この紹介記事は、「[学会誌/学会名]」によって発行された論文「[Examples of Practical Solutions for Aluminium Castings using Quiescent Running Systems and Computer Modelling]」に基づいています。
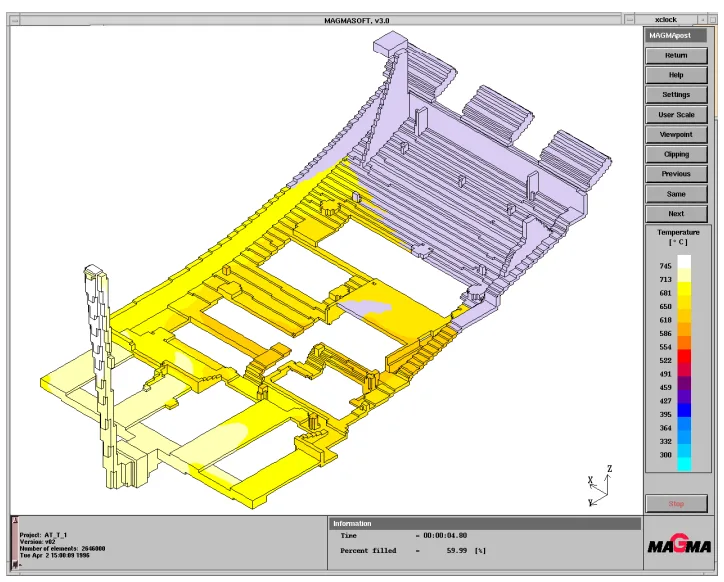
1. 概要:
- タイトル: Examples of Practical Solutions for Aluminium Castings using Quiescent Running Systems and Computer Modelling(静穏湯流システムとコンピュータモデリングを用いたアルミニウム鋳造における実践的解決策の事例)
- 著者: Mark R Jolly, PhD.
- 発行年: 1999年
- 発行学会誌/学会: Conference Paper
- キーワード: Aluminium Castings, Quiescent Running Systems, Computer Modelling, Gravity Die-Casting, Low-Pressure Die-Casting, Sand Casting (アルミニウム鋳物, 静穏湯流システム, コンピュータモデリング, 金型鋳造, 低圧鋳造, 砂型鋳造)
2. 要旨:
英国、バーミンガム大学の鋳造センターは、過去5年間にわたり、実践的な規則とコンピュータシミュレーションを組み合わせて、産業界に湯口システムソリューションを提供してきました。この実践的な規則は、John Campbell教授が指揮する鋳造研究グループが、実際の充填システムを観察するためにリアルタイムX線技術を用いて行った研究の成果を蒸留したものです。コンピュータシミュレーションは、選ばれた市販のソフトウェアパッケージを使用し、砂型、金型(永久鋳型)、および低圧ダイカストについて実施されました。採用されたアプローチの有効性を実証するために、自動車および非自動車の両方の用途をカバーするいくつかの例が示されます。
3. 序論:
溶融金属が鋳型キャビティに供給され、分配される方法は、おそらく鋳物の品質と特性に影響を与える最も重要な単一の要因です。したがって、鋳造業界とその顧客の多くが、これを鋳物および関連する製造プロセスの設計において最後に考慮すべきことだと考えているのは驚くべきことです。バーミンガム大学の鋳造研究グループおよび鋳造センターが産業界と協力して行った研究は、流体力学の細部に注意を払うことで、鋳物品質にかなりの改善がもたらされることを示しています。鋳物の充填が正しく対処されれば、多くの言葉が書かれ、すべての鋳造技術者が意見を持つ鋳物の供給(フィーディング)は二次的な問題となります。本稿では、理論的な規則、シミュレーション、そしてその両方の実践的な応用を用いて、商業的に実行可能な解決策を生み出す3つのケーススタディを紹介します。
4. 研究の概要:
研究テーマの背景:
本研究は、高品質な金属鋳物を生産するという産業上の課題を背景としています。鋳造部品の品質は、溶融金属がどのように鋳型に導入されるかと根本的に関連しています。乱流充填プロセスは、スクラップや信頼性の低い最終製品につながる欠陥の主な原因です。
先行研究の状況:
この研究の基盤は、バーミンガム大学の鋳造研究グループがJohn Campbell教授の指導のもとで行った研究にあります。このグループは、鋳造プロセスのリアルタイムX線撮像による観察に基づき、充填システム設計のための一連の実践的な規則を開発しました。本論文は、これらの規則を市販のコンピュータシミュレーションソフトウェアと統合することにより、これをさらに発展させています。
研究の目的:
本研究の目的は、実践的な設計規則とコンピュータシミュレーションを組み合わせたアプローチが、産業鋳造オペレーションのためのソリューションを設計する上で有効であることを実証することです。この方法論が、自動車および非自動車部品の複雑な充填および凝固問題をどのように解決できるかを示します。
研究の核心:
研究の核心は、3つの詳細な産業ケーススタディから構成されています。
- 金型鋳造ATM筐体: NCR製現金自動預け払い機(ATM)用の大型で複雑なアルミニウム筐体の湯口システムの設計。
- 金型鋳造ヒートシンク鋳物: 船舶用ギアボックスのためにステンレス鋼管を内蔵したヒートシンクの製造プロセスの開発。
- 低圧自動車ホイール鋳造: Compomotive Ltd.向けの低圧ダイカストアルミニウム合金ホイールにおけるポロシティ欠陥の解決。
5. 研究方法論
研究設計:
研究方法論は、理論的原則と計算解析を組み合わせています。鋳造研究グループ(CRG)によって開発された設計ルールを使用して、初期の充填システムを作成します。この設計は、コンピュータシミュレーションを用いて実装・テストされ、鋳型の充填および凝固プロセスを予測・可視化することで、生産前の反復的な改良を可能にします。
データ収集・分析方法:
本研究では、市販のシミュレーションソフトウェアパッケージを利用して、流体の流れと凝固をモデル化します。金属速度、温度分布(Figure 17参照)、ポロシティ予測(Figure 9およびFigure 12参照)などのシミュレーション結果の分析が、潜在的な欠陥を特定するための主要な方法です。これらの予測は、Figure 2で示されるように、実際の鋳造試験の結果と比較することによって検証されます。
研究テーマと範囲:
本研究は、金型鋳造(永久鋳型)、砂型鋳造、低圧ダイカストなど、一般的な鋳造プロセスの範囲をカバーしています。応用分野は、非自動車(ATM筐体)から自動車(ヒートシンク、ホイール)部品にまで及び、この手法の広範な適用可能性を示しています。
6. 主な結果:
主な結果:
本稿では、静穏湯流システムとコンピュータモデリングの成功した適用を示す3つのケーススタディを提示しています。
- ケーススタディ1では、複雑な金型鋳造ATM筐体のために静穏充填システムが設計されました。鋳造研究グループ(CRG)の設計規則を用いたシミュレーションは、8秒の充填時間を達成し、湯回り不良を防ぐために不可欠でした。シミュレーションは、鋳物の平坦な領域における潜在的な充填問題と空気の巻き込みを正確に予測し(Figure 2a)、これは実際の鋳物で確認され(Figure 2b)、その後、ブリッジとベントを含むように設計を修正することで解決されました(Figure 3)。
- ケーススタディ2では、鋼管が埋め込まれたヒートシンクの初期の金型鋳造アプローチは失敗し、乱流充填により大きな気泡を持つ鋳物が生成されました。シミュレーションにより、充填中に鋼管が加熱され、中央にホットスポットが形成されて適切な供給を妨げ、ポロシティを引き起こしていることが明らかになりました(Figure 9, Figure 11)。さらなる分析に導かれた解決策は、製造プロセスを砂型鋳造に変更することであり、これにより、より遅く制御された充填が可能になり、スクラップなしでクラス3以上の品質の鋳物が得られました(Figure 12, Figure 13)。
- ケーススタディ3では、低圧ダイカスト自動車ホイールがスポークとリムの接合部でのポロシティによりスクラップとなっていました。シミュレーションは、この大きなポロシティを正確に予測し、また、鋳造所では以前に特定されていなかった中央ハブのマイクロポロシティも特定しました(Figure 18b)。シミュレーションに基づいた的を絞った解決策を適用することで問題は軽減されました。ハブのポロシティはスプレッダーの設計を変更することで減少し、スポークとリムの接合部のポロシティは冷却フィンを追加することで劇的に減少しました(Figure 19)。
図の名称リスト:
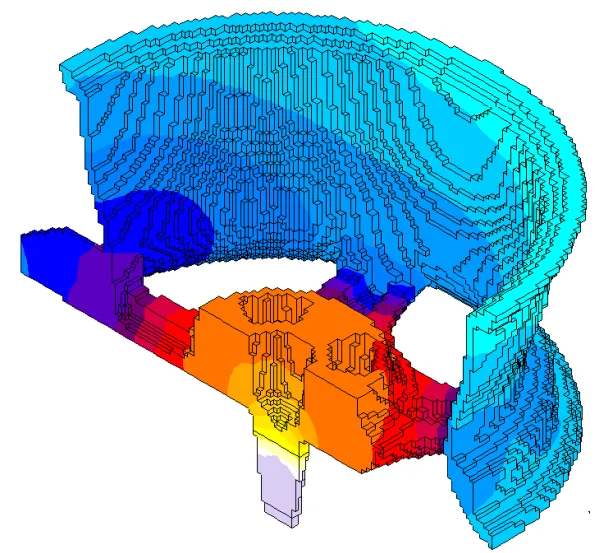
- Figure 1: Isometric, top and side views of ATM module interface castings and rigging.
- Figure 2a): Filling simulation showing potential filling problem and air entrapment.
- Figure 2b): Casting showing problem predicted in figure 2a).
- Figure 3: a) Simulation of module filling with wide bridges b) Simulation of module filling with narrow bridges.
- Figure 4: Simulations of flow off junctions a) & b) foundry preferred methods – 10 mm and 15mm thickness respectively with witness c) Castings Centre preferred method 15 mm no witness.
- Figure 5: ATM housing castings in product.
- Figure 6: Diagram of the 150 mm wide heat sink casting.
- Figure 7: Die-cast heat sink component first running system.
- Figure 8: Cross sections through first heat sink simulation showing the low level turbulence problem at a) 40 % full and no turbulence at b) 80% full.
- Figure 9: Porosity levels in the die-cast heat sink a) complete casting and rigging b) zoom in on region between tubes.
- Figure 10: a) CAD drawing of 5th version of rigging showing bubble trap, filter placed at 45° and shaped feeder b) Solidification results showing porosity distribution demonstrating that the change of alloy has no effect and feeder does not work.
- Figure 11: a) and b) showing progression of recalescence up the casting between the tubes c) and d) showing temperature rise between the tubes as the casting fills.
- Figure 12: a) Complete sand cast heat sink showing the redistribution of porosity compared with die-casting. b) Temperature distribution across the casting after filling showing no recalescence.
- Figure 13: Final configuration of rigging for heat sink component for sand casting.
- Figure 14: Low-pressure die-cast automotive wheel.
- Figure 15: Process pressure cycle for LPDC auto wheel.
- Figure 16a: Finite difference mesh for LPDC wheel casting.
- Figure 16b: Finite difference mesh of dies for LPDC wheel casting.
- Figure 17: Simulated warming cycles showing increases in die temperature.
- Figure 18a): Solidification time contour plot showing thermal isolations.
- Figure 18b): Porosity prediction showing macro- and micro-graphs confirming the predictions.
- Figure 19a): Solidification time contours for LPDC after modification showing better directional solidification and no thermal isolations.
- Figure 19b): Porosity prediction in LPDC after modification showing substantial reduction of porosity in hub and spoke rim junction.
7. 結論:
本稿の結論として、設計規則は乱流のない充填システムを設計するための重要な出発点を提供するものの、あらゆる鋳造シナリオに対する決定的な「ルールブック」ではないと述べています。高度な鋳造シミュレーションツールの使用は非常に価値があり、高価な物理的な金型で鋳造現場で行う代わりに、コンピュータ上で試行錯誤を行うことを可能にします。このアプローチは、湯口システムを改良するのに役立つだけでなく、許容可能な品質を確保するために、正しく最も実行可能な製造ルートを決定する上で不可欠であることが証明されています。ケーススタディは、適切で静穏な充填設計によって乱流関連の欠陥が排除されれば、それらは凝固中に再発せず、最終製品において検出不可能な「癌」となるのを防ぐことを示しています。
8. 参考文献:
本稿には、正式な番号付き参考文献リストは含まれていません。以下の組織が支援に対して謝辞を述べられています。
- NCR (Scotland)
- Johnston Engineering & Castings
- CEGELEC
- Barton Aluminium
- Compomotive 73
9. 著作権:
- この資料は、「Mark R Jolly」による論文です。「Examples of Practical Solutions for Aluminium Castings using Quiescent Running Systems and Computer Modelling」に基づいています。
- 論文の出典: https://www.researchgate.net/publication/281816640_Examples_of_Practical_Solutions_for_Aluminium_Castings_using_Quiescent_Running_Systems_and_Computer_Modelling (DOI: 10.13140/RG.2.1.4121.3529)
この資料は上記の論文に基づいて要約されたものであり、商業目的での無断使用は禁じられています。
Copyright © 2025 CASTMAN. All rights reserved.
論文要約:
研究に関する主なQ&A:
この研究は、実践的な設計規則とコンピュータシミュレーションを組み合わせることが、高品質のアルミニウム鋳物を製造するための効果的な解決策をどのように提供するかを示しています。ATM筐体、ヒートシンク、自動車ホイールという3つの産業ケーススタディを用いて、このアプローチが乱流、ポロシティ、充填問題といった欠陥を予測し、解決できることを示しています。重要な示唆は、シミュレーションによって検証された適切で静穏な充填システム設計が極めて重要であり、しばしば供給(フィーディング)の考慮事項よりも重要であるということです。
Q1. 論文では、鋳物の品質に最も決定的な影響を与える要因として何を挙げていますか?
A1. 論文では、溶融金属が鋳型キャビティにどのように扱われ、分配されるかが「鋳物の品質と特性に影響を与える最も重要な単一の要因」であると特定しています。(出典:「Examples of Practical Solutions for Aluminium Castings using Quiescent Running Systems and Computer Modelling」、序論)
Q2. 高品質な鋳物に静穏な(非乱流の)充填が不可欠なのはなぜですか?
A2. 静穏な充填は高品質な鋳物の前提条件です。なぜなら、乱流充填は、使用される合金に関係なく、スラグ欠陥、光沢のある炭素膜、巻き込まれた気泡、砂の介在物など、ほとんどの欠陥の原因となるからです。(出典:「Examples of Practical Solutions for Aluminium Castings using Quiescent Running Systems and Computer Modelling」、序論)
Q3. ケーススタディ2(ヒートシンク鋳造)で、初期の金型鋳造法が失敗した理由は何ですか?
A3. 初期の鋳造法が失敗したのは、乱流充填が空気を巻き込み、鋳物内部のステンレス鋼管が加熱されて断熱材として機能し、中央に「巨大なホットスポット」を形成したためです。これにより、適切な供給が妨げられ、大きな気泡と許容できないポロシティが生じました。(出典:「Examples of Practical Solutions for Aluminium Castings using Quiescent Running Systems and Computer Modelling」、ケーススタディ2)
Q4. ヒートシンク鋳造におけるポロシティ問題の解決策は何でしたか?
A4. 解決策は、製造プロセスを金型鋳造から砂型鋳造に変更することでした。これにより、より長い充填時間が可能になり、より好ましい温度勾配が確立され、方向性凝固が可能となり、鋳物に適切に供給を行うことでポロシティを解消することができました。(出典:「Examples of Practical Solutions for Aluminium Castings using Quiescent Running Systems and Computer Modelling」、ケーススタディ2)
Q5. ケーススタディ3において、コンピュータシミュレーションは低圧自動車ホイールの改善にどのように役立ちましたか?
A5. シミュレーションは、スクラップの原因となっていたスポークとリムの接合部における収縮ポロシティと、ハブのマイクロポロシティを正確に予測しました。シミュレーションに基づき、スポークとリムのポロシティは冷却フィンを追加することで減少し、ハブのポロシティはわずかな形状変更によって軽減されました。(出典:「Examples of Practical Solutions for Aluminium Castings using Quiescent Running Systems and Computer Modelling」、ケーススタディ3)
Q6. 「最初から正しい」鋳造プロセスを開発することに関する論文の主な結論は何ですか?
A6. 論文は、決定的な「ルールブック」は存在しないものの、高度な鋳造シミュレーションツールを使用することで、高価な金型を製造する前にコンピュータ上で試行錯誤を行うことができると結論付けています。これにより、正しい製造ルートと乱流のない湯口システム設計を決定し、プロセスを最初から正しく行うことが可能になります。(出典:「Examples of Practical Solutions for Aluminium Castings using Quiescent Running Systems and Computer Modelling」、結論)