この論文の要約は、['Ultra Large Castings to Produce Low Cost Aluminum Vehicle Structures']という論文に基づいており、['SAE TECHNICAL PAPER SERIES']で発表されました。
1. 概要:
- タイトル: 超大型鋳造による低コストアルミニウム車体構造の製造 (Ultra Large Castings to Produce Low Cost Aluminum Vehicle Structures)
- 著者: T. N. Meyer, M. J. Kinosz, E. M. Bradac, M. Mbaye, J. T. Burg, M. A. Klingensmith
- 発表年: 1999年
- 掲載ジャーナル/学会: SAE TECHNICAL PAPER SERIES、Government/Industry Meetingにて発表、ワシントンD.C.、1999年4月26-28日
- キーワード: 超大型鋳造 (Ultra Large Castings)、アルミニウム車体構造 (Aluminum Vehicle Structures)、低コスト (Low Cost)、ダイカスト (Die Casting)、金型鋳造 (Metal Mold)、多点射出 (Multiport Injection)、垂直鋳造プロセス (Vertical Casting Process)、自動車 (Automotive)、軽量化 (Lightweighting)
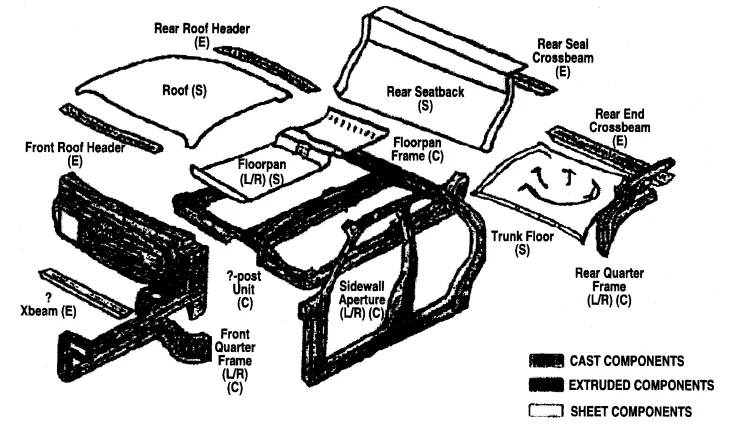
2. 研究背景:
研究トピックの背景:
自動車産業は、ますます厳しくなる環境排出基準を満たし、燃費効率を向上させるために、継続的に車両重量の削減に努めています。アルミニウムは優れた軽量化の可能性を提供しますが、地上輸送車両(自動車、スポーツ用多目的車/小型トラック/バン、バス、大型トラック)への普及は、鋼鉄と比較してコストが高いことが障壁となっています。このコストは、アルミニウム製品の基本的な材料コスト(例:シート、押出成形品、または鋳造品)と、その後の製造および組立コスト(例:成形、接合、仕上げ工程)の両方に起因します。
既存研究の現状:
フロアパンフレームなどの車体構造の従来の製造方法は、複数の成形された鋼鉄スタンピングを抵抗スポット溶接で組み立てることを含みます。アルコアの既存のアルミニウム真空ダイカスト(AVDC)プロセス(米国特許第5,370,171号)は、高品質の薄肉鋳造品を製造できますが、超大型部品に関連するコストと複雑さに対処するためには、さらなる進歩が必要です。航空宇宙分野で利用されているレベルポア鋳造プロセスは、複雑な形状には不向きであり、大型の薄肉部品からのランナー除去に課題があります。
研究の必要性:
軽量アルミニウム構造のコスト障壁を克服し、自動車分野での大量生産(例:年間100,000ユニット)を促進するためには、低コストで超大型の薄肉部品を製造できる革新的な鋳造プロセスが不可欠です。この研究は、従来の鋼鉄アセンブリと軽量アルミニウム代替品との間のコストギャップを埋めることを目的としています。
3. 研究目的と研究課題:
研究目的:
主な研究目的は、車体構造用の超大型薄肉アルミニウム部品を製造するための新しい鋳造プロセスを開発し、実証することです。このプロセスは、部品点数と組立コストの両方を大幅に削減し、それによって軽量輸送車両構造の全体的なコストを削減することを目的としています。
主要な研究:
主要な研究は、低圧、熱間チャンバー、多点射出垂直鋳造プロセスの開発と実装に焦点を当てています。研究には以下も含まれます。
- サイズと幾何学的複雑さを代表する実証部品の選定。
- 経済性とプロセス要件に適合する熱間チャンバー射出システムの開発。
- 高品質の鋳造のための構造的および鋳造プロセス要件を満たす部品設計、金属射出ポートの位置と初期射出条件の最適化。
- 射出システムへの溶融金属供給システムの確立。
- すべてのシステムコンポーネントの仕様決定、製造、設置、およびデバッグ。
研究仮説:
明示的に仮説として述べられていませんが、研究は以下の前提で進められています。
- 開発されたプロセスで製造された超大型鋳造品は、アルミニウム車体構造のコストを大幅に削減できる。
- 低圧、熱間チャンバー、多点射出垂直鋳造プロセスは、そのような大型の薄肉アルミニウム部品を製造するための実行可能で効率的な方法である。
4. 研究方法
研究デザイン:
この研究では、開発および実証的な研究デザインを採用しています。新しい超大型鋳造システムの概念化、設計、製造、およびテストが含まれます。クライスラーミニバンリフトゲートインナーパネルは、プロセスを評価するための実証部品として選択されました。
データ収集方法:
データ収集方法には以下が含まれます。
- コンピュータシミュレーション: 構造性能評価のための有限要素解析(FEA)と、プロセスパラメータと部品設計を最適化するための鋳造シミュレーション(充填と凝固)。
- システム開発とテスト: 開発された鋳造システムの実装とテスト。コンポーネントの製造、システム統合、およびプロセスシェイクダウンが含まれます。
- コスト分析: 超大型鋳造アプローチの費用対効果を評価するための生産施設とプロセスの経済評価。
分析方法:
- 有限要素解析(FEA): 鋳造アルミニウムインナーパネルの構造性能を分析し、従来の鋼鉄アセンブリと比較するために使用。
- 鋳造シミュレーション: ガス閉じ込め、多孔質を回避し、指向性凝固を確実にするために、射出ポートの位置、金型温度制御、冷却要件など、鋳造プロセスを最適化するために使用。
- 経済分析: 鋳造アルミニウム部品の製造コストを見積もり、既存の鋼鉄アセンブリのコストと比較するために実施。
研究対象と範囲:
研究は、アルミニウム車体構造用の超大型鋳造プロセスの開発に焦点を当てています。範囲は、特定の自動車部品であるダイムラー・クライスラーミニバンリフトゲートインナーパネルを使用したプロセスの実証に限定されています。システムは、フロアパンフレームやサイドウォール開口部構造に代表される大型自動車部品を製造できるように設計されています。
5. 主な研究結果:
主要な研究結果:
研究は、超大型薄肉部品を製造するための低圧、金型鋳造、多点射出垂直鋳造プロセスを開発することに成功しました。アルコアのテクノロジーセンターに専用の鋳造システムが設計および製造され、長さ3m、幅1.7m、高さ0.4mまでの部品を製造できます。クライスラーミニバンリフトゲートインナーパネル(11部品の鋼鉄アセンブリ)は、プロセス実証のためにワンピースのアルミニウム鋳造品として再設計されました(図2b)。FEAは、鋳造アルミニウム設計がダイムラー・クライスラーの性能要件を満たしていることを確認しました。当初の重量削減目標は40%でしたが、既存の鋼鉄部品のエンベロープによって制約された剛性主導の設計により、重量削減は25%近くになりました。生産施設(図5)のコスト分析では、26ポンドの鋳造アルミニウム部品は、33ポンドの鋼鉄アセンブリと比較して、7.00ドルから14.00ドルのコストプレミアムの可能性があることが示されました。
データ解釈:
熱間チャンバー金属射出システムの開発と、金型直下での金属品質の維持が、主要な成果として強調されています。複雑な形状のリフトゲートインナーパネルの鋳造の成功は、超大型鋳造プロセスの実現可能性を示しています。コスト分析(図6)は、コストプレミアムが存在するものの、軽量化と部品統合の可能性が大きな利点を提供することを示唆しています。アルミニウム固有の設計最適化を通じて、目標の40%の軽量化を達成することで、コストプレミアムをさらに削減し、アルミニウム構造の競争力を高めることができます。
図のリスト:
- 図1. 超大型鋳造の候補部品 (Candidate Parts for Ultra Large Castings)
- 図2a. 従来の鋼鉄製インナーパネル (Conventional Steel Inner Panel)
- 図2b. シングルアルミニウム鋳造インナーパネル (Single Aluminum Cast Inner Panel)
- 図3. リフトゲートパーマネントモールド (Liftgate Permanent Mold)
- 図4. プレスプラテンに配置されたミニバン (Minivan Located on Press Platen to Scale)
- 図5. 生産システムレイアウト (Production System Layout)
- 図6. 生産施設のコスト内訳 (Cost Breakdown for Production Facility)
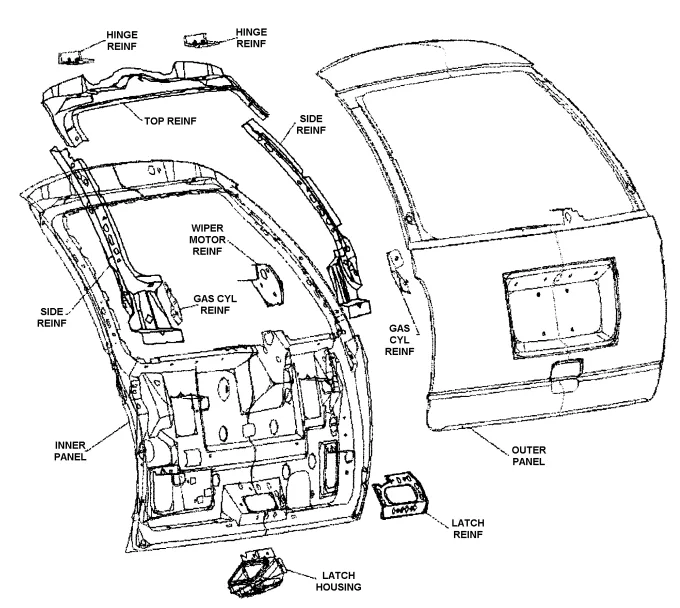
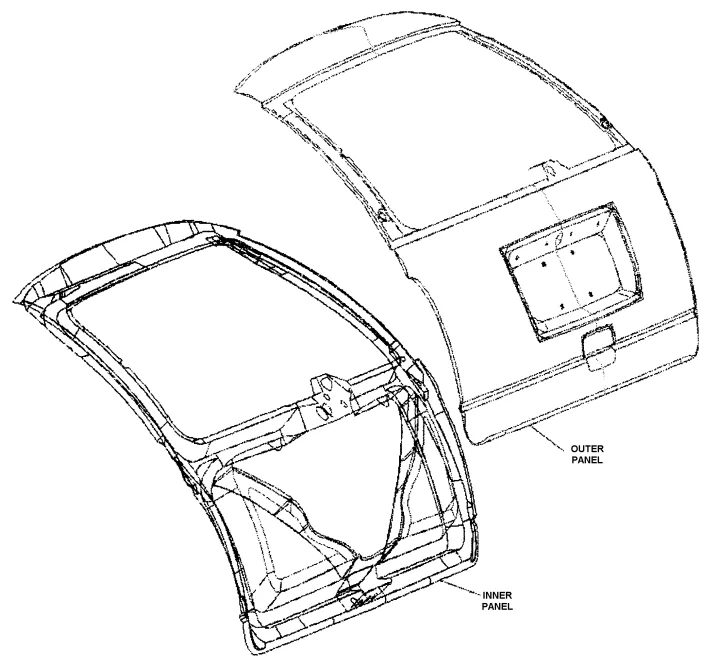
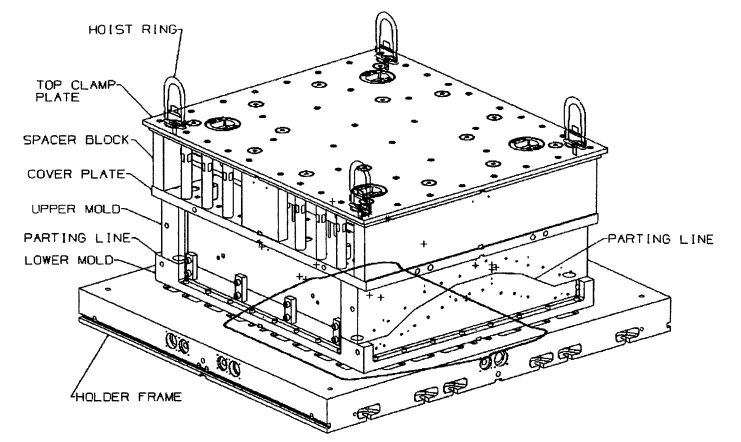
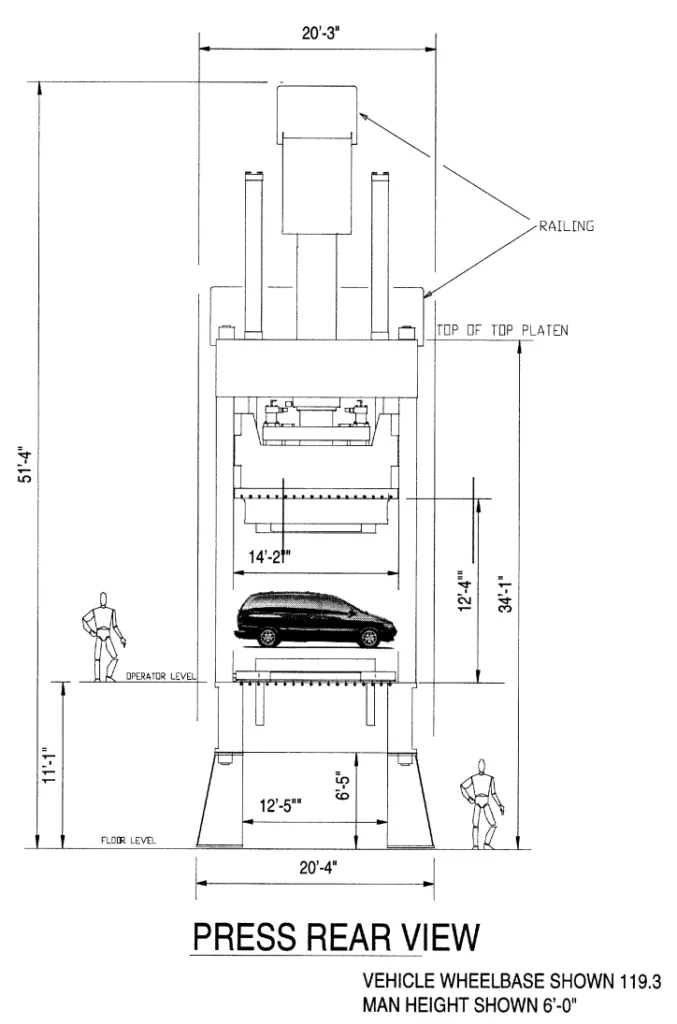
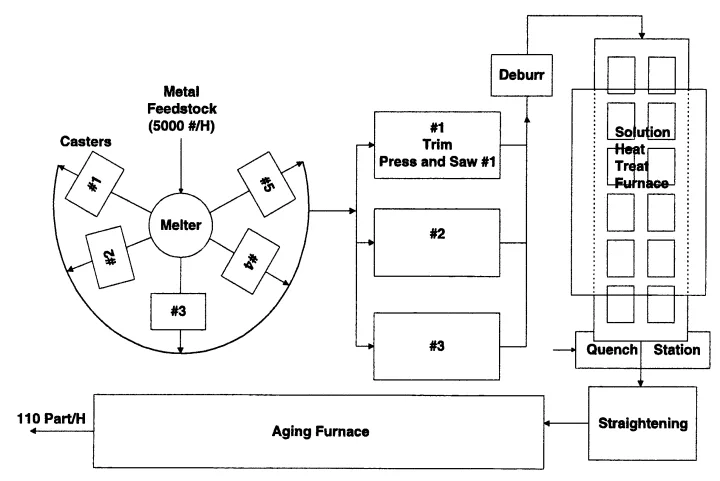
6. 結論:
主な調査結果の要約:
この研究は、超大型薄肉アルミニウム車体構造を製造するための低圧、熱間チャンバー、多点射出垂直鋳造プロセスの実現可能性を実証することに成功しました。開発されたプロセスと鋳造システムは、部品点数と組立作業を削減することにより、軽量アルミニウム部品のコストを大幅に削減する道筋を提供します。クライスラーミニバンリフトゲートインナーパネルの実証は、複雑な形状を鋳造し、従来の鋼鉄アセンブリと比較して軽量化を達成する能力を示しました。
研究の学術的意義:
この研究は、大型で複雑なアルミニウム鋳造品を製造するための新しいアプローチを導入し、検証することにより、ダイカスト技術の進歩に貢献しています。低圧、熱間チャンバー、多点射出システムの設計と実装、および自動車の軽量化への応用に関する貴重な洞察を提供します。
実際的な意義:
この超大型鋳造プロセスの開発の成功は、自動車産業にとって大きな実際的な意義を持っています。アルミニウム車体構造のコストを削減する潜在的なソリューションを提供し、鋼鉄との経済的競争力を高め、燃費効率を向上させ、排出量を削減するための軽量化戦略の普及を促進します。
研究の限界と今後の研究分野:
実証で達成された軽量化は、既存の鋼鉄部品のエンベロープによって課せられた剛性要件によって制限されました。今後の研究では、軽量化の可能性を最大限に高めるために、アルミニウム専用の部品設計の最適化に焦点を当てる必要があります。さらなるプロセスの最適化、産業規模への拡大、および実証部品を超えたより広範なアプリケーションの探求が、今後の研究分野として推奨されます。
7. 参考文献:
- 米国特許第5,370,171号、1994年12月6日、「ダイカストプロセスおよび装置」、J. R. Fieldsら、アルコア。
8. 著作権:
- この資料は、「T. N. Meyer, M. J. Kinosz, E. M. Bradac, M. Mbaye, J. T. Burg, M. A. Klingensmith」の論文:「Ultra Large Castings to Produce Low Cost Aluminum Vehicle Structures」に基づいています。
- 論文ソース: SAE TECHNICAL PAPER SERIES 1999-01-2252
この資料は上記の論文に基づいて要約されたものであり、商業目的での無断使用は禁止されています。
Copyright © 2025 CASTMAN. All rights reserved.