本紹介内容は、「[出版社名: Elsevier B.V.]」が出版した論文「[論文タイトル: Wear properties of a new Al80Mg10Si5Cu5 multicomponent alloy]」に基づいています。
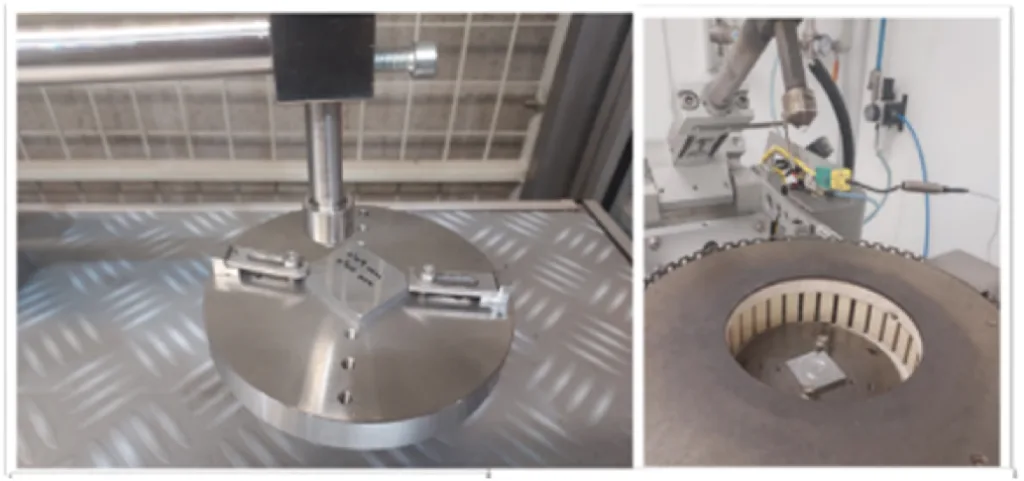
1. 概要:
- 論文タイトル: Wear properties of a new Al80Mg10Si5Cu5 multicomponent alloy (新規Al80Mg10Si5Cu5多成分合金の摩耗特性)
- 著者: Ester Villanueva, Iban Vicario, Joseba Albizuri, Gurutze Arruebarrena, Teresa Guraya
- 発行年: 2024
- 発行学術誌/学会: Wear
- キーワード: Ball on disc, Friction, Wear, Aluminium multicomponent alloy, Abrasion (ボールオンディスク, 摩擦, 摩耗, アルミニウム多成分合金, アブレージョン)
2. 概要:
本研究は、軽量自動車用途、特に後輪ドラムディスク向けに、Al80Mg10Si5Cu5系をベースとして新たに開発された多成分アルミニウム軽量合金の摩耗に関するトライボロジー特性を調査するものです。サンプルは、鋳造合金リターン材と二次アルミニウムインゴットを用い、高圧ダイカスト(HPDC)法で製造され、室温(RT)および200℃で試験されました。A180Mg10Si5Cu5合金は、RTおよび特に200℃において、参照合金であるAlSi9Cu3と比較して高い硬度と耐摩耗性(摩耗率で10倍の低減)を示すことが観察されました。HPDC鋳造部品の外面層(スキン)を維持することの影響がボールオンディスク試験で研究され、トライボロジー特性の向上と接触面の機械加工回避の可能性が示されました。表面層を持つ鋳放し状態のA180Mg10Si5Cu5合金は、RTにおいて5 × 10⁻⁴ mm³/N·m²の摩耗率係数を示し、これはスキンなしのサンプルよりも50%低い値でした。表面層を持つ溶体化処理サンプル(440℃で72時間、75℃で水焼入れ、自然時効)は、11 × 10⁻⁴ mm³/N·m²の摩耗率係数を示し、これは表面層なしのサンプルよりも約20%低い値でした。AlSi9Cu3合金の摩耗率は、RTにおいてスキンなしのサンプルで50%以上減少しました。200℃では、表面層を持つサンプルの摩耗率係数の方が低い値でした。
3. 緒言:
多成分コンセプトに基づくアルミニウム多相および非等原子量高エントロピー合金(HEA)は、単相合金とは対照的に、優れた物理的および機械的特性を有することが示されています[1]。これらの合金において強化された単相微細構造を得るための急速凝固プロセスの効果は、最近の研究でまとめられています[2]。一方、産業界における軽量車両への要求は、アルミニウム鋳造部品の製造、特に高圧ダイカスト(HPDC)によるGIGAPRESS技術を用いた電気自動車において急成長を引き起こしています[3]。電気自動車市場は継続的に拡大しており、軽量化は航続距離を伸ばすために重要です。アルミニウム製ドラムブレーキは、後輪ブレーキの力が前輪ブレーキよりも低く、運動エネルギー回生システム(KERS)を使用することでブレーキ力を低減できるため、軽量電気自動車に使用できます。また、前輪ディスクブレーキは後輪ドラムブレーキよりも先に作動し、後輪ブレーキの圧力が低減されます[4]。アルミニウム製ドラムは鉄製ドラムよりも軽量で、放熱性が向上し、フェードが減少し、ねずみ鋳鉄ディスクの腐食の可能性やディスク故障を回避できます[5]。
AlSiCuはHPDCで最も一般的に使用されるアルミニウム合金ですが、その機械的特性には特定の制限があります[6]。AlSiMgCu合金はより高い耐食性と強度を提供し、一般的に熱処理によって改善され、良好な耐摩耗性と摩擦が要求されるさまざまな自動車部品に適しています[7,8]。不十分な耐摩耗性はアルミニウム合金の問題ですが[9]、Al合金のトライボロジー特性は、合金元素の種類と量を調整したり、外部からの強化相を導入したり、熱処理を行ったりすることで向上させることができます[10–12]。鋳鉄製ブレーキを置き換え、車両重量を削減するために、アルミニウム基複合材料(AMC)ブレーキローターが開発されました。AMCはアルミニウム合金よりも高い熱伝導率、低い密度、高い比強度を持っています。AMCは、カスタマイズされた特性を得るために、Al2O3、SiC、SiO2などの硬質セラミック粒子で強化された延性のあるアルミニウムマトリックスを特徴としています[13]。
しかし、AMCの主な欠点は、製造コスト(特に機械加工コスト)、粒子サイズと分布の制御の難しさ(摩耗特性が強化粒子の体積とサイズに大きく依存するため)[14]、複雑な鋳造プロセス、そして主としてリターン材やスクラップの低いまたは困難なリサイクル性です。
AMCではない鋳造アルミニウム合金の摩耗特性を向上させる最も一般的な方法は、シリコン合金化です。Siの割合を増やすと、より多くの硬質Si結晶が生成され、合金の硬度と耐摩耗性が向上します。トライボロジー用途では、通常、共晶相のアルミニウムと組み合わされた初晶シリコン相を持つ過共晶Al-Si合金(Si > 13 wt%)が用いられます。シリコン相の種類、形態、サイズ、分布は、塑性変形したアルミニウムマトリックス領域で荷重の重要な部分を支持することにより、摩擦と耐摩耗性を向上させる上で重要です[15–17]。これらの合金では、SiはMgと結合してMg2Siとして析出する傾向があります。Mg量の増加は耐摩耗性の向上を促進します[18]。複雑な金属間化合物相は、摩耗メカニズムにおける接合部の成長と凝着を防止する鍵となります。金属間化合物相が多い合金は摩耗率が低くなります[19]。合金中の銅の増加は機械的特性を向上させ、耐食性を低下させ、気孔率を増加させる可能性があります[20,21]。AlSi7Mg合金では、微細な結晶粒を促進し、硬度と耐摩耗性を向上させて摩擦係数を低下させるAl₂Cu金属間化合物相を得るために、最低1 wt%のCuが必要でした[22]。アルミニウム鋳造合金の硬度を向上させるメカニズムは、MgとAl、およびCuとSiの反応によっても影響を受け、合金の強化に関与する異なる析出物を促進します。異なる相の形成とその挙動の定義は、β(Mg2Si)、θ(Al₂Cu)、S(Al₂CuMg)またはQ(Al5Cu2Mg8Si6)など、いくつかの相が近接してまたは同時に析出する可能性があるため、複雑な作業です[23]。熱処理中、溶体化温度、冷却速度、時間は重要な役割を果たし、いくつかの複雑な相互作用をもたらします。最適な温度での時効処理は、強度と延性を低下させる可能性のある大きく非整合な粒子の析出を回避します。Fe、Mn、Crなどの他の元素の少量の組み合わせは、Al-Si合金の硬度と強度を向上させ、耐摩耗性を高めます[24]。
AlSiやAlSiCuMg(X)などの鋳造アルミニウム合金のトライボロジー研究に焦点を当てた研究[25–27]が最も多く行われています。高シリコンアルミニウム合金では、一般に、荷重の増加に伴い、摩耗メカニズムは延性剥離、アブレージョン、脆性剥離からプラウイングアブレージョン摩耗へと変化します[28]。アブレージョンと酸化は、軽度摩耗領域における主要な摩耗現象ですが、常にそうとは限りません。剥離、凝着、および激しい塑性変形は、AlSi9Cu3 HPDC合金の過酷摩耗領域で支配的です[23]。剥離は、表面下クラック核生成とその後のクラック伝播によって発生する表面層の塑性変形による大きな摩耗粒子の除去と関連付けられています[29,30]。このメカニズムは、表面下分離が接着して摩擦係数を増加させる移着層を形成する高温で特に顕著です[31]。さらに、高温での摩耗率は室温よりも10倍大きいと報告されています[32]。これらの条件下では、激しい塑性変形、材料および層の移着と蓄積を伴うスカッフィングメカニズムが発生する可能性があります。高温では層間の接着力が低下し、剥離が促進される可能性があります。
いくつかの研究では、摩耗メカニズムは温度によって、RTでの剥離から部分的なアブレージョン摩耗へ、150℃以上では塑性変形と酸化摩耗(塑性緩和メカニズムが支配的になる)へと変化します[33–36]。AlSi9Cu3合金では、異なる相の析出により、硬度、機械的および摩耗特性が低下します[23,24]。摩耗率は150℃よりも高い温度ではRTよりもはるかに高くなりますが、温度との線形比例関係はなく、約200℃で著しく増加します。AMCおよびアルミニウム合金における摩耗試験の温度上昇は、表面層のより高い緻密性と平均抵抗を促進し、粒子の酸化を加速します。表面層の破壊前に表面層が形成されると、摩耗率は減少します[6]。しかし、表面層が緻密でない場合、表面粒子が除去され、表面が損傷し、剥離が発生して摩耗率が増加します[23]。
軽度から過酷な摩耗への遷移メカニズムは、適用荷重、相手材ボール材料、滑り速度、接触面温度などの試験変数の組み合わせによって説明されます。通常、過酷摩耗は合金の熱軟化による大規模な塑性変形に関連しており、条件によっては、アルミニウム合金は剥離摩耗を制御しながら非過酷摩耗条件で動作することができます[9]。AlSiCu(Fe)鋳造合金で軽度摩耗メカニズムを得るための条件が研究されています[9,11,12,16,37–39]。
また、摩耗用途にコーティングを使用することへの関心が高まっていることも注目されます[40,41]。
ボールオンディスク(BOD)試験は、材料の摩耗特性を決定するために最も広く用いられる試験の1つです。ボールオンディスク試験データを分析する摩耗率メカニズムは、3つの主要な段階またはフェーズに分けることができます[42–45]。第1フェーズは、表面突起の変形と残留粒子数の増加により、母材とボール間の最大接着力で表面層が除去されることに対応します。第2フェーズは、通常、保護的なトライボケミカル表面層の形成、またはプラウイングと突起変形プロセスの減少に関連しています。ピン表面温度の上昇が、滑り面に酸化物層を形成し、軟質マトリックス材料が相手材ボール表面に露出するのを防ぎ、ピン表面の摩耗率を減少させるサブフェーズが存在する場合もあります[46,47]。第3フェーズは、トライボロジー条件の界面定常状態によって特徴付けられます。
摩耗率に対する適用荷重の影響は合金によって異なり、一部の合金は低荷重で低い摩耗率を示し、中程度の荷重で摩耗率が急激に増加し、高荷重で徐々に増加します。低い適用圧力は、通常、摩耗によって形成されたデブリが相手材表面の谷に捕捉されるのを促進します。デブリが谷に捕捉されるため、ディスクの突起による点接触が接触面にシフトします。接触面へのシフトとサンプルの加工硬化が定常状態摩耗につながりました[48,49]。
適用圧力の増加は温度上昇を示し、酸化物層の除去につながりました[48]。破断/断片化した酸化物層と相手材表面の摩耗デブリは、機械的混合層(MML)または移着膜(TF)の形成を引き起こす可能性があります。適用圧力の影響下で、移着膜(TF)の変形は摩耗デブリのひずみ硬化をもたらし、TFの硬度を高めます[48]。TFの絶え間ない形成と除去は、金属間の接触を防ぎ、摩耗率が定常状態摩耗領域で一定に保たれます。
軽度から過酷な摩耗値への遷移は、適用荷重に応じて約4~8Nから最大30Nまで変化する可能性があります[50]。一般に、比摩耗率の値は適用荷重の増加とともに増加します。
商用ブレーキローターの場合、摩擦係数(COF)の値は0.45~0.69の間です。一部の著者にとっては、荷重増加に伴うCOF値の線形増加はありません[51]。他の著者にとっては、例えばAl-Al2O3 MMCおよびAl-SiC MMC合金では、ブレーキローター用途で0.30~0.60の安定した摩擦係数を持つ線形増加があります[52]。
ドラムブレーキの軽度または過酷な摩耗状態を定義するために報告されている摩耗率は異なります。Al7.1Si合金ではk = 15 × 10⁻³ mm³/N·m[53]、LM17合金では6 × 10⁻³ mm³/N·m、圧力と速度(それぞれ0.2–1.0 N/mm²および1.6 m/s)がブレーキローターの制動条件を代表するアルミニウム複合材では7.5–10 × 10⁻³ mm³/N·m[54]で過酷な摩耗率が報告されています。ブレーキローター用途向けのルチルおよびシリマナイト鉱物ハイブリッドAMC(HAMC)で強化されたLM27合金は、商用ローター材料で500mで約16.5 × 10⁻³ mm³/N·m、HAMCで18 × 10⁻³ mm³/N·mの摩耗率を示し、最終的な定常摩耗値はそれぞれ約6および7 × 10⁻³ mm³/N·mでした。0.37x10⁻⁴~2.37x10⁻⁴ mm³/N·mの値は、一般的に過酷摩耗領域内にあります[55]。しかし、アルミニウム鋳造合金の場合、15Nの試験力では、約5 × 10⁻³ mm³/N·mです[56]。試験荷重を決定するために、試験された合金によって参考文献データの変動が大きいため、アルミニウムブレーキに関する参考文献情報と結果を比較するために15Nが選択されました[56]。
ボール材料の選択は最終結果を変える可能性があるため重要です。アルミニウム合金では、鋼球を使用するとアルミニウムと鋼の親和性[55–57]のため、試験中にAl-Fe-Oを含むMMLの形成を避けるために、アルミナがボール材料としてしばしば使用され、最小限の化学駆動凝着による接着摩耗の化学駆動側面を最小化します。したがって、アルミニウム合金が摩耗特性に及ぼす影響の判断は、アルミナカウンターボールの方が容易です[58]。
新たに開発されたA180Mg10Si5Cu5合金は、約200℃までその特性を維持するように設計されており、合金元素の選択は、Mg2SiおよびAl₂Cu金属間化合物相(耐摩耗性を向上させる)を得るが、初晶Siは存在しない(より良い機械的特性と延性を得るため)ように慎重に決定されました。新たに開発された合金の用途は、アルミニウム製ドラムブレーキ、特に小型電気自動車の後輪ブレーキである可能性があります。
最近、スクラップ許容性のあるAl65Cu10Mg10Si10Zn5およびAl80Cu5Mg5Si5Zn5 HEAアルミニウム合金が研究され、有望な機械的および摩耗特性を示していますが[59]、HEAアルミニウム合金の摩耗特性に関する情報はまだ非常に少なく、二次アルミニウム合金またはスクラップに基づく工業プロセスで製造された材料に関する情報はさらに少ないです。二次アルミニウムインゴット、鋳造アルミニウムリターン材、およびマグネシウムスクラップを電気るつぼ炉で溶解し、HPDCプロセスを使用して低いCO2製造値を得ました[60]。
したがって、本研究では、開発された合金をRTおよび200℃で研究し、鋳放しおよび熱処理(TT)状態で最も標準的な鋳造合金(AlSi9Cu3合金)と比較します。
並行して、HPDCで製造されたアルミニウム鋳造部品は、外面にスキン領域(または表面層)を示し、これは欠陥がほとんどなく、機械的特性が向上しています[61]。しかし、ボールオンディスク(BOD)試験において外面層を維持することが摩耗特性に及ぼす影響は、研究されていないか、非常にまれにしか研究されていません[62]。
4. 研究の概要:
研究トピックの背景:
自動車産業、特に電気自動車(EV)における軽量化の推進により、低密度のアルミニウム合金に対する需要が高まっています。高圧ダイカスト(HPDC)は、これらの部品を製造するための重要なプロセスです。一般的なAlSiCu合金には限界がありますが、多成分合金は特性向上の可能性を提供します。アルミニウム製ドラムブレーキは、後輪の制動力が低く、鋳鉄よりも軽量であるため、EVに検討されています。しかし、アルミニウム合金の耐摩耗性は依然として課題です。
先行研究の状況:
標準的なAlSiCuおよびAlSiMgCu合金はHPDCで広く使用されており、特性向上のためにしばしば熱処理が必要です。Al合金の耐摩耗性は、合金元素(Si、Mg、Cu)の制御、強化相の導入(アルミニウムマトリックス複合材料、AMCなど)、または熱処理によって改善できます。AMCは優れた特性を提供しますが、高コスト、複雑なプロセス、および低いリサイクル性という欠点があります。非AMC合金の場合、Si含有量は硬度を増加させ(Mg2Si形成)、Cu添加はAl₂Cuを形成して硬度を高め、他の元素(Fe、Mn、Cr)も寄与します。Al合金の摩耗メカニズムは、通常、アブレージョン、酸化、剥離を含み、温度(摩耗はしばしば150〜200℃以上で著しく増加)と荷重に大きく影響され、軽度領域から過酷領域へと遷移します。ボールオンディスク(BOD)試験は、トライボロジー特性を評価するための一般的な方法です。HPDC部品は、微細な粒子の表面「スキン」を特徴とし、特性が向上していますが、摩耗への影響はほとんど研究されていません。
研究の目的:
本研究は、200℃までの耐摩耗性のために設計された新規多成分合金Al80Mg10Si5Cu5のトライボロジー特性(摩擦および摩耗)を調査することを目的としました。この研究では、二次材料を使用してHPDCで製造されたこの合金を、標準のAlSi9Cu3合金と比較しました。主な目的には、室温(RT)および200℃での性能評価、特に鋳放し状態の外面層(スキン)を維持した場合と機械加工された表面を試験した場合の影響評価が含まれます。対象となる潜在的な用途は、自動車用の軽量アルミニウムドラムブレーキです。
核心研究:
研究の核心は、新規Al80Mg10Si5Cu5合金および参照AlSi9Cu3合金の試験サンプルを、二次アルミニウムを使用して工業用HPDCプロセスで製造することでした。一部のAl80Mg10Si5Cu5サンプルは、溶体化熱処理(TT)を受けました。トライボロジー性能は、RTおよび200℃の両方で、アルミナカウンターボールに対して乾燥滑り条件下でボールオンディスク(BOD)摩耗試験を使用して評価されました。試験は、元のHPDC表面スキンを維持したサンプルと、スキンを除去した(研磨された表面)サンプルに対して実施されました。微細構造(光学顕微鏡、SEM/EDS)、相組成(XRD)、および硬度(ビッカース、RT&200℃)が特性評価されました。この研究では、新規合金と標準合金の摩擦係数および比摩耗率を比較し、表面スキンの影響、熱処理の影響、および高温が摩耗挙動とメカニズムに及ぼす影響を分析しました。
5. 研究方法論
研究デザイン:
本研究では比較実験デザインを採用しました。新規開発されたAl80Mg10Si5Cu5合金を標準参照合金であるAlSi9Cu3と比較しました。両合金はHPDCを用いて製造されました。実験変数は、合金タイプ、鋳放し表面スキンの有無、材料状態(新規合金の鋳放し対熱処理)、試験温度(室温対200℃)を含みました。
データ収集および分析方法:
- 製造: 950t機を用いて高圧ダイカスト(HPDC)によりサンプルを製造。二次Al合金とリターン材を装入材料として使用。一部のAl80Mg10Si5Cu5サンプルは溶体化処理(440℃、72時間)後、水焼入れ(75℃)および自然時効(TT状態)を実施。
- 化学組成分析: 発光分光分析(OES)を使用。
- 微細構造解析: 光学顕微鏡(MO)およびエネルギー分散型X線分光法(EDS)を装備した走査型電子顕微鏡(SEM)を用いて特性評価。標準的な金属組織学的試料作製手順に従った。
- 相同定: Cu-Kα放射線を用いたX線回折(XRD)により実施。
- 硬度試験: UNE EN ISO 6507-1に従い、RTおよび200℃にてビッカースダイヤモンド圧子(HV3)を用いて測定。
- 摩耗・摩擦試験: ASTM G99-05に従い、乾燥滑り、往復動モード(球-平板構成)のボールオンディスク型トライボメーターを用いて実施。RTおよび200℃にて、6mmアルミナボールカウンターフェース、荷重15N、滑り速度0.1m/s、総滑り距離500mで試験実施。摩擦係数(COF)は連続的に記録。
- 摩耗率測定: 3Dレーザー走査型共焦点顕微鏡を用いて摩耗痕の体積損失を決定。比摩耗率(w)は式(1): w = V / (s x F)を用いて算出。
- 摩耗表面/表面下分析: SEM/EDSおよびOMによる断面分析を用いて摩耗メカニズムを決定。
研究トピックと範囲:
本研究は、新規Al80Mg10Si5Cu5多成分合金と従来のAlSi9Cu3合金のトライボロジー特性(摩擦および摩耗)に焦点を当てました。範囲は以下の通りです:
- HPDC鋳放し表面層(スキン)が摩耗および摩擦に及ぼす影響の評価。
- 特定の溶体化処理(TT)がAl80Mg10Si5Cu5合金のトライボロジー性能に及ぼす影響の評価。
- 高温(200℃)が室温(RT)と比較して摩擦、摩耗率、摩耗メカニズムに及ぼす影響の調査。
- 異なる条件下での合金の微細構造、相、硬度の特性評価。
- 試験は、特定のBODパラメータ(15N荷重、0.1m/s速度、アルミナカウンターフェース)を用いた乾燥滑り条件に限定されました。
6. 主要な結果:
主要な結果:
- 硬度: 新規Al80Mg10Si5Cu5合金は、鋳放しおよび熱処理(TT)状態の両方で、RTおよび200℃の両方において、参照AlSi9Cu3合金よりも高い硬度を示しました。表面層(スキン)は、微細な微細構造のため、内部材料よりも一貫してわずかに高い硬度を示しました。TT状態は、Al80Mg10Si5Cu5合金の鋳放し状態と比較して硬度が低下しました。
- 摩擦 (COF): RTでは、両合金(鋳放し)はほぼ同様の定常状態COF値(約0.37-0.39)を示しました。200℃では、顕著な差が現れました: Al80Mg10Si5Cu5は比較的低いCOF(鋳放しで約0.41-0.42、TTで約0.50-0.53)を維持しましたが、AlSi9Cu3ははるかに高いCOF(スキンありで約0.64、スキンなしで約0.80)を示しました。表面スキンの存在は、特に初期段階において、一般的にわずかに低いCOF値をもたらしました。TT-Al80Mg10Si5Cu5は、200℃において鋳放しバージョンよりも高いCOFを示しました。すべての試験で典型的な3段階の摩擦曲線が示されました(初期のなじみ段階が抑制された200℃を除く)。
- 摩耗率: Al80Mg10Si5Cu5合金は、AlSi9Cu3よりも著しく優れた耐摩耗性を示しました。RTでは、スキン付きの鋳放しAl80Mg10Si5Cu5が最も低い摩耗率(4.9 x 10⁻⁴ mm³/N·m)を示しました。スキンを除去すると、鋳放しAl80Mg10Si5Cu5では約50%、AlSi9Cu3では約57%摩耗が増加しました。200℃では、Al80Mg10Si5Cu5の耐摩耗性の利点はさらに顕著になり、AlSi9Cu3よりも約10倍低い摩耗率を示しました(例: スキンなしサンプルで4.4 x 10⁻³ 対 44.8 x 10⁻³ mm³/N·m)。表面スキンは、両方の温度で一貫して摩耗率を低減しました。注目すべきは、熱処理(TT)が、RTおよび200℃の両方で、鋳放し状態と比較してAl80Mg10Si5Cu5合金の摩耗率を増加させたことです。
- 摩耗メカニズム: 鋳放しAl80Mg10Si5Cu5の場合、RTおよび200℃の両方でアブレージョンが主要な摩耗メカニズムであり、軽度摩耗を示しました。TT-Al80Mg10Si5Cu5の場合、一部の延性剥離を伴うアブレージョンが観察され、RTではより多くのクラックを伴う軽度摩耗、200℃では軽度から過酷な摩耗に分類されました。AlSi9Cu3合金は、RTでは延性剥離を伴うアブレージョン(軽度-過酷の兆候)を示し、200℃では主に過酷な延性剥離を示しました。SEM/EDS分析により、観察された摩耗挙動における微細構造(より微細なスキン)、相(Mg2Si、Al₂Cu、Al₂CuMg)、酸化、およびデブリ形成の役割が確認されました。
- カウンターボール分析: すべての試験において、アルミナカウンターボールへの材料移着(凝着)が観察され、これは200℃、特にAlSi9Cu3合金でより顕著でした。
図のリスト (Figure Name List):
- Fig. 1. Detail of tribometer employment and their components.
- Fig. 2. Detail of wearing surface topography.
- Fig. 3. XRD analysis of as-cast A180Mg10Si5Cu5 alloy.
- Fig. 4. XRD analysis of heat-treated A180Mg10Si5Cu5 alloy.
- Fig. 5. Analyzed phases in as-cast A180Mg10Si5Cu5 alloy.
- Fig. 6. Surface cast layer backscattered SEM images (x400 augmentation) of as-cast A180Mg10Si5Cu5 alloy.
- Fig. 7. Prepared sample backscattered SEM images (x400 augmentation) of as-cast A180Mg10Si5Cu5 alloy.
- Fig. 8. Surface cast layer sample SEM images (x400 augmentation) of the heat-treated A180Mg10Si5Cu5 alloy.
- Fig. 9. Inner region sample SEM images (x400 augmentation) of the heat-treated A180Mg10Si5Cu5 alloy.
- Fig. 10. Outside region optical microscopy images (x200 augmentation) of as-cast AlSi9Cu3 alloy.
- Fig. 11. Inner region optical microscopy images (x200 augmentation) of as-cast AlSi9Cu3 alloy.
- Fig. 12. Evolution of the coefficient of friction for the studied alloys at RT (0.1 m/s) with the surface layer.
- Fig. 13. Evolution of the coefficient of friction for the studied alloys at RT (0.1 m/s) without the surface layer.
- Fig. 14. Evolution of coefficient of friction for the experimental alloys at 200 °C (0,1 m/s) with the surface layer.
- Fig. 15. Evolution of coefficient of friction for the experimental alloys at 200 °C (0,1 m/s) without the surface layer.
- Fig. 16. Wear profiles at RT and 200 °C.
- Fig. 17. Material track area after BOD tests. (a) As-cast A180Mg10Si5Cu5 RT, (b) TT-A180Mg10Si5Cu5 RT, (c) As-cast AlSi9Cu3 RT, (d) As-cast A180Mg10Si5Cu5 200 °C, (e) TT-A180Mg10Si5Cu5 200 °C, (f) As-cast AlSi9Cu3 200 °C.
- Fig. 18. Material track thickness determination at RT: (a) As-cast A180Mg10Si5Cu5 RT, (b) TT-A180Mg10Si5Cu5 RT, (c) As-cast AlSi9Cu3 RT, and at 200 °C: (d) As-cast A180Mg10Si5Cu5, (e) TT-A180Mg10Si5Cu5, (f) As-cast AlSi9Cu3.
- Fig. 19. SEM images of worn surface tested at RT for as-cast A180Mg10Si5Cu5. (a), (b) and (c) = With surface layer at the magnification of×40, ×400 and x800. (d), (e) and (f) = Without surface layer at the magnification of×40, × 400 and x800.
- Fig. 20. SEM images of worn surface tested at RT for heat-treated A180Mg10Si5Cu5. (a), (b) and (c) = With surface layer at the magnification of×40, ×400 and x800. (d), (e) and (f) = Without surface layer at the magnification of×40, ×400 and x800.
- Fig. 21. SEM images of worn surface tested at RT for as-cast AlSi9Cu3. (a), (b) and (c) = With surface layer at the magnification of×40, ×400 and x800. (d), (e) and (f) = Without surface layer at the magnification of×40, × 400 and x800.
- Fig. 22. SEM images of worn surface for as-cast A180Mg10Si5Cu5. (a), (b) and (c) = With surface layer at the magnification of×40, ×400 and x800. (d), (e) and (f) = Without surface layer at the magnification of×40, ×400 and ×800 at 200 °C.
- Fig. 23. SEM images of worn surface for TT-A180Mg10Si5Cu5. (a), (b) and (c) = With surface layer at the magnification of×40, ×400 and x800. (d), (e) and (f) = Without surface layer at the magnification of×40, ×400 and ×800 at 200 °C.
- Fig. 24. SEM images of worn surface for as-cast AlSi9Cu3. (a), (b) and (c) = With skin at the magnification of×40, ×400 and x800. (d), (e) and (f) = Without skin at the magnification of×40, × 400, ×800 at 200 °C.
- Fig. 25. OM cross-section micrographs of the wear tracks tested at RT for as-cast A180Mg10Si5Cu5 at x100 (a), x200 (b), and ×500 (c) and as-cast AlSi9Cu3 at x100 (d), x200 (e) and ×500 (f).
- Fig. 26. OM cross-section micrographs of the wear tracks tested at 200 °C for as-cast A180Mg10Si5Cu5 at x100 (a), x200 (b), x500 (c), as-cast AlSi9Cu3 at ×100 (d), x200 (e) and ×500 (f).
7. 結論:
本論文は、新規A180Mg10Si5Cu5鋳造合金の摩擦および摩耗特性を包括的に調査し、鋳放しおよび熱処理状態においてRTおよび200℃でAlSi9Cu3鋳造合金と比較し、ダイカスト部品の外面スキンの影響も含めて分析しました。結論は以下の通りです:
(1) →HPDC用に開発された新規A180Mg10Si5Cu5合金は、RTにおいて標準AlSi9Cu3合金と比較して強化された耐摩耗性(摩耗率で+50%の低減)を特徴とします。この改善は、表面および表面下の硬度、ならびに新規合金の微細構造の種類と形態に起因し、アブレージョンが主な摩耗メカニズムです。AlSi9Cu3合金は、一部の延性剥離を伴うアブレージョンを示し、より高い比摩耗率を示しました。RTにおいて、A180Mg10Si5Cu5合金は軽度摩耗率を示し、AlSi9Cu3は一部の過酷摩耗の兆候を伴う軽度摩耗を示しました。
(2) →200℃では、摩耗率とCOF値が高くなります。表面層を持つ鋳放し状態のA180Mg10Si5Cu5合金は、アブレージョン摩耗を示し、再び最も低い摩耗率を示し、軽度摩耗を示しました。TT-A180Mg10Si5Cu5合金は、鋳放しA180Mg10Si5Cu5合金と比較して、優勢な二次延性剥離摩耗メカニズムとともにアブレージョンを示し、一部の過酷摩耗の兆候を伴う軽度摩耗を示しました。鋳放しAlSi9Cu3合金は、最も高い摩耗率(摩耗率で10倍の低減)を示し、主に延性剥離メカニズムを示し、過酷摩耗を示しました。
(3) →表面層を持つサンプルは、より高い硬度、より良い微細構造、および減少した品質欠陥のため、低いCOF値と比摩耗率を示しました。HPDC鋳造部品の機械加工を避けることは、摩耗条件下での使用中の性能を向上させる可能性があります。
(4) → 新規開発された合金は、アルミニウム製ドラムブレーキのための費用対効果が高く低CO2の代替品として有望です。二次アルミニウム合金から得られる性能特性により利点を提供し、これはまた鉄よりも軽量であり、潜在的に燃料効率を向上させます。さらに、その製造に使用されるHPDCプロセスは、他の利点の中でもサイクルタイムの短縮をもたらします。
8. 参考文献 (References):
- [References] - (参考文献リストは原文通りとします)
- [1] P. Sharma, V.K. Dwivedi, S.P. Dwivedi, Development of high entropy alloys: a review, Mater. Today: Proc. 43 (1) (2021) 502–509, https://doi.org/10.1016/j.matpr.2020.12.023.
- [2] S. Salifu, P.A. Olubambi, Effects of fabrication techniques on the mechanical properties of high entropy alloys: a review, Int. J. Lightweight Mater Manufact (2023) 13–53, https://doi.org/10.1016/j.ijlmm.2023.08.001.
- … (以下、全ての参考文献は原文通り) …
- [96] G. Plasensia, A.T. Utigard, High temperature oxidation mechanism of dilute copper aluminium alloys, Corrosion Sci. 47 (2005) 1149–1163, https://doi.org/10.1016/j.corsci.2004.06.031.
9. 著作権:
- 本資料は、「Ester Villanueva, Iban Vicario, Joseba Albizuri, Gurutze Arruebarrena, Teresa Guraya」氏による論文です。「Wear properties of a new Al80Mg10Si5Cu5 multicomponent alloy」に基づいています。
- 論文の出典: https://doi.org/10.1016/j.wear.2024.205585
本資料は上記の論文に基づいて要約したものであり、商業目的での無断使用は禁じられています。
Copyright © 2025 CASTMAN. All rights reserved.