本論文概要は、['Hong-Kyu Kwon']氏が['MDPI']から発表した論文、['Layout Design and Die Casting Using CAE Simulation for Household Appliances']に基づいて作成されました。
1. 概要:
- タイトル:家庭用機器のためのCAEシミュレーションを用いたレイアウト設計とダイカスト (Layout Design and Die Casting Using CAE Simulation for Household Appliances)
- 著者:洪 奎權 (Hong-Kyu Kwon)
- 発表年:2021年
- 発表ジャーナル/学会:Applied Sciences (MDPI)
- キーワード:ゲートシステム (gate system); 高圧ダイカスト (high pressure die casting); CAEシミュレーション (CAE simulation); 流動解析 (flow analysis); クッキンググリル (cooking grill)
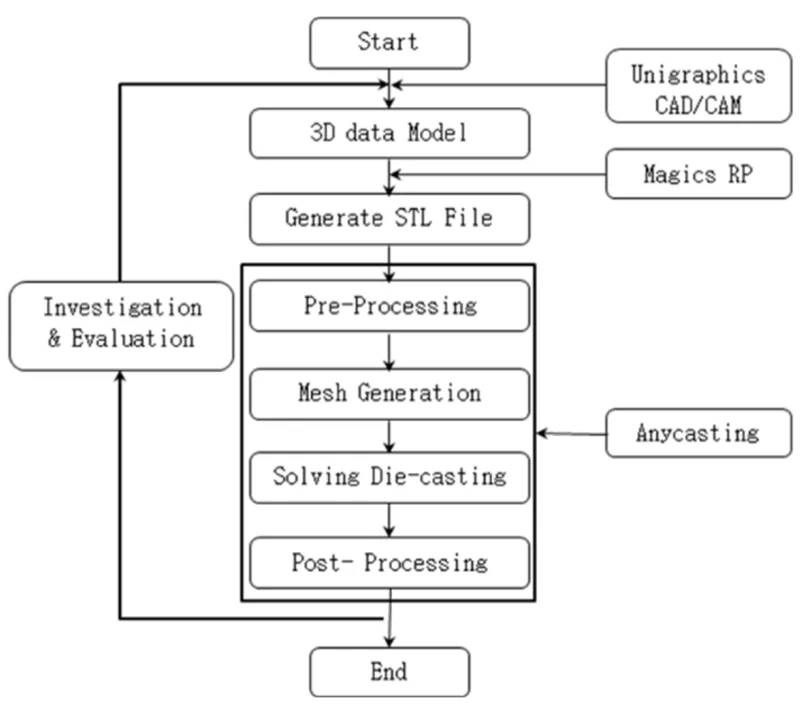
2. 概要または序論
本研究は、家庭用機器、特にクッキンググリルの高圧ダイカスト(HPDC)におけるコンピュータ支援エンジニアリング(CAE)技術の応用について調査しています。本研究は、様々な産業分野におけるアルミニウム合金部品の需要増加と、生産コスト削減および製品品質向上のための効率的な鋳造レイアウト設計の必要性に対処しています。鋳造業界において金型設計者の経験と知識に大きく依存している従来の鋳造レイアウト設計は、急速な技術進歩と経済的圧力に対応するにはますます不十分になっています。CAE技術は、鋳造欠陥を予測し、金型設計段階で充填および凝固解析を実行することにより、金型開発および製作プロセスにおける試行錯誤を最小限に抑え、最適な金型設計手法を可能にするソリューションとして提示されています。本研究は、製品品質を保証し、生産コストを削減するために、CAEシミュレーションを使用して家庭用機器金型の健全な鋳造レイアウトを確立することを目的としています。
3. 研究背景:
研究テーマの背景:
科学技術の発展と工業化により、アルミニウム合金の活用が増加しました。資源保全、省エネルギー、および環境問題への関心の高まりから、鋳造業界、特に高圧ダイカスト(HPDC)において、アルミニウム製品が鋳鉄部品を代替する傾向が強まっています。HPDCは、複雑な部品を一度に大量生産できる経済的な大量生産技術であり、高品質、低コスト、および短納期を要求する消費財、自動車、および電子機器産業において重要な製造技術として認識されています。しかし、HPDCは、溶融金属の高温、金型表面の高圧、製品形状の複雑さと精密さのために、より高度な金型製作技術を必要とします。
既存研究の現状:
既存の研究では、HPDCにおける鋳造レイアウト設計およびゲートシステムの重要な役割が認識されており、これは伝統的に金型設計者の経験に依存してきました。CAE技術の適用は、経験に基づく設計の限界を克服するために急速に拡大しています。先行研究では、薄肉ハウジング[10]の凝固シミュレーション、燃料電池バイポーラプレート[11]の充填および凝固解析、自動車ギアハウジング[13]の最適化、薄肉部品[14]のLPDCパラメータ最適化など、様々な鋳造プロセス解析におけるCAEの有効性が実証されています。さらに、コンピュータ支援パラメトリック設計を用いた半自動ゲートシステム設計[15]に関する研究も行われています。これらの研究は、鋳造プロセス設計および欠陥予測を向上させるためにCAEシミュレーションを活用する傾向を強調しています。
研究の必要性:
従来の試行錯誤による鋳造レイアウト設計および金型製作は、時間とコストがかかります。CAE技術の進歩は、このような経験的手法への依存度を減らすための重要な機会を提供します。鋳造中の充填および凝固プロセスを迅速かつ正確に予測し、堅牢で費用対効果の高い生産方法を確立できる方法論が必要です。特にクッキンググリルのような家庭用機器の場合、CAEシミュレーションを通じて鋳造レイアウトを最適化することで、金型開発および製作に関連する生産コストと時間を削減しながら、エアポロシティや引け巣などの欠陥を最小限に抑えて製品品質を保証できます。
4. 研究目的と研究課題:
研究目的:
本研究の主な目的は、家庭用機器(クッキンググリル)のダイカストにおける充填および凝固プロセスを予測するためにCAEシミュレーション技術を活用することです。これは、生産コストを最小限に抑え、製品品質を保証する健全な鋳造方法を確立することを目的としています。本研究は、金型充填および凝固プロセスを分析して、欠陥制御方法を開発し、ダイカスト金型設計および製作プロセスに対する最適な鋳造方法を決定しようとしています。
主要な研究課題:
主要な研究課題は、ADC12合金で作られたクッキンググリルに対する3つの異なる鋳造レイアウトを分析するためにCAEシミュレーションソフトウェア(AnyCasting)を適用することに焦点を当てています。本研究では、内部エアポロシティおよび引け巣欠陥を最小限に抑え、鋳造品質と安定性を保証するために、ゲートシステム設計が溶融金属の流れおよび凝固パターンに及ぼす影響を調査します。
研究仮説:
本研究では、CAEシミュレーションを使用し、ゲートシステム設計を体系的に修正することによって、特に多点インゲートシステム(Case 1)からリングゲートシステム(Case 2および3)に移行し、ビスケット設計をさらに改良(Case 3)することによって、よりバランスの取れた溶融金属の流れを達成し、エアポロシティの隔離を減らし、逆流および渦流現象を最小限に抑え、凝固を最適化してダイカストクッキンググリルの引け巣欠陥を減らすことができると仮定します。本研究では、改良されたゲートおよびビスケット設計を備えたCase 3が、Case 1およびCase 2と比較して優れた鋳造性能を示すと予想しており、これは最適な鋳造レイアウトにつながります。
5. 研究方法:
研究デザイン:
本研究では、家庭用機器(クッキンググリル)に対する3つの異なる鋳造レイアウトの性能を分析および比較するために、CAEソフトウェア(AnyCasting)を使用するシミュレーションベースの実験デザインを採用しています。本研究は、材料特性、プロセスパラメータ、および金型設計のバリエーションによって定義された制御条件下での溶融金属の流れおよび凝固プロセスの数値解析に焦点を当てています。
データ収集方法:
データは、AnyCastingソフトウェアを使用して実行されたCAEシミュレーションを通じて収集されます。シミュレーションプロセスには、3D CADモデルの前処理、メッシュ生成、ダイカストプロセス方程式の求解、および結果の視覚化と分析のための後処理が含まれます。ソフトウェアは、PM(多孔質媒体)法とCut-Cell法を組み合わせたハイブリッド数値解析法を使用します。シミュレーション出力には、さまざまな充填段階での溶融金属の流れパターンの視覚的表現と凝固の進行状況、およびエアポロシティと引け巣欠陥の予測位置が含まれます。
分析方法:
分析方法は、3つの鋳造レイアウトに対するシミュレーション結果の比較評価を含みます。流動解析の結果は、溶融金属の流れの均一性、未充填またはコールドシャットの存在、エアポロシティの隔離、および逆流現象に基づいて評価されます。凝固解析の結果は、予測された引け巣欠陥の位置と範囲に基づいて評価されます。シミュレーション出力の定性的および視覚的分析、特に図3〜11を使用して、各鋳造レイアウトの性能を比較し、最適な設計を特定します。
研究対象と範囲:
研究対象は、ADC12アルミニウム合金で作られた家庭用クッキンググリルのダイカストプロセスです。研究の範囲は、AnyCastingソフトウェアを使用した3つの特定の鋳造レイアウト設計(Case 1、Case 2、およびCase 3)の数値シミュレーション解析に限定されます。材料特性、プロセスパラメータ(射出速度、温度)、および金型材料(SKD61)は、一般的なHPDC条件に基づいて定義されます。分析は、充填および凝固段階に焦点を当て、欠陥の最小化と品質向上を目的としてゲートシステムと全体的な鋳造レイアウトを最適化することを目指しています。
6. 主な研究結果:
主要な研究結果:
- 流動解析:
- Case 1(8点インゲート):不均衡な流れと潜在的なエアポロシティの隔離(図4)。
- Case 2(リングゲート):Case 1と比較して流れのバランスが改善されたが、ビスケット(スプルー)に渦の形成と逆流現象が見られた(図6)。
- Case 3(丸型ビスケットフィーチャで修正されたリングゲート):最も均一な溶融金属の流れを示し、逆流と渦流現象を最小限に抑え、エアポロシティを減少させた(図8、図11)。
- 凝固解析:
- Case 3の凝固解析の結果、厚肉部に潜在的な引け巣欠陥が示された(図9、図10)。
- AnyCastingのモジュール式手法を使用して、引け巣欠陥領域を特定した。
- 研究では、引け巣を軽減するために金型温度の制御と詳細な冷却設計の実装を提案している。
提示されたデータの分析:
- 図3: 3つのケース(Case 1、2、3)すべての溶融金属充填プロセスを、さまざまな割合(25%、45%、60%、80%、93%、96%)で示しています。Case 2と3は、Case 1と比較してより均一な充填を示しています。
- 図4: Case 1の93%および96%充填段階における不均衡な流れと予想される隔離されたエアポロシティ領域を強調しています。
- 図5: Case 1とCase 2の96%充填挙動を比較し、ゲートシステム再設計によりCase 2で流れのバランスが改善され、隔離された領域が減少したことを示しています。
- 図6: Case 2の45%および60%充填段階におけるビスケットの渦形成を示しており、潜在的な逆流の問題を示唆しています。
- 図7: Case 2とCase 3の間のゲートシステム設計の違いを示しており、逆流を最小限に抑えるためにCase 3のビスケットに追加された丸型フィーチャを強調しています。
- 図8: Case 3の45%および60%充填段階における改善された溶融金属の流れを示しており、設計変更により渦と逆流が最小限に抑えられたことを実証しています。
- 図9: Case 3のさまざまな凝固割合(5%、15%、30%、40%、50%、65%)に対する凝固シミュレーション結果を示しており、凝固隔離領域を示しています。
- 図10: AnyCastingのモジュール式手法を使用して、Case 3の65%凝固で予想される引け巣欠陥領域を詳細に示しています。
- 図11: Case 3の最終鋳造レイアウトシミュレーション結果(固定側と可動側)をさまざまな充填割合(30%、45%、75%、85%、95%)で表示し、最小限に抑えられた渦流と潜在的なミクロポロシティを示しています。
図のリスト:
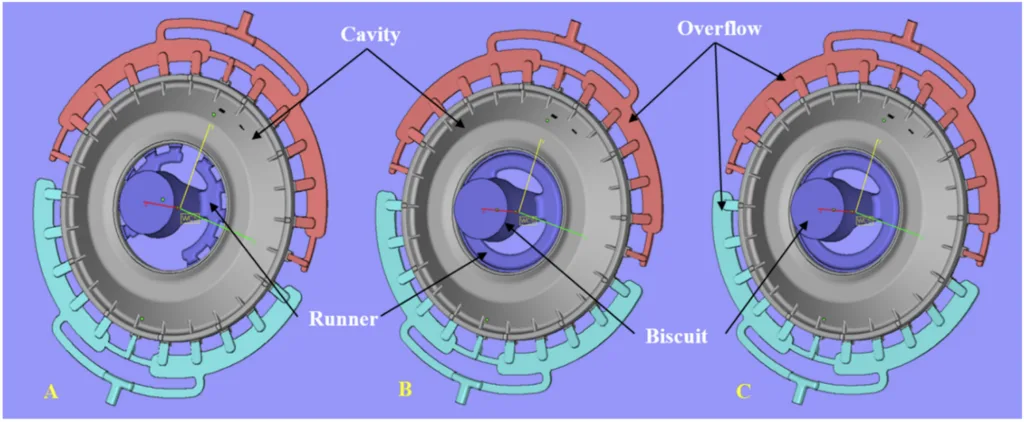
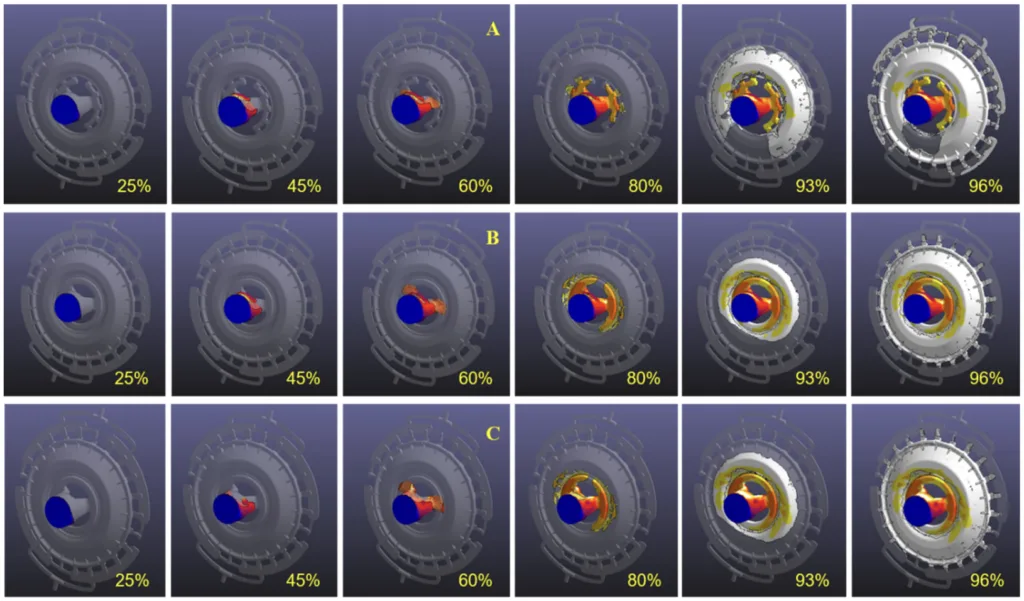
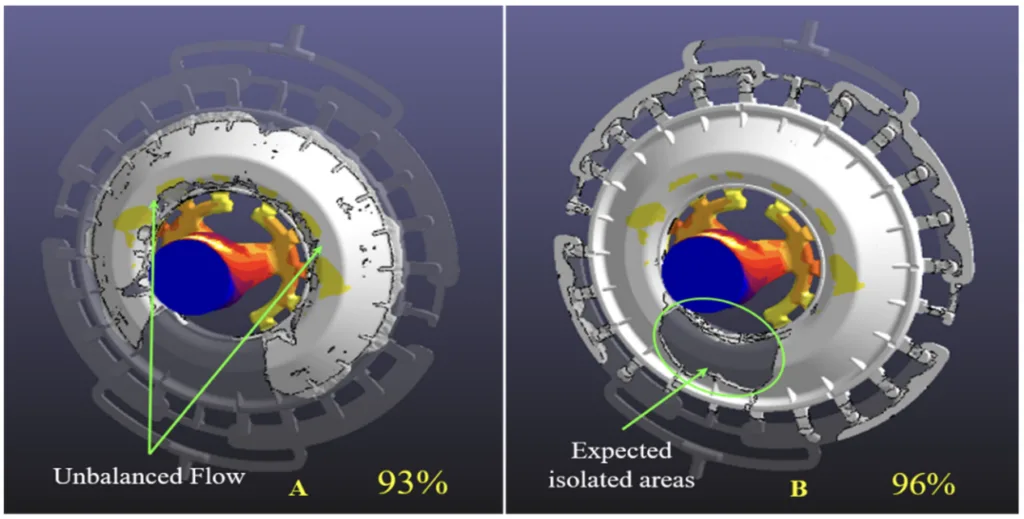
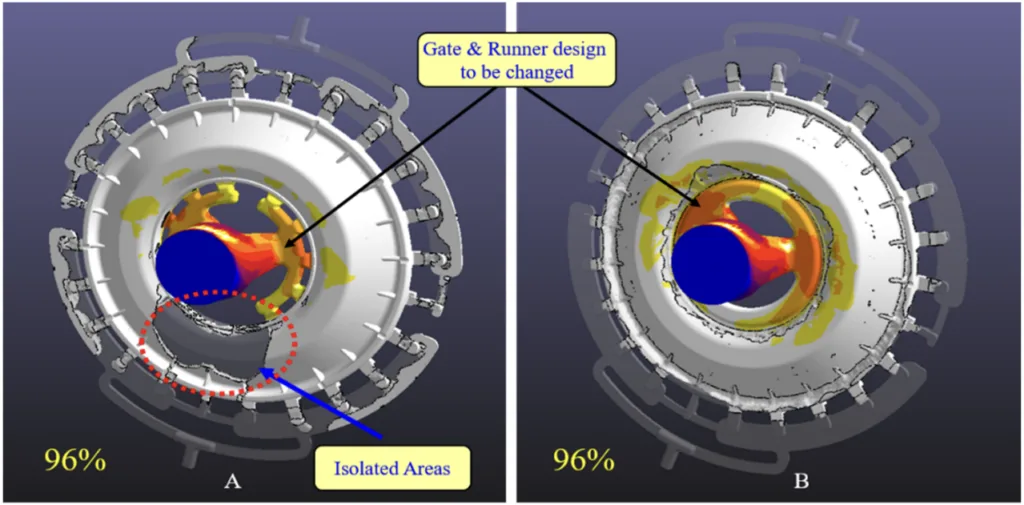
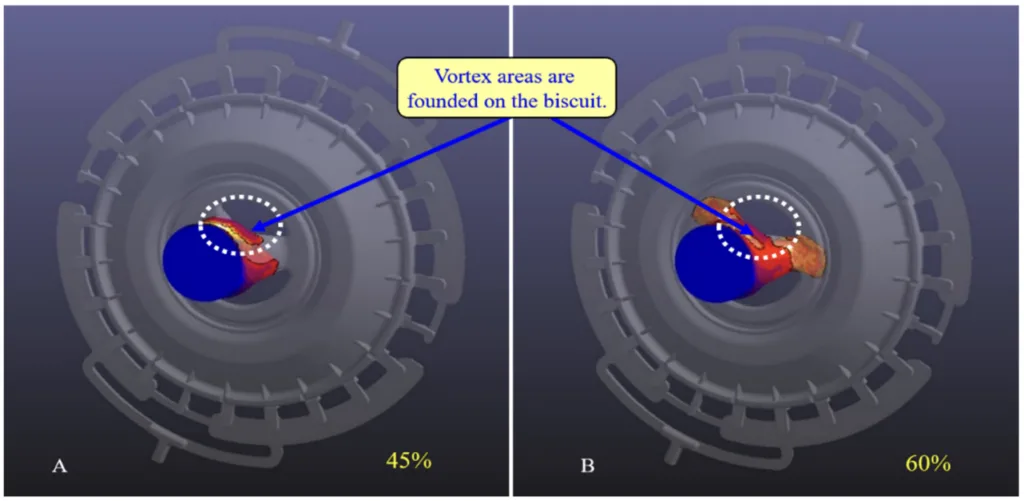
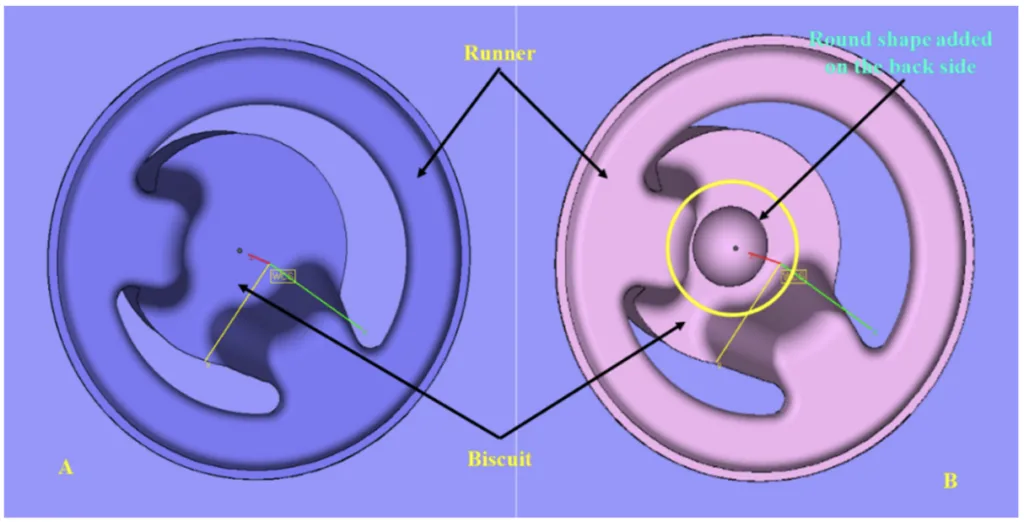
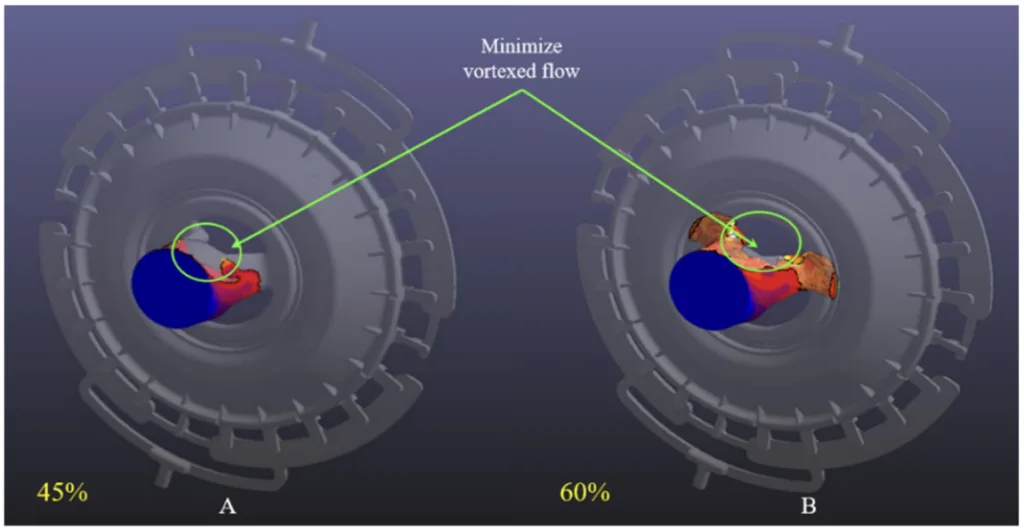
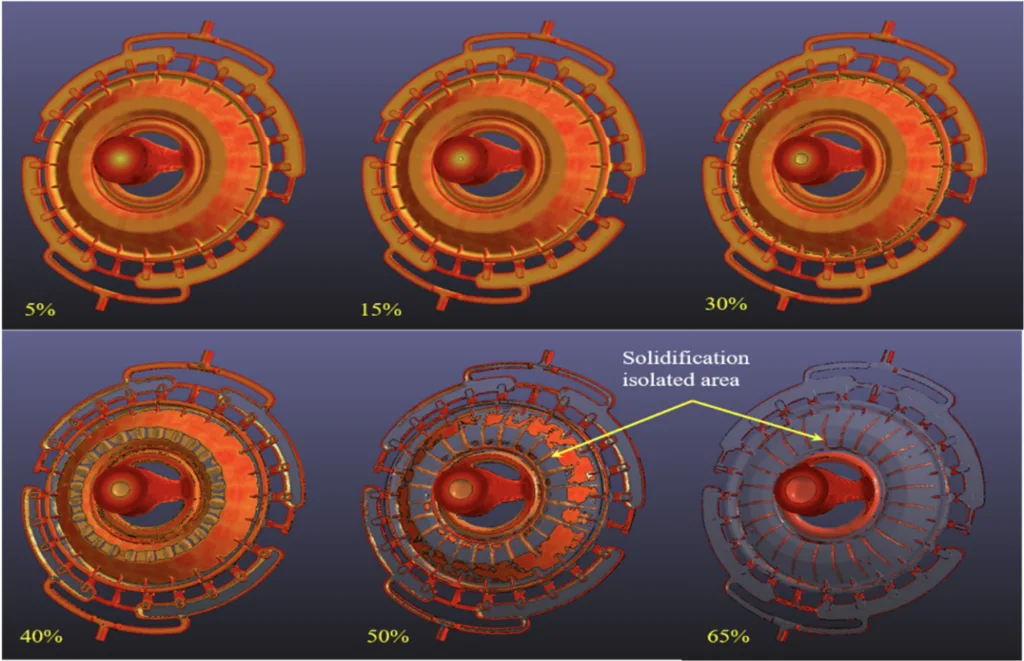
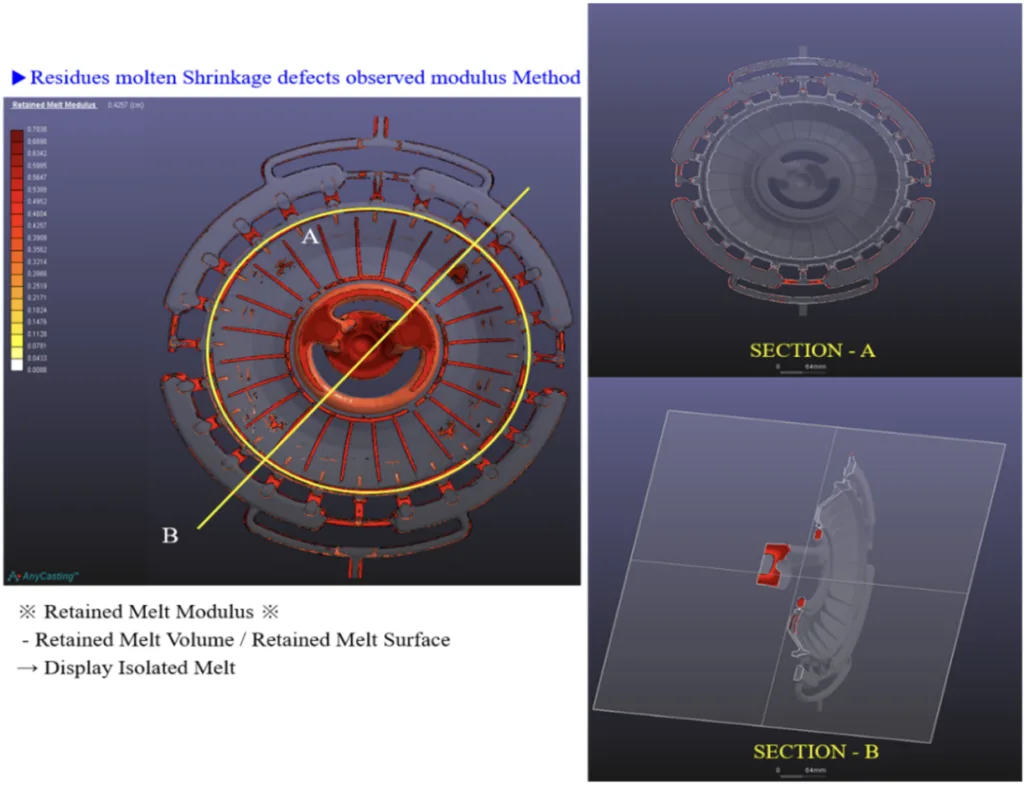
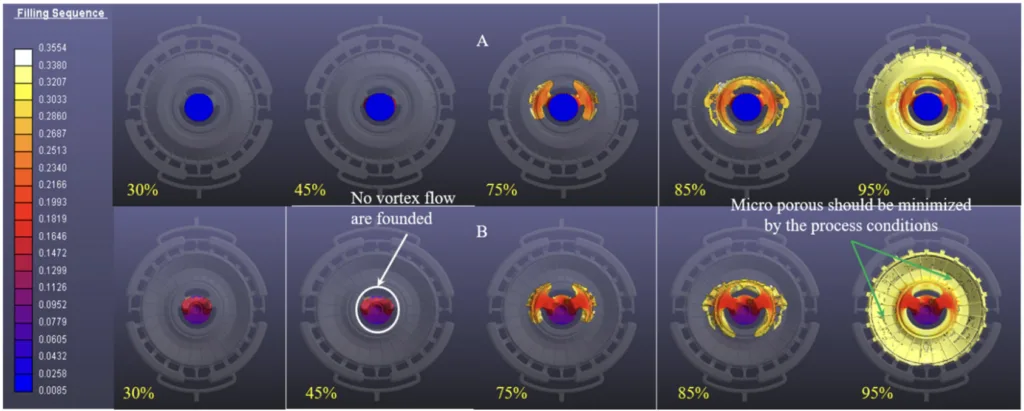
- 図 1. CAEシミュレーションのフローチャート (Figure 1. Flow Chart of CAE simulation.)
- 図 2. クッキンググリルの鋳造モデル:(A)Case 1、(B)Case 2、(C)Case 3 (Figure 2. Casting model of cooking grill: (A) Case 1; (B) Case 2; (C) Case 3.)
- 図 3. 溶融金属充填プロセスのシミュレーション結果:(A)Case 1、(B)Case 2、(C)Case 3 (Figure 3. Simulation results of the melt filling process: (A) Case 1; (B) Case 2; (C) Case 3.)
- 図 4. Case 1の溶融金属流動シミュレーション結果:(A)93%充填、(B)96%充填 (Figure 4. Simulation results of the melt flow for Case 1: (A) 93% filling; (B) 96% filling.)
- 図 5. 溶融金属流動シミュレーション結果:(A)Case 1の96%充填、(B)Case 2の96%充填 (Figure 5. Simulation results of the melt flow: (A) 96% filling of case 1; (B) 96% filling of case 2.)
- 図 6. Case 2の溶融金属流動シミュレーション結果:(A)45%充填、(B)60%充填 (Figure 6. Simulation results of the melt flow for case 2: (A) 45% filling; (B) 60% filling.)
- 図 7. ゲートシステム:(A)Case 2、(B)Case 3 (Figure 7. Gate system: (A) case 2; (B) case 3.)
- 図 8. Case 3の溶融金属流動シミュレーション結果:(A)45%充填、(B)60%充填 (Figure 8. Simulation results of the melt flow for Case 3: (A) 45% filling; (B) 60% filling.)
- 図 9. Case 3の凝固シミュレーション結果 (Figure 9. Simulation results of the solidification for case 3.)
- 図 10. Case 3の65%凝固で予想される引け巣欠陥領域 (Figure 10. Expected shrinkage defect area for Case 3 at 65% solidification.)
- 図 11. 最終鋳造レイアウトのシミュレーション結果:(A)固定側、(B)可動側 (Figure 11. Simulation results with the final casting layout: (A) Fixed side; (B) Moving side.)
7. 結論:
主な研究結果の要約:
本研究は、CAEシミュレーションがHPDCプロセスの鋳造レイアウトの最適化に効果的であると結論付けています。流動解析は、ゲートシステムの反復的な設計変更を通じて、不均衡な流れ、エアポロシティ、および逆流の問題を特定し、解決しました。リングゲートと修正されたビスケット設計を特徴とするCase 3は、Case 1およびCase 2と比較して、最も均一な溶融金属の流れを示し、逆流とエアポロシティを最小限に抑えました。Case 3の凝固解析では、厚肉部に潜在的な引け巣欠陥が明らかになり、最適化された冷却戦略の必要性が強調されました。
研究の学術的意義:
本研究は、ダイカストレイアウト設計におけるCAEシミュレーションの実用的な応用を示し、潜在的な鋳造欠陥を予測および軽減する能力を検証します。数値解析を使用して複雑な形状に対するゲートシステムを最適化する体系的なアプローチを示すことにより、純粋に経験に基づく設計手法から脱却し、知識体系に貢献します。本研究は、高品質のダイカスト部品を達成するために、設計段階で流動および凝固シミュレーションを統合することの重要性を強調しています。
実用的な意義:
本研究の知見は、家庭用機器および類似部品のゲートシステムを設計するダイカストエンジニアに実用的なガイドラインを提供します。AnyCastingのようなCAEシミュレーションツールを活用することで、金型開発プロセスにおける試行錯誤を大幅に削減でき、設計サイクルの短縮と生産コストの削減につながります。最適化された鋳造レイアウト(Case 3)は、同様のクッキンググリル設計のテンプレートを提供し、改善された冷却戦略の必要性を特定したことは、ダイカスト金型設計における包括的な熱管理の重要性を強調しています。
研究の限界と今後の研究分野:
本研究は数値シミュレーションに限定されており、シミュレーション結果の実験的検証は含まれていません。今後の研究では、Case 3の予測された鋳造性能を検証し、鋳造プロセスパラメータをさらに改良するために、物理的な実験を実施することに焦点を当てる必要があります。特定された引け巣欠陥領域に対処し、より均一な凝固を達成するために、最適化された冷却チャネル設計と鋳造レイアウトとの統合に関する追加の研究が推奨されます。さらに、CAEシミュレーションを使用してプロセスパラメータの変動が鋳造品質に及ぼす影響を調査することは、本研究の価値ある拡張となるでしょう。
8. 参考文献:
- [1] Hu, B.; Tong, K.; Niu, X.; Pinwill, I. Design and optimisation of runner and gating systems for the die casting of thin-walled magnesium telecommunication parts through numerical simulation. J. Mater. Process. Technol. 2000, 105, 128-133. [CrossRef]
- [2] Park, J.-Y.; Kim, E.-S.; Park, Y.-H.; Park, I.-M. Optimization of Casting design for automobile transmission gear housing by 3D filling and solidification simulation in local squeeze diecasting process. Korean J. Mater. Res. 2006, 16, 668-675. [CrossRef]
- [3] Kim, E.; Park, J.; Jeon, E.; Park, I. Current state and technology trend of domestic diecasting industry for automotive parts. J. Korea Foundry Soc. 2007, 27, 13–19.
- [4] Jeong, B.-G.; Kwon, H.-K. A case study on developing automotive part (housing) by filling and solidification analysis. J. Soc. Korea Ind. Syst. Eng. 2015, 38, 44-51. [CrossRef]
- [5] Cho, G.-S.; Choe, K.-H. Study on the rationalization of aluminium casting alloys for automobiles components. J. Korea Foundry Soc. 2011, 31, 319-325. [CrossRef]
- [6] Jeong, W.; Yoon, H.; Hong, S.; Park, I. Optimal gating system design of escalator step die casting part by using Taguchi method. J. Korea Foundry Soc. 2000, 20, 97-103.
- [7] Fu, M.; Yong, M. Simulation-enabled casting product defect prediction in die casting process. Int. J. Prod. Res. 2009, 47, 5203-5216. [CrossRef]
- [8] Jeon, E.; Park, J.; Park, I. Application trend of aluminum castings in automotive component. J. Korea Foundry Soc. 2007, 27, 20-23.
- [9] Lee, D.; Kang, C.; Lee, S. Prediction defect of automotive components by filling and solidification analysis. J. Korea Foundry Soc. 2000, 20, 159-166.
- [10] Kim, Y.; Choi, S.; Cho, J.; Jeong, C.; Kang, C. Optimization of thin-walled aluminum die casting design by solidification simulation. J. Korea Foundry Soc. 2008, 28, 190–194.
- [11] Jin, C.-K.; Kang, C.-G. Fabrication process of aluminum bipolar plate for fuel cell using vacuum die casting. J. Korea Foundry Soc. 2011, 31, 71-78. [CrossRef]
- [12] Gramegna, N.; Della Corte, E.; Poles, S. Manufacturing process simulation for product design chain optimization. Mater. Manuf. Process. 2011, 26, 527-533. [CrossRef]
- [13] Park, J.; Kim, E.; Park, I. Die casting process design of automobile gear housing by metal flow and solidification simulation. J. Korea Foundry Soc. 2004, 24, 347-355.
- [14] Zhang, L.; Li, L.; Zhu, B. Simulation study on the LPDC process for thin-walled aluminum alloy casting. Mater. Manuf. Process. 2009, 24, 1349-1353. [CrossRef]
- [15] Wu, S.; Fuh, J.; Lee, K. Semi-automated parametric design of gating systems for die-casting die. Comput. Ind. Eng. 2007, 53, 222-232. [CrossRef]
- [16] AnyCasting. User Manual Version 6.5; AnyCasting Software: Seoul, Korea, 2019; pp. 55-62.
- [17] Kwon, H.; Kwon, H. Computer aided engineering (CAE) simulation for the design optimization of gate system on high pressure die casting (HPDC) process. Robot. Comput. Integr. Manuf. 2019, 55, 147–153. [CrossRef]
- [18] Kim, T.G.; Choi, J.K.; Hong, J.P.; Lee, Z.H. Reduction of computing time through FDM using implicit method and latent heat treatment in solidification analysis. J. Korea Foundry Soc. 1993, 13, 323-332.
- [19] Xun, S.; Junqing, W.; Hwang, H.Y.; Choi, J.K. Numerical simulation of mold filling process of castings by using of predictor-two step Corrector-VOF. J. Korea Foundry Soc. 2002, 22, 299-303.
- [20] Lee, Y.C.; Choi, J.K.; Hong, C.P. Development of an Integrated Simulation System and its Application to Casting Design. J. Korea Foundry Soc. 1997, 17, 552–559.
- [21] Kwon, H.Y.; Yoon, T.H.; Lee, B.J. Computer simulation on the High-Pressure Die Casting (HDPC) process by filling and solidification analysis. Int. J. Appl. Eng. Res. 2015, 10, 142–145. [CrossRef]
- [22] Jin, C.-K.; Jang, C.-H.; Kang, C.-G. Vacuum die casting mold design of fuel cell bipolar plate using die filling simulation and experimental verification. J. Korea Foundry Soc. 2012, 32, 65–74. [CrossRef]
- [23] Hosseini, S.M.; Utlu, Z. Design optimization of clutch housing mold by fluid flow and solidification simulation. J. Mech. Sci. Technol. 2016, 30, 2731-2742. [CrossRef]
9. 著作権:
- 本資料は、"[Hong-Kyu Kwon]"氏の論文:"[Layout Design and Die Casting Using CAE Simulation for Household Appliances]"に基づいています。
- 論文ソース:https://doi.org/10.3390/app112110128
本資料は上記の論文を要約したものであり、商業目的での無断使用は禁止されています。
Copyright © 2025 CASTMAN. All rights reserved.