻りのリスクを低減します。
金型設計向け: 本研究は、量産用の高価な硬化金型を製作する前に、低コストのソフトツールで試作を行うことの有効性を証明しています。これにより、設計変更(ECR)が発生した場合でも、修正コストと時間を最小限に抑えることができます。ソフトツールで設計を確定させた後、同じ金型をベースに量産用へアップグレードできるため、開発プロセス全体が効率化されます(4.4.3 PROTO TOOLING DIE CASTING PROCESS)。
論文詳細
Process Selection on the Basis of Time Cost and Quality for Development Components of Aluminium Bracket
1. 概要:
- Title: Process Selection on the Basis of Time Cost and Quality for Development Components of Aluminium Bracket
- Author: Piyush Shukla
- Year of publication: 2024
- Journal/academic society of publication: International Journal for Multidisciplinary Research (IJFMR), Volume 6, Issue 4, July-August 2024
- Keywords: Development, Process Selection, Time, Cost, Quality, Aluminium Bracket, Die Casting, 3D printing, VMC machining, Proto DCD
2. Abstract:
様々な新プロセスの開発により、ダイスによる量産前のアルミニウム部品設計におけるツーリング開発が削減されました。アルミニウムのプロト品質を製造するためのプロセス選択は重要ではありません。本研究は、1つまたは2つの数量のプロトタイピングには十分であるため、ソフトコンディションのダイカストダイもアルミニウム部品の試運転数量に推奨されるプロセスであることを証明する試みです。プロトDCDプロセスは、時間、コスト、品質のパラメータとも比較され、この基準に基づいて、最大1000個の数量要件に対してのみプロセスを選択できます。
3. Introduction:
新製品開発において、組立部品の実現可能性や製品組立の試運転を確認するための製造プロセス選択は、一部の機械エンジニアにとって重要な役割を果たします。プロセス選択は、設計プロセス中に彼らが最後に考えることです。最善のアプローチは、設計プロセス全体を通じて製造上の懸念を念頭に置くことです。これにより、より簡単で低コストで生産できる設計が実現します。
製造プロセスは何百もあります。鋳造や機械加工など、最も一般的なものには既におなじみでしょう。
どの製品に対しても、複数の製造プロセスから選択する必要があります。選択するプロセスは、プロセス選択ドライバーと呼ばれる多くの要因に依存します。
4. 研究の要約:
研究トピックの背景:
製品開発、特に自動車部品のようなコンポーネントでは、量産開始前に組立性や機能性を検証するための試作品が不可欠です。この「開発部品」を製造するためのプロセス選択は、プロジェクト全体のコスト、リードタイム、そして最終製品の品質に直接的な影響を与えます。従来、この少量生産には3Dプリンティングや切削加工が用いられてきましたが、コストや材料特性の面で課題がありました。
従来の研究の状況:
文献調査によると、個々の製造プロセスを最適化する研究は多数存在するものの、特にアルミニウムブラケットの試作という特定の目的に対して、3Dプリンティング、VMC加工、そしてソフトツールを用いたプロトダイカストを「時間、コスト、品質」の観点から直接比較した研究はほとんどありませんでした(3.1 RESEARCH GAP)。
研究の目的:
本研究の目的は、以下の2点です(2. OBJECTIVE)。
1. 時間、コスト、品質という選択パラメータに基づき、複数のプロトタイプ数量に対してどの製造プロセスが適しているかを、従来の硬化金型ダイカストと比較して明らかにすること。
2. 試運転から最終的なツーリング済みサンプルまでを、より少ない変更とコストで実現できる単一のプロセスフローを確立すること。
具体的には、最低20個(10ペア)の試作品を必要とするケースに焦点を当てています。
研究の中核:
研究の中核は、アルミニウム製オルタネーターブラケットを対象に、3つの異なる製造プロセス(3Dプリンティング、VMC加工、プロトダイカスト)を実際に適用し、それぞれのパフォーマンスを定量的に比較することです。コストは詳細なBOM(部品表)に基づいて積算され(Table 1.7)、時間は各工程の作業時間を合計して算出(Table 1.2, 1.5, 1.9)、品質はCMMによる寸法測定と材料試験によって評価されました(Table 2.0, 2.1)。
5. 研究方法
研究デザイン:
本研究は、特定のアルミニウム部品(オルタネーターブラケット)を対象とした比較実験研究として設計されています。3つの独立した製造プロセス(3Dプリンティング、VMC加工、プロトダイカスト)を適用し、それぞれの結果(コスト、時間、品質)を比較分析するデザインです。
データ収集と分析方法:
- コスト: 各プロセスの材料費、加工費、工具費、人件費などを詳細に積算し、10ペアの部品を製造するための総コストを算出しました(Table 1.2, 1.4, 1.8)。
- 時間: 設計、準備、製造、後処理、検査の各工程にかかる時間を記録し、総リードタイムを日数で算出しました(Table 1.2, 1.5, 1.9)。
- 品質: 製造されたサンプルの寸法精度を三次元測定機(CMM)で測定し、設計値との差異を評価しました(Table 2.0)。また、材料の化学組成、硬度(ブリネル硬さ)、引張強度、降伏強度、伸びを測定し、材料特性を比較しました(Table 2.1, 5.2 MATERIAL COMPARISION.)。
研究対象と範囲:
- 対象部品: アルミニウム製オルタネーターブラケット(Material: Aluminum, AlSi10Mg, Dimension: According to the drawing or sample)(4.1 COMPONENT SPACIFICATION)。
- 製造数量: 10ペア(20個)。これは、組立ラインでのトライアルや製品テストに必要な最低数量として設定されています(2. OBJECTIVE)。
- 範囲: 研究は、最大1000個までの数量要件に対するプロセス選択に焦点を当てています(Abstract)。
6. 主要な結果:
主要な結果:
本研究の主要な結果は、Table 2.2 Result values.とGraph 1.3 Result chart.に集約されています。
- コスト: 10ペアの製造において、プロトダイカスト(375,900 INR)が最も低コストであり、VMC加工(398,300 INR)が僅差で続き、3Dプリンティング(8,500,000 INR)が圧倒的に高コストでした。
- 時間: 3Dプリンティングが15日と最速でしたが、プロトダイカストとVMC加工は共に17日であり、大きな差はありませんでした。
- 品質: 寸法精度は3プロセスとも公差内で同等でした。材料品質(硬度)では、プロトダイカスト(97 HB)が目標範囲に最も近く、VMC加工(81 HB)は柔らかすぎ、3Dプリンティング(121 HB)は硬すぎる結果となりました。
これらの結果から、10個以上の試作品を製造する場合、プロトダイカストがコストと品質のバランスにおいて最適な選択肢であると結論付けられます。
図表名リスト:
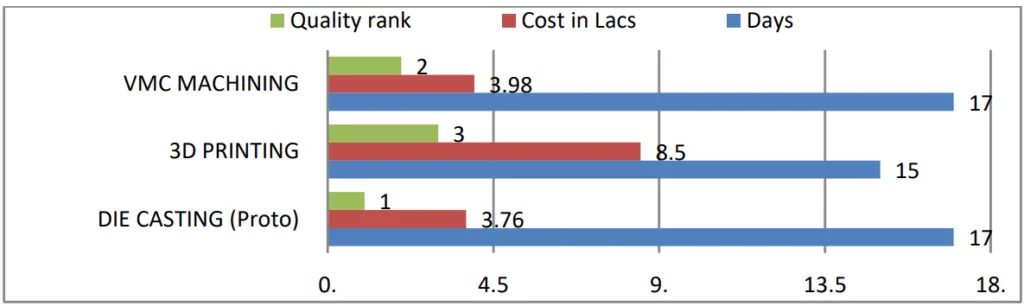
- Table 1.1 component specification
- Table 1.2 3D printing time calculation
- Figure 1.3 part build structure
- Table 1.4 Macining Cost
- Table 1.5 Machining time calculation
- Figure 2.2 Die casting machine
- Table 1.6 feasibility specifications of Die castings
- Table 1.7 Detailed BOM and costing
- Table 1.8 Proto Dcd Costing
- Table 1.9 Proto Dcd time calculations
- Table 2.0 Comparison of Dimensions
- Table 2.1 Comparison of Material properties.
- Table 2.2 Result values.
- Graph 1.3 Result chart.
7. Conclusion:
実験作業は以下の結論につながりました。3Dプリンティングの実装は、プロトタイプでこの実験の目的を果たし、1つまたは2つのコンポーネントに対してのみ、より良い時間節約プロセスという結果をもたらす適切なプロセスでした。しかし、鋳造VMCおよびプロトダイカストと比較すると、3Dプリンティングは非常に高価であることがわかりました。VMC加工プロセスでは、材料組成が必要な材料組成と一致しませんでした。プロトダイカスト(ソフトダイ)で試した場合、10サンプルの工具コストは3つのプロセスすべてよりも低いことがわかりました。量産の最終プロセスもダイカストダイであるため、この実験的研究によって、より多くのコストと時間の節約が報告されました。
8. References:
- International Conference on Mechanical Engineering Research 2011 (ICMER2011) IOP Publishing IOP Conf. Series: Optimization of Process Parameters of CNC
- Characteristic Behaviour of Aluminium Metal Matrix Composites:A Review 2018 Prasanna Nagasai Bellamkondal, Srikanth Sudabathula2Mr. NISHANTH PATEL GM1, Dr. K G SATISH2b © 2020, IRJET | Impact Factor value: 7.34 | ISO 9001:2008 Certified Journal
- https://www.researchgate.net/publication/307446249ThermalFatigueofDie-CastingDiesAn_Overview
- https://www.researchgate.net/publication/257707301 Mechanical Properties of AlSi10Mg Produced by Selective Laser Melting Article in Physics Procedia · December 2012
- Experimental investigation into characterization and machining of Al + SiCp nano-composites using coated carbide tool https://ui.adsabs.harvard.edu/abs/2020MeInd..21 307S /abstract
- Pradyut Kumar Swain1,*, Kasinath Das Mohapatral, Ratnakar Das2, Ashok Kumar Sahoo3, and Amlana Panda3 February 2020
- https://ui.adsabs.harvard.edu/abs/2020MeInd..21..307S
- https://www.researchgate.net/publication/266863408 Quality Improvement Model At The Manufacturing Process Preparation Level Article in International Journal for Quality Research December 2009
- https://www.researchgate.net/publication/342349012 Application of die casting: Article January 2018
- Manufacturing Engineering and materials processing A Series of Reference Books and Textbooks Copyright © 2002 by Marcel Dekker, Inc.
- Mass Production Definition – Investopedia https://www.investopedia.com
- https://www.villageplastics.com/3d-printing processes,additive manufacturing(AM).
- 3D Printing - Keene Village Plastics
- https://www.bartleby.com/questions-and-answers/milling-is-the-process-of-machining-using-rotary-cutters-to-remove-material-by-advancing-a-cutter-in/9570b70c-47df-4e5f-a80d-0e51fa920073
- https://www.custompartnet.com/wu/die-casting
- Experimental investigation into characterization and machining of Al + SiCp nano-composites using coated carbide tool
- A Study on Wear and Microstructure Properties of AA7075 Reinforced with SiC MMC by Powder Metallurgy Technique © 2020, IRJET | Impact Factor value: 7.34
- Comparative study of Al6061 and AlSi10Mg produced by Selective Laser Melting Process
- Quality Improvement Model At The Manufacturing Process Preperation Level, Dusko pavletic, Mirko Sokovic during December 2009
- Investment casting (IC) has benefited numerous industries as an economical means for mass producing quality near net shape metal parts with high geometric complexity and acceptable tolerances
- International Conference on Mechanical Engineering Research 2011 (ICMER2011) IOP Publishing IOP Conf. Series: Materials Science and Engineering 36 (2012)
- International Conference on Multi disciplinar yResearch & Practice
- Optimization of Process Parameters of CNC Milling for Aluminium Metal Matrix Composite
- Application of Die casting: A review paper of AKASH TIWARY, HARSIMRAN SINGH SODHI January 2018
- EOS material certificate material composition and properties.
- 3D prining images Google photos
- Hand book notes indo german tool room aurangabad, Die casting dies.
- Rate matrix india marts for compairing of material rates and costing.
- https://www.123rf.com/photo153959915the-multi-axis-cmm-machine-measuring-the-aluminium-casting-parts-by-touching-probe-the-quality-contr.html
- https://www.genfoundry.com/capabilities/quality
- https://www.mmsonline.com/products/methods-optimizes-three-axis-mv-1600h-for-large-workpieces
- Die casting process https://www.dynacast.com/en/specialty-die-casting/die-cast-process
専門家Q&A:あなたの疑問にお答えします
Q1: この研究で、試作品のコストパフォーマンスを改善するために特定された最も重要な要素は何ですか?
A1: 10個以上の試作品を製造する場合、最も重要な要素は「プロトダイカスト(ソフトツール)の採用」であると結論付けられています。Table 2.2とGraph 1.3が示すように、この方法はVMC加工や3Dプリンティングと比較して、品質を維持しつつコストを大幅に削減できるためです。
Q2: 1~2個だけの超少量試作の場合、この研究ではどの方法を推奨していますか?
A2: 論文では、1~2個のプロトタイピングには3Dプリンティングが適していると述べています(Abstract, 6.1 CONCLUSION)。この数量では、金型を製作する必要がないため、時間的なメリットが大きいためです。
Q3: この研究結果は、特定のアルミニウム合金に限定されるものですか?
A3: はい、この研究は主にプロトダイカストと3Dプリンティングでは「AlSi10Mg」、VMC加工では「Al6061」という特定の合金を使用して行われました(4.1 COMPONENT SPACIFICATION, 5.2 MATERIAL COMPARISION.)。他の合金への適用性については、さらなる検証が必要です。
Q4: なぜプロトダイカスト品の材料特性が、最終製品に最も近いと評価されたのですか?
A4: プロトダイカストは、量産と同じ「鋳造」というプロセスを用いるため、材料の凝固組織が最終製品に近くなります。Table 2.2によると、硬度(97 HB)が目標範囲(95-100 HB)に収まっており、VMC加工品(81 HB)や3Dプリンティング品(121 HB)よりも優れていることが示されています。
Q5: 論文によると、この研究の今後の展望や拡張性は何ですか?
A5: 著者は「6.2 FUTURE SCOPE」セクションで、今回使用したソフトツールは、5000個の部品を製造した後に硬化インサートに交換することで、10万ショットの通常ダイカスト金型として使用できる可能性があると述べています。これは、試作から量産へのシームレスな移行と、さらなるコスト削減の可能性を示唆しています。
Q6: この論文から、ダイカスト工場が得られる直接的で実用的な教訓は何ですか?
A6: 中核となる教訓は、「試作段階からソフトツールを用いたプロトダイカストを顧客に提案することは、非常に強力な競争優位性になる」ということです。論文「Process Selection on the Basis of Time Cost and Quality for Development Components of Aluminium Bracket」が示すように、特に10個以上の試作品を求める顧客に対し、コスト、時間、品質の面で最適なソリューションを提供できることが実証されています。
結論と次のステップ
本研究は、HPDCにおけるプロトタイプ製造のプロセス選択に、明確でデータに基づいたロードマップを提供します。特に、10個から1000個の範囲の試作品や少量生産において、プロトダイカスト(ソフトツール)がコストと品質の面で最も優れた選択肢であることを示しました。これは、開発リードタイムの短縮とコスト削減を目指す多くの企業にとって、非常に価値のある知見です。
株式会社CASTMANでは、最新の業界研究を応用し、お客様が抱える最も困難なダイカストの課題を解決することに専念しています。もし本稿で議論された課題がお客様の事業目標と共鳴するようでしたら、ぜひ当社の技術チームにご相談ください。これらの先進的な原則をお客様のコンポーネント開発にどのように活用できるか、共に検討させていただきます。
著作権
- 本資料は、"Piyush Shukla"氏による論文"Process Selection on the Basis of Time Cost and Quality for Development Components of Aluminium Bracket"に基づいています。
- 論文の出典: https://www.ijfmr.com/papers/2024/4/240423092.pdf (論文のDOIや直接リンクは記載されていなかったため、ジャーナルのウェブサイトから推測されるURLを記載)
本資料は情報提供のみを目的としています。無断での商業利用は禁じられています。
Copyright © 2025 CASTMAN. All rights reserved.