本稿は、「[MDPI]」によって公開された論文「[Automated Defect Detection through Flaw Grading in Non-Destructive Testing Digital X-ray Radiography]」に基づいています。
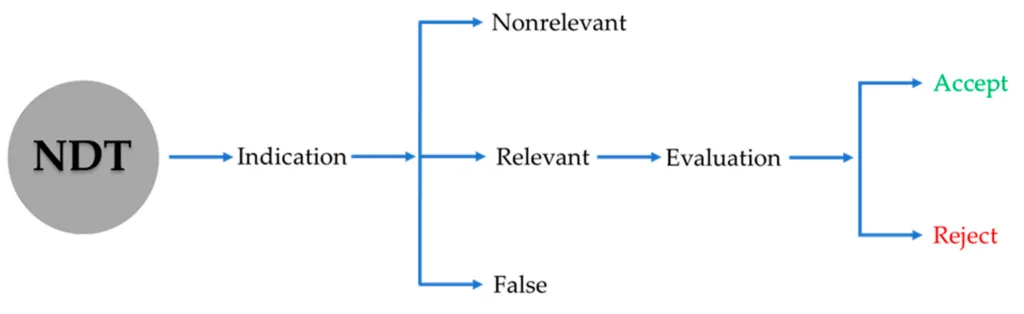
1. 概要:
- 論文タイトル: Automated Defect Detection through Flaw Grading in Non-Destructive Testing Digital X-ray Radiography (非破壊検査デジタルX線ラジオグラフィにおける欠陥等級判定による自動欠陥検出)
- 著者: Bata Hena, Gabriel Ramos, Clemente Ibarra-Castanedo, Xavier Maldague
- 発行年: 2024
- 発行学術誌/学会: NDT
- キーワード: 非破壊検査; デジタルX線ラジオグラフィ; 機械学習; 自動欠陥認識; 欠陥等級判定; K-Dツリー (non-destructive testing; digital X-ray radiography; machine learning; automated defect recognition; defect grading; K-D tree)
2. 抄録:
プロセスオートメーションは、特殊な技術と装置を利用して生産プロセスを自動化および強化し、より高い製造効率、生産性、コスト削減をもたらします。アルミニウムダイカスト産業は、自動車や航空宇宙などの安全性が重要な分野に部品を供給する製造において、プロセスオートメーションソリューションの導入から大きな恩恵を受けてきました。しかし、この部品製造方法は製造上のきず(flaw)を生成しやすく、そのため、これらの部品の使用適合性を確認するために適切な非破壊検査(NDT)が必要となります。近年、機械学習はデジタルX線ラジオグラフィにおけるきずの検出と分類のための自動化ソリューション開発ツールとして中心的な役割を担っています。これらの機械学習ベースのソリューションは、製造業における高い生産スループットに対応するため、部品検査用にますます開発・導入されています。本研究は、検出されたきずが部品を使用不適格にする可能性のある欠陥(defect)に該当するかどうかを評価する欠陥等級判定アルゴリズムの開発に焦点を当てています。ASTM 2973-15(アルミニウムおよびマグネシウムダイカスト検査のための標準デジタル参照画像)に導かれ、K-D(k次元)ツリーを利用した等級判定パイプラインが開発され、検出されたきずを効果的に構造化し、システムが許容可能な等級判定基準に基づいて決定を下せるようにしました。このソリューションは、異なる等級判定基準への適合性という点で動的であり、デジタルX線ラジオグラフィアプリケーションにおける自動意思決定(合否判定)を実現する可能性を提供します。
3. 緒言:
プロセスオートメーションは、特殊な技術と装置を利用して生産を強化し、ハードウェア、ソフトウェア、ITを組み合わせて製造オペレーションを管理・制御することで、より高い製造効率、生産性、コスト削減を実現します[1]。アルミニウムダイカスト(ADC)産業は、製造におけるプロセスオートメーションソリューションの導入から大きな恩恵を受けており、自動車や航空宇宙産業などの分野に供給されるアルミニウムダイカスト部品の非常に高い生産スループットを達成しています[2]。この製造技術は、溶融アルミニウム合金を金型に注入し、金型を冷却して部品を取り出す工程を含みます。しかし、この生産方法は関連するプロセスにより製造上のきずが発生しやすく、適切なモニタリングが必要です[3]。それでもなお、アルミニウムダイカスト(ADC)は、製品の軽量化、大量生産要件に対する競争力のあるコスト、高い生産スループット、より高いプロセス自動化の可能性、およびより良い製品の一貫性など、他の製造プロセスに比べていくつかの利点を提供します[4]。
製造されたアルミニウムダイカスト部品の欠陥が見過ごされることがどれほど危険であるかを考えると、要求される製造部品に対して適切なNDT検査を実施することが不可欠です[5]。NDT技術(ラジオグラフィ、超音波探傷、目視検査、赤外線サーモグラフィ、液体浸透探傷、渦電流探傷など)は、部品に損傷を与えたり機能を損なったりすることなく、きずの検出を可能にする様々な技術を提供します[6]。研究によると、ラジオグラフィはアルミニウムダイカスト部品の品質を評価するために使用される様々なNDT手法の中で最も好まれる方法として際立っています[7]。この何世紀も前からあるラジオグラフィ手順は、材料を透過するのに十分な強度のX線またはガンマ線を使用し、検査対象部品の体積全体を徹底的に検査することを可能にします[8]。X線は人間の自然な視覚では見えないため、画像取得中にX線信号に含まれる潜在的な情報を明らかにするために、デジタル検出器アレイ(DDA)、光子計数検出器、X線フィルムなどのセンサーを使用する必要があります。
デジタルラジオグラフィ(DR)は、従来のフィルムラジオグラフィの使用をますます置き換えています。このイメージングモードでは、検出器の感応ユニット(ピクセル)によって捕捉されたX線光子が数値に変換されます。さらに、視覚的な訴求力と人間の理解を容易にするために、ピクセル値の2Dマトリックスがグレースケール分布に変換され、デジタルラジオグラフが形成されます。デジタルラジオグラフィ画像は計算処理に有用です[9-12]。したがって、画像特性の様々な後処理調整(例:知覚可能なコントラスト、シャープネス、明るさ)や他の画像フィルタリングプロセスがデジタルラジオグラフィ画像で可能です。DRシステムの適切な性能を確保し、NDTでのデジタル画像の使用を完全に統合するために、関連する規格が確立されています。NDT規格をラジオグラフィ試験に組み込むことは、様々な産業全体で正確で信頼性の高い検査を保証するために重要です。NDT規格は、ラジオグラフィ技術、露出パラメータ、画質、および結果の解釈に関する必須のガイドラインを提供します。これらの規格は、亀裂や介在物などのきずを検出することが安全性と品質保証にとって重要である航空宇宙や自動車などの産業で広く適用されています。これらの規格を理解し、遵守することは、ラジオグラフィ検査の一貫性と信頼性を高め、NDTプロセスの不可欠な部分となります。米国機械学会(ASME)、米国材料試験協会(ASTM)、国際標準化機構(ISO)などの団体は、NDT産業内の実践の標準化に対する規制監督を提供しています。産業におけるNDT実践の理想的なケースは、NDT検査員の資格に関する運用NDT規格(例:ISO 9712)の要件を満たした有資格のNDT検査員によってNDT検査が実施されることです。そのような訓練された検査員は、関連する運用NDT規格に従ってラジオグラフィ画像を取得し、解釈します[13]。画質が許容可能であると見なされた後、検査員は関連する検出された指示に焦点を当て、部品が受け入れられるか拒否されるかを評価し、決定します(図1参照)。NDT実践における潜在的なエラーを防ぐための規制があるにもかかわらず、NDT検査員が人間であるためにエラーを犯す可能性を排除するのは誤りです[14, 15]。NDT検査員によるラジオグラフィ画像の解釈は、疲労、検査経験、精神状態などの要因によって影響を受ける可能性があります。したがって、構造化された規制ガイドラインのセットを実施した後でも、ある研究では視覚的な人間による解釈の有効性が約80%であることがわかりました[16]。
近年の計算能力の向上に伴い、非破壊検査(NDT)プロセスを自動化するアイデアが考案され、開発され、製造された部品の100%検査を達成するための実行可能な道筋が提供されています。NDTデータからのきずの認識と評価を自動化するための人工知能(AI)ソリューションの使用は、特に材料のラジオグラフィ画像におけるきずの識別のために、NDT分野の多くの研究者によって広く探求されてきたアプローチです[17]。この自動化は、伝統的に人間のオペレーターによって実行されてきたタスクを自動化する必要性の高まりによって推進されています[18]。プロセスオートメーションを活用した製造業におけるNDTの需要増加と、この増大する検査ニーズを満たすための有資格NDT検査員の減少を考慮すると、非破壊検査におけるAI使用の必要性はますます明らかになります[19]。コンピュータビジョンベースのソリューションは有益である可能性がありますが、安全性が重要な分野での受け入れを促進するためには、関連する運用NDT規格に従って開発および適用されなければなりません。
4. 研究の概要:
研究トピックの背景:
アルミニウムダイカスト(ADC)部品は広く使用されていますが、内部の製造上のきず(flaw)の影響を受けやすいです[20, 21]。自動化されたダイカストにおける高い生産スループットは、時間、コスト、および検査タスクを実施するための有資格NDT人員の不足といった交絡因子の影響により、製造されたすべての部品を検査することを困難にしています。統計的サンプリングを使用する産業もありますが、これは製造されたすべての部品の100%検査には劣ります。コンピュータベースのNDT、特にデジタルX線ラジオグラフィは、100%検査への道を提供します。ADC部品はしばしば重要な機能を果たし、その故障は重大な経済的および安全上の影響を引き起こす可能性があります[22]。効果的なNDTを通じてこれらの部品の品質と完全性を確保することが最も重要です。
先行研究の状況:
デジタルX線ラジオグラフィを用いた自動欠陥認識(ADR)は、ADCの品質管理においてますます重要になっています。先行研究ではADRアルゴリズムが探求されてきました。例えば、オブジェクト検出手法(YOLO、RetinaNet、EfficientDet)は欠陥識別の支援において有望であることが示されました[23]。YOLOv3_EfficientNet[24]や様々な畳み込みニューラルネットワーク(CNN)[25, 26]などの深層学習モデルが、きず検出を合理化するために適用され、より良い精度のためのアーキテクチャの継続的な改良を示しています。しかし、複雑な欠陥形状、様々なラジオグラフィ条件[26]、深層学習モデルが様々なきずタイプや鋳造条件にわたって効果的に一般化するために必要な広範なトレーニングデータ[23]、および高度なCNNの高い計算要件がリアルタイムの産業応用を妨げる[25]など、課題は残っています。決定的に重要なのは、きずの識別と特性評価において実質的な進歩が存在する一方で[17, 28]、検出されたきずの重大度と影響を判断して使用適合性を評価する欠陥等級判定は、まだ十分に研究されていない分野であるということです。既存の研究では、運用基準に従った明確な等級判定プロセスなしに、検出された不連続部をきずまたは欠陥として扱うことがよくあります[29-31]。
研究の目的:
本研究は、包括的なきず等級判定アルゴリズムを開発することにより、ADRにおけるギャップを埋めることを目的としています。目的は以下の通りです:
- 検出されたきずを、参照規格(ASTM E2973-15など)または顧客固有の仕様に合わせた異なる重大度レベルに分類する等級判定アルゴリズムを開発すること。
- 単純な検出を超えて適格な等級判定に進む方法を提案することにより、安全性が重要な分野におけるADRソリューションの統合を強化すること。
- 等級判定プロセスにおける精度と解釈可能性を向上させるために、決定論的な結果を生み出すコンピュータビジョン技術を実装すること。
動機は、NDT規格(具体的にはASTM E2973-15およびASTM E1316の用語)に基づいて、検出されたきず(不完全性)を評価し、それらが拒否可能な欠陥(defect)を構成するかどうかを判断するための体系的なアプローチを提供し、それによってアルミニウムダイカストの品質管理を改善することです。
コア研究:
本研究の核心は、アルミニウムおよびマグネシウムダイカストのデジタルX線ラジオグラフィ画像のための新しいきず等級判定方法論の開発と適用です。この方法論は、他のアルゴリズムによって実行される初期の検出および特性評価段階に続きます。これは特に、気孔、湯回り不良、引け巣、異物などの不連続性の異なる重大度レベルに対するデジタル参照画像を提供するASTM E2973-15規格によって主に導かれる、確立された基準に基づいて検出されたきずを等級判定することに焦点を当てています[27]。
本研究は、ASTM E1316で定義されている重要な区別を強調しています:
- 不連続部 (Discontinuity): 材料構造の中断。
- きず (Flaw): 検出可能であるが、必ずしも拒否可能ではない不完全性または不連続部。
- 欠陥 (Defect): その特性(サイズ、形状、位置など)が指定された受け入れ基準に違反し、部品を拒否可能にする1つ以上のきず。
開発されたアルゴリズムは、検出され特性評価されたきず(通常はセグメンテーションマスクとして入力される)を受け取り、規格(またはカスタム基準)から導出された等級判定ルールに照らして評価し、それらが欠陥に該当するかどうかを判断し、最終的に合否判定を下します。等級判定プロセスは、定義された評価領域(ASTM E2973に従って700mm²)内のきず面積や数量などのきず特性を考慮します。この方法論の重要な構成要素は、検出されたきずの効率的な空間的構成とクエリのためのK-Dツリーデータ構造の使用です。
5. 研究方法論
研究設計:
本研究は、きずの検出、セグメンテーション、および特性評価ステップに続く独立したパイプラインとして意図された、きず等級判定アルゴリズムを設計します。入力は、個別のきずとそのクラスを識別するセグメンテーションマスクであると想定されます。出力は、等級判定に基づく合否判定です。等級判定ロジックは、ASTM E2973-15規格から導出されたルールに基づいており、4つのきずカテゴリ(気孔、引け巣、湯回り不良、異物)に焦点を当てています。
主要な方法論的ステップは以下の通りです:
- 入力処理: 入力画像内で異なるきずクラスが識別可能な(例えば、研究の合成データ生成で行われたカラーコーディングによる - 図3、表1参照)セグメント化された画像の受信。
- クラス分離: 入力画像に存在する各きずクラスに対するバイナリマスクの生成。
- きず特性抽出: 各クラス固有のバイナリマスクについて、画像解析ライブラリ(
skimage.measure.regionprops
)を使用して個々のきずの特性(例:面積)を抽出。 - 空間インデックス作成: 効率的な空間クエリのために、検出されたきずの重心を使用してK-D(k次元)ツリーを構築[32, 33]。これにより、特定の関心領域(ROI)内のきずを迅速に検索することが容易になります。
- ROI管理と反復: ROI(700mm²評価領域)を定義するためにスライディングウィンドウアプローチを採用。K-Dツリーと組み合わせて「ストライド関数」を使用し、画像を効率的にナビゲートし、ROIをきずを含む次の領域に動的に移動させ、空の領域の処理を回避。
- 等級判定ロジック適用: 各ROI内で、ROI内のきずを検索するためにK-Dツリーをクエリし、それらのサイズ(面積)と数量を定義された重大度レベル基準に対して評価することにより、等級判定ルール(ASTM E2973用語から導出された表2に基づく)を適用。
- 決定集約と報告: すべてのROIにわたる等級判定結果を集約し、潜在的に視覚化(等級判定マップなど)を伴う最終報告書を生成。全体的な方法論は図5に概略的に示されています。K-Dツリーは、このアプリケーションの2D空間コンテキストにおける効率性と複雑性のバランスから、Rツリー[34]のような代替手段よりも選択されました。
データ収集と分析方法:
等級判定パイプラインをテストおよび検証するために、テスト画像が合成的に生成されました。4つのクラス(気孔、引け巣、湯回り不良、異物)について、様々なサイズと形態を持つ実際のきず(アルミニウムダイカスト部品のグラウンドトゥルースアノテーションから)が抽出され、きずのリポジトリが形成されました。これらの抽出されたきずは、その後、背景画像上にランダムに配置されました。各きずクラスには、後続の処理ステップによる識別のために、固有のカラーコードが割り当てられました(表1)。(図4aは生成されたきずを示し、4bはカラーコード化された分類を示します)。この合成アプローチにより、様々なきず分布を持つ多様なデータセットの作成が可能になりました。
ASTM E2973-15規格は参照画像を使用します(例:気孔については図2)。計算アプリケーションのために、これらの視覚的参照は、700mm²の検査領域内のきず面積と数量に基づく定量的なデジタルメトリック(等級判定ルール)に変換されました。きず面積範囲と700mm²あたりの最大数量に基づいて重大度等級(1〜4)を定義するカスタム参照表(表2)が研究に使用されました。skimage.measure.regionprops
ライブラリは、バイナリマスクから検出されたきず(ブロブ)の幾何学的特性(面積など)を抽出するために使用されました。K-Dツリーは、きずの重心を空間的に整理することにより、効率的な分析を可能にしました。
研究トピックと範囲:
本研究は、アルミニウムおよびマグネシウムダイカストのデジタルX線ラジオグラフィ画像で検出されたきずの自動等級判定に焦点を当てています。範囲は、ASTM E2973-15で定義されている4つの不連続性カテゴリ(気孔、引け巣、湯回り不良、異物)に限定されます。中心的なタスクは、この規格(またはカスタマイズ可能な顧客基準)から導出された基準に対して検出されたきずを評価し、それらが拒否可能な欠陥に該当するかどうかを判断することです。方法論には、2Dラジオグラフィ画像の処理、きず特性の抽出、定義された評価領域(700mm²)内での効率的な空間分析のためのK-Dツリーの利用、およびきずのサイズと数量に基づく特定の等級判定ルールの適用が含まれます。本研究は、きずの事前の検出と分類を前提として、等級判定アルゴリズム自体を開発します。
6. 主要な結果:
主要な結果:
開発された等級判定パイプラインの主要な出力は、処理された入力画像上のオーバーレイとして表示され、等級判定ルールが適用された活性化された関心領域(ROI)を強調表示します(図6)。結果は、より良い視覚化と容易な人間による検証のために、各きずクラス(気孔 - 行a、引け巣 - 行b、湯回り不良 - 行c、異物 - 行d)について別々に示されています。
4つの重大度レベル(等級1〜4)が考慮され、各レベルには識別のための固有のROIカラーが割り当てられています:
- 等級1:青
- 等級2:緑
- 等級3:オレンジ
- 等級4:茶色
等級判定は、カスタム参照(表2)で定義された基準に基づいて実行され、参照文書に記載されているように、入力画像の700mm²単位面積あたりに適用されます。異なる重大度レベルに対応する複数の活性化されたROIが重なる場合、より高い重大度レベルに関連付けられたROIが視覚化において優先されます。使用された参照条件(表2)によると、異物クラスの存在は自動的に等級4(茶色のROI)分類になります。図6の列は、きずクラスに基づいた分離されたきずクラス(i)、分析中に生成された境界ボックス(ii)、および評価された領域全体の重大度レベルを示す最終的に強調表示された等級判定マップ(iii)を示しています。
図のリスト:
- 図1. ASTM E1316-22aに基づくNDTのプロセスフロー。
- 図2. 気孔きずの視覚化を強化したASTM 2973からの等級判定参照。重大度の増加順(1から4)に配置。
- 図3. 実際のきずを使用して入力画像を生成するワークフロー。各きずは4つの異なるクラスを区別するために色分けされている。
- 図4. (a) 生成されたきずのランダムな分布を持つ画像。(b) 4つの異なるカラーコードへのきずのランダムな分類を示す。元の画像サイズは3098 × 3097ピクセル。
- 図5. 提案された欠陥等級判定方法論の概略図。
- 図6. 行(a-d)はそれぞれ気孔、引け巣、湯回り不良、異物を表す。列(i-iii)は、きずクラス、境界ボックス、および強調表示された境界ボックスに基づく分離されたきずクラスを示す。境界ボックスの色は等級を示す:等級1(青)、等級2(緑)、等級3(オレンジ)、等級4(茶色)。
7. 結論:
本研究は、きずと欠陥の間の重要な区別を強調することによって、欠陥検出を再検討します。きず検出アルゴリズムに堅牢な等級判定システムを組み込むことにより、ダイカストのデジタルラジオグラフィ画像で検出されたきずから真の欠陥を識別するための詳細で信頼性が高く、適応可能なアプローチを提供します。提案された方法は、ASTM E1316に概説されている評価プロセスを切り離し、業界で使用されている確立された非破壊検査(NDT)規格(ASTM E2973-15など)に基づいて関連するきずを等級判定し、欠陥の有無に関する情報に基づいた合否判定を行うことに焦点を当てています。
この研究で提案された等級判定パイプラインは、検査プロセスの効率と精度を向上させるだけでなく、製造されたコンポーネントのラジオグラフィ評価における意思決定と品質管理を完全に自動化するための道筋を提供します。この方法を既存のNDTワークフローにシームレスに統合することにより、産業界は欠陥等級判定の精度と信頼性を維持または向上させながら、検査時間とコストを大幅に削減できます。これは運用NDT規格の遵守の重要性を強調し、コンポーネントの使用適合性を損なう可能性のあるきず(またはきずのグループ)のみが、合意された基準に基づいて欠陥として分類されることを保証します。このソリューションは、この分野における重要な進歩を表し、様々な産業向けの多用途で適応可能なツールを提供します。
今後の研究では、提案された等級判定アルゴリズムを、コンピュータ断層撮影画像などの体積画像の3Dアプリケーションに統合するためにアップグレードすることを検討できます。さらに、機械学習ベースの技術を組み込んで等級判定基準をさらに洗練させることは、提案されたアプローチの適用可能性を多様化し、さらに高い精度を可能にする可能性があります。これらの方向性は、提案されたアプローチの範囲を広げ、次世代の自動化NDTデジタルラジオグラフィソリューションにおけるその役割を確固たるものにする可能性があります。
8. 参考文献:
- References
- [1] Hahn, J.; Bequette, B.W. Process Automation. In Springer Handbook of Automation; Nof, S.Y., Ed.; Springer International Publishing: Cham, Switzerland, 2023; pp. 585–600. ISBN 978-3-030-96729-1.
- [2] Perzyk, M.; Dybowski, B.; Kozłowski, J. Introducing Advanced Data Analytics in Perspective of Industry 4.0 in a Die Casting Foundry. Arch. Foundry Eng. 2019, 19, 53-57. [CrossRef]
- [3] Fiorese, E.; Bonollo, F.; Timelli, G.; Arnberg, L.; Gariboldi, E. New Classification of Defects and Imperfections for Aluminum Alloy Castings. Int. J. Met. 2015, 9, 55-66. [CrossRef]
- [4] Sigworth, G. Aluminum Casting Alloys and Casting Processes. In Aluminum Science and Technology; ASM International: Almere, The Netherlands, 2018; ISBN 978-1-62708-207-5.
- [5] Ferguson, M.; Ak, R.; Lee, Y.-T.T.; Law, K.H. Detection and Segmentation of Manufacturing Defects with Convolutional Neural Networks and Transfer Learning. arXiv 2018, arXiv:1808.02518. [CrossRef] [PubMed]
- [6] Silva, M.I.; Malitckii, E.; Santos, T.G.; Vilaça, P. Review of Conventional and Advanced Non-Destructive Testing Techniques for Detection and Characterization of Small-Scale Defects. Prog. Mater. Sci. 2023, 138, 101155. [CrossRef]
- [7] Wilczek, A.; Długosz, P.; Hebda, M. Porosity Characterization of Aluminium Castings by Using Particular Non-Destructive Techniques. J. Nondestruct. Eval. 2015, 34, 26. [CrossRef]
- [8] Dwivedi, S.K.; Vishwakarma, M.; Soni, P.A. Advances and Researches on Non Destructive Testing: A Review. Mater. Today Proc. 2018, 5, 3690-3698. [CrossRef]
- [9] Körner, M.; Weber, C.H.; Wirth, S.; Pfeifer, K.-J.; Reiser, M.F.; Treitl, M. Advances in Digital Radiography: Physical Principles and System Overview. Radiographics 2007, 27, 675-686. [CrossRef]
- [10] de Carvalho, A.A.; Suita, R.C.d.S.B.; Silva, R.R.d.; Rebello, J.M.A. Evaluation of the Relevant Features of Welding Defects in Radiographic Inspection. Mat. Res. 2003, 6, 427-432. [CrossRef]
- [11] Aryan, P.; Sampath, S.; Sohn, H. An Overview of Non-Destructive Testing Methods for Integrated Circuit Packaging Inspection. Sensors 2018, 18, 1981. [CrossRef]
- [12] Wang, B.; Zhong, S.; Lee, T.-L.; Fancey, K.S.; Mi, J. Non-Destructive Testing and Evaluation of Composite Materials/Structures: A State-of-the-Art Review. Adv. Mech. Eng. 2020, 12, 168781402091376. [CrossRef]
- [13] Ulus, Ö.; Davarcı, F.E.; Gültekin, E.E. Non-Destructive Testing Methods Commonly Used in Aviation. Int. J. Aeronaut. Astronaut. 2024, 5, 10-22. [CrossRef]
- [14] Dobrzański, L.A.; Krupinski, M.; Sokolowski, J.H. Computer Aided Classification of Flaws Occurred during Casting of Aluminum. J. Mater. Process. Technol. 2005, 167, 456–462. [CrossRef]
- [15] Wu, B.; Zhou, J.; Ji, X.; Yin, Y.; Shen, X. Research on Approaches for Computer Aided Detection of Casting Defects in X-Ray Images with Feature Engineering and Machine Learning. Procedia Manuf. 2019, 37, 394-401. [CrossRef]
- [16] Hou, W.; Zhang, D.; Wei, Y.; Guo, J.; Zhang, X. Review on Computer Aided Weld Defect Detection from Radiography Images. Appl. Sci. 2020, 10, 1878. [CrossRef]
- [17] Yu, H.; Li, X.; Song, K.; Shang, E.; Liu, H.; Yan, Y. Adaptive Depth and Receptive Field Selection Network for Defect Semantic Segmentation on Castings X-Rays. NDT E Int. 2020, 116, 102345. [CrossRef]
- [18] Vrana, J.; Singh, R. NDE 4.0—A Design Thinking Perspective. J. Nondestruct. Eval. 2021, 40, 8. [CrossRef]
- [19] Dobmann, G. Quo Vadis NDT?-A Forecast of the Future. BNiD 2020, 5, 6-17. [CrossRef]
- [20] Min, C.; Yi, W.; Jigui, Z.; Jiang, F.; Jianjun, M. Simulation and Optimization of Casting Process for Aluminum Alloy Special-Shaped Parts. J. Phys. Conf. Ser. 2021, 1986, 012018. [CrossRef]
- [21] Samuel, A.M.; Samuel, E.; Songmene, V.; Samuel, F.H. A Review on Porosity Formation in Aluminum-Based Alloys. Materials 2023, 16, 2047. [CrossRef]
- [22] Itamura, M.; Anzai, K.; Hirata, N.; Akahoshi, N.; Maeda, T.; Tanazawa, H.; Furuya, Y.; Fukuoka, S.; Yamamoto, N. Development of Aluminum Die Casting Products with High Accuracy as Well as Superior Die-to-Casting Transcriptional Capability by Using Semi-Solid Method. In Proceedings of the Semi-Solid Processing of Alloys and Composites XII; Trans Tech Publications Ltd.: Stafa-Zurich, Switzerland, 2013; Volume 192, pp. 447-453.
- [23] Mery, D. Aluminum Casting Inspection Using Deep Object Detection Methods and Simulated Ellipsoidal Defects. Mach. Vis. Appl. 2021, 32, 72. [CrossRef]
- [24] Xue, L.; Hei, J.; Wang, Y.; Li, Q.; Lu, Y.; Liu, W. A High Efficiency Deep Learning Method for the X-Ray Image Defect Detection of Casting Parts. Meas. Sci. Technol. 2022, 33, 095015. [CrossRef]
- [25] Hu, C.; Wang, Y. An Efficient Convolutional Neural Network Model Based on Object-Level Attention Mechanism for Casting Defect Detection on Radiography Images. IEEE Trans. Ind. Electron. 2020, 67, 10922–10930. [CrossRef]
- [26] Tang, J.; Liu, S.; Zhao, D.; Tang, L.; Zou, W.; Zheng, B. An Algorithm for Real-Time Aluminum Profile Surface Defects Detection Based on Lightweight Network Structure. Metals 2023, 13, 507. [CrossRef]
- [27] Mizgan, H.; Ganea, M. Optimization of Aluminium Die-Casting Process through Predictive Maintenance and Parameter Traceability Systems. IOP Conf. Ser. Mater. Sci. Eng. 2022, 1256, 012028. [CrossRef]
- [28] Zhang, J.; Guo, Z.; Jiao, T.; Wang, M. Defect Detection of Aluminum Alloy Wheels in Radiography Images Using Adaptive Threshold and Morphological Reconstruction. Appl. Sci. 2018, 8, 2365. [CrossRef]
- [29] Mery, D.; Filbert, D. Automated Flaw Detection in Aluminum Castings Based on the Tracking of Potential Defects in a Radioscopic Image Sequence. IEEE Trans. Robot. Automat. 2002, 18, 890–901. [CrossRef]
- [30] Koshti, A.M. Using Requirements on Merit Ratios for Assessing Reliability of NDE Flaw Detection in Multi-Hit Detection in Digital Radiography. In Proceedings of the Health Monitoring of Structural and Biological Systems XV; Fromme, P., Su, Z., Eds.; SPIE: St Bellingham, WA, USA, 2021; Volume 11593, p. 115932K.
- [31] Yahaghi, E.; Mirzapour, M.; Movafeghi, A.; Rokrok, B. Interlaced Bilateral Filtering and Wavelet Thresholding for Flaw Detection in the Radiography of Weldments. Eur. Phys. J. Plus 2020, 135, 42. [CrossRef]
- [32] Friedman, J.H.; Bentley, J.L.; Finkel, R.A. An Algorithm for Finding Best Matches in Logarithmic Expected Time. ACM Trans. Math. Softw. 1977, 3, 209-226. [CrossRef]
- [33] Bentley, J.L. Multidimensional Binary Search Trees Used for Associative Searching. Commun. ACM 1975, 18, 509-517. [CrossRef]
- [34] Guttman, A. R-Trees: A Dynamic Index Structure for Spatial Searching. In Proceedings of the ACM SIGMOD Conference, Boston, MA, USA, 18-21 June 1984.
9. 著作権:
- この資料は「[Bata Hena, Gabriel Ramos, Clemente Ibarra-Castanedo, Xavier Maldague]」による論文です。「[Automated Defect Detection through Flaw Grading in Non-Destructive Testing Digital X-ray Radiography]」に基づいています。
- 論文の出典: [https://doi.org/10.3390/ndt2040023]
この資料は上記の論文に基づいて要約されており、商業目的での無断使用は禁じられています。
Copyright © 2025 CASTMAN. All rights reserved.