この紹介資料は、「[韓国鋳造工学会誌]」に掲載された論文「[セラミック溶融コアの微세組織と機械的特性]」に基づいています。
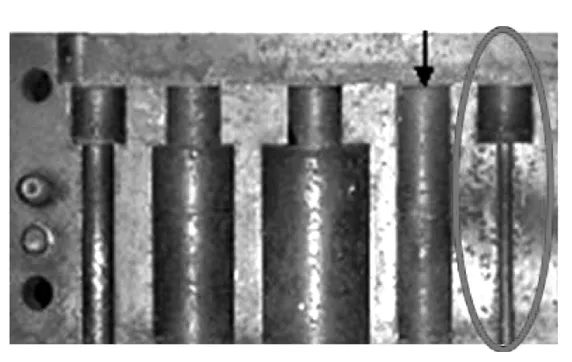
1. 概要:
- タイトル: セラミック溶融コアの微細組織と機械的特性評価 (Evaluation of Microstructure and Mechanical Property of a Novel Ceramic Salt Core)
- 著者: 이준호 (Jun-Ho Lee), 이덕영 (Dock-Young Lee)
- 発行年: 2008
- 掲載学術誌/学会: 韓国鋳造工学会誌 (Journal of the Korean Foundrymen's Society)
- キーワード: Salt core (塩コア), Ceramic (セラミック), Compression strength (圧縮強度), Casting (鋳造).
2. 抄録 (Abstract):
本研究は、セラミック粒子の添加による低融点溶融コアの開発に関するものである。高圧ダイカストまたはスクイズキャスティングプロセスにおいて、複雑な内部形状やアンダーカットを必要とする一体型鋳造部品を製造するために、新しい概念の塩コア(salt core)が導入された。セラミック粒子の添加は微細組織の生成を助け、溶融コアの機械的特性を向上させた。高い圧縮強度を有する新しい溶融コア材料の製造のための新技術が確立された。セラミック粒子の添加は溶融コア材料の機械的特性を向上させた。セラミック粒子の割合と機械的強度との間には、60%まで増加する関係が存在した。
3. 序論 (Introduction):
ダイカスト法では、メタルコア、コーティングされたシェル(shell)、高融点コアなどが使用されている。これらの方法は、溶湯が浸透したり、コアの強度が弱くて破損したりする現象が起こり、鋳造後の抽出が非常に困難であるという欠点がある。新しい溶融コア(fusible core)は、従来のコアとは異なり、融点が270〜520°C程度の低融点化学塩(salt)を基本素材として使用し、セラミック粒子を添加して強度とコア物性を向上させる[1, 2]。これらのコアは、溶融金属が低速/高速で注入されてもコアが破壊されたり、溶融金属がコア内部に浸透したりしないという利点を持つ。これは、熱伝導率が金型材料である特殊鋼の約1/400程度と非常に低いため、コアが熱変形する前に溶融金属の表面凝固層を形成させることができるため、ダイカストを行っても溶融コアの破壊はなく、溶融コアの複雑な形状をそのまま実現できる。
本研究では、鋳造時に必要な溶融コアの特性を評価した。また、溶融コアの機械的特性を評価しようとした。ダイカスト[3-6]と高圧凝固に該当する溶湯鍛造法(Squeeze casting)は、金型に溶融金属を注入した後、油圧装置を利用して機械的な高圧力を溶湯に加え、定められた金型空間を充填させると同時に50〜200 MPaの加圧下で凝固完了させる鋳造プロセスである[7-13]。このように加圧力が作用する状態で、溶融コアが破壊や崩壊することなく強度を維持しなければならない。新たに開発された溶融コア(fusible core)は、従来のコアとは異なり、融点が270〜520℃程度の低融点化学塩(salt)を基本素材として使用する。熱伝達率が金型材料である特殊鋼の約1/400程度と非常に低いため、コアが熱変形する前に溶融金属の表面凝固層を形成させることができる。したがって、ダイカストプロセスでも溶融コアの破壊はなく、溶融コアの複雑な形状をそのまま実現できるという利点がある。しかし、低融点コアの融点が低いため、製品製造時に複雑な内部が凝固前に溶融する現象が見られる可能性がある。本研究は、このような複雑な形状実現の利点を活かし、溶融コアが溶融する欠点を減らす方策をダイカストプロセスに適用し、適切な溶融コアの製造方法と機械的特性を調査しようとした。低融点化学塩にセラミック粒子の含有量を変化させて強度の変化を分析した。
4. 研究の概要 (Summary of the study):
研究テーマの背景 (Background of the research topic):
ダイカストおよびスクイズキャスティングプロセスでは、鋳造部品に複雑な内部形状やアンダーカットを作成するためにコアが必要となることが多い。従来のコア方式は、破損、溶湯浸透、除去困難などの課題に直面している。低融点塩ベースの溶融コアは潜在的な利点を提供するが、高い鋳造圧に耐える十分な機械的強度と、早期溶融を避けるための熱的安定性が必要である。
従来の研究状況 (Status of previous research):
本論文は、セラミック粒子で強化された新しい概念の塩コアを紹介する。一般的なコア技術が存在し[3-13]、溶融塩の特性が知られているが[1]、この研究は特に高圧ダイカストおよびスクイズキャスティング用途向けに機械的特性を改善するために、低融点塩とセラミック添加剤の新しい組み合わせに焦点を当てている。既存のコアの限界と基本的な低融点塩コアの潜在的な問題点から、強化された材料に関するこの調査が必要とされる。
研究の目的 (Purpose of the study):
本研究の目的は、低融点塩ベースにセラミック粒子を添加することにより、新規な溶融コア材料を開発し評価することである。この研究は、これらの新しい溶融コアの製造技術を確立し、高圧ダイカストおよびスクイズキャスティングへの適合性のために機械的特性(特に圧縮強度)を改善し、添加されたセラミック粒子の量と結果として得られるコア強度との関係を理解することを目的とする。
中核研究 (Core study):
研究の中核は、低融点化学塩ベースに様々な重量パーセント(20 wt.%、40 wt.%、50 wt.%、60 wt.%)のセラミック粒子を混合して溶融コアサンプルを製造することであった。これらの異なるコア組成物の機械的特性、特に室温圧縮強度を測定した。さらに、破断したコア表面の微細組織をSEMを用いて分析し、セラミック粒子の添加がコアの内部構造にどのように影響し、その機械的強度と関連しているかを理解した。
5. 研究方法論 (Research Methodology)
研究設計 (Research Design):
本研究では、異なる組成で作られた溶融コアの機械的特性と微細組織を比較するための実験計画を用いた。独立変数は、一定の塩ベースに添加されたセラミック粒子の重量パーセント(0, 20, 40, 50, 60 wt.%)であった。従属変数は、圧縮強度と観察された微細組織であった。
データ収集および分析方法 (Data Collection and Analysis Methods):
- コア製造: 溶融コアは塩とセラミック粉末を用いて準備された。圧縮試験片(直径50 mm、長さ150 mm)のために、4つの組成が作られた:
- 試料1:塩(salt) 200g + セラミック 50g (セラミック 20 wt.%)
- 試料2:塩(salt) 200g + セラミック 133g (セラミック 40 wt.%)
- 試料3:塩(salt) 200g + セラミック 200g (セラミック 50 wt.%)
- 試料4:塩(salt) 200g + セラミック 300g (セラミック 60 wt.%)
塩はステンレスるつぼ(直径300mm、高さ300mm)で370℃で溶融された。所定量のセラミック粉末を加え、混合物を1時間加熱・攪拌して均質性を確保した。溶融した混合物(370℃)を250℃に予熱したSKD61鋼種の金型(Fig. 1)に重力鋳造してコア試料(Fig. 2)を製作した。
- 圧縮試験: 室温圧縮試験は、熱間加工再現試験装置(Thermecmastor_Z Exhaust System, Fuji Electronic Industrial Co., LTD)を用いて実施された。純粋な塩試料と、セラミック含有量が20, 40, 50, 60 wt.%の塩コアについて試験を行った。変形速度は1 mm/minであった。応力-ひずみ曲線を記録し(Fig. 3, Fig. 4, Fig. 5, Fig. 6)、上降伏点(upper yield point)に基づいて圧縮強度(UCS)を決定し、セラミック重量%の関数としてプロットした(Fig. 7)。
- 微細組織分析: 圧縮試験されたコアの破断面を走査型電子顕微鏡(SEM)を用いて微細組織を分析した(Fig. 8, Fig. 9)。
研究テーマと範囲 (Research Topics and Scope):
研究は、様々なセラミック粒子含有量(20, 40, 50, 60 wt.%)を持つ低融点塩ベースの溶融コア製造に焦点を当てた。範囲には、これらのコアの室温圧縮強度測定、SEMによる破断面分析を通じた微細組織変化の観察、コア製造のためのセラミック添加可能限界(70 wt.%まで試験)の決定が含まれた。
6. 主な結果 (Key Results):
主な結果 (Key Results):
- 室温圧縮試験の結果、添加されたセラミック粒子の重量パーセントが20%から60%に増加するにつれて、溶融コアの強度が向上した(Fig. 3 - Fig. 7)。鋳造環境下での荷重下における寸法精度維持に重要と考えられる上降伏点(upper yield point)は、セラミック含有量が高いほど一貫して上昇した。
- SEMを用いた破断面分析(Fig. 8は40%セラミック、Fig. 9は50%セラミック)の結果、セラミック含有量が増加するにつれて、コア材料の微細組織がより微細になった。
- この微細組織の微細化は、塩ベース材料と比較してセラミック粒子の熱伝導率が著しく高いためであると考えられる。この差は、溶融コアの製造(凝固)中の冷却速度を増加させる。
- 結果として得られたより微細で緻密な微細組織が、観察された圧縮強度の増加に寄与した。さらに、セラミック粒子は塩マトリックス内で強化相として機能し、強度を高める複合材料効果を生み出す。
- 最大60 wt.%のセラミック粒子を含むコア試料を成功裏に製造することが可能であった。70 wt.%のセラミックを添加する試みは、混合物の粘性が過度に高くなり、注入によってコア試料を成形することが不可能となった。
図の名称リスト (Figure Name List):
- Fig. 1. Mold for fusible core preparation. (溶融コア準備用金型)
- Fig. 2. Fusible core samples. (溶融コア試料)
- Fig. 3. Stress-strain curve of fusible core; salt-wt20% ceramic. (溶融コアの応力-ひずみ曲線; 塩-20wt%セラミック)
- Fig. 4. Stress-strain curve of fusible core; salt-40wt% ceramic. (溶融コアの応力-ひずみ曲線; 塩-40wt%セラミック)
- Fig. 5. Stress-strain curve of fusible core; salt-50wt% ceramic. (溶融コアの応力-ひずみ曲線; 塩-50wt%セラミック)
- Fig. 6. Stress-strain curve of fusible core; salt-60wt% ceramic. (溶融コアの応力-ひずみ曲線; 塩-60wt%セラミック)
- Fig. 7. Compressive stress of fusible core as a function of ceramic weight. (セラミック重量に応じた溶融コアの圧縮応力)
- Fig. 8. Fractured surface analysis of fusible core; salt-40% ceramic. (溶融コアの破断面分析; 塩-40%セラミック)
- Fig. 9. Fractured surface analysis of fusible core; salt-50% ceramic. (溶融コアの破断面分析; 塩-50%セラミック)
7. 結論 (Conclusion):
ダイカストおよび他の高圧鋳造プロセスで遭遇する外部からの衝撃に耐えるコアの能力を評価するために圧縮試験を実施した。塩に20t, 40t, 50t, 60 wt.%のセラミック含有量を増加させながら圧縮試験を行い、本研究を通じて以下の結論を得ることができた。
- 溶融コアを常温で加圧実験を行い、これを通じて常温強度を分析した結果、セラミック含有量が増加するにつれて強度は増加した。セラミック含有量が20, 40, 60%と増加するたびに圧縮強度が上昇することを確認できた。これは鋳造圧力下での変形に対する抵抗性が向上したことを示している。
- Saltコアの破断面分析(SEM)において、ceramic粒子含有量の増加に伴い組織が微細化した。この現象は、添加したセラミック粉末の熱伝導率が塩材料よりもかなり大きいため、低融点溶融コア製造時の冷却速度が大幅に増加して現れた結果と判断される。また、セラミック材料が緻密に密集して強度の増加にも寄与していることが分かり、セラミック粉末と塩材料間の複合材としての役割により強度が上昇したものと判断される。
8. 参考文献 (References):
- [1] Tatsuhico Ejima, J. of the Korean Inst. of Metals "Thermo-physical Properties of Molten Salts", Vol.25. (1987) 368-377
- [2] J. Kor. Foundrymen's Soc.," Microstructural evolution of electromagnetically stirred Al alloy billet during isothermal reheating at the solid-liquid state", Vol.28.No.3,(2008),129-135
- [3] C. P. Hong, T. Umeda and Y. Kimura, Metall. Trans., "Numerical Models for Solidification: Part 1 & Part 2", 15B, p. 91-101, p. 103-113, (1984)
- [4] K. Ohsasa and T. Takahashi, "Radial Contraction Behavior of Solidifying Shell for Cylindrical Al-3%Si Al-3%Si Alloy Ingot", J. Japan Inst. Metals, 52(12), (1988) 1012-1019,
- [5] S. Engler, D. Boenisch and B. Kohler, "Metal and Mold Wall Movement during Solidification of Cast Iron", AFS Cast Metals Research Journal, 3 (1973) 20-30
- [6] N. Chvorinov, "Theorie der Erstarrung von Gubtucken”, Giesseri, 27 (1940) 177-186 201-208, 222-225
- [7] T. M. Yue, Jour. of Mater. Process. Tech., "Squeeze casting of high-strength aluminium wrought alloy AA7010", 66 (1997) 179-185
- [8] Z.W. Chen, W.R. Thorpe, Mater Sci. and Eng. A, "The effect of squeeze casting pressure and iron content on the impact energy of Al-7Si-0.7Mg alloy", 221 (1996) 143-153
- [9] Fatih ay, S. Can Kurnaz, Mater. & Design, "Hot tensile and fatigue behaviour of zinc-aluminum alloys produced by gravity and squeeze casting", 26 (2005) 479-485
- [10] A Bloyce, J.C Summers, Mater. Sci. and Eng. A, "Static and dynamic properties of squeeze-cast A357-SiC particulate Duralcan metal matrix composite", 135 (1991) 231-263
- [11] M. R. Ghomashchi, K. N. Strafford, Jour. of Mater. Process. Tech., "Factors influencing the production of high integrity aluminium/silicon alloy components by die and squeeze casting processes", 38 (1993) 303-326
- [12] P.V. Evans, R. Keyte, R.A. Ricks, Mater. &Design, "Squeeze casting of aluminium alloys for near net shape manufacture", 14 (1993) 65-67
- [13] M.A. Sava, S. Altinta, Mater. Sci. and Eng. A, "Effects of squeeze casting on the wide freezing range binary alloys", 173 (1993) 227-231
9. 著作権 (Copyright):
- 本資料は、「[이준호 (Jun-Ho Lee), 이덕영 (Dock-Young Lee)]」氏の論文です。「[セラミック溶融コアの微細組織と機械的特性]」論文に基づいています。
- 論文出典: [DOI URL not found]
本資料は上記の論文に基づいて要約されたものであり、商業目的での無断使用を禁じます。
Copyright © 2025 CASTMAN. All rights reserved.