この論文の概要は、['POLITECNICO DI TORINO']によって発行された['LIGHTWEIGHT DESIGN OF VEHICLE SIDE DOOR']という論文に基づいて作成されました。
1. 概要:
- タイトル:LIGHTWEIGHT DESIGN OF VEHICLE SIDE DOOR (車両サイドドアの軽量設計)
- 著者:JINDONG JI
- 発行年:2015年2月
- 発行ジャーナル/学会:POLITECNICO DI TORINO、DOCTORATE SCHOOL、Ph.D in Mechanics(博士論文)
- キーワード:Vehicle side door (車両サイドドア)、Lightweight design (軽量設計)、Composite material (複合材料)、Crashworthiness (耐衝撃性)、Finite element analysis (有限要素解析)、NVH、Static analysis (静的解析)
![Figure 1.1-1 Passenger cars registrations by member state [1]](https://castman.co.kr/wp-content/uploads/image-741-png.webp)
2. 抄録または序論
本論文では、温室効果ガス(GHG)排出量の増加に関する環境への懸念と、車両安全に関する政府規制の強化に対処しており、自動車産業がより軽量で安全な車両を製造するために新しい技術を採用する必要性を述べています。軽量設計は、燃費を向上させ、車両排出量を削減するための効果的な戦略として提示されています。研究は、従来は鋼鉄で作られている複雑なシステムである車両側面ドアのサブ構造に焦点を当て、安全性と性能を損なうことなく軽量化を達成するための複合材料の可能性を探求しています。本研究では、トヨタ ヤリス 2010年モデル用の複数の複合サイドドア構造を開発および評価し、静的設計要件、NVH設計基準、および耐衝撃性を考慮しています。ABAQUSおよびLS-DYNA数値シミュレーションツールを使用して、複合材設計の性能を、基準ソリューションとして機能する元の鋼製ドア構造と比較評価します。本論文は、複合材料の特性評価、有限要素モデルシミュレーション、静的およびモーダル解析、耐衝撃性評価を包括的に網羅し、複合材料を使用した車両サイドドアの軽量設計に関する包括的な調査を提供します。
3. 研究背景:
研究トピックの背景:
GHG排出量の増加に関する環境への懸念と、車両安全に関する政府規制の強化により、自動車メーカーは新しい技術を模索せざるを得なくなっています。軽量設計は、燃費の向上と車両排出量の削減のためにますます重要になっています。ただし、車両の軽量化技術は、顧客の快適性と車両の安全性を損なうものであってはなりません。
既存研究の現状:
自動車の研究開発部門は、従来の材料を代替するために、高張力鋼、アルミニウム、マグネシウム、複合材などの先進材料を積極的に研究しています。複合材は、より高い強度、より低い重量、より優れた耐食性などの利点を提供します。しかし、製造コスト、生産量、設計方法論、接合技術、リサイクル問題など、複合材の広範な採用には課題が残っています。車両の安全性は、自動車に軽量材料を実装する際に依然として重要な考慮事項です。
研究の必要性:
本研究は、安全性基準を維持しながら、軽量車両設計の課題に対処する必要性から動機付けられています。車両側面ドアのサブ構造は、その構造的な複雑さと機能的な重要性から、研究対象として選ばれました。従来の鋼製ドア構造は重量があり、このコンポーネントの複合材代替案を検討することは、車両全体の軽量化と性能向上を達成するために不可欠です。
4. 研究目的と研究課題:
研究目的:
主な研究目的は、車両用の複合サイドドア構造を開発および評価し、軽量設計を達成しながら、静的、NVH、および耐衝撃性の要件を満たすことです。本論文は、従来の鋼鉄の代替として、車両サイドドアの設計に複合材料を使用することの実現可能性と利点を実証しようとしています。
主要な研究課題:
主要な研究は、以下の点に焦点を当てています。
- トヨタ ヤリス 2010年モデル用の複数の複合サイドドア構造の開発。
- ABAQUSおよびLS-DYNA数値ツールを使用した、これらの複合構造の性能のシミュレーションと分析。
- 静的挙動、NVH特性、および耐衝撃性の観点から、複合ドアソリューションの性能を元のヤリス鋼製ドア構造と比較。
- 車両サイドドア用の革新的な複合補強パネル設計の研究。
研究仮説:
本研究では、複合サイドドア構造は、従来の鋼製ドアと比較して大幅な軽量化を達成しながら、剛性、NVH、および耐衝撃性の点で構造性能を維持または向上させることができると仮説を立てています。また、革新的な複合補強パネル設計は、従来の鋼製衝撃ビームと補強材を効果的に置き換え、複合サイドドアの全体的な性能を向上させることができるとも仮説を立てています。
5. 研究方法論
研究設計:
本研究では、複合サイドドア構造を設計および評価するために、数値シミュレーションベースのアプローチを採用しています。従来の鋼鉄と複合材の両方のドア設計の有限要素(FE)モデルを開発し、さまざまな荷重条件下で解析します。
データ収集方法:
データは、ABAQUSおよびLS-DYNAソフトウェアを使用した数値シミュレーションを通じて収集されます。鋼鉄およびさまざまな複合材料(CFRP、GFRP、GMT、GMT-UD、GMT-TEX、SIMS)の材料特性は、FEモデルの入力パラメータとして使用されます。シミュレーション出力には、応力分布、変位、侵入測定、および衝突シミュレーションにおけるダミーの生体力学的反応が含まれます。
分析方法:
- 静的解析: 垂直、水平、横剛性、およびたるみ荷重ケースにおける複合ドア設計の構造剛性と強度を評価するために、線形および非線形静的解析を実施します。NVH特性を評価するためにモーダル解析を実施します。
- 動的解析: 耐衝撃性評価には明示的動的解析を使用し、FMVSS214規制に従って側面衝突シナリオをシミュレーションします。頭部傷害基準(HIC)、肋骨のたわみ、腹部力、および恥骨結合力を含む生体力学的反応を分析して、乗員の安全性を評価します。
- 比較分析: 複合ドアソリューションの性能を、静的、NVH、および耐衝撃性基準に関するシミュレーション結果に基づいて、元のヤリス鋼製ドア構造(基準ソリューション)と比較します。
研究対象と範囲:
研究対象は車両サイドドア構造であり、特にトヨタ ヤリス 2010年モデルを対象としています。範囲には以下が含まれます。
- CFRP、GFRP、GMT、GMT-UD、GMT-TEX、およびSIMS材料を使用した複合サイドドア構造の設計と解析。
- 静的、モーダル、および耐衝撃性性能の数値シミュレーション。
- 側面衝突シナリオにおける侵入変位と生体力学的反応の評価。
- 基準鋼製ドア構造との比較。
6. 主な研究結果:
主要な研究結果:
- 静的およびモーダル解析: 複合ドア構造、特に複合フレームを備えた構造は、垂直および水平荷重ケースにおいて、鋼鉄基準ドアと同等またはわずかに高い剛性を示しました。モーダル解析では、複合ドア構造がより高い固有振動数を示し、NVH性能が向上していることが示されました。
- 耐衝撃性評価: 複合ドアソリューションは、側面衝突シミュレーションにおいて、鋼製ドアと比較して侵入変位が減少しました。エネルギー吸収能力は、複合ドアの方が大幅に高くなりました(約20%増加)。肋骨のたわみ、腹部力、および恥骨結合力を含む生体力学的反応は、複合ドア設計のFMVSS214規制制限内にあり、乗員保護が十分であることを示しています。
- 革新的な複合パネル: 革新的な複合補強パネル設計が開発および評価され、従来の鋼製衝撃ビームと補強材を置き換え、耐衝撃性を維持しながら重量をさらに削減できる可能性を示しました。
- 軽量化: 複合材による材料置換により、大幅な軽量化が実現し、鋼製ドアと比較して最終的な質量削減率は、複合ソリューションによって32%から38%の範囲でした。
提示されたデータの分析:
論文全体、特に第6章と第7章に示されている図表のデータは、主要な研究結果を裏付けています。図6.1-4、6.1-8、および6.1-11は、静的荷重下での変位分布を示しており、複合ドアの変位が減少していることを示しています。表6.1-1、6.1-3、および6.1-5は、応力と変位を定量化し、同等または改善された静的性能を確認しています。図7.1-3は、衝突シミュレーションにおける侵入変位履歴を示しており、複合ドアの侵入が減少していることを示しています。図7.2-5、7.2-8、7.2-9、および7.2-10は、生体力学的反応を示しており、複合ドアが安全規制の制限を満たしていることを示しています。表7.3-1は、質量削減データを要約し、複合ソリューションの軽量化の可能性を強調しています。
図のリスト:
![Figure 1.1-2 Passenger cars registrations by vehicle brand [1]](https://castman.co.kr/wp-content/uploads/image-742-png.webp)
![Figure 1.2-1 Average fuel consumption in the EU by vehicle manufacture [1]](https://castman.co.kr/wp-content/uploads/image-743-png.webp)
![Figure 1.2-2 Passenger cars 𝑪𝑶𝟐 emissions by member state [1]](https://castman.co.kr/wp-content/uploads/image-744-png.webp)
![Figure 1.2-3 Passenger cars 𝑪𝑶𝟐 emissions by vehicle segment [1]](https://castman.co.kr/wp-content/uploads/image-745-1024x368.webp)
![Figure 2.1-1 Representative vehicle energy flows in an urban driving cycle [1]](https://castman.co.kr/wp-content/uploads/image-746-1024x414.webp)
![Figure 2.1-2 Energy flow within an automotive vehicle [2]](https://castman.co.kr/wp-content/uploads/image-747-png.webp)
![Figure 2.1-3 Future propulsion system pathways [1]](https://castman.co.kr/wp-content/uploads/image-748-png.webp)
![Figure 2.2-2 Different segment vehicle mass change [6]](https://castman.co.kr/wp-content/uploads/image-749-png.webp)
![Figure 2.2-4 Vehicle weight composition by mass ratio [8]](https://castman.co.kr/wp-content/uploads/image-750-png.webp)
![Figure 2.2-5 1975 and 2007 average vehicle mass breakdown by material [9]](https://castman.co.kr/wp-content/uploads/image-751-1024x427.webp)
![Figure 2.2-11 Vehicle material compositions by percent mass [15]](https://castman.co.kr/wp-content/uploads/image-752-png.webp)
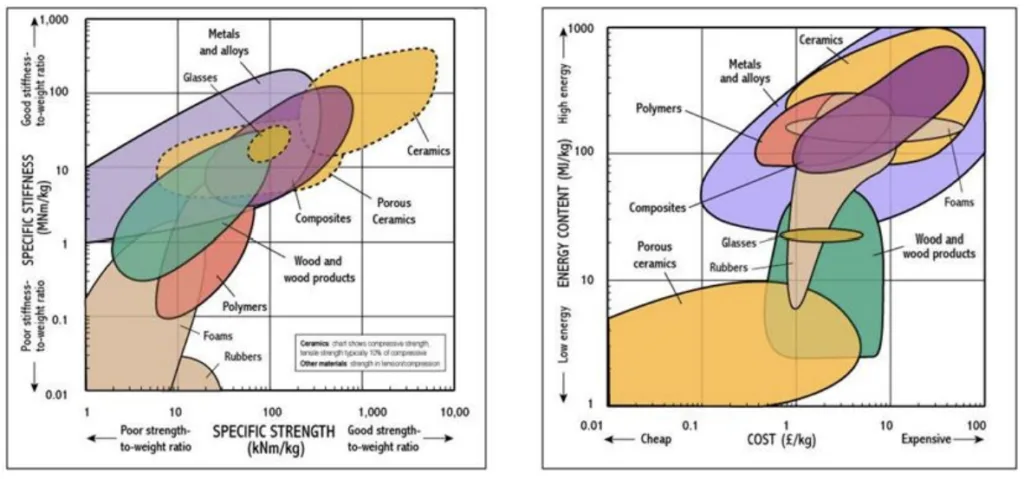
![Figure 2.2-15 Configure of BMW i3 [19]](https://castman.co.kr/wp-content/uploads/image-754-1024x281.webp)
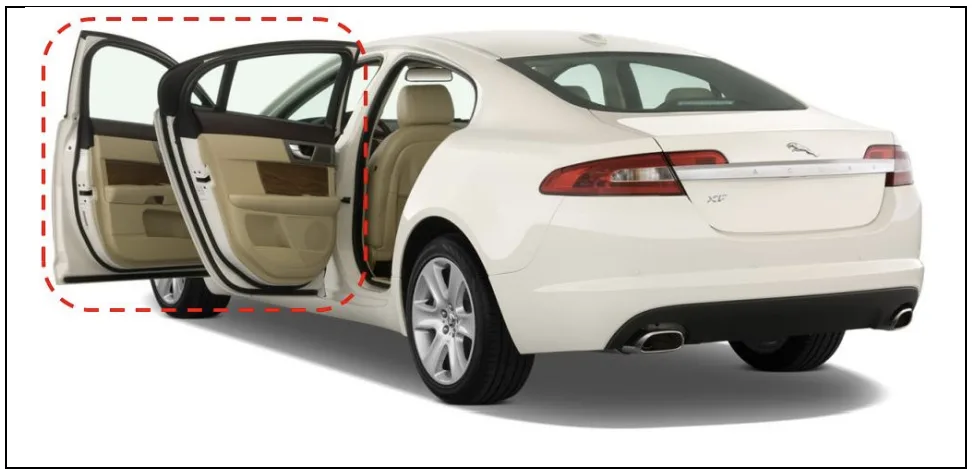
![Figure 3.1-4 Side door components of Toyota Yaris 2010 model [3]](https://castman.co.kr/wp-content/uploads/image-756-png.webp)
![Figure 3.2-2 Active safety and passive safety in automotive engineering [12]](https://castman.co.kr/wp-content/uploads/image-757-1024x667.webp)
![Figure 3.2-3 Different zones in vehicle crash impact [13]](https://castman.co.kr/wp-content/uploads/image-758-png.webp)
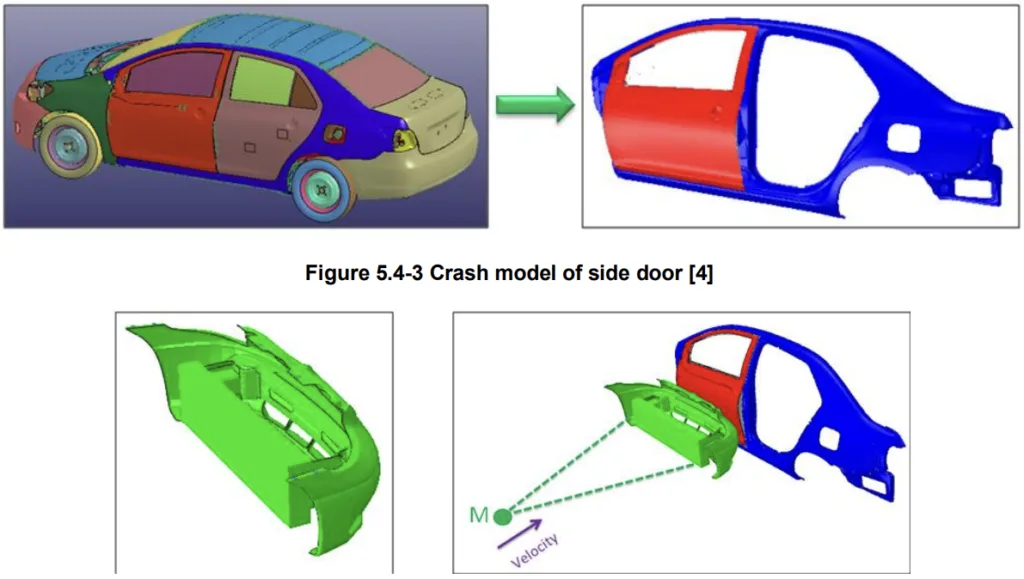
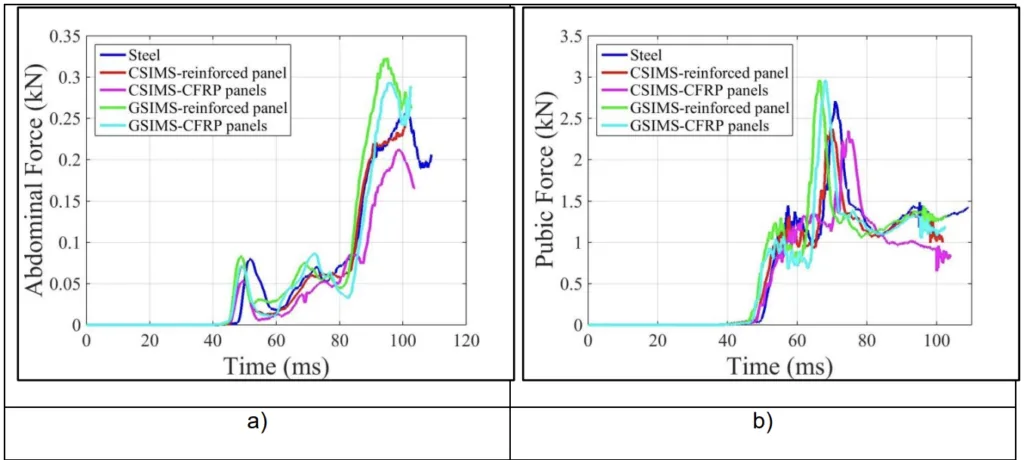
- 図 1.1-1 会員国別の乗用車登録台数 [1]
- 図 1.1-2 車両ブランド別の乗用車登録台数 [1]
- 図 1.2-1 EUにおける自動車メーカー別の平均燃料消費量 [1]
- 図 1.2-2 会員国別の乗用車CO2排出量 [1]
- 図 2.1-1 都市部での運転サイクルにおける代表的な車両エネルギーフロー [1]
- 図 2.1-2 自動車車両内のエネルギーフロー [2]
- 図 2.1-3 将来の推進システム経路 [1]
- 図 2.1-4 米国モデルイヤー2005年の車両重量と燃料消費量 [1]
- 図 2.2-1 車両総重量の推移 [5]
- 図 2.2-2 セグメント別車両重量の変化 [6]
- 図 2.2-3 EU加盟国別の車両重量の変化 [7]
- 図 2.2-4 質量比による車両重量構成 [8]
- 図 2.2-5 1975年と2007年の平均車両重量の材料別内訳 [9]
- 図 2.2-6 乗用車の異なる部品の引張強度要件とHSSの適用範囲 [10]
- 図 2.2-7 西ヨーロッパにおける自動車1台あたりの平均アルミニウム使用量 [11]
- 図 2.2-8 ヨーロッパ車におけるアルミニウムの相対的および絶対的な使用量 [11]
- 図 2.2-9 アルミニウム集約型車両
- 図 2.2-10 さまざまな分野における複合材料の応用
- 図 2.2-11 質量パーセントによる車両材料構成 [15]
- 図 2.2-12 材料の機械的性能の比較のためのアシュビーマップ
- 図 2.2-13 材料の強度とコストの比較のためのアシュビーマップ
- 図 2.2-14 炭素繊維で強化された車両
- 図 2.2-15 BMW i3の構成 [19]
- 図 3.1-1 従来の自動車サイドドア
- 図 3.1-2 車両サイドドアの異なるタイプ [1]
- 図 3.1-3 3つの異なるドアアーキテクチャ [2]
- 図 3.1-4 トヨタ ヤリス 2010年モデルのサイドドア部品 [3]
- 図 3.1-5 2010年式トヨタ ヤリス セダンとFEモデル
- 図 3.2-1 EUにおける事故、死亡者数、負傷者数の推移 [11]
- 図 3.2-2 自動車工学におけるアクティブセーフティとパッシブセーフティ [12]
- 図 3.2-3 車両衝突時の異なるゾーン [13]
- 図 3.2-4 車両衝突基準
- 図 3.3-1 規制FMVSS 214. [14]
- 図 3.3-2 可動式変形バリア(MM)の寸法 [14]。
- 図 3.3-3 サイドクラッシュテストで使用されるダミーファミリーと異なるダミー
- 図 3.3-4 FMVSS規格の評価システム
- 図 4.1-1 マトリックス材料に基づく複合材料の分類 [1]
- 図 4.1-2 構造特性に基づく複合材料の分類 [2]
- 図 4.1-3 マトリックス材料の概要 [2]
- 図 4.1-4 織り方:平織り、綾織り、朱子織り [11]
- 図 4.2-1 衝突後の車両の変形
- 図 4.2-2 a) GMTの構造、b) GMT-UDの構造、c) GMT-TEXの構造
- 図 4.2-3 a) CSIMSのスタッキング、b) GSIMSのスタッキング
- 図 4.2-4 ヤリスドアのアウターパネル、インナーパネル、インパクトビームの材料特性 [16]
- 図 5.3-1 ヤリスドアの簡略化されたFEモデル [4]
- 図 5.3-2 従来のドアモデルを取得するための抽出プロセス [4]
- 図 5.3-3 複合ビーム
- 図 5.3-4 平面モデルと曲面モデルにおける複合ビームの分布
- 図 5.3-5 複合ドアモデルにおけるジョイント形状と位置
- 図 5.3-6 側面フロントドアの3つのFEモデル
- 図 5.4-1 ヤリス サイドドアモデル [4]
- 図 5.4-2 考慮された部品:アウターパネル、インナーパネル、インパクトビーム
- 図 5.4-3 サイドドアの衝突モデル [4]
- 図 5.4-4 側面衝突のシミュレーション:変形可能なバンパーとサイドドア構造
- 図 5.5-1 シミュレーションモデル、a) 規制FMVSS 214、b) ヤリスモデル、c) 可動式変形バリア(MDB)、d) EURO-SID 2ダミー
- 図 5.6-1 a) 簡略化された全アルミニウム補強材(STAR)パネルを含む概略的なアルミニウムドア構造。b) インナーパネル、アウターパネル、STARパネルを示す垂直ドア断面。c) STARパネルの波形形状。[9]
- 図 5.6-2 a) ヤリスのSTARパネル。b) ヤリスのオリジナルドアモデル。c) ヤリスの革新的なドアモデル
- 図 5.6-3 a) 交換可能な部品。b) 複合材で作られた革新的な部品。c) 4つの接続領域
- 図 5.7-1 ABAQUSの複合材料モデル
- 図 5.7-2 LS-DYNAの複合材料モデル
- 図 6.1-1 車両サイドドアの3つのFEモード
- 図 6.1-2 - 垂直荷重ケースと複合モデルのヒンジ位置に適用された力。
- 図 6.1-3 荷重ケース1における3つのモデルのフォンミーゼス応力分布。
- 図 6.1-4 荷重ケース1における垂直変位分布。
- 図 6.1-5 荷重ケース1における垂直変位と反力。
- 図 6.1-6 – 水平荷重ケース。
- 図 6.1-7 - 水平荷重下における3つのモデルのフォンミーゼス応力。
- 図 6.1-8 - 水平荷重に対する3つのモデルの水平変位。
- 図 6.1-9- 荷重ケース2に対する水平変位と反力。
- 図 6.1-10- 準静的侵入シミュレーションモデル
- 図 6.1-11- 荷重ケース3に対する3つのモデルの押し出し方向の変位。
- 図 6.1-12- 準静的侵入シミュレーションにおける変位と反力。
- 図 6.2-1 ヤリスのサイドドア構造モデル
- 図 6.2-2 等しい剛性基準
- 図 6.2-3 横剛性とたるみ荷重ケース。
- 図 6.2-4 さまざまな荷重ケースに対する荷重-変位線図
- 図 6.2-5 たるみケースにおける3つのモデルの荷重-変位線図
- 図 6.3-1 1次モードと2次モードのモーダル形状。
- 図 6.3-2 周波数変化理論
- 図 7.1-1 ヤリス サイドドア構造モデル。
- 図 7.1-2 耐衝撃性評価のための衝突モデル。
- 図 7.1-3 3つのモデルの侵入変位履歴
- 図 7.1-4 3つのモデルの反力履歴
- 図 7.1-5 サイドドア構造によって吸収されたエネルギー
- 図 7.1-6 CFRP_Panel&Beamモデルの運動エネルギーと内部エネルギー。
- 図 7.2-1 側面衝突モデル:a) トヨタ ヤリス 2010、b) 可動式変形バリア、c) 側面衝突規制FMVSS214、d) ES-2ダミー。
- 図 7.2-2 ヤリスドアで考慮された部品:a) アウターパネル、b) インナーパネル、c) 補強インパクトビーム。
- 図 7.2-3 側面衝突の影響中のダミーの動き
- 図 7.2-4 インナーパネルの侵入変位調査のための9つの重要なポイント。
- 図 7.2-5 サイドドアのインナーパネルの9つの重要なポイントの侵入変位
- 図 7.2-6 反力と頭部加速度
- 図 7.2-7 a) ルーフレールとのダミーヘッドインパクト、b) ルーフレール周辺のフォーム、c) サイドエアバッグ。
- 図 7.2-8 肋骨のたわみ、a) 上部肋骨、b) 中部肋骨、c) 下部肋骨。
- 図 7.2-9 腹部力。
- 図 7.2-10 恥骨結合力。
- 図 7.3-1 アウターパネル、補強パネル、インナーパネル。
- 図 7.3-2 乗員コンパートメントの侵入変位
- 図 7.3-3 肋骨のたわみ
- 図 7.3-4 腹部合力
- 図 7.3-5 恥骨結合力
- 図 7.3-6 侵入変位
- 図 7.3-7 肋骨のたわみ a) 上部肋骨、b) 中部肋骨、c) 下部肋骨
- 図 7.3-8 a) 腹部力、b) 恥骨結合力
- 図 7.3-9 侵入変位
- 図 7.3-10 肋骨のたわみ a) 上部肋骨、b) 中部肋骨、c) 下部肋骨
- 図 7.3-11 a) 腹部力、b) 恥骨結合力
- 図 7.3-12 侵入変位
- 図 7.3-13 肋骨のたわみ a) 上部肋骨、b) 中部肋骨、c) 下部肋骨
- 図 7.3-14 a) 腹部力、b) 恥骨結合力
7. 結論:
主な調査結果の概要:
本研究は、複合材料が車両サイドドア構造において鋼鉄に代わる実行可能な代替案を提供し、大幅な軽量化を達成し、構造的および安全性能を維持または向上させるという結論を下しています。複合ドアソリューションは、同等の静的剛性、強化されたNVH特性、および侵入低減とエネルギー吸収の点で優れた耐衝撃性を示しました。衝突シミュレーションにおける生体力学的反応は、FMVSS214規制制限内にあり、適切な乗員保護を示しています。革新的な複合補強パネル設計は、軽量化の可能性をさらに高めます。
研究の学術的意義:
本研究は、車両サイドドア設計への複合材料の応用に関する包括的な調査を提供することにより、学術分野に貢献しています。複合構造の静的、NVH、および耐衝撃性性能を評価するための詳細な数値シミュレーション方法論を提供します。また、本研究は、自動車構造用途における複合材料の挙動に関する理解を深め、軽量車両設計と安全に関する将来の研究のための貴重なデータを提供します。
実際的な意味合い:
調査結果は、自動車産業にとって重要な実際的な意味合いを持っています。軽量複合サイドドアの実現可能性を実証することで、車両重量を削減し、燃費を向上させ、排出量を削減するための道筋を提供し、世界の環境規制と消費者の要求に合致します。本研究は、自動車エンジニアが車両生産に複合サイドドア構造を開発および実装するために利用できる設計ガイドラインと検証済みの数値モデルを提供します。
研究の限界と今後の研究分野:
本研究では、側面エアバッグの除外や、衝突シミュレーションにおけるフォームおよびシートベルトシステムの詳細なモデリングなど、頭部加速度の結果に影響を与える可能性のある限界を認めています。今後の研究分野には、以下が含まれます。
- プロトタイプ複合サイドドアの物理的テストによる数値シミュレーション結果の実験的検証。
- 強化された性能と費用対効果のための複合材料の選択と積層構成の最適化。
- 複合材-アルミニウムハイブリッドドア構造の接合技術の研究。
- より正確な耐衝撃性予測のために、詳細なエアバッグおよび拘束システムを組み込むためのFEモデルのさらなる改良。
- 複合サイドドアの大量生産のための製造プロセスとスケーラビリティの探求。
8. 参考文献:
- [1]. The International Council on Clean Transportation, ―European Vehicle Market Statics, Pocketbook 2013‖.
- [2]. The Organization for Economic Co-operation and Development (OECD), ―Strategies to Reduce Greenhouse Gas Emissions from Road Transport: Analytical Methods‖, 2002.
- [3]. European Environment Agency, ―Monitoring CO2 emissions from new passenger cars in the EU: summary of data for 2012‖.
- [4]. David C., Sean B., Emily W. and Martin W., ―Trends in NOx and NO2 emissions and ambient measurements in the UK‖, 2011.
- [5]. TNO Science and Industry, ―Review and analysis of the reduction potential and cost of technological and other measures to reduce CO2-emisssions from passenger cars‖, 2006.
- [6]. www.autosteel.org.
- [7]. Nicholas L., ―Review of technical literature and trends related to automobile mass-reduction technology‖, report for California Air Resources Board, May 2010.
- [8]. The International Council on Clean Transportation, ―European Vehicle Market Statics, Pocketbook 2013‖.
- [9]. Stodolsky F., A. Vyas, et al. (1995), ―Life-Cycle Energy Savings Potential from Aluminum-Intensive Vehicles‖, Conference Paper, 1995 Total Life Cycle Conference&Exposition. October 16-19, 1995, Vienna, Austria.
- [10]. Abraham, A. Ducker Worldwide. (2011, May). ―Future Growth of AHSS [PowerPoint presentation at Great Designs in Steel Seminar]‖.
- [11]. J. Galan, L. Samek, P. Verleysen, K. Verbeken and Y.Houbaert, ―Advanced high strength steels for automotive industry‖, Revista de Metalurgia, 48 (2), ISSN: 0034-8570.
- [12]. J.Hirsch, ―Automotive Trends in Aluminum- The European Perspective‖, Materials Forum Volume 28, 2004.
- [13]. Ducker Worldwide, ―The Past, Present and Future of Aluminum in North American Light Vehicles‖, October 16, 2012.
- [14]. McWilliams A., ―Advanced Materials, Lightweight Materials in Transportation‖, report, Report Code: AVM056A, 2007.
- [15]. Ghassemieh E., ―Materials in Automotive Application, State of the Art and Prospects, New Trends and Developments in Automotive Industry‖, InTech, Marcello Chiaberge, ISBN: 978-953-307-999-8, 2011.
- [16]. http://wardsauto.com/subscriptions/facts-figures.
- [17]. Taub A., Krajewski P., Luo A. and Owens J., ―The Evolution of Technology for Materials Processing over the Last 50 Years: The Automotive Example ‖, JOM, February.
- [18]. Marc R., Deena P. and Tom W., ―Vehicle Design and the Physics of Traffic Safety‖, Physics Today, January 2006.
- [19]. http://www.bmw.com/
- [20]. http://www.euroncap.com/tests/fiat_500_2007/298.aspx.
- [21]. European Aluminum Association, ―The Aluminum Automotive MANUAL-Hang on parts‖, 2013.
- [22]. Daniel E.Whitney, MIT Engineering System Division and Cambridge MA, ―Design and Manufacturing of Car Doors: Report on Visits Made to US, European and Japanese Car Manufacturers in 2007‖, March 2008.
- [23]. National Crash Analysis Center, http://www.ncac.gwu.edu/
- [24]. World Health Organization, ―Global Status Report on Road Safety‖, 2013.
- [25]. Volvo Trucks, ―European Accident Research and Safety Report 2013‖.
- [26]. National Highway Traffic Safety Administration, ―An Analysis of Recent Improvements to Vehicle Safety‖, DOT HS 811 572, June 2012.
- [27]. EVALUE Project, ―Testing and evaluation methods for active vehicle safety‖, http://www.evalue-project.eu/.
- [28]. Final report of ELVA Project, ―Societal scenarios and available technologies for electric vehicle architectures in 2020‖, Grant Agreement Number 265898.
- [29]. Nat’l Highway Traffic Safety Admin., DOT §571.214, Dec. 13, 1979.
- [30]. Juan M. A. G, PhD thesis, ―A study to improve the crash compatibility between cars in side impact‖, Marzo 2008.
- [31]. Samaha RR, Elliott DS, ―NHTSA side impact research: motivation for upgraded test procedures‖, 18th International Technical Conference on the Enhanced Safety of Vehicles, Nagoya, Japan, 2003.
- [32]. Kathleen D. K., Carol A. C. F., Kristen N., Lawrence W. S. and Jonathan D. R., ―Abdominal injury in motor-vehicle crashes‖, UMTRI-2008-40, Nov. 2008.
- [33]. Peter S., Uli F., Sebastian S., Markus P., Arno E., DYNAmore GmbH, MAGNA STEYR, ―Comparison of ES-2re with ES-2 and USSID Dummy‖ , DYNAmore GmbH, 2014.
- [34]. Aimar A., Molina G. and Volpenge M., ―The magnesium door project‖, proc. of Int. Conf. Florence ATA 2003, Florence (1), paper 03A1039.
- [35]. Seong S. C, Dai G. L and Kwang S. J., ―Composite side-door impact beams for passenger cars.‖ Composite Structures Vol. 38, No. 1-4, 1997, pp. 229-239.
- [36]. Patberg L., Philipps M. and Dittmann R., ―Fiber-reinforced composites in the car side structure‖, Proc Instn Mech Engrs, 1999, Vol.213 part D, pp. 417-423.
- [37]. Belingardi G., ―Recent advances in joining technology for car body applications‖, proc. Int. Conf. MVM 2006 (Motor Vehicle and Motors), Kragujevac (Serbia), 4-6 October 2006.
- [38]. Banea M. D. and Da Silva L. F., ―Adhesively bonded joints in composite materials: an overview‖, Proc Instn Mech Engrs, 2009, Vol.223 part L, pp.1-18.
- [39]. http://www.slideshare.net/BKLR/polymer-matrix-composites.
- [40]. Giovanni B. , presentation of course ―Progettazione di strutture meccaniche in materiale composito‖, Politecnico di Torino, 2014.
- [41]. Frederick T. W., James C. W. and Hong Li, PPG Industries, Inc, ―Glass Fibers‖, ASM Handbook, Vol. 21: Composites (#06781G), 2001.
- [42]. Paul J. W., Zoltek Corporation, ―Carbon Fibers‖, ASM Handbook, Vol.21: Composites, 2001.
- [43]. http://www.angelfire.com/ma/ameyavaidya/b_fiber.htm#boron
- [44]. Reashad B. K. and Nasrin F., ―Kevlar-The Super Tough Fiber‖, International Journal of Textile Science 2012, pp78-83.
- [45]. David Roylance, ―Introduction to composite materials‖, March 24, 2000.
- [46]. Curt A., ―NM EPOXY HANDBOOK‖, third edition,2004.
- [47]. http://www.netcomposites.com/guide/polyester-resins/8
- [48]. Ermias G. Korico., ―Implementation of Composites and Plastics Materials for Vehicle Lightweight‖, PhD thesis,2012.
- [49]. MIL-HDBK-17-5, ―Composite Materials Handbook‖, 17 June, 2002.
- [50]. http://composite.about.com/library/data/blc-cfs003ltm25-rtd.htm
- [51]. Giovanni B. and Brunetto M., ―Recent research results in composite materials and adhesive applications for vehicle lightweight‖, Int. Cong. Motor Vechiles&Motors 2014,October 9th-10th.
- [52]. Patent US2002/0064640A1, ―Thin composite laminate and use thereof in making sports articles, especially boots‖.
- [53]. P. Nieri, I. Montanari, A. Terenzi, L. Torre and J. M. Kenny, ―A novel composite configuration for low-cost panels with improved toughness‖, 29th International Conference and Forum- SECO 08, March 31st–April 2nd.
- [54]. http://www.ncac.gwu.edu/
- [55]. Giovanni B., Alem T. Beyene and Ermias G. Korico., ―Geometrical optimization of bumper beam profile made of pultruded composite by numerical simulation‖, Composite Structures, 2013.
9. 著作権:
- この資料は、"JINDONG JI"の論文:「LIGHTWEIGHT DESIGN OF VEHICLE SIDE DOOR」に基づいています。
- 論文ソース:[DOI URL]
この資料は上記の論文を要約したものであり、商業目的での無断使用は禁止されています。
Copyright © 2025 CASTMAN. All rights reserved.