本紹介論文は、「Mälardalen University Press Licentiate Theses」によって発行された論文「OPTIMIZATION PRODUCT PARTS IN HIGH PRESSURE DIE CASTING PROCESS」に基づいています。
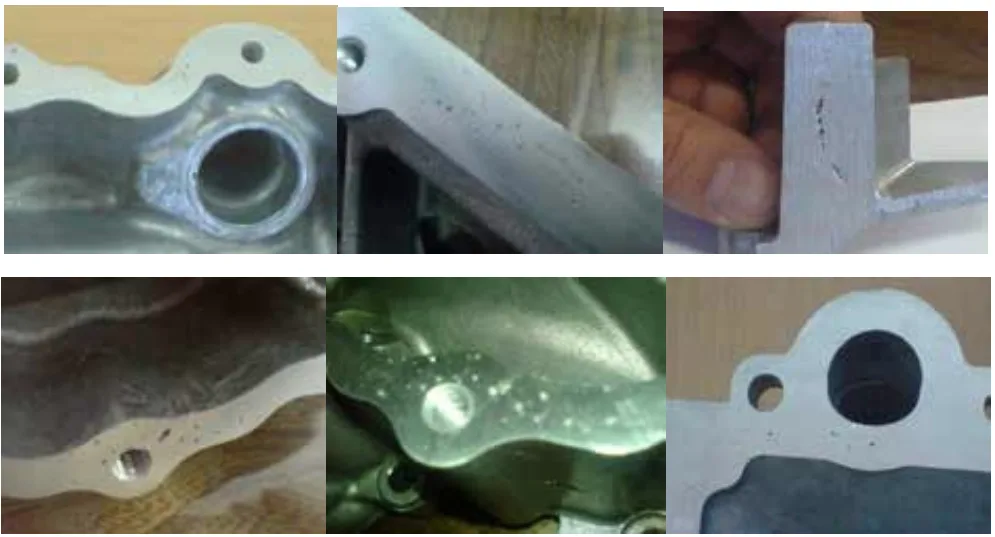
1. 概要:
- タイトル: 高圧ダイカストプロセスにおける製品部品の最適化 (OPTIMIZATION PRODUCT PARTS IN HIGH PRESSURE DIE CASTING PROCESS)
- 著者: Mohammad Sadeghi
- 発行年: 2015
- 発行学術誌/学会: Mälardalen University Press Licentiate Theses, No. 197
- キーワード: 高圧ダイカスト (HPDC)、金型温度最適化、A380アルミニウム合金、数値シミュレーション、実験的観察、欠陥最小化
2. アブストラクト:
本論文は、統計ツールを用いた実験的観察と数値シミュレーションにより、A380合金の高圧ダイカスト(HPDC)における金型温度の最適化について述べるものです。本研究の目的は、これらの欠陥の発生を最小限に抑え、それによって欠陥のない部品の生産を最大化するための最適な金型温度を決定することです。
HPDCでは、溶融金属が高速(アルミニウム合金の場合40-60 m/s)で金型に射出されます。金型温度は、不良部品の発生率に重要な役割を果たします。したがって、非常に複雑な形状を持つ自動車部品(EF7モーターのラダーフレーム)のHPDCにおける溶融金属の流動パターンを検討し、最適な金型温度を決定しました。
生産プロセスにおける欠陥は、表面欠陥、内部欠陥、寸法欠陥の3つのカテゴリーに分類されます。実験で生産されたサンプルは、存在する欠陥に応じて分類されました。
鋳造欠陥に影響を与えるもう1つの重要なパラメータは冷却速度です。金型温度は、初期段階と最終充填位置で測定されました。実験は、150°Cから250°Cの範囲の金型温度で行われました。その結果、初期段階と最終充填位置の間の金型内の溶融金属の温度差は20〜25°Cでした。
回帰、関係、最大値、最小値、相関、ANOVA、T検定、主成分分析(PCA)、記述統計などの統計ツールを使用して、ダイカスト実験からのデータの解釈を容易にしました。
プロセスの挙動を研究し、影響パラメータに関するより良い知識を得て、必要なパラメータを測定するために、いくつかのケーススタディを実行します。収集されたデータは、次の目的で利用されます。
- モデルの設定
- モデルの検証・確認
ProCastソフトウェアを使用して流体の流れと凝固ステップをシミュレーションし、その結果は実験測定によって検証されました。この合金の最適な金型温度は200°C以上であることがわかりました。
実験結果の統計分析により、ラダーフレームのHPDCにおいて、210°Cから215°Cの金型温度範囲内で欠陥が最小化され、良品部品が最大化されることがわかりました。
3. 緒言 (はじめに):
高圧ダイカスト(HPDC)プロセスは、アルミニウム、マグネシウム、銅、亜鉛から部品を製造するために広く使用されている製造方法であり、金型への正確な適合性、良好な機械的特性、低コスト、複雑な形状の部品を製造できる能力などの利点があります。このプロセスは、自動車産業や航空宇宙産業を含む様々な産業で不可欠です。しかし、HPDC部品の品質は、溶湯温度、射出圧力、金型温度、部品の複雑さ、射出速度など、多くのパラメータに影響されます。本研究は、製造された部品の欠陥に対する金型温度の影響を調査することに焦点を当てています。部品の複雑化と最適化の必要性の高まりに伴い、数値解析手法は製造プロセスに関連する物理的問題を解決するための不可欠なツールとなりつつあり、従来の試行錯誤によるアプローチと比較して時間とコストを大幅に削減できます。本論文は、特にダイカストアルミニウム合金とその自動車産業への応用を取り上げ、鋳造形状、製造パラメータ、ダイカストプロセス構成要素間の関係を理解し最適化することで、廃棄物を削減し欠陥を最小限に抑えることを目的としています。
4. 研究の概要:
研究テーマの背景:
高圧ダイカスト(HPDC)は、A380アルミニウムなどの合金を使用し、特に自動車分野で複雑な金属部品を製造するための重要な製造プロセスです。このプロセスでは、溶融金属を高速・高圧で金型に射出します。HPDCはネットシェイプに近い形状での製造や良好な機械的特性といった利点がありますが、最終的な部品品質はプロセスパラメータに非常に敏感です。最適でない条件では欠陥が発生し、コスト増や廃棄物の原因となります。これらのパラメータ、特に金型温度を最適化することは、健全な鋳物を保証するために不可欠です。これらのパラメータ間の複雑な相互作用を理解し最適化するために、数値シミュレーションツールがますます利用されています。
先行研究の状況:
本研究は、HPDCプロセスの物理、凝固理論、および欠陥形成メカニズムに関する既存の知識体系に基づいています。核生成理論(例:古典的ギブスモデル、非古典的モデル)および凝固微細構造の発達に関する確立された理論が、研究の科学的基盤を形成しています。ProCastのような計算ツールを鋳造プロセスにおける流体の流れ、熱伝達、および凝固のシミュレーションに使用することは、十分に開発された分野です。本研究は、これらの確立された原理とツールを適用して、新たに設計された複雑な自動車部品(EF7エンジン用ラダーフレーム)の金型温度を最適化し、欠陥を最小限に抑えるという特定の課題に取り組みます。
研究の目的:
本研究の主な目的は、A380アルミニウム合金の高圧ダイカスト(HPDC)において、欠陥の発生を最小限に抑え、それによって良品部品の生産を最大化するための最適な金型温度を決定することです。具体的な目的は次のとおりです。
- 生産プロセスに影響を与えるパラメータとダイカスト法の設計パラメータを理解すること。
- ダイカスト設計の構成要素、ランナーとオーバーフローの位置、および部品の幾何学的複雑さの間の関係を決定すること。
- 設計パラメータと製造パラメータの関係を調査し、それらを最適化して欠陥と不良部品の数を減らすこと。
核心的研究:
本研究の核心は、HPDCプロセスによって製造されるA380アルミニウム合金自動車部品(EF7モーターのラダーフレーム)の金型温度最適化に関する包括的な調査です。これは、実験的観察と数値シミュレーションの組み合わせによって達成されました。実験は、金型温度(150℃から250℃)と溶湯温度を体系的に変化させながら、欠陥形成を監視することによって行われました。その複雑な形状のために選択されたラダーフレームが試験部品として使用されました。ProCastソフトウェアを使用した数値シミュレーションにより、流体の流れと凝固段階をモデル化し、その結果は実験測定によって検証されました。回帰分析、ANOVA、PCAなどの統計ツールを使用して実験データを分析し、最適なプロセス条件を特定しました。
5. 研究方法:
研究計画:
本研究では、実験と数値シミュレーションを組み合わせたアプローチを採用しました。実験は、工業用HPDC機(IDRA1600)を使用し、A380アルミニウム合金を用いて、EF7モーターの複雑な自動車部品である「ラダーフレーム」を製造する形で行われました。調査した主な変数は金型温度で、150℃から250℃の範囲とし、溶湯温度も監視・制御しました。ProCastソフトウェアを用いて、様々な条件下での金型充填および凝固プロセスをモデル化する数値シミュレーションを実施しました。その後、シミュレーション結果の精度と信頼性を確保するために、実験測定によって検証を行いました。
データ収集・分析方法:
データ収集には、初期段階と最終充填位置での金型温度の測定、およびダイ入口(射出開始時)とダイ出口(射出終了時)での溶湯温度の測定が含まれました。信頼性を確保するために各条件で3回の繰り返し実験を行い、合計800回の実験を実施しました。欠陥部品を特定し、X線検査、三次元測定機(CMM)、金属組織検査、目視検査などの様々な分析手法を用いて欠陥の種類(表面、内部、寸法)を決定しました。
データ分析は、回帰、関係、最大値、最小値、相関、ANOVA、T検定、主成分分析(PCA)、記述統計などの一連の統計ツールを使用して行われました。ProCastソフトウェアは、流体の流れと凝固のシミュレーションに使用され、温度分布、充填パターン、および潜在的な欠陥箇所に関する洞察を提供しました。
研究課題と範囲:
本論文の範囲は、高圧ダイカスト法を用いて、複雑な形状で欠陥を最小限に抑えたA380アルミニウム合金製部品の製造に焦点を当てています。中心的な研究課題は、鋳造欠陥を最小限に抑えるための金型温度の最適化です。本研究は、非常に複雑な形状を持つ特定の自動車部品(ラダーフレーム)の品質に対する金型温度の影響を調査します。本研究は、実験結果をモデル化し、シミュレーション結果を経験的に確認するために、エンジニアリングProCastソフトウェアを使用した数値シミュレーションと実験作業を組み合わせています。また、ランナーやオーバーフローの位置などの設計パラメータと、金型温度や溶湯温度などの製造パラメータとの関係も探求します。
6. 主要な結果:
主要な結果:
本研究は、複雑なラダーフレーム部品において欠陥を最小限に抑え、A380アルミニウム合金のHPDCによる良品部品の生産を最大化するための最適な金型温度範囲を特定することに成功しました。
- この合金の最適な金型温度は200°C以上であることが判明しました。
- 実験結果の統計分析によると、金型温度が210°Cから215°Cの範囲にある場合、欠陥が最小化され、良品部品が最大化されました。したがって、理想的な金型温度範囲は212.5±2.5°Cです。
- 記述統計によると、210°Cの金型温度が95%の信頼水準で最も高い良品率(99.45%)を示しました。
- 分散分析(ANOVA)によると、210°Cの金型温度は最大の分散も示し、良品部品と最小欠陥に対するその有意な効果を実証しました。
- 主成分分析(PCA)はさらに、210°Cの金型温度が部品品質にとって最適であり、試験された温度の中で最も大きな影響を与えることを確認しました。
- 210°Cの金型温度と668°Cから680°Cの注入温度での実験が、金型品質に関して最適であることがわかりました。
- 異なる金型温度では、異なる欠陥タイプが優勢でした。金型温度が200°C未満の場合、タイプ1(表面欠陥)が最も頻繁に発生しましたが、金型温度が200°C以上の場合、タイプ2(内部欠陥)とタイプ3(寸法欠陥)がより頻繁に発生しました。
- ProCastソフトウェアを使用した数値シミュレーションは、巨視的および微視的欠陥の可能性のある位置と流れのパターンを効果的に予測しました。金型内部の3つの穴をなくすなどの変更により、流れのパターンが改善されることが示されました。
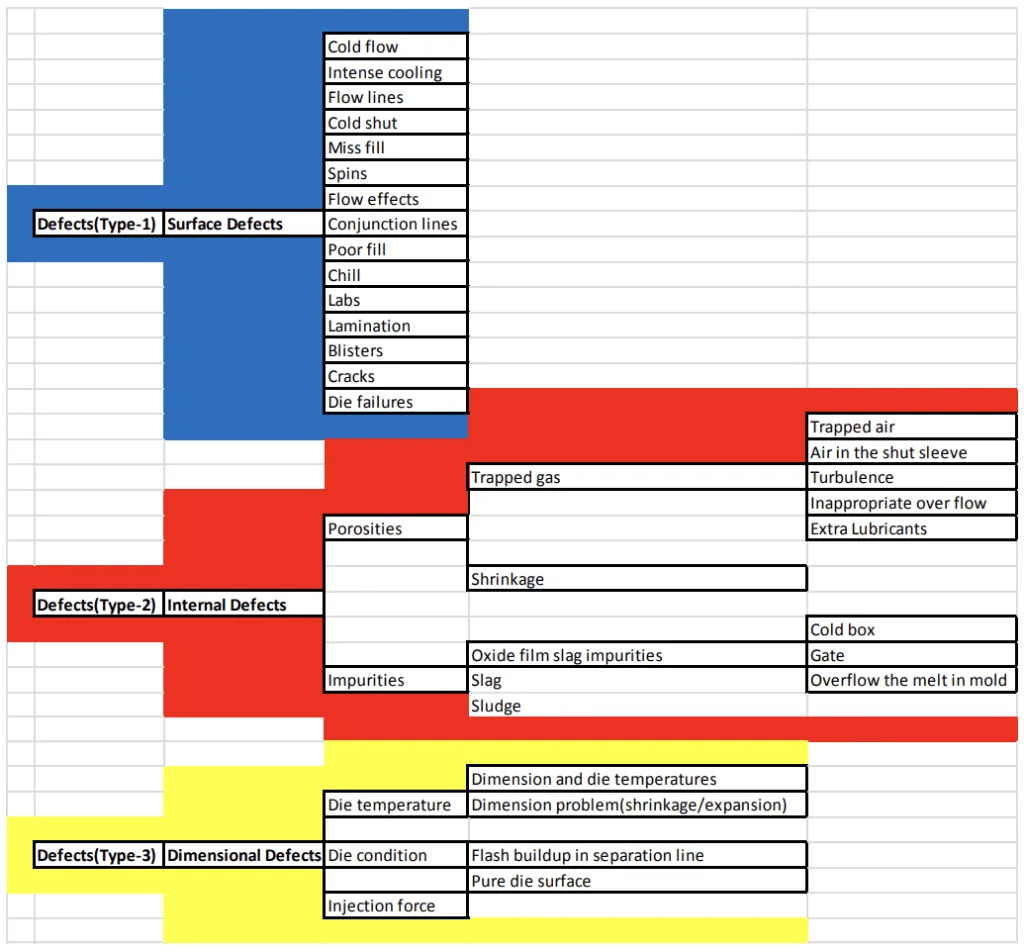
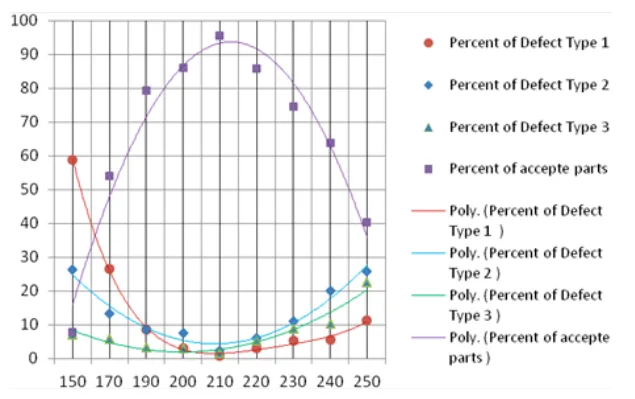
図のリスト:
- FIGURE 2.1: AL-SI BINARY PHASE DIAGRAM
- FIGURE 2.2: GRAIN MICROSTRUCTURE AFTER SOLIDIFICATION OF CASTING PART SCHEMATIC (LEFT), AND MICROSTRUCTURE OF AL-4%CU BILLET (RIGHT) [1]
- FIGURE 2.3: RELATIONSHIP BETWEEN PHASE DIAGRAM WITH DISTRIBUTION COEFFICIENT K, AND DEVELOPMENT OF CONSTITUTIONAL UNDER COOLING [1]
- FIGURE 2.4: FORMATION OF DIFFERENT PHASE BOUNDARY STRUCTURES ACCORDING TO CONSTITUTIONAL UNDER COOLING: PLANAR (LEFT), CELLULAR (MIDDLE), AND DENDRITIC (RIGHT). THERMAL GRADIENT AND MELTING TEMPERATURE (TOP GRAPHS) AND RESULTING MICROSTRUCTURE (BOTTOM GRAPHS)
- FIGURE 2.5: EFFECT OF GL AND VS ON THE SOLIDIFIED MICROSTRUCTURE [1].
- FIGURE 2.6: VARIATION OF INTERNAL ENERGY OF THE SINGLE-PHASE SYSTEM VERSUS RADIUS OF FORMED NUCLEUS
- FIGURE 2.7: CATEGORIES OF DEFECTS OCCURRING IN THE PRODUCTION OF ALUMINUM PARTS THROUGH HPDC.
- FIGURE 2.8: (A) SCHEMATIC OF A SMALL SOLIDIFYING VOLUME ELEMENT OF UNIFORM TEMPERATURE WITHIN WHICH NUCLEATION AND GROWTH CAN OCCUR FROM THE MOLD WALL AND IN BULK;(B) SCHEMATICS OF THE CELLULAR AUTOMATON USED TO PREDICT MICROSTRUCTURE FORMATION IN THE SMALL SOLIDIFYING SPECIMEN SHOWN IN(A).
- FIGURE 2.9: DETAILS OF THE GROWTH OF ACELLULAR AUTOMATON CELL CORRECTION APPLIED TO ADENDRITE TIP
- FIGURE3.1: GEOMETRY OF LADDER FRAME PART
- FIGURE 3.2: THE INFLUENCE GRAPH
- FIGURE 3.3: THE LOADING GRAPH
- FIGURE 3.4: EFFECT OF DIE TEMPERATURE ON THE PERCENTAGE OF ACCEPTED PARTS AND THE THREE DEFECT TYPES OF THE DIE-CASTING PARTS.
- FIGURE 3.5: EFFECT OF DIE TEMPERATURE ON THE PERCENTAGE OF ACCEPTED PARTS AND THE THREE TYPES OF DEFECT IN THE DIE-CASTING PARTS
- FIGURE 3.6: MELT TEMPERATURES AT DIE ENTRANCE AND START INJECTION VERSUS DIE TEMPERATURES.
- FIGURE 3.7: MELT TEMPERATURES AT THE END OF THE DIE AND END INJECTION VERSUS DIE TEMPERATURES.
- FIGURE 3.8: REDUCTION OF MELT TEMPERATURE AT VARIOUS DIE TEMPERATURES AT THE INITIAL AND THE END OF INJECTION
- FIGURE 3.9: GEOMETRY OF LADDER FRAME PRODUCT
- FIGURE 3.10: TEMPERATURE FIELD IN THE PART DURING FILLING AT DIE TEMPERATURE OF 150°C.
- FIGURE 3.11: TEMPERATURE FIELD IN THE PART DURING FILLING AT DIE TEMPERATURE OF 200°C.
- FIGURE 3.12: TEMPERATURE FIELD IN THE PART DURING FILLING AT DIE TEMPERATURE OF 250°C.
- FIGURE 3.13: FILLING AND SOLIDIFICATION PATTERN AT DIE TEMPERATURE 200°C, MELT TEMPERATURE 680°CAND PISTON VELOCITY3 M/S.
- FIGURE 3.14: RESULT OF EXPERIMENT IN SIMILAR CONDITIONS TO SIMULATION
- FIGURE 3.15: OVERFLOWS LOCATIONS IN THE DIE
- FIGURE 3.16: TEMPERATURE DISTRIBUTION AND FILLING SEQUENCE OF THE MOLD AT200°C
- FIGURE 3.17: FINAL SOLIDIFICATION POSITIONS.
- FIGURE 3.18: GAS AND SHRINKAGE DEFECTS IN THE SECTION SURFACE
- FIGURE 3.19: EFFECT OF THE HOLES ON THE FLOW PATTERN AND SOLIDIFICATION.
- FIGURE 3.20: EFFECT OF THE HOLES LOCATED ON THE VELOCITY VECTORS OF THE MELT
7. 結論:
鋳物の形状と金型設計の間には、数値的および統計的手法を用いて最適化できる実証可能な関係があります。研究結果は、金型設計の有益な変更、具体的には3つの穴の除去を示唆しており、これにより、急速な凝固と圧力伝達の欠如による薄肉部の収縮などの問題を防止し、鋳造品質を向上させることができます。
実験により、210°Cの金型温度と668°Cから680°Cの注入温度が金型品質にとって最適であることが確認されました。本研究は、シミュレーションによって予測された流動パターンからオーバーフローの位置を効果的に決定できることを示しました。PCAやANOVAなどの統計ツールの適用は、ダイカスト実験からのデータの分析を大幅に容易にし、より簡単かつ正確にします。
金型温度は、欠陥の数と種類に明確な影響を与えることが示されました。金型温度が200°C未満の場合、タイプ1の欠陥(表面)が最も頻繁に発生しました。逆に、金型温度が200°C以上の場合、タイプ2(内部)およびタイプ3(寸法)の欠陥がより頻繁に発生しました。全体的な欠陥を最小限に抑えるための最適な金型温度範囲は、210〜215°Cであると決定されました。したがって、研究されたA380合金および部品形状の理想的な金型温度範囲は212.5±2.5°Cです。
8. 参考文献:
- [1- W. Kurz and D.J. Fisher. Fundamentals of Solidification. Switzerland: Trans Tech Pub., 4th edition, 1998.]
- [2- J.W. Gibbs, H.A. Bumstead, and W.R. Longley. The Collected Works of J. Willard Gibbs. Longmans,Green and Co, 1928.]
- [3- J.D. Van der Waals. Translation of J. D. van der Waals' "The thermodynamic theory of capillarity under the hypothesis of a continuous variation of density”. Journal of Statistical Physics, 20(2):200–244, 1979]
- [4- J.W. Cahn and J.E. Hilliard. Free energy of a nonuniform system. I. Interfacialfreeenergy. The Journal ofChemicalPhysics, 28:258, 1958.]
- [5- J.W. Cahn. Free energy of a nonuniform system. II. Thermodynamic basis. The Journal of Chemical Physics, 30:1121, 1959.]
- [6- J.W. Cahn and J.E. Hilliard. Free energy of a nonuniform system. III. Nucleation in a twocomponent incompressible fluid. The Journal of Chemical Physics, 31:688, 1959.]
- [7- D.W. Oxtoby and R. Evans. Nonclassical nucleation theory for the gas-liquid transition. The Journal ofChemicalPhysics, 89:7521, 1988.]
- [8- D.W. Oxtoby. Density functional methods in the statistical mechanics of materials. Annual Review of Materials Research, 32(1):39–52, 2002.]
- [9- S.F. Jones, G.M. Evans, and K.P. Galvin. Bubble nucleation from gas cavities a review. Advances in colloid and interface science, 80(1):27–50, 1999.]
- [10- E.N. Harvey, W.D. McElroy, and AH Whiteley. On cavity formation in water. Journal ofAppliedPhysics, 18:162, 1947.]
- [11- R.A. Outlaw, D.T. Peterson, and F.A. Schmidt. Hydrogen partitioning in pure cast aluminum as determined by dynamic evolution rate measurements. Metallurgical and Materials Transactions A, 12(10):1809–1816, 1981.]
- [12- J. Campbell. Castings. Butterworth-Heinemann, 2003.]
- [13- R.B. Dean. The formation of bubbles. Journal ofAppliedPhysics, 15:446, 1944.]
- [14- R. Sasikumar, M.J. Walker, S. Savithri, and S. Sundarraj. Initiation of microporosity from preexisting bubbles: a computational study. Modelling and Simulation in Materials Science and Engineering, 16(3):35009, 2008.]
- [15- D. Dispinar and J. Campbell. Critical assessment of reduced pressure test. Part 1: Porosityphenomena. International Journal ofCastMetals Research, 17(5):280–286, 2004.]
- [16- D. Dispinar and J. Campbell. Use of bifilm index as an assessment of liquid metal quality. International Journal ofCastMetals Research, 19(1):5–17, 2006.]
- [17- Z.W. Chen, M.Z. Jahedi., Die erosion and its effect on soldering formation in high pressure die casting of aluminum alloys,Materials and Design ,1999, vol.20,pp.303-309.]
- [18- P.W. Cleary, J. Ha, M. Prakash, T. Nguyen,∃3D SPH flow predictions and validation for high pressure die casting of automotive components∃,Applied Mathematical Modeling,2006, vol.30, pp. 1406–1427.]
- [19- Laws, K.J., Gun, B., Ferry, M.,∃Effect of die-casting parameters on the production of high quality bulk metallic glass samples∃,Mater. Sci. Eng., 2006, A425, pp.114–120.]
- [20- NADCA product specification standards for die castings/1997]
- [21- http://www.ewp.rpi.edu]
- [22- http://www.wtm.uni-erlangen.de]
- [23- ProCAST 2011.User's Manual]
- [24- M. Rappaz,Ch. A. Gandin, “Probabilistic Modelling of Microstructure Formation in Solidification Processes”, Actametallmater,Vol. 41 . No.2, pp.345-360, 1993]
9. 著作権:
- 本資料は、「Mohammad Sadeghi」氏による論文です。「OPTIMIZATION PRODUCT PARTS IN HIGH PRESSURE DIE CASTING PROCESS」に基づいています。
- 論文の出典: http://www.diva-portal.org/smash/record.jsf?pid=diva2:804075
本資料は上記論文に基づいて要約したものであり、商業目的での無断使用を禁じます。
Copyright © 2025 CASTMAN. All rights reserved.