本紹介論文は、「Jönköping University, School of Engineering, Dissertation Series No. 084」によって発行された「The Effect of Microstructural Features, Defects and Surface Quality on the Fatigue Performance in Al-Si-Mg Cast Alloys」論文に基づいています。
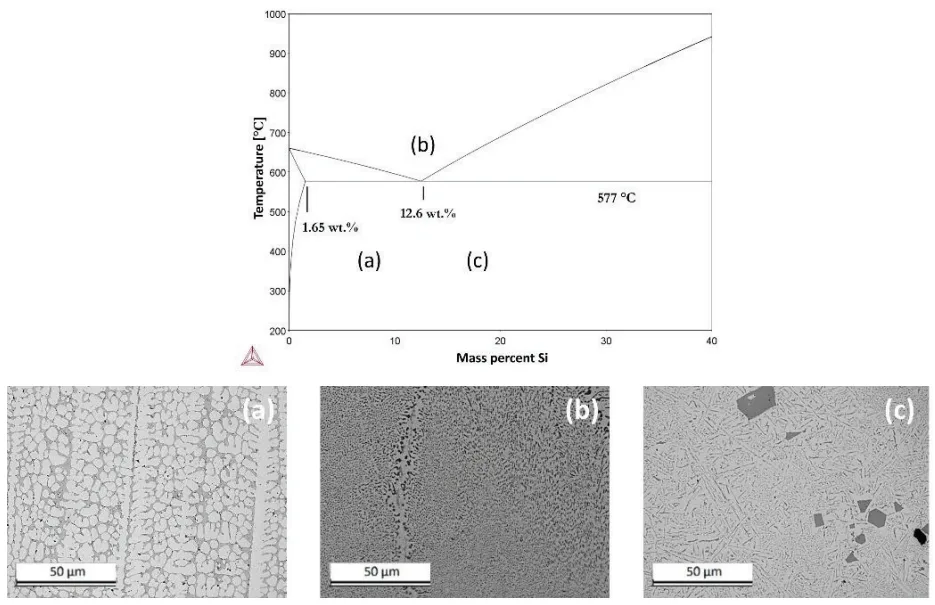
1. 概要:
- タイトル: 組織特徴、欠陥および表面品質がAl-Si-Mg鋳造合金の疲労性能に及ぼす影響 (The Effect of Microstructural Features, Defects and Surface Quality on the Fatigue Performance in Al-Si-Mg Cast Alloys)
- 著者: Toni Bogdanoff
- 発行年: 2023
- 発行ジャーナル/学会: Jönköping University, School of Engineering, Dissertation Series No. 084
- キーワード: Al-Si-Mg鋳造合金, 疲労性能, 組織特徴, 欠陥, 表面品質, 溶湯品質, 銅添加, 酸化介在物(bifilms), HIP, 熱処理, アルミニウム鋳物.
2. 抄録:
地球温暖化により、産業界は二酸化炭素(CO2)排出量を削減するために、より軽量な部品を製造する必要に迫られています。これを達成するための有望な候補として、アルミニウム-シリコン(Al-Si)鋳造合金があり、高い重量対強度比、優れた耐食性、良好な鋳造性を提供します。しかし、これらの合金の機械的特性のばらつきを理解することは、重要な用途向けの高性能部品を製造する上で不可欠です。欠陥や酸化物は、機械的特性に悪影響を与えるため、疲労用途において鋳造部品が不合格となる主な理由です。
Al-Si鋳物におけるα-アルミニウム素地、Al-Si共晶、表面粗さ、気孔、水素含有量、酸化物、金属間化合物などのパラメータと疲労性能との相関関係に関する包括的な理解は、まだ達成されていません。
本論文で提示された研究では、最先端の実験技術を用いて、周期的荷重下でのAl-Si-Mg鋳造合金の機械的特性およびき裂発生・進展挙動を調査しました。走査型電子顕微鏡(SEM)と電子後方散乱回折(EBSD)、デジタル画像相関法(DIC)、集束イオンビーム(FIB)加工を組み合わせたその場(In-situ)周期的試験を実施しました。これらの技術により、水素含有量、表面粗さ、酸化物、金属間化合物相を含む、疲労性能に影響を与えるパラメータに関する包括的な研究が可能になりました。具体的には、溶湯品質、銅(Cu)含有量、酸化介在物(oxide bifilms)、表面品質、および気孔率の影響を調査しました。
熱処理されたAl-Si合金におけるCu濃度の増加は、金属間化合物相の量を増加させ、き裂挙動に影響を与えました。さらに、高ひずみ領域から遠く離れた領域であっても、き裂発生サイトで酸化介在物が検出されました。Siリッチおよび鉄(Fe)リッチな金属間化合物が、これらの介在物上に析出していることが観察されました。これらの酸化物は非常に小さいため、一般的に非破壊検査では検出されませんが、比較的低い引張応力で開口するように見えるため、機械的特性に影響を与えます。最後に、Al-Si合金の鋳肌(casting skins)は、疲労性能を向上させるという点で興味深い効果を示し、そのような合金に対する表面研磨の悪影響を浮き彫りにしました。
3. 緒言:
温室効果ガス、特にCO2の排出削減は世界的な主要な焦点であり、自動車などの産業においてアルミニウムのような軽量材料の使用を推進しています[1]。アルミニウム-シリコン(Al-Si)鋳造合金は、高い強度対重量比、費用対効果、耐食性、鋳造性により、主要な候補です[2, 3]。リサイクルアルミニウムの使用が増加しており、一次生産と比較して大幅なエネルギー節約を提供します[4-6]。純アルミニウムは強度が限られていますが、特にSi、Cu、Mgとの合金化は、固溶強化および析出強化を通じて機械的特性を向上させます[7-12]。しかし、鋳造アルミニウム部品の高サイクル疲労(HCF)性能は依然として課題であり、疲労は全破壊の約90%を占めます[13]。酸化膜(bifilms)や気孔などの欠陥は、疲労寿命を大幅に低下させます[14-17]。しばしば部品の潜在的な疲労寿命のわずか1%に制限します[17]。気孔のような一部の欠陥は検出できますが[19]、酸化介在物のような他の欠陥は破壊が発生するまで隠れたままであることが多いです[20, 21]。粗さを含む表面状態も、疲労発生に決定的な影響を与えます[16]。機械加工された試験片に対する標準的な実験室疲労試験は、鋳肌(casting skins)を持つ実際の部品の挙動を完全には表していない可能性があります[22]。したがって、組織特徴、欠陥、および表面品質が、鋳造Al-Si合金の機械的性能、特に疲労にどのように影響するかについてのより良い理解は、要求の厳しい用途向けに部品を最適化するために不可欠です。
4. 研究の概要:
研究トピックの背景:
CO2排出削減のための軽量部品の必要性は、様々な産業、特に自動車産業においてAl-Si鋳造合金の使用を推進しています[1, 2]。これらの合金は、高い強度対重量比や良好な鋳造性といった有利な特性を提供します[3]。しかし、特に疲労が重要な部品への適用は、固有の組織特徴や欠陥によってしばしば制限されます。
先行研究の状況:
疲労破壊は、鋳造Al部品における主要な課題です[13]。気孔や酸化介在物のような欠陥、および表面粗さは、疲労性能を著しく低下させることが知られています[14-17, 22]。多くの研究が存在しますが、α-アルミニウム素地、Al-Si共晶、様々な欠陥(気孔、酸化物)、金属間化合物相、水素含有量、および表面粗さ間の複雑な相互作用が疲労寿命に及ぼす影響に関する包括的な理解はまだ不足しています[24]。特に、表面粗さや溶湯状態から生じる欠陥の役割に関しては、文献中に矛盾する結果やギャップが存在します[24]。
研究の目的:
本研究の主な目的は、様々な組織特徴、欠陥(酸化物/介在物、気孔を含む)、溶湯品質パラメータ(水素含有量)、合金添加物(特に銅)、および表面品質(粗さ、鋳肌)が、Al-Si-Mg系鋳造合金の機械的特性、特に疲労性能(き裂発生および進展)に及ぼす影響を調査し、理解することでした[25, 28]。目標は、高性能用途向けにこれらの合金を最適化し、生産におけるエネルギー消費を潜在的に削減するための知識を提供することでした。
コア研究:
本研究は、Al-Si-MgおよびAl-Si-Mg-Cu鋳造合金の疲労性能に影響を与えるいくつかの主要な側面に焦点を当てました:
- 溶湯品質: 鋳造工場での溶湯処理および取り扱い(例:回転式脱ガス)が最終的な機械的特性に及ぼす影響を評価し、RPTや引張試験などの技術を用いて、目に見える(気孔)および隠れた(介在物)損傷を明らかにします(補遺I、II)。
- 銅の役割: 様々なCu含有量(0~3 wt.%)が、鋳放しおよび熱処理状態における疲労き裂の発生および進展メカニズムにどのように影響するかを調査し、これを組織(金属間化合物相 例:Q相、θ相)および素地特性の変化と関連付けます(補遺IV、V)。
- 隠れた損傷(酸化介在物): 溶湯状態から生じる固有の酸化介在物(しばしば「隠れた損傷」と呼ばれる)の性質と、それが局所的なひずみ集中および破壊挙動に及ぼす影響を、DIC、SEM、FIBトモグラフィ、およびSTEM-EDSを用いて特性評価します。HIPがこれらの欠陥を軽減する役割を調査します(補遺III、VI、VII)。
- 表面品質と欠陥サイズ: 表面状態(鋳肌 対 機械加工/研磨面)と内部欠陥特性(水素含有量に影響される気孔サイズ分布)の複合的な影響が、Al-Si-Cu-Mg鋳物の疲労寿命に及ぼす影響を評価します(補遺VIII)。
5. 研究方法論
研究デザイン:
本研究は、実証主義的視点と演繹的推論に基づく実験的アプローチを採用しました[132, 133]。実験は、管理された条件下での実験室規模と、実際の工業的鋳造現場(HPDCおよび砂型鋳造)の両方で実施されました。適用可能な場合は標準化された試験手順(ISO、ASTM)に従い、必要に応じて修正が記録されました[25]。設計は、独立変数(例:Cu含有量、表面状態、水素レベル、処理ステップ)が従属変数(機械的特性、疲労寿命、き裂挙動)に及ぼす影響を分離して研究することを目的としました[26, 27]。
データ収集および分析方法:
幅広い技術が利用されました:
- 材料準備: HPDC、砂型鋳造(コーティング/非コーティング鋳型)、および方向性凝固(ブリッジマン炉)による鋳造[29-33]。鋳造後処理には、熱間等方圧加圧(HIP)および様々なT6類似熱処理サイクル(溶体化処理、焼入れ、時効処理)が含まれました[38, 50]。
- 溶湯品質評価: 減圧凝固試験(RPT)、HYCAL水素分析、化学組成のための発光分光分析(OES)、らせん流動性試験、密度測定(アルキメデス原理)[35, 45-49]。
- 組織キャラクタリゼーション: 光学顕微鏡(OM)、エネルギー分散型X線分光法(EDS)付き走査型電子顕微鏡(SEM)、波長分散型X線分光法(WDS)、結晶粒径/方位のための電子後方散乱回折(EBSD)、断面観察、3Dトモグラフィ、および走査透過電子顕微鏡(STEM)試料作製のための集束イオンビーム(FIB)加工[39-41]。定量分析には、SDAS、結晶粒径、粒子サイズ/分布(例:3NN距離)、相分率、および欠陥キャラクタリゼーションが含まれました。
- 機械的試験: ISO 6892-1に準拠した引張試験(ST, σY, eF)、階段法(ISO 12107)を用いた軸方向疲労試験(R=-1, 50 Hz)およびS-N曲線生成のための疲労試験[43]。
- き裂発生/進展研究: SEM内での小型コンパクトテンション試験片を用いたその場(In-situ)周期的疲労試験、MatchIDソフトウェアを用いたデジタル画像相関法(DIC)(マイクロスケール用2D、マクロスケール用3DステレオDIC)によるひずみ場(フォン・ミーゼスひずみ)マッピング[41, 43-44, 53-56]。
- 欠陥分析: 計算機トモグラフィー(CT)スキャン、SEMを用いた破面分析(フラクトグラフィ)[62, 71]。
- 統計分析: 伸び(eF)、品質指数(QT)、疲労寿命(Nf)のワイブル分布分析、気孔サイズ(deq)の対数正規分布分析、バスキン則パラメータ推定、アンダーソン-ダーリング適合度検定、線形回帰[59, 64, 91, 97, 102, 104, 106]。
研究トピックと範囲:
本研究は、以下の4つの主要な問い(RQ1-RQ4)に取り組みました:
- RQ1: 鋳造Al-Si部品の機械的特性、特にリサイクル合金を使用した場合の、生産プロセス(インゴットから最終部品まで、溶湯処理および脱ガスを含む)の影響。HPDCにおけるEN-AC 46000の研究。
- RQ2: 鋳放しおよび熱処理されたAl-Si-Mg合金における、Cu添加(0-3 wt.%)が疲労き裂の発生および進展に及ぼす影響。ブリッジマン炉で鋳造された改質Al7SiMgの研究。
- RQ3: 溶湯状態から生じる隠れた損傷(酸化介在物)の同定、キャラクタリゼーション、および機械的特性への影響。EN-AB 42000(砂型鋳造)、EN-AC 46000(HPDC)、C355(ブリッジマン)の研究。HIP効果の調査。
- RQ4: 表面粗さ(鋳肌 対 機械加工/研磨面)と内部欠陥(水素に関連する気孔)の複合的な影響が、Al-Si鋳物の疲労性能に及ぼす影響。砂型鋳造されたAl7Si3CuMg合金の研究。
6. 主要な結果:
主要な結果:
- 溶湯品質と脱ガス: 溶湯品質の評価にはRPT以上のものが必要です。引張試験、特にワイブル統計で分析された伸び(eF)は、溶湯処理(移送ステップ)による「隠れた」巻き込み損傷を明らかにします[補遺I]。研究された工業的事例(EN-AC 46000)における回転式脱ガスは、RPT試験片の目に見える気孔を減少させましたが、効果的な除去なしに既存の粗大な介在物をより微細なものに分解することにより、最終鋳物の実際の機械的特性(eF, QT)を改善せず、潜在的に悪化させました[補遺I, II]。脱ガスは、非脱ガス試験片で観察されたワイブル混合分布を除去しましたが、単一分布をより低い品質側にシフトさせました[補遺II]。
- 銅の影響: Al7SiMg合金におけるCu含有量(0~3.2 wt.%)の増加は、鋳放しおよび熱処理状態の両方で降伏強度(σY)および引張強度(ST)を増加させましたが、特に脆性なCuリッチ金属間化合物相(Q-Al5Mg8Cu2Si6, θ-Al2Cu)により、鋳放し状態で延性(eF)を著しく減少させました[補遺IV, V]。熱処理は強度をさらに向上させ、鋳放し状態と比較して延性の低下を緩和しました。き裂発生は、鋳放し状態ではスリップバンド/Si粒子(低Cu)から共晶領域/Cuリッチ相(高Cu)へと変化しました。熱処理合金では、き裂発生は一次デンドライト(低Cu)で起こり、デンドライト間領域および結晶粒界(高Cu)へと変化しました。き裂進展経路は、Cu含有量および素地強化に伴い、より蛇行し、デンドライト横断からデンドライト間/粒界へと変化しました。より高いCu含有量は、特に熱処理条件下で、疲労中の二次き裂を増加させました[補遺V, VII]。
- 隠れた損傷(酸化介在物): 溶湯処理および鋳造中に形成される酸化介在物は、重要な「隠れた」欠陥として作用します。DICは、幾何学的な応力集中部から遠く離れていても、これらの介在物に関連する局所的なひずみ集中を明らかにしました[補遺VI]。FIB/STEM-EDS分析により、これらのき裂にはアルミニウム酸化物層が含まれており、荷重下で開口した既存の介在物であることが確認されました[補遺VI, VII]。これらの介在物は、金属間化合物相(例:Al5FeSi)およびSi粒子の核生成サイトとして機能します[補遺VII]。HIPはガス気孔を効果的に閉じましたが、これらの酸化介在物を完全に治癒または除去することはできず、その後の疲労荷重中に依然として開口する可能性がありました[補遺III, VII]。鋳物で観察される損傷は、巻き込み損傷(液相からの介在物)と機械的損傷(使用荷重による)とを区別する必要があります[補遺VII]。
- 表面品質と気孔率: 一般的な仮定とは対照的に、砂型鋳造Al-Si-Cu-Mg合金の場合、鋳肌の存在は、機械加工および研磨(PS)表面と比較して疲労寿命を著しく改善しました[補遺VIII]。研磨は鋳肌を除去し、表面下の欠陥(気孔/介在物)を直接表面に露出させるため、き裂発生段階を短縮または排除し、疲労寿命を大幅に低下させました。疲労破壊は、鋳放し試験片では表面下の欠陥(鋳肌近くの気孔/不完全性)から開始されましたが、研磨試験片では表面に露出した欠陥から直接開始されました。水素含有量の増加は、より大きな気孔とより高い気孔率をもたらし、特に研磨試験片の場合、より広い疲労寿命分布(低いワイブル係数M)をもたらしましたが、粗い鋳放し表面の平均疲労寿命への影響は少なかったです。表面品質と気孔サイズ分布間の相互作用は複雑です。既存の疲労寿命予測モデル(例:Juvinall)は、鋳肌の有益な効果を考慮するために修正が必要です[補遺VIII]。
図のリスト:
- Figure 1. Al-Si phase diagrams: a) hypoeutectic, b) eutectic, and c) hypereutectic microstructures.
- Figure 3. Entrainment of surface oxides [79].
- Figure 4. Hydrogen solubility in pure aluminium and aluminium alloys [42].
- Figure 5. a) Impurity-induced twinning [97]; b) restricted TPRE growth [98].
- Figure 6. The stress-strain curve of an as-cast Al7SiMg alloy, with emphasis placed on the essential parameters used in the research presented in this thesis.
- Figure 7. Overview of the research methodology.
- Figure 8. a) Cylindrical rods (length 150 mm and diameter 9 mm). b) schematic illustration of the Bridgman furnace; c) stair casting geometry (dimensions in mm).
- Figure 9. The geometry of the casting in the sand mould.
- Figure 10. The production process used in the HPDC plant.
- Figure 11. a) Schematic diagram of the tensile testing sample; b) a sample exposed to the HIP process and heat treatment.
- Figure 12. a) Dimensions of the compact-tension sample in mm; b) miniature stage for in-situ cyclic testing; c) FOV of the compact-tension sample.
- Figure 13. Tensile- and fatigue-testing sample geometry.
- Figure 14. The cross-sections of the RPT samples at different stages of production.
- Figure 15. The Weibull distributions of elongation in the different stages of production.
- Figure 16. Cross-sections of RPT samples taken at different stages of the production process, with and without degassing.
- Figure 17. The Weibull distributions of the structural quality of the two production routes.
- Figure 18. (a) Alloy Cu 0 in as-cast condition, b) Alloy Cu 0 in heat-condition.
- Figure 19. Three-nearest-neighbour (3NN) distances between particles: a) Si particles; b) Q-phases. The error bars represent the standard deviation.
- Figure 20. Beginning of crack initiation in as-cast condition: a) Alloy Cu 0; b) Alloy Cu 1.5.
- Figure 21. Crack propagation in all heat-treated alloys, imaged using a combination of EBSD and DIC: a–b) Alloy Cu 0; c–d) Alloy Cu 0.5; e–f) Alloy Cu 1.5; g–h) Alloy Cu 3.0. The yellow dashed lines represent grain boundaries, superimposed from EBSD, and the red arrows point to the initiation sites. The colour bar represents the von Mises equivalent strain, and is valid for all frames.
- Figure 22. Crack propagation in all as-cast alloys, imaged using a combination of EBSD and DIC: a) Alloy Cu 0; b) Alloy Cu 0.5; c) Alloy Cu 1.5; d) Alloy Cu 3.0. The yellow dashed lines represent grain boundaries, superimposed from EBSD. The final fracture, shown as a black dashed line in the picture, was manually added. The colour bar represents the von Mises equivalent strain.
- Figure 23. Development of slip bands during the cycling testing of alloys with different Cu contents: a) Alloy Cu 0, at the crack edge; b) Alloy Cu 0, 150 µm from the crack edge; c) Alloy Cu 1.5, at the crack edge, d) Alloy Cu 1.5, 150 µm from the crack edge.
- Figure 24. Development of secondary cracks (indicated by arrows) in heat-treated Alloy Cu 3.0 after a) 825 cycles; b) 925 cycles. c–d) magnified micrographs of the secondary cracks visible in b).
- Figure 25. FIB milling was used to investigate the material around the crack in heat-treated alloys. a) Alloy Cu 0, test stopped at 1253 cycles; b) and c) show related sections. d) Alloy Cu 3.0, test stopped at 640 cycles; e) and f) show related sections. The black arrows point to Fe-rich phases, the white arrows point to superficial cracks, and the red arrows point to the crack coming from underneath.
- Figure 26. Three-dimensional reconstruction of the FIB sections of cracks in heat-treated alloys. a) FIB section of Alloy Cu 0, test stopped at 1253 cycles, and b) three-dimensional reconstruction. c) FIB section of Alloy 3.0 Cu, test stopped at 640 cycles, and d) three-dimensional reconstruction. The red arrows show the cracks, and the blue arrows indicate the intermetallic phases.
- Figure 27. Microstructures of Al7SiMg alloy: (a) as-cast condition, 16 mm thickness, (b) as-cast condition, 32 mm thickness. The red squares highlight a magnified area. The red ovals highlight the inhomogeneous microstructure in the 32 mm-thick sample.
- Figure 28. Microstructures of the Al7SiMg alloy: (a) heat-treated condition, 16 mm thickness; (b) heat-treated condition, 32 mm thickness. The red squares highlight a magnified area.
- Figure 29. CT scan of the material in as-cast condition, showing the porosities (blue); having been HIPped (red); and having been heat-treated (green). a) 16 mm, b) 32 mm.
- Figure 30. Crack propagation in the HIPped and heat-treated conditions. a–c) the 16 mm sample, showing initiation and propagation; d–f) the 32 mm sample, showing cracks and evaluation of crack propagation.
- Figure 31. Full-field distributions of von Mises equivalent strain in a sample A under a load of (a) 11.9 kN and (b) 15.4 kN.
- Figure 32. (a) Sample A after fracture. The red circle indicates the location of the strain concentration seen in Figure 31b. (b), which is an SEM image of the oxide film found in the strain-concentration area. (c) Increased magnification of the oxide draped over the microstructure.
- Figure 33. Stress-strain curve throughout tensile testing of sample A for both the strain concentration and a symmetry reference point.
- Figure 34. (a) DIC strain field of sample B under a load of 15.9 kN just before fracture. (b) Close-up image of the upper strain concentration with an optical microscope after failure. (c) Visible crack on the sample surface after paint removal in the SEM.
- Figure 35. (a) Location of the lamella in front of the crack. (b) Extraction of the lamella. (c) STEM-EDS map of oxygen distribution in the lamella, which revealed the oxide film inside the crack.
- Figure 36. a) The FOV (300 × 300 μm) had no visible cracks after 100 cycles. b) cracks outside the FOV after 100 cycles.
- Figure 37. a) After 200 cycles, the cracks showed no continued propagation. (b) A crack was initiated at the notch after 550 cycles.
- Figure 38. a) Two cracked phases perpendicular to the loading direction. (b) BSE image of the trenching of the lamella. (c) BSE image of the 1.2 μm lamella before lifting.
- Figure 39. a) BSE, b) STEM, c) HADF, d) DF images of the lamella. The arrow points to the observed line around the open crack.
- Figure 40. a) SEM image of a crack. b) STEM-EDS image of the same crack, showing the intermetallic phases around it.
- Figure 41. a) STEM-EDS measurement of oxygen in the crack. b) EDS line scan results from points 1 to 51.
- Figure 42. Three-dimensional scans of a 900 × 900 µm area of as-cast components a) without coating (rough surface) and b) with coating (fine surface).
- Figure 43. The investigated surface conditions: a) PS, b) FS, and c) RS.
- Figure 44. Microstructure of the cast material, showing the aluminium dendrites, Si particles, and Cu- and Fe-rich phases.
- Figure 45. a) The microstructure of the sand-cast material with low hydrogen content; b) an enlarged view of the area highlighted by a red square in (a), showing oxides in the vicinity of the porosity; c) a sample with high hydrogen content, where two distinct pore sizes are evident.
- Figure 46. The probability density functions of the pore size distributions for the LH and HH conditions.
- Figure 47. Wöhler curves for a) LH and b) HH samples.
- Figure 48. Fatigue-life distributions for (a) LH and (b) HH samples with different surface conditions.
- Figure 49. a) The crack initiation point in the fracture surface of an LH sample with a casting skin. The red arrow is pointing to the casting skin. b) The crack initiation point in the fracture surface in the PS sample, at a defect located at the surface.
- Figure 50. The probability density functions of Weibull distributions for (a) samples with casting skins and (b) MS and PS samples.
7. 結論:
本研究は、組織特徴、欠陥、および表面品質がAl-Si-Mg鋳造合金の疲労性能に及ぼす影響を調査しました。主要な結論は以下の通りです:
- 溶湯品質: 完全な溶湯品質評価には、隠れた損傷を明らかにするためにRPTと引張試験の両方が必要です。回転式脱ガスは、初期溶湯が損傷している場合、特性を改善しない可能性があり、機械的性能を改善することなくワイブル混合分布を除去する可能性があります。
- 銅の役割: Cu含有量の増加は強度(σY, ST)を向上させますが、特に鋳放し状態で延性(eF)を低下させます。これは金属間化合物を増加させ、き裂発生/進展経路を変更し、特に熱処理後に二次き裂を増加させます。
- 隠れた損傷: 酸化介在物は溶湯から生じる重要な欠陥であり、核生成サイトとして機能し、引張応力下で開口します。DICおよびSTEM-EDSはその存在と影響を確認しました。HIPは気孔を閉じますが、介在物を完全に治癒しない場合があります。巻き込み損傷と機械的損傷を区別することが重要です。
- 表面品質と欠陥サイズ: 鋳肌は、表面下の欠陥に対する障壁として機能し、表面に露出した欠陥からのき裂発生を遅延/防止することにより、研磨表面と比較して疲労寿命を著しく改善します。研磨は疲労寿命を大幅に低下させます。気孔率の増加(高Hによる)は、主に疲労寿命のばらつきに影響を与え、表面状態と複雑に相互作用します。最小限の機械加工で部品を設計することが疲労性能に有利です。
8. 参考文献:
- [1] N. Hooftman, M. Messagie, J. Van Mierlo, T. Coosemans, A review of the European passenger car regulations–Real driving emissions vs local air quality, Renewable and Sustainable Energy Reviews 86 (2018) 1-21.
- [2] A.C. Serrenho, J.B. Norman, J.M. Allwood, The impact of reducing car weight on global emissions: the future fleet in Great Britain, Philosophical Transactions of the Royal Society A: Mathematical, Physical and Engineering Sciences 375(2095) (2017) 20160364.
- [3] A.I. Taub, A.A. Luo, Advanced lightweight materials and manufacturing processes for automotive applications, Mrs Bulletin 40(12) (2015) 1045-1054.
- [4] E. Balomenos, D. Panias, I.J.M.P. Paspaliaris, E.M. Review, Energy and exergy analysis of the primary aluminum production processes: a review on current and future sustainability, 32(2) (2011) 69-89.
- [5] I. Polmear, D. StJohn, J.-F. Nie, M. Qian, Light alloys: metallurgy of the light metals, Butterworth-Heinemann2017.
- [6] C. Jirang, H.J.J.T.o.N.M.S.o.C. Roven, Recycling of automotive aluminum, 20(11) (2010) 2057-2063.
- [7] S. Seifeddine, E. Sjölander, T. Bogdanoff, On the role of copper and cooling rates on the microstructure, defect formations and mechanical properties of Al-Si-Mg alloys, (2013).
- [8] C. Caceres, C. Davidson, J. Griffiths, Q. Wang, The effect of Mg on the microstructure and mechanical behavior of Al-Si-Mg casting alloys, Metallurgical and materials transactions A 30(10) (1999) 2611-2618.
- [9] S. Shabestari, H. Moemeni, Effect of copper and solidification conditions on the microstructure and mechanical properties of Al–Si–Mg alloys, Journal of Materials Processing Technology 153 (2004) 193-198.
- [10] M.T. Di Giovanni, E.A. Mørtsell, T. Saito, S. Akhtar, M. Di Sabatino, Y. Li, E. Cerri, Influence of Cu addition on the heat treatment response of A356 foundry alloy, Materials Today Communications 19 (2019) 342-348.
- [11] Y. Zheng, W. Xiao, S. Ge, W. Zhao, S. Hanada, C. Ma, Effects of Cu content and Cu/Mg ratio on the microstructure and mechanical properties of Al–Si–Cu–Mg alloys, Journal of Alloys and Compounds 649 (2015) 291-296.
- [12] S. Morin, E. Elgallad, H. Doty, S. Valtierra, F.J.A.i.M.S. Samuel, Engineering, Effect of Mg content and heat treatment on the mechanical properties of low pressure Die-Cast 380 alloy, 2016 (2016).
- [13] U. Krupp, Fatigue crack propagation in metals and alloys: microstructural aspects and modelling concepts, John Wiley & Sons2007.
- [14] I. Serrano-Munoz, J.-Y. Buffiere, R. Mokso, C. Verdu, Y. Nadot, Location, location & size: defects close to surfaces dominate fatigue crack initiation, Scientific reports 7(1) (2017) 45239.
- [15] I. Serrano-Munoz, J.-Y. Buffiere, C. Verdu, Y. Gaillard, P. Mu, Y. Nadot, Influence of surface and internal casting defects on the fatigue behaviour of A357-T6 cast aluminium alloy, International Journal of Fatigue 82 (2016) 361-370.
- [16] H. Jiang, P. Bowen, J.J.J.o.m.s. Knott, Fatigue performance of a cast aluminium alloy Al-7Si-Mg with surface defects, 34(4) (1999) 719-725.
- [17] C. Nyahumwa, Ν.R. Green, J. Campbell, The concept of the fatigue potential of cast alloys, Journal of the Mechanical Behavior of Materials 9(4) (1998) 227-236.
- [19] O. Lashkari, L. Yao, S. Cockcroft, D. Maijer, X-ray microtomographic characterization of porosity in aluminum alloy A356, Metallurgical and Materials Transactions A 40 (2009) 991-999.
- [20] Z. Ma, A. Samuel, F. Samuel, H. Doty, S. Valtierra, A study of tensile properties in Al–Si–Cu and Al–Si–Mg alloys: Effect of β-iron intermetallics and porosity, Materials Science and Engineering: A 490(1-2) (2008) 36-51.
- [21] J. Campbell, M. Tiryakioğlu, Fatigue Failure in Engineered Components and How It Can Be Eliminated: Case Studies on the Influence of Bifilms, Metals 12(8) (2022) 1320.
- [22] M.R. Bayoumi, A. Abdellatif, Effect of surface finish on fatigue strength, Engineering Fracture Mechanics 51(5) (1995) 861-870.
- [24] A.E. Jarfors, A comparison between semisolid casting methods for aluminium alloys, Metals 10(10) (2020) 1368.
- [25] J. Olofsson, I.L. Svensson, Incorporating predicted local mechanical behaviour of cast components into finite element simulations, Materials & Design 34 (2012) 494-500.
- [26] M. Tiryakioglu, D. Askeland, C. Ramsay, Relationship between metal fluidity and optimum pouring time: a literature review, TRANSACTIONS AMERICAN FOUNDRYMENS SOCIETY (1993) 685-685.
- [27] J. Olofsson, I.L. Svensson, P. Lava, D. Debruyne, Characterisation and investigation of local variations in mechanical behaviour in cast aluminium using gradient solidification, Digital Image Correlation and finite element simulation, Materials & Design 56 (2014) 755-762.
- [28] D. Dwivedi, R. Sharma, A. Kumar, Influence of silicon content and heat treatment parameters on mechanical properties of cast Al–Si–Mg alloys, International Journal of Cast Metals Research 19(5) (2006) 275-282.
- [29] S. Roy, L.F. Allard, A. Rodriguez, W.D. Porter, A. Shyam, Comparative evaluation of cast aluminum alloys for automotive cylinder heads: Part II—mechanical and thermal properties, Metallurgical and Materials Transactions A 48(5) (2017) 2543-2562.
- [30] N. Tenekedjiev, J. Gruzleski, Hypereutectic aluminium-silicon casting alloys—a review, Cast Metals 3(2) (1990) 96-105.
- [31] O. Atasoy, F. Yilmaz, R. Elliott, Growth structures in aluminium-silicon alloys I. The coupled zone, Journal of crystal growth 66(1) (1984) 137-146.
- [32] A. Dahle, K. Nogita, S. McDonald, J. Zindel, L. Hogan, Eutectic nucleation and growth in hypoeutectic Al-Si alloys at different strontium levels, Metallurgical and Materials Transactions A 32(4) (2001) 949-960.
- [33] A. Samuel, F. Samuel, Effect of alloying elements and dendrite arm spacing on the microstructure and hardness of an Al-Si-Cu-Mg-Fe-Mn (380) aluminium die-casting alloy, Journal of Materials Science 30(7) (1995) 1698-1708.
- [35] E. Sjölander, S. Seifeddine, The heat treatment of Al–Si–Cu–Mg casting alloys, Journal of Materials Processing Technology 210(10) (2010) 1249-1259.
- [38] S.J.M.S. Shabestari, E. A, The effect of iron and manganese on the formation of intermetallic compounds in aluminum–silicon alloys, 383(2) (2004) 289-298.
- [39] C.M. Dinnis, J.A. Taylor, A.K.J.S.m. Dahle, As-cast morphology of iron-intermetallics in Al–Si foundry alloys, 53(8) (2005) 955-958.
- [40] A. Dahle, K. Nogita, S. McDonald, C. Dinnis, L. Lu, Eutectic modification and microstructure development in Al–Si Alloys, Materials Science and Engineering: A 413 (2005) 243-248.
- [41] A. Greer, Overview: Application of heterogeneous nucleation in grain-refining of metals, The Journal of Chemical Physics 145(21) (2016) 211704.
- [42] J. Campbell, Castings, Butterworth-Heinemann2003.
- [43] J. Campbell, Entrainment defects, Materials science and technology 22(2) (2006) 127-145.
- [45] M. Divandari, J. Campbell, Mechanisms of bubble trail formation in castings, Trans. AFS 109 (2001) 433-442.
- [46] G. Gyarmati, G. Fegyverneki, M. Tokár, T. Mende, The effects of rotary degassing treatments on the melt quality of an Al–Si casting alloy, International Journal of Metalcasting 15(1) (2021) 141-151.
- [48] M.B. Đurđević, Z. Odanović, J. Pavlović-Krstić, Melt quality control at aluminum casting plants, Metalurgija 16(1) (2010) 63-76.
- [49] M. Riestra, A. Bjurenstedt, T. Bogdanoff, E. Ghassemali, S. Seifeddine, Complexities in the Assessment of Melt Quality, International Journal of Metalcasting 12(3) (2018) 441-448.
- [50] M. Uludağ, R. Çetin, D. Dispinar, M.J.M. Tiryakioğlu, Characterization of the effect of melt treatments on melt quality in Al-7wt% Si-Mg alloys, 7(5) (2017) 157.
- [52] G. Eisaabadi, M. Tiryakioğlu, P. Davami, S.-K. Kim, Y.O. Yoon, G.-Y. Yeom, N.-S. Kim, The effect of remelting on the melt and casting quality in Al–7% Si–Mg castings, Materials Science and Engineering: A 605 (2014) 203-209.
- [59] G. Timelli, F. Bonollo, Fluidity of aluminium die castings alloy, International Journal of Cast Metals Research 20(6) (2007) 304-311.
- [60] M. Di Sabatino, L. Arnberg, A review on the fluidity of Al based alloys, Metallurgical Science and Tecnology 22(1) (2004).
- [61] A. Dahle, P. Tøndel, C. Paradies, L. Arnberg, Effect of grain refinement on the fluidity of two commercial Al-Si foundry alloys, Metallurgical and Materials Transactions A 27(8) (1996) 2305-2313.
- [62] A. Rotella, Y. Nadot, M. Piellard, R. Augustin, M. Fleuriot, Fatigue limit of a cast Al-Si-Mg alloy (A357-T6) with natural casting shrinkages using ASTM standard X-Ray inspection, International Journal of Fatigue (2018).
- [64] K. Fisher, W. Kurz, Fundamentals of solidification, Trans Tech Publications (1986).
- [65] Y. Cho, H.-C. Lee, K. Oh, A. Dahle, Effect of strontium and phosphorus on eutectic Al-Si nucleation and formation of β-Al 5 FeSi in hypoeutectic Al-Si foundry alloys, Metallurgical and Materials Transactions A 39(10) (2008) 2435-2448.
- [66] E.A. Mørtsell, F. Qian, C.D. Marioara, Y. Li, Precipitation in an A356 foundry alloy with Cu additions-A transmission electron microscopy study, Journal of Alloys and Compounds 785 (2019) 1106-1114.
- [67] T. Saito, E.A. Mørtsell, S. Wenner, C.D. Marioara, S.J. Andersen, J. Friis, K. Matsuda, R. Holmestad, Atomic structures of precipitates in Al–Mg–Si alloys with small additions of other elements, Adv. Eng. Mater. 20(7) (2018) 1800125.
- [68] S. Roy, L.F. Allard, A. Rodriguez, T.R. Watkins, A. Shyam, Comparative Evaluation of Cast Aluminum Alloys for Automotive Cylinder Heads: Part I—Microstructure Evolution, Metallurgical and Materials Transactions A (2017) 1-14.
- [69] R. Taghiabadi, A. Fayegh, A. Pakbin, M. Nazari, M. Ghoncheh, Quality index and hot tearing susceptibility of Al–7Si–0.35 Mg–xCu alloys, Transactions of Nonferrous Metals Society of China 28(7) (2018) 1275-1286.
- [70] M. Avalle, G. Belingardi, M.P. Cavatorta, R. Doglione, Casting defects and fatigue strength of a die cast aluminium alloy: a comparison between standard specimens and production components, International journal of Fatigue 24(1) (2002) 1-9.
- [71] F. Guerra, A. Bedolla-Jacuinde, H. Valdes-Vera, J. Quintero-Ortiz, A. Zarate-Rangel, J. Pacheco-Cedeño, Measurement of Air Entrainment and its Effect on the Microstructure and Mechanical Properties of a A356 Aluminum Alloy, International Journal of Metalcasting (2022) 1-19.
- [73] M. Tiryakioğlu, P. Yousefian, P.D.J.M. Eason, M.T. A, Quantification of entrainment damage in A356 aluminum alloy castings, 49(11) (2018) 5815-5822.
- [74] D. Dispinar, J. Campbell, Porosity, hydrogen and bifilm content in Al alloy castings, Materials Science and Engineering: A 528(10) (2011) 3860-3865.
- [76] X. Cao, J.J.M. Campbell, M.T. A, The nucleation of Fe-rich phases on oxide films in Al-11.5 Si-0.4 Mg cast alloys, 34(7) (2003) 1409-1420.
- [79] J. Campbell, Perspective chapter: A personal overview of casting processes, Casting Processes and Modelling of Metallic Materials (2020) 1-17.
- [80] M. Tiryakioğlu, The Effect of Hydrogen on Pore Formation in Aluminum Alloy Castings: Myth Versus Reality, Metals 10(3) (2020) 368.
- [82] V.-D. Le, N. Saintier, F. Morel, D. Bellett, P. Osmond, Investigation of the effect of porosity on the high cycle fatigue behaviour of cast Al-Si alloy by X-ray micro-tomography, International Journal of Fatigue 106 (2018) 24-37.
- [86] C. Caceres, M. Djurdjevic, T. Stockwell, J. Sokolowski, The effect of Cu content on the level of microporosity in Al-Si-Cu-Mg casting alloys, Scripta Materialia 40(5) (1999) 631-637.
- [97] S.-Z. Lu, A. Hellawell, Growth mechanisms of silicon in Al-Si alloys, Journal of Crystal growth 73(2) (1985) 316-328.
- [98] D. Jenkinson, L. Hogan, The modification of aluminium-silicon alloys with strontium, Journal of Crystal Growth 28(2) (1975) 171-187.
- [99] M. Timpel, N. Wanderka, R. Schlesiger, T. Yamamoto, N. Lazarev, D. Isheim, G. Schmitz, S. Matsumura, J. Banhart, The role of strontium in modifying aluminium–silicon alloys, Acta Materialia 60(9) (2012) 3920-3928.
- [100] A. Knuutinen, K. Nogita, S. McDonald, A. Dahle, Modification of Al–Si alloys with Ba, Ca, Y and Yb, Journal of Light Metals 1(4) (2001) 229-240.
- [101] S.J. Mashl, H. Bodycote, Hot Isostatic Pressing of Castings, Casting, 2008.
- [102] A. Eklund, M. Ahlfors, Heat treatment of PM parts by Hot Isostatic Pressing, Metal Powder Report 73(3) (2018) 163-169.
- [103] H. Atkinson, S. Davies, Fundamental aspects of hot isostatic pressing: an overview, Metallurgical and Materials Transactions A 31(12) (2000) 2981-3000.
- [104] M.H. Lee, J.J. Kim, K.H. Kim, N.J. Kim, S. Lee, E.W. Lee, Effects of HIPping on high-cycle fatigue properties of investment cast A356 aluminum alloys, Materials Science and Engineering: A 340(1-2) (2003) 123-129.
- [105] C. Lei, W. Frazier, E. Lee, The effect of hot isostatic pressing on cast aluminum, Jom 49(11) (1997) 38-39.
- [106] G. Ran, J. Zhou, Q. Wang, The effect of hot isostatic pressing on the microstructure and tensile properties of an unmodified A356-T6 cast aluminum alloy, Journal of alloys and compounds 421(1-2) (2006) 80-86.
- [107] L. Ceschini, A. Morri, G. Sambogna, The effect of hot isostatic pressing on the fatigue behaviour of sand-cast A356-T6 and A204-T6 aluminum alloys, Journal of materials processing technology 204(1-3) (2008) 231-238.
- [109] T. Rich, J. Orbison, R. Duncan, P. Olivero, R. Peterec, The effect of hot isostatic pressing on crack initiation, fatigue, and mechanical properties of two cast aluminum alloys, Journal of materials engineering and performance 8(3) (1999) 315-324.
- [113] A. Mohamed, F. Samuel, Influence of Mg and solution heat treatment on the occurrence of incipient melting in Al–Si–Cu–Mg cast alloys, Materials Science and Engineering: A 543 (2012) 22-34.
- [116] N.E. Dowling, Mechanical behavior of materials: engineering methods for deformation, fracture, and fatigue, Pearson2012.
- [117] E. Ghassemali, M. Riestra, T. Bogdanoff, B.S. Kumar, S. Seifeddine, Hall-Petch equation in a hypoeutectic Al-Si cast alloy: grain size vs. secondary dendrite arm spacing, Procedia Engineering 207 (2017) 19-24.
- [118] T. Bogdanoff, S. Seifeddine, A.K. Dahle, The effect of SI content on microstructure and mechanical properties of Al-Si alloy, La Metallurgia Italiana 108(6) (2016).
- [119] C. Caceres, I.L. Svensson, J. Taylor, Strength-ductility behaviour of Al-Si-Cu-Mg casting alloys in T6 temper, International Journal of Cast Metals Research 15(5) (2003) 531-543.
- [122] S. Suresh, Fatigue of materials, Cambridge university press1998.
- [124] M. Leitner, C. Garb, H. Remes, M. Stoschka, Microporosity and statistical size effect on the fatigue strength of cast aluminium alloys EN AC 45500 and 46200, Materials Science and Engineering: A 707 (2017) 567-575.
- [126] J.T. Staley Jr, M. Tiryakioğlu, J. Campbell, The effect of hot isostatic pressing (HIP) on the fatigue life of A206-T71 aluminum castings, Materials Science and Engineering: A 465(1-2) (2007) 136-145.
- [127] D.A. Lados, D. Apelian, Fatigue crack growth characteristics in cast Al–Si–Mg alloys: Part I. Effect of processing conditions and microstructure, Materials Science and Engineering: A 385(1-2) (2004) 200-211.
- [128] D.A. Lados, D. Apelian, J.F. Major, Fatigue crack growth mechanisms at the microstructure scale in Al-Si-Mg cast alloys: Mechanisms in regions II and III, Metallurgical and Materials Transactions A 37(8) (2006) 2405-2418.
- [131] Q. Wang, D. Apelian, D. Lados, Fatigue behavior of A356/357 aluminum cast alloys. Part II–Effect of microstructural constituents, Journal of light metals 1(1) (2001) 85-97.
- [132] K. Williamson, Research methods for students, academics and professionals: Information management and systems, Elsevier2002.
- [133] P. Johannesson, E. Perjons, An introduction to design science, Springer2014.
- [134] K.A. Kasvayee, E. Ghassemali, K. Salomonsson, S. Sujakhu, S. Castagne, A.E. Jarfors, Microstructural strain mapping during in-situ cyclic testing of ductile iron, Materials Characterization 140 (2018) 333-339.
- [135] K.A. Kasvayee, K. Salomonsson, E. Ghassemali, A.E. Jarfors, Microstructural strain distribution in ductile iron; comparison between finite element simulation and digital image correlation measurements, Materials Science and Engineering: A 655 (2016) 27-35.
- [136] E. Erzi, M. Tiryakioğlu, A simple procedure to determine incoming quality of aluminum alloy ingots and its application to A356 alloy ingots, International Journal of Metalcasting 14(4) (2020) 999-1004.
- [137] D. Dispinar, J. Campbell, A comparison of methods used to assess aluminium melt quality, 136th TMS Annual Meeting, Shape Casting: 2nd International Symposium, Orlando, Florida, USA,(February 2007), 2007, pp. 11-18.
- [138] D. Dispinar, S. Akhtar, A. Nordmark, M. Di Sabatino, L. Arnberg, Degassing, hydrogen and porosity phenomena in A356, Materials Science and Engineering: A 527(16-17) (2010) 3719-3725.
- [139] W. Weibull, A statistical theory of strength of materials, IVB-Handl. (1939).
- [140] W. Weibull, A statistical distribution function of wide applicability, Journal of applied mechanics (1951).
- [141] M. Tiryakioğlu, D. Hudak, On estimating Weibull modulus by the linear regression method, Journal of materials science 42(24) (2007) 10173-10179.
- [142] M. Tiryakioğlu, D. Hudak, Guidelines for two-parameter Weibull analysis for flaw-containing materials, Metallurgical and Materials Transactions B 42(6) (2011) 1130-1135.
- [143] M. Tiryakioğlu, D. Hudak, G. Ökten, On evaluating Weibull fits to mechanical testing data, Materials Science and Engineering: A 527(1-2) (2009) 397-399.
- [144] D. Dispinar, J. Campbell, Metal quality studies in secondary remelting of aluminium, Foundry Trade Journal 178(3612) (2004) 78-81.
- [145] R. Kimura, Molten Metal Quality of Aluminium Alloy Die Castings, J.JFS 87 (2015) 412-416.
- [146] M. Tiryakioğlu, J. Campbell, N.D. Alexopoulos, On the ductility of cast Al-7 pct Si-Mg alloys, Metallurgical and Materials Transactions A 40(4) (2009) 1000-1007.
- [147] M. Tiryakioğlu, J. Campbell, N.D. Alexopoulos, On the ductility potential of cast Al–Cu–Mg (206) alloys, Materials Science and Engineering: A 506(1-2) (2009) 23-26.
- [148] M. Tiryakioğlu, J. Campbell, N.D. Alexopoulos, Quality indices for aluminum alloy castings: A critical review, Metallurgical and Materials Transactions B 40(6) (2009) 802-811.
- [149] M. Tiryakioğlu, J. Campbell, Quality index for aluminum alloy castings, International Journal of Metalcasting 8(3) (2014) 39-42.
- [150] M. Tiryakioğlu, J. Campbell, Weibull analysis of mechanical data for castings: A guide to the interpretation of probability plots, Metallurgical and Materials Transactions A 41 (2010) 3121-3129.
- [151] T. Lu, J. Wu, Y. Pan, S. Tao, Y. Chen, Optimizing the tensile properties of Al–11Si–0.3 Mg alloys: Role of Cu addition, Journal of Alloys and Compounds 631 (2015) 276-282.
- [152] E. Sjölander, S. Seifeddine, Optimisation of solution treatment of cast Al–Si–Cu alloys, Materials & design 31 (2010) S44-S49.
- [153] J.H. Sokolowski, X. Sun, G. Byczynski, D. Northwood, D. Penrod, R. Thomas, A. Esseltine, The removal of copper-phase segregation and the subsequent improvement in mechanical properties of cast 319 aluminium alloys by a two-stage solution heat treatment, Journal of Materials Processing Technology 53(1-2) (1995) 385-392.
- [154] G. Wang, Q. Sun, L. Feng, L. Hui, C. Jing, Influence of Cu content on ageing behavior of AlSiMgCu cast alloys, Materials & design 28(3) (2007) 1001-1005.
- [155] S. Toschi, Optimization of A354 Al-Si-Cu-Mg Alloy Heat Treatment: Effect on Microstructure, Hardness, and Tensile Properties of Peak Aged and Overaged Alloy, Metals 8(11) (2018) 961.
- [156] J.J. Friel, Practical guide to image analysis, ASM international2000.
- [157] J.-M. Song, C.-F. Huang, H.-Y. Chuang, Microstructural characteristics and vibration fracture properties of Sn-Ag-Cu-TM (TM= Co, Ni, and Zn) alloys, Journal of electronic materials 35(12) (2006) 2154-2163.
- [158] D.A. Lados, D. Apelian, P.E. Jones, J.F. Major, Microstructural mechanisms controlling fatigue crack growth in Al–Si–Mg cast alloys, Materials Science and Engineering: A 468 (2007) 237-245.
- [159] N. Rathod, J. Manghani, Effect of modifier and grain refiner on cast Al-7Si aluminum alloy: A review, International Journal of emerging trends in engineering and development 5(2) (2012) 574-582.
- [160] M. Riestra, E. Ghassemali, T. Bogdanoff, S. Seifeddine, Interactive effects of grain refinement, eutectic modification and solidification rate on tensile properties of Al-10Si alloy, Materials Science and Engineering: A 703 (2017) 270-279.
- [161] L. Ceschini, A. Morri, S. Toschi, S. Seifeddine, Room and high temperature fatigue behaviour of the A354 and C355 (Al–Si–Cu–Mg) alloys: Role of microstructure and heat treatment, Materials Science and Engineering: A 653 (2016) 129-138.
- [162] T. Bogdanoff, L. Lattanzi, M. Merlin, E. Ghassemali, S. Seifeddine, The Influence of Copper Addition on Crack Initiation and Propagation in an Al-Si-Mg Alloy During Cyclic Testing, Materialia (2020) 100787.
- [163] T. Bogdanoff, L. Lattanzi, M. Merlin, E. Ghassemali, A.E. Jarfors, S.J.M.S. Seifeddine, E. A, The complex interaction between microstructural features and crack evolution during cyclic testing in heat-treated Al–Si–Mg–Cu cast alloys, 825 (2021) 141930.
- [164] G. Gyarmati, G. Fegyverneki, Z. Kéri, D. Molnár, M. Tokár, L. Varga, T. Mende, Controlled precipitation of intermetallic (Al, Si) 3Ti compound particles on double oxide films in liquid aluminum alloys, Materials Characterization 181 (2021) 111467.
- [165] X. Cao, J. Campbell, The solidification characteristics of Fe-rich intermetallics in Al-11.5 Si-0.4 Mg cast alloys, Metallurgical and Materials Transactions A 35(5) (2004) 1425-1436.
- [170] M. Schaffer, B. Schaffer, Q. Ramasse, Sample preparation for atomic-resolution STEM at low voltages by FIB, Ultramicroscopy 114 (2012) 62-71.
- [171] Y. Umeno, A. Kushima, T. Kitamura, P. Gumbsch, J. Li, Ab initio study of the surface properties and ideal strength of (100) silicon thin films, physical Review B 72(16) (2005) 165431.
- [172] S.-M. Dubois, G.-M. Rignanese, T. Pardoen, J.-C. Charlier, Ideal strength of silicon: An ab initio study, Physical Review B 74(23) (2006) 235203.
- [173] M. Mueller, G. Žagar, A. Mortensen, In-situ strength of individual silicon particles within an aluminium casting alloy, Acta Materialia (2017).
- [174] M. Mueller, M. Fornabaio, G. Žagar, A. Mortensen, Microscopic strength of silicon particles in an aluminium–silicon alloy, Acta Materialia 105 (2016) 165-175.
- [175] A. Noreyan, Y. Qi, V. Stoilov, Critical shear stresses at aluminum–silicon interfaces, Acta materialia 56(14) (2008) 3461-3469.
- [176] M. Tiryakioğlu, On the heterogeneous nucleation pressure for hydrogen pores in liquid aluminium, International Journal of Cast Metals Research 33(4-5) (2020) 153-156.
- [177] P. Yousefian, M. Tiryakioğlu, Pore formation during solidification of aluminum: reconciliation of experimental observations, modeling assumptions, and classical nucleation theory, Metallurgical and Materials Transactions A 49 (2018) 563-575.
- [178] S. Pomberger, M. Leitner, M.J.M.T.P. Stoschka, Evaluation of surface roughness parameters and their impact on fatigue strength of Al-Si cast material, Materials Today Preceedings 12 (2019) 225-234.
- [179] M. Tiryakioğlu, J. Campbell, C.J.M. Nyahumwa, M.T. B, Fracture surface facets and fatigue life potential of castings, 42(6) (2011) 1098-1103.
- [180] H. Dvorak, E. Schwegtier Jr, Statistical distribution of flaw sizes, International Journal of Fracture Mechanics 8(1) (1972) 110-111.
- [181] M. Tiryakioğlu, Pore size distributions in AM50 Mg alloy die castings, Materials Science and Engineering: A 465(1-2) (2007) 287-289.
- [182] M. Tiryakioğlu, On fatigue life variability in cast Al–10% Si–Mg alloys, Materials Science and Engineering: A 527(6) (2010) 1560-1564.
- [183] T.W. Anderson, D.A. Darling, A test of goodness of fit, Journal of the American statistical association 49(268) (1954) 765-769.
- [184] O. Basquin, The exponential law of endurance tests, Proc Am Soc Test Mater, 1910, pp. 625-630.
- [185] S. Sarkani, T. Mazzuchi, D. Lewandowski, D. Kihl, Runout analysis in fatigue investigation, Engineering Fracture Mechanics 74(18) (2007) 2971-2980.
- [186] R. Hidalgo Coca, J.A. Esnaola Ramos, I. Llavori Osa, M. Larrañaga Serna, N. Herrero Dorca, I. Hurtado Hurtado, A. Kortabarria Lezeta, Influence of Surface Finish and Porosity on the Fatigue behaviour of A356 Aluminium Casting Alloy, 12th International Fatigue Congress (FATIGUE 2018), France, 2018.
- [187] J. Linder, M. Axelsson, H. Nilsson, The influence of porosity on the fatigue life for sand and permanent mould cast aluminium, International Journal of Fatigue 28(12) (2006) 1752-1758.
- [188] B. Zhao, J. Song, L. Xie, Z. Hu, J. Chen, Surface roughness effect on fatigue strength of aluminum alloy using revised stress field intensity approach, Scientific reports 11(1) (2021) 19279.
- [189] B. Skallerud, T. Iveland, G. Härkegård, Fatigue life assessment of aluminum alloys with casting defects, Engineering Fracture Mechanics 44(6) (1993) 857-874.
- [191] L. Wang, N. Limodin, A. El Bartali, J.-F. Witz, R. Seghir, J.-Y. Buffiere, E. Charkaluk, Influence of pores on crack initiation in monotonic tensile and cyclic loadings in lost foam casting A319 alloy by using 3D in-situ analysis, Materials Science and Engineering: A 673 (2016) 362-372.
- [192] R.C. Juvinall, Engineering considerations of stress strain and strength, 1967, 580 P. MCGRAW-HILL BOOK CO., NEW YORK (1967).
- [193] H. Özdeş, M. Tiryakioğlu, On estimating high-cycle fatigue life of cast Al-Si-Mg-(Cu) alloys from tensile test results, Materials Science and Engineering: A 688 (2017) 9-15.
- [194] H. Özdeş, M. Tiryakioğlu, The effect of structural quality on fatigue life in 319 aluminum alloy castings, Journal of Materials Engineering and Performance 26 (2017) 736-743.
9. 著作権:
- 本資料は「Toni Bogdanoff」氏の論文です。「The Effect of Microstructural Features, Defects and Surface Quality on the Fatigue Performance in Al-Si-Mg Cast Alloys」に基づいています。
- 論文の出典: http://urn.kb.se/resolve?urn=urn:nbn:se:hj:diva-61111
本資料は上記の論文に基づいて要約されており、商業目的での無断使用は禁じられています。
Copyright © 2025 CASTMAN. All rights reserved.