本紹介資料は、「International Journal of Mechanical Engineering」に掲載された論文「Minimise the Nonfilling defect in the high pressure casting process component for an automotive application with metal flow simulation analysis」に基づいています。
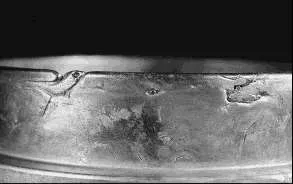
1. 概要:
- タイトル: Minimise the Nonfilling defect in the high pressure casting process component for an automotive application with metal flow simulation analysis (自動車用途向け高圧鋳造プロセス部品における湯回り不良の金属流動シミュレーション解析による最小化)
- 著者: R.Govindarao, Dr.K.Eshwara Prasad (Rted)
- 発行年: 2022
- 掲載学術誌/学会: International Journal of Mechanical Engineering
- キーワード: Nonfilling (湯回り不良、充填不足), Machine parameters (マシンパラメータ), Simulation flow analysis (流動シミュレーション解析)
2. 抄録:
高圧ダイカストプロセスは、あらゆるエンジニアリング用途を解決するための、世界で不可欠な主要鋳造プロセスの一つです。高圧ダイカスト製品は、航空宇宙、自動車、家庭用、農業、その他のエンジニアリング用途など、非常に多くの用途で使用されています。高圧ダイカストプロセスにおける不良率は約7%から10%です。不良率には、表面欠陥および内部欠陥による不合格品が含まれます。表面欠陥は目視可能であり、プロセス稼働中に最大限解決できます。すべての表面欠陥の中で、充填不足(non-filling)は、鋳物のあらゆる構成において最も繰り返し発生する欠陥の一つです。コールドショット、チップオフ、クラック、鋳物破損などの一部の表面欠陥は、プロセス自体で排除できます。しかし、充填不足のような表面欠陥は、すぐには解決できません。これには、マシンパラメータの最適化や金型設計コンセプトのような分析が必要です。
3. 緒言:
高圧ダイカストプロセスでは、高温の溶融金属を閉じた鋼製金型に射出します。鋳物の厚さに応じて、鋳物の凝固のために一定時間(最小6秒~最大15秒)保持する必要があります。凝固後、金型が開き、鋳物が突き出され、エキストラクタが鋳物を回収します。次の操作を行う前に、金型を所望の温度値(240°C)まで冷却する必要があります。そうしないと、鋳物が金型に固着する可能性があります。この目的のために、金型はRO水と混合された特殊な化学クーラントを使用して冷却されます。金型は、鋳物の面積に応じて、スプレーにより数秒間(最小4秒~最大10秒)化学クーラントで冷却されます。その後、次のサイクルが繰り返されます。鋳物は、バリや余分な突出材料を除去するためのさらなる工程に進みます。
4. 研究の概要:
研究テーマの背景:
現在の高圧ダイカストプロセスでは、不合格品が非常に高いコストをもたらしています。不合格率は最大9%に達し、これは組織にとって非常に大きな損失です。これらの不合格品は、充填不足5%、ボディリーク3%、残りが表面欠陥によるものです。表面欠陥の寄与はわずか1%までです。充填不足欠陥は、表面欠陥の一つとしても知られています。一部の表面欠陥は、金属温度、圧力、速度などのプロセスパラメータを変更することによって、プロセス自体で低減できます。1バッチ数量(500個)の不合格品詳細の寄与をパレート分析で示します。提示されたパレート分析によると、充填不足欠陥が全鋳造不合格品の約47%を占めており、最も重要な欠陥となっています。
先行研究の状況:
論文によると、従来の方法では、ダイカスターが機械と金型から欠陥のない新しい鋳物を得るまで、試行錯誤を通じてプロセスパラメータを微調整することが含まれます。この手動アプローチは時間がかかると説明されています。MAGMASOFTのようなシミュレーション方法は存在し、圧力ダイカストを含む様々な鋳造プロセスに広く使用されており、乱流充填や金属温度を分析する機能を提供します。
研究の目的:
本研究は、金属流動シミュレーション解析を用いることにより、自動車部品向け高圧ダイカスト部品における充填不足欠陥を最小化することを目的としています。シミュレーションを使用して金属流動経路を確認し、異なる場所での温度を分析し、鋳物内の欠陥位置を特定し、ランナー設計とマシンパラメータを最適化することで、不良を削減しプロセスを改善することが目的です。
研究の核心:
研究の核心は、MAGMASOFT流動シミュレーションソフトウェアを使用して自動車部品の高圧ダイカストプロセスを分析することでした。主に金属の入口位置とランナー断面積を変えた4つの異なるランナー設計モデルが作成されました。シミュレーションでは、ショットサイクルの3つのフェーズ(S1:低速アプローチ、S2:高速充填、S3:増圧)にわたる溶融金属の金型への乱流充填を分析しました。金属温度、圧力、速度、充填時間、充填率などの主要なパラメータを、様々な場所と段階(モデルごとに18段階を分析)で評価し、4つのランナー設計の性能を比較しました。目標は、充填不足欠陥のリスクを最もよく軽減する設計を特定することでした。シミュレーション結果は、最適な設計(Model-4)に基づいて金型を製造するために使用され、その後、結果を検証するために実験的試行が行われました。
5. 研究方法論
研究設計:
本研究では、シミュレーションに基づく比較研究を行い、その後、実験的検証を行いました。高圧ダイカスト金型用の4つの異なるランナー設計をMAGMASOFTを使用してシミュレーションしました。シミュレーション結果(充填時間、充填率、温度分布)を比較して、充填不足欠陥を最小化するための最適な設計を特定しました。次に、選択された設計(Model-4)に基づいて金型を製造し、実際の不良率を測定してシミュレーション予測を検証するための生産試行を実施しました。
データ収集と分析方法:
データ収集には以下が含まれました:
- 部品図面に基づいて、金型セグメント(コア、キャビティ、ランナー、ゲート、オーバーフロー、チャネル、冷却/加熱ライン)の完全な3Dモデルを作成。
- 鋳物の構成と面積に基づいて機械能力を計算(例:800T、900T)。
- プランジャーチップとチャンバー寸法を含む数学的計算のために3Dモデル寸法を同期。
- シミュレーションソフトウェア(MAGMASOFT)にプロセスパラメータを入力し、シミュレーションを反復実行(低、中、高パラメータ範囲)。
- 精度のためのジオメトリのメッシングとショットサイクルの3つのフェーズの分析を含むシミュレーションを実行。
- 4つのモデルそれぞれについて18段階にわたるシミュレーション出力データを収集(金属温度、圧力、速度、プランジャー移動長、溶融金属流動方向、総充填時間、充填率(単位時間あたりに充填された金属の体積))。
- 4つのモデル間の充填時間と温度分布(特にオーバーフローやチルベントなどの充填終了位置)の比較に焦点を当てたシミュレーション結果の分析。
- 選択されたシミュレーションモデル(Model-4)に従って製造された金型を使用した実験的試行(500個バッチ)を実施。
- パレート分析を使用して、実験的試行から得られた不良データ(特に充填不足欠陥)を収集および分析。
研究トピックと範囲:
本研究は、自動車部品の高圧ダイカスト(HPDC)プロセスに焦点を当てました。主な範囲は、金属流動シミュレーション解析(具体的にはMAGMASOFT)の適用による充填不足欠陥の削減でした。研究には以下が含まれました:
- 溶融金属充填プロセスのシミュレーション。
- 4つの異なるランナー設計の比較。
- 3つのショットフェーズ(S1 - 低速ショット、S2 - 高速ショット/充填、S3 - 増圧)の分析。
- 主要なプロセス指標の評価:充填時間、充填率、金属温度分布、圧力、速度。
- シミュレーション結果に基づく最適なランナー設計の特定。
- 生産バッチにおける欠陥率の測定による選択された設計の実験的検証。
6. 主な結果:
主な結果:
- 初期のパレート分析(Graph 1.0)では、調査対象ケースにおいて充填不足欠陥が鋳造不合格品の47%を占め、最も重要な欠陥であることが示されました。
- 流動シミュレーション解析により、4つのランナー設計(Model 1-4)が比較されました。Model 1と2は、充填時間が長く充填率が低いため、不適切と判断されました。
- Model 3は、4つのモデルの中で最も短い充填時間を示しました(Graph 2.0)。しかし、Model 4と比較して、オーバーフローおよびチルベント領域での金属温度が低い(592°C - 615°C)ことが示されました。
- Model 4は、Model 3とほぼ同等の充填時間でしたが、チルベントおよびオーバーフロー領域でより高い金属温度を維持しました。これらの領域での高温は、隠れたガスの排出を促進し、ブローホールや収縮気孔などの欠陥の可能性を低減するのに有利です。Model 4はまた、他のモデルと比較してより高い充填率を示しました(Graph 3.0)。
- シミュレーション結果に基づき、Model 4が金型製造に最も適していると選択されました。
- Model 4に従って設計された金型を使用して実施された実験的試行では、充填不足欠陥率が初期の6.0%から1.60%へと大幅に減少したことが実証されました(Graph 5.0)。検証バッチの不良データをGraph 4.0に示します。
- 本研究は、シミュレーションがランナー設計とプロセスパラメータを最適化し、充填不足欠陥を効果的に削減し、時間のかかる手動の試行錯誤方法への依存を減らすための貴重なツールであると結論付けました。
図表リスト:
- Graph 1.0 Diecasting defects Pareto analysis (ダイカスト欠陥パレート分析)
- Fig: 1.0 Nonfilling defect (充填不足欠陥)
- Fig: 2.0 The runner design models in four types for the simulation model (シミュレーションモデル用の4タイプのランナー設計モデル)
- Fig:3.0 Metal flow during Firsr phase (第一フェーズ中の金属流動)
- Fig 4.0 Metal flow during second phase (第二フェーズ中の金属流動)
- Fig 5.0 Metal flow during third phase (第三フェーズ中の金属流動)
- Graph 2.0 The filling time in each model for each cycle in Second phase condition (第二フェーズ条件における各サイクル、各モデルの充填時間)
- Graph 3.0 Fill ratios of the all simulation models (全シミュレーションモデルの充填率)
- Graph:4.0 Non filling rejection data (充填不足不良データ)
- Graph 5.0 Initial nonfilling and final nonfilling (初期および最終の充填不足)
7. 結論:
シミュレーションモデルは、すべてのダイカスト産業に適用可能であり、不合格品による廃棄物の削減がシミュレーションパッケージのコストを相殺できるため、大幅なコスト削減の可能性を提供します。高圧ダイカスト設計におけるシミュレーションは非常に効果的であり、鋼鋳造シミュレーションよりも効果的である可能性があり、高品質の鋳物の生産を可能にします。シミュレーションソフトウェアは100%完璧な結果をもたらさないかもしれませんが、金型メーカーに重要な情報を提供し、大きな間違いを避けるのに役立ちます。時間、コスト、品質の改善を達成するために、あらゆる新規プロジェクトにおいて金型流動シミュレーションを必要な活動として検討することが推奨されます。新規プロジェクトでシミュレーションモデルを利用することは、時間と費用の節約につながり、不合格品や機械の故障による無駄を排除し、最終的に顧客満足度を向上させることができます。
8. 参考文献:
- [1] Proceedings of the NADCA, “Diecasting defects and design of experiments”, WG. Cleveland, USA Year -1993, Chapter-2 Page: 13-14
- [2] Edward J,Vinarcik, “High Integrity Die-casting processes", Year- 2003.Page: 134-136.
- [3] Genick, Bar-Meir,Minneapolis, “Fundamentals of Die Casting Design", Version: 0.1.2 April 1, 2009, Chapter-1, Page 8-9.
- [4] Hyuk-jae kwon, Hong-kyu Kown, “Computer aided engineering (CAE) simulation for the design optimisation of gate system on high pressure diecasting process (HPDC)”, Elsevier 2018 Page: 149-152
- [5] A J Norwood, P M Dickens*, "Surface temperature of tools during the high-pressure die casting of aluminium", Wolfsan School of Mechanical and Manufacturing Engineering, Loughborough University,UK DOI: 10.1243/09544054JEM745. Year-Aug-2007, Page-1659
- [6] Emil Ragan, Marta Kollarova, "Calculation of Transient Haracterostics in Mould cavity, International journal of Engineering", Tome IX (Year 2011). Fascicule 3. ISSN 1584 – 2673 Page: 1-2.
- [7] Hanxue,chaos shen, chengwang,Hui xui, Direct “Observation of filling Process and Porosity Prediction in High Pressure" Diecasting, Journal name: Materials MPDI 2nd April-2009. Page: 2-9
- [8] M. T. Alonso Rasgado, K. Davey, L. D. Clark and S. Hinduja “Simplified Thermal Stress Analysis "- Department of Mechanical, Aerospace and Manufacturing Engineering UMIST, Manchester, 12TH INTERNATIONAL SCINETIFIC CONFERENCE. Year-2003, Page: 1-2.
- [9] G-Bar Meir, Minnesota The mathematical “Theory of PQ² Diagram", Supercomputing Institute. University of MINNESOTA USA, USMI 99/40 MARCH-1999. Page- 5-6
- [10] John wronowicz, Mike Cox, RexFish,” PQ²- EC-700", July 1998. Page 1-29
9. 著作権:
- 本資料は「R.Govindarao and Dr.K.Eshwara Prasad (Rted)」による論文です。「Minimise the Nonfilling defect in the high pressure casting process component for an automotive application with metal flow simulation analysis」に基づいています。
- 論文の出典: [論文中にDOI URLの記載なし]
本資料は上記の論文に基づいて要約されており、商業目的での無断使用は禁じられています。
Copyright © 2025 CASTMAN. All rights reserved.