この論文概要は、['VIABILITY OF FLAX FIBER-REINFORCED SALT CORES FOR ALUMINUM HIGH-PRESSURE DIE CASTING IN EXPERIMENT AND SIMULATION']という論文に基づいており、['International Journal of Metalcasting']に掲載されました。
1. 概要:
- タイトル:VIABILITY OF FLAX FIBER-REINFORCED SALT CORES FOR ALUMINUM HIGH-PRESSURE DIE CASTING IN EXPERIMENT AND SIMULATION (アルミニウム高圧ダイカスト用フラックス繊維強化塩コアの実験とシミュレーションによる実現可能性)
- 著者:Dominik Boos, Klaus Drechsler, Swen Zaremba
- 出版年:2024年
- 出版ジャーナル/学会:International Journal of Metalcasting
- キーワード:water-soluble core, expendable core, lost core, hollow parts in HPDC, salt core, fiber reinforcement, flax fiber, aluminum casting, high-pressure die casting, simulation, cavity venting, mechanical characterization, three-point bending, wet compression molding
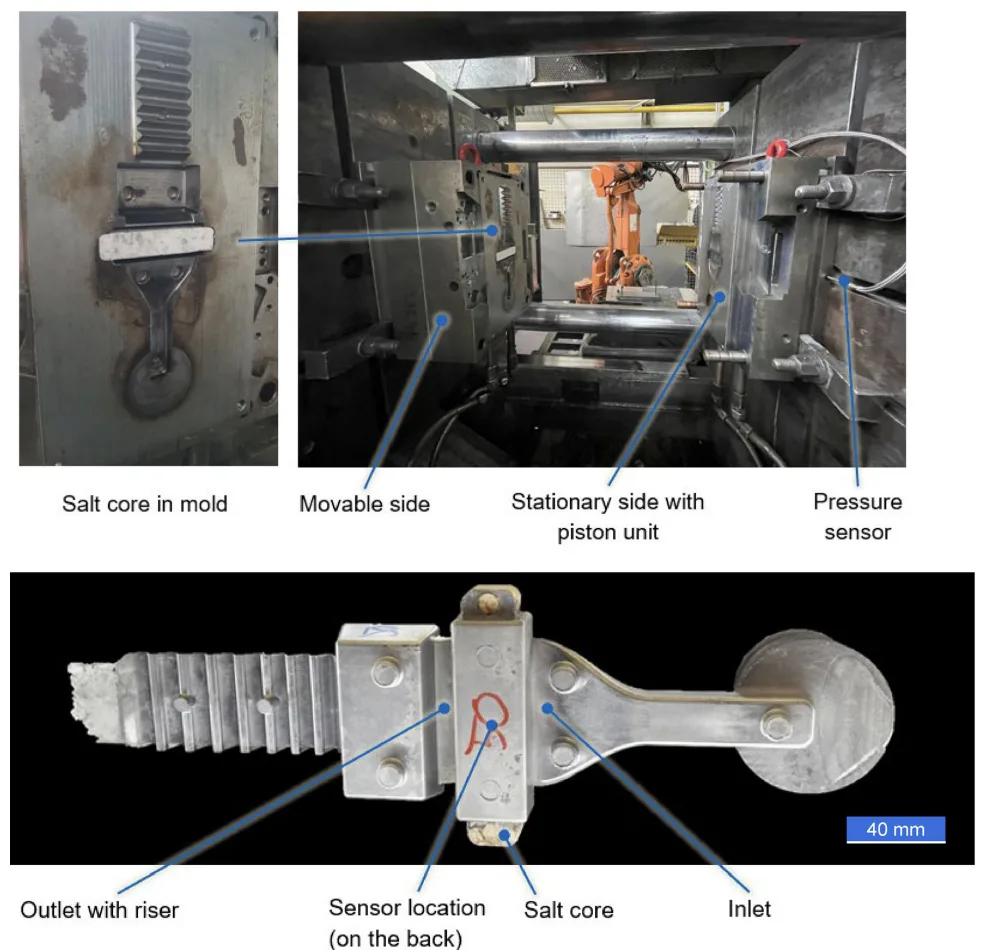
2. 研究背景:
研究トピックの背景:
世界的な脱炭素化と排出量削減の要求の高まりは、軽量設計の概念を促進しており、中空部品またはアンダーカットのある部品がこのタスクを達成できます。アルミニウム高圧ダイカスト(HPDC)は、複雑でニアネットシェイプの3D部品を薄肉で大量生産するための経済的に効果的なプロセスであり、高い軽量化の可能性を提供します。しかし、高いゲート速度(60m/s)、高い充填圧力(1200 bar)、金型温度(最大280℃)、溶融温度(最大700℃)などの厳しい条件のため、HPDCによる複雑な中空軽金属部品の製造は困難です。後処理で除去される消耗品またはロストコアは、これらの複雑な形状を実現できます。課題は、プロセスにおける高い抵抗性と容易な除去性の両方をバランス良く備えたロストコア材料を見つけることです。
既存研究の現状:
バインダーフリー塩と融点の高い塩混合物は、バインダー安定化コアよりも強度と表面品質が優れている適切なロストコア材料であることが証明されています。バインダーフリー塩コアは、粉末の焼結、溶融物の鋳造、またはスラリーの湿式圧縮成形によって製造できます。しかし、凝集のためにイオン結合に依存するバインダーフリー塩の脆さは、動的な負荷がクラックやフラッシュを引き起こす可能性があるHPDCでの適用を制限します。これらの問題を軽減するための既存のアプローチには、コアをゲートから遠ざける、機械パラメータを減らす、肉厚を厚くする、または高温での強度低下を受け入れるなどがあります。
研究の必要性:
従来の塩コアは、HPDCの非常に動的な負荷の下ではしばしば破損し、スクラップ部品につながります。特にモビリティ分野のように要求の厳しい分野で、複雑な中空部品へのHPDCの適用を拡大するためには、より堅牢なロストコア材料が必要です。
3. 研究目的と研究課題:
研究目的:
本論文の目的は、HPDCにおけるロストコア用の新しい繊維強化塩材料の実現可能性を示すことです。本研究では、シミュレーションを利用してコアインサートに作用する過渡的な曲げモーメントを推定し、これらの知見を鋳造実験で検証します。
主要な研究課題:
取り組むべき主要な研究課題は次のとおりです。
- フラックス繊維強化は、HPDCにおける塩コアの生存可能性を高めることができるか?
- 溶融金属の流れと圧力分布のシミュレーション結果は、繊維強化塩コアを使用したHPDCの実験結果とどのように相関するか?
- フラックス繊維強化塩コアの曲げ強度とエネルギー吸収能力は、従来の塩コアと比較してどの程度か?
研究仮説:
中心的な仮説は、フラックス繊維強化が塩コアの靭性を向上させ、HPDCの動的な負荷に耐えることを可能にし、複雑な中空アルミニウム部品の製造に実行可能な状態を維持できるということです。また、シミュレーションはHPDC充填中の塩コアにかかる負荷を正確に予測できるという仮説も立てられています。
4. 研究方法
研究デザイン:
本研究では、実験的調査とシミュレーションベースの調査を組み合わせた混合手法アプローチを採用しています。実験には、繊維強化塩コアの機械的特性を評価するための三点曲げ試験と、実際の鋳造条件下でのコアの生存可能性を評価するためのHPDC実験が含まれます。シミュレーションには、アルミニウム溶融金属の流れとHPDC充填中の圧力分布をモデル化するために、ANSYS Fluent 2023R1を使用した2Dおよび3D数値流体力学(CFD)分析が含まれます。
データ収集方法:
- 三点曲げ試験: 10kNロードセルとビデオ伸び計を使用して、力と変位のデータを収集しました。試験片の形状は長方形のバーであり、試験はDIN EN 843規格に従って実施されました。
- HPDC実験: コア表面付近の圧力プロファイルを、HBM QuantumX MX410B測定アンプに接続されたKistler 6175A2圧力センサーを使用して記録しました。実験後、鋳造部品と塩コアの目視検査を実施しました。
- CFDシミュレーション: 圧力分布、溶融金属速度、および体積分率に関するデータは、ANSYS Fluentシミュレーションから生成されました。
分析方法:
- 機械的特性評価: 曲げ強度、曲げ弾性率、および吸収エネルギーは、三点曲げ試験データから計算されました。
- CFDシミュレーション分析: シミュレーション結果を分析して、塩コアに作用する圧力負荷と曲げモーメントを決定しました。一次元解析出口モデルを開発し、検証のためにCFD結果と比較しました。数値精度を確保するために、メッシュ収束研究を実施しました。
- シミュレーションと実験の相関関係: シミュレーションで予測された負荷をHPDC実験における塩コアの性能と比較して、コアの生存可能性を評価し、シミュレーションアプローチを検証しました。
研究対象と範囲:
本研究は、湿式圧縮成形によって製造されたフラックス繊維強化塩コアに焦点を当てています。2種類のフラックス繊維強化塩コア試験片(F0310およびF3010)と従来の焼結塩コア(NaCIEM)を試験しました。HPDC実験は、Italpress IP 300 SC冷間チャンバーダイカストマシンとEN-AC AlSi9Cu3(Fe)アルミニウム合金を使用して実施されました。シミュレーションは、コアインサートを備えた長方形パイプ鋳造形状の2Dおよび3Dモデルを使用して実行されました。
5. 主な研究結果:
主要な研究結果:
- 機械的特性: フラックス繊維強化塩コアは、従来の塩コアと比較して、三点曲げ試験で大幅に高いエネルギー吸収量(8〜31倍)を示し、靭性が向上していることを示しました。曲げ強度は、繊維パラメータに応じて、繊維強化コアの場合、11〜37 MPaの間で変化しました。
- CFDシミュレーションの検証: 2D充填シミュレーションは、メッシュ収束を実証しました。一次元解析出口モデルは、ベント圧力損失に関するCFD結果と優れた一致を示しました。3Dシミュレーションは、64m/sのインゲート速度で塩コアに最大33 MPaの応力ピークを予測しました。
- HPDCコアの生存可能性: 従来の塩コア(曲げ強度〜15 MPa)は、高いパラメータ設定のHPDC実験で破損し、シミュレーション予測と一致しました。繊維強化塩コアは、より高い曲げ強度と靭性により、HPDC実験で生存可能性を維持し、その堅牢性を実証しました。
データ解釈:
- エネルギー吸収量の増加によって証明されるように、フラックス繊維強化塩コアの強化された靭性は、HPDCにおける生存可能性にとって非常に重要です。この靭性により、高い動的な負荷に耐え、従来の塩コアで観察される脆性破壊に抵抗することができます。
- CFDシミュレーション、特に3Dシミュレーションは、HPDC充填中の塩コアにかかる応力負荷を予測するための貴重なツールを提供し、コア材料とプロセスパラメータの最適化を可能にします。検証済みの出口ベントモデルは、これらのシミュレーションの精度を向上させます。
- 実験的検証は、繊維強化がHPDCにおける塩コアの性能を向上させる効果的な戦略であることを確認し、より複雑な中空部品の製造の可能性を開きます。
図のリスト:
- Figure 1. Wet compression molding process and basic tool components for a short fiber-reinforced salt core.14
- Figure 2. Fracture patterns of unreinforced salt (left) and flax fiber-reinforced salt (right). Due to the partly translucent salt matrix, the fibers close to the surface are visible in the non-damaged areas creating a marbled appearance.
- Figure 3. Bending test results representing brittle (left) or pseudo-ductile (right) material behavior for NaCIEM (benchmark) or F1520* specimens, respectively.14
- Figure 4. Summary of three-point bending test results for flax fiber-reinforced and conventional salt core specimens.14 Bars represent the 25% and 75% percentiles; the circles represent the mean values, and the antennas reach out to the extrema of the test series. Plots generated with boxplot_custom.m.45
- Figure 5. Typical HPDC mold setup (top) and surrogate model (bottom) for vent modeling according to Bar-Meir et al.64 or Nouri-Borujerdi and Goldak.65
- Figure 6. The HPDC mold setup (top) and demonstrator part (bottom)66.
- Figure 7. Shot curves measured by the HPDC sensor for "high" and "low" parameter settings. The averaged curves show the mean of the curves. Scatter area is represented by the hull curves. Please note the log scale on the abscissa.
- Figure 8. Geometric features of a sharp bend according to Idel'chik68
- Figure 9. Mesh and boundaries for the 2D CFD vent model.
- Figure 10. Mesh domains for the HPDC simulation.
- Figure 11. Mesh with polyhedral surface mesh and polyhedral and hexahedral volume elements for the 3D HPDC simulation. The dash-dotted line on the left represents the symmetry plane.
- Figure 12. Mach number and static pressure distribution for a stagnation pressure of 1e5 Pa at the inlet.
- Figure 13. Mach number and static pressure distribution for a stagnation pressure of 1e7 Pa at the inlet.
- Figure 14. Loss coefficient (fD,CFD) and inlet Mach number (Min,CFD) obtained from the CFD solution for the 2D vent model with sensitivity checks for higher stagnation temperature ("-hot") or finer mesh (“-fine”).
- Figure 15. Loss coefficient over the mean Re number in the vent for the modified 1D analytical model (fD,V), 1D analytical model according to the original literature (fD,f) and 2D CFD simulation (fD,CFD). The discontinuity in the curves for the analytical models is caused by the discrete transition from laminar to turbulent flow at Re=2300.
- Figure 16. Jet breakup at a fill fraction of 22% for the 2D mesh variants. The dimensionless characteristic numbers for the jet based on the hydraulic diameter of the gate are: Re = 215e3, We = 519, Oh = 8e-4. Red cells represent the melt volume fraction, whereas blue cells represent air.
- Figure 17. Solution on M2D1 at fill time 2.886 ms/fill fraction 22%.
- Figure 18. Solution on M2D1 at fill time 3.830 ms/fill fraction 30%.
- Figure 19. Solution on M2D1 at fill time 5.281 ms/fill fraction 40%.
- Figure 20. Solution on M2D1 at fill time 8.010 ms/fill fraction 60%.
- Figure 21. Solution on M2D1 at fill time 12.033 ms/fill fraction 86%.
- Figure 22. Simulated cavity pressure at the sensor location for parameter setting "high".
- Figure 23. Resulting total forces on the core in x- and y-direction on M2D1 for parameter setting "high".
- Figure 24. Simulated outlet Mach number for parameter setting "high".
- Figure 25. High interface velocities and cell residuals in vicinity of a merging phase interface for the solution on M2D1 at fill fraction 60% (close-up view of Figure 20, upper right corner). The figure shows an overlay of the phase fraction field where the interface between melt and air is indicated by a dashed line. Vectors that are colored according to their magnitude represent the velocity field. The imbalance of the energy equation is shown by the temperature residual for each cell. The maximum air speed is 330 m/s (Mach 0.54).
- Figure 26. Absolute values of the maximum bending stress in the core during the 2D filling simulation for parameter setting "high".
- Figure 27. Solution on M3D at fill time 1.992 ms/fill fraction 14%.
- Figure 28. Solution on M3D at fill time 3.101 ms/fill fraction 22%.
- Figure 29. Solution on M3D at fill time 4.203 ms/fill fraction 30%.
- Figure 30. Solution on M3D at fill time 5.801 ms/fill fraction 40%.
- Figure 31. Solution on M3D at fill time 12.702 ms/fill fraction 86%.
- Figure 32. Absolute values of the maximum bending stress in the core and sensor pressure during the 3D filling simulation for parameter settings "low" and "high".
- Figure 33. Cross sections of salt cores after aluminum HPDC for “low” and “high” parameter settings.
- Figure 34. Micrographs of overmolded F0310 (left) and F3010 (right) specimens for the parameter setting "high".
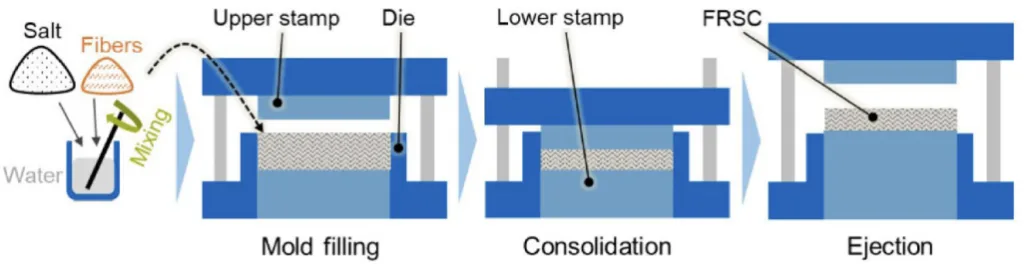
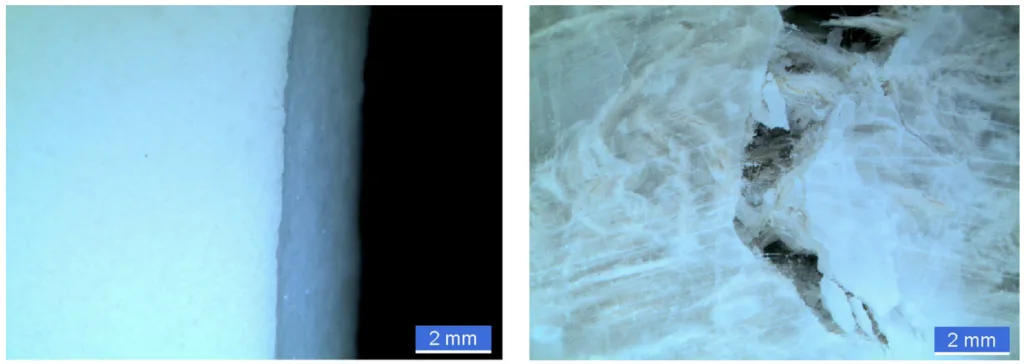
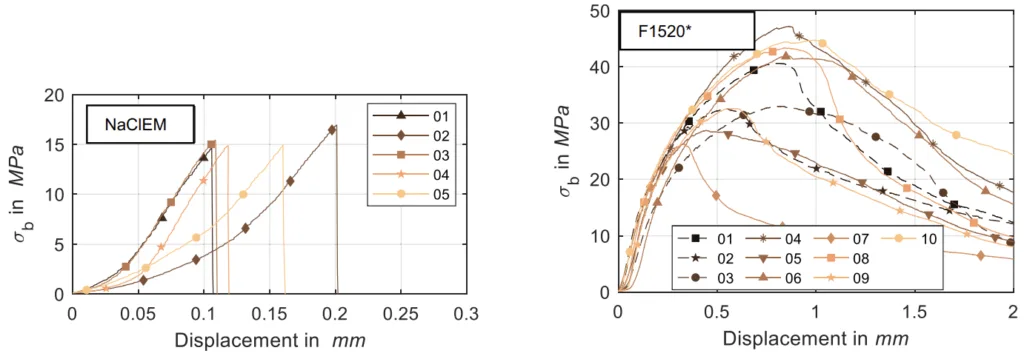
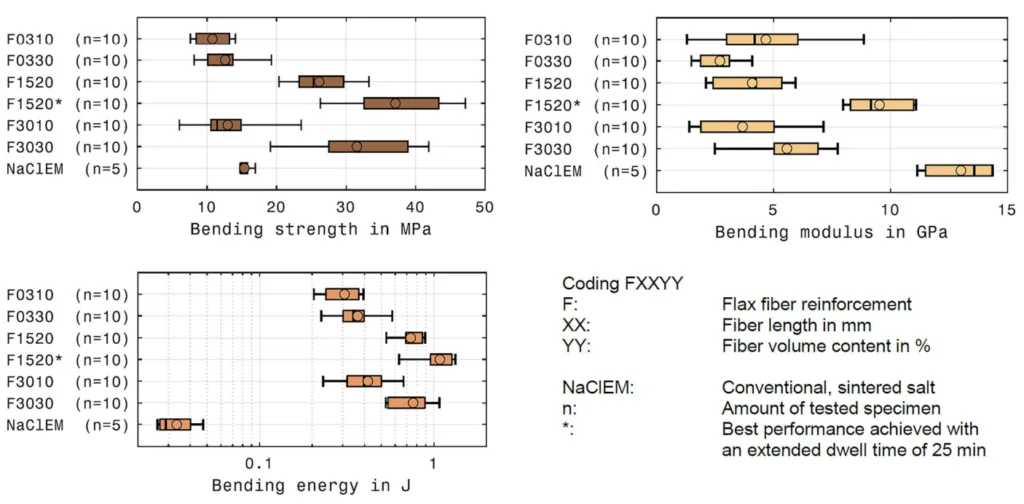
specimens.14 Bars represent the 25% and 75% percentiles; the circles represent the mean values, and the antennas reach out to the extrema of the test series. Plots generated with boxplot_custom.m.45
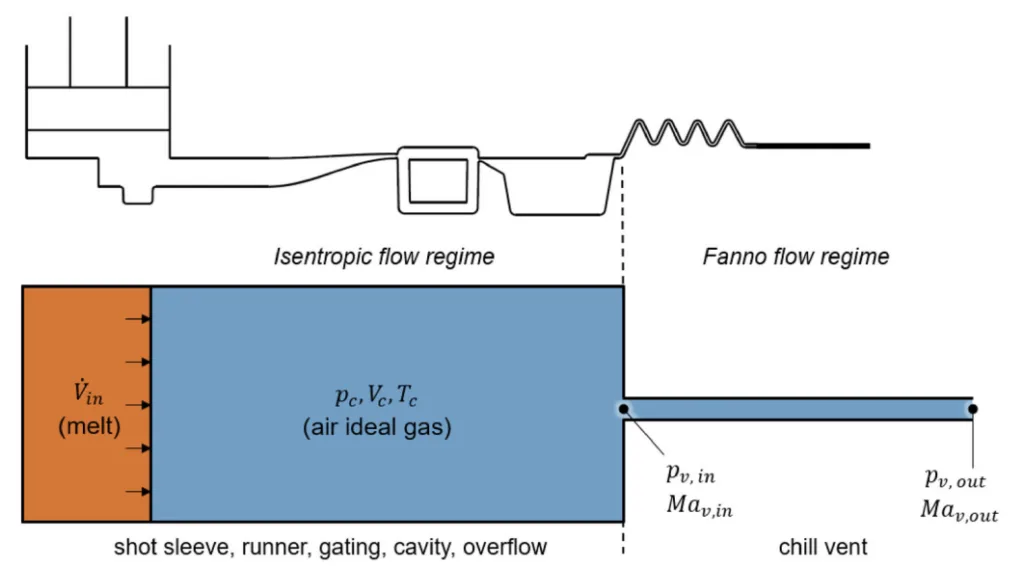
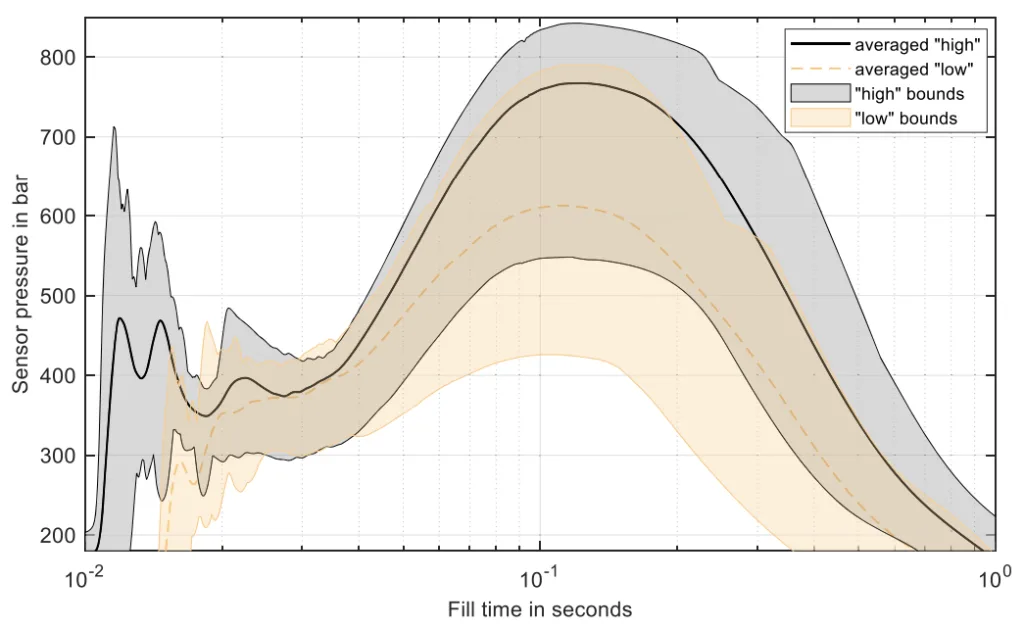
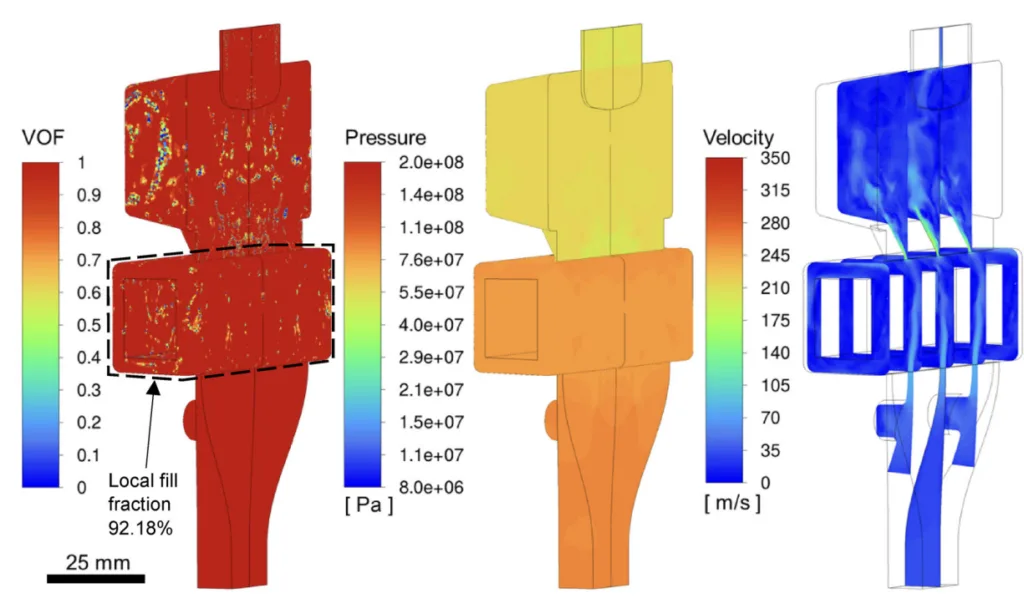
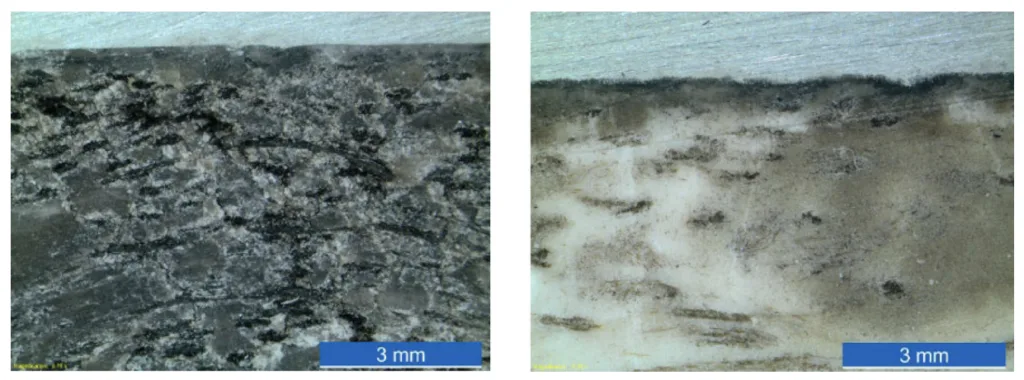
6. 結論:
主な結果の要約:
本研究では、アルミニウムHPDC用のフラックス繊維強化塩コアの実現可能性を実証することに成功しました。主な調査結果は次のとおりです。
- フラックス繊維強化は、曲げ試験でのエネルギー吸収の増加によって証明されるように、塩コアの靭性を大幅に向上させます。
- 実験データによって検証されたCFDシミュレーションは、HPDC充填中の塩コアにかかる応力負荷を正確に予測します。
- 従来の塩コアはHPDC条件下で破損しますが、繊維強化塩コアは、その改善された機械的特性により、実行可能な状態を維持します。
- 修正された一次元ベントモデルは、複雑なベント形状を正確に表現し、シミュレーションの精度を向上させます。
研究の学術的意義:
本研究は、学術分野に以下の貢献をします。
- 実験およびシミュレーション手法を組み合わせた、HPDCにおける繊維強化塩コアの応用に関する包括的な調査を提供します。
- 正確なベントモデリングに焦点を当てて、HPDCにおけるコアの生存可能性を予測するためのツールとしてCFDシミュレーションを検証します。
- HPDC条件下での材料挙動、特にロストコア材料における靭性の役割に関する理解を深めます。
実際的な意義:
本研究の実用的な意義は、ダイカスト業界にとって重要です。
- フラックス繊維強化塩コアは、従来の塩コアに代わる堅牢な代替品を提供し、HPDCを介してアンダーカットと中空断面を備えた、より複雑で軽量なアルミニウム部品の製造を可能にします。
- 開発されたシミュレーション手法は、コア設計とプロセスパラメータを最適化し、スクラップ率を削減し、鋳造品質を向上させるために使用できます。
- 新しいロストコア材料は、鋳造工場に技術的な優位性を提供し、特に軽量化が重要なモビリティ分野で、新しい市場を開拓する可能性があります。
研究の限界
本研究では、以下の限界を認識しています。
- フラックス繊維強化塩コアの材料特性評価は、主に室温で行われています。HPDC予熱に関連する高温での挙動については、さらなる調査が必要です。
- HPDCの動的な負荷に関連する高ひずみ速度での材料挙動は、完全には特性評価されておらず、より洗練されたシミュレーションモデルのために調査する必要があります。
- 本研究は、特定のフラックス繊維強化パラメータ(長さと体積含有量)に焦点を当てています。繊維パラメータとコア組成のさらなる最適化が可能になる可能性があります。
- シミュレーションモデルは、充填段階の無視や理想化された機械挙動の仮定など、HPDCプロセスの特定の側面を簡略化しています。
7. 今後のフォローアップ研究:
- フォローアップ研究の方向性
今後の研究方向には、以下が含まれます。 - 予熱されたコアインサートをシミュレーションするために、フラックス繊維強化塩コアの破壊挙動を高温で試験します。
- シミュレーションの精度を向上させるために、材料挙動のひずみ速度依存性を調査します。
- 性能向上のために、フラックス繊維パラメータとコア組成を最適化します。
- 特定の繊維強化のために重要なコア領域を特定するために、シミュレーションで流体と構造損傷モデルを結合します。
- コア製造において、フラックス繊維と塩を分離して再利用することの実現可能性を評価するために、溶解およびリサイクル実験を実施します。
- さらなる探求が必要な領域
さらなる探求が必要な領域には、以下が含まれます。 - 繊維強化塩コアで製造された鋳物の表面品質とその改善方法。
- 複雑な繊維強化塩コアの湿式圧縮成形のためのツーリング設計および製造上の考慮事項。
- 産業用HPDC生産におけるフラックス繊維強化塩コアの使用に関する経済分析。
- プロトタイピングおよび少量生産のツーリングコストを削減するために、複雑なコア形状のためのモジュール式要素と接合技術の使用を調査します。
8. 参考文献:
- 1. B. Fuchs, Salzkerntechnologie für Hohlgussbauteile im Druckguss, Dissertation, FAU Erlangen-Nürnberg, 1st edn. (Cuvillier Verlag, Göttingen, 2014)
- 2. L.H. Kallien, Salzkerne im Druckguss, Giesserei-Special(01), (2016), pp. 32–43
- 3. J. Campbell, Complete casting handbook: metal casting processes, techniques and design, 2nd edn. (Butterworth-Heinemann, Amsterdam, 2015)
- 4. P. Fickel, Hohl- und Verbundguss von Druckgussbauteilen-Numerische Auslegungsmethoden und experimentelle Verifikation, Dissertation, Universität Stuttgart (2017). https://doi.org/10.18419/opus-9068
- 5. C. Herrmann, H. Pries, G. Hartmann (eds.), Energie- und ressourceneffiziente Produktion von Aluminium-druckguss, 1st ed., Springer Vieweg, Berlin, Heidelberg (2013). https://doi.org/10.1007/978-3-642-39853-7
- 6. M. Scheydecker, K.-L. Weisskopf, Innovationspotenzial Salzkerne. Herausforderungen für die Serienanwendung im Aluminium-Guss, VDI-Berichte 2217, pp. 19–39 (2014)
- 7. K. Vollrath, Herstellung hochwertiger Salzkerne durch Warmkammer-Druckgießen. Giesserei 104(01), 32-37 (2017)
- 8. T. Nitschke-Pagel, Thermisches Fügen, in Handbuch Leichtbau: Methoden, Werkstoffe, Fertigung. ed. by F. Henning, E. Moeller (Hanser, München Wien, 2011), pp.855-885
- 9. L.H. Kallien, V. Görgrün, Einfluss der Elektromobilität auf die Gussproduktion in der deutschen Gießerei-Industrie: Teil 1. Giesserei 105(4), 70–80 (2018)
- L.H. Kallien, V. Görgrün, Einfluss der Elektromobilität auf die Gussproduktion in der deutschen Gießerei-Industrie: Teil 2. Giesserei 105(7), 60–66 (2018)
- H. Mählmann, M. Baader, GDA Jahresbericht 2020, Gesamtverband der Aluminiumindustrie e. V. (2020)
- F. Bonollo, N. Gramegna, G. Timelli, High-pressure die-casting: contradictions and challenges. Miner. Metals Mater. Soc. 67(5), 901–908 (2015). https://doi.org/10.1007/s11837-015-1333-8
- M.T. Murray, M. Murray, High pressure die casting of aluminium and its alloys, in Fundamentals of aluminium metallurgy: production, processing and applications, 1st edn., ed. By R. Lumley (Woodhead Publishing Limited, Cambridge, 2011), pp. 217–261. https://doi.org/10.1533/9780857090256.1.217
- D. Boos, S. Zaremba, K. Drechsler, Towards a robust, water-soluble, lost core material:part two-fiber-reinforced salt by wet compression molding. J. Plast. Technol. 19(5), 190–226 (2023). https://doi.org/10.3139/0999.01052023
- P. Jelínek, E. Adámková, F. Mikšovský, J. Beňo, Advances in technology of soluble cores for die castings. Arch. Foundry Eng. 15(2), 29–34 (2015). https://doi.org/10.1515/afe-2015-0032
- W. Jiang, J. Dong, L. Lou, M. Liu, Z. Hu, Preparation and properties of a novel water soluble core material. J. Mater. Sci. Technol. 26(3), 270–275 (2010)
- A. Dworog, Abschlussbericht des Verbundprojektes 3D-Freiformkanäle im Druckguss/Medienführende Kanäle, BMBF Forschung für die Produktion von morgen, Förderkennzeichen 02PU2243, Nordwalde (2011)
- Z. Xiao, L.T. Harper, A.R. Kennedy, N.A. Warrior, A water-soluble core material for manufacturing hollow composite sections. Compos. Struct. 182, 380-390 (2017). https://doi.org/10.1016/j.compstruct.2017.09.058
- T. Hartig, G. Schiller, C. Bütterich, Salt Core Technology. Lost cores aluminium casting applications, Wilhermsdorf (2018)
- A. Kugel, A. Bührig-Polaczek, Möglichkeiten zur Erzeugung von Hohlräumen in Druckgussteilen. Gießereiforschung 56(1), 14–22 (2004)
- J. Yaokawa, D. Miura, K. Anzai, Y. Yamada, H. Yoshii, Strength of salt core composed of alkali carbonate and alkali chloride mixtures made by casting technique. Mater. Trans. 48(5), 1034–1041 (2007). https://doi.org/10.2320/matertrans.48.1034
- F. Czerwinski, M. Mir, W. Kasprzak, Application of cores and binders in metalcasting. Int. J. Cast Met. Res. 28(3), 129–139 (2015). https://doi.org/10.1179/1743133614Y.0000000140
- H.D. Grözinger, WO 2005/080022 A2 (2005)
- P.A.M. Vitor, P.H.F. Santos, A.K. Alves, C.P. Bergmann, Study of densification by pressing and sintering of NaCl and KCl salts, in 7th International Congress on Ceramics & 62° Congresso Brasileiro de Cerâmica, (2018), pp. 734–740
- X. Gong, X. Liu, Z. Chen, Z. Yang, W. Jiang, Z. Fan, 3D printing of high-strength water-soluble salt cores via material extrusion. Int. J. Adv. Manuf. Technol. 118, 2993-3003 (2022). https://doi.org/10.1007/s00170-021-08131-x
- K. Oikawa, K. Meguro, J. Yaokawa, K. Anzai, Y. Yamada, A. Fujiwara, H. Yoshii, Mechanical properties of mixed salt core made by die casting machine. J. Jpn. Foundry Eng. Soc. 81(5), 232–237 (2009). https://doi.org/10.11279/jfes.81.232
- D. Pierri, C. Beck, Lost Core Technologie-offen für alle. Chancen und Grundlagen des Verfahrens, Giesserei 103(10), 46–52 (2016)
- L.H. Kallien, T. Weidler, M. Becker, Production of magnesium die castings with hollow structures using gas injection technology in the hot chamber die casting process. Int. Foundry Res. 66(4), 20–27 (2014)
- L.H. Kallien, C. Böhnlein, A. Dworog, B. Müller, Ergebnisse aus dem Forschungsprojekt 3-D-Freiform-medienführende Kanäle im Druckguss. Giesserei 100(12), 36-43 (2013)
- R. Huang, B. Zhang, Study on the composition and properties of salt cores for zinc alloy die casting. Int. J. Metalcast. 11, 440–447 (2017). https://doi.org/10.1007/s40962-016-0086-7
- K. Oikawa, K. Sakakibara, Y. Yamada, K. Anzai, High-temperature mechanical properties of NaCl–Na2CO3 salt-mixture removable cores for aluminum die-casting. Mater. Trans. 60(1), 19–24 (2019). https://doi.org/10.2320/matertrans.MG201804
- S. Tu, F. Liu, G. Li, W. Jiang, X. Liu, Z. Fan, Fabrication and characterization of high-strength water-soluble composite salt core for zinc alloy die castings. Int. J. Adv. Manuf. Technol. 95, 505-512 (2018). https://doi.org/10.1007/s00170-017-1208-y
- S. Findeisen, R. van der Auwera, M. Heuser, F.-J. Wöstmann, Gießtechnische Herstellung von E-Motorengehäusen mit interner Kühlung. Giesserei 106(06), 72-78 (2019)
- X. Gong, W. Jiang, F. Liu, Z. Yang, F. Guan, Z. Fan, Effects of glass fiber size and content on microstructures and properties of KNO3-based water-soluble salt core for high pressure die casting. Int. J. Metalcast. 15, 520-529 (2021). https://doi.org/10.1007/s40962-020-00480-9
- C. Cantas, B. Baksan, Effects of composition on the physical properties of water-soluble salt cores. Int. J. Metalcast. 15, 839–851 (2021). https://doi.org/10.1007/s40962-020-00511-5
- F. Liu, S. Tu, X. Gong, G. Li, W. Jiang, X. Liu, Z. Fan, Comparative study on performance and microstructure of composite water-soluble salt core material for manufacturing hollow zinc alloy castings. Mater. Chem. Phys. 252, 123257 (2020). https://doi.org/10.1016/j.matchemphys.2020.123257
- X. Wang, W. Liu, X. Liu, L. Song, First-principles calculation and mechanical properties of NaCl–Na2SO4 composite water-soluble salt core. Int. J. Metalcast. 17, 263–271 (2023). https://doi.org/10.1007/s40962-022-00769-x
- M. Becker, Hohle Aluminiumstrukturbauteile durch Salzkerne im Druckguss, Dissertation, TU Clausthal, Clausthal-Zellerfeld (2021). https://doi.org/10.21268/20211123-0
- B. Fuchs, H. Eibisch, C. Körner, Core viability simulation for salt core technology in high-pressure die casting. Int. J. Metalcast. 7, 39–45 (2013). https://doi.org/10.1007/BF03355557
- A. Schilling, D. Schmidt, J. Glück, N. Schwenke, H. Sharabi, M. Fehlbier, About the impact on gravity cast salt cores in high pressure die casting and rheocasting. Simul. Modelling Pr. Theory 119, 102585 (2022). https://doi.org/10.1016/j.simpat.2022.102585
- DIN EN 843-1, Hochleistungskeramik - Mechanische Eigenschaften monolithischer Keramik bei Raumtemperatur—Teil 1: Bestimmung der Biegefestigkeit, Beuth Verlag GmbH, Berlin (2008)
- DIN EN 843-2, Hochleistungskeramik - Mechanische Eigenschaften monolithischer Keramik bei Raumtemperatur—Teil 2: Bestimmung des Elastizitätsmoduls, Schubmoduls und der Poissonzahl, Beuth Verlag GmbH, Berlin (2007)
- R. Telle (ed.), Keramik, 7th edn. (Springer, Berlin Heidelberg, 2007)
- H.L. Bos, The potential of flax fibres as reinforcement for composite materials, Dissertation, Technische Universiteit Eindhoven, Eindhoven (2004)
- G. Talbot, Boxplots Custom, MATLAB Central File Exchange (2022)
- E.J. Vinarcik, High integrity die casting processes, 1st edn. (John Wiley & Sons, INC., New York, 2003)
- S. Mirjalili, S.S. Jain, M.S. Dodd, Interface-capturing methods for two-phase flows: an overview and recent developements, Annual Research Briefs, Center for Turbulence Research, Stanford University (2017)
- S. Kohlstädt, M. Vynnycky, J. Jäckel, Towards the modelling of fluid-structure interactive lost core deformation in high-pressure die casting. Appl. Math. Model. 80, 319–333 (2020). https://doi.org/10.1016/j.apm.2019.10.060
- S. Kohlstädt, M. Vynnycky, A. Neubauer, A. Gebauer-Teichmann, Comparative RANS turbulence modelling of lost salt core viability in high pressure die casting. Prog. Comput. Fluid Dyn. 19(5), 316-327 (2019). https://doi.org/10.1504/PCFD.2019.102054
- J.H. Ferziger, M. Perić, R.L. Street, Computational methods for fluid dynamics (Springer, Cham, 2020). https://doi.org/10.1007/978-3-319-99693-6
- B. Nogowizin, Theorie und Praxis des Druckgusses, 1st edn. (Schiele & Schön, Berlin, 2011)
- M.C. Carter, S. Palit, M. Littler, Characterizing flow losses occuring in air vents and ejector pins in high pressure die castings (2010)
- E. Koya, M. Nakagawa, S. Kitagawa, J. Ishimo, Y. Nakano, N. Ochiai, Visualization of microscopic behavior of atomized flow in high-pressure die casting products using a multiphase flow analysis system. Int. J. Metalcast. 17, 2508–2521 (2023). https://doi.org/10.1007/s40962-023-01015-8
- S. Kohlstädt, M. Vynnycky, S. Goeke, On the CFD modelling of slamming of the metal melt in high-pressure die casting involving lostcores. Metals 11(1), 78 (2021). https://doi.org/10.3390/met11010078
- M. Kan, O. Ipek, M. Koru, An investigation into the effect of vacuum conditions on the filling analysis of the pressure casting process. Int. J. Metalcast. 17, 430-446 (2023). https://doi.org/10.1007/s40962-022-00770-4
- E. Koya, M. Nakagawa, S. Kitagawa, J. Ishimoto, Y. Nakano, N. Ochiai, CFD analysis of mechanisms underlying the porosity-reducing effect of atomized flows in high-pressure die cast products, in MATEC Web Conference, vol. 326, pp. 1-10 (2020). https://doi.org/10.1051/matecconf/202032606006
- M. Karkkainen, L. Nastac, Evaluation and implementation of a fundamental model for interfacial heat transfer coefficient in high-pressure die-casting. Metall. Mater. Trans. B 51(2), 664–676 (2020). https://doi.org/10.1007/s11663-020-01784-1
- T. Wang, J. Huang, H. Fu, K. Yu, S. Yao, Influence of process parameters on filling and feeding capacity during high-pressure die-casting process. Appl. Sci. 12, 4757 (2022). https://doi.org/10.3390/app12094757
- A.I.N. Korti, S. Abboudi, Effects of shot sleeve filling on evolution of the free surface and solidification in the high-pressure die casting machine. Int. J. Metalcast. 11, 223–239 (2017). https://doi.org/10.1007/s40962-016-0051-5
- P. Homayonifar, R. Babaei, E. Attar, S. Shahinfar, P. Davami, Numerical modeling of splashing and air entrapment in high-pressure die casting. Int. J. Adv. Manuf. Technol. 39, 219–228 (2008). https://doi.org/10.1007/s00170-007-1214-6
- E. Altuncu, A. Doğan, N. Ekmen, Performance evaluation of different air venting methods on high pressure aluminum die casting process. Acta Phys. Pol. A 135(4), 664–667 (2019). https://doi.org/10.12693/APhysPolA.135.664
- D.T. Phan, S.H. Masood, S.H. Riza, H. Modi, Development of high performance copper alloy chill vent for high pressure die casting. IJMERR 9(7), 943–948 (2020). https://doi.org/10.18178/ijmerr.9.7.943-948
- P. Meethum, C. Suvanjumrat, Evaluate of chill vent performance for high pressure die-casting production and simulation of motorcycle fuel caps, in MATEC Web Conference, vol. 95, pp. 1–4 (2017). https://doi.org/10.1051/matecconf/20179507025
- G. Bar-Meir, E.R.G. Eckert, R.J. Goldstein, Pressure die casting: a model of vacuum pumping. J. Manuf. Sci. Eng. 118(2), 259–265 (1996). https://doi.org/10.1115/1.2831019
- A. Nouri-Borujerdi, J.A. Goldak, Modeling of air venting in pressure die casting process. J. Manuf. Sci. Eng. 126(3), 577–581 (2004). https://doi.org/10.1115/1.1767187
- P. Erhard, D. Boos, D. Günther, In-mold coating in pressing of natural-fiber-reinforced salt cores for high-pressure die-casting applications, in Proceedings of the Munich Symposium on Lightweight Design, 1st edn., ed. by J. Rieser, F. Endress, A. Horoschenkoff, P. Höfer, T. Dickhut, M. Zimmermann (Springer, Berlin, Heidelberg, 2021), pp. 35-43. https://doi.org/10.1007/978-3-662-65216-9_4
- N. N., Ansys Fluent 2023 R1 Documentation (2023)
- I.E. Idel'chik, Handbook of hydraulic resistance: coefficients of local resistance and friction, Israel Programm for Scientific Translations Ltd., Jerusalem (1966)
- Ν.Ν., ΜATLAB R2021b Documentation (2021)
- W. Sutherland, LII. The viscosity of gases and molecular force. Lond. Edinb. Dublin Philos. Mag. J. Sci. 36(223), 507–531 (1893). https://doi.org/10.1080/14786449308620508
- F.R. Menter, Two-equation eddy-viscosity turbulence models for engineering applications. AIAA J. 32(8), 1598–1605 (1994). https://doi.org/10.2514/3.12149
- C. Rumsey, The menter shear stress transport turbulence model, turbulence modeling resource, NASA Langley Research Center (2023). https://turbmodels.larc.nasa.gov/sst.html. Accessed 11 Apr 2024
- P.H. Oosthuizen, W.E. Carscallen, Compressible Fluid Flow, 1st edn. (The McGraw-Hill Companies Inc, New York, 1997)
- N.T. Basse, Mind the gap: boundary conditions for turbulence modelling, Danfoss CFD Community Tech Talk, Gothenburg (2022). https://doi.org/10.13140/RG.2.2.23072.87043/1
- B. Sasanapuri, M. Kumar, S. Wirogo, Simulation of flow through supersonic cruise nozzle: a validation study, thermal & fluids analysis workshop, NASA Langley Research Center (2011). https://tfaws.nasa.gov/TFAWS11/. Accessed 23 Oct 2024
- E. Michaelides, C.T. Crowe, J.D. Schwarzkopf (eds.), Multiphase flow handbook, 2nd edn. (CRC Press, Taylor & Francis Group, LLC, Boca Raton, 2017)
- N.I. Kolev, Multiphase flow dynamics 1: fundamentals, 5th edn. (Springer, Cham Heidelberg, New York Dordrecht London, 2015). https://doi.org/10.1007/978-3-319-15296-7
- J.U. Brackbill, D.B. Kothe, C. Zemach, A continuum method for modeling surface tension. J. Comput. Phys. 100, 335–354 (1992)
- D.C. Wilcox, Turbulence modeling for CFD, 3rd ed., DCW Industries, La Canada Calif. (2006)
- C.W. Hirt, B.D. Nichols, Volume of fluid (VOF) method for the dynamics of free boundaries. J. Comput. Phys. 39, 201–225 (1981)
- R. Mayon, Z. Sabeur, T. Mingyi, K. Djidjeli, Free surface flow and wave impact at complex solid structures, in 12th International Conference on Hydrodynamics, article 154, pp. 1–11 (2016)
- P.J. Martínez-Ferrer, D.M. Causon, L. Qian, C.G. Mingham, Z.H. Ma, A multi-region coupling scheme for compressible and incompressible flow solvers for two-phase flow in a numerical wave tank. Comput. Fluids 125, 116–129 (2016). https://doi.org/10.1016/j.compfluid.2015.11.005
- R. Wemmenhove, R. Luppes, A.E.P. Veldman, T. Bunnik, Application of a VOF method to model compressible two-phase flow in sloshing tanks, in Proceedings of the ASME 27th International Conference on Offshore Mechanics and Arctic Engineering, OMAE2008-57254, pp. 1–10 (2008)
- M. Jadidi, M. Tembely, S. Moghtadernejad, A. Dolatabadi, Coupled level set and volume of fluid method in openfoam with application to compressible two-Phase flow, in 22nd Annual Conference of the CFD Society of Canada, pp. 1–5 (2014)
- E. Johnsen, F. Ham, Preventing numerical errors generated by interface-capturing schemes in compressible multi-material flows. J. Comput. Phys. 231, 5705–5717 (2012). https://doi.org/10.1016/j.jcp.2012.04.048
- S.A. Beig, E. Johnsen, Maintaining interface equilibrium conditions in compressible multiphase flows using interface capturing. J. Comput. Phys. 302, 548-566 (2015). https://doi.org/10.1016/j.jcp.2015.09.018
- D.L. Youngs, Time-dependent multi-material flow with large fluid distortion: atomic weapons research establishment, Aldermaston, in Numerical Methods in Fluid Dynamics, ed. by K.W. Morton, Baines, M.J. (eds.) (Academic Press, 1982), pp. 273–285
- Q.M. Bui, D. Osei-Kuffuor, N. Castelletto, J.A. White, A scalable multigrid reduction framework for multiphase poromechanics of heterogeneous media. SIAM J. Sci. Comput. 42(2), B379–B396 (2020). https://doi.org/10.1137/19M1256117
- V. Inguva, A. Schulz, E.Y. Kenig, On methods to reduce spurious currents within VOF solver frameworks. Part 1: a review of the static bubble/droplet. Chem. Prod. Process. Model. 17(2), 121–135 (2022). https://doi.org/10.1515/cppm-2020-0052
- DIN EN 1676, Aluminium and aluminium alloys-alloyed ingots for remelting-specifications (Beuth Verlag GmbH, Berlin, 2020)
- H. Cao, C. Wang, J. Che, Z. Luo, L. Wang, L. Xiao, J. Wang, T. Hu, Effect of flow state of pure aluminum and A380 alloy on porosity of high pressure die castings. Materials (2019). https://doi.org/10.3390/ma12244219
- J. Eggers, E. Villermaux, Physics of liquid jets. Rep. Prog. Phys. 71, 1–79 (2008). https://doi.org/10.1088/0034-4885/71/3/036601
- E. Koya, M. Nakagawa, S. Kitagawa, J. Ishimoto, Y. Nakano, N. Ochiai, Atomization in high-pressure die casting-step 2 simulation of atomized flow of molten aluminum by LES-VOF method, in SAE Technical Paper, 2018-01-1393 (2018). https://doi.org/10.4271/2018-01-1393
- H.K. Barton, The pressure diecasting of metals. Metal. Rev. 9(36), 305–414 (1964). https://doi.org/10.1179/mtlr.1964.9.1.305
- M. Wörner, Numerical modeling of multiphase flows in microfluidics and micro process engineering: a review of methods and applications. Microfluid. Nanofluid. 12(6), 841–886 (2012). https://doi.org/10.1007/s10404-012-0940-8
- B. Sjögreen, H.C. Yee, Grid convergence of high order methods for multiscale complex unsteady viscous compressible flows. J. Comput. Phys. 185(1), 1-26 (2003). https://doi.org/10.1016/S0021-9991(02)00044-X
- S. Kohlstädt, On determining lost core viability in high-pressure die casting using computational continuum mechanics, Dissertation, KTH Royal Institute of Technology, Stockholm (2019)
9. 著作権:
- この資料は、"Dominik Boos and Klaus Drechsler and Swen Zaremba"の論文:"VIABILITY OF FLAX FIBER-REINFORCED SALT CORES FOR ALUMINUM HIGH-PRESSURE DIE CASTING IN EXPERIMENT AND SIMULATION"に基づいています。
- 論文ソース:https://doi.org/10.1007/s40962-024-01461-y
この資料は上記の論文に基づいて要約されており、商業目的での無断使用は禁止されています。
Copyright © 2025 CASTMAN. All rights reserved.