この論文の紹介は、トリノ工科大学によって発行された「自動車用途向け自己硬化性アルミニウム合金」に基づいて作成されました。
1. 概要:
- タイトル: 自動車用途向け自己硬化性アルミニウム合金 (Self hardening aluminum alloys for automotive applications)
- 著者: クリスチャン・カステッラ (Christian Castella)
- 出版年: 論文中に明記されていません。(著者の出版リストから2014年と推定)
- 発行ジャーナル/学会: トリノ工科大学 工学部 材料科学技術博士課程 (Politecnico di Torino, Facoltà di Ingegneria, PhD in materials science and technology)
- キーワード: 自己硬化性アルミニウム合金 (Self-hardening aluminum alloys), 自動車用途 (Automotive applications), Al-Zn-Si-Mg 合金 (Al-Zn-Si-Mg alloys), ナックルコンポーネント (Knuckle component), 耐食性 (Corrosion resistance), 機械的特性 (Mechanical properties), 熱処理コスト (Heat treatment costs)
![Figure 26: Aluminum applications in a car [30].](https://castman.co.kr/wp-content/uploads/image-650-png.webp)
2. 概要
この博士論文は、トリノ近郊カルマニョーラに位置するアルミニウム鋳造所であるテクシッド・アルミニウムとの協力により実施されました。本研究は、革新的な軽アルミニウム合金のクラスであり、特に輸送産業において、さまざまな産業用途に適した高い機械的特性を示す自己硬化性アルミニウム合金(Al-Zn-Si-Mg合金)に焦点を当てています。重要な特徴は、熱処理を必要とせずに優れた性能を発揮できることであり、約7〜10日間の保管期間後、室温で自然時効を受けます。熱処理を回避できる可能性は、製造コスト、エネルギー消費、および部品の変形リスクを低減する上で重要な利点となります。本論文は、自動車部品製造において実際に使用されているT6熱処理A356合金の代替ソリューションを見つけることを目的としており、ナックルサスペンション部品への自己硬化性合金の適用可能性を評価しています。熱処理を回避することによる省エネルギーに関する経済的考察も探求されています。論文の大部分は、ナックルサスペンション部品製造に最適な合金組成を定義するために、Mg含有量と冷却速度の影響を調べながら、自己硬化性アルミニウム合金の構造的特徴、機械的特性、および耐食性を調査しています。
3. 研究背景:
研究トピックの背景:
アルミニウム合金は、軽量性により自動車産業での利用が増加しており、車両重量の削減と燃費の向上に貢献しています。論文では、「アルミニウムは軽量金属であり、地球上で最も豊富な金属元素の1つであり…アルミニウムは非常に重要な経済的競争相手となり、アルミニウム産業は指数関数的な成長を遂げました[2-3]。」と述べています。この軽量化の推進は、「自動車の燃料消費を抑制し、同時にガス、特にCO2の排出を抑制する」必要性によってさらに動機づけられています。
既存研究の現状:
現在、ナックルコンポーネントを含む自動車部品の製造には、T6熱処理されたA356合金が使用されています。論文は、「この博士論文の目標は、自動車部品製造に実際に使用されているT6熱処理A356合金の代替ソリューションを見つけることでした。」と述べています。熱処理は、アルミニウム合金の機械的強度を高めるために一般的に使用されていますが、エネルギー集約型であり、製造上の複雑さを招く可能性があります。文書では、「一般的に、熱処理はアルミニウム鋳造所においてアルミニウム合金の機械的強度を高めるために広く使用されています。実際には、環境への影響を小さくするためにエネルギー消費を最小限に抑える傾向が強くあります。」と指摘しています。
研究の必要性:
この研究は、部品の性能を維持または向上させながら、自動車製造におけるエネルギー消費と製造コストを削減する必要性に対処しています。自己硬化性アルミニウム合金は、エネルギー集約型の熱処理の必要性をなくすことで、潜在的な解決策を提供します。論文では、「熱処理を回避できる可能性は、一部の部品の製造コストと製造プロセスに関与するエネルギー量を大幅に削減する上で重要な利点となります。さらに、熱処理なしでは、製造中の部品の変形のリスクが完全に排除されます。」と強調しています。この研究は、自動車用途における従来の熱処理合金に代わる、実行可能で費用対効果の高い代替材料として、自己硬化性アルミニウム合金を探求し、最適化するために不可欠です。
4. 研究目的と研究課題:
研究目的:
主な研究目的は、「自動車部品製造において実際に使用されているT6熱処理A356合金の代替ソリューションを見つけること」です。これには、特にナックルサスペンション部品の製造において、自己硬化性アルミニウム合金を代替材料として評価することが含まれます。
主要研究:
主要な研究分野は次のとおりです。
- 「自己硬化性アルミニウム合金の構造的特徴と機械的特性の研究」
- 「それらの耐食性の調査」
- 「Mg含有量と冷却速度が、3つの異なる自己硬化性アルミニウム合金の微細構造に及ぼす影響」
- 「ナックルサスペンション部品製造に最適な合金組成を定義することを目指す」
研究仮説:
正式な仮説として明示されていませんが、研究は次の前提の下で実施されています。
- 自己硬化性Al-Zn-Si-Mg合金は、自動車部品においてT6熱処理A356合金の代替として、同等または十分な機械的特性を達成できる。
- 自己硬化性合金による熱処理の排除は、製造における大幅なコストおよびエネルギー削減につながる。
- 自己硬化性Al-Zn-Si-Mg合金の微細構造、機械的特性、および耐食性は、鋳造中のMg含有量と冷却速度を調整することで最適化できる。
5. 研究方法
研究デザイン:
本研究では、代表的な自動車部品として「ナックルコンポーネント」に焦点を当てた、実例研究アプローチを採用しています。ダイカストによって製造された「自己硬化性」アルミニウム合金の実験的調査と最適化が含まれます。
データ収集方法:
以下のデータ収集方法が利用されました。
- 微細構造解析: 「微細構造解析用のサンプルは、標準的な冶金学的技術によって準備されました…次に、サンプルは、光学顕微鏡(OM、MeF4 Reichart-Jung)とエネルギーX線分散分光ユニット(EDS、Oxford microprobe)を備えた走査型電子顕微鏡(SEM、Leo 1450VP)によって組成分析のために調査されました。」 X線回折も使用されており、「図56:AlZn10Si8Mg自己硬化性合金のX線回折図」に示されています。
- 機械的特性試験: 機械的性能は、「引張試験とブリネル硬さ試験」によって評価されました。さらなる機械的特性評価には、「三点曲げ試験、シャルピー衝撃試験、ビッカース硬さ試験」が含まれていました。疲労特性は、「疲労試験機(TESTRONIC 100K RUMUL)」を使用して評価されました。
- 耐食性評価: 耐食性は、「ISO 9227規格に従って実施された塩水噴霧腐食試験」および「BS 11846、方法B [79] に準拠した粒界腐食試験」を使用して評価されました。
分析方法:
分析には以下が含まれていました。
- 定量的微細構造解析: 「二次デンドライトアーム間隔(SDAS)」の測定、および「面積(A)、真円度(R)、および等価直径(Deq.)」を使用したシリコン粒子の特性評価。
- 機械的特性の比較: 取得された機械的特性は、「テクシッドで現在使用されているT6熱処理されたA356合金、およびナックルコンポーネントに必要な特性と比較されました。」
- 腐食挙動評価: 目視検査、SEM分析、およびEDS分析を使用して腐食を評価し、粒界腐食試験では「腐食深さ」と「腐食後の重量減少」を測定しました。
- 統計分析: 疲労限度評価には階段法が使用されました。
研究対象と範囲:
研究は、「自己硬化性アルミニウム合金(Al-Zn-Si-Mg合金)」、具体的には「AlZn10Si8Mg」、「AlZn10Si8Mg1」、「AlZn10Si8Mg3」の組成に焦点を当てました。範囲は、「自動車用途」におけるこれらの合金の評価に限定され、特に「ナックルコンポーネント」に焦点を当てました。「Mg含有量」(0.3〜0.5 wt%から最大3 wt%)と「冷却速度」の影響が調査されました。
6. 主な研究成果:
主要研究成果:
- 微細構造の進化: 「鋳造状態と7日間の自然時効後の微細構造の主な違いは、二次デンドライトアーム間隔(SDAS)値に関するものです…7日間の自然時効後、微細構造は鋳造状態よりも微細に見えます。」 冷却速度が速いほど、微細構造が微細になり、SDAS値が低くなりました。「Mg含有量が増加するにつれて、より顕著なデンドライト形態の発達が観察されます。」
- 機械的特性: 「AlZn10Si8Mg自己硬化性アルミニウム合金の機械的特性は、T6熱処理されたA356(AlSi7Mg0.3)アルミニウム合金の機械的特性に匹敵します。」 ただし、「AlZn10Si8Mg合金の破断伸びA%は、わずかに異なり、そのような部品には許容できません。」 AlZn10Si8Mg1は、最高の曲げ応力を示しました。Mg含有量が1wt%を超えると(AlZn10Si8Mg3)、曲げ応力と衝撃エネルギーが低下しました。
- 耐食性: 「これらの結果は、研究対象の合金が機械的観点からA356合金の代替として有望であるように見えても、AlZn10Si8Mgには適切な耐食性がないことを示しています。」 ただし、「AlZn10Si8Mg1およびAlZn10Si8Mg3合金は、腐食環境に対してより耐性があるように見えます。」 AlZn10Si8Mg3は最高の粒界腐食抵抗を示し、「重量減少と浸透深さの両方で最低値を示しました。」
- 疲労特性: 「AlZn10Si8Mg1自己硬化性アルミニウム合金の疲労限度は約92 MPaであることが観察できます。この疲労限度値は、T6熱処理され、常設金型技術によって鋳造されたA356(AlSi7Mg0.3)合金の疲労限度値に匹敵します[3]。」
提示されたデータの分析:
微細構造画像、機械的特性グラフ、腐食試験結果を含む論文で提示されたデータは、自己硬化性Al-Zn-Si-Mg合金におけるMg含有量と冷却速度の変化に伴う機械的特性と耐食性のトレードオフを一貫して示しています。冷却速度が速いほど、一般的に微細構造が微細化され、機械的特性が向上します。Mg含有量を増やすと、最初は強度が向上しますが、高レベル(3wt%)では有害になる可能性があり、延性と衝撃抵抗に悪影響を与える一方で、耐食性が向上します。収縮空孔は、機械的性能、特に疲労寿命に影響を与える反復的な欠陥として特定されました。
図のリスト:
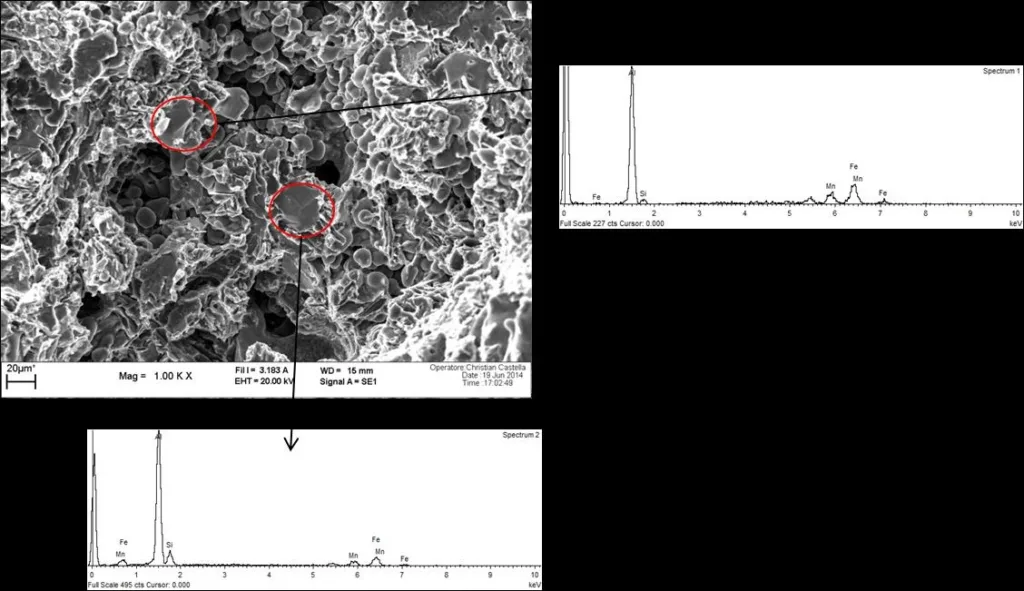
![Figure 25: Components realized with aluminum in a modern car [31].](https://castman.co.kr/wp-content/uploads/image_28-1.webp)
![Figure 27: Relative mass saving, absolute mass saving and market penetration
obtainable with aluminum alloys [32].](https://castman.co.kr/wp-content/uploads/image_30-1024x441.webp)
![Figure 28: Final result of the SLC project based on the "multi-material design" concept
[32].](https://castman.co.kr/wp-content/uploads/image_31-1024x459.webp)
![Figure 44: Car's door panel produced with UNIFONT-90 self-hardening aluminum
alloy [70].](https://castman.co.kr/wp-content/uploads/image_53.webp)
![Figure 49: Knuckle component [71].](https://castman.co.kr/wp-content/uploads/image_58-1024x492.webp)
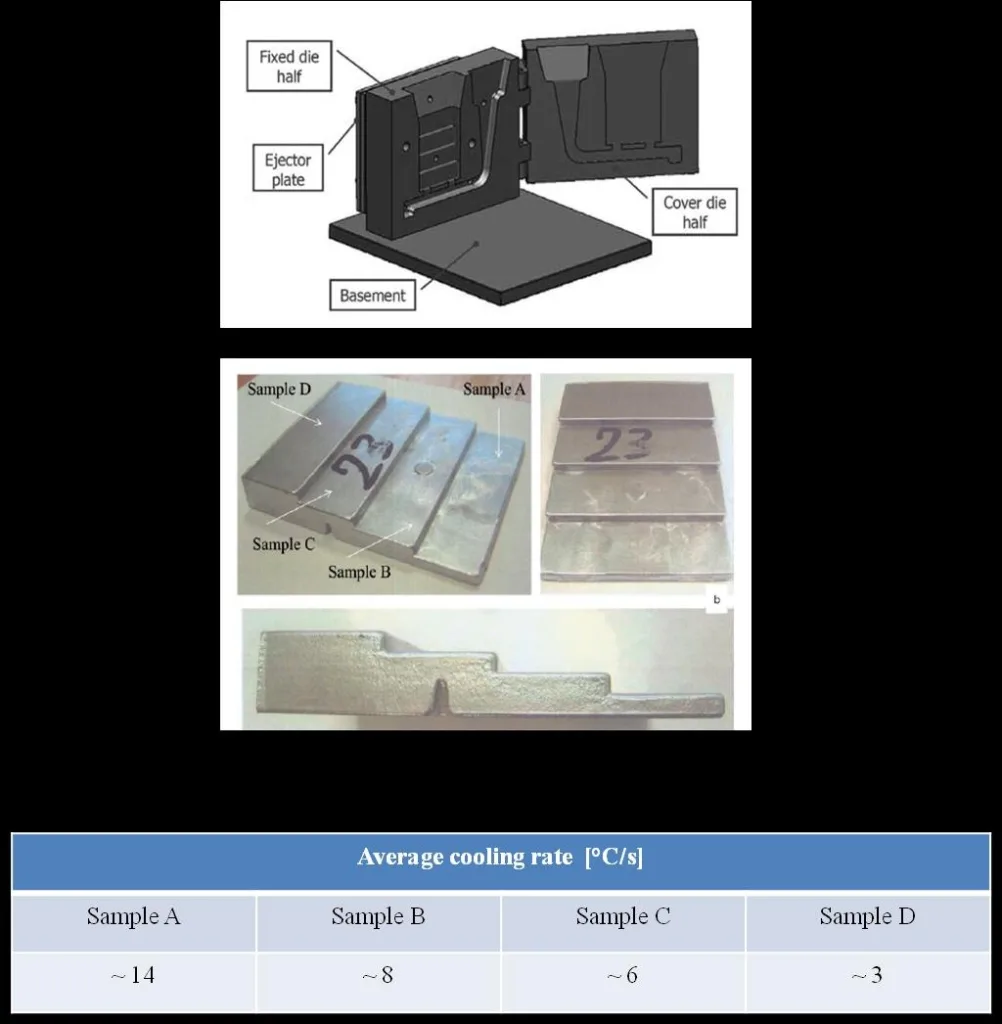
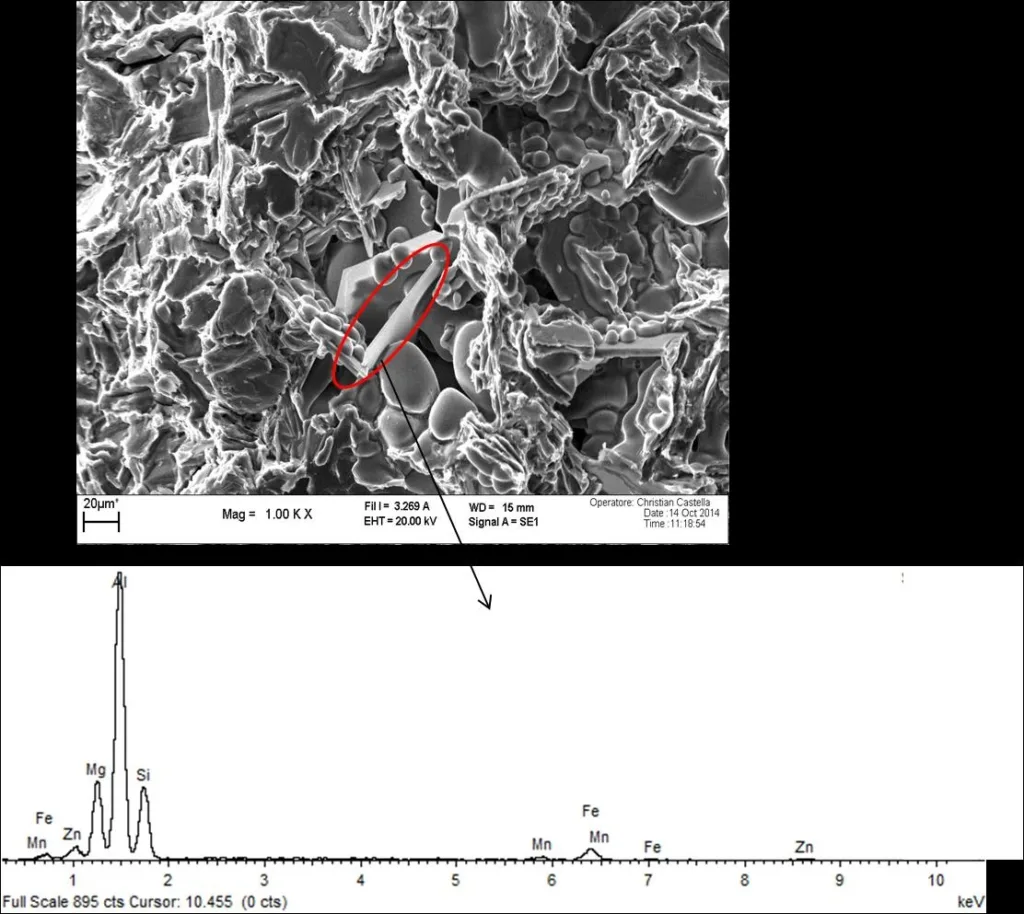
- 図 1: 微細構造: a) 中国語のスクリプト形態を持つ α-Al15(Fe,Mn)3Si2 相、b) β-Al5FeSi 板状晶 [7]
- 図 2: Al-Cu 合金の場合における溶体化処理、焼入れ、時効に関連するメカニズムの表現 [12]
- 図 3: 温度対時間線図: a) 従来型焼入れ、b) アップヒル焼入れ [15]
- 図 4: 転位バイパス析出物: a) フリーデル効果、b) オロワン機構。c) 強度対粒子半径図 [10]
- 図 5: 時効時間の対数関数としての強度と硬さ [16]
- 図 6: Al-Si-Cu 合金の析出シーケンス [16]
- 図 7: さまざまな時効温度における硬さ-引張強度-時間曲線 [16]
- 図 8: コックスによる鋳造欠陥の分類 [17]
- 図 9: キャンベルによる鋳造欠陥の分類 [18]
- 図 10: シーベルトの法則の図。
- 図 11: ガス空孔 (テクシッド・アルミニウム提供)。
- 図 12: 収縮空孔 (テクシッド・アルミニウム提供)。
- 図 13: 疲労亀裂の核生成サイトとして作用する収縮空孔 (テクシッド・アルミニウム提供)。
- 図 14: 酸化物粒子 (テクシッド・アルミニウム提供)。
- 図 15: ビフィルムの生成メカニズム [26]。
- 図 16: A354 アルミニウム合金で個別に特定された一部のビフィルム (テクシッド・アルミニウム提供)。
- 図 17: A354 アルミニウム合金で個別に特定された一部のビフィルム (テクシッド・アルミニウム提供)。
- 図 18: 一部のアルミニウム部品で明らかになったコールドシャット [19]。
- 図 19: アルミニウムサンプルの破断面で個別に特定された亀裂 (テクシッド・アルミニウム提供)。
- 図 20: β-Al5FeSi、α-Al15(FeMn)3Si2 を示す光学顕微鏡写真 [28]。
- 図 21: アルミニウムサンプルの破断面にある α-Al15(FeMn)3Si2 鉄金属間化合物 (テクシッド・アルミニウム提供)。
- 図 22: アルミニウムサンプルの破断面にある α-Al15(FeMn)3Si2 鉄金属間化合物。収縮空孔の近くで検出 (テクシッド・アルミニウム提供)。
- 図 23: 過去 40 年間の自動車におけるアルミニウム含有量の傾向 [30]。
- 図 24: 車の移動に対する抵抗力 [30]。
- 図 25: 最新の自動車でアルミニウムで実現された部品 [31]。
- 図 26: 自動車におけるアルミニウムの用途 [30]。
- 図 27: アルミニウム合金で得られる相対質量削減、絶対質量削減、市場浸透率 [32]。
- 図 28: 「マルチマテリアル設計」コンセプトに基づいた SLC プロジェクトの最終結果 [32]。
- 図 29: アルミニウム表面に形成される保護酸化膜の構造 [36]。
- 図 30: 25℃ における Al-H2O 系のポーベ図 [37]。
- 図 31: 純粋な Al および AA2024-T3 を 0.1M NaCl に 7 日間曝露した場合の分極曲線。1mV/s-1 で収集 [37]。
- 図 32: アルミニウムの電解液電位に対する一部の合金元素の影響。電位は、高純度二元合金溶体化熱処理および焼入れの場合です。データは、25℃ に維持された 53 g/l NaCl + 3 g/l H2O2 の溶液を使用して取得されました [2]。
- 図 33: 99.999% アルミニウムの半球状ピット。E¼1.84 VSHE で 1.0M NaNO3 溶液中 [39]。
- 図 34: 合金-溶液界面と AlOOH/Al2O3 層内の SiO2 粒子の存在を示す概略図 [40]。
- 図 35: 2xxx アルミニウム合金の粒界領域の概略図 [38]。
- 図 36: 7055 アルミニウム合金の粒界領域の概略図 [47]。
- 図 37: 7075-T6 アルミニウム合金試験片の表面の光学顕微鏡写真。脱気された 0.5M NaCl 溶液、-685mVSCE に曝露: (a) 受領したままの試験片、(b)、(c)、(d) 粒径がそれぞれ 40、130、290 µm の試験片 [48]。
- 図 38: SCC を説明するために現在までに開発されたいくつかの理論の概略図: a) 陽極溶解、b) 水素誘起割れ、c) 不動態皮膜の破壊 [2]。
- 図 39: SCC に対する感受性の程度を変えるために処理後の 5356-H12 合金の微細構造。a) 冷間圧延 20%。耐性が高い。b) 冷間圧延 20%、その後 100℃ で 1 年間加熱。感受性が高い。c) 冷間圧延 20%、その後 150℃ で 1 回加熱。わずかに感受性がある。d) 冷間圧延 20%、その後 205℃ で 1 回加熱。耐性が高い [2]。
- 図 40: Al–Zn–Mg–Cu–Zr および Al–Zn–Mg–Cu–Zr–Er–Cr 合金の 3.5 wt% NaCl 溶液中の亀裂伝播速度 (v) 対亀裂先端応力拡大係数 (KI) [45]。
- 図 41: さまざまな化学溶液による 1100-H14 合金の腐食に対する pH の影響 [2]。
- 図 42: 硫酸中の 1100 アルミニウム合金の腐食に対する温度の影響 [2]。
- 図 43: 押出 AA6060 アルミニウム合金片の陽極酸化皮膜の SEM 画像 [38]。
- 図 44: UNIFONT-90 自己硬化性アルミニウム合金で製造された自動車のドアパネル [70]。
- 図 45: UNIFONT-90 自己硬化性アルミニウム合金で実現されたロボット用シャーシ [70]。
- 図 46: UNIFONT-94 自己硬化性アルミニウム合金で製造された振動ダンパー用サポート [70]。
- 図 47: UNIFONT-94 自己硬化性アルミニウム合金で製造された飛行機の座席テーブル用サポート [70]。
- 図 48: テクシッドが製造したナックルコンポーネント (テクシッド・アルミニウム提供)。
- 図 49: ナックルコンポーネント [71]。
- 図 50: 図 48 のナックルコンポーネントに使用される熱処理のコスト要素と、400,000 個のナックルコンポーネントに使用される熱処理の年間製造コスト。
- 図 51: AlZn10Si8Mg 自己硬化性アルミニウム合金の微細構造: a) 鋳造状態 (100 倍)、b) 7 日間の自然時効後 (100 倍)、c) 鋳造状態 (500 倍)、d) 7 日間の自然時効後 (500 倍)。
- 図 52: アルミニウム-亜鉛二元系状態図 [72]。
- 図 53: 鋳造状態における AlZn10Si8Mg 自己硬化性アルミニウム合金の SEM 顕微鏡写真と EDS 分析結果。
- 図 54: 7 日間の自然時効後の AlZn10Si8Mg 自己硬化性アルミニウム合金の SEM 顕微鏡写真と EDS 分析結果。
- 図 55: さまざまな量の Mn を含む Al-Si-Fe 系の部分状態図: a) 0 wt%、b) 0.1 wt%、c) 0.2 wt%、d) 0.3 wt% [73]。
- 図 56: AlZn10Si8Mg 自己硬化性合金の X 線回折図。
- 図 57: 引張試験結果: a) 極限引張強度、b) 耐力、c) 破断伸び (A%)。
- 図 58: ブリネル硬さ試験結果。
- 図 59: 塩水噴霧腐食試験中にバッチ内部にサンプルを配置した位置。
- 図 60: 塩水噴霧腐食試験後のサンプル写真。
- 図 61: 塩水噴霧腐食試験に供されたサンプルの写真と、EDS 分析によって得られた変質層の組成。
- 図 62: ステップ鋳造形状: a) 一般図、b) 側面図を使用した分析に使用される形状、c) 熱電対で測定された平均冷却速度。
- 図 63: 冷却速度の関数としての AlZn10Si8Mg 自己硬化性アルミニウム合金の OM 顕微鏡写真と SDAS 値 [µm]。
- 図 64: 冷却速度の関数としての AlZn10Si8Mg1 自己硬化性アルミニウム合金の OM 顕微鏡写真と SDAS 値 [µm]。
- 図 65: 冷却速度の関数としての AlZn10Si8Mg3 自己硬化性アルミニウム合金の OM 顕微鏡写真と SDAS 値 [µm]。
- 図 66: すべての検討対象合金について、ゾーン C の微細構造を比較した OM 顕微鏡写真。
- 図 67: 異なる冷却速度における AlZn10Si8Mg 自己硬化性合金の OM 顕微鏡写真: a) サンプル D (3 °C/s)、b) サンプル C (6°C/s)、c) サンプル B (8°C/s)、d) サンプル A (14°C/s) (500 倍)。
- 図 68: 異なる冷却速度における AlZn10Si8Mg1 自己硬化性合金の OM 顕微鏡写真: a) サンプル D (3 °C/s)、b) サンプル C (6°C/s)、c) サンプル B (8°C/s)、d) サンプル A (14°C/s) (500 倍)。
- 図 69: 異なる冷却速度における AlZn10Si8Mg3 自己硬化性合金の OM 顕微鏡写真: a) サンプル D (3 °C/s)、b) サンプル C (6°C/s)、c) サンプル B (8°C/s)、d) サンプル A (14°C/s) (500 倍)。
- 図 70: Mg wt% と冷却速度が異なる場合のシリコン粒子の逆面積。
- 図 71: Mg wt% と冷却速度が異なる場合の共晶シリコン粒子の真円度。
- 図 72: Mg wt% と冷却速度が異なる場合のシリコン粒子の等価直径。
- 図 73: 合金の SDAS 値。
- 図 74: a) ゾーン B およびゾーン D から抽出された AlZn10Si8Mg、AlZn10Si8Mg1、および AlZn10Si8Mg3 合金のサンプルの微細構造を示す OM 顕微鏡写真、b) EDS 分析結果。
- 図 75: 研究対象合金の X 線スペクトル。
- 図 76: 寸法: a) Mg2Si および b) MgZn2 硬化析出物。シェラーの式に従って計算。
- 図 77: 調査対象合金の曲げ応力: a) 7 日間の自然時効後、b) 10 か月間の自然時効後。
- 図 78: 調査対象合金の曲げひずみ: a) 7 日間の自然時効後、b) 10 か月間の自然時効後。
- 図 79: シャルピー試験結果: a) 7 日間の自然時効後、b) 10 か月間の自然時効後。
- 図 80: ビッカース硬さ値: a) 7 日間の自然時効後、b) 10 か月間の自然時効後。
- 図 81: 破断面の SEM 顕微鏡写真。
- 図 82: 破断面の詳細を示す SEM 画像: a) 収縮空孔、b) 酸化物粒子。
- 図 83: 塩水噴霧腐食試験後のサンプル調査。
- 図 84: AlZn10Si8Mg サンプルの外部表面で個別に特定された変質層の化学組成。EDS 分析によって取得。
- 図 85: シャルピー衝撃試験結果: a) 塩水噴霧腐食試験前、b) 塩水噴霧腐食試験後。
- 図 86: 光学顕微鏡写真 a)、b) および SEM 顕微鏡写真と EDS 分析結果 c) 腐食サンプルの横断面。共晶 Al マトリックスに対して局所的なカソードとして作用する Si 粒子を示す。
- 図 87: SEM 顕微鏡写真と EDS 分析結果。腐食サンプルの横断面。共晶 Al マトリックスに対して局所的なカソードとして作用する Fe 金属間化合物を示す。
- 図 88: SEM 画像 a) および FESEM 画像 b) Al–Fe–Si–Mg 化合物。
- 図 89: a) 重量減少および b) 浸透深さ。粒界腐食試験後に測定。
- 図 90: 粒界腐食試験に供されたサンプルの外部表面で実施された分析の EDS 結果。
- 図 91: 三点曲げ試験、曲げ応力の結果: a) 粒界腐食試験前、b) 粒界腐食試験後。
- 図 92: 三点曲げ試験、曲げひずみの結果: a) 粒界腐食試験前、b) 粒界腐食試験後。
- 図 93: シャルピー試験結果: a) 粒界腐食試験前、b) 粒界腐食試験後。
- 図 94: 疲労試験結果: a) S-N 曲線、b) 階段法によって得られた生存確率。
- 図 95: 亀裂開始サイトとして作用した収縮空孔を示す SEM 顕微鏡写真。
- 図 96: Fe-Mn 金属間化合物を示す SEM 顕微鏡写真。収縮空孔の発達の原因の 1 つであり、EDS 分析結果。
7. 結論:
主な調査結果の要約:
この博士論文は、自己硬化性Al-Zn-Si-Mg合金が、特にナックルサスペンションのような部品において、T6熱処理されたA356合金の実行可能な代替品となることを結論付けました。「得られた機械的特性は、T6熱処理されたA356(AlSi7Mg0.3)アルミニウム合金の機械的特性と完全に匹敵し、ナックルコンポーネントに必要な特性を満たしています。」 特に、約14℃/秒の冷却速度で鋳造されたAlZn10Si8Mg1合金は、機械的特性、耐食性、および疲労限度の有望なバランスを示し、「T6熱処理され、常設金型技術によって鋳造されたA356(AlSi7Mg0.3)合金の疲労限度値に匹敵します[3]。」 Mg含有量を最大3wt%(AlZn10Si8Mg3)まで増加させると、粒界腐食抵抗がさらに向上し、研究対象の合金の中で最も耐食性の高い合金となりました。ただし、Mg含有量が多いほど、延性と衝撃エネルギーに悪影響を与える可能性があります。これらの合金の大きな利点は、熱処理を排除できることであり、製造コストとエネルギー消費の削減につながる可能性があります。
研究の学術的意義:
この研究は、自己硬化性アルミニウム合金の学術的理解に貢献し、Mg含有量と冷却速度がその微細構造、機械的挙動、および腐食特性に及ぼす影響に関する詳細な洞察を提供します。この研究は、これらの合金における析出メカニズムと、観察された特性との相関関係を解明します。調査結果は、一般的な自己硬化性アルミニウム合金の合金設計および最適化戦略にとって貴重です。
実践的な意義:
この研究の実践的な意義は、自動車産業にとって重要です。この研究は、自己硬化性Al-Zn-Si-Mg合金、特にAlZn10Si8Mg1を、ナックルサスペンションのような自動車部品において、熱処理されたA356合金の直接的な代替品として使用できる可能性を示しています。この代替により、「熱処理プラントの実現なしに実現されるコスト削減[€] 2,170,000」と、熱処理プロセスを排除することによるエネルギー消費の削減の可能性が提供されます。匹敵する疲労限度は、これらの合金の実用的な適用性をさらに裏付けています。
研究の限界と今後の研究分野:
特定された主な限界は、AlZn10Si8Mg合金の「破断伸び(A%)」であり、「ナックルサスペンションコンポーネントの要件を満たしていません。」 今後の研究では、この限界に対処し、これらの合金の延性を向上させることが推奨されます。論文では、今後の研究の方向性として、以下も示唆しています。
- 「自動車産業で要求される基準に到達するために、破断伸びの値を増加させること。」
- 「さらに、最も有望な合金の疲労抵抗は高温で評価されます。」
- 自動車用途向けの自己硬化性アルミニウム合金の全体的な性能を向上させるための、合金組成と加工パラメータのさらなる最適化。
8. 参考文献:
- [1] Atlante metallografico delle leghe di alluminio da fonderia, Ettore di Russo, Edimet.
- [2] Corrosion of aluminum and aluminum alloys, edited by J.R.Davis, The materials information society.
- [3] ASM handbook, volume 2 edited by Joseph R. Davis.
- [4]E.A. Starke Jr.; Aluminum alloys: Alloy, Heat Treatment, and Temper Designation; Encyclopedia of Materials: Science and Technology (Second Edition), 2001, Pages 106-107.
- [5] H.A. Elhadari, H.A. Patel, D.L. Chena,W. Kasprzak; Tensile and fatigue properties of a cast aluminum alloy with Ti, Zr and V additions; Materials Science and Engineering A 528 (2011) 8128–8138.
- [6] R. S. Rana, Rajesh Purohit, and S Das; Reviews on the Influences of Alloying elements on the Microstructure and Mechanical Properties of Aluminum; International Journal of Scientific and Research Publications, Volume 2, Issue 6, June 2012 .
- [7] G.Timelli, E.Fiorese, Metodi di neutralizzazione del Fe in leghe Al-Si da fonderia, La Metallurgia Italiana n.3 Marzo (2011) 9-23.
- [8] GUO Hong-min, YANG Xiang-jie; Preparation of semi-solid slurry containing fine and globular particles for wrought aluminum alloy 2024; Trans. Nonferrous Met. SOC. China 17(2007) 799-804.
- [9] D.G. Eskin, Suyitno, L. Katgerman; Mechanical properties in the semi-solid state and hot tearing of aluminium alloys; Progress in Materials Science 49 (2004) 629–711.
- [10] Emma Sjölander, Salem Seifeddine; The heat treatment of Al–Si–Cu–Mg casting alloys; Journal of Materials Processing Technology 210 (2010) 1249–1259.
- [11] M.F. Ibrahim, A.M. Samuel, F.H. Samuel, A preliminary study on optimizing the heat treatment of high strength Al-Cu-Mg-Zn alloys, Materials and Design 57 (2014) 342–350.
- [12] Higgins R.A., Engineering metallurgy, Second Edition, ELBS, ISBN 034018468X, (1986).
- [13] J.S. Robinson, D.A. Tanner, C.E. Truman, A.M. Paradowska, R.C.Wimpory; The influence of quench sensitivity on residual stresses in the aluminium alloys 7010 and 7075; Materials Characterization 65 (2012) 73 – 8 5.
- [14] Jasim M. Salman, Shaymaa Abbas Abd Alsada and Khadim F. Al-Sultani; Improvement Properties of 7075-T6 Aluminum Alloy by Quenching in 30% Polyethylene Glycol and Addition 0.1%B; Research Journal of Material Sciences Vol. 1(6), 12-17, July (2013).
- [15] Diana A. Lados, Diran Apelian, Libo Wang; Minimization of residual stress in heat-treated Al–Si–Mg cast alloys using uphill quenching: Mechanisms and effects on static and dynamic properties; Materials Science and Engineering A 527 (2010) 3159–3165.
- [16] William D. Callister, Jr.; Fundamentals of Materials Science and Engineering; Fifth edition.
- [17] D.L. Cocks, A proposed simple qualitative classification for die-casting defects, Proc. Die-Casting Conference, Montreaux (1996), p. 19/1.
- [18] J. Campbell, R.A. Harding, Casting Technology, in TALAT 2.0 cd-rom, EEA, Brussels (2000).
- [19] Manuale della difettologia nei getti pressocolati, E.Gariboldi – F.Bonollo – P.Parona, Associazione Italiana di Metallurgia.
- [20] S.B. Ghanti, E.A.Druschitz, A.P. Druschitz, J.A.Griffin; The effects of soilidification underpressure on the porosity and mechanical properties of A206-T6 cast aluminum alloy; Paper 11-048 page 1-8 AFS proceedings 2011 America Foundry Society Schaumburg, IL USA.
- [21] H.R. Ammar, A.M. Samuel, F.H. Samuel; Porosity and the fatigue behavior of hypoeutectic and hypereutectic aluminum–silicon casting alloys; International Journal of Fatigue 30 (2008) 1024–1035.
- [22] Bita Ghaffari, George Mozurkewich, Larry A. Godlewski, JacobW. Zindel; Ultrasonic characterization of shrinkage microporosity in aluminum castings; Ultrasonics 41 (2004) 699–707.
- [23] C. Tian, J. Law, J. van der Touw, M. Murray, J.-Y. Yao, D. Graham, D. St. John; Effect of melt cleanliness on the formation of porosity defects in automotive aluminium high pressure die castings; Journal of Materials Processing Technology 122 (2002) 82–93.
- [24] O. Majidi, S.G. Shabestari, M.R. Aboutalebi; Study of fluxing temperature in molten aluminum refining process; Journal of Materials Processing Technology 182 (2007) 450–455.
- [25] Yun Wang, Hu-Tian Li, Zhongyun Fan; Oxidation of Aluminium Alloy Melts and Inoculation by Oxide Particles; Trans Indian Inst Met DOI 10.1007/s12666-012-0194-x.
- [26] J.Campbell, Castings, Butterworth, Oxford, 1991.
- [27] D.Dispinar, J.Campbell, International Journal of cast metal research 17,2004, 280-286.
- [28] Salem Seifeddine, Torsten Sjögren and Ingvar L Svensson; Variations in microstructure and mechanical properties of cast aluminum EN AC 43100 alloy; Metallurgical Science and Technology 12-22.
- [29] J. Hirsch, T. Al-Samman; Superior light metals by texture engineering: Optimized aluminum and magnesium alloys for automotive applications; Acta Materialia 61 (2013) 818–843.
- [30] European Aluminium Association.
- [31] Ju¨rgen Hirsch; Aluminium in Innovative Light-Weight Car Design; Materials Transactions, Vol. 52, No. 5 (2011) pp. 818 to 824.
- [32] Jürgen HIRSCH; Recent development in aluminium for automotive applications; Trans. Nonferrous Met. Soc. China 24(2014) 1995−2002.
- [33]J.Hirsch; Aluminium in innovative light-weight car design; Proc Innovative Development for Lightweight Vehicle Structures; Wolfsburg, Germany: VW, 2009: 101.
- [34] SLC Super Light Car Project [EB/OL]. http://www.superlightcar.com.
- [35] K. Shimizu, R.C. Furneaux, G.E. Thompson, G.C. Wood, A. Gotoh and K. Kobayashi; On the nature of “easy paths” for the diffusion of oxygen in thermal oxide films on aluminium; Oxidation of Metals vol.35, Nos.5/6 pp.427-439, 1991.
- [36] J.R. Davis; Corrosion of aluminum and aluminum alloys; Edited by J.R.Davis ASM International.
- [37] N. L. Sukiman, X. Zhou, N. Birbilis, A.E. Hughes, J. M. C. Mol, S. J. Garcia, X. Zhou and G. E. Thompson; Aluminium Alloys - New Trends in Fabrication and Applications; Edited by Zaki Ahmad, Intech.
- [38] G. M. Scamans, N. Birbilis, R. G. Buchheit; Corrosion of Aluminum and its Alloys; 2010 Elsevier B.V..
- [39] M.G. Alvarez, J.R. Galvele; Pitting Corrosion; Shreir's Corrosion Volume 2, 2010, Pages 772-800.
- [40] M.A. Pech-Canul, M.I. Pech-Canul, P. Bartolo-Pérez, M. Echeverría; The role of silicon alloying addition on the pitting corrosion resistanceof an Al-12 wt.%Si alloy; Electrochimica Acta 140 (2014) 258–265.
- [41] S. Jain; Corrosion and protection of heterogeneous cast Al–Si (356) and Al–Si–Cu–Fe (380) alloys by chromate and cerium inhibitors; The Ohio State University, Ohio, USA, 2006.
- [42] K. Nisancioglu; Electrochemical behavior of aluminum-base intermetallics containing iron; J. Electrochem. Soc. 137 (1990) 69–77.
- [43] K.A. Yasakau, M.L. Zheludkevich, S.V. Lamaka, M.G.S. Ferreira; Role of intermetallic phases in localized corrosion of AA5083; Electrochim. Acta 52 (2007) 7651–7659.
- [44] R. Arrabal, B. Mingo, A. Pardo, M. Mohedano, E. Matykina, I. Rodriguez; Pitting corrosion of rheocast A356 aluminium alloy in 3.5 wt.% NaCl solution; Corrosion Science 73 (2013) 342–355.
- [45] H.C. Fang, H. Chao, K.H. Chen; Effect of recrystallization on intergranular fracture and corrosion of Al–Zn–Mg–Cu–Zr alloy; Journal of Alloys and Compounds 622 (2015) 166–173.
- [46] Fengxuan Song, Xinming Zhang, Shengdan Liu, Qi Tan, Dongfeng Li; The effect of quench rate and overageing temper on the corrosion behaviour of AA7050; Corrosion Science xxx (2013).
- [47] Lanping Huang, Kanghua Chen, Song Li; Influence of grain-boundary pre-precipitation and corrosion characteristics of inter-granular phases on corrosion behaviors of an Al–Zn–Mg–Cu alloy; Materials Science and Engineering B 177 (2012) 862– 868.
- [48] Amjad Saleh El-Amoush; Intergranular corrosion behavior of the 7075-T6 aluminum alloy under different annealing conditions; Materials Chemistry and Physics 126 (2011) 607-613.
- [49] W.J. Liang, P.A. Rometsch, L.F. Cao, N. Birbilis; General aspects related to the corrosion of 6xxx series aluminium alloys:Exploring the influence of Mg/Si ratio and Cu; Corrosion Science 76 (2013) 119–128.
- [50] Starink M.J., Li X M.; A model for electrical conductivity of peak-aged and overaged Al−Zn−Mg−Cu alloys; [J]. Metallurgical and Materials Transactions A, 2003, 34(4): 899−911.
- [51] Chen Song-yi, Chwn Kang-hua, Peng Guo-sheng, Liang Xin, Chen Xue-hai; Effect of quenching rate on microstructure and stress corrosion cracking of 7085 aluminum alloy; [J]. Transactions of Nonferrous Metals Society of China, 2012, 22(1): 47−52.
- [52] Knight S. P., Birbilis N., Muddle B. C., Trueman A. R., Lynch S. P.; Correlations between intergranular stress corrosion cracking, grain-boundary microchemistry, and grain-boundary electrochemistry for Al−Zn−Mg−Cu alloys; [J]. Corrosion Science, 2010, 52(12): 4073−4080.
- [53] Andreatta F., Terryn H., de Wit J. H. W.; Effect of solution heat treatment on galvanic coupling between intermetallics and matrix in AA7075-T6; [J]. Corrosion Science, 2003, 45(8): 1733−1746.
- [54] Zhang Ping, Li Qi, Zhao Jun-jun, Zeng Qing-qiang.; Analysis of secondary phases and measurement of volta potential of 7A52aluminum alloy; [J]. The Chinese Journal of Nonferrous Metals, 2011, 21(6): 1252−1257.
- [55] Venugopal A., Panda R., Manwatkar S., Sreekumar K., Rama Krishna L., Sundararajan G.; Effect of micro arc oxidation treatment on localized corrosion behaviour of AA7075 aluminum alloy in 3.5% NaCl solution; [J]. Transactions of Nonferrous Metals Society of China, 2012, 22(3): 700−710.
- [56] Huan She, Wei Chu, Da Shu, Jun Wang, Bao-de Sun; Effects of silicon content on microstructure and stress corrosion cracking resistance of 7050 aluminum alloy; Trans. Nonferrous Met. Soc. China 24(2014) 2307−2313.
- [57] S. Geng, S. Joshi, W. Pinc, W.G. Fahrenholtz, M.J. O’Keefe, T.J. O’Keefe, P. Yu; Influence of processing parameters on cerium based conversion coatings; in: Proc. Tri-Service Corrosion Conference, Denver, CO, NACE International, 2007,p. 10.
- [58] B. Valdez, S. Kiyota, M. Stoytcheva, R. Zlatev, J.M. Bastidas; Cerium-based conversion coatings to improve the corrosion resistance of aluminium alloy 6061-T6; Corrosion Science 87 (2014) 141–149.
- [59] Peter Plagemann, Joerg Weise, Anja Zockoll; Zinc–magnesium-pigment rich coatings for corrosion protection of aluminum alloys; Progress in Organic Coatings 76 (2013) 616– 625.
- [60] Du Nan, Wang Shuai-xing, Zhao Qing, Shao Zhi-song; Effects of boric acid on microstructure and corrosion resistance of boric/sulfuric acid anodic film on 7050 aluminum alloy; Trans. Nonferrous Met. Soc. China 22(2012) 1655-1660.
- [61] J. Singh-Beemat, J.O. Iroh; Effect of clay on the corrosion inhibition and dynamic mechanical properties of epoxy ester–polyurea–polysiloxane hybrid coatings; Polym. Eng. Sci. (2012).
- [62] J. Singh-Beemat, J.O. Iroh; Characterization of corrosion resistant clay/epoxy ester composite coatings and thin films; Progress in Organic Coatings 74 (2012) 173–180.
- [63] Jaspreet Singh-Beemat, Jude O. Iroh, Linqian Feng; Mechanism of corrosion protection of aluminum alloy substrate byhybrid polymer nanocomposite coatings; Progress in Organic Coatings 76 (2013) 1576– 1580.
- [64] E. Tillová, E. Ďuriníková, M. Chalupová; Structural analysis of secondary AlZn10Si8Mg cast alloy; Acta Metallurgica Slovaca, Vol. 17, 2011, No. 1, p. 4-10.
- [65] E. Tillová, E. Ďuriníková, M. Chalupová; Characterization of phases in secondary AlZn10Si8Mg cast alloy; Materials Engineering - Materiálové inžinierstvo 18 (2011) 1-7.
- [66] http://www.dietermann-guss.de/_pdf-Dateien/IN%20FORM_01_12%20eng.pdf.
- [67] M.Rosso, I.Peter, C.Castella , R.Molina; Investigation on AlZn10Si8Mg alloys for automotive application; Metallurgical Science and Technology Vol. 31-1 - Ed. 2013.
- [68] M.Rosso, I.Peter, C.Castella , R.Molina; Properties of AlZn10Si8Mg Alloys for High Performances Application; Light metals 2014 p.213-218.
- [69] I.Peter, M.Rosso, C.Castella, R.Molina; Self-hardening alloys for automotive application; Materials Science Forum Vols. 794-796 (2014) pp 1221-1226.
- [70] http://www.rheinfelden-alloys.eu/.
- [71] C. Y. Song, J. Lee; Reliability-based design optimization of knuckle component using conservative method of moving least squares meta-models; Probabilistic Engineering Mechanics 26 (2011) 364–379.
- [72] J. L. Murray; The Al-Zn (Aluminum-Zinc) System; Bulletin of Alloy Phase Diagrams Vol. 4 No. 1 1983.
- [73] G.Timelli, E.Fiorese; Metodi di neutralizzazione del Fe in leghe Al-Si da fonderia; La Metallurgia Italiana n.3 Marzo 2011 9-23.
- [74] C. Mascré, Fonderie, 108 (1955), 4330-4334.
- [75] R. Arrabal, B. Mingo, A. Pardo, M. Mohedano, E. Matykina, I. Rodriguez, Pitting corrosion of rheocast A356 aluminium alloy in 3.5 wt.% NaCl solution, Corrosion Science 73 (2013) 342–355.
- [76] Kiryl A. Yasakau, Mikhail L. Zheludkevich ,Sviatlana V. Lamaka, Mario G.S. Ferreira; Role of intermetallic phases in localized corrosion of AA5083; Electrochimica Acta 52 (2007) 7651–7659.
- [77] V.A. Hosseini, S.G. Shabestari, R. Gholizadeh; Study on the effect of cooling rate on the solidification parameters, microstructure, and mechanical properties of LM13 alloy using cooling curve thermal analysis tecjnique; Materials and Design 50 (2013) 7–14.
- [78] Deepak Singla1, S.R. Mediratta; Evaluation of mechanical properties of Al 7075-fly ash composite material; International Journal of Innovative Research in Science, Engineering and Technology Vol. 2, Issue 4, April 201.
- [79] Determination of resistance to IGC of solution heat-treatable aluminium alloys, Standard BS11846:1995, Brithish Standards Institution (1995).
9. 著作権:
- この資料は "Christian Castella" 氏の論文: "自動車用途向け自己硬化性アルミニウム合金 (Self hardening aluminum alloys for automotive applications)" に基づいています。
- 論文ソース: [DOI URL]
この資料は上記の論文に基づいて要約されたものであり、商業目的での無断使用は禁止されています。
Copyright © 2025 CASTMAN. All rights reserved.