This paper introduction was written based on the 'INDUSTRY 4.0 FOUNDRY DATA MANAGEMENT AND SUPERVISED MACHINE LEARNING IN LOW-PRESSURE DIE CASTING QUALITY IMPROVEMENT' published by 'International Journal of Metalcasting'.
1. 概要:
- タイトル: INDUSTRY 4.0 FOUNDRY DATA MANAGEMENT AND SUPERVISED MACHINE LEARNING IN LOW-PRESSURE DIE CASTING QUALITY IMPROVEMENT (INDUSTRY 4.0 鋳造データ管理と教師あり機械学習による低圧ダイカスト品質改善)
- 著者: Tekin Ç. Uyan, Maria Santos Silva, Pedro Vilaça, Kevin Otto, Elvan Armakan
- 出版年: 2023年
- 出版ジャーナル/学会: International Journal of Metalcasting
- キーワード: 低圧ダイカスト, 機械学習, アルミホイール, インダストリー4.0, スマートファウンドリ, 持続可能な金属加工
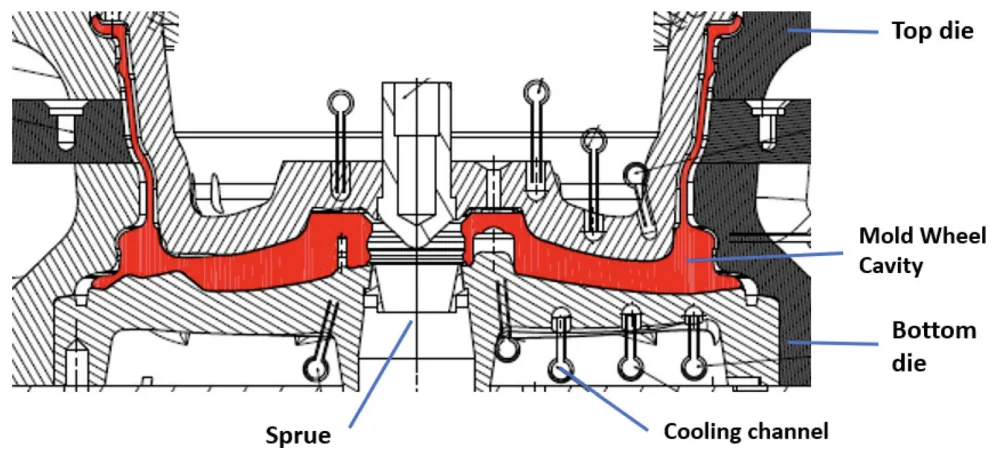
2. 概要または序論
低圧ダイカスト(LPDC)は、高性能、高精度なアルミニウム合金自動車ホイール鋳物の製造に広く使用されており、気孔率欠陥などの欠陥は許容されません。LPDC部品の品質は、鋳造プロセス条件に大きく影響されます。ガスや収縮気孔率などの困難な欠陥に対する部品品質を向上させるためには、プロセス変数を最適化する必要があります。これを行うには、プロセス変数の測定値を欠陥の発生率と照らし合わせて調査する必要があります。本論文では、Industry 4.0クラウドベースのシステムを使用してデータを抽出します。これらのデータを用いて、実際の鋳造アルミニウムLPDCプロセスで欠陥を予測する条件を特定するために、教師あり機械学習分類モデルが提案されています。このプロセスの欠陥率は小さく、潜在的なプロセス測定変数が多数存在するため、根本原因の分析は困難です。XGBoost分類アルゴリズムに基づくモデルを使用して、プロセス条件と欠陥のあるホイールリムの生成との間の複雑な関係をマッピングしました。データは、特定のLPDCマシンとダイモールドから、3シフト、6日間連続で収集されました。気孔率欠陥の発生率は、かなり小さなサンプル(1077個のホイール)から収集された13のプロセス変数からの36の特徴量を使用して予測でき、非常に偏っており(欠陥品62個)、良品で87%の精度、気孔率欠陥のある部品で74%の精度でした。この研究は、欠陥を減らすための新製品の量産前段階でのプロセスパラメータ調整を支援する上で役立ちました。
3. 研究背景:
研究トピックの背景:
低圧ダイカスト(LPDC)は、高性能、高精度、大量生産が求められる金属鋳造部品、特に自動車産業におけるアルミニウム合金ホイールリムの製造において広く利用されています。気孔率の不連続性は、LPDCアルミニウム製品で最も頻繁に見られる欠陥の一つです。これらは回避が難しく、部品の完全性と性能を損なう可能性があります。したがって、気孔率欠陥の原因と防止は品質管理において重要な考慮事項であり、部品品質を向上させるためにプロセス変数を最適化する要求を生み出しています。気孔率欠陥の原因は、金属組成、水素含有量、鋳造圧力、温度、指向性凝固速度を得るための金型熱管理など、さまざまな要因に起因する可能性があります。このような鋳造欠陥が発生した場合、正確な根本原因を診断し、適切なプロセスパラメータ変更を行うことはしばしば困難です。気孔率欠陥を引き起こす可能性のあるプロセス設定と逸脱を監視および分析する手段が必要です。Industry 4.0品質管理システムは、すべてのプロセス測定ポイントから記録されたデータを、検査結果を含む個々の部品に関連付けることができます。これにより、機械学習分類器アルゴリズムを利用して、プロセス欠陥を引き起こすプロセス設定の組み合わせを特定できます。これらは、プロセス制御の調整に役立てることができます。
既存研究の現状:
LPDC生産は歴史的に高い不良率を示しており、通常、すべての生産部品は気孔率欠陥についてX線検査されています。この研究は気孔率欠陥を予測するのに役立ちますが、検査のためのX線装置に取って代わることはできません。しかし、気孔率欠陥の原因を定量化するのに役立ちます。典型的な鋳造工場では、数百種類のモデルと、毎年数十種類の新製品モデルが導入されます。量産前のプロセス設定を迅速に調整することが重要です。最初のセクションでは、LPDC鋳造工場の生産運転中に欠陥の原因を特定する際の課題が提示され、その後、関連研究について議論します。「Industry 4.0 Foundry Data Collection」では、鋳造工場全体で部品と関連データをデジタルタイムスタンプで追跡するためのIndustry 4.0データ収集システムが提示されています。「LPDC Porosity Defect Prediction」では、監視された鋳造欠陥について議論します。次に、「Classification Algorithm Model」では、気孔率欠陥が発生するプロセス条件を分類する統計的機械学習モデルが提示されています。
研究の必要性:
工場データを使用して欠陥部品の発生を予測する機械学習モデルを構築することは、いくつかの理由から困難です。潜在的な因果関係の要因の数が膨大であること、これらのプロセスデータをすべて収集するために計測することが困難な場合があります。また、時系列データの特徴を特定する必要があります。これには、高低シフト、変動が大きすぎる、またはデータ対時間のジャンプなどが含まれます。欠陥の原因に関連付けられる可能性のある特徴が検討されます。さらに、収集されたプロセスデータは、実際に生産されている部品に関連付けられている必要があります。これにより、これらのプロセス条件を部品の合格または不合格の指標に関連付けることができます。プロセスデータを収集するだけでは不十分であり、プロセスデータは部品にタグ付けする必要があります。これは、どのプロセスデータをどの部品に関連付けるかを知るために、部品を鋳造工場全体で追跡する必要があることを意味します。これは、スマートファウンドリの重要なIndustry 4.0の課題の1つです。鋳造工場は過酷な条件下で操業しており、投入材料の流れの開始から最終鋳造部品まで、各部品を追跡およびマークすることは困難です。2番目の課題は、時系列データを機械学習統計分析用の特徴量に前処理することです。完全なデータセットではなく、プロセスエンジニアが理解できるエンジニアリング統計を検討することが有用です。たとえば、時系列の圧力、温度、冷却データを位相に分離し、各位相内の統計量を計算できます。これには、データを充填や凝固などの位相に分離し、位相内の平均や分散などの特徴量を計算することが含まれる場合があります。プロセスエンジニアは、さまざまな位相での平均シフトと変動の大小が歩留まりにどのように影響するかを理解したいと考えています。最後に、特徴量が与えられた場合、これらの特徴量を欠陥率に関連付けるために利用可能な代替分類手法も多数存在します。全体として、機械学習を活用して欠陥の原因と根本原因をより深く理解するための研究機会が存在します。現在の鋳造工場のプロセス制御は、一般的に検査ベースの受入手順です。投入材料、鋳造結果の品質管理、およびプロセス制御は、指定された制限内でコンプライアンスについて検査または監視されます。部品の欠陥は、気孔率ボイドの存在に関するX線画像の目視検査によって定義されます。操業上の問題は、入力が許容範囲外になった場合に定義されます。この現状では、欠陥制御が困難になっています。第一に、目視検査と手動制御は、かなりの再現性と再現性の測定誤差を伴う可能性があります。また、このアプローチでは、許容範囲内の入力の組み合わせが、気孔率欠陥を発生させることを知らずに許容してしまう可能性があります。プロチャによって導入されたように、ステップバイステップの知識ベースのアプローチを採用して、より高品質な成果を得るために、鋳造プロセスの人工知能とデータ駆動型プロセス制御を構築します。Industry 4.0スマートファウンドリを構築する上での課題は、データサイエンス、機械学習、および人工知能手法を鋳造工場の操業に適用することです。部門内のデータサイロ、利用可能なプロセス測定ポイントの過多、および部品検査ポイントの限定的なセットという障壁が存在します。最初の課題は、データの時間スケールと、データが生成および保存される鋳造工場内の場所の違いです。材料データはバッチレベルであり、溶解工場内で保持されます。プロセスデータは1秒間隔であり、個々のLPDCマシン内で保持されます。検査データは部品レベルであり、X線装置内で保持されます。これらのデータセットは、通常、部門内でサイロ化されており、共有されることはほとんどありません。
4. 研究目的と研究課題:
研究目的:
本研究の目的は、LPDC鋳造工場のプロセスデータを収集し、機械学習モデルを使用して、プロセスパラメータと公差を、使用できなくなる重大な欠陥の発生と関連付ける方法を開発することです。この方法には、機械プロセスデータ収集、部品追跡、および欠陥データの品質検査が含まれます。この研究は、プロセス設定の確立を支援するために、小規模なデータセットで機械学習アプリケーションを備えた産業用鋳造工場を代表するものである点で異なります。LPDCマシンおよび金属関連の特徴量は、アルミニウム合金高性能自動車ホイールのLPDC加工における気孔率欠陥を予測するために利用されました。
主要な研究課題:
- LPDC鋳造工場向けのIndustry 4.0データ収集システムを開発し、部品と関連データをデジタルタイムスタンプで追跡する。
- 教師あり機械学習分類モデル、特にXGBoostを適用して、気孔率欠陥を予測するプロセス条件を特定する。
- 時系列プロセスデータを、機械学習分析に関連する統計的特徴量に特徴量エンジニアリングする。
- 小規模で不均衡な産業データセットを使用して、気孔率欠陥を予測するモデルの性能を評価する。
- Shapley値を用いた特徴量重要度分析により、気孔率欠陥に影響を与える主要なプロセスパラメータを特定する。
研究仮説:
- Industry 4.0データ収集システムと機械学習を組み合わせることで、日常的に収集される生産データを使用して、LPDCプロセスにおける気孔率欠陥を効果的に予測できる。
- XGBoostアルゴリズムは、不均衡なデータセットの処理に適しており、限られたデータセットでLPDCにおける気孔率欠陥を予測する上で許容可能な精度を達成できる。
- 時系列プロセスデータから抽出された統計的特徴量は、プロセス変動を効果的に表現し、気孔率欠陥の発生と相関関係がある。
- 特徴量重要度分析を通じて主要なプロセスパラメータを特定することで、LPDCにおけるプロセス最適化と欠陥削減のための実用的な洞察が得られる。
5. 研究方法
研究デザイン:
本研究では、産業用LPDC鋳造工場からの過去の生産データを利用したデータ駆動型アプローチを採用しました。研究は、アルミニウム合金ホイール鋳物を製造する特定のLPDCマシンとダイモールドに焦点を当てました。データ収集は、3シフト、6日間連続で行われました。研究デザインには以下が含まれます。
- データ収集システムの実装: Industry 4.0クラウドベースのシステムを利用して、さまざまなソース(LPDCマシンセンサー、材料バッチデータ、X線検査データ)からプロセスデータを抽出し、統合する。
- 部品追跡: 部品を鋳造プロセス全体で追跡するシステムを実装し、プロセスデータを品質検査結果にリンクする。
- 特徴量エンジニアリング: 時系列プロセスデータを前処理して、気孔率欠陥の形成に関連する統計的特徴量(平均、標準偏差、期間)を抽出する。
- 機械学習モデルの開発: 抽出された特徴量に基づいて気孔率欠陥を予測するために、XGBoost分類モデルをトレーニングおよび評価する。
- モデル検証: データセットの層化分割をトレーニングセットとテストセットに用いてモデル性能を評価し、10分割交差検証を採用する。
- 特徴量重要度分析: Shapley値を利用してXGBoostモデルを解釈し、気孔率欠陥に影響を与える主要なプロセスパラメータを特定する。
データ収集方法:
データは、トルコ、イズミルにあるCevher Wheels Casting Plantから収集されました。データ収集プロセスには以下が含まれます。
- LPDCマシンデータ: 成形圧力、温度、空気および水路冷却を監視するセンサーからの時系列データ。1〜2秒間隔で記録。
- 材料バッチデータ: アルミニウム合金金属バッチ特性。密度指数(DI)とシリコン含有量(Si)を含む。炉で採取したサンプルの実験室化学分析から取得。
- X線検査データ: 気孔率欠陥の合否結果。DIN EN ISO 19232-1およびDIN EN ISO 19232-5規格に従って、ホイールリムの100%X線スキャンによって決定。
- 部品追跡データ: プロセスの各段階(LPDCマシン、X線検査)でのタイムスタンプと部品識別子。データセットをリンクするため。
分析手法:
採用された分析手法は以下のとおりです。
- 統計的特徴量抽出: 時系列データは位相(充填、凝固など)にセグメント化され、圧力や温度などの変数について各位相の統計的特徴量(平均、標準偏差)が計算されました。
- XGBoost分類: XGBoostアルゴリズムは、二項分類(良品/不良品)に使用されました。ハイパーパラメータチューニングは、Hyperoptライブラリのベイズ最適化を使用して実行されました。
- 性能指標: モデル性能は、精度、適合率、再現率、F1スコアを使用して評価されました。曲線下面積(AUC)は、ハイパーパラメータ最適化の目的関数として使用されました。
- Shapley値分析: Shapley値は、各入力特徴量のモデル予測への寄与を決定するために計算され、特徴量重要度に関する洞察を提供しました。
研究対象と範囲:
研究対象は、Cevher Wheels Casting Plantの特定のLPDCマシンとダイモールドで製造されたアルミニウム合金ホイール鋳物でした。データセットは1077個のホイールリムで構成され、そのうち62個が気孔率による欠陥品と特定されました。範囲は気孔率欠陥に限定されており、他の種類の鋳造欠陥は含まれていません。分析は、LPDCマシンの操作と材料特性に関連する13のプロセス変数から派生した36の特徴量に焦点を当てました。
6. 主な研究結果:
主要な研究結果:
- XGBoost分類モデルは、テストデータセットで良品を予測する精度が87%、気孔率欠陥のある部品を予測する精度が74%を達成しました。
- Shapley値を用いた特徴量重要度分析により、気孔率欠陥の最も重要な予測因子として、エアチャネル流量、特に中心ハブ付近のチャネルにおけるエアフローの標準偏差、および溶融シリコン含有量が特定されました。
- このモデルは、小規模で不均衡な産業データセットを使用して気孔率欠陥を予測する能力を示し、LPDCにおける品質改善のための機械学習の可能性を強調しました。
- 適合率と再現率のトレードオフが観察され、特定の鋳造工場のニーズに基づいて偽陽性または偽陰性を最小限に抑えることを優先するようにモデルパラメータを調整することが可能になりました。
提示されたデータの分析:
- 混同行列(図6): モデルの分類性能を示しており、TN=440、FN=65、FP=8、TP=23となっています。これは、不良品(再現率74%)と比較して、良品(再現率87%)の精度が高いことを示しています。
- 統計的要約レポート(表2): 良品と不良品の両方について、適合率、再現率、F1スコアを提供し、モデルの性能をさらに定量化しています。
- 二項決定木推定器の例(図7): XGBoostモデルからの簡略化された決定木を示しており、特定の特徴量値(エアチャネル2 std、密度指数など)が故障の確率にどのように影響するかを示しています。
- 特徴量重要度順序(図8): Shapley指数に基づいて入力特徴量をランク付けし、気孔率欠陥の予測において最も影響力のある変数を強調しています。上位の特徴量は、さまざまな冷却チャネルのエアフロー標準偏差と溶融シリコン含有量に関連しています。
- モデルトレードオフ曲線(図9): 合格精度と不合格精度のトレードオフを示しており、不良品予測精度を上げると良品予測精度が低下し、その逆もまた然りであることを示しています。
図の名前リスト:
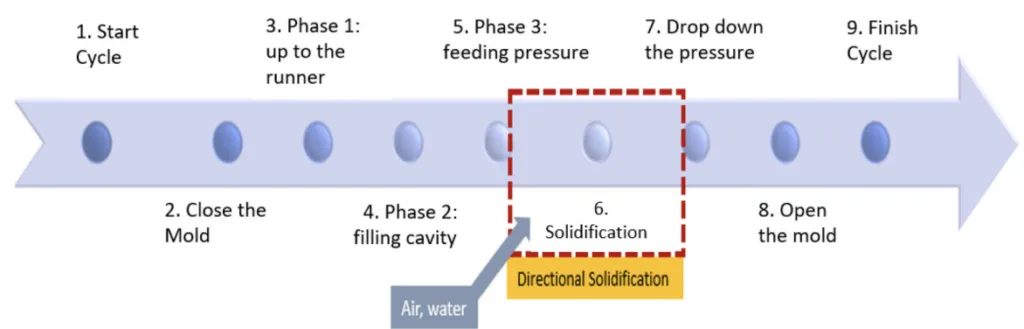


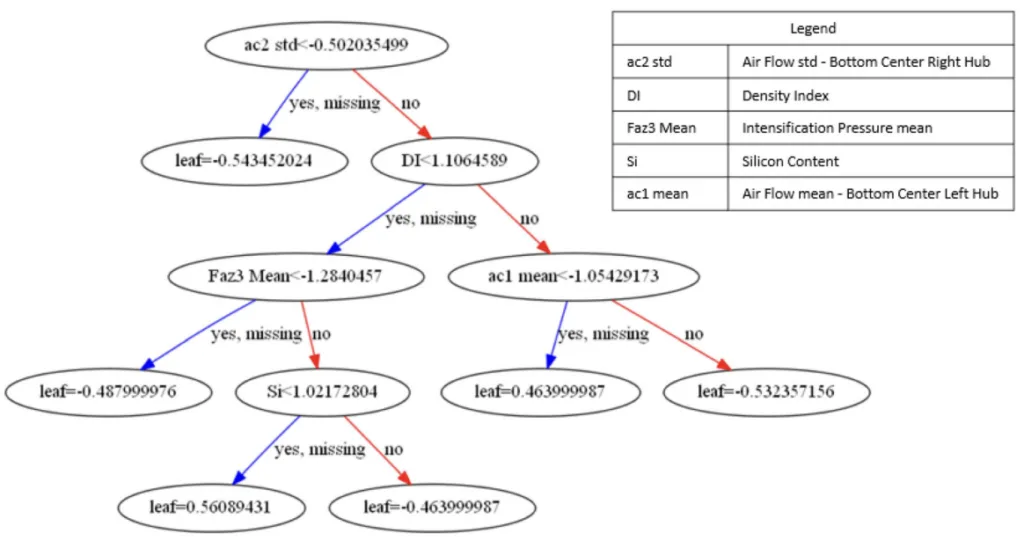
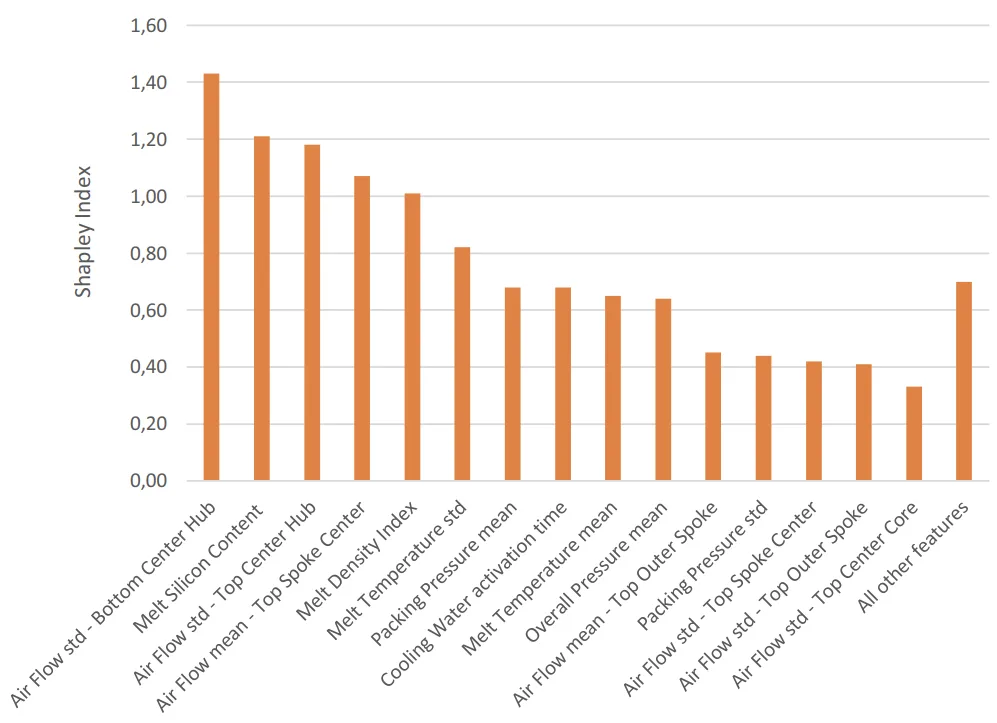
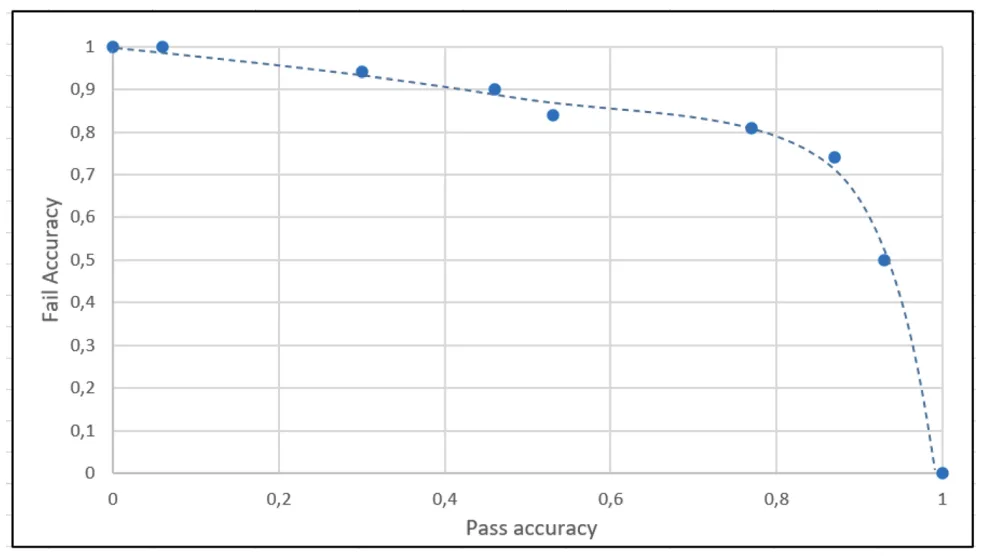
- 図 1. LPDCマシンのダイモールドの断面図
- 図 2. 低圧ダイカストプロセスサイクル
- 図 3. LPDCマシンでの時系列圧力測定
- 図 4. スポークに気孔率欠陥があるダイカストホイールリムのX線スキャン
- 図 5. 変動の大きい増圧サイクルの一例
- 図 6. 部品品質に関するXGBoostモデルの混同行列
- 図 7. 二項決定木推定器の例
- 図 8. 特徴量重要度順序
- 図 9. 合格精度と不合格精度の間のモデルトレードオフ
7. 結論:
主な調査結果の要約:
本研究では、Industry 4.0データ管理と教師あり機械学習のLPDCにおける品質改善への応用を実証することに成功しました。XGBoostモデルは、小規模で不均衡な産業データセットを使用して、妥当な精度で気孔率欠陥を効果的に予測しました。気孔率欠陥の主要な予測因子は、エア冷却チャネル流量の変動と溶融シリコン含有量として特定されました。この研究は、鋳造工場がプロセス最適化と欠陥削減のために生産データを活用するための方法論を提供します。
研究の学術的意義:
本研究は、製造業、特に金属鋳造における機械学習の応用に関する文献の増加に貢献しています。入手可能な産業データと、XGBoostやShapley値などの高度な機械学習手法を使用して、LPDCにおける複雑な品質管理の課題に対処できることを実証しています。この研究はまた、産業環境における効果的な機械学習モデル開発のための特徴量エンジニアリングとデータ前処理の重要性を強調しています。
実際的な意義:
この調査結果は、LPDC鋳造工場にとって大きな実際的な意義があります。開発された方法論は、以下を目的として実装できます。
- 量産前の気孔率欠陥の予測: 新製品の迅速なプロセスパラメータ調整を支援する。
- 重要なプロセスパラメータの特定: 欠陥を減らすための的を絞ったプロセス最適化の取り組みを可能にする。
- 品質管理の改善: 従来の検査方法を予測機能で補完する。
- スクラップ率と生産コストの削減: 欠陥の原因に事前に対処することで。
- データ駆動型の意思決定を可能にする: プロセス調整と品質管理のための定量的な根拠を提供する。
研究の限界と今後の研究分野:
- 小規模なデータセット: モデルは、単一のLPDCマシンとダイモールドからの比較的小規模なデータセットでトレーニングおよび検証されました。モデルの汎化性能とロバスト性を向上させるためには、より大規模で多様なデータセットが必要です。
- 限定的な欠陥タイプ: 研究は気孔率欠陥のみに焦点を当てました。今後の研究では、範囲を拡大して他の種類の鋳造欠陥を含め、多クラス分類モデルを開発することができます。
- 特徴量セット: 36の特徴量が使用されましたが、追加のプロセスパラメータと、より洗練された特徴量エンジニアリング手法を検討することで、モデル性能をさらに向上させることができます。
- 自動データ収集と追跡: 現在のデータ収集は半自動化されています。今後の研究では、シームレスな統合とリアルタイムの品質監視のために、完全に自動化された部品追跡およびデータ取得システムの実装に焦点を当てる必要があります。
- リアルタイム予測と制御: 今後の研究では、開発されたモデルをリアルタイムプロセス制御システムに統合して、事前欠陥防止を検討することができます。
8. 参考文献:
- [参考文献リストは英語の原文と同様]
9. 著作権:
- この資料は、"[論文著者]"の論文:「"[論文タイトル]"」に基づいています。
- 論文ソース: [DOI URL]
この資料は上記の論文に基づいて要約されたものであり、商業目的での無断使用は禁止されています。
Copyright © 2025 CASTMAN. All rights reserved.