この紹介論文は、[Publisher is not included in the paper] によって出版された ["Local stress/strain field analysis of die-casting Al alloys via 3D model simulation with realistic defect distribution and RVE modelling"] 論文の研究内容です。
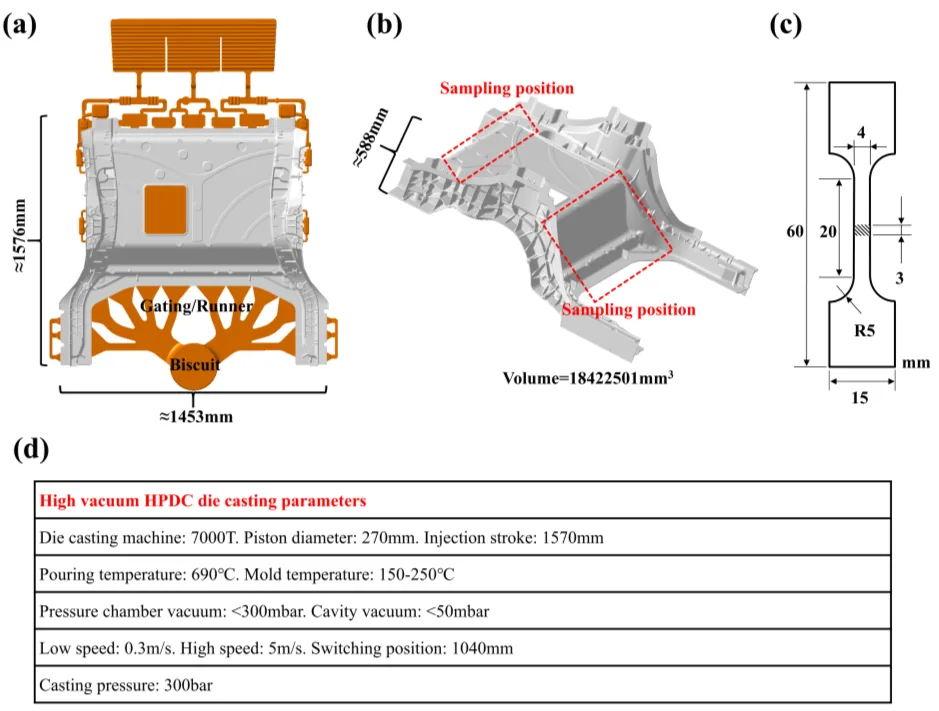
1. 概要:
- タイトル: Local stress/strain field analysis of die-casting Al alloys via 3D model simulation with realistic defect distribution and RVE modelling (実欠陥分布と RVE モデリングによるダイカスト Al 合金の局所応力/ひずみ場解析)
- 著者: Jian Yang, Bo Liu, Dongwei Shu, Qin Yang, Tiegang Hu
- 出版年: 2024
- 掲載ジャーナル/学会: プレプリント
- キーワード: Die-casting(ダイカスト); Aluminium alloy(アルミニウム合金); Representative volume element(代表体積要素); X-ray computed tomography(X線コンピュータ断層撮影); Automotive lightweighting(自動車軽量化).
2. 要旨
ダイカストアルミニウム(Al)合金の変形と破壊挙動は非常に複雑です。特性の局所的なばらつきにより、材料の微細構造と機械的挙動は非常に異方性を示します。本論文では、実験および有限要素計算手法を用いて高圧鋳造 Al 合金部品の欠陥特性を定量的に研究し、局所的な気孔率と気孔サイズが塑性に及ぼす影響を解析することを試みました。実欠陥分布を持つ 3 次元固体は、3D X 線コンピュータ断層撮影を用いて得られ、有限要素モデル構築のための入力として使用されました。複合応力状態下における鋳造 Al 合金の損傷開始は、ミクロスケールからマクロスケールまで解析されます。微小多孔質凝集の 2 つのモードを通して亀裂伝播が生じます:凝集した気孔は、内部ネッキングと応力集中から亀裂を生成します。その後、それらは同じ方向に拡大し、特定の方向に凝集して最終的に破壊します。続いて、デジタル画像相関測定によって局所的な応力/ひずみ挙動を得ることにより、気孔率が不均一性に及ぼす影響を解明しました。さらに、微細構造の弾塑性変形に関する理論的枠組みと 3D 代表体積要素モデルを開発し、材料の周期的境界条件下での変形と損傷プロセスをシミュレーションしました。シミュレーション結果は、気孔周辺の局所的な応力/ひずみが変形とともに徐々に変化することを示しています。ダイカストプロセスにおいて、この方法は Al 合金の機械的挙動を予測する能力を示しています。
3. 研究背景:
研究テーマの背景:
ダイカストアルミニウム(Al)合金は、自動車および航空宇宙産業において軽量化のために使用されています[1]。高圧ダイカスト(HPDC)は、Al 合金部品の主要な製造プロセスです[2, 3]。しかし、気孔タイプの欠陥は、製品の機械的特性に影響を与える可能性があります[4, 5]。気孔の存在は、微細構造の不連続性を引き起こし、外部荷重が加わったときに局所的な応力集中の可能性を高めます[6-8].
先行研究の現状:
多くの研究者が、微小欠陥が巨視的な機械的特性に及ぼす影響を調査するために、実験と有限要素シミュレーションの組み合わせを用いてきました[12]。
- Sun[13] は、AM50 合金の引張特性と破壊挙動に対する微小気孔率の影響を調査しました。
- Jiang[14] は、HPDC AZ91 マグネシウム合金の気孔率と機械的特性の関係を調査しました。
- Zhang[7] は、実欠陥に基づく 3D 有限要素モデルを開発しました。
- Zhang[16] は、数値シミュレーションと DIC 試験を用いて、不均一構造の変形と破壊挙動を検証しました。
- Zhang[17] は、Al-10 Si-0.3 Mg 部品における気孔の空間分布と形態学的特性、および塑性への影響を調査しました。
- Sun[20] は、さまざまな作業条件下での気孔率、気孔サイズ、および分布が損傷効果に及ぼす影響をシミュレーションしました。
- Ma[21] は、ダイカスト Al 合金の構成方程式を確立しました。
- 多くの研究により、微細構造の不均一性が材料の損傷開始挙動に影響を与える重要な要因であることが示されています[22-26]。
研究の必要性:
境界条件と巨視的な要因により、有限要素シミュレーションの精度を向上させる必要があります。
4. 研究目的と研究課題:
研究目的:
本研究は、複合応力状態下における鋳造 Al 合金の損傷開始亀裂に焦点を当て、実験解析と計算モデリングを組み合わせたフレームワークを提案します。
主要な研究:
- X線CT技術を用いてHPDC部品の気孔の3次元特性を定量的に研究します。
- 局所的な気孔率、気孔サイズ、および位置が塑性に及ぼす影響を解析します。
- X線CT技術で捉えた内部気孔の画像に基づいて逆モデリングを行います。
- 実欠陥分布に基づくモデルの数値結果を、DIC測定から得られた局所的な応力/ひずみ挙動と比較します。
- 3D微細構造の弾塑性変形とRVEモデルの理論的枠組みを確立し、周期的境界条件下での変形と損傷プロセスをシミュレーションします。
5. 研究方法
研究フレームワークは Fig. 1 に示されています。研究は 3 つの主要な部分に分けられます。
- 欠陥解析: X 線 CT スキャンを使用して、欠陥のサイズと空間分布を定量的に解析します。
- 逆モデリングとシミュレーション: 内部気孔 (X 線 CT から) の 3D 画像を使用して、実欠陥分布を持つソリッドモデルを作成します。欠陥と機械的特性の関係は、シミュレーションを通じて探求され、破壊メカニズムを解明します。
- RVE モデリング: RVE モデルは、周期的境界条件下での変形と損傷プロセスをシミュレーションするために構築されます。
実験方法:
- 材料選択: 非熱処理ダイカスト Al 合金 (Al-9Si, Al-7Si) が選択されました。化学組成は、誘導結合プラズマ発光分光計 (PerkinElmer Optima 8300) を使用して決定されました (Table 1)。
- HPDC 実験: YIZUMI LEAP 7000T 水平コールドチャンバーダイカスト機が使用されました。プロセスパラメータは Fig. 2 に詳述されています。
- X 線 CT スキャンと逆モデリング: X 線 CT (XPloreVista 2000 4D) は、ASTM E505、ASTM E2422、および CASE 301-2023 規格に従って、気孔サイズ、形態、および位置を調べるために使用されました。逆モデリングプロセスは、AVIZO および ABAQUS ソフトウェアのステップを含め、Fig. 3 に説明されています。
- 引張試験と DIC 試験: 引張試験は、MTS C45.305EEEY 試験機を用いて行われました。HAYTHAM DV 1200-32 システムが変位測定に使用されました。デジタル画像相関 (DIC) は、ひずみ分布を気孔変形と関連付けるために使用されました。
- 弾塑性材料挙動則:
J2 等方性弾塑性モデルは、Al マトリックスの固有の挙動を調査するために使用されました。
Eq. (1) によると、n の値は 0.15、K の値は 356 に適合させることができます。
6. 主要な研究結果:
主要な研究結果と提示されたデータ分析:
- 気孔率特性評価: X 線 CT スキャンにより、欠陥の空間分布と形態が明らかになりました (Fig. 5)。欠陥は、体積と球形度 (Eq. 2) に基づいて、ガス気孔、収縮気孔、ガス-収縮気孔に分類されました[32-34]。ほとんどの欠陥はガス気孔として識別されました。体積と球形度、体積と投影面積の関係は Fig. 6 に示されています。
- 実欠陥を用いた塑性変形解析: 実気孔特性を持つ体積メッシュが有限要素シミュレーションに使用されました。Fig. 7 は、シミュレーションフローチャートと結果を示しています。シミュレーションモデルは、マトリックス脆性破壊モードを正確に予測しました。
- シミュレーションと実験の比較: シミュレーションと実験の破壊結果が比較されました (Table 2, Fig. 8)。実欠陥分布を持つ CAE モデルは、欠陥のないモデルと比較して精度の向上が見られました。
- 変形と微小亀裂形成メカニズム: ガス気孔の変形と微小亀裂形成メカニズムは Fig. 9 に示されています。亀裂進展は、2 つのモードの微小多孔質凝集によって発生します。
- 気孔特性と局所ひずみの関係: DIC 解析により、欠陥分布と相関する局所的な高ひずみ領域が示されました (Fig. 10)。
- 3D マイクロスケール RVE モデル開発:
Digimat ソフトウェアを使用して、鋳造 Al 合金の 3D RVE モデルを生成しました。RVE モデルの設定パラメータは Fig. 11(a) に示されています。 - 代表体積要素予測:
さまざまな気孔体積率を持つ RVE モデルとシミュレーション結果を Fig. 13 に示します。
Fig. 14 は、さまざまな体積気孔率における気孔変形と損傷の概略図を示しています。
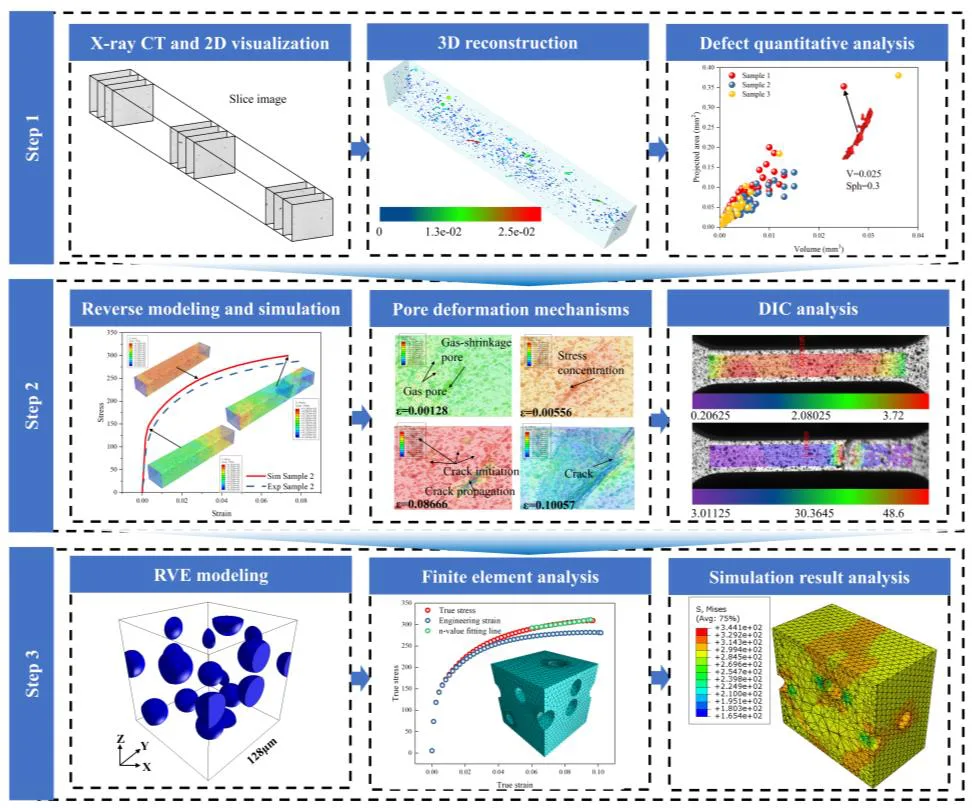
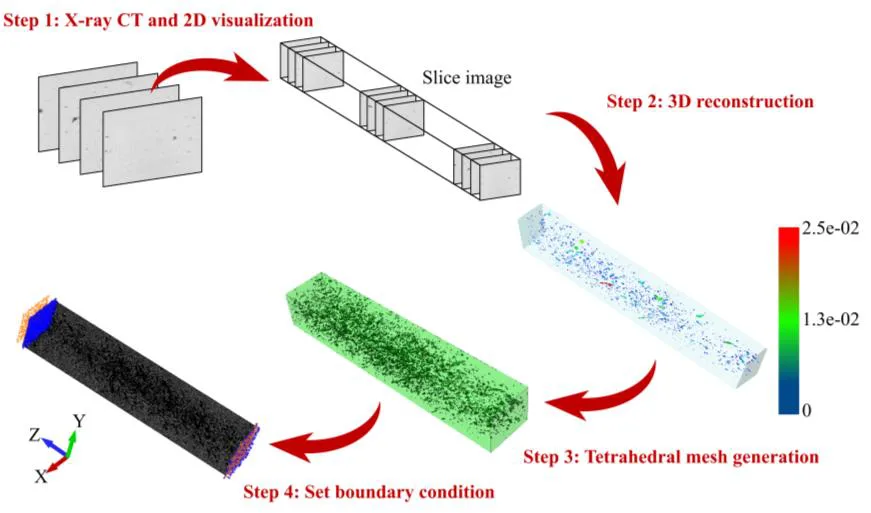
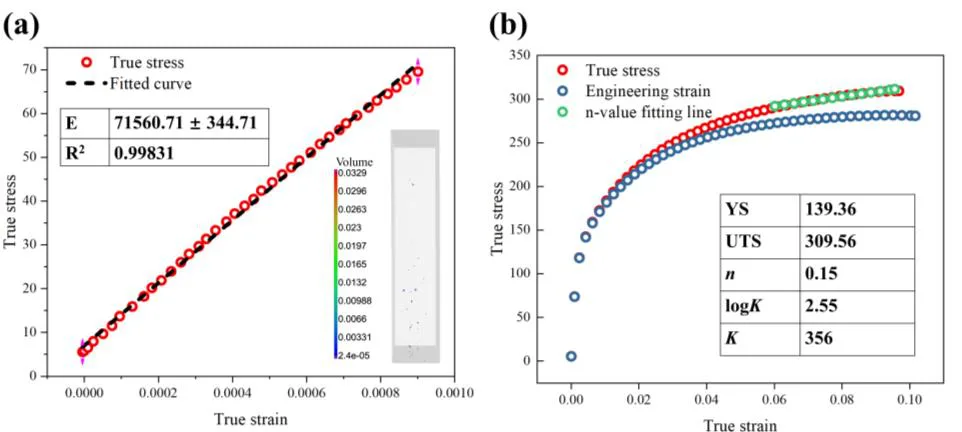
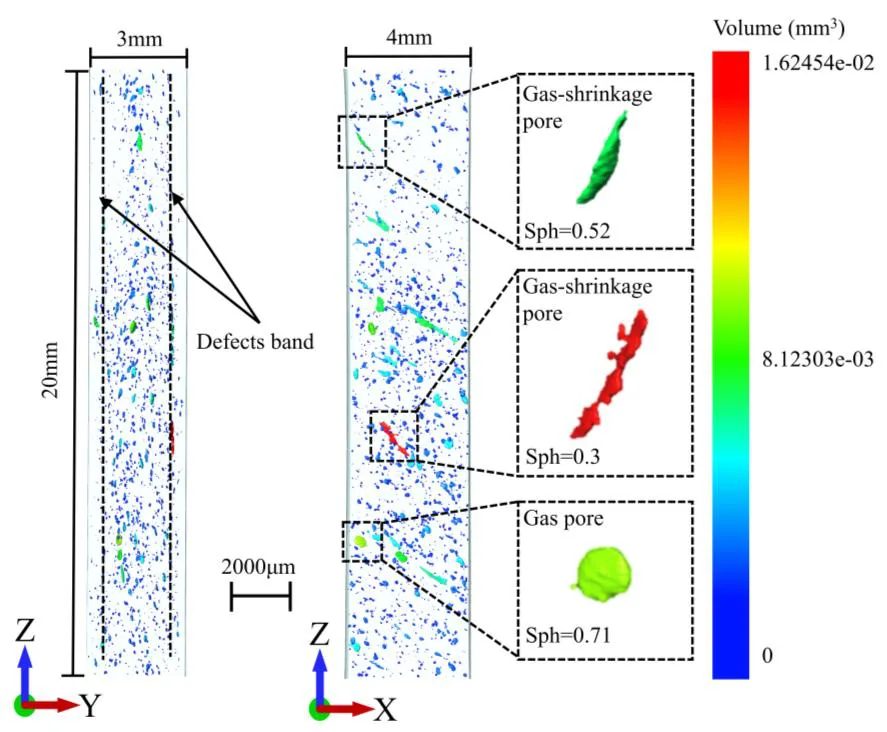
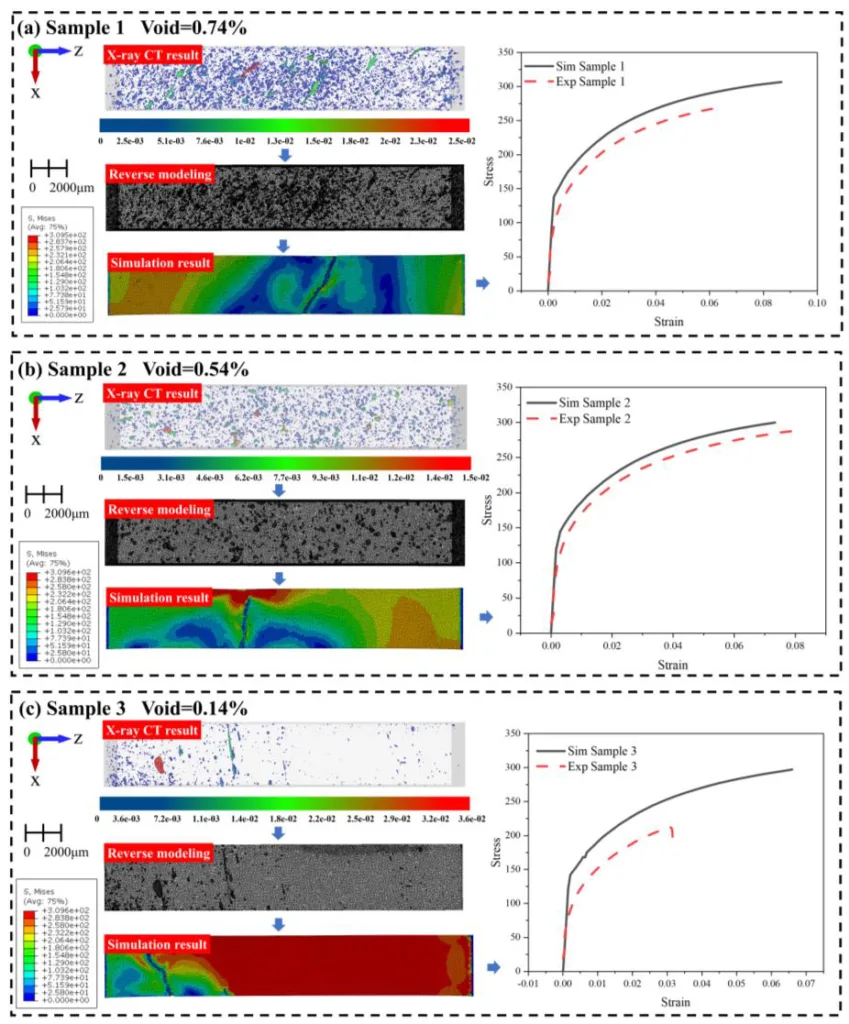
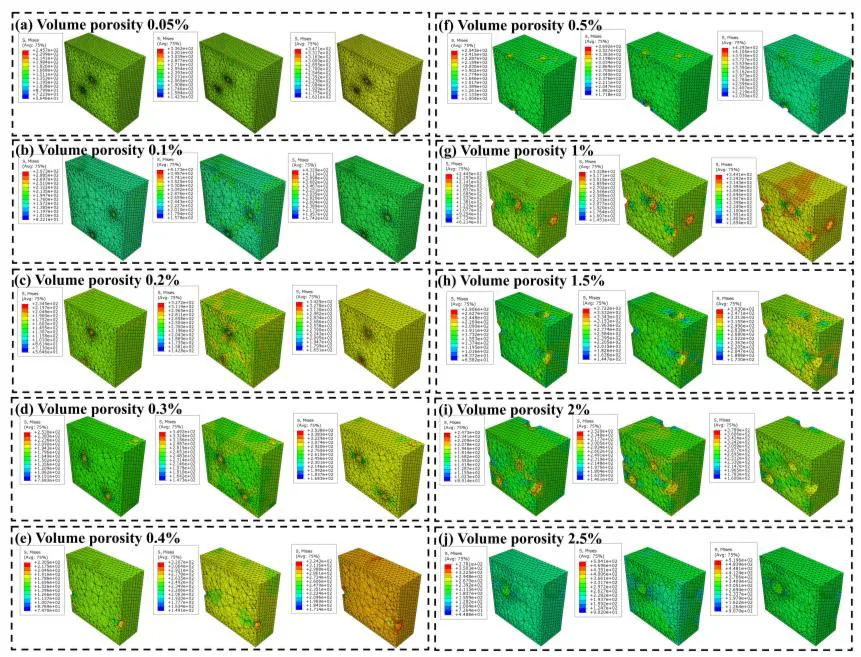
図表名リスト:
- Figure 1: Research idea framework for this study. (本研究の研究アイデアフレームワーク)
- Figure 2: Part structure, dimensions and process parameters. (部品構造、寸法、およびプロセスパラメータ)
- Figure 3: Inverse modelling method for finite element volumetric meshing and method of setting boundary conditions. (有限要素体積メッシングのための逆モデリング手法と境界条件設定方法)
- Figure 4: Elastic-plastic material behavior law. (弾塑性材料挙動則)
- Figure 5: Spatial distribution and morphological characteristics of defects (欠陥の空間分布と形態学的特性)
- Figure 6: Quantitative statistical analysis of defects. (欠陥の定量的統計解析)
- Figure 7: Inverse modelling steps and simulation analysis results. (逆モデリングステップとシミュレーション解析結果)
- Figure 8: Mechanical property data and statistical results. (機械的特性データと統計結果)
- Figure 9: Deformation and microcrack formation mechanism of gas pores. (ガス気孔の変形と微小亀裂形成メカニズム)
- Figure 10: Simulation, tensile experiment and DIC analysis. (シミュレーション、引張試験、DIC 解析)
- Figure 11: Setting parameters of the RVE model. (RVE モデルの設定パラメータ)
- Figure 12: Schematic representation of the periodic boundary conditions. (周期的境界条件の概略図)
- Figure 13: RVE models with different porosities and simulation results. (さまざまな気孔率を持つ RVE モデルとシミュレーション結果)
- Figure 14: Schematic representation of porosity deformation and damage at different porosities. (さまざまな気孔率における気孔変形と損傷の概略図)
7. 結論:
主要な結果の要約:
- X 線 CT と逆モデリングを用いて、実気孔形態を持つ 3D モデルが得られました。欠陥のないモデルと比較して、シミュレーション精度が大幅に向上しました。
- シミュレーションモデルは、引張破壊中のマトリックス脆性破壊モードを正確に予測しました。凝集した気孔は、内部ネッキングと応力集中から亀裂を生成します。
- 3D RVE モデルが開発され、有限要素弾塑性変形フレームワークと統合されました。気孔率が増加すると、局所領域に異常な塑性ひずみ蓄積が生じます。
- この方法は、気孔発生メカニズム、破壊モード、およびダイカスト Al 合金の巨視的特性予測の研究に重要な利点を提供します。
8. 参考文献:
- [1] J. Allison, M. Li, C. Wolverton, and X. Su, "Virtual aluminum castings: an industrial application of ICME," Jom, vol. 58, pp. 28-35, 2006.
- [2] S. Dash, D. Li, X. Zeng, and D. Chen, "Heterogeneous microstructure and deformation behavior of an automotive grade aluminum alloy," Journal of Alloys and Compounds, vol. 870, p. 159413, 2021.
- [3] T. Li et al., "Progress and prospects in Mg-alloy super-sized high pressure die casting for automotive structural components," Journal of Magnesium and Alloys, 2023.
- [4] X. Hu and L. Xie, "FEA Simulations of Temperature Changes of Castings When Solidified and Cooled in Mould," in Advances in Computer Science and Education Applications: International Conference, CSE 2011, Qingdao, China, July 9-10, 2011. Proceedings, Part II, 2011: Springer, pp. 178-183.
- [5] Q. Pan, L. Zheng, Y. Sang, Y. Li, L. Zhou, and H. Zhang, "Effect of casting temperature on microstructure in a directionally solidified Ni-44Ti-5Al-2Nb-1Mo alloy," Rare Metals, vol. 30, pp. 349-353, 2011.
- [6] Y. Tijani, A. Heinrietz, T. Bruder, and H. Hanselka, "Quantitative evaluation of fatigue life of cast aluminum alloys by non-destructive testing and parameter model," International journal of fatigue, vol. 57, pp. 73-78, 2013.
- [7] Y. Zhang et al., "Analysis of local stress/strain fields in an HPDC AM60 plate containing pores with various characteristics," Engineering Failure Analysis, vol. 127, p. 105503, 2021.
- [8] G. Nicoletto, R. Konečná, and S. Fintova, "Characterization of microshrinkage casting defects of Al-Si alloys by X-ray computed tomography and metallography," International journal of fatigue, vol. 41, pp. 39-46, 2012.
- [9] Y. Zhang et al., "The gradient microstructure and deformation heterogeneity in HPDC AM60 alloy," Materials Science and Engineering: A, vol. 792, p. 139647, 2020.
- [10] J. H. Forsmark, J. W. Zindel, L. Godlewski, J. Zheng, J. E. Allison, and M. Li, "Using quality mapping to predict spatial variation in local properties and component performance in Mg alloy thin-walled high-pressure die castings: an ICME approach and case study," Integrating Materials and Manufacturing Innovation, vol. 4, pp. 81-118, 2015.
- [11] G. Hahn and A. Rosenfield, "Metallurgical factors affecting fracture toughness of aluminum alloys," Metallurgical Transactions A, vol. 6, pp. 653-668, 1975.
- [12] M. Luetje, M. Wicke, I. Bacaicoa, A. Brueckner-Foit, A. Geisert, and M. Fehlbier, "3D characterization of fatigue damage mechanisms in a cast aluminum alloy using X-ray tomography," International Journal of Fatigue, vol. 103, pp. 363-370, 2017.
- [13] X. Sun, Z. Cao, H. Liu, W. Jiang, and L. Liu, "Predicting the influence of microporosity on the mechanical properties and fracture behavior of high-pressure die-cast AM50 magnesium alloy," Applied Mechanics and Materials, vol. 670, pp. 90-94, 2014.
- [14] W. Jiang, Z. Cao, X. Sun, and H. Liu, "Three-dimensional microstructure reconstruction and finite element simulation of gas pores in the high-pressure die-casting AZ91 Mg alloy," Microscopy and Microanalysis, vol. 21, no. 6, pp. 1420-1425, 2015.
- [15] Y. Zhang et al., "Porosity quantification for ductility prediction in high pressure die casting AM60 alloy using 3D X-ray tomography," Materials Science and Engineering: A, vol. 772, p. 138781, 2020.
- [16] Y. Zhang et al., "Ductility prediction of HPDC aluminum alloy using a probabilistic ductile fracture model," Theoretical and Applied Fracture Mechanics, vol. 119, p. 103381, 2022.
- [17] Y. Zhang et al., "Quantitative analysis of 3D pore characteristics effect on the ductility of HPDC Al-10Si-0.3 Mg alloy through X-ray tomography," Journal of Materials Research and Technology, vol. 26, pp. 8079-8096, 2023.
- [18] S. Isavand and A. Assempour, "Strain localization and deformation behavior in ferrite-pearlite steel unraveled by high-resolution in-situ testing integrated with crystal plasticity simulations," International Journal of Mechanical Sciences, vol. 200, p. 106441, 2021.
- [19] S. Isavand and A. Assempour, "Effects of microstructural morphology on formability, strain localization, and damage of ferrite-pearlite steels: experimental and micromechanical approaches," Metallurgical and Materials Transactions A, vol. 52, pp. 711-725, 2021.
- [20] D. Z. Sun, Y. S. Ma, and F. Andrieux, "Modeling of the influence of pore morphology on damage behavior of an aluminum die casting alloy," in Materials Science Forum, 2014, vol. 794: Trans Tech Publ, pp. 319-324.
- [21] Y.-S. Ma, D.-Z. Sun, F. Andrieux, and K.-S. Zhang, "Influences of initial porosity, stress triaxiality and Lode parameter on plastic deformation and ductile fracture," acta mechanica solida sinica, vol. 30, pp. 493-506, 2017.
- [22] J. Lian, H. Yang, N. Vajragupta, S. Münstermann, and W. Bleck, "A method to quantitatively upscale the damage initiation of dual-phase steels under various stress states from microscale to macroscale," Computational materials science, vol. 94, pp. 245-257, 2014.
- [23] Y. Abdin, S. Lomov, A. Jain, G. Van Lenthe, and I. Verpoest, "Geometrical characterization and micro-structural modeling of short steel fiber composites," Composites Part A: Applied Science and Manufacturing, vol. 67, pp. 171-180, 2014.
- [24] S. A. H. Motaman, F. Roters, and C. Haase, "Anisotropic polycrystal plasticity due to microstructural heterogeneity: A multi-scale experimental and numerical study on additively manufactured metallic materials," Acta Materialia, vol. 185, pp. 340-369, 2020.
- [25] S. J. Wolff, S. Lin, E. J. Faierson, W. K. Liu, G. J. Wagner, and J. Cao, "A framework to link localized cooling and properties of directed energy deposition (DED)-processed Ti-6Al-4V," Acta Materialia, vol. 132, pp. 106-117, 2017.
- [26] S. Isavand, M. Kardan-Halvaei, and A. Assempour, "Crystal plasticity modeling and experimental characterization of strain localization and forming limits in ferrite-pearlite steels," International Journal of Solids and Structures, vol. 233, p. 111205, 2021.
- [27] R. Liu et al., "Influence of pore characteristics and eutectic particles on the tensile properties of Al-Si-Mn-Mg high pressure die casting alloy," Materials Science and Engineering: A, vol. 783, p. 139280, 2020.
- [28] T. Li et al., "Anisotropic cyclic deformation behavior of an extruded Mg-3Y alloy sheet with rare earth texture," Journal of Magnesium and Alloys, vol. 10, no. 6, pp. 1581-1597, 2022.
- [29] Y. Xia et al., "The ductility variation of high-pressure die-cast AE44 alloy: the role of inhomogeneous microstructure," Metallurgical and Materials Transactions A, vol. 52, pp. 2274-2286, 2021.
- [30] Z. Li et al., "Characterization on the formation of porosity and tensile properties prediction in die casting Mg alloys," Journal of Magnesium and Alloys, vol. 10, no. 7, pp. 1857-1867, 2022.
- [31] E. Fiorese, F. Bonollo, G. Timelli, L. Arnberg, and E. Gariboldi, "New classification of defects and imperfections for aluminum alloy castings," International Journal of Metalcasting, vol. 9, pp. 55-66, 2015.
- [32] D. Cocks, "A proposed simple qualitative classification for die-casting defects," in Proc. Diecasting Conference, Montreaux, 1996, p. 19.
- [33] J. Campbell, Castings. Elsevier, 2003.
- [34] W. G. Walkington, Die casting defects.. Causes and solutions. NADCA, 1997.
- [35] M. Avalle, G. Belingardi, M. P. Cavatorta, and R. Doglione, "Casting defects and fatigue strength of a die cast aluminium alloy: a comparison between standard specimens and production components," International journal of Fatigue, vol. 24, no. 1, pp. 1-9, 2002.
- [36] S. G. Lee and A. M. Gokhale, "Formation of gas induced shrinkage porosity in Mg-alloy high-pressure die-castings," Scripta Materialia, vol. 55, no. 4, pp. 387-390, 2006.
- [37] E. Lordan et al., "On the probabilistic nature of high-pressure die casting," Materials Science and Engineering: A, vol. 817, p. 141391, 2021.
- [38] Y.-T. Yang et al., "Al-enabled properties distribution prediction for high-pressure die casting Al-Si alloy," Advances in Manufacturing, pp. 1-12, 2024.
- [39] M. M. Thakur, N. A. Henningsson, J. Engqvist, P.-O. Autran, J. P. Wright, and R. C. Hurley, "On mesoscale modeling of concrete: Role of heterogeneities on local stresses, strains, and representative volume element," Cement and Concrete Research, vol. 163, p. 107031, 2023.
- [40] W. Zhang, H. Jing, L. Xu, L. Zhao, Y. Han, and C. Li, "Numerical investigation of creep crack initiation in P92 steel pipes with embedded spherical defects under internal pressure at 650° С," Engineering Fracture Mechanics, vol. 139, pp. 40-55, 2015.
- [41] V. Poroshin and A. Shlishevsky, "The forecasting of deformational and strength properties of metals with uniformly scattered defects in form of spherical hollows at single and cyclic loading," Materials Today: Proceedings, vol. 11, pp. 58-65, 2019.
- [42] F. Klein and P. Wimmer, "Experimental Determination of the Influence of Casting Conditions on the Solidifaction of Zinc Die Castings," in Materials Science Forum, 1996, vol. 215: Trans Tech Publ, pp. 409-414.
- [43] J. Weiler and J. Wood, "Modeling the tensile failure of cast magnesium alloys," Journal of alloys and compounds, vol. 537, pp. 133-140, 2012.
- [44] S. Mohd, Y. Mutoh, Y. Otsuka, Y. Miyashita, T. Koike, and T. Suzuki, "Scatter analysis of fatigue life and pore size data of die-cast AM60B magnesium alloy," Engineering Failure Analysis, vol. 22, pp. 64-72, 2012.
- [45] F. Nichols, "Plastic instabilities and uniaxial tensile ductilities," Acta metallurgica, vol. 28, no. 6, pp. 663-673, 1980.
- [46] J. Lian and J. Chen, "Plastic instability and strain to fracture for damaged materials," Materials Science and Engineering: A, vol. 131, no. 1, pp. 9-15, 1991.
- [47] C. Hamilton, "Superplasticity," in Strength of Metals and Alloys (ICSMA 7): Elsevier, 1986, pp. 1831-1857.
- [48] I. Serrano-Munoz, J.-Y. Buffiere, C. Verdu, Y. Gaillard, P. Mu, and Y. Nadot, "Influence of surface and internal casting defects on the fatigue behaviour of A357-T6 cast aluminium alloy," International Journal of Fatigue, vol. 82, pp. 361-370, 2016.
- [49] Z. Xu, W. Wen, and T. Zhai, "Effects of pore position in depth on stress/strain concentration and fatigue crack initiation," Metallurgical and Materials Transactions A, vol. 43, pp. 2763-2770, 2012.
- [50] Y. Zhang et al., "Microstructure-property relationships in HPDC Aural-2 alloy: Experimental and CP modeling approaches," Materials Science and Engineering: A, vol. 848, p. 143364, 2022.
- [51] P. M. Carneiro, P. V. Gamboa, C. Baudín, and A. P. Silva, "Modelling of elastic modulus of a biphasic ceramic microstructure using 3D representative volume elements," Journal of the European Ceramic Society, vol. 40, no. 3, pp. 901-910, 2020.
- [52] G. Chen, A. Bezold, and C. Broeckmann, "Influence of the size and boundary conditions on the predicted effective strengths of particulate reinforced metal matrix composites (PRMMCs)," Composite Structures, vol. 189, pp. 330-339, 2018.
- [53] Q. Sun, S. Asqardoust, A. Sarmah, and M. K. Jain, "Elastoplastic analysis of AA7075-0 aluminum sheet by hybrid micro-scale representative volume element modeling with really-distributed particles and in-situ SEM experimental testing," Journal of Materials Science & Technology, vol. 123, pp. 201-221, 2022.
- [54] A. Moumen, M. Jammoukh, L. Zahiri, and K. Mansouri, "Numerical modeling of the thermo mechanical behavior of a polymer reinforced by horn fibers," Int. J, vol. 9, no. 4, 2020.
- [55] V. Felli, B. Noris, and R. Ognibene, "Eigenvalues of the Laplacian with moving mixed boundary conditions: the case of disappearing Dirichlet region," Calculus of Variations and Partial Differential Equations, vol. 60, pp. 1-33, 2021.
- [56] E. Totry, C. González, and J. LLorca, "Failure locus of fiber-reinforced composites under transverse compression and out-of-plane shear," Composites Science and Technology, vol. 68, no. 3-4, pp. 829-839, 2008.
- [57] Q. Sun et al., "Failure criteria of unidirectional carbon fiber reinforced polymer composites informed by a computational micromechanics model," Composites Science and Technology, vol. 172, pp. 81-95, 2019.
- [58] S. L. Kramer et al., "The third Sandia Fracture Challenge: predictions of ductile fracture in additively manufactured metal," International Journal of Fracture, vol. 218, pp. 5-61, 2019.
- [59] D. P. Naragani, J.-S. Park, P. Kenesei, and M. D. Sangid, "Void coalescence and ductile failure in IN718 investigated via high-energy synchrotron X-ray tomography and diffraction," Journal of the Mechanics and Physics of Solids, vol. 145, p. 104155, 2020.
- [60] O. West, J. Lian, S. Münstermann, and W. Bleck, "Numerical determination of the damage parameters of a dual-phase sheet steel," ISIJ international, vol. 52, no. 4, pp. 743-752, 2012.
- [61] V. Brinnel, J. Langenberg, F. Kordtomeikel, Y. Di, and S. Münstermann, "Numerical derivation of strain-based criteria for ductile failure: Discussions on sensitivity and validity," Engineering Fracture Mechanics, vol. 148, pp. 421-440, 2015.
9. 著作権:
- 本資料は、"Jian Yang, Bo Liu, Dongwei Shu, Qin Yang, Tiegang Hu" の論文 "Local stress/strain field analysis of die-casting Al alloys via 3D model simulation with realistic defect distribution and RVE modelling" に基づいています。
- 論文出典: https://ssrn.com/abstract=4968855
本資料は上記論文を紹介するために作成されたものであり、商業目的での無断使用を禁じます。 Copyright © 2025 CASTMAN. All rights reserved.