この紹介論文は、「Journal of Materials Processing Technology」によって発行された論文「Studies on Die Filling of A356 Al alloy and Development of a Steering Knuckle Component using Rheo Pressure Die Casting System」に基づいています。
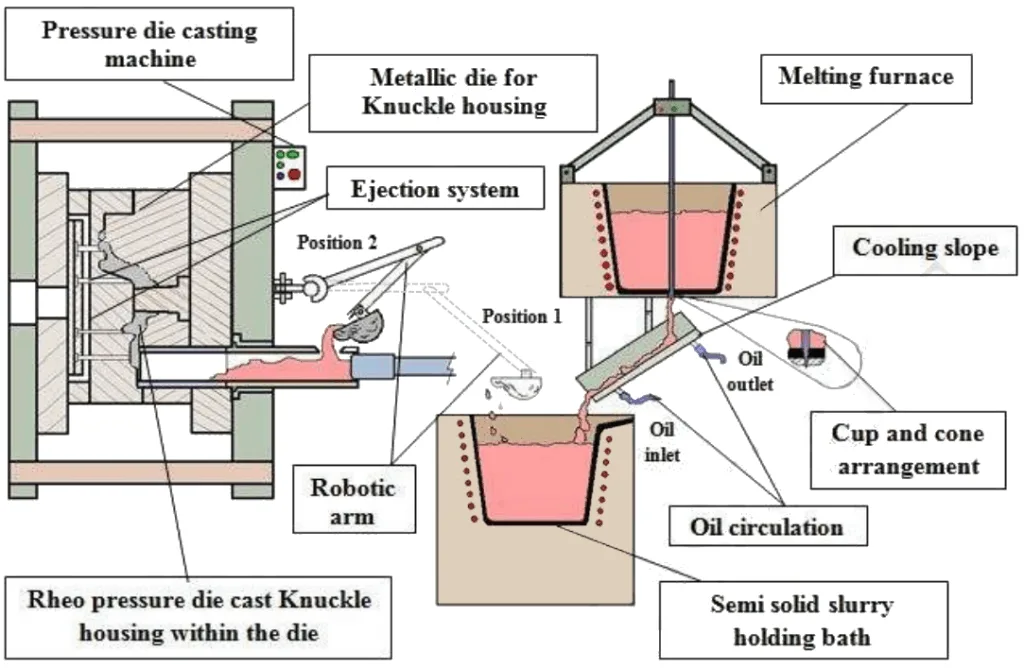
1. 概要:
- タイトル: Studies on Die Filling of A356 Al alloy and Development of a Steering Knuckle Component using Rheo Pressure Die Casting System
- 著者: Prosenjit Das, Bikash Bhuniya, Sudip K. Samanta, Pradip Dutta
- 発行年: 2019年
- 発行学術誌/学会: Journal of Materials Processing Technology
- キーワード: ステアリングナックル, 半凝固, RPDC, A356合金, ダイ充填
2. 抄録:
本研究では、レオ圧力ダイカスト (RPDC) システムの一部として、半凝固スラリーのダイ充填を調査するために、数値流体力学 (CFD) モデルを開発する。ダイ充填キャビティは自動車のステアリングナックルのものに対応し、スラリーはA356アルミニウム合金で作られる。CFDシミュレーションで使用されるレオロジーモデルは実験的に決定される。現在の数値モデルから得られた結果には、ダイキャビティ内のスラリーの流動場、粘度変化、固相率分布、ダイ充填段階中のキャビティ内凝固中の温度および圧力分布が含まれる。本研究の主な目的は、開発された部品の望ましい微細構造および機械的特性のためのゲーティング配置、注入温度、および射出条件を決定することである。当該合金スラリーのダイ充填能力に対する射出条件の影響を研究するために、最終射出速度を2~3.2 m/sの間で変化させて5つの射出プロファイルを研究する。本研究の知見を裏付けるために、凝固した部品の異なる位置からサンプルを取得することにより、主に光学顕微鏡およびマクロ硬度測定の形で、微細構造形態および構造特性相関を研究した。
3. はじめに:
自動車産業における燃費向上のための要求は、自動車部品の軽量化、特に他の軽量自動車部品と比較して優れた強度対重量比および伸び値を必要とするサスペンション部品の軽量化に向けた努力を動機付けている。アルミニウムおよびマグネシウム合金の鍛造や従来のダイカストなどの伝統的な製造プロセスは、多段階の処理ステップ、一貫性のない機械的特性、デンドライト微細構造、および液体偏析などの課題を提示する。半凝固ダイカスト、特にレオダイカスト (RDC) およびその変形であるレオ圧力ダイカスト (RPDC) は、改善された構造的完全性と費用対効果を備えた、健全でニアネットシェイプの部品を製造するための有望なワンステップソリューションとして浮上している。これらのプロセスの成功は、複雑なダイキャビティの適切な充填を保証するために、ほぼ球状の初晶粒子を持つ半凝固スラリーの調製に大きく依存する。多くの研究がチクソダイカスト (TDC) およびRDCを調査してきたが、RPDCにおけるダイ充填のCFDシミュレーション、特に実験的検証を伴うものは比較的少ない。本研究は、CFDシミュレーションを用いてA356 Al合金ステアリングナックルのRPDCプロセスパラメータを最適化し、実験作業によって検証することにより、このギャップを埋めることを目的とする。
4. 研究の概要:
研究トピックの背景:
主な動機は、燃費を向上させるための軽量自動車部品の必要性である。伝統的に鋼鉄または鋳鉄で作られていた自動車のサスペンション部品は、アルミニウムおよびマグネシウム合金を使用して開発されている。しかし、これらの軽合金の従来の製造方法では、しばしば欠陥や特性のばらつきが生じる。
従来の研究状況:
従来の研究では、従来のグラビティダイカスト (GDC)、高圧ダイカスト (HPDC)、スクイズキャスティング、およびチクソダイカスト (TDC) やレオダイカスト (RDC) を含む半凝固金属 (SSM) プロセスなど、さまざまな鋳造プロセスが検討されてきた。研究では、HPDCにおける偏析バンド、微小気孔、高温割れなどの欠陥が強調されている。RDCはTDCよりもエネルギー効率とコスト効率に優れていることが注目されている。いくつかの研究者がさまざまな部品や合金に対してRDCを調査し、一部はさまざまなレオロジーモデルを使用してダイ充填をシミュレートするためにCFDを使用している。しかし、RPDCの包括的な理解、特にステアリングナックルのような複雑な部品に対する検証済みのシミュレーションによる理解はまだ発展途上である。
研究の目的:
本研究の主な目的は、A356 Al合金から自動車のステアリングナックル部品を開発するためのレオ圧力ダイカスト (RPDC) システムのプロセスパラメータを最適化することである。これには、ダイ充填プロセスを調査し、望ましい微細構造と機械的特性を達成するための理想的なゲーティング配置、注入温度、および射出条件を決定するためにCFDシミュレーションを使用することが含まれる。この研究はまた、シミュレーションの知見を実験的に検証することも目的としている。
核心研究:
本研究の核心は、ステアリングナックルのダイキャビティにおけるA356半凝固スラリーのダイ充填をシミュレートするためのCFDモデルを開発することである。これには、A356合金の実験的なレオロジーモデルの確立が含まれる。本研究では、注入温度、ゲーティング設計(ゲートの位置と数)、および射出速度プロファイルが、固相率分布、巻き込み空気、スラリー粘度、速度、温度場、圧力分布などのダイ充填特性に及ぼす影響を調査する。次に、数値結果は、自社開発のRPDC設備を使用した実験的試行によって検証され、その後、鋳造されたステアリングナックルの微細構造特性評価および機械的特性試験(硬度、引張強度)が行われる。
5. 研究方法論
研究設計:
本研究は、2つのアプローチを採用している。
- 数値流体力学 (CFD) モデリング: ステアリングナックル部品のRPDCシステムにおける半凝固A356 Al合金スラリーのダイ充填プロセスをシミュレートするための数値モデルが開発された。これには、質量、運動量、エネルギーの保存則、および金属-空気界面を追跡するためのVOF (volume-of-fluid) 法の解法が含まれた。実験的に導出されたレオロジーモデルが組み込まれた。
- 実験的検証: 自社RPDC設備を使用して物理実験が行われた。CFDシミュレーションから導出された最適パラメータを使用してステアリングナックルが鋳造された。その後、鋳造部品に対して微細構造解析および機械的試験が行われ、シミュレーション予測を検証し、部品品質を評価した。
データ収集および分析方法:
- CFDシミュレーション:
- 支配方程式(連続の式、運動量方程式、エネルギー方程式、VOF)は、商用CFDソフトウェアFOLW-3D Castを使用して解かれた。
- 実験データ(Das et al., 2015)から導出された定数を持つオストワルド・ド・ワーレのべき乗則に基づくレオロジーモデルを使用して、スラリー粘度を記述した(μ = (2.786 E - 05) e^(14430.50 / T) γ⁻¹, Eq. 10)。
- ゲーティング付きナックルハウジングの3D CADモデルが作成され(Fig. 3a)、ドメインは六面体格子で離散化された(Fig. 3b)。格子独立性が研究された。
- 境界条件、ベント位置(Fig. 3c)、合金(Table 1, Table 2)およびダイ材料(Table 3)の熱物性値が指定された。
- 固相率変化は、実験的なDTA結果(Fig. 4)およびScheil方程式(Eq. 11)に基づいていた。
- 実験作業:
- A356 Al合金を溶解し、脱ガス処理し、冷却スロープを介して処理して半凝固スラリーを生成した。
- スラリーはRPDC機に移送する前に等温保持された(Fig. 17はスラリー形態を示す)。
- 最適化されたパラメータを使用してステアリングナックルを鋳造した。
- 鋳造部品のさまざまな位置からサンプルを切り出し(Fig. 19)、以下を実施した。
- 微細構造解析: 光学顕微鏡、FESEM(Fig. 22)を使用して、結晶粒径、形態、および共晶組織を観察した。結晶粒径と球形度を定量化した(Eqs. 13, 14, Fig. 20)。
- 機械的試験: マクロ硬度測定(Fig. 21)および引張試験(ASTM E8ガイドライン)を実施した。破断面を分析した(Fig. 23)。
- 最大キャビティ圧力を測定し、数値予測と比較した(Fig. 18)。
研究トピックと範囲:
本研究は以下に焦点を当てた。
- 複雑なステアリングナックルのダイキャビティにおけるA356 Al合金半凝固スラリーのRPDCプロセスを用いたダイ充填挙動の調査。
- RPDCプロセスのためのCFDモデルの開発と検証。
- 主要なプロセスパラメータの影響の研究:
- スラリー注入温度(585°C, 600°C, 605°C, 610°C)。
- ゲートの位置と数(シングルゲート、2ゲート、引張試験片の位置が異なる3ゲート、Fig. 11参照)。
- 射出速度プロファイル(5つの異なるプロファイル、Fig. 13)。
- ダイ充填特性の分析: 固相率分布、巻き込み空気の体積分率、スラリー粘度、スラリー速度、温度分布、およびキャビティ圧力。
- 鋳造されたステアリングナックルの微細構造(初晶Al結晶粒径、球形度、共晶Si形態)および機械的特性(マクロ硬度、引張強度)とプロセスパラメータとの相関。
- CFDモデルによって予測された最適プロセス条件の実験的検証。
6. 主要結果:
主要結果:
- 最適注入温度: 610°Cのスラリー注入温度が、ダイ充填能力および部品鋳造に最適であることが判明し、均一な固相率分布(Fig. 6a)を保証し、低温と比較して未充填領域を最小限に抑えた。変更されたベント位置は、この温度での空気排出をさらに改善した(Fig. 7d)。
- 最適ゲーティング設計: 3ゲート配置(Fig. 11eのように)が、均質な微細構造形態に不可欠な、部品内の均一な凝固速度を保証するのに最も効果的であることが確認された。
- 最適射出速度プロファイル: 射出プロファイル1(最終速度3 m/s、Fig. 13a)は、最適なスラリー圧力と固相率分布(Fig. 14a、Fig. 15a)をもたらし、スムーズなダイ充填と良好な構造的完全性を促進した。
- レオロジーと流動挙動: 実験的に決定されたレオロジーモデルは、A356スラリーのせん断減粘挙動を効果的に捉えた。スラリー粘度は、ダイ内の局所的なせん断速度と温度に大きく依存することが示された(Fig. 8)。
- 実験的検証:
- 最適化されたパラメータ(610°Cスラリー、3ゲート、射出プロファイル1)を用いた実験により、ステアリングナックルが正常に製造された。
- スラリーは、その球状微細構造の著しい劣化なしに、約14分間610°Cで保持することができた(Fig. 17)。
- 最大キャビティ圧力の数値予測は実験値を過小評価したが、傾向は同等であった(Fig. 18)。乱流およびガス吸収による欠陥が増加する最適キャビティ圧力が特定された。
- 微細構造: RPDC鋳造ナックルは、一般的に均一な初晶α-Al粒子の分布(約55%の面積分率)を持つバイモーダルな粒子構造を示した。初晶粒子のメジアンサイズは24µmで、平均球形度は0.88であった(Fig. 20)。中途充填された位置は、最も良好な球状初晶Al粒子を示した(Fig. 19)。
- 機械的特性:
- 鋳放しRPDC部品の平均マクロ硬度は約70 VHNであり(Fig. 21)、これは従来のHPDC部品と比較して大幅な改善であった。
- 平均引張特性は、降伏強度170 MPa、極限引張強度219 MPa、伸び9.72%であった。破断面は混合モード破壊を示した(Fig. 23)。
図の名称リスト:
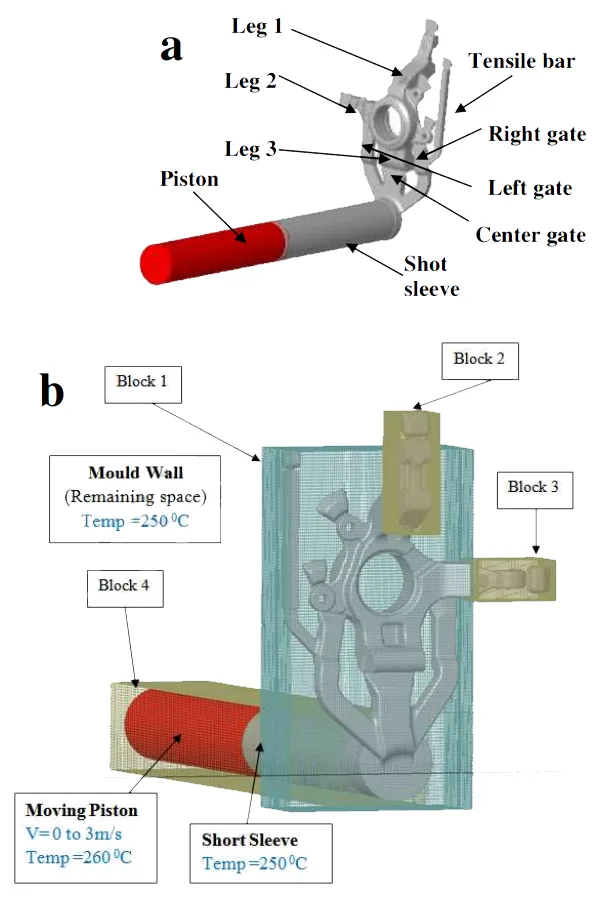
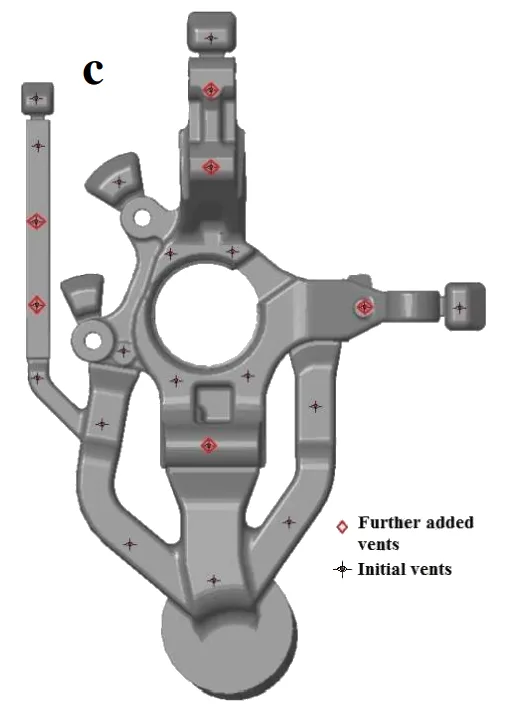
- Fig. 1: Schematic of the Rheo pressure die casting system, showing its functional parts.
- Fig. 2: Slurry viscosity as a function of (a) shear rate, and (b) temperature.
- Fig. 3: (a) Solid model of Knuckle housing with gating arrangement, (b) discretized solution domain, and (c) location of vents considered to perform die filling simulations.
- Fig. 4: (a) Solid fraction vs. temperature curve, and (b) DTA analysis results.
- Fig. 5: Flowchart of the numerical scheme.
- Fig. 6: Solid fraction and temperature distribution within the die cavity after filling completion: (a) Solid fraction and (b) Temperature (Das et al., 2015).
- Fig. 7: Volume fraction of entrained air within the die cavity for different slurry pouring temperatures: (a) 585°C, (b) 600°C, (c) 605°C, and (d) 610°C.
- Fig. 8: Slurry viscosity profiles for different slurry pouring temperatures: (a) 585°C, (b) 600°C, (c) 605°C, and (d) 610°C.
- Fig. 9: Variation of slurry velocity with filling time, for the central gate.
- Fig. 10: Slurry temperature distribution vs. filling time.
- Fig. 11: Slurry temperature distribution for different cavity designs: (a) with central gate, (b) with central and left gate, (c) with central and right gate, (d) three gates with tensile sample position 1, and (e) three gates with tensile sample position 2.
- Fig. 12: Effect of gate no. and locations on (a) solid fraction evolution, (b) viscosity, and (c) velocity of the semi solid slurry.
- Fig. 13: Injection velocity profiles considered for the present study: (a) profile 1, (b) profile 2, (c) profile 3, (d) profile 4, and (e) profile 5.
- Fig. 14: Cavity pressure distribution for different injection velocity profiles: (a) profile 1, (b) profile 2, (c) profile 3, (d) profile 4, and (e) profile 5.
- Fig. 15: Effect of injection velocity profile on solid formation: (a) profile 1, (b) profile 2, (c) profile 3, (d) profile 4, and (e) profile 5.
- Fig. 16: Temporal variation of slurry velocity during filling of the die cavity for different injection velocity profile: (a) profile 1, (b) profile 2, (c) profile 3, (d) profile 4, and (e) profile 5.
- Fig. 17: Representative optical micrographs of oil quenched samples showing slurry morphology, at different slurry formation stages.
- Fig. 18: Comparative plot of numerical and experimental findings of maximum cavity pressure and radiographs of Leg 1 (Fig. 2) of the solidified Knuckle housing for all five injection conditions.
- Fig. 19: Digital photograph of the Rheo pressure die cast prototype Knuckle housing, and optical micrographs of different locations of the solidified component.
- Fig. 20: Distribution of (a) primary Al particle size and their (b) sphericity for the samples taken from different sections of the solidified knuckle housing.
- Fig. 21: Distribution of macro hardness for the samples taken from different sections of the solidified knuckle housing.
- Fig. 22: Representative FESEM micrographs: (a) distribution of globular primary solid grains and eutectic Si particles, (b) high magnification image of eutectic morphology.
- Fig. 23: Representative SEM factographs: (a) at 1000X magnification, and (b) at 1500X magnification.
7. 結論:
本研究では、レオ圧力ダイカスト経路に従ってナックルハウジングを開発するためのダイ形状およびプロセス変数の最適化が提示された。本研究から得られた結論は以下の通りである。
- シミュレーション結果に基づき、0.15の固相率に対応する610°Cのスラリー注入温度、3.0 m/sの射出チップ速度、および250°Cの予熱温度を持つ3ゲートダイキャビティが、健全な構造的完全性を持つ3脚ナックルハウジングを首尾よく開発するための最適条件であることが見出された。
- 初晶Al粒子の微細構造形態は、RPDC鋳造部品全体にわたって等方性であり、約70 VHNの平均マクロ硬度を持つことが見出された。これは、従来の高圧ダイカスト (HPDC) 部品と比較して著しく改善されている。
- 冷却スロープで生成されたスラリーは、部品開発に利用する前に、その微細構造形態の大きな劣化なしに、等温スラリー保持浴内で約14分間保持できることが観察された。
- 凝固した部品の数値結果および代表的なX線写真から、最大キャビティ圧力のある特定の値まではRPDC鋳造部品の構造的完全性が向上し、それを超える圧力では、ダイ充填中の可能性のある乱流およびその後のガス吸収により、鋳造部品内に欠陥が形成されることが明らかである。
- 充填された部品キャビティの凝固段階に関するシミュレーション研究、および鋳放し状態と熱処理状態におけるRPDC鋳造部品の微細構造と引張特性の詳細な調査は現在進行中であり、その結果は将来の出版物で報告される予定である。
8. 参考文献:
- Blanco, A., Azpilgain, Z., Lozares, J., Kapranos, P., Hurtado, I., 2010. Rheological characterization of A201 aluminum alloy. Trans. Nonferrous Met. Soc. China, 20, 1638-1642.
- Brabazon, D., Browne, D.J., Carr, A.J., 2003. Experimental investigation of the transient and steady state rheological behaviour of Al–Si alloys in the mushy state. Materials Science and Engineering A, 356, 69-80.
- Campbell, J., 2003. Castings. Butterworth-Heinemann: Oxford, UK; Chapter 9.
- Campo, K. N., Proni, C. T. W., Zoqui, E. J., 2013. Influence of the processing route on the microstructure of aluminum alloy A356 for thixoforming. Materials Characterization, 85, 26-37.
- Choi, B. H., Jang, Y. S., Sim, J. G., Kim, H. S., Hong, C. P., 2013. Application of Rheo-diecasting of a High Strength Al-Si-Mg Alloy to Automotive Suspension Arms. ISIJ International, 53, 502-510.
- Das, P., Dutta, P., 2016. Phase field modelling of microstructure evolution and ripening driven grain growth during Cooling Slope processing of A356 Al alloy. Computational Materials Science, 125, 8–19.
- Das, P., Samanta, S.K., Chattopadhyay, H., Dutta, P., 2012. Effect of pouring temperature on cooling slope casting of semi-solid Al-Si-Mg alloy. Acta Metallurgica Sinica (English Letters), 25, 329-339.
- Das, P., Samanta, S.K., Chattopadhyay, H., Sharma, B.B., Dutta, P., 2013. Eulerian two-phase flow simulation and experimental validation of semisolid slurry generation process using cooling slope. Material Science and Technology, 29, 83-92.
- Das, P., Samanta, S.K., Das, R., Dutta, P., 2014. Optimization of degree of sphericity of primary phase during cooling slope casting of A356 Al alloy: Taguchi method and regression analysis. Measurement, 55, 605–615.
- Das, P., Samanta, S.K., Dutta, P., 2015. Rheological Behavior of Al-7Si-0.3Mg Alloy at Mushy State, Metall. Mater. Trans. B. 46, 1302-1313.
- Das, P., Samanta, S.K., Tiwari, S., Dutta, P., 2015. Die Filling Behaviour of Semi Solid A356 Al Alloy Slurry During Rheo Pressure Die Casting, Trans Indian Inst Met. 68, 1215–1220.
- Das, P., Samanta, S.K., Mondal, B., Dutta, P., 2018. Multiphase Model of Semisolid Slurry Generation and Isothermal Holding During Cooling Slope Rheoprocessing of A356 Al Alloy. Metallurgical and Materials Transactions B, 49, 1925-1944.
- Gourlay, C. M., Laukli, H. I., Dahle, A. K., 2004. Segregation Band Formation in Al-Si Die Castings, Metall. Mater. Trans. A. 35, 2881-2891.
- Gourlay, C. M., Laukli, H. I., Dahle, A. K., 2007. Defect Band Characteristics in Mg-Al and Al-Si High-Pressure Die Castings, Metall. Mater. Trans. A. 38, 1833-1844.
- Guanglei, Z., Jun, X., Zhifeng, Z., Guojun, L., 2010. Numerical simulation of die filling behavior of AZ91D in the semisolid process, China Foundry. 7(2), 127-131.
- Guan-hai, Y., Sheng-dun, Z., Zheng-hui S., 2010. Simulation of semisolid diecasting process of four-way valve of HPb59-1 alloy for air-conditioner, Nonferrous Met. Soc. China. 20, s931-s936.
- Hirt, C. W., 2012. Modeling Turbulent Entrainment of Air at a Free Surface, Flow Science Report, 01-12.
- Hirt, C. W., 2013. Void Regions and Bubble Models in FLOW-3D, Flow Science Report, 01-13.
- Hitchcock, M., Wang, Y., Fan, Z., 2007. Secondary solidification behaviour of the Al–Si-Mg alloy prepared by the rheo-diecasting process. Acta Materialia, 55, 1589–1598.
- Hongmin, G., Xiangjie, Y., Bin, H., Guanglei, Z., 2007. Rheo-diecasting Process for Semi-solid Aluminum Alloys, Journal of Wuhan University of Technology-Mater. Sci. Ed. 22(4), 590-595.
- Kang, C. G., Lee, S. M., 2008. Effect of Solid Fraction and Pressure on Microstructure and Mechanical Properties and Reduction in Liquid Segregation in the Thixo-Die-Casting Process with Al-7 Pct Si Alloy, Metallurgical and Materials Transactions A, 39, 1213-1224.
- Kang, C. G., Lee, S. M., Kim, B. M., 2008. A study of die design of semi-solid die casting according to gate shape and solid fraction, Journal of Materials Processing Technology. 204, 8-21.
- Kang, C.G., Seo, P.K., 2003. The effect of gate shape on the filling limitation in the semi-solid forging process and the mechanical properties of the products, Journal of Materials Processing Technology. 135, 144–157.
- Kang, C.G., Seo, P.K., Kang, S. S., 2006. The effect of injection velocity on liquid segregation and mechanical properties in arm part fabricated by semi-solid die casting process, Journal of Materials Processing Technology. 176, 32-40.
- Kapranos, P., Haga, T., Bertoli, E., Pola, A., Azpilgain, Z., Hurtado, I., 2008. Thixo-extrusion of 5182 aluminium alloy. Solid State Phenom. 141–143, 115–120.
- Kleiner, S., Ogris, E., Beffort, O., Uggowitzer, P. J., 2003. Semi Solid Metal Processing of Aluminum Alloy A356 and Magnesium Alloy AZ91: Comparison Based on Metallurgical Considerations. 5, 653–658.
- Lakshmi, H., Kumar, M.C.V., Raghunath, Kumar, P., Ramanarayanan, V., Murthy, K. S. S., Dutta, P., 2010. Induction Reheating of Aluminum Alloy A356 and Thixocasting of an Automobile Component, Transaction of Nonferrous Metals Society of China. 20, S961-S967.
- Laukli, H.I., Gourlay, C.M., Dahle, A.K., 2005. Migration of Crystals during the Filling of Semi-Solid Castings, Metall. Mater. Trans. A, 36, 805-818.
- Liu, Z. Y., Mao, W. M., Wang, W. P., Zheng, Z. K., Yue, R., 2017. Investigation of rheo-diecasting mold filling of semi-solid A380 aluminum alloy slurry, International Journal of Minerals, Metallurgy and Materials, 24, 691-700.
- Pola, A., Tocci, M., Kapranos, P., 2018. Microstructure and Properties of Semi-Solid Aluminum Alloys: A Literature Review, Metals, 8, 181, doi:10.3390/met8030181.
- Ri, K., Mao, W. M., Zheng, Z. K, Kim, M., Sin, Y., 2016. Effect of rheo-diecast process on the mechanical properties of A390 alloy by serpentine channel, International Journal of Minerals, Metallurgy and Materials, 23, 1177-1186.
- Otarawanna, S., Gourlay, C. M., Laukli, H. I., Dahle, A. K., 2009. Microstructure Formation in AlSi4MgMn and AlMg5Si2Mn High-Pressure Die Castings, Metall. Mater. Trans. A, 40, 1645-1659.
- Otarawanna, S., Gourlay, C. M., Laukli, H. I., Dahle, A. K., 2009. The thickness of defect bands in high-pressure die castings, Materials Characterisation, 60, 1432-1441.
- Pirovano, R., Mascetti, S., 2016. Tracking of collapsed bubbles during a filling simulation Die-casting. Metall. Ital., 6, 37–40.
- Qi, M., Kang, Y., Zhou, B., Liao, W., Zhu, G., Li, Y., Li, W., 2016. A forced convection stirring process for Rheo-HPDC aluminum and magnesium alloys, Journal of Materials Processing Technology, 234, 353-367.
- Qi, M., Kang, Y., Qiu, Q., Tang, W., Li, J., Li, B., 2018. Microstructures, mechanical properties, and corrosion behavior of novel high-thermal-conductivity hypoeutectic Al-Si alloys prepared by rheological high pressure die-casting and high pressure die-casting, Journal of Alloys and Compounds, 749, 487-502.
- Reikher, A., Pillai, K.M., 2013. A fast simulation of transient metal flow and solidification in a narrow channel. Part I: Model development using lubrication approximation, International Journal of Heat and Mass Transfer. 60, 797-805.
- Reikher, A., Pillai, K.M., 2013. A fast simulation of transient metal flow and solidification in a narrow channel. Part II. Model validation and parametric study, International Journal of Heat and Mass Transfer. 60, 806-815.
- Rosso, M., 2012. Thixocasting and rheocasting technologies, improvements going on, Journal of Achievements in Materials and Manufacturing Engineering. 54(1), 110-119.
- Sabau, A. S., Porter, W. D., Frankel, J. I., 2004. Conduction and Radiation parameters for analytical models of Differential Scanning Calorimetry instruments, TMS (The Minerals, Metals & Materials Society), 1-10.
- Seo, P.K., Kim, D.U., Kang, C.G., 2006. Effects of die shape and injection conditions proposed with numerical integration design on liquid segregation and mechanical properties in semi-solid die casting process, Journal of Materials Processing Technology. 176, 45-54.
- Seo, P.K., Kim, D.U., Kang, C.G., 2007. The effect of the gate shape on the microstructural characteristic of the grain size of Al–Si alloy in the semi-solid die casting process, Materials Science and Engineering A, 20–30, 445–446.
- Seo, P.K., Kim, H.C., Kang, C.G., 2007. Numerical integration design process to development of suspension parts by semi-solid die casting process, Journal of Materials Processing Technology, 183, 18-32.
- Sigworth, G.K., 1996. Rheological Properties of Metal Alloys in the Semi-Solid State, Can. Metall. Q., 35, 101–22.
- Taghavi, F., Ghassemi, A. 2009. Study on the effects of the length and angle of inclined plate on the thixotropic microstructure of A356 aluminum alloy, Mater. Des., 30, 1762–1767.
- Wei-min, M., Qiu, Z., Da-ping, Z., 2010. Rheo-squeeze casting of semi-solid A356 aluminum alloy slurry, Trans. Nonferrous Met. Soc. China, 20, 1769-1773.
- Xu, C., Zhao, J., Guo, A., Li, H., Dai, G., Zhang, X., 2017. Effects of injection velocity on microstructure, porosity and mechanical properties of a rheo-diecast Al-Zn-Mg-Cu aluminum alloy, Journal of Materials Processing Tech., 249, 167–171.
- Yue-long, B., Wei-min, M., Jun, X., Hong, X., Hua, H., 2008. Numerical simulation on rheo-diecasting mould filling of semi-solid key-shaped component, Nonferrous Met. Soc. China, 18, 682-685.
- Zhang, F., Song, N., Zhang, J., Kang, Y., Zhu, Q., 2013. Numerical simulation on the filling process of rheological die casting and forming defects analysis, Solid State Phenomena, 192-193, 293-298.
- Zhang, F., Hu, X. G., Li, D. Q., He, Y. F., Xu, X. J., Zhu, Q., 2015. Simulation on the Thixocasting Process of the Turbocharger Impellers and Selection of the Viscosity Models, Solid State Phenomena, 217-218, 219-224.
- Zheng, Z. K., Ji, Y. J., Mao, W. M., Yue, R., Liu, Z.Y., 2017. Influence of rheo-diecasting processing parameters on microstructure and mechanical properties of hypereutectic Al-30%Si alloy, Trans. Nonferrous Met. Soc. China, 27, 1264–1272.
9. 著作権:
- この資料は、「Prosenjit Das, Bikash Bhuniya, Sudip K. Samanta, Pradip Dutta」による論文です。「Studies on Die Filling of A356 Al alloy and Development of a Steering Knuckle Component using Rheo Pressure Die Casting System」に基づいています。
- 論文の出典: https://doi.org/10.1016/j.jmatprotec.2019.04.014
この資料は上記の論文に基づいて要約されており、商業目的での無断使用は禁止されています。
Copyright © 2025 CASTMAN. All rights reserved.
要約:
本論文は、A356アルミニウム合金製ステアリングナックルの製造におけるレオ圧力ダイカスト (RPDC) プロセスの最適化に関する包括的な研究を提示する。数値流体力学 (CFD) シミュレーションと実験的検証を通じて、スラリー注入温度 (610°C)、射出速度 (3.0 m/s)、およびダイゲーティング (3ゲートシステム) の最適パラメータが決定された。本研究は、これらの最適化された条件が、従来のダイカスト法と比較して、改善された微細構造均一性 (メジアン結晶粒径24µm、球形度0.88) および向上した機械的特性 (平均マクロ硬度約70 VHN、UTS 219 MPa) を持つ健全な鋳物を生み出すことを実証し、高信頼性軽量自動車部品製造のためのRPDCの可能性を強調している。
研究に関する主要な質疑応答:
本研究は、数値流体力学 (CFD) モデルを開発・検証することにより、A356 Al合金ステアリングナックルを製造するためのレオ圧力ダイカスト (RPDC) プロセスパラメータを最適化することを目的とした。研究は、スラリー注入温度610°C、射出速度3.0 m/s、3ゲートダイ設計を含む最適条件を特定し、実験的に検証することに成功した。得られた部品は、従来のダイカスト法と比較して、平均マクロ硬度70 VHNなど、改善された微細構造均一性と機械的特性を示した。
Q1. A356 Al合金ステアリングナックルのRPDCプロセスに関する本研究の主な目的は何でしたか?
A1. 主な目的は、CFDモデルと実験的検証を用いて、ステアリングナックル部品において望ましい微細構造と機械的特性を達成するための最適なゲーティング配置、注入温度、および射出条件を決定することでした。(出典: 抄録; Studies on Die Filling of A356 Al alloy and Development of a Steering Knuckle Component using Rheo Pressure Die Casting System)
Q2. RPDCシステムのシミュレーションによって特定された主要な最適プロセスパラメータは何でしたか?
A2. シミュレーション結果は、0.15の固相率に対応する610°Cのスラリー注入温度、3.0 m/sの射出チップ速度、および250°Cの予熱温度を持つ3ゲートダイキャビティが、健全なステアリングナックルを製造するための最適条件であることを示しました。(出典: Section 6. Conclusions; Studies on Die Filling of A356 Al alloy and Development of a Steering Knuckle Component using Rheo Pressure Die Casting System)
Q3. RPDC鋳造ステアリングナックルの機械的特性は、従来の方法と比較してどうでしたか?
A3. RPDC鋳造部品は、約70 VHNの平均マクロ硬度を示し、これは従来の高圧ダイカスト (HPDC) 部品と比較して著しく改善されていました。引張特性も、RDC A356 Al合金サンプルについて報告されているものと同等でした。(出典: Section 5.2 Mechanical properties, Section 6. Conclusions; Studies on Die Filling of A356 Al alloy and Development of a Steering Knuckle Component using Rheo Pressure Die Casting System)
Q4. 本研究で開発されたレオロジーモデルの意義は何でしたか?
A4. オストワルド・ド・ワーレのべき乗則に基づいた実験的に決定されたレオロジーモデルは、A356半凝固スラリーのせん断減粘挙動を正確に記述するために開発され、これはダイ充填プロセスのCFDシミュレーションの予測能力にとって極めて重要です。(出典: Section 2.2 Rheology model; Studies on Die Filling of A356 Al alloy and Development of a Steering Knuckle Component using Rheo Pressure Die Casting System)
Q5. 注入温度は、ダイ充填能力と最終部品品質にどのような影響を与えましたか?
A5. 610°Cの注入温度は、完全なダイ充填と均一な固形分分布に適していることが判明しましたが、より低い温度(例:585°C)では不完全な充填と不均一な固相率が生じ、部品開発には不適切でした。(出典: Section 4.1.1 Solid fraction distribution; Studies on Die Filling of A356 Al alloy and Development of a Steering Knuckle Component using Rheo Pressure Die Casting System)
Q6. 冷却スロープで生成されたスラリーは、鋳造前に著しい劣化なしにどのくらいの時間保持できましたか?
A6. 冷却スロープで生成されたスラリーは、部品鋳造前にその微細構造形態の大きな劣化なしに、等温スラリー保持浴内で約14分間保持できることが観察されました。(出典: Section 5. Experimental validation, Section 6. Conclusions; Studies on Die Filling of A356 Al alloy and Development of a Steering Knuckle Component using Rheo Pressure Die Casting System)