本要約の内容は、「[Laserax Inc., Université Laval, Viami International]」所属の研究者らが発表した論文「[Review of technologies for identification of die casting parts]」に基づいています。
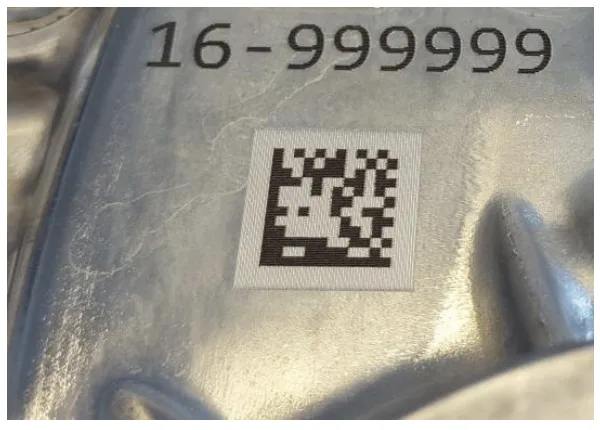
1. 概要:
- タイトル: Review of technologies for identification of die casting parts (ダイカスト部品の識別技術レビュー)
- 著者: A. Fraser, J. Maltais¹, M. Hartlieb³, C. Frayssinous², R. Vallée² and X. P. Godmaire¹ (所属: ¹Laserax Inc, ²Université Laval, ³Viami International)
- 発行年: 提供された文書には明記されていません。
- 発行学術誌/学会: 明記されていません。所属機関にはLaserax Inc., Université Laval, Viami Internationalが含まれます。
- キーワード: 論文中にキーワードは提供されていません。
2. 抄録 (Abstract):
部品トレーサビリティは、安全性が重要な用途だけでなく、様々な産業における多くのアプリケーションでますます要求されています。ダイカストも例外ではなく、構造用/高信頼性市場が最も急成長しているセグメントであることを考えると、ダイカストのトレーサビリティとマーキングが注目されているのは当然です。高信頼性部品は通常、生産される部品の100%に対する識別要件があります。これは、部品に関するインシデントが発生した場合に合金およびプロセスデータに即座にアクセスできるだけでなく、部品の品質と管理の向上にも役立ちます。市場にはさまざまな技術が存在し、それぞれに固有の長所と短所があります。ダイカスト産業は、適切なマーキング技術を選択する際に考慮すべき非常に重要な側面をいくつか提示しています。不均一な表面を持つ複雑な部品、マーキング時にしばしば高温であること、短いサイクルタイム、ショットブラスト処理のようなマーキング後のプロセスなどが最も重要なものです。部品マーキングは、鋳造品の生産プロセスにおける重要なステップでありながら、プロセスのボトルネックになるべきでも、不良率の原因となるべきでもありません。本稿は、利用可能なさまざまなマーキング方法を分析し、ダイカスト部品のインラインマーキングに最も適した方法を指摘することを目的としています。温度、サイクルタイム、ショットブラスト後処理の影響に重点を置いたいくつかのマーキング結果が提示されます。結果は、レーザーベースの技術がダイカスト産業のすべての要件に対応するのに適していることを示しています。
3. 序論 (Introduction):
トレーサビリティ、ひいては個々の鋳造品へのマーキングは、開発プロセス(プロセスの欠陥を迅速に特定し、どのプロセスパラメータを修正する必要があるかを特定するのに役立つ)と、高信頼性部品の量産[1]の両方において、ますます要求が高まっています。工業的なダイカスト環境における明白な課題は、(a) 速いサイクルタイム(そして部品マーキングは、この非常に資本集約的なプロセスにおいて決してボトルネックになるべきではない)、(b) 完全に平坦ではない表面へのマーキング、(c) マーキング時に通常まだ高温であり、潤滑剤や汚れの残渣で覆われて完全に清浄ではない部品、(d) 熱処理、ショットブラスト、洗浄、エッチング、化成処理などの追加処理にも耐えるマーキングの能力です。最後に、マーキングはその全運用寿命にわたって部品上に安全に残る必要があります。
従来、部品マーキングは完全に反復的なマーキングを得るために、部品を正確な位置にクランプする必要がありました。サイクルタイムが重要であり、プロセスの複雑さと投資を最小限に抑える必要がある場合、理想的には、距離があり、ある程度の公差があっても完全に機能するマーキングシステムが望まれます(例:マーカーから1フィートの距離で、どちらかの方向に1〜2インチの公差があり、部品をどの点にもクランプする必要がなく、単に抽出ロボットがマーカーの前に保持している状態)。本稿では、ダイカスト部品を識別するために利用可能な技術のレビューを提示します。さまざまな技術の長所と短所、およびそれらがどの用途に適しているかを提示します。次に、温度、マーキング速度、ショットブラストなどの後処理の影響に関する結果を提示します。
4. 研究の要約:
研究テーマの背景:
様々な産業、特に安全性が重要な高信頼性ダイカスト部品において、部品トレーサビリティへの要求が高まっているため、信頼性が高く効率的な識別方法が必要です。トレーサビリティは、品質管理、プロセス最適化に役立ち、部品のインシデント発生時に重要なデータアクセスを提供します。
従来の研究状況:
部品識別にはいくつかの技術が存在しますが、ダイカストの文脈ではそれぞれに限界があります。
- ラベルおよびネームプレート (Labels and Nameplates): 処理中または使用中に剥がれやすく、消耗品費や人件費がかかり、高温や不均一な表面には不向きです。
- ピンスタンピング / ドットピーン (Pin Stamping / Dot Peen): 深く永続的なマークを作成しますが、比較的遅く、近接接触と正確な位置決めが必要で、コントラストを提供できない場合があり、表面変形が高信頼性部品の品質仕様を超える可能性があります。
- インクジェット印刷 (Inkjet Printing): カラーマークを提供しますが、機械加工、ショットブラスト、洗浄/エッチングなどの後続プロセスに対する耐久性が不足しています。
- 金型直接マーキング (Direct Mold Marking): 合金、生産施設、キャビティなどの静的情報には適していますが、特定のプロセスパラメータにリンクされた個々の部品データや2Dバーコードには使用されません。
研究の目的:
本研究は、ダイカスト部品に利用可能なマーキング技術を分析し、業界特有の課題(サイクルタイム、温度、表面状態、後処理)を考慮してインラインマーキングに最も適した方法を特定し、特にレーザーマーキングの性能、ショットブラスト後処理に対する耐性を重点的に調査することを目的としています。
中核研究:
研究の中核は、その潜在的な利点(速度、堅牢性、非接触、高温対応能力、不均一表面での精度)から、レーザーマーキング技術に焦点を当てています。特定された主要な課題は、標準的なレーザーブラックマーキング(表面よりわずかに上に位置する)がショットブラストによって除去されやすいことです。本研究では、ショットブラスト耐性を向上させるために、この窪み内にブラックマークを適用する前にレーザーでクレーターを事前エッチングする戦略(Figure 6)を提案し、調査します。実験は、アルミニウムダイカスト表面に100Wファイバーレーザーを使用して行われ、事前エッチングパラメータ(パス数、速度、ライン間隔)およびコードサイズを変更しました。マーキングされたサンプルは、2つの異なるスチールボールサイズ(S170およびS460)を使用してショットブラスト処理されました。効果は、表面プロフィロメータ(Dektak 150)および目視検査を使用して評価されました。
5. 研究方法論
研究デザイン:
本研究は、2部構成のデザインを採用しました。
- 既存の部品識別技術(ラベル、ピンスタンピング、インクジェット印刷、金型直接マーキング、レーザーマーキング)の比較レビューを行い、耐久性、速度、コスト、プロセス条件との互換性などの基準に基づいてダイカスト産業への適合性を評価しました。
- レーザーマーキングに焦点を当てた実験的調査を行い、特にショットブラスト後処理がマークの耐久性に与える影響を調査し、耐性を改善するための事前エッチング戦略を探求しました。
データ収集および分析方法:
- レーザーマーキング: 1.06 µmファイバーレーザー(平均出力100W、パルス幅100 ns、周波数100 kHz)を使用して、アルミニウムサンプルにデータマトリックスコードをマーキングしました。変更されたパラメータには、事前エッチングパス数(3〜15回)、事前エッチング速度(3000〜7000 mm/s)、ライン間隔(0.025〜0.125 mm)、コードサイズ(4x4 mm、6x6 mm)が含まれました。ブラックマーキングパラメータは一定に保たれました(速度400 mm/s、ライン間隔0.125 mm)。
- ショットブラスト処理: マーキングされたサンプルは、S170(直径0.355 mm)およびS460(直径1 mm)のスチールボールを使用してショットブラスト処理されました。処理時間は様々でした。
- 表面分析: Dektak 150表面プロフィロメータを使用して、ショットブラスト処理前後の表面プロファイルを測定し、材料除去と表面変質を定量化しました。3D表面マッピングも行われました。
- 目視検査: 処理前後のマーキングの外観を記録するために写真が撮影されました。マークの読み取り可能性は目視で評価されました。
研究トピックと範囲:
本研究は以下をカバーしました。
- ダイカスト用各種部品識別技術のレビューと比較。
- ダイカスト環境に適した技術としてのレーザーマーキングの評価。
- ショットブラスト後処理がレーザーマーキングに与える影響の調査。
- レーザーマーキングのショットブラスト耐性を向上させるための事前エッチング戦略の開発とテスト。
- レーザーパラメータ(事前エッチング深さ)およびショットブラストパラメータ(ボールサイズ、時間)がマークの生存性と読み取り可能性に与える影響の分析。
- アルミニウムダイカスト合金へのマーキング評価。
6. 主要な結果:
主要な結果:
- レーザーマーキングは、速度、精度、高温・不均一表面へのマーキング能力からダイカストに適しているように見えますが、隆起した特徴を生成する標準的なブラックマーキングはショットブラストに対して脆弱です。
- マークを保護するために、ブラックマーキングの前に窪みを作成する事前エッチング戦略が調査されました。表面プロファイルは、複数回のレーザーパスが元のアルミニウムレベルよりも下に窪みを作成できることを確認しました(Figure 7)。
- ショットブラストは表面プロファイルを大幅に変更し、ブラックマーキングに関連するピークや、場合によっては周囲のエッチングされたエッジを除去します(Figure 8)。
- より大きなS460ボール(より高い運動エネルギー)によるショットブラストは、深い表面衝撃(約48 µm深の穴)を引き起こし、レーザーマーキングを完全に破壊しました(Figure 10, Figure 12)。
- より小さなS170ボール(より低い運動エネルギー)によるショットブラストは、より浅い衝撃(約20 µm深の穴)とより滑らかな表面をもたらしました。ブラックコントラストは完全に消去されましたが、コード構造の残骸が時々見られましたが、一般的にアルゴリズムでは読み取れませんでした(Figure 9)。
- 事前エッチング戦略の有効性は、ショットブラストの衝撃とボールサイズに対して十分な深さを達成できるかどうかに決定的に依存します。テストされたパラメータは、複数回の事前エッチングパスを行っても、特にS460ボールに対して、テストされたショットブラスト条件下でマーキングを完全に保護するには不十分でした。
- マークの生存性は、部品がショットブラスト流中に滞在する時間や、部品の特徴に対するマークの位置(例:突起部の近くのマークは保護される可能性がある)などのランダムな要因に影響されます。
- より小さなコードセルサイズ(例:幅0.25 mm)とより深い事前エッチング(約100 µm深)を組み合わせることで、標準のS170ボールがエッチングされたセルの底にある黒化(blackening)を破壊せずに通過できるようにする最適化の可能性があります。
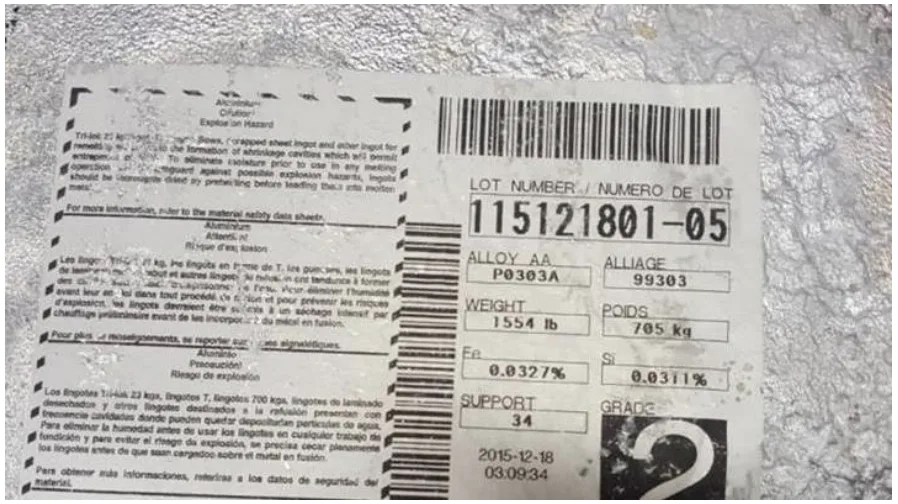
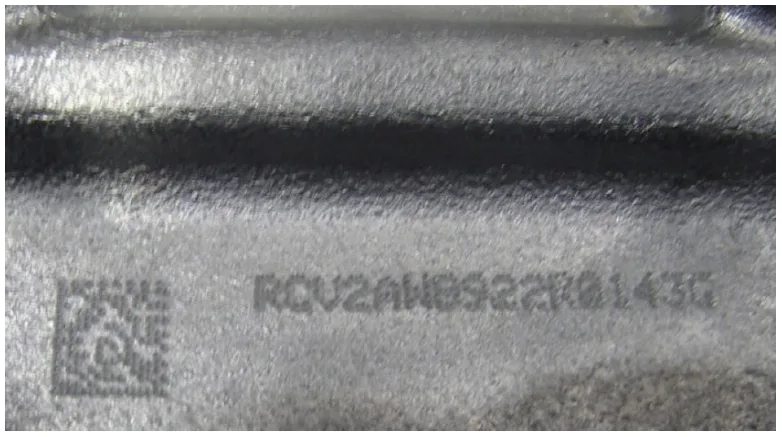
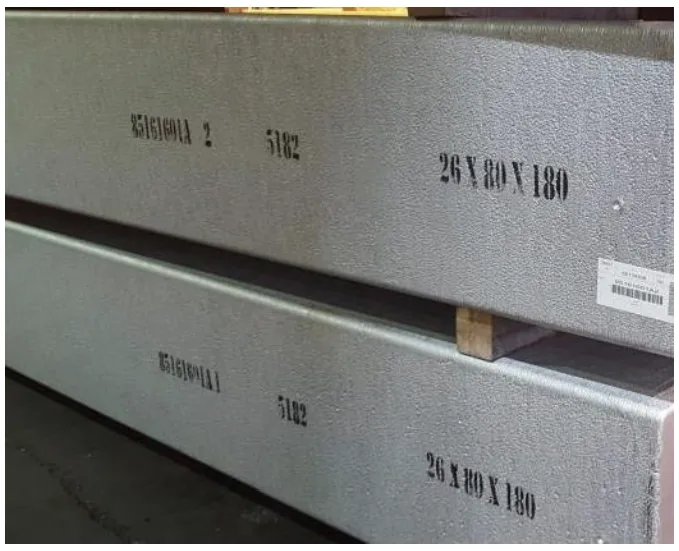
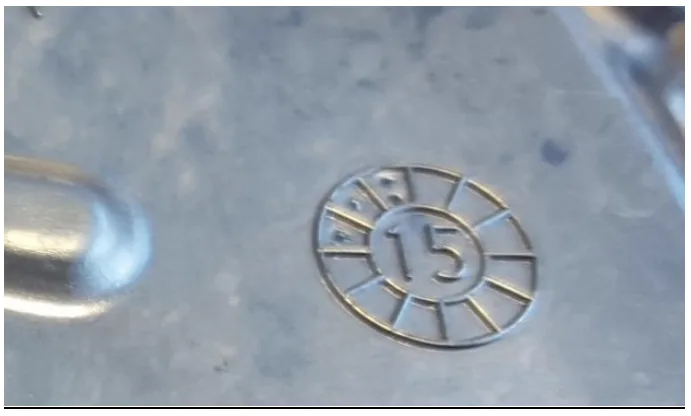
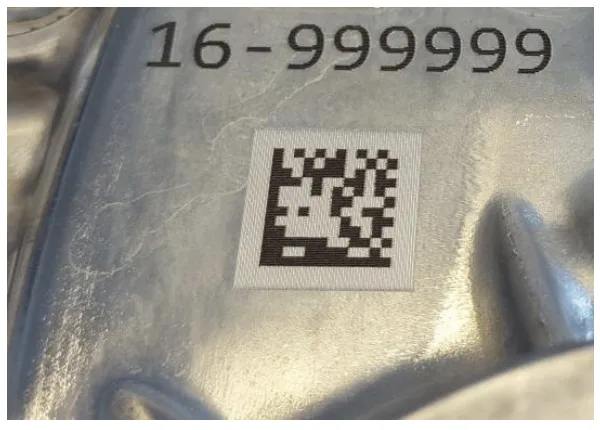
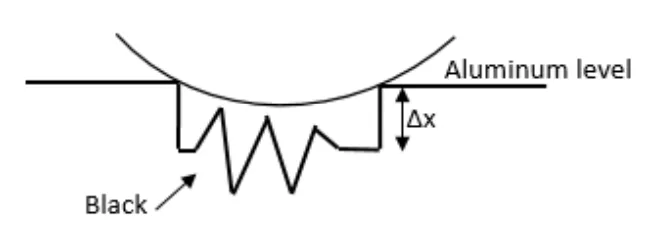
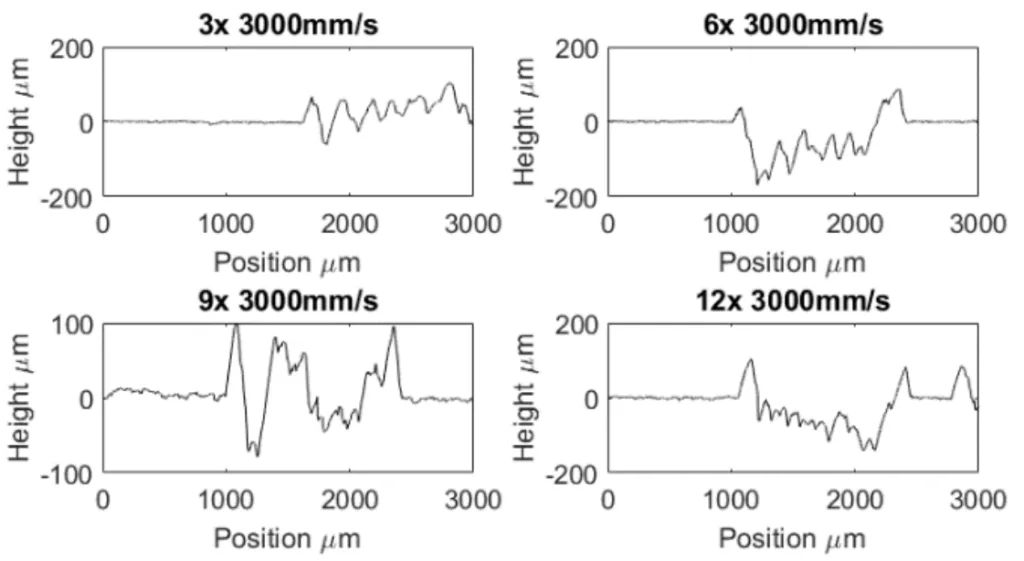
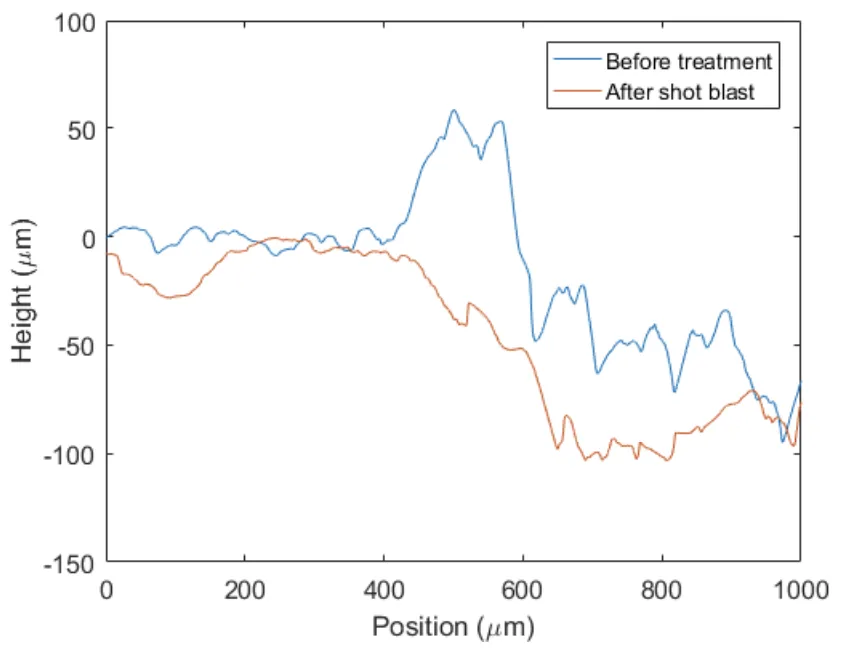
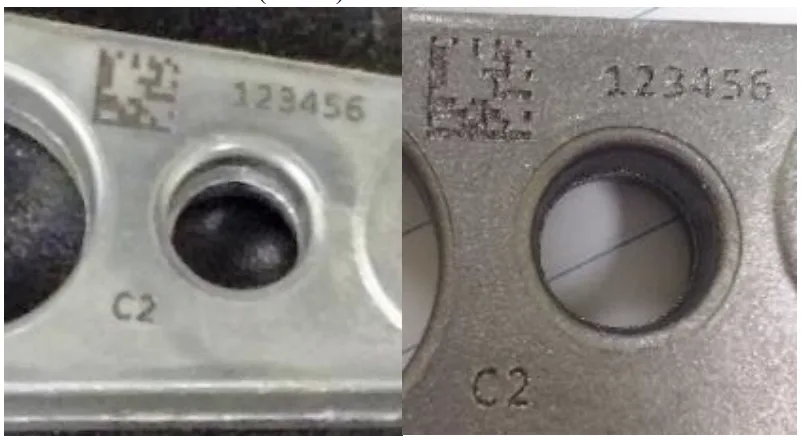
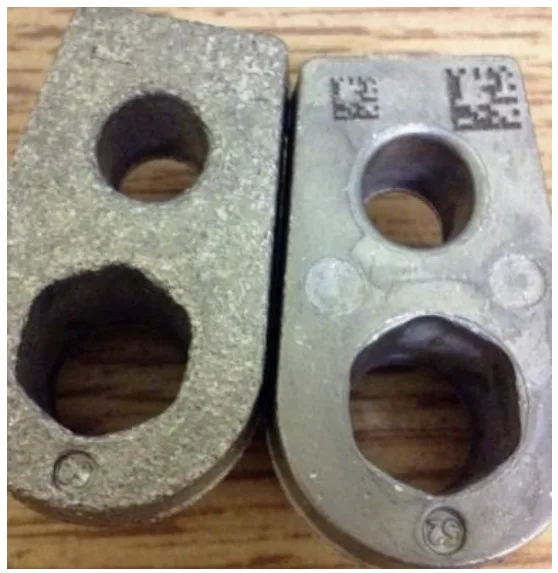
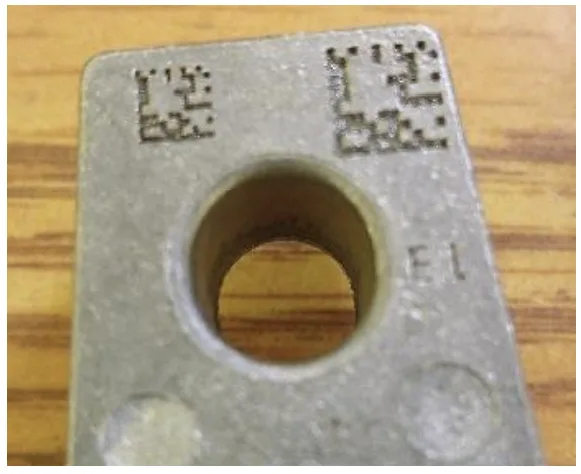
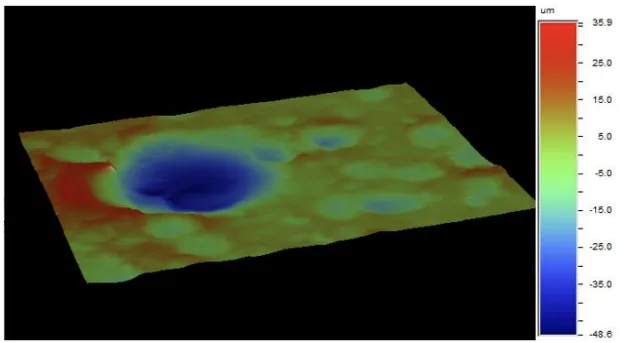
図のリスト (Figure Name List):
- Figure 1: Printed label (sticker) (印刷ラベル(ステッカー))
- Figure 2: Pinstamp®/Dot peen marked die casting. (ピンスランプ®/ドットピーンによるダイカストマーキング)
- Figure 3: Inkjet printing. (インクジェット印刷)
- Figure 4: Direct mold marking and punch (金型直接マーキングとパンチ)
- Figure 5: Laser marked identifier on aluminum die casting alloy. (アルミニウムダイカスト合金へのレーザーマーキング識別子)
- Figure 6: Sketch of the idea behind the protected marking. (保護マーキングの背後にあるアイデアのスケッチ)
- Figure 7: Surface profile of samples before treatment where the laser was passed multiple times before marking the black. (ブラックマーキング前にレーザーを複数回照射した処理前のサンプルの表面プロファイル)
- Figure 8: Surface profile measured with Dektak 150 of a marking before and after treatment with S170 balls. (S170ボールによる処理前後のマーキングのDektak 150による表面プロファイル測定)
- Figure 9: Photo of a marking before treatment (left) and after shot blast with S170 balls (center). (処理前のマーキング(左)とS170ボールによるショットブラスト後(中央)の写真)
- Figure 10: Photo of 2 samples after 20 seconds shot blast with S460 balls. (S460ボールによる20秒間のショットブラスト後の2つのサンプルの写真)
- Figure 11: Photo of sample after a treatment of 20 seconds with S460 balls and another 20 seconds with S170 balls. (S460ボールによる20秒間の処理と、さらにS170ボールによる20秒間の処理後のサンプルの写真)
- Figure 12: 3D profile of surface after being hit by S470 and S170 balls. (S470およびS170ボールによる打撃後の表面の3Dプロファイル) ※注記: 図12のキャプションではS470と記載されていますが、本文中ではS460とS170が使用されているため、S460の誤記の可能性があります。原文に従いS470と記載します。
7. 結論 (Conclusion):
レーザーマーキングは、ダイカスト部品に永続的なマーキングを行うための最も適したプロセスです。望ましいサイクルタイム、品質、再現性を達成できます。ダイカストに通常適用されるほとんどすべての表面処理に容易に耐えることができます。主な課題はショットブラストであり、これについて深く研究されました。以前に提示されたすべてのショットブラストパラメータは、コードの耐性に影響を与えます。適切なショットブラスト条件下では、我々の意見では、ダイカスト部品にショットブラスト処理後も読み取り可能なコードを保持することが可能であるはずです。これには、比較的短いプロセス時間も含まれます。アルミニウム表面を破壊することが確認されたため、ボールが大きすぎないことも重要です。ブラック表面をそのまま維持するためには、ボールがケースの底に到達しない程度に十分に大きい必要があります。コードの寸法も決定的なパラメータです。より小さなケースが処理後に読み取り可能なコードを得る可能性を高めると考えます。レーザープロセスは、幅約0.25 mm、深さ約100 µmのセルサイズを達成するように最適化されるべきです。これにより、標準のS170ボールを使用し、底部の黒化を損なわずに維持できると考えられます。これを実証するためのさらなるテストが行われ、NADCA会議で発表される予定です。
その多様性のおかげで、レーザー技術は、ダイカスト産業で非常に一般的な処理に対する耐性の向上を含む、複数の要件に適応できます。レーザーマーキングは、堅牢性、速度、不均一な表面および高温でのマーキング能力など、多くの産業ニーズを満たします。
8. 参考文献 (References):
- [1] S. Desrosiers et Al., Alloy and heat treatment development for weldable structure parts, 2014 Die Casting ongress conference proceedings
- [2] J. Maltais and al., Surface analysis study of laser marking of aluminum, submitted to ICSOBA 2016 conference proceedings
- [3] Alex Fraser and al., Important considerations for laser marking an identifier on aluminum, Light metals 2016 (Proceedings of TMS 2016), p. 261-264
- [4] J. Benes, The lowdown on laser marking, americanmachinist.com, March 25th 2008
9. 著作権 (Copyright):
- 本資料は、「A. Fraser, J. Maltais, M. Hartlieb, C. Frayssinous, R. Vallée and X. P. Godmaire」による論文の要約です。基論文:「Review of technologies for identification of die casting parts」。
- 論文の出典:論文中にDOIは提供されていません。
本資料は上記の論文に基づいて要約されており、商業目的での無断使用を禁じます。
Copyright © 2025 CASTMAN. All rights reserved.