この論文の要約は、"[A Novel Approach to Visualize Liquid Aluminum Flow to Advance Casting Science]"と題された論文に基づいており、"[Materials* (MDPI)]"にて発表されました。
1. 概要:
- *タイトル: 液体アルミニウムの流れを可視化し鋳造科学を進歩させるための新しいアプローチ (A Novel Approach to Visualize Liquid Aluminum Flow to Advance Casting Science)
- *著者: Casey Bate, Philip King, Jay Sim, Guha Manogharan
- *発表年: 2023年
- *掲載ジャーナル/学会: *Materials* (MDPI)
- *キーワード: 鋳型充填; 砂型鋳造; スクシノニトリル; 鋳造流体力学; 水モデル; 金属アナログ; 流れシミュレーション
![Figure 1. Casting geometry based on prior experimental study [17], units in mm](https://castman.co.kr/wp-content/uploads/image-361-png.webp)
2. 研究背景:
*研究トピックの社会的/学術的背景:
砂型鋳造において、溶融金属の乱流充填は、二重皮膜、気孔率、酸化物介在物などの鋳造欠陥の既知の前兆です。これらの欠陥は、機械的特性に悪影響を及ぼし、砂型鋳物のスクラップ率を増加させます。したがって、砂型鋳型内の金属の流れ、すなわち鋳造流体力学を理解し制御することは、欠陥を最小限に抑えるために最も重要です。数値シミュレーション手法は、この現象をモデル化するために広範囲に適用されてきましたが、実験的検証は、鋳造環境の過酷な条件と高価なX線装置の制約によって妨げられてきました。
*既存研究の限界:
砂型鋳型内の金属の流れを可視化するための従来の研究アプローチは、重大な課題に直面しています。不透明な砂型鋳型と、過酷な鋳造条件(高温、ガス放出、研磨砂、湿度)が組み合わさることで、直接観察とデータ取得が制限されます。以前に流れの可視化にX線装置を利用した研究は、定性的なデータに限定され、X線を透過できる形状、高コスト、安全上の懸念、および渦のような複雑な3D流れ現象を捉えられない2D画像化の制約を受けました。水モデルは、費用対効果の高いアナログとして使用されてきましたが、熱流体特性が異なり、室温で凝固しないため、溶融金属の挙動を正確に表現できるか懸念があります。
*研究の必要性:
鋳造科学を進歩させ、欠陥を最小限に抑えるためには、砂型鋳型内の液体金属の流れを正確に可視化および分析するための改良された実験技術が不可欠です。この研究は、水と比較してより代表的な流れの可視化を提供でき、より制限の少ない条件下で試験できる代替金属アナログ材料を使用するという新しいアプローチを提案し、検証することで、このギャップに対処します。
3. 研究目的と研究課題:
*研究目的:
主な研究目的は、砂型鋳造実験において、液体金属の流れ、特に溶融アルミニウムを可視化するための水のアナログとして、スクシノニトリル(SCN)の適合性を評価することです。この研究は、SCNがその独自の特性により、溶融金属の流れ挙動を効果的に模倣できるかどうかを判断することを目的としています。
*主な研究課題:
- スクシノニトリル(SCN)は、鋳造プロセスにおける液体アルミニウムの流れを可視化するために、水と比較してより正確な金属アナログとして機能するか?
- SCNを使用した正確な金属流れアナログ試験を達成するために考慮すべき重要な無次元数は何か?
- SCNの流れ挙動は、実験的にも数値シミュレーション的にも、同様の鋳造条件下で水と溶融アルミニウムの両方の流れとどのように比較されるか?
*研究仮説:
この研究では、スクシノニトリル(SCN)は、溶融アルミニウムと同様の体心立方(BCC)結晶構造と樹枝状晶状凝固、および扱いやすい融点(〜60℃)のため、水よりも優れた金属アナログであると仮説を立てています。この研究ではさらに、フルード数と壁面粗さが、鋳造実験において正確な金属流れアナログを達成するための重要な無次元変数であると想定しています。
4. 研究方法
*研究デザイン:
本研究では、液体流れ挙動を分析するために、実験的調査と数値シミュレーションを組み合わせた混合法アプローチを採用しました。
*データ収集方法:
実験は、水とSCNを作動流体として使用し、透明なアクリル鋳型内で実施され、以前の研究[17](図1)からのベンチマーク砂型鋳造形状を再現しました。流れの可視化は、300fpsのハイスピードビデオ録画によって達成され、SCNの視認性を高めるために緑色の食用色素が添加されました。数値シミュレーションは、Flow3D Castソフトウェアを使用して、同等の条件下でのアルミニウム、水、およびSCNの流れをモデル化するために実行されました。
*分析方法:
この研究では、水、SCN、およびシミュレーションされたアルミニウムの流れプロファイルを、流れパターンの視覚的分析による定性的な比較と、鋳型充填時間とスプルーおよびランナーの平均速度の測定による定量的な比較の両方によって比較しました。無次元数、特にフルード数、レイノルズ数、およびウェーバー数を計算し、異なる流体間の流れの類似性に及ぼす影響を分析しました。実験結果は、数値シミュレーションの結果およびアルミニウム流れのベンチマークX線実験データ[17]とも比較されました。
*研究対象と範囲:
この研究は、ベンチマークアルミニウム板(10 mm × 200 mm × 100 mm)[17]を鋳造するために設計された簡略化された底ゲート砂型鋳造形状における液体流れ挙動に焦点を当てました。この研究では、水とSCNをアナログ流体として使用し、比較の基準として溶融アルミニウムの流れを対象としました。範囲は鋳型充填段階に限定され、凝固の側面は主にSCNをアナログ材料として選択する文脈で考慮されました。
5. 主な研究結果:
*主な研究結果:
実験結果は、SCN流れ試験が水モデルと比較して溶融アルミニウムの流れプロファイルをより正確に再現したことを示しました。具体的には、「実験結果は、SCN流れ試験が溶融アルミニウムの流れプロファイルをより正確に再現し、金属流れ研究のための金属アナログとしての有用性を検証したことを示しています。」研究では、フルード数と壁面粗さが、正確な金属流れアナログを達成するための重要な無次元変数として特定されました。
*統計的/定性的な分析結果:
流れパターンの定性的な比較(図7、図8、図9、図11、図12、図13、図14)は、SCNの流れが水流よりも以前のX線研究[17]からのアルミニウムの流れに視覚的により類似していることを示しました。定量的な分析(表9、表10、表11)は、水のレイノルズ数を一致させると充填時間が類似するものの、流れ挙動はSCNと比較してアルミニウムの代表性が低いままであることを示しました。より高いフルード数試験は、より高い速度とより短い充填時間を示しました(表9)。
*データ解釈:
これらの知見は、水モデルにおけるレイノルズ数の類似性は、充填時間のいくらかの類似性を提供できるものの、溶融金属の流れパターンを正確に表現することを保証するものではないことを示唆しています。フルード数の類似性は、全体的な流れのダイナミクスを捉えるためにより重要であるように思われます。SCNは、レイノルズ数が低いにもかかわらず(SCNの場合は6800、アルミニウムの場合は28,000)、水よりも溶融アルミニウムに定性的に類似した流れパターンを示し、無次元数の一致だけでなく、材料特性の重要性を示しています。この研究では、ムーディ線図分析(図15)によって示されるように、壁面粗さと圧力降下が流れの類似性に及ぼす潜在的な影響も強調しました。
*図の名前リスト:
- 図 1. 以前の実験研究[17]に基づいた鋳造形状、単位はmm。
- 図 2. [17]の研究からの充填画像。
- 図 3. 鋳型部品のCAD設計。
- 図 4. 組み立てられたアクリル鋳型の例(以前の試験から)。
- 図 5. SCN、アルミニウム、および水のシミュレーション結果(a)0.7秒(b)0.9秒(c)1秒(d)1.2秒。
- 図 6. 予想されるアルミニウムの流れ条件。
- 図 7. フルード数不一致(左)対フルード数一致(右)の水試験結果(a)プラグ引き抜き後0.5秒、(b)0.74秒(c)1秒、(d)1.24秒。
- 図 8. レイノルズ数不一致(左)対レイノルズ数一致(右)の水試験結果(a)プラグ引き抜き後0.5秒、(b)0.74秒(c)1秒、(d)1.24秒。
- 図 9. スクシノニトリル試験結果(a)プラグ引き抜き後0.5秒、(b)0.74秒(c)1秒、(d)1.24秒。
- 図 10. SLA印刷チャネル内の水(左)とSCN(右)。
- 図 11. 砂型鋳型内のアルミニウム(左[17])、砂型鋳型シミュレーション内のアルミニウム(中央)、および一致したSCN可視化(右)。
- 図 12. 砂型鋳型内のアルミニウム(左)、砂型鋳型シミュレーション内の水(左中央)、フルード数不一致のアクリル内の水(右中央)、フルード数一致のアクリル内の水(右)。
- 図 13. 砂型鋳型内のアルミニウム(左)、砂型鋳型シミュレーション内の水(左中央)、レイノルズ数不一致のアクリル内の水(右中央)、レイノルズ数一致のアクリル内の水(右)。
- 図 14. 砂型鋳型内のアルミニウム(左)、砂型鋳型シミュレーション内のスクシノニトリル(中央)、アクリル内のスクシノニトリル(右)。
- 図 15. ムーディ線図[61](1)アクリル内の水 Re ≈ >28,000(2)アクリル内のSCN Re ≈ 6800(3)Re ≈ 28,000での物質の相対粗さは、SCNによって発生する圧力降下と相関しています。
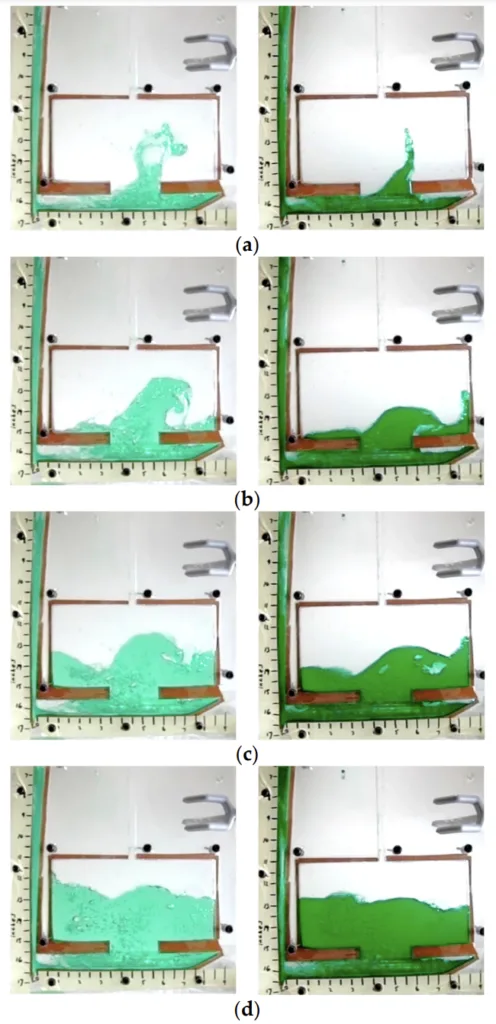
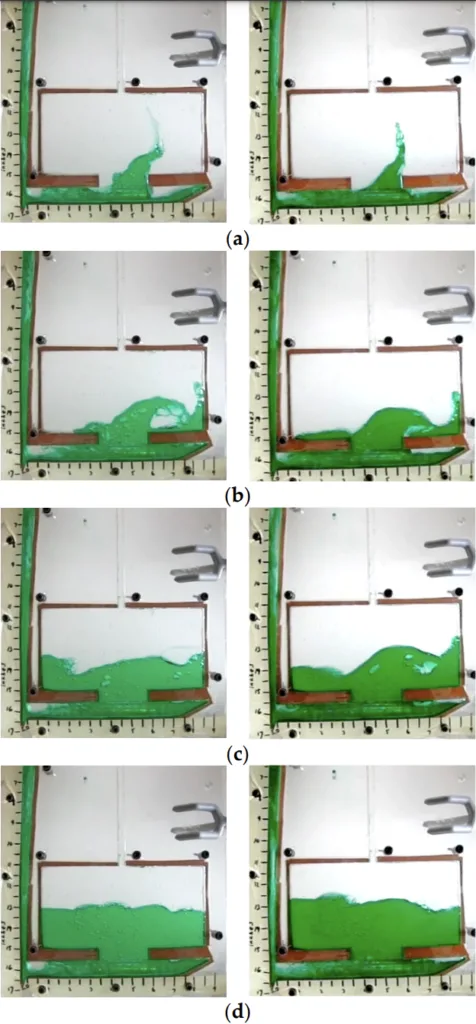
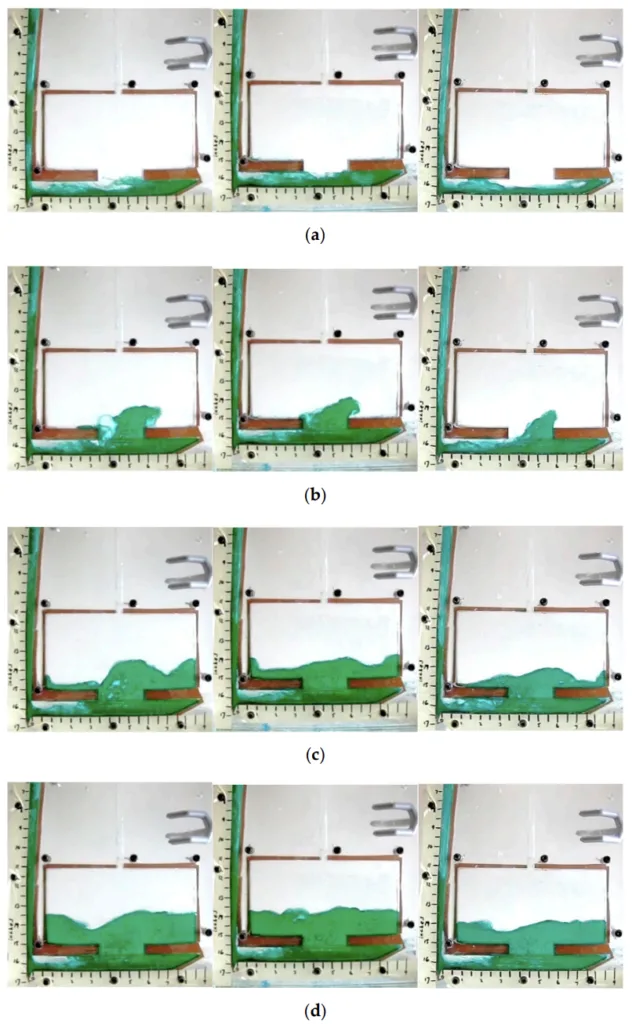
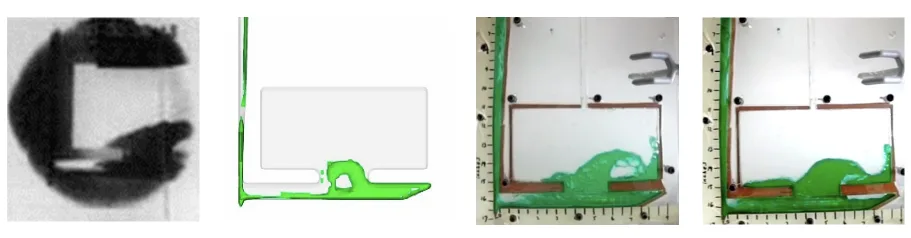
6. 結論と考察:
*主な結果の要約:
この研究は、スクシノニトリル(SCN)が砂型鋳造実験において液体アルミニウムの流れを可視化するための水よりも効果的な金属アナログであると結論付けています。「実験結果は、SCN流れ試験が溶融アルミニウムの流れプロファイルをより正確に再現し、金属流れ研究のための金属アナログとしての有用性を検証したことを示しています。」水モデルは簡略化された表現を提供できますが、SCNは、溶融金属との材料特性の類似性が高いため、流れ挙動のより正確な定性的および潜在的に定量的な表現を提供します。この研究では、アナログ試験におけるフルード数の類似性の重要性を強調し、壁面粗さと圧力降下が流れの類似性に影響を与える重要な要因であり、厳密なレイノルズ数の一致よりも重要である可能性があることを示唆しています。
*研究の学術的意義:
この研究は、鋳造研究のための溶融流れを正確に可視化するために、新しい鋳造流体力学実験を通してSCNを適用した最初の報告された研究です。これは、金属流れ可視化技術の基本的な理解に貢献し、鋳造研究のための貴重なツールとしてのSCNの使用を検証します。この知見は、水モデルとレイノルズ数の類似性への過度の依存に異議を唱え、正確なアナログ試験には、他の無次元数と材料特性を考慮する必要があることを強調しています。
*実際的な意味合い:
SCNの金属アナログとしての応用成功は、高価で複雑な鋳造実験やX線施設への依存を減らし、実験室環境での鋳造流体力学の実験的調査のための新しい道を開きます。「この研究からの知見は、ランナー、インゲート、および統合された充填-給湯-凝固研究などの将来の金属流れ分析で使用できます。」このアプローチは、特にアディティブマニュファクチャリングによって可能になった複雑な形状の革新的なゲートシステムの設計と検証を促進し、統合された流れ-凝固シミュレーションのためのより正確な数値モデルの開発に貢献できます。この論文で詳述された方法論は、「革新的なゲート形状の検証のためのロードマップ」も提供します。
*研究の限界:
この研究では、砂型鋳型と比較して熱特性と表面粗さが異なるアクリル鋳型の使用など、限界があることを認めています。「アクリル鋳型の限られた熱容量は、SCNをより高い温度で注ぐことを禁じており、鋳型の深刻なひび割れにつながる可能性があり、アクリルに代わる材料が今後の研究の焦点となります。」さらに、この研究は主に流れの可視化に焦点を当てており、流れ条件と結果として生じる凝固挙動の複合的な影響を十分に調査していません。
7. 今後のフォローアップ研究:
*フォローアップ研究の方向性:
今後の研究では、砂型鋳型条件をより適切に模倣するために、熱容量が改善され、表面粗さを制御できる代替の透明鋳型材料を調査する必要があります。SCNを金属アナログとしての可能性を最大限に活用するために、鋳造条件下でのSCNの凝固挙動と金属凝固との相関関係をさらに調査する必要があります。「さらに、今後の研究では、溶融金属に類似した、表面に酸化物を形成する液体金属のアナログを調査して、溶融流れで一般的に発生する酸化物二重皮膜をより正確にエミュレートする必要があります。」
*さらなる探求が必要な分野:
さらなる探求が必要な分野には、以下が含まれます。
- 熱特性と表面特性を調整した高度な透明材料の調査。
- 鋳造条件下でのSCNの凝固挙動とその金属凝固との相関関係の研究。
- 溶融金属の挙動をより適切に表現するために、SCN実験に表面酸化物形成を組み込む方法の開発。
- 鋳型内の定量的でリアルタイムの速度測定のために、容量性センサーまたはその他のセンサーをSCNベースの実験に統合すること。「最後に、容量性センサーを鋳型に組み込むことで、従来の砂型鋳型における金属流れの詳細な速度の基準を提供できます[62]。」
8. 参考文献:
- EPA Metal Casting 2016. Available online: https://archive.epa.gov/sectors/web/html/casting.html (accessed on 7 December 2022).
- Shinde, V.D.; Mhamane, D.A. Evaluation of Sand Quality in Thermal Sand Reclamation System. Therm. Sci. Eng. 2018, 2, 538.
[CrossRef] - Campbell, J. Entrainment Defects. Mater. Sci. Technol. 2006, 22, 127–145. [CrossRef]
- Cross, M.; McBride, D.; Croft, T.N.; Williams, A.J.; Pericleous, K.; Lawrence, J.A. Computational Modeling of Mold Filling and
Related Free-Surface Flows in Shape Casting: An Overview of the Challenges Involved. Metall. Mater. Trans. B 2006, 37, 879–885.
[CrossRef] - Mi, J.; Harding, R.A.; Campbell, J. Effects of the Entrained Surface Film on the Reliability of Castings. Metall. Mater. Trans. A 2004,
35, 2893–2902. [CrossRef] - Campbell, J. Complete Casting Handbook, 1st ed.; Elsevier: Amsterdam, The Netherlands, 2015; ISBN 9780444635099.
- Dai, X.; Yang, X.; Campbell, J.; Wood, J. Effects of Runner System Design on the Mechanical Strength of Al-7Si-Mg Alloy Castings.
Mater. Sci. Eng. A 2003, 354, 315–325. [CrossRef] - Tiryakio ˘glu, M.; Campbell, J.; Alexopoulos, N.D. Quality Indices for Aluminum Alloy Castings: A Critical Review. Metall. Mater.
Trans. B 2009, 40, 802–811. [CrossRef] - Sama, S.R.; Wang, J.; Manogharan, G. Non-Conventional Mold Design for Metal Casting Using 3D Sand-Printing. J. Manuf.
Process. 2018, 34, 765–775. [CrossRef] - Sama, S.R.; Badamo, T.; Lynch, P.; Manogharan, G. Novel Sprue Designs in Metal Casting via 3D Sand-Printing. Addit. Manuf.
2019, 25, 563–578. [CrossRef] - Cleary, P.W.; Ha, J. Three-Dimensional Smoothed Particle Hydrodynamics Simulation of High Pressure Die Casting of Light
Metal Components. J. Light Met. 2002, 2, 169–183. [CrossRef] - Kermanpur, A.; Mahmoudi, S.; Hajipour, A. Numerical Simulation of Metal Flow and Solidification in the Multi-Cavity Casting
Moulds of Automotive Components. J. Mater. Process. Technol. 2008, 206, 62–68. [CrossRef] - Renukananda, K.H.; Ravi, B. Multi-Gate Systems in Casting Process: Comparative Study of Liquid Metal and Water Flow. Mater.
Manuf. Process. 2016, 31, 1091–1101. [CrossRef] - Sutaria, M.; Ravi, B. Computation of Casting Solidification Feed-Paths Using Gradient Vector Method with Various Boundary
Conditions. Int. J. Adv. Manuf. Technol. 2014, 75, 209–223. [CrossRef] - Sutaria, M.; Gada, V.H.; Sharma, A.; Ravi, B. Computation of Feed-Paths for Casting Solidification Using Level-Set-Method. J.
Mater. Process. Technol. 2012, 212, 1236–1249. [CrossRef] - Lee, P.; Chirazi, A.; See, D. Modeling Microporosity in Aluminum–Silicon Alloys: A Review. J. Light Met. 2001, 1, 15–30. [CrossRef]
- Sirrell, B.; Holliday, M.; Campbell, J. Benchmark Testing the Flow and Solidification Modeling of Al Castings. JOM 1996, 48, 20–23.
[CrossRef] - Kashiwai, S.; Ohnaka, I.; Kimatsuka, A.; Kaneyoshi, T.; Ohmichi, T.; Zhu, J. Numerical Simulation and X-Ray Direct Observation
of Mould Filling during Vacuum Suction Casting. Int. J. Cast Met. Res. 2005, 18, 144–148. [CrossRef] - Di Sabatino, M.; Syvertsen, F.; Arnberg, L.; Nordmark, A. An Improved Method for Fluidity Measurement by Gravity Casting of
Spirals in Sand Moulds. Int. J. Cast Met. Res. 2005, 18, 59–62. [CrossRef] - Sulaiman, S.; Hamouda, A.M.S. Modelling and Experimental Investigation of Solidification Process in Sand Casting. J. Mater.
Process. Technol. 2004, 155–156, 1723–1726. [CrossRef] - Johnson, W.H.; Bishop, H.F.; Pellini, W.S. Gating Factors. Foundry 1954, 102–272.
- Richins, D.S.; Wetmore, W.O. Fluid Mechanics Applied to Founding. AFS Trans. 1951, 1–24.
- Skov-Hansen, S.; Green, N.R.; Tiedje, N.S. Experimental Analysis of Flow of Ductile Cast Iron in Stream Lined Gating Systems.
Giessereiforschung. 2009, 60. - Tiedje, N. Flow through Bends in Gating Systems in Vertically Parted Moulds. AFS Trans. 1999, 581–590.
- Tiedje, N.S.; Larsen, P. Investigation of the Stability of Melt Flow in Gating Systems. Metall. Mater. Trans. B Process Metall. Mater.
Process. Sci. 2011, 42, 189–201. [CrossRef] - Cao, H.; Shen, C.; Wang, C.; Xu, H.; Zhu, J. Direct Observation of Filling Process and Porosity Prediction in High Pressure Die
Casting. Materials 2019, 12, 1099. [CrossRef] [PubMed] - Thomas, B.G.; Mika, L.J.; Najjar, F.M. Simulation of Fluid Flow inside a Continuous Slab-Casting Machine. Metall. Trans. B 1990,
21, 387–400. [CrossRef] - Thomas, B.G.; Najjar, F.M. Finite Element Modelling of Turbulent Fluid Flow and Heat Transfer in Continuous Casting. Appl.
Math. Model. 1991, 15, 226–243. [CrossRef] - Sahai, Y.; Emi, T. Criteria for Water Modeling of Melt Flow and Inclusion Removal in Continuous Casting Tundishes. ISIJ Int.
1996, 36, 1166–1173. [CrossRef] - Kuyucak, S. Sponsored Research: Clean Steel Casting Production—Water Modeling Studies of Bottom-Pouring Ladle Operations.
Trans. Am. Foundry Soc. 2006, 114, 811–818. - Beckermann, C. Water Modeling of Steel Flow, Air Entrainment and Filtration. In Proceedings of the 46th SFSA Technical and
Operating Conference, Chicago, IL, USA, 4–7 November 1992; pp. 1–18. - Derollez, P.; Lefebvre, J.; Descamps, M.; Press, W.; Fontaine, H. Structure of Succinonitrile in Its Plastic Phase. J. Phys. Condens.
Matter 1990, 2, 6893–6903. [CrossRef] - Glicksman, M.E.; Schaefer, R.J.; Ayres, J.D. Dendritic Growth—A Test of Theory. Metall. Trans. A 1976, 7, 1747–1759. [CrossRef]
- Janz, G.J.; Fitzgerald, W.E. Infrared Spectrum and Molecular Structure of Succinonitrile. J. Chem. Phys. 1955, 23, 1973–1974.
[CrossRef] - Fitzgerald, W.E.; Janz, G.J. Vibrational Spectra and Molecular Structure of 1,2-Dicyanoethane. J. Mol. Spectrosc. 1957, 1, 49–60.
[CrossRef] - Weinberg, F.; Chalmers, B. Dendritic Growth in Lead. Can. J. Phys. 1951, 29, 382. [CrossRef]
- Weinberg, F.; Chalmers, B. Further Observations on Dendritic Growth in Metals. Can. J. Phys. 1952, 30, 488. [CrossRef]
- Chalmers, B. The Preparation of Single Crystals and Bicrystals by the Controlled Solidification of Molten Metals. Can. J. Phys.
1953, 31, 132. [CrossRef] - Huang, S.C.; Glicksman, M.E. Overview 12: Fundamentals of Dendritic Solidification-I. Steady-State Tip Growth. Acta Metall.
1981, 29, 701–715. [CrossRef] - Teng, J.; Liu, S. Re-Determination of Succinonitrile (SCN)–Camphor Phase Diagram. J. Cryst. Growth 2006, 290, 248–257. [CrossRef]
- Shang, S.; Han, Z.; Luo, A.A. Study on the Response of Dendritic Growth to Periodic Increase–Decrease Pressure in Solidification
via in Situ Observation Using Succinonitrile. J. Cryst. Growth 2018, 498, 85–92. [CrossRef] - Losert, W.; Shi, B.Q.; Cummins, H.Z. Evolution of Dendritic Patterns during Alloy Solidification: From the Initial Instability to the
Steady State. Proc. Natl. Acad. Sci. USA 1998, 95, 439–442. [CrossRef] - Karma, A.; Lee, Y.H.; Plapp, M. Three-Dimensional Dendrite-Tip Morphology at Low Undercooling. Phys. Rev. E 2000, 61,
3996–4006. [CrossRef] - Jeong, J.-H.; Dantzig, J.A.; Goldenfeld, N. Dendritic Growth with Fluid Flow in Pure Materials. Metall. Mater. Trans. A 2003, 34,
459–466. [CrossRef] - Trivedi, R.; Shen, Y.; Liu, S. Cellular-to-Dendritic Transition during the Directional Solidification of Binary Alloys. Metall. Mater.
Trans. A 2003, 34, 395–401. [CrossRef] - Chopra, M.A.; Glicksman, M.E.; Singh, N.B. Dendritic Solidification in Binary Alloys. Metall. Trans. A Phys. Metall. Mater. Sci.
1988, 19, 3087–3096. [CrossRef] - Shen, H.F.; Beckermann, C. An Experimental Study of Deformation of a Columnar Dendritic Mushy Zone Using a Transparent
Succinonitrile-Acetone Alloy. Metall. Mater. Trans. B Process Metall. Mater. Process. Sci. 2002, 33, 69–78. [CrossRef] - Esaka, H.; Wakabayashi, T.; Shinozuka, K.; Tamura, M. Origin of Equiaxed Grains and Their Motion in the Liquid Phase. ISIJ Int.
2003, 43, 1415–1420. [CrossRef] - Khalifa, W.; Tsunekawa, Y.; Okumiya, M. Ultrasonic Grain Refining Effects in A356 Al-Si Cast Alloy. AFS Trans. 2010, 91–98.
- Bryne, O. Performance Comparison of C-Si, Mc-Si and a-Si Thin Film PV by PVsyst Simulation. J. Optoelectron. Adv. Mater. 2013,
15, 326–334. [CrossRef] - Tin, P.; de Groh, H.C., III. Surface Tension and Viscosity of Succinonitrile—Acetone Alloys Using Surface Light Scattering
Spectrometer. Int. J. Thermophys. 2004, 25, 1143–1153. [CrossRef] - Ceynar, D.L.; Beckermann, C. Measurement of the Density of Succinonitrile—Acetone Alloys. J. Cryst. Growth 2001, 222, 380–391.
[CrossRef] - Petrakis, L.; Rao, A. Rotational Transition and Self-Diffusion in Polycrystalline Succinonitrile. J. Chem. Phys. 1963, 39, 1633–1635.
[CrossRef] - Sigma-Aldrich. Material Safety Data Sheet. 2018, pp. 1–8. Available online: https://www.sigmaaldrich.com/US/en/sds/
aldrich/160962 (accessed on 7 December 2022). - Hockaday, L.A. Rapid 3D Printing of Anatomically Accurate and Mechanically Heterogeneous Aortic Valve Hydrogel Scaffolds.
Int. Soc. Biofabr. 2012, 4, 035005. [CrossRef] [PubMed] - Morgan, A.J.L.; Hidalgo, L.; Jose, S.; Jamieson, W.D.; Wymant, M.; Song, B.; Stephens, P.; Barrow, D.A.; Castell, O.K. Simple and
Versatile 3D Printed Microfluidics Using Fused Filament Fabrication. PLoS ONE 2016, 11, e0152023. [CrossRef] [PubMed] - Cooper, D.E.; Stanford, M.; Kibble, K.A.; Gibbons, G.J. Additive Manufacturing for Product Improvement at Red Bull Technology.
J. Mater. 2012, 41, 226–230. [CrossRef] - Amili, O.; Schiavazzi, D.; Moen, S.; Jagadeesan, B. Hemodynamics in a Giant Intracranial Aneurysm Characterized by in Vitro 4D
Flow MRI. PLoS ONE 2018, 13, e0188323. [CrossRef] - Kinstlinger, I.S.; Miller, J.S.; Miller, J.S.; Miller, J.S. 3D-Printed Fluidic Networks as Vasculature for Engineered Tissue. Lab Chip
2016, 16, 2025–2043. [CrossRef] - Klein, J.; Stern, M.; Franchin, G.; Kayser, M.; Inamura, C.; Dave, S.; Weaver, J.C.; Houk, P.; Colombo, P.; Yang, M.; et al. Additive
Manufacturing of Optically Transparent Glass. 3D Print. Addit. Manuf. 2015, 2, 92–105. [CrossRef] - Munson, B.R.; Young, F.D.; Okiishi, T.H. Fundamentals of Fluid Mechanics; John Wiley & Sons: Hoboken, NJ, USA, 2006; ISBN
978-0-471-67582-2. - Sama, S.R.; MacDonald, E.; Voigt, R.; Manogharan, G. Manogharan Measurement of Metal Velocity in Sand Casting during Mold
Filling. Metals 2019, 9, 1079. [CrossRef]
Disclaimer/Publisher’s Note: The statements, opinions and data contained in all publications are solely those of the individual
author(s) and contributor(s) and not of MDPI and/or the editor(s). MDPI and/or the editor(s) disclaim responsibility for any injury to
people or property resulting from any ideas, methods, instructions or products referred to in the content.
9. 著作権:
*この資料は、"[Casey Bate, Philip King, Jay Sim and Guha Manogharan]"の論文:「液体アルミニウムの流れを可視化し鋳造科学を進歩させるための新しいアプローチ (A Novel Approach to Visualize Liquid Aluminum Flow to Advance Casting Science)」に基づいています。
*論文ソース: https://doi.org/10.3390/ma16020756
この資料は上記の論文に基づいて要約されたものであり、商業目的での無断使用は禁止されています。
Copyright © 2025 CASTMAN. All rights reserved.