本要約は、['Scientia Iranica' に掲載された論文 'Design of Conformal Cooling Channels Using Numerical Methods in a Metal Mold and Calculating Exergy Destruction in Channels' に基づいて作成されました。]
1. 概要:
- タイトル:金属金型におけるコンフォーマル冷却チャネルの数値的設計手法とチャネル内エクセルギー損失の計算 (Design of Conformal Cooling Channels Using Numerical Methods in a Metal Mold and Calculating Exergy Destruction in Channels)
- 著者:Ali BOLATTÜRK, Osman İPEK, Karani KURTULUŞ, Mehmet KAN
- 出版年:2018年8月
- 出版ジャーナル/学術団体:Scientia Iranica
- キーワード:金属金型 (Metal Mold)、エクセルギー損失 (Exergy Destruction)、冷却チャネル設計 (Cooling Channel Design)
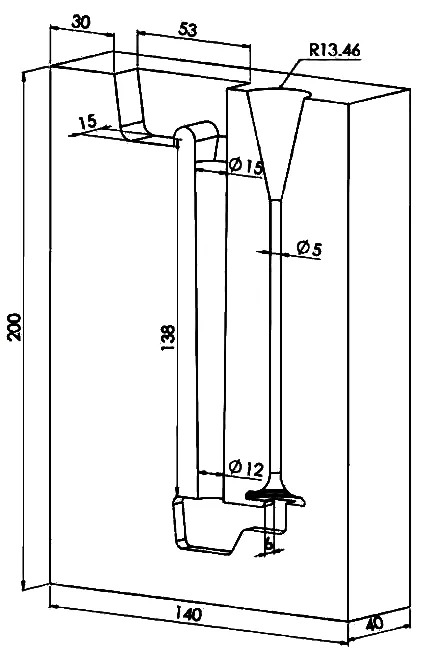
2. 概要または序論
金属金型において、より速い冷却はサイクルタイムの短縮、製品品質の向上、製品ロス低減を可能にします。しかし、従来の製造方法では、金型冷却チャネルは線形方向と限定された形状でのみ製作可能であり、金型冷却性能を制限していました。近年開発された積層造形技術は、複雑な形状とモノブロック3D製品の製造を可能にします。この技術により、様々な形状のコンフォーマル冷却チャネルを備えた金属金型を製作し、優れた冷却性能を確保できます。本研究では、モノブロック永久金型において最適な冷却性能を達成するために、コンフォーマル冷却チャネルを設計しました。本研究では、設計されたコンフォーマル冷却チャネルと従来の冷却チャネル金型について、定常状態条件下でCFD(数値流体力学)解析を実施しました。チャネル内の流速変化に応じた圧力損失、冷却チャネル出口温度、エクセルギー損失を計算しました。数値解析の結果、コンフォーマル冷却チャネルは従来の冷却チャネルよりも約5%高い冷却性能を達成できることが示されました。しかし、コンフォーマル冷却チャネルの圧力損失は従来の冷却チャネルよりも高く観察されました。また、コンフォーマル冷却チャネルのエクセルギー損失は従来の冷却チャネルよりも約12%大きくなりました。
3. 研究背景:
研究テーマの背景:
金属金型における冷却プロセスは、液体金属の凝固における重要な要素の一つであり、鋳造製品の品質に影響を与えます。冷却が均一でない場合、ホットスポット欠陥や歪みなどの成形不良が発生します。逆に、適切かつ迅速な冷却は製品品質にプラスの影響を与えます。従来の製造方法では、金型冷却チャネルは線形方向と円形断面でのみ製作可能です。これは金型冷却性能を制限します [1]。積層造形法で製作されたコンフォーマル冷却チャネルを備えた熱間押出ダイスの冷却性能に関する研究があります [2]。コンフォーマル冷却チャネル金型を使用した場合、標準冷却チャネル金型と比較して生産速度が最大300%向上することが観察されました。成形におけるサイクルタイムは、製品コストと品質に影響を与えます。サイクルタイムが短いほど、温度分布がより均一になり、部品の変形が少ないことが観察されました。したがって、コンフォーマル冷却チャネルを備えた射出成形金型では、より良い製品品質が得られました [3-9]。積層造形法で製作された金属金型の製造コストが高いという事実は、所望の性能を備えたコンフォーマル冷却チャネル設計を製造する必要性を生じさせます。有限要素法を用いて、金型冷却チャネルの冷却性能と液体金属の凝固プロセスをシミュレーションできます。数値研究の結果、コンフォーマル冷却チャネルを通じて凝固時間を短縮することで冷却性能を向上させることができることが示唆されました [10-12]。プラスチック射出成形金型用のコンフォーマル冷却チャネルが設計されました [1]。当該研究は、数値的および実験的に実施されました。
既存研究の現状:
数値および実験的研究の結果、コンフォーマル冷却チャネルを使用した場合、サイクルタイムが12.8%短縮されることが明らかになりました。また、Park and Dang [9] は、プラスチック射出成形金型用のコンフォーマル冷却チャネルを開発しました。研究結果は、コンフォーマル冷却チャネルを使用した場合、サイクルタイムが30%短縮されることを示しました。
摩擦損失、温度差による熱伝達、急激な膨張と圧縮は、システムにおけるエクセルギー損失を引き起こします [13-15]。溶融金属の熱は冷却チャネルを介して伝達されます。溶融金属と冷却チャネル間の熱伝達は、熱交換器の作動原理と類似しています。熱交換器におけるエクセルギー損失に関する多くの研究が文献に存在します。しかし、金属金型冷却チャネルにおけるエクセルギー損失に関する研究は、文献において非常に少ないです。熱交換器または熱力学的サイクルの最適作動条件を決定し、エクセルギー損失を低減するために、流体速度、圧力損失、温度分布などのパラメータが研究者によって調査されました。彼らは、エクセルギー損失はこれらのパラメータを改善することによって減少することを強調しました [16-19]。
近年開発された積層造形技術により、複雑な形状とコンパクトな構造で製品を製造できます。本研究では、従来の製造方法では製造できない様々な形状の金属金型内の冷却チャネルを設計しました。2種類の異なるコンフォーマル冷却チャネル金型を設計し、定常状態条件下で標準冷却チャネル金型と数値的に比較しました。各チャネルについて、様々な流量における熱伝達率、エクセルギー損失、圧力損失を計算しました。
研究の必要性:
積層造形法で製造された金属金型の高い製造コストのため、所望の性能を備えたコンフォーマル冷却チャネル設計を製造する必要性があります。コンフォーマル冷却チャネルは冷却性能を向上させることができますが、圧力損失およびエクセルギー損失の観点から従来の冷却チャネルとの比較分析が必要です。最適な冷却チャネル設計のためには、熱伝達性能だけでなく、エネルギー効率を考慮したエクセルギー分析が不可欠です。
4. 研究目的と研究課題:
研究目的:
本研究の主な目的は、金属金型において最適な冷却性能を達成するためにコンフォーマル冷却チャネルを設計し、数値的に解析して従来の冷却チャネル設計と比較することです。本研究は、熱伝達、圧力損失、エクセルギー損失の観点から性能差を評価することを目的としています。
主要な研究課題:
- 永久金型用コンフォーマル冷却チャネルの設計はどのように行われるか?
- コンフォーマル冷却チャネル(曲線チャネル(CC)および球状フィンチャネル(SFC))と標準チャネル(SC)の金属金型内冷却性能をCFDを用いて数値的に比較するとどのような結果が得られるか?
- 様々な冷却チャネル設計について、流量変化に伴う圧力損失、冷却チャネル出口温度、エクセルギー損失を計算し比較するとどのような結果が得られるか?
研究仮説:
- コンフォーマル冷却チャネルは、従来の冷却チャネルよりも高い冷却性能を示すであろう。
- コンフォーマル冷却チャネルの圧力損失およびエクセルギー損失は、従来の冷却チャネルよりも高くなる可能性がある。
- 最適化されたコンフォーマル冷却チャネル設計は、圧力損失およびエクセルギー損失の増加の可能性にもかかわらず、冷却効率を向上させることができる。
5. 研究方法:
研究デザイン:
本研究では、数値シミュレーションベースの研究デザインを採用しています。標準チャネル(SC)、曲線チャネル(CC)、球状フィンチャネル(SFC)の3種類の冷却チャネル構成を設計しました。CFD解析を定常状態条件下で実施し、これらの設計の熱的および流体力学的性能を比較しました。
データ収集方法:
データは、ANSYS-FLUENT 16.1ソフトウェア [24] を用いたCFDシミュレーションを通じて収集されました。シミュレーションでは、様々な冷却油速度における各チャネル設計の圧力損失、冷却チャネル出口温度、熱伝達率を計算しました。材料特性および境界条件は、文献および実験データに基づいて定義されました。
分析方法:
収集された数値データを分析し、様々な冷却チャネル設計の性能を比較しました。エクセルギー損失は、Engineering Equation Solver(EES)ソフトウェア [25] を用いて計算されました。分析は、各チャネルタイプにおける流量の関数としての熱伝達率、圧力損失、出口温度、エクセルギー損失を評価することに焦点を当てました。数値モデルの検証は、Imran et al. [23] の既存の実験データと結果を比較することにより実施されました。
研究対象と範囲:
研究対象は重力ダイカスト用永久金型であり、特にガソリン内燃機関の排気バルブ用にモデル化されています(Fig. 1)。研究範囲は、この金型形状内における3種類の異なる冷却チャネル設計(SC、CC、SFC)の数値解析に限定され、「Petro-therm」ブランドの熱媒体油を冷媒として使用し、GGG 50ダクタイル鋳鉄(SC用)およびステンレス鋼316 L(CCおよびSFC用)を金型材料として使用しています。
6. 主な研究成果:
主要な研究成果:
- 冷却性能: SFCは基準速度1 m/sでSCよりも約5%高い熱伝達率を示しました。SFCはCCおよびSCよりも多くの熱を伝達します(Figure 7a)。
- 圧力損失: SFCの圧力損失(約50 kPaまで)は、速度が増加するにつれてSC(1-4 kPa)よりも大幅に高くなりました。
- エクセルギー損失: SFCのエクセルギー損失はSCよりも約12%大きくなりました。SCおよびCCの場合、エクセルギー損失は速度が増加するにつれて最初は増加し、その後減少しましたが、SFCは約0.37 kW付近で変動するエクセルギー損失を示しました(Figure 7b)。
- 出口温度: 速度が増加するにつれて、すべてのチャネルの出口温度が低下しました。入口と出口の間の温度差は、すべてのチャネルで小さかったです(4K)。
提示されたデータの分析:
数値結果は、コンフォーマル冷却チャネル、特にSFCが標準チャネルと比較して熱伝達を向上させることを示しています。しかし、この性能向上には、圧力損失とエクセルギー損失の増加というトレードオフが伴います。SFC設計は、最も高い熱伝達率を提供しますが、最も高い圧力損失とエクセルギー損失も示します。SFCで変動するエクセルギー損失は、球状フィン構造内の複雑な流れのダイナミクスを示唆しています。すべてのチャネルで入口と出口の間の温度差が小さいことは、効率的な熱除去を示していますが、エクセルギー損失を最小限に抑えるためのチャネル設計の最適化の必要性も強調しています。
図のリスト:
- Figure 1. 金属金型対称部品のソリッドモデル
- Figure 2. 金型冷却チャネル熱伝達メカニズムの仮定
- Figure 3. 解析された冷却チャネルの計算領域
- Figure 4. 解析された金型構成に使用された境界条件
- Figure 5. Imran et al. [23] および現在の研究結果の基準温度の比較
- Figure 6. Imran et al. [23] および現在の研究結果の圧力損失の比較
- Figure 7 a. 流量に応じたSC、CC、SFCの熱伝達率と圧力損失の比較、b. 流量に応じたSC、CC、SFCのチャネル出口温度とエクセルギー損失の比較
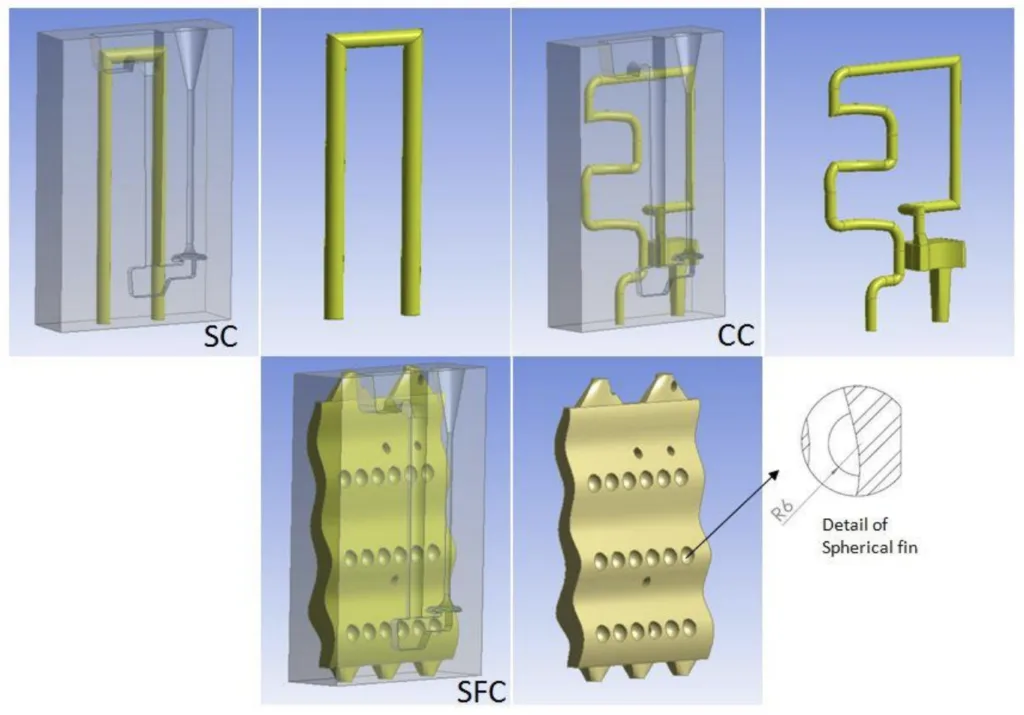
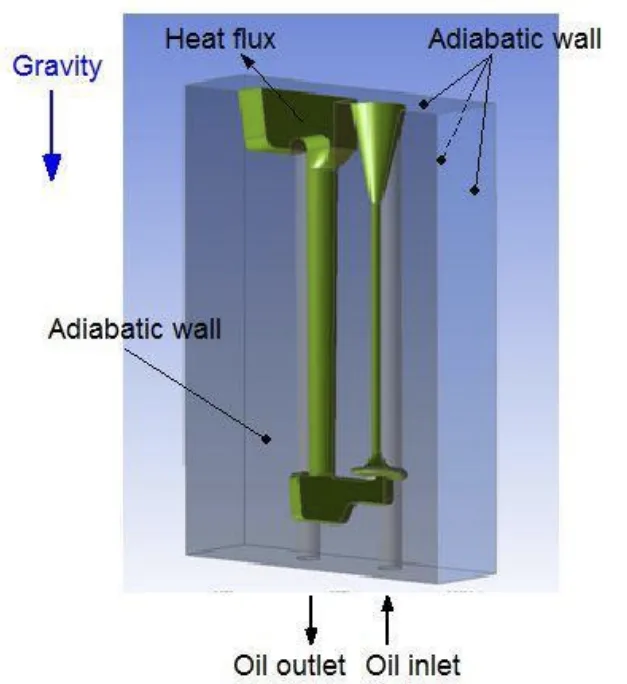
![Figure 5. Comparison of Imran et al. [23] and current study results for base temperature](https://castman.co.kr/wp-content/uploads/image-950-1024x707.webp)
![Figure 6. Comparison of Imran et al. [23] and current study results for pressure drop](https://castman.co.kr/wp-content/uploads/image-951-1024x699.webp)
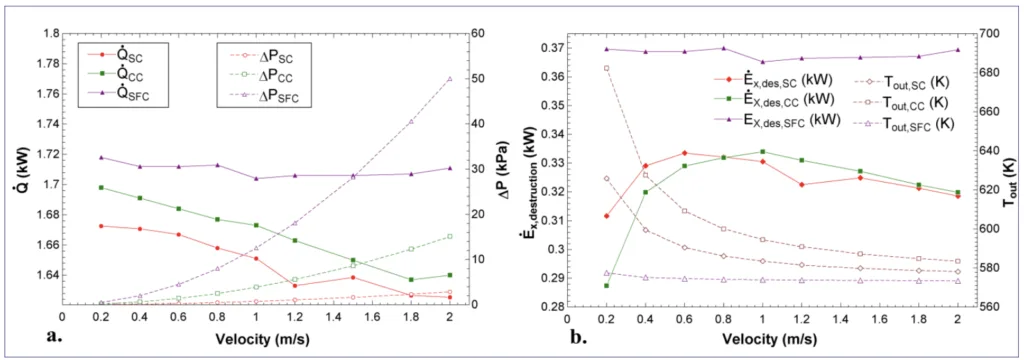
7. 結論:
主な研究結果の要約:
本研究では、金属金型用の標準(SC)、曲線(CC)、球状フィン(SFC)コンフォーマル冷却チャネルを数値的に比較しました。SFCは基準速度1 m/sでSCよりも5%高い熱伝達率を示しましたが、圧力損失も大幅に高く、エクセルギー損失は12%大きくなりました。熱伝達率はサイクルタイムが減少するにつれて増加します。1m/sの速度では、SCとSFCはそれぞれ0.157 Wと11.7 Wのポンプ動力を必要としました。SFCは40W多くの熱伝達率を達成しましたが、圧力損失はSFCで最も高くなりました。流量が減少するにつれて、出口と入口の間の温度差はSFCと比較してSCおよびCCで高くなりました。SFCのエクセルギー損失は変動的であり、SCよりも一貫して高くなりました。
研究の学術的意義:
本研究は、コンフォーマル冷却チャネル設計の詳細な数値解析を提供し、従来の設計と比較してその熱的および流体力学的性能に関する理解を深めます。本研究は、コンフォーマル冷却における強化された熱伝達と増加した圧力損失およびエクセルギー損失の間のトレードオフを強調し、金属金型における冷却チャネル設計を最適化するための貴重な洞察を提供します。
実用的な意味合い:
研究結果は、コンフォーマル冷却チャネル、特にSFCが冷却性能を向上させ、サイクルタイムを短縮する可能性がある一方で、設計者は増加した圧力損失とエクセルギー損失を考慮する必要があることを示唆しています。冷却チャネル設計の選択は、所望の熱伝達率、許容可能な圧力損失、エネルギー効率のバランスに基づいて行う必要があります。熱伝達を最大化することが重要なアプリケーションの場合、SFCはエネルギー消費量が多くても適している可能性があります。エネルギー効率を優先するアプリケーションの場合、SCまたはCC設計の方がより適切である可能性があります。
研究の限界と今後の研究分野:
本研究は数値シミュレーションに限定されており、調査された特定の金型形状およびチャネル設計に関する実験的検証を含んでいません。今後の研究では、これらの数値的結果の実験的検証に焦点を当てる必要があります。高い熱伝達率を維持しながら、コンフォーマル冷却チャネル設計におけるエクセルギー損失を最小限に抑えるための追加の最適化研究が必要です。金型性能および鋳造品質に対する様々なコンフォーマル冷却チャネル形状および流動パラメータの影響を調査することも有益でしょう。
8. 参考文献:
- [1] Hsu, F.H. Wang, K. Huang, C.T. Chang, R.Y. “Investigation on conformal cooling system design in injection molding”, Advances in Production Engineering & Management., 8(2), pp.107-115 (2013).
- [2] Hölker, R. Haase, M. Khalifa, N.B. Takkaya, A. E. “Hot extrusion dies with conformal cooling channels produced by additive manufacturing”, Aluminum Two Thousand World Congress and International Conference on Extrusion and Benchmark ICEB, pp. 4838-4846 (2015).
- [3] Sachs, E. Wylonis, E. Allen, S. Cima, M. Guo, H. “Production of Injection Moulding Tooling With Conformal Cooling Channels Using the Three Dimensional Printing Process”, Polymer Engineering and Science., 40(5), (2000).
- [4] Eimsa-ard, K. and Wannisorn, K. “Conformal bubbler cooling for molds by metal deposition process”, Computer-Aided Design., 69, pp. 126-133 (2015).
- [5] Wang, Y. Yu, K. M. Wang, C. C. L. “Spiral and conformal cooling in plastic injection molding", Computer-Aided Design., 63, pp. 1-11 (2015).
- [6] Vojnová, E. "The benefits of a conforming cooling systems the molds in injection moulding process", Procedia Engineering., 149, pp. 535-543 (2016).
- [7] Venkatesh, G. Y. Ravi, K. Raghavendra, G. "Comparison of Straight Line to Conformal Cooling Channel in Injection Molding", Materials Today: Proceedings., 4(2), pp. 1167-1173 (2017).
- [8] Jahan, A.S. and Mounayri, H. "Optimal Conformal Cooling Channels in 3D Printed Dies for Plastic Injection Molding", Procedia Manufacturing., 5, pp. 888-900 (2016).
- [9] Park, H. Dang, X.P. "Development of a smart plastic injection mold with conformal cooling channels", Procedia Manufacturing., 10, pp. 48-59 (2017).
- [10] Wang, G. Zhao, G. Li, H. Guan, Y. “Multi-objective optimization design of the heating/cooling channels of the steam-heating rapid thermal response mold using particle swarm optimization”, Int. J. of Thermal Science., 50, pp. 790-802 (2011).
- [11] Franke, M. M. Hilbinger, R. M. Lohmüller, A. Singer, R. F. “The effect of liquid metal cooling on thermal gradients in directional solidification of super alloys: Thermal analysis”, Journal of Material Processing Technology., 213, pp. 2081-2088 (2013).
- [12] Furumoto, T. Ueda, T. Amino, T. Ksunoki, D. Hosokowa, A. Tanaka, T. “Finishing performance of cooling channel with face protuberance inside the molding die", Journal of Material Processing Technology., 212, pp. 2154-2160 (2012). DOI: 10.1016/j.jmatprotec.2012.05.016
- [13] Khairul, M. A. Alim, M. A. Mahbubul, I. M. Saidur, R. Hepbasli, A. Hossain, A. “Heat transfer performance and exergy analyses of a corrugated plate heat exchanger using metal oxide nanofluids", International Communications in Heat and Mass Transfer., 50, pp. 8–14 (2014).
- [14] Dizaji, H. S. Jafarmadar, S. Asaadi, S. “Experimental exergy analysis for shell and tube heat exchanger made of corrugated shell and corrugated tube”, Experimental Thermal and Fluid Science., 81, pp. 475-481 (2017).
- [15] Ipek, O. Kan, M. Gurel, B. “Examination of Different Heat Exchangers and the Thermal Activities of Different Designs”, Acta Physica Polonica A., 132(3), pp. 580-583 (2017).
- [16] Kan, M. Ipek, O. Gurel, B. "Plate Heat Exchangers as a Compact Design and Optimization of Different Channel Angles”, Acta Physica Polonica A., 128(2B), B-49 (2015).
- [17] Karaail, R. Öztürk, I. T. “Thermoeconomic Analyses of Steam Injected Gas Turbine Cogeneration Cycles", Acta Physica Polonica A., I, 128(2B), B-279 (2015).
- [18] Zehtabiyan, R. N. Damirci, D. S. Fazel, Z.M.H. Saffar, A. M. "Generalized heat transfer and entropy generation of stratified air-water flow in entrance of a mini-channel", Scientia Iranica B., 24(5), pp. 2406-2417 (2017).
- [19] Nouri, B. A. and Seyyed, H. M. H. "Numerical analysis of thermally developing turbulent flow in partially filled porous pipes", Scientia Iranica В., 22(3), pp. 835-843 (2015).
- [20]Altinsoy, İ. Çelebi Efe, G.F. Yener, T. Önder, K. G. Bindal, C. “Effect of Double Stage Nitriding on 34CrAlNi7-10 Nitriding Steel”, Acta Physica Polonica A., 132, pp. 663-666 (2017).
- [21] Arunkumar, S. Rao, K. S. Kumar, T. P. "Spatial variation of heat flux at the metal-mold interface due to mold filling effects in gravity die-casting", Int. J. of Heat and Mass Transfer., 51(11), pp. 2676-2685 (2008).
- [22] Hallam, C. P. and Griffiths, W. D. “A model of the interfacial heat-transfer coefficient for the aluminum gravity die-casting process”, Metallurgical and materials transactions B., 35(4), pp. 721-733 (2004).
- [23] Imran, A. A. Nabeel, S. M. Hayder, M. J. "Numerical and experimental investigation of heat transfer in liquid cooling serpentine mini-channel heat sink with different new configuration models" Thermal Science and Engineering Progress., 6, pp. 128-139 (2018).
- [24] Fluent, Version 16.1 User's Guide, Fluent Inc., Lebanon (NH) (2016).
- [25] Klein, S. A. “Engineering Equation Solver (EES)”, Academic Commercial V8.208.F-Chart Software, www.fChart.com (2008).
9. 著作権:
- 本資料は、"Ali BOLATTÜRK, Osman İPEK, Karani KURTULUŞ, Mehmet KAN" の論文 "Design of Conformal Cooling Channels Using Numerical Methods in a Metal Mold and Calculating Exergy Destruction in Channels" に基づいて要約されています。
- 論文ソース:https://doi.org/10.24200/sci.2018.50090.1502
本資料は上記の論文を要約したものであり、商業目的での無断使用は禁止されています。
Copyright © 2025 CASTMAN. All rights reserved.