[Computer-Aided Design & Applications]에서 발행한 ["Predicting Die Cracking in Die-Cast Products Using a Surrogate Model Based on Geometrical Features"] 의 논문 연구 내용을 소개합니다.
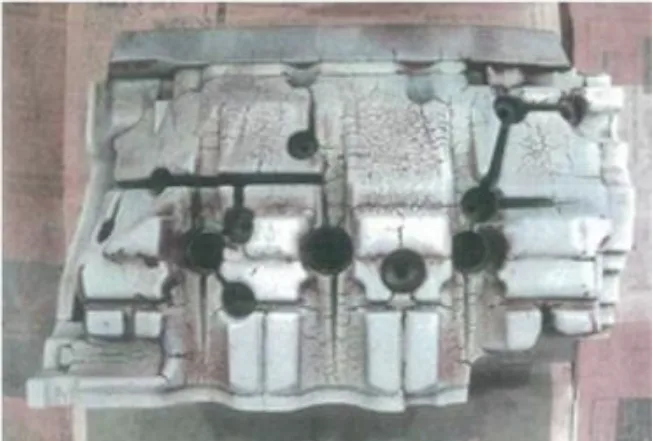
1. 概要:
- タイトル: 幾何学的特徴に基づく代用モデルを用いたダイカスト製品のダイクラック予測 (Predicting Die Cracking in Die-Cast Products Using a Surrogate Model Based on Geometrical Features)
- 著者: Tomoya Yamazaki, Koh Hirokawa, Akira Murakami, Misato Baba, Chisako Muramatsu
- 出版年: 2025年
- 掲載ジャーナル/学会誌: Computer-Aided Design & Applications, 22(2), 2025, 217-228
- キーワード: ダイカスト, 代用モデル, VAE, ニューラルネットワーク, コンピュータ支援設計, ダイクラック, 幾何学的特徴, 自動車産業, 機械学習, 欠陥予測, 3D形状データ (Die casting, Surrogate model, VAE, Neural network, Computer-aided design, die cracking, geometrical features, automotive industry, machine learning, defect prediction, 3D shape data)
2. 概要または序論
本論文では、製品設計の幾何学的特徴に着目し、ダイカスト製品におけるダイクラックを予測するための代用モデルの開発と応用について探求しています。ダイカストは、複雑な形状の製品を迅速に量産する効率性で知られる工法であり、特に自動車産業においては、車両重量の削減と部品点数の削減に大きく貢献しています。しかし、製品の品質保証と開発リードタイムの短縮は依然として重要な課題であり、製品設計段階における複雑な形状の欠陥予測の困難さによってさらに悪化しています。従来のシミュレーション技術は標準的であるものの、準備と実行に長時間を要するため、より効率的な欠陥予測のためにビッグデータと機械学習を活用する方向へと移行が進んでいます。本研究では、ダイカストにおける喫緊の課題であり、生産の遅延とコストの増大につながるダイクラックの発生を予測するために、Variational Autoencoders (VAE) とニューラルネットワークを用いた新規な代用モデルを導入します。トヨタ自動車株式会社のエンジンブロック部品とトランスアクスルケースを分析することにより、このモデルはダイクラックを高精度に予測する上で有望な結果を示しました。この知見は、製品形状データを活用して早期の欠陥検出を行うことでダイカストプロセスを改善し、製造効率と製品品質を向上させるための新たな方向性を示唆しています。
3. 研究背景:
研究トピックの背景:
ダイカストは、複雑な形状の製品を高速で量産できるため、工業生産、特に自動車産業で広く利用されており、近年、車両の軽量化と製品の部品点数削減の観点から改めて注目されています。工業製品としての高い競争力を確保するためには、市場のトレンドを正確に反映した製品をタイムリーに供給する必要があり、そのためには製品開発のリードタイムを短縮することが重要です。自動車産業における製品開発プロセスは通常、「製品設計」から「金型設計」、「生産性シミュレーション」、「工程設計」、「機能評価」、そして最終的に「量産」という流れを辿ります。このプロセスは一方通行ではなく反復的であり、各段階のサイクルを繰り返すことで製品設計の完成度を高めます。しかし、プロセスが進むにつれて仕様はより複雑になり、修正や手戻りが増加する傾向があります。したがって、可能な限り手戻りを少なくしてプロセスを進めることが重要です。手戻りの回数を減らし、製品開発リードタイムを短縮するためには、製品形状だけでなく、材料選定や製造計画の策定も製品設計の初期段階から考慮した高品質な設計を実現することが不可欠です。Pahl and Beitz [2] が述べているベストプラクティスによれば、最終製品が必要な基準をすべて満たすように、製品設計はこれらの側面を包含する必要があります。しかし、初期設計段階で複雑な形状の製品に対して正確な予測を行うことはしばしば困難であり、これらの要因が設計プロセスの初期段階で適切に考慮されない場合、手戻りにつながる可能性があります。このような背景から、「事前予測」とは、初期設計段階における潜在的な欠陥の予備的な見積もりを指します。これは、後続の設計段階で実施される詳細な予測とは異なります。正確な事前予測は、複雑な形状の製品にとっては困難であり、この段階での不正確さは手戻りの必要性を招く可能性があります。
既存研究の現状:
この問題を解決する一つの方法は、製品を製造する前にシミュレーションを用いて機能を予測し、事前に問題を修正することです。実際、シミュレーション技術は広く採用されており、工業製品の開発プロセスにおける標準的な技術となっています [3, 4, 5, 6]。鋳造シミュレーションにおいては、従来は溶融金属の流体解析に焦点が当てられていましたが、現在では背圧の影響を検証し、スパウトでの跳ね返り挙動に関する精度を向上させるために、周囲の空気圧縮挙動の計算も組み込まれるなど、精度向上の取り組みも行われています [7]。さらに、量子コンピュータを用いて計算時間を短縮し、検討サイクルを高速化する研究も行われています [8]。しかし、これらの技術が実用化されたとしても、シミュレーションを実行するためには、製造用の金型モデル情報を作成する必要があります。修正を含めると、1回のシミュレーションを完了するのに数日を要します。したがって、シミュレーションの精度向上と時間短縮が実現されたとしても、シミュレーションを利用した予備検討時間の長期化という問題の一部しか解決されず、製品開発の初期段階における容易な欠陥予測という課題は未解決のまま残されています。
研究の必要性:
シミュレーション技術の進歩には限界があるため、過去に製造された製品の欠陥発生情報や蓄積されたシミュレーション結果から得られたビッグデータを分析・活用し、パターン認識を現在および将来の生産性予測の付加価値に転換する代替アプローチが積極的に追求されています [9]。これらの取り組みの中でも、代用モデルとして知られる技術は、詳細なシミュレーションを実行する代わりに、既知のデータから得られたパターンを用いて予測を行う機械学習などの手法を採用しており、計算コストと事前準備情報の削減を可能にするため、注目を集めています。例えば、Amir Pouya は、ニューラルネットワークを用いてレーザー溶接加工パラメータを学習することにより、溶融プールの断面温度分布を予測できるモデルを提案しました [10]。さらに、Andres らは、低計算コストで航空機ブレードの断面形状を推定する手段として SVM を利用した予測モデルの有効性を報告しました [11]。したがって、既知のデータに基づいて、削減された元の情報で必要な予測を実行する代用モデルは、製品開発の初期段階において製品形状から製品品質を正確に予測するという問題を解決する可能性があります。しかし、これまでに報告されている事例の多くは、3次元現象を2次元に縮小して問題を単純化しており、複雑な3次元形状が予測の対象となる現象に直接適用できるかどうかを明確にする必要があります。また、製品の幾何学的情報に基づいた鋳造プロセスにおける欠陥発生に対する代用モデルの有効性に関する報告は非常に少ないです。実現可能性が示されれば、工業製品の開発プロセスに大きな影響を与えると考えられます。
4. 研究目的と研究課題:
研究目的:
本研究の目的は、製品設計の幾何学的特徴を利用して、ダイカスト製品におけるダイクラックを予測するための代用モデルを開発し、検証することです。その目標は、製品形状データを活用して早期の欠陥検出を強化し、ダイカストプロセスの効率を向上させることです。
主要な研究課題:
- ダイクラック予測のための Variational Autoencoders (VAE) とニューラルネットワークを用いた新規な代用モデルの開発。
- トヨタ自動車株式会社のエンジンブロック部品とトランスアクスルケースにおけるダイクラック予測におけるモデルの精度評価(幾何学的特徴を使用)。
- ダイカストにおける早期欠陥検出のための製品形状データ利用の有効性の検証。
- F1スコアを用いたモデル性能の分析と、ダイソルダーリングに関する既存の代用モデルとの比較。
5. 研究方法
研究デザイン:
本研究では、ダイクラック予測のための代用モデルを開発・評価する定量的なアプローチを採用しています。モデルは VAE とニューラルネットワークを用いて構築され、エンジンブロック部品とトランスアクスルケースのデータセットで訓練されます。モデルの予測性能は、その予測結果と CAE 解析結果を比較することで評価されます。
データ収集方法:
データは、トヨタ自動車株式会社がダイカストで製造した113種類のエンジンブロック部品と130種類のトランスアクスルケースの3D CADモデルで構成されています。SCSK株式会社の Adventure cluster を用いて計算された最大圧縮ひずみのシミュレーション結果が、ダイクラック予測の目標変数として使用されます。CADモデルは、特徴抽出のためにボクセルベースのモデルに変換されます。
分析方法:
- 代用モデルの構築: VAE は、ボクセル化された3Dモデルの表面から切り取られた立方体形状から特徴ベクトルを抽出するために訓練されます。次に、ニューラルネットワークは、これらの特徴ベクトルからシミュレーション結果(最大圧縮ひずみ)を予測するように訓練されます。
- モデル評価: F1スコアを評価指標として使用します。予測結果と CAE 解析結果は、閾値を超える値を持つ領域を欠陥領域として定義することで比較されます。F1スコアは、予測された欠陥領域と実際の欠陥領域の重複に基づいて計算されます。ブートストラップ法を用いて、ダイソルダーリングに関する既存の代用モデルとの性能比較を行います。
研究対象と範囲:
本研究は、トヨタ自動車株式会社がダイカストを用いて製造したエンジンブロック部品とトランスアクスルケースにおけるダイクラック予測に焦点を当てています。これらの部品の幾何学的特徴が、代用モデルの主要な入力となります。範囲は、熱応力、特に低サイクル疲労によって引き起こされるダイクラックに限定されます。
6. 主な研究成果:
主要な研究成果:
- 幾何学的特徴に基づいて、VAEとニューラルネットワークを用いたダイカスト製品のダイクラックを予測する代用モデルの開発に成功しました。
- このモデルは、トヨタ自動車株式会社のエンジンブロック部品とトランスアクスルケースにおけるダイクラック予測において有望な結果を示しました。
- エンジンブロック部品の場合、モデルは約0.62のF1スコアを達成し、真陽性 (TP) 594件、偽陰性 (FN) 208件、偽陽性 (FP) 530件でした。
- トランスアクスルケースモデルの場合、F1スコアは約0.58で、TP 174件、FN 73件、FP 178件でした。
- ダイクラック予測モデルの性能は、以前に開発されたダイソルダーリングの代用モデルの性能に匹敵します。
提示されたデータの分析:
- 図 6: VAEとニューラルネットワークの学習曲線を示しており、エンジンブロックモデルとトランスアクスルケースモデルの両方で適切な学習の進捗を示しています。
- 図 7: 決定閾値が変化するにつれてF1スコアの推移を示しており、両方のモデルで比較的高いF1スコアを達成できることを示しています。
- 図 8: F1スコアの差のブートストラップ分布を示しており、ダイクラック予測モデルがダイソルダーリングモデルと同程度の予測精度を達成していることを示唆しています。
- 図 9: モデル数の増加に伴うF1スコアの傾向を示しており、データ量が増加しても精度向上が飽和することを示しており、データ量を増やすだけでなく、アーキテクチャの変更が必要であることを示唆しています。
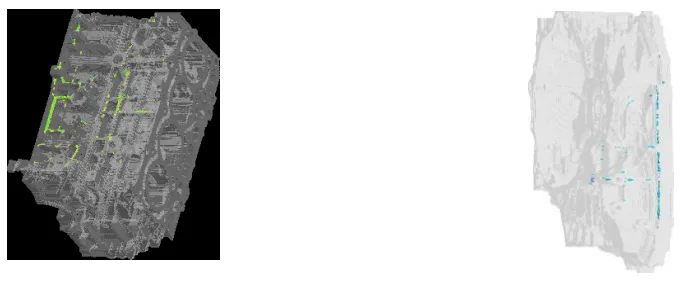
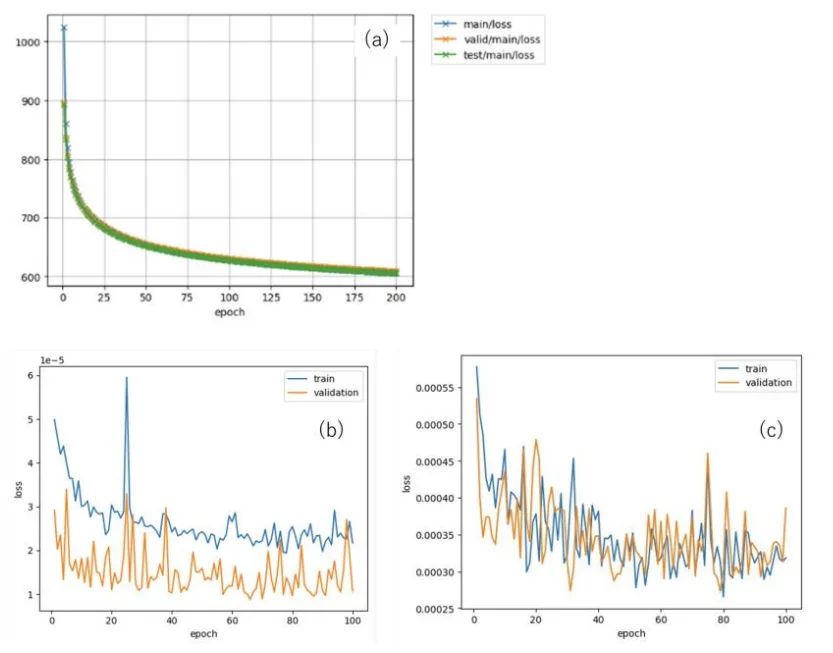
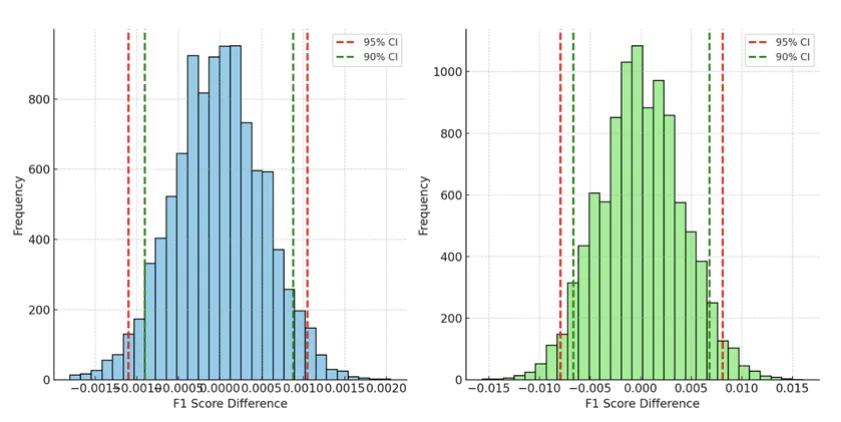
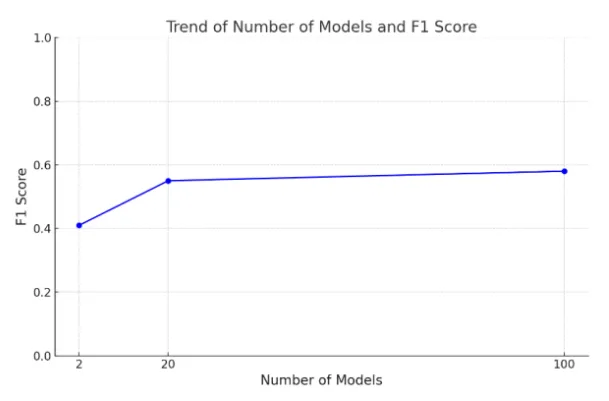
図のリスト:
- 図 1: 実際のダイカスト工程における金型の画像。表面にクラック(赤線)が入っている。 (Figure 1: Image of Die in the actual die-casting process, which has cracks (red lines) on the surface.)
- 図 2: 製品形状の画像 (a)エンジンブロック、(b)トランスアクスルケース。 (Figure 2: Image of product shape (a)Engine block, (b)Trans axel case.)
- 図 3: 代用モデルの構築のイメージ。 (Figure 3: Image of constructing the surrogate model.)
- 図 4: 評価方法のイメージ。 (Figure 4: Image of evaluation method.)
- 図 5: VAEとニューラルネットワークのアーキテクチャ。 (Figure 5: Architecture of VAE and neural network.)
- 図 6: a) VAE、b) エンジンブロック用ニューラルネットワーク、c) トランスアクスルケース用ニューラルネットワークの学習曲線。 (Figure 6: Train curve of a) VAE, b) Neural network for the engine block, and (c)Trans axel case.)
- 図 7: a) エンジンブロックの代用モデル、b) トランスアクスルケースの代用モデルのF1スコアの推移。 (Figure 7: Transition of F1 score of a) Engine block's surrogate model and b) Trans axel case's surrogate model.)
- 図 8: (a) エンジンモデルと参照モデル、(b) トランスアクスルケースモデルと参照モデル間のF1スコアの差のブートストラップ分布。 (Figure 8: Bootstrap distribution of F1 score difference between (a) Engine model and referenced model, and (b)Trans axel case model and referenced model.)
- 図 9: エンジンブロックモデルの数とF1スコアの傾向。 (Figure 9: Trends of the Number of Engine block models and F1 score)
- 図 10: (a) ルールベース予測と (b) 実際の金型モデルの例。 (Figure 10: Example of (a) rule-based prediction and (b) actual die model.)
- 図 11: 問題部分の金型アーキテクチャ。 (Figure 11: Die architecture of the pertinent part)
7. 結論:
主な知見の要約:
本研究では、製品形状のみを利用し、VAEとNNを活用することで、ダイカスト金型のダイクラック予測にある程度の精度を持つ代用モデルを構築できることが評価結果から示唆されました。このモデルは幾何学的特徴を活用し、以前のダイソルダーリング予測モデルと同等の性能を示しています。しかし、反対側の製品形状に冷却回路のような特徴的な形状要素が含まれている場合、この研究で適用された形状特性からの金型への応力影響を完全に考慮することができず、これらの領域での精度低下につながります。学習データに詳細な金型設計の特徴を含めることで精度を向上させることができますが、この試みの主な動機は、製品形状のみから欠陥を予測することであり、これは本研究で使用されたアプローチの固有の限界を示す可能性があります。
研究の学術的意義:
本研究は、ダイカストにおける重大な欠陥であるダイクラックの予測に、幾何学的特徴に基づく代用モデルを用いることの実現可能性を示すことで、この分野に貢献しています。VAEとニューラルネットワークをこの目的のために用いるという新しいアプローチを導入し、形状データを用いた予測精度のベンチマークを提供します。本研究は、ダイカストにおける形状ベースの欠陥予測の可能性と限界を明らかにし、この分野におけるさらなる研究への道を開くものです。
実用的な意義:
開発された代用モデルは、従来のシミュレーション技術と比較して、ダイカストにおける早期欠陥予測のためのより迅速かつ効率的な手法を提供します。製品形状データを活用することで、エンジニアは設計の初期段階でダイクラックのリスクの可能性を特定するのに役立ち、製品品質を向上させ、開発リードタイムとコストを削減するためのプロアクティブな設計変更を可能にします。
研究の限界と今後の研究分野:
モデルの精度は、表面形状データのみに依存しているため、熱応力とクラックに大きな影響を与える冷却回路のような金型内部の特徴を無視していることに限界があります。特に隠れた設計要素を持つ領域での偽陽性の発生は、この限界を示しています。今後の研究では、冷却回路の配置や金型内の温度分布など、より多面的な要因をモデルに組み込むことで、予測精度を向上させ、偽陽性を減らすことに焦点を当てる必要があります。学習アーキテクチャの根本的な変更を検討し、モデル学習データを最適化することも、さらなる精度向上のために提案されています。
8. 参考文献:
- [1] Czerwinski, F.: Current Trends in Automotive Lightweighting Strategies and Materials, Materials, 14(6631), 2024. http://doi.org/10.3390/ma14216631
- [2] Pahl, G.; Beitz, W.; Feldhusen, J.; Grote, K.-H.: Engineering Design: A Systematic Approach (3rd ed., Wallace, K.; Blessing, L., Trans. & Eds.), Springer, 2007.
- [3] Morgan, J. M.; Liker, J. K.: The Toyota Product Development System, Productivity Press, New York, NY, 2006.
- [4] Khalilpourazary, S.; Dadvand, A.; Azdast, T.; Sadeghi, M. H.: Design and manufacturing of a straight bevel gear in hot precision forging process using finite volume method and CAD/CAE technology, International Journal of Advanced Manufacturing Technology, 56, 87-95. http://doi.org/10.1007/s00170-011-3159-z
- [5] Kwon, H.-J.; Kwon, H.-K.: Computer-aided engineering (CAE) simulation for the design optimization of gate system on high pressure die casting (HPDC) process, Robotics and Computer-Integrated Manufacturing, 55(Part B), 2019, 147-153. http://doi.org/10.1016/j.rcim.2018.01.003
- [6] Liu, J.; Ma, Y.; Fu, J.; Duke, K.: A novel CACD/CAD/CAE integrated design framework for fiber-reinforced plastic parts, Advances in Engineering Software, 87, 2015, 13-29. http://doi.org/10.1016/j.advengsoft.2015.04.013
- [7] Matsushita, S.; Aoki, T.: Gas-liquid two-phase flows simulation based on a weakly compressible scheme with interface-adapted AMR method, 2021.
- [8] Gaitan, F.: Finding Solutions of the Navier-Stokes Equations through Quantum Computing—Recent Progress, a Generalization, and Next Steps Forward, 2021.
- [9] Fei, T.; Jiangfeng, C.; Qinglin, Q.; Meng, Z.; He, Z.; Fangyuan, S.: Digital twin-driven product design, manufacturing and service with big data, International Journal of Advanced Manufacturing Technology, 94, 2018, 3563-3576.
- [10] Hemmasian, A. P.; Ogoke, F.; Akbari, P.; Malen, J.; Beuth, J.; Barati Farimani, A.: Surrogate Modeling of Melt Pool Temperature Field using Deep Learning, Additive Manufacturing Letters, 5, 2023
- [11] Paulete-Periáñez, C.; Andrés-Pérez, E.; Lozano, C.: Surrogate modelling for aerodynamic coefficients prediction in aeronautical configurations, Proceedings of the 8th European Conference for Aeronautics and Space Sciences (EUCASS), http://doi.org/10.13009/EUCASS2019-870.
- [12] Yamazaki, T.; Hirokawa, K.; Murakami, A.; Baba, M.; Muramatsu, C.: Predicting Soldering Failure in Die-Cast Products Using a Surrogate Model Based on Geometrical Features, CAD Journal, 21(4), 2024, 581-590. http://www.cad-journal.net/files/vol_21/CAD_21(4)_2024_581-590.pdf
- [13] Brock, A.; Lim, T.; Ritchie, J. M.; Weston, N.: Generative and Discriminative Voxel Modeling with Convolutional Neural Networks, arXiv preprint arXiv:1608.04236.
- [14] Klobčar, D.; Tušek, J.; Taljat, B.: Thermal fatigue of materials for die-casting tooling, Materials Science and Engineering: A, 472(1-2), 2008, 198-207. http://doi.org/10.1016/j.msea.2007.03.025
- [15] ADVENTURE PROJECT Seminar Materials: Material and Geometric Nonlinear Algorithms (ADV_Solid), Presented on May 15, 2001, University of Tokyo. Retrieved from: https://adventure.sys.t.u-tokyo.ac.jp/jp/pub/seminar20010515/adv_seminar_solver_algo/index.htm
- [16] Roger, L.: An Introduction to the Boostrap, 2021.
- [17] Namiki, K.; Kawano, M.; Schade, T.: High Thermal Conductivity Steel and its Application to Die Casting Tools, NADCA Die Casting Congress & Exposition, Transaction No. T12-071, 2012.
- [18] Morris Jr, J. W.; Guo, Z.; Krenn, C. R.; Kim, Y.-H.: The Limits of Strength and Toughness in Steel, ISIJ International, 41(6), 2001, 599-611.
9. 著作権:
- この資料は、"Tomoya Yamazaki"氏の論文 "Predicting Die Cracking in Die-Cast Products Using a Surrogate Model Based on Geometrical Features" に基づいています。
- 論文ソース: https://doi.org/10.14733/cadaps.2025.217-228
この資料は上記論文を紹介するために作成されたものであり、商業目的での無断利用は禁止されています。
Copyright © 2025 CASTMAN. All rights reserved.