この記事では、[MDPI Materials] によって発行された論文 ["構造最適化とプロセス保証の統合:鋳造部品の陰関数モデリング"] を紹介します。
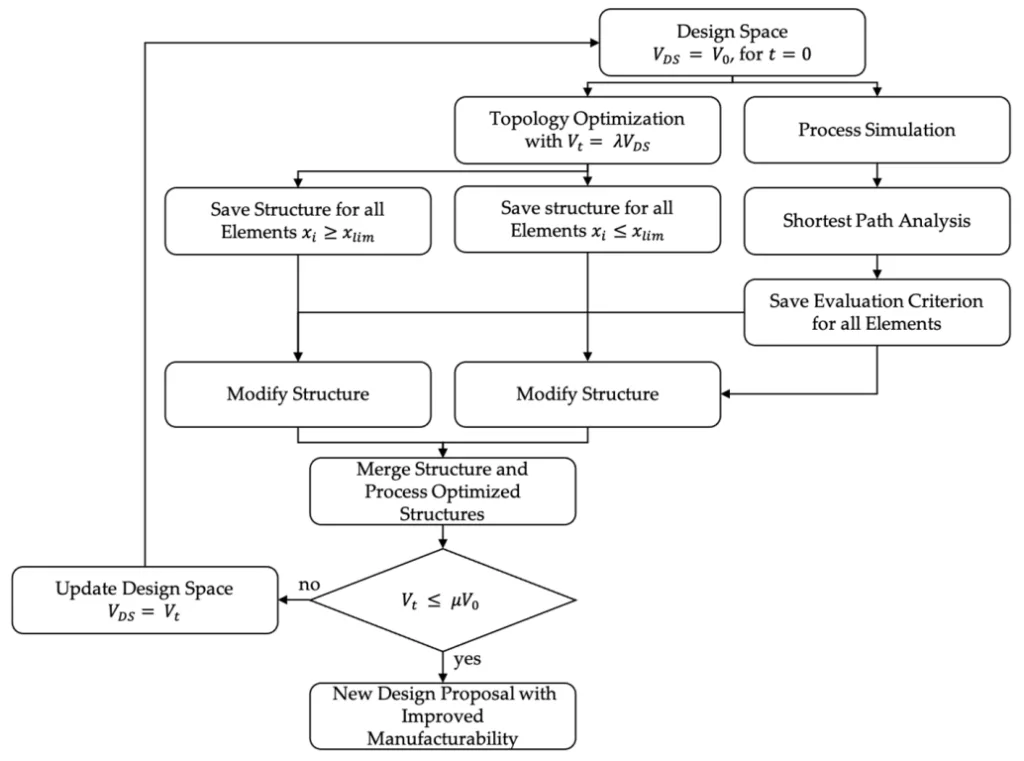
1. 概要:
- タイトル: 構造最適化とプロセス保証の統合:鋳造部品の陰関数モデリング (Combining Structural Optimization and Process Assurance in Implicit Modelling for Casting Parts)
- 著者: Tobias Rosnitschek, Maximilian Erber, Christoph Hartmann, Wolfram Volk, Frank Rieg, Stephan Tremmel
- 出版年: 2021年
- 出版ジャーナル/学会: Materials
- キーワード: ダイカスト (die casting); 陰関数モデリング (implicit modeling); プロセス保証 (process assurance); 構造最適化 (structural optimization); バーチャル製品開発 (virtual product development)
2. 概要または序論
製造可能な鋳造部品の構造最適化は、依然として挑戦的で時間のかかる課題です。今日では、トポロジー最適化 (TO) に続いて、設計案の手動再構築と、設計案を保証するためのプロセス保証シミュレーションが行われています。その結果、このプロセスは満足のいく妥協点に達するまで繰り返し反復されます。この記事では、陰関数ジオメトリモデリングを使用して、構造的およびプロセス的に最適化されたダイカスト部品を自動的に生成するために、構造最適化とプロセス保証の結果を組み合わせる方法を示します。したがって、現在の設計案を評価し、2つの反復間の製造可能性の改善を定量的に測定するための評価基準が開発されました。提案された方法をテストするために、片持ち梁をプルーフの例として使用します。組み合わせた反復法は、手動で設計された部品および直接最適化アプローチと比較され、機械的性能と製造可能性について評価されます。トポロジー最適化 (TO) とプロセス保証 (PA) 結果の組み合わせは自動化されており、設計案の手動再構築を大幅に強化することが示されています。さらに、製造可能性の改善は、計算量を削減しながら、この分野の以前の研究と同等以上であり、反復時間を大幅に短縮するために適切なメタモデルの必要性を強調しています。
3. 研究背景:
研究トピックの背景:
今日の製品開発は、市場投入までの時間の短縮と、エラーを最小限に抑えた製品設計の必要性によって特徴付けられます。したがって、部品は構造的に最適化され、プロセスも最適化されるべきです。なぜなら、最適化されたプロセス設計は、製造コストと不良率を削減するからです [1]。これらの最適化タスクは時間がかかり、高度な専門知識を必要とし、その結果を複数の手作業と組み合わせる必要があります。その結果、鋳造部品の構造最適化とプロセス保証を組み合わせるデジタルエンジニアリングには、大きな可能性があります [1-4]。
既存研究の現状:
基本的に、構造とプロセスの最適化は、2つの専門部門間で分担されており、部門間で部品が反復的に引き渡されます。各部門は、それぞれのプロセス用に取得したファイルを準備する必要があり、その後、最適化結果に基づいて新しい部品を手動で再設計する必要があります。このプロセスは、満足のいく妥協点に達するまで繰り返されます [1,2]。したがって、この記事では、構造的およびプロセス的に最適化された部品を自動的に作成するために、陰関数モデリングによる構造最適化とプロセス保証 (PA) の組み合わせに取り組みます。鋳造部品の構造最適化に関する既存の研究には、最小フィーチャサイズ、対称性、押し出しなどの製造制約を伴うトポロジー最適化 (TO) が含まれます。プロセスシミュレーションは、既知の形状の金型またはインゲートシステムを最適化するために使用されます。プロセス知識は、製造制約によって市販のTOに組み込まれていますが、プロセス知識のTOへのより深い統合は限られています。フルスケールの鋳造プロセスシミュレーションをTOに組み込んだ既存の研究は、高い反復時間のために計算コストが高くなります。
研究の必要性:
文献には、HPDC (高圧ダイカスト) および LPDC (低圧ダイカスト) 用の形状連動評価基準の開発に関するギャップがあり、TO中のプロセスシミュレーションの必要性を潜在的に減らすことができ、それでも設計案の製造可能性を質的に記述するのに十分な情報を示すことができます。設計案の形状を修正するための評価基準を調査し、プロセス全体を完全に自律化するために自動化を高度化する必要があります。この記事では、部品形状の修正のみに焦点を当てており、例えば [33] に示されているようなインゲートシステムの修正は、この記事の範囲外です。
4. 研究目的と研究課題:
研究目的:
本研究の目的は、TOとPAの結果を自動的に組み合わせ、構造的およびプロセス的に最適化された設計案を作成するための新しいワークフローを提示することです。鋳造プロセスベースの基準に基づいて、構造的に最適化された形状は、製造可能性を高めるために陰関数モデリングを介して修正されます。長期的な目標は、開発された基準を評価するためのメタモデルで鋳造プロセスシミュレーションを置き換えることです。
主な研究課題:
主な研究課題は、鋳造プロセス用の形状連動評価基準の機能性を開発し、証明することに焦点を当てています。ワークフローは、プロセス知識を鋳造部品のTOに統合し、陰関数モデリングを使用してTOとPAの結果を組み合わせます。PAには、CFDベースのプロセスシミュレーションに続いて、最短経路解析と評価基準の計算が使用されます。
研究仮説:
提案されたワークフローは、標準的なTO部品と比較して製造可能性が向上した新しい設計案をもたらすでしょう。TOとPAの組み合わせは、構造的およびプロセス的に最適化された部品につながるでしょう。
5. 研究方法
研究デザイン:
この研究では、TOとPAを並行して実施し、その後、陰関数モデリングを使用してそれぞれの最良の側面を組み合わせるワークフローを採用しています。ワンステップ最適化と反復最適化アプローチを区別しています。ワークフローは、HPDCプロセスとLPDCプロセスの両方でテストされています。
データ収集方法:
TOには、nTopologyソフトウェア (バージョン 3.0.4) と、SIMPを備えた密度ベースのTO法が使用されています。プロセスシミュレーションは、Flow-3D (v5.0 Update 4) ソフトウェアを使用して実行され、有限体積法 (FVM) と流体体積 (VOF) 法を採用しています。片持ち梁がベンチマークの例として使用されています。
分析方法:
製造可能性は、プロセスシミュレーションの結果から導き出された形状連動評価基準を使用して評価されます。HPDCの場合、最初の流体到達時間 (tffa) と理論的な最短経路時間 (tsp) の修正された商 (QuotHPDC) が使用されます。LPDCの場合、凝固時間 (tsol) とインゲートレベルまでの距離 (h) の対数商 (QuotLPDC) が使用されます。構造性能は、有限要素解析からの相対体積関連剛性 (SVR) によって評価されます。評価基準の中央値と製造可能な要素の数が分析されます。
研究対象と範囲:
研究は、ダイカスト部品、特にHPDCプロセスとLPDCプロセスを使用することに焦点を当てています。片持ち梁形状がテストケースとして使用されています。この研究では、ワンステップ最適化アプローチと反復最適化アプローチを調査し、それらをTOのみの設計および手動で再設計された部品と比較します。
6. 主な研究結果:
主な研究結果:
- 提案されたワークフローは、HPDCプロセスとLPDCプロセスの両方でTOとPAを組み合わせることに成功しました。
- 陰関数モデリングを使用した自動化された後処理ワークフローは、プロセス保証基準に基づいてTO形状を効果的に修正します。
- HPDCの場合、ワンステップ最適化 (HPDC-OS) は、初期設計空間と比較して159%の製造可能性の向上を達成し、反復最適化 (HPDC-IT) は68%の向上を示しました。
- LPDCの場合、ワンステップ (LPDC-OS) と反復最適化 (LPDC-IT) の両方のアプローチは、TOのみの設計と比較して、指向性凝固経路と製造可能性が向上した設計案をもたらしました。
- HPDC-OS設計案は、手動で設計されたHPDC-50と同等の製造可能性を示し、構造性能においてTOのみで最適化された形状よりも優れていました。
- LPDCの場合、両方の最適化アプローチは、TO形状と同等の相対体積関連剛性を達成しました。
提示されたデータの分析:
- 図17 は、HPDC設計のQuotHPDCの中央値を示しており、HPDC-OSが中央値が最も低いことを示しており、HPDC-ITおよび参照設計と比較して製造可能性が優れていることを示唆しています。
- 図18 は、HPDC設計の製造可能性を評価しており、HPDC-OSが初期設計空間と比較して製造可能な要素の割合が最も高いことを示しています。
- 図21 は、LPDC設計のQuotLPDCの中央値を提示しており、反復アプローチとワンステップアプローチで同様の中央値を示していますが、TO設計では値が低くなっています。
- 図22 は、LPDC設計の製造可能性を評価しており、TO形状は、提案されたアプローチと比較して、製造可能な要素の数が大幅に少ないことを示しています。
- 図23 は、HPDC設計の体積関連剛性を示しており、TO設計がワンステップアプローチと反復アプローチよりも優れていることを示していますが、HPDC-OSは手動で設計されたHPDC-50と同等です。
- 図24 は、LPDC設計の体積関連剛性を提示しており、TO形状を含むすべてのアプローチで同様の剛性を示しています。
図の名前リスト:
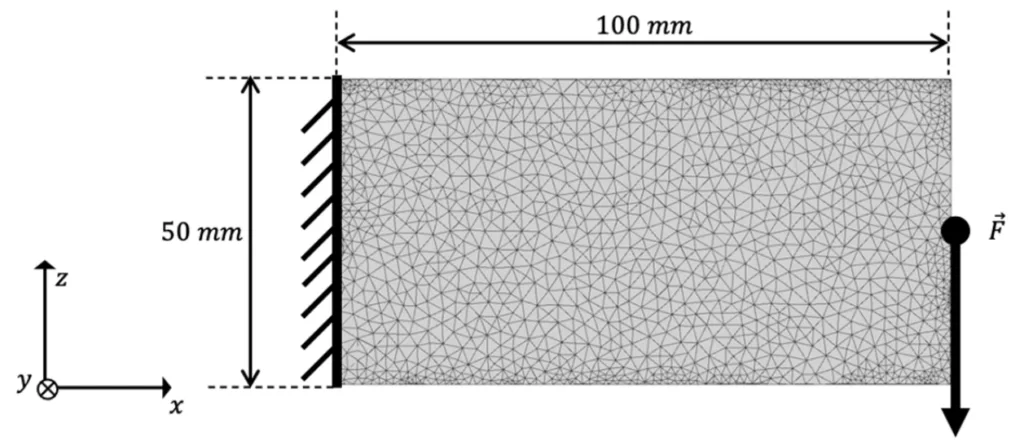
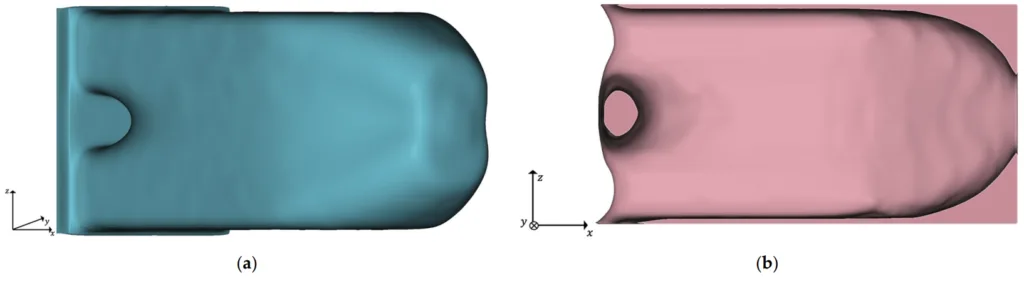
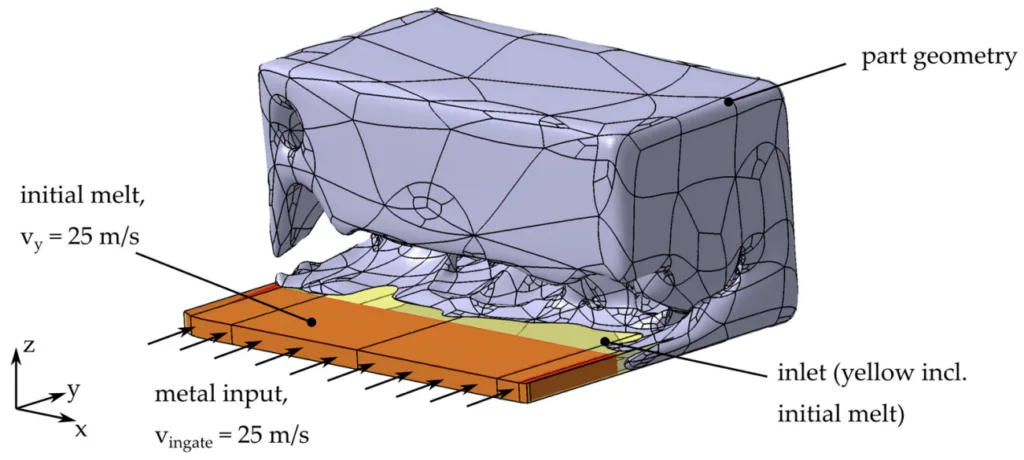
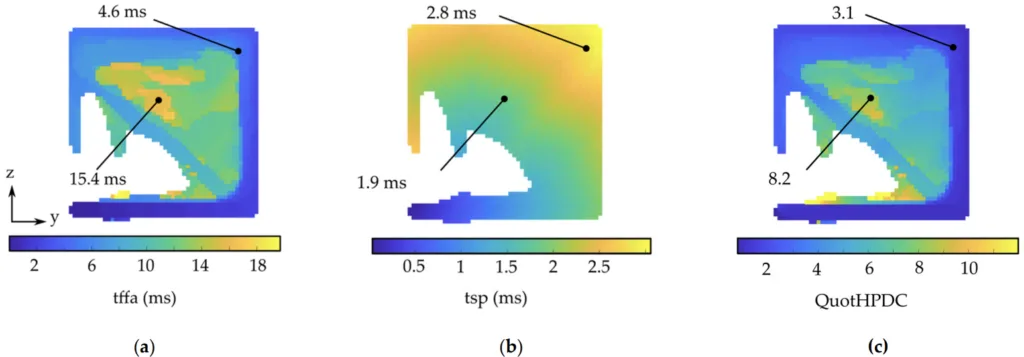
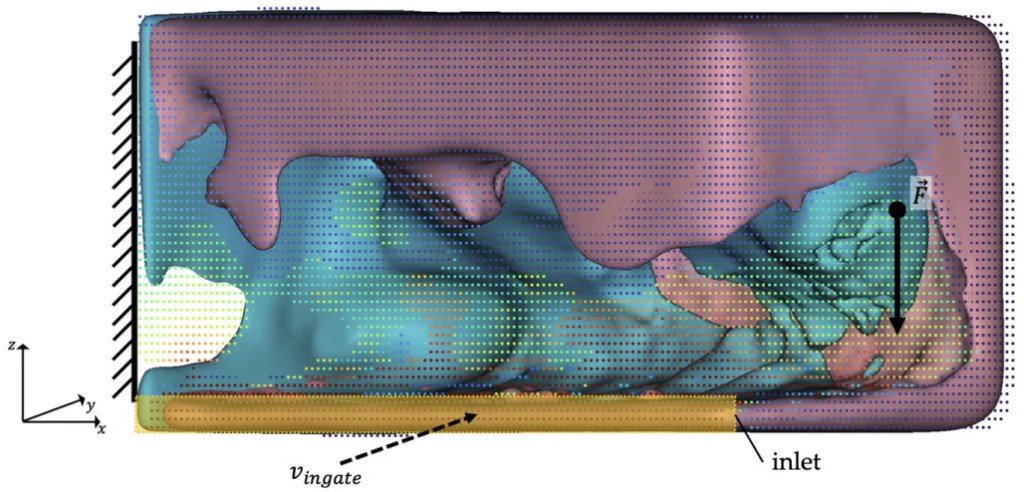
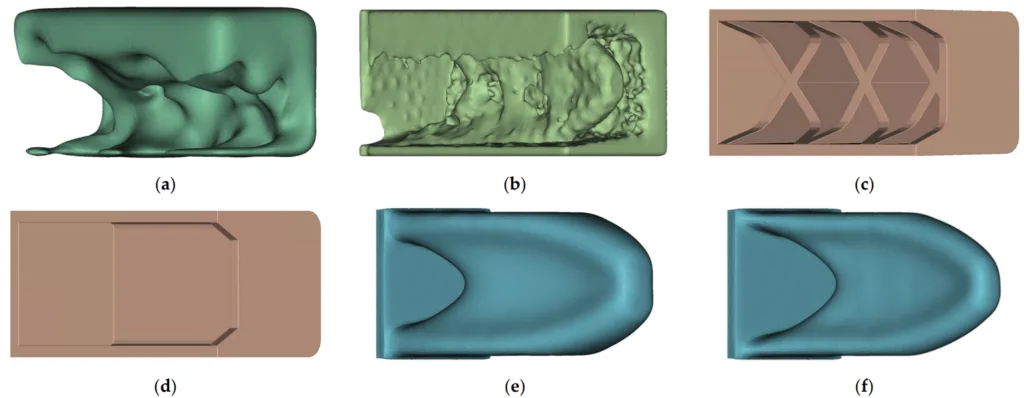
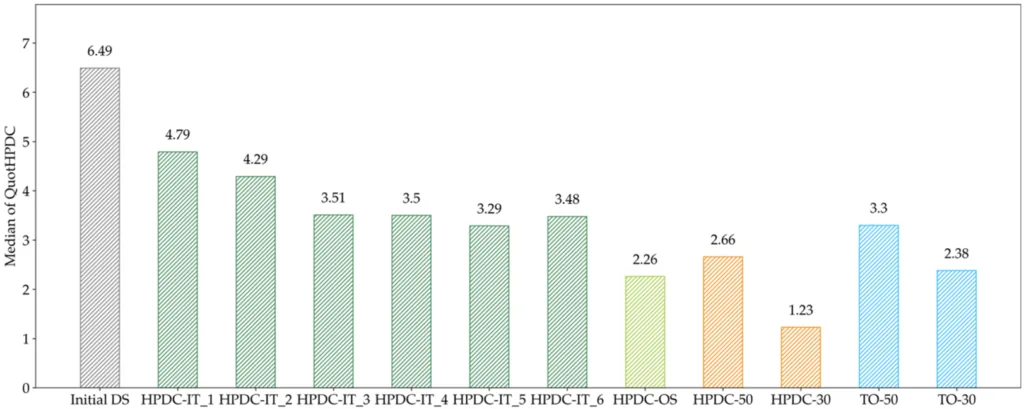
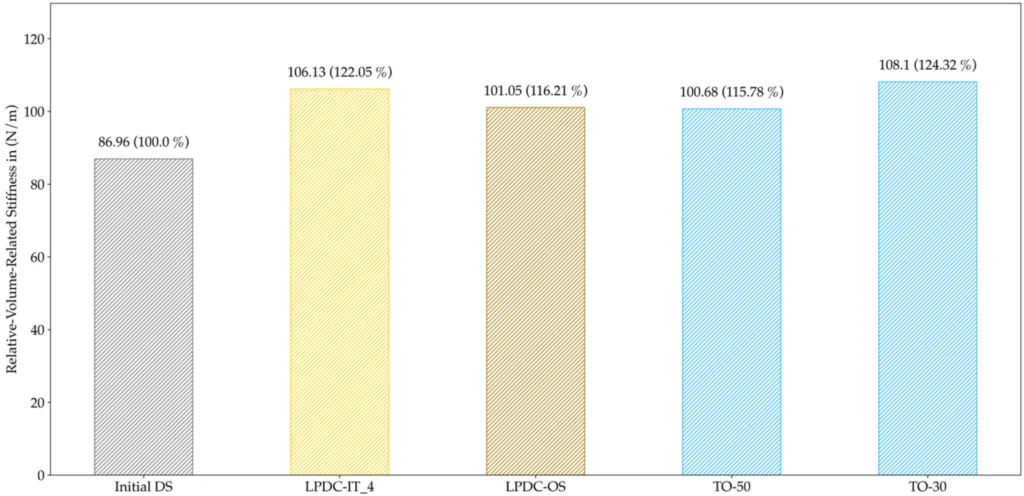
- Figure 1. トポロジー最適化とプロセス保証の組み合わせのための最適化の提案されたワークフロー。
- Figure 2. ベンチマーク例として使用される片持ち梁のセットアップ。
- Figure 3. λ = 0.2 および xlim = 0.6 の初期 TO の結果: (a) 最適化された構造の陰関数ジオメトリ; (b) TOマージンの陰関数ジオメトリの断面。
- Figure 4. HPDCのシミュレーションセットアップ、反復 t = 2 の例として示す。
- Figure 5. HPDCプロセスの充填シミュレーションの評価。
- Figure 6. LPDCのシミュレーションセットアップ、反復 t = 4 の例として示す。
- Figure 7. 後処理ワークフロー。
- Figure 8. 反復高圧ダイカストシミュレーションにおけるQuotHPDCの例示的なポイントマップ、反復 t = 2。
- Figure 9. 反復HPDC最適化の例によるTOマージンの適応メッシュの作成、反復 t = 5。
- Figure 10. 反復高圧鋳造最適化の例による平滑化前のTOマージンの陰関数ボリュームメッシュ、反復 t = 5。
- Figure 11. 反復高圧鋳造最適化の例による後処理ワークフローの最終結果、反復 t = 5。
- Figure 12. HPDC-OS最適化の結果、初期設計空間と比較して50%のボリューム。
- Figure 13. LPDC-OS最適化の結果、初期設計空間と比較して49%のボリューム。
- Figure 14. λ = 0.2 のHPDC部品の反復最適化の各反復の結果。
- Figure 15. λ = 0.2 のLPDC部品の反復最適化の各反復の結果。
- Figure 16. すべてのHPDCおよびTO設計案の比較。
- Figure 17. すべての最適化された形状のQuotHPDCの中央値の評価。
- Figure 18. HPDC設計案の製造可能性の評価。
- Figure 19. すべてのLPDCおよびTO設計案の比較: (a) LPDC-IT_4; (b) LPDC-OS; (c) TO-50; (d) TO-30。
- Figure 20. 中央面沿いの断面の凝固時間。
- Figure 21. LPDCプロセスにおけるすべての調査対象形状のQuotLPDCの中央値の評価。
- Figure 22. LPDC設計案の製造可能性の評価。
- Figure 23. すべてのHPDC形状の体積関連剛性。
- Figure 24. すべてのLPDC形状の体積関連剛性。
7. 結論:
主な調査結果の要約:
本研究では、陰関数モデリングと形状ベースの評価基準を使用してTOとPAを組み合わせる方法を提示し、設計案の再構築の自動化と鋳造部品の開発の加速化を実現しました。このアプローチは、片持ち梁でHPDCプロセスとLPDCプロセスに対して検証され、TOのみの設計と比較して製造可能性が向上していることが実証されました。ワンステップ最適化アプローチは、製造可能性と構造性能の点でHPDCに対して特に有望な結果を示しました。LPDCの場合、この方法は指向性凝固経路を促進しました。
研究の学術的意義:
この研究は、形状連動評価基準に関する文献のギャップに対処し、プロセス知識をトポロジー最適化に統合するための新しいワークフローを提供します。TOとPAの結果の自動化された組み合わせと陰関数モデリングの使用は、鋳造の設計最適化における進歩を表しています。開発された評価基準 (QuotHPDC および QuotLPDC) は、製造可能性評価のための定量的尺度を提供します。
実際的な意味合い:
自動化されたワークフローは、最適化された鋳造部品の開発における手動再設計の労力と時間を大幅に削減します。この方法により、設計者はプロセス保証の準備ができた構造的およびプロセス的に最適化された設計を生成でき、反復設計サイクルでの時間を節約できます。このアプローチは、市販のTOソフトウェアに適用可能であり、さまざまな鋳造プロセスに適応可能です。
研究の限界と今後の研究分野:
この研究では、ステップ長と設計空間が最適化の結果に影響を与える重要なパラメータとして特定されており、さらなる調査が必要です。後処理における平滑化パラメータとランプ設定も、今後の研究が必要です。時間のかかるプロセスシミュレーションを置き換えるメタモデルの必要性は、パラメータ研究とワークフロー全体のパフォーマンスの効率を高めるための今後の開発の重要な分野として強調されています。今後の研究では、複雑なLPDC部品の望ましい凝固軸を記述する方法の開発と、多目的最適化における製造可能性と構造性能のトレードオフの調査にも焦点を当てる必要があります。
8. 参考文献:
- [1] Hautsch, S.; Heilmeier, F.; Rieg, F.; Volk, W. Effiziente Entwicklung von prozessoptimalen druckgussbauteilen durch kombination von topologieoptimierung und prozesssimulation. In Stuttgarter Symposium für Produktentwicklung SSP17; Binz, H., Bertsche, B., Spath, D., Roth, D., Eds.; Fraunhofer-Institut für Arbeitswirtschaft und Organisation IAO: Stuttgart, Germany, 2017.
- [2] Heilmeier, F.; Goller, D.; Opritescu, D.; Thoma, C.; Rieg, F.; Volk, W. Support for Ingate Design by Analysing the Geometry of High Pressure Die Cast Geometries Using Dijkstra's Shortest Path Algorithm. Adv. Mater. Res. 2016, 1140, 400-407. [CrossRef]
- [3] Franke, T.; Fiebig, S.; Paul, K.; Vietor, T.; Sellschopp, J. Topology optimization with integrated casting simulation and parallel manufacturing process improvement. In Advances in Structural and Multidisciplinary Optimization; Schumacher, A., Vietor, T., Fiebig, S., Bletzinger, K.-U., Maute, K., Eds.; Springer International Publishing: Basel, Switzerland, 2018; ISBN 978-3-319-67987-7.
- [4] Franke, T.; Fiebig, S.; Bartz, R.; Vietor, T.; Hage, J.; vom Hofe, A. Adaptive Topology and Shape Optimization with Integrated Casting Simulation. In EngOpt 2018, Proceedings of the 6th International Conference on Engineering Optimization, Braunschweig, Germany, 5–9 June 2017; Rodrigues, H.C., Herskovits, J., Mota Soares, C.M., Araújo, A.L., Guedes, J.M., Folgado, J.O., Moleiro, F., Madeira, J.F.A., Eds.; Springer International Publishing: Basel, Switzerland, 2019; ISBN 978-3-319-97772-0.
- [5] Glamsch, J.; Deese, K.; Rieg, F. Methods for Increased Efficiency of FEM-Based Topology Optimization. Int. J. Simul. Model. 2019, 18, 453-463. [CrossRef]
- [6] Harzheim, L. Strukturoptimierung Grundlagen und Anwendung, 3rd ed.; Europa-Lehrmittel: Haan-Gruiten, Germany, 2019.
- [7] Rosnitschek, T.; Hentschel, R.; Siegel, T.; Kleinschrodt, C.; Zimmermann, M.; Alber-Laukant, B.; Rieg, F. Optimized One-Click Development for Topology-Optimized Structures. Appl. Sci. 2021, 11, 2400. [CrossRef]
- [8] Harzheim, L.; Graf, G. A Review of Optimization of Cast Parts Using Topology Optimization: I—Topology Optimization without Manufacturing Constraints. Struct. Multidisc. Optim. 2005, 30, 491-497. [CrossRef]
- [9] Harzheim, L.; Graf, G. A Review of Optimization of Cast Parts Using Topology Optimization: II—Topology Optimization with Manufacturing Constraints. Struct. Multidisc. Optim. 2006, 31, 388-399. [CrossRef]
- [10] Vatanabe, S.L.; Lippi, T.N.; de Lima, C.R.; Paulino, G.H.; Silva, E.C.N. Topology Optimization with Manufacturing Constraints: A Unified Projection-Based Approach. Adv. Eng. Softw. 2016, 100, 97-112. [CrossRef]
- [11] Gersborg, A.R.; Andreasen, C.S. An Explicit Parameterization for Casting Constraints in Gradient Driven Topology Optimization. Struct. Multidisc. Optim. 2011, 44, 875-881. [CrossRef]
- [12] Sato, Y.; Yamada, T.; Izui, K.; Nishiwaki, S. Manufacturability Evaluation for Molded Parts Using Fictitious Physical Models, and Its Application in Topology Optimization. Int. J. Adv. Manuf. Technol. 2017, 92, 1391-1409. [CrossRef]
- [13] Li, Q.; Chen, W.; Liu, S.; Fan, H. Topology Optimization Design of Cast Parts Based on Virtual Temperature Method. Comput. Aided Des. 2018, 94, 28-40. [CrossRef]
- [14] Wang, Y.; Kang, Z. Structural Shape and Topology Optimization of Cast Parts Using Level Set Method: Structural Shape and Topology Optimization of Cast Parts Using Level Set Method. Int. J. Numer. Meth. Eng. 2017, 111, 1252–1273. [CrossRef]
- [15] Xu, B.; Han, Y.S.; Zhao, L.; Xie, Y.M. Topology Optimization of Continuum Structures for Natural Frequencies Considering Casting Constraints. Eng. Optim. 2019, 51, 941-960. [CrossRef]
- [16] Nogowizin, B. Theorie und Praxis des Druckgusses; Schiele & Schön: Berlin, Germany, 2011.
- [17] Cuesta, R.; Delgado, A.; Maroto, A.; Mozo, D. Numerically modeling oxide entrainment in the filling of castings: The effect of the webber number. J. Oper. Manag. 2006, 58, 62–65. [CrossRef]
- [18] Kwon, H.-J.; Kwon, H.-K. Computer Aided Engineering (CAE) Simulation for the Design Optimization of Gate System on High Pressure Die Casting (HPDC) Process. Robot. Comput. Integr. Manuf. 2019, 55, 147-153. [CrossRef]
- [19] Dou, K.; Lordan, E.; Zhang, Y.J.; Jacot, A.; Fan, Z.Y. A Complete Computer Aided Engineering (CAE) Modelling and Optimization of High Pressure Die Casting (HPDC) Process. J. Manuf. Process. 2020, 60, 435-446. [CrossRef]
- [20] Mehtedi, M.E.; Mancia, T.; Buonadonna, P.; Guzzini, L.; Santini, E.; Forcellese, A. Design Optimization of Gate System on High Pressure Die Casting of AlSi13Fe Alloy by Means of Finite Element Simulations. Procedia CIRP 2020, 88, 509-514. [CrossRef]
- [21] Shahane, S.; Aluru, N.; Ferreira, P.; Kapoor, S.G.; Vanka, S.P. Finite Volume Simulation Framework for Die Casting with Uncertainty Quantification. Appl. Math. Model. 2019, 74, 132-150. [CrossRef]
- [22] Hirt, C.W.; Nichols, B.D. Volume of fluid (VOF) method for the dynamics of free boundaries. J. Comput. Phys. 1981, 39, 201-225. [CrossRef]
- [23] Cleary, P.; Ha, J.; Alguine, V.; Nguyen, T. Flow modelling in casting processes. Appl. Math. Model. 2002, 26, 171-190. [CrossRef]
- [24] Dabade, U.A.; Bhedasgaonkar, R.C. Casting Defect Analysis using Design of Experiments (DoE) and Computer Aided Casting Simulation Technique. Procedia CIRP 2013, 7, 616-621. [CrossRef]
- [25] Hahn, I.; Sturm, J. Von der Simulation zur gießtechnischen Optimierung. Giesserei 2015, 102, 86–100.
- [26] Hahn, I.; Sturm, J. Autonomous optimization of casting processes and designs. In Proceedings of the World Foundry Congress, Hangzhou, China, 16–20 October 2010; pp. 16-20.
- [27] Jadhav, A.R.; Hujare, D.P.; Hujare, P.P. Design and Optimization of Gating System, Modification of Cooling System Position and Flow Simulation for Cold Chamber High Pressure Die Casting Machine. Mater. Today Proc. 2021, S2214785320389598. [CrossRef]
- [28] Pinto, H.A.; Silva, F.J.G.; Martinho, R.P.; Campilho, R.D.S.G.; Pinto, A.G. Improvement and Validation of Zamak Die Casting Moulds. Procedia Manuf. 2019, 38, 1547–1557. [CrossRef]
- [29] Shahane, S.; Aluru, N.; Ferreira, P.; Kapoor, S.G.; Vanka, S.P. Optimization of Solidification in Die Casting Using Numerical Simulations and Machine Learning. J. Manuf. Process. 2020, 51, 130-141. [CrossRef]
- [30] Liu, J.; Ma, Y. A Survey of Manufacturing Oriented Topology Optimization Methods. Adv. Eng. Softw. 2016, 100, 161–175. [CrossRef]
- [31] Dijkstra, E.W. A note on two problems in connexion with graphs. Numer. Math. 1959, 1, 269-271. [CrossRef]
- [32] OPTIMAT: Entwicklung und Validierung von Softwaretools zur Simulation des Betriebsverhaltens von Werkstoffen in thermisch und Mechanisch Hoch Belasteten Komponenten, Arbeitsanteil NEMAK Wernigerode GmbH: Abschlussbericht, Berichtszeitraum: 1 May 2007–31 October 2010. Werkstoffinnovation für Industrie und Gesellschaft—WING: 2010. Available online: https://www.tib.eu/de/suchen?tx_tibsearch_search%5Baction%5D=download&tx_tibsearch_search%5Bcontroller%5D=Download&tx_tibsearch_search%5Bdocid%5D=TIBKAT%3A717891933&cHash=74e07aebe8553baac3ac1f2580585d68#download-mark (accessed on 1 July 2021).
- [33] Majernik, J.; Gaspar, S.; Kmec, J.; Karkova, M.; Mascenik, J. Possibility of Utilization of Gate Geometry to Modify the Mechanical and Structural Properties of Castings on the Al-Si Basis. Materials 2020, 13, 3539. [CrossRef]
- [34] nTopology's Implicit Modeling Technology. Available online: https://ntopology.com/resources/whitepaper-implicit-modeling-technology/ (accessed on 25 April 2021).
9. 著作権:
- この資料は、"[Copyright: 2021 by the authors.]" 氏の論文「"構造最適化とプロセス保証の統合:鋳造部品の陰関数モデリング"」に基づいています。
- 論文ソース: https://doi.org/10.3390/ma14133715
この資料は上記の論文を紹介するために作成されたものであり、商業目的での無断使用は禁止されています。
Copyright © 2025 CASTMAN. All rights reserved.